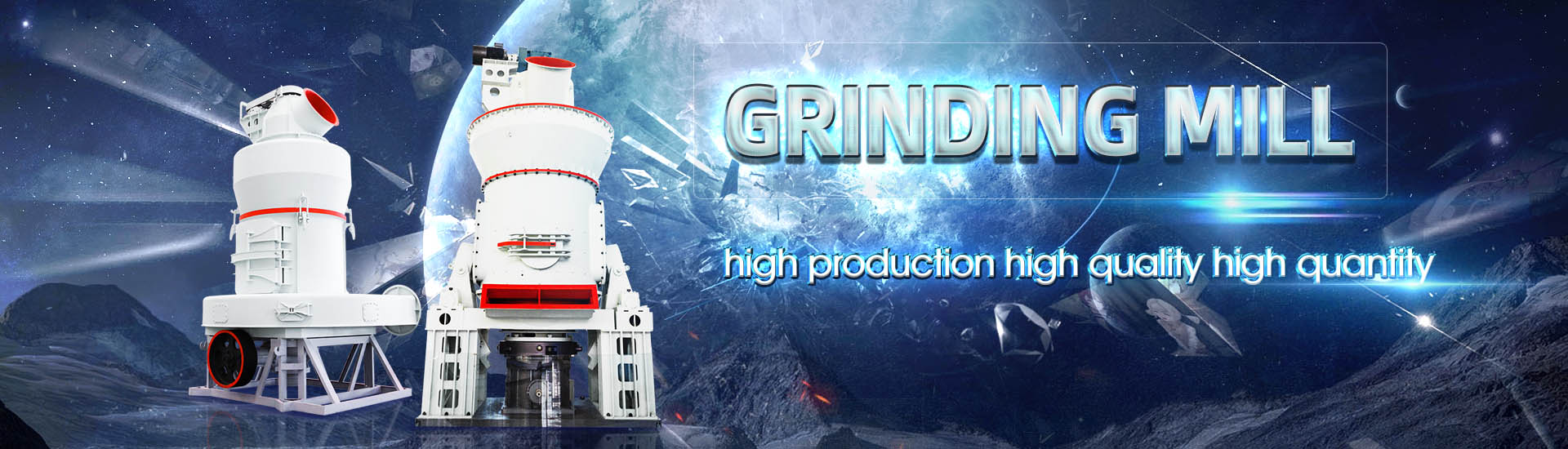
Cement grinding roller quality assurance period
.jpg)
Thomas Holzinger, Holzinger Consulting, grinding system
For the cement quality of a roller press finish‑grinding system, studies show that for a standard type cement compared to VRM or ball mill, no differences could be observed Only for fine cement types (>4500 Blaine), requiring high early strengths, did the roller press finish‑grinding system Over the past decade, roller compacted concrete (RCC) has been successfully used on projects ranging in complexity from large dams to small building pads Regardless of the project’s size RollerCompacted Concrete Quality Control Manualraw materials, burning, grinding and quality control are supported by a range of chapters addressing critial topics such as maintenance and plant reporting, alongside a detailed The Cement Plant Operations Handbook International Cement Optimization addresses the grinding process, maintenance and product quality The objective is to achieve a more efficient operation and increase the production rate as well as improve the run OPTIMIZATION OF CEMENT GRINDING OPERATION IN BALL MILLS
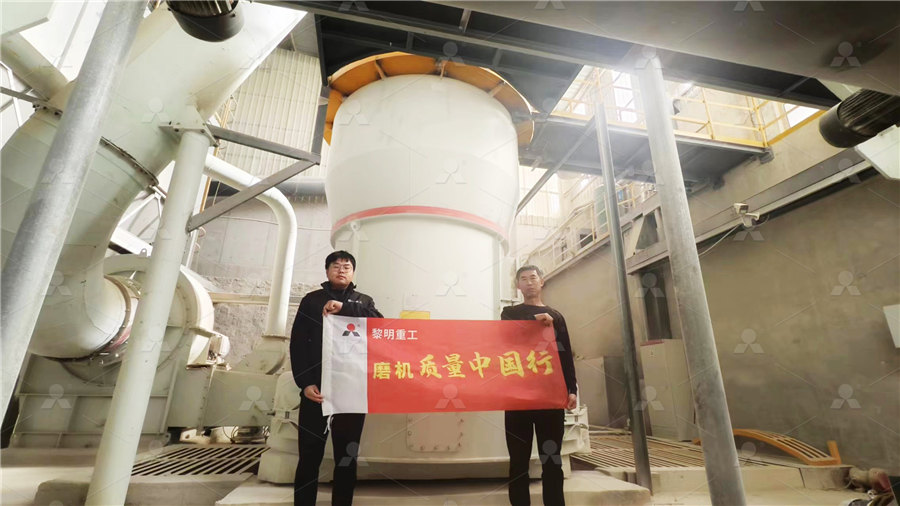
Operational Experience from the United States' First Vertical Roller
the quality of the cement produced is extremely important in cement grinding and there is little experience with cement produced from a VRM in the US market This paper relates the AutoControl scheme of BS12:1991 provides incentives to reduce SD through QA Provision of 5% additive enables better control of strength variation and cost saving Endusers are benefit Quality Assurance of Cement from Production to Construction2024年8月1日 This research provides an effective solution for enhancing energy efficiency and product quality assurance in the cement milling process In the future, we will focus on Collaborative optimization decision making of cement grinding In this paper we describe in details an industrial test performed during the production of slag cement in a vertical mill, showing how the use of grinding aids can improve both process Improvement of cement performances through the use of
.jpg)
Grinding process optimization IEEE Xplore
2017年6月19日 The modular vertical roller mill for grinding cement raw material, cement clinker, and additives with an installed power of up to 12,000 kW was specifically designed to meet the The grinding of the finished cement consumes approximately one third of the total electrical energy of a cement plant Vertical Roller Mills (VRM) have a clearly higher energy efficiency SikaGrind® for vertical roller mills2018年3月14日 They are made of high hardness ZG30Mn material in sizes from 320 tons to solve wear issues CHAENG produces customized grinding roller shells using CAE software and quality assurance testing Their roller shells Grinding roller shell PDF SlideShare2018年7月1日 Among the industries, the nonmetallic industry was reported as the third largest energy user and accounted for about 12% of the global energy use [1]Within this portion, cement industry had the majority of the utilization with 85–12% [1], [2]US Energy Information Administration (EIA) [7] named cement industry as the most energy intensive among the Energy and cement quality optimization of a cement grinding circuit
.jpg)
Roller press:Efficient grinding solutions Indian Cement Review
2021年7月1日 Stability in operation: Feeding material like fly ash, GGBS are fine in nature and they show a fineness below 3 mm hence where other grinding systems like vertical roller mills required water spray to form a grinding bed but in roller press when a premixing of fines with coarse material is made properly it can efficiently grind up to higher fineness [below 5 per cent The wheel hub is the core part of a vertical roller mill that performs grinding with the grinding rollers The quality of the wheel hub is essential for the normal operation of the grinding roller assembly The roller shell In the later period, each product is strictly 360° nondestructive inspected before leaving the factory Wood pattern Wheel Hub For Vertical Roller Mill Robust Cement Spares2024年8月1日 Cement is a fundamental material in the construction industry, in which the growth of China’s sector has also stimulated consistent progress in the cement industry [1]With regard to cement production, the energy consumption of the grinding process accounts for 40% of the entire production process [2], [3]Additionally, the fineness of the grinding process directly Collaborative optimization decision making of cement grinding Loesche VRMs in the Holcim Group 3 Grinding Systems and Cement Types 4 5 6 7 Holcim Approach to ensure high VRM Performance and Reliability Focus of Holcim and 06 Flacher Holcim Vertical Roller Mills For Clinker Grinding
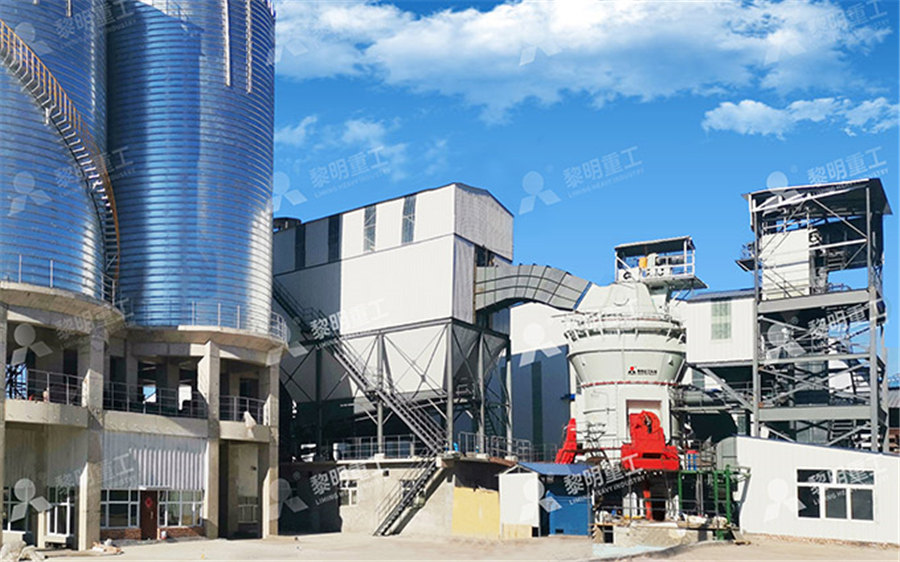
Quality Assurance of Cement PDF
VDZ's quality surveillance organization underwent changes over the past decade to transition from nationally focused quality surveillance to internationally oriented quality assurance in line with harmonized European standards and regulations The organization certified around 540 cement and binder products from 64 plants in the reported period, maintaining its core function The cement roller press is a type of material crushing machine which is often used in cement plants It usually works together with a ball mill to form a pregrinding or finalgrinding system for the grinding of raw materials, coal, and clinker Compared with the traditional tube mill and ball mill, the roller press has lower energy consumption and higher production efficiency, Hydraulic Roller Press AGICO Cement Plant2022年8月10日 Depending on the quality of clinker and type of cement, blending material/gypsum are added in controlled proportion to produce a quality product to meet the prescribed quality as per given codes Optimum fineness needs to be found for the type of raw materials, coal, and clinker to avoid overgrinding, which comes with ‘excess energy’ Efficient grinding unit selection impacts profitability Indian Cement 2016年10月5日 In this chapter an introduction of widely applied energyefficient grinding technologies in cement grinding and description of the operating principles of the related equip‐ ments and comparisons over each other in terms of grinding efficiency, specific energy consumption, production capacity and cement quality are given A case study per‐ formed on a EnergyEfficient Technologies in Cement Grinding
.jpg)
DOUDCGAN: Optimization of cement grinding operational
Therefore, this paper decides to use the cement specific surface area, which reflects the cement product quality, and the unit power consumption, which reflects the production efficiency, as the objective functions, with the 14 variables selected in Table 1 as the decision variables to optimize the cement grinding processWithout proper grinding, cement quality could suffer, affecting the overall structural integrity of concrete applications Process Overview of Cement Grinding Grinding in cement manufacturing typically involves breaking down clinker nodules and other raw materials into finer particlesGrinding in Cement Manufacturing: Key Process, Types of Mills, 2017年5月19日 Grinding is an essential operation in cement production given that it permits to obtain fine powder which reacts quickly with water, sets in few hours and hardens over a period of weeks i Overview of cement grinding: fundamentals, This is the solution for grinding aids sika can offer Grinding aids, strength enhancers and quality improvers are based on chemical products Grinding aids work mainly by dispersing ground cement particles to avoid agglomerates, enabling an increase in production of up to 25 per cent 1 In vertical roller mills, they can additionally be used to reduce vibrations and the amount of Grinding Aids Cement Admixture Sika
.jpg)
Operational Experience from the United States' First Vertical Roller
QUALITY CONTROL In a cement vertical roller mill grinding is performed in closed circuit and with an integral high efficiency separator This arrangement will give a good steep PSD Experience has shown that the overall product particle size distribution is consistent with that obtained from a ball mill grinding plant with a modern high Understand the fundamentals and gain insights on how to improve the performance and productivity, efficiency, and product quality of your grinding systems This 3day seminar covers ball and vertical mills with a focus oncomminution theory, design basis, operational principles, control and regulation, process troubleshooting, calculation methods, and optimizationCement Production Seminar: GrindingQuality assurance certificate is released along with Cement being packed as per customer’s needs Quality Control / Assurance and Management Systems Implementation: Thousands of different quality control and assurance tests are performed to ensure the quality of each bag of cement and the clinker producedQuality Control Assurance Process – #1 Quality Cement in PakistanOne stop cement spare parts supplier roller press Roller press developed in the mid1980s, is a modern, energyefficient cement grinding equipment It serves as a precrushing unit in cement grinding systems, working alongside other components like separators and ball mills The roller press offers advantages such as high crushing ratiosRoller Press Sinoma Cement spare parts
.jpg)
Cement grinding Vertical roller mills versus ball mills
grinding conditions associated with fine grinding of cement clinker and related products, enabling a high grinding efficiency and stable operation Figure 3: H However, despite a generally good performance of vertical roller mills used for grinding of cement and related products the vertical roller mill is still inferior to the ball5 Calculation of the Top Size Grinding Media 6 Ball Charges analysis calculator Weight and Surface of the Grinding Charges 7 Ball Charge Makeup Calculator 8 Ball Mill Simulation 9 Grinding Media Wear Rate Monochamber Mill 10 Grinding Media Wear Rate 2 chambers Mill 11 Marked Ball Test Calculator Section 2: Volume Load Power Kit 12Training Courses based on the Grinding SoftwareThe document summarizes quality assurance of cement from production to construction It discusses customer requirements, raw material constraints, the cement standard migration process, quality plans involving product Quailty Assurance of Cement PDF Cement Quality Lucky Cement Corp in 1993 and commissioned in 1994, for grinding cement at its Pu Shin plant While producers were initially concerned that the quality of the cement produced Ball mill system LoescheCEMENTS GROUND IN THE VERTICAL ROLLER MILL FULFIL THE QUALITY
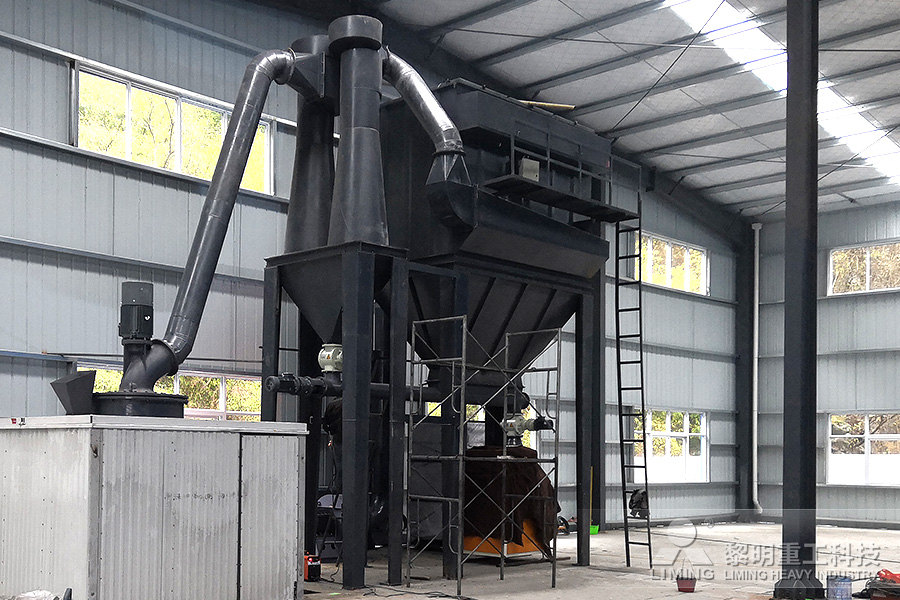
Vertical Roller Mill Indian Cement Review
2021年10月14日 The vertical roller mill is suitable for grinding quartz, feldspar, calcite, cement clinker, activated carbon, dolomite, granite and other nonflammable burst materials whose hardness are below 93 The innovative design ensures that it grinds the material directly on the disc, with low energy consumption The roller is not contact with the disc directly in the []2019年1月3日 Clinker grinding technology is the most energyintensive process in cement manufacturing Traditionally, it was treated as "low on technology" and "high on energy" as grinding circuits use more than 60 per cent of total energy consumed and account for most of the manufacturing cost Since the increasing energy cost started burning the benefits significantly, Clinker grinding technology in cement manufacturing2019年1月4日 This article discusses the recent trends in varying requirements, critical selection criteria for selection of grinding technology for a given application The grinding technology for cement production has evolved over period of last 100 years, matching with the trends of types and specifications of cements, scaling up in plant capacities, changing limestone and solid fuel Technology trends in grinding systems Indian Cement ReviewINTERNATIONAL JOURNAL OF ENGINEERING SCIENCES RESEARCH TECHNOLOGY, 2014 Rolling is an important steel production process Productivity and quality improvements in metal rolling are possible by paying a detailed attention to the various roll failure modesA proper understanding of the causes of roll failure modes is usually complex and depends on the GLOBAL CEMENT: GRINDING Major vertical roller mill
.jpg)
Field Based Quality Assessment of Cement ResearchGate
2019年9月30日 Furthermore, results of design mix showed that M and Sa cements could be adopted in the sites under study with minimum cement content of 340 kg/m 3 for M20 and 375 kg/m 3 for M25 concretes whereas Condition in one of the grinding chambers of the mill Results of Optimization The graphical analysis presented in Figure 2 represents progress of grinding along the length of the mill after optimizing the grinding process rogress of grinding is clearly visible in Desired p the graphs Figure 2: Analysis of longitudinal samplesOPTIMIZATION OF CEMENT GRINDING OPERATION IN BALL MILLSCommissioning Guide Lines Free download as PDF File (pdf), Text File (txt) or read online for free The document provides instructions for commissioning various components of a cement plant, including the raw mill, limestone crushing, shale/gypsum/coal crushing, raw meal handling, and kiln startup It describes checking equipment is correctly installed and calibrated before Commissioning Guide Lines PDF Mill (Grinding) CementBesides, when used together with a ball mill, it can be used in various process flows, like pregrinding, mixing, semifinished grinding, finished grinding, and more Due to the change in its grinding principles, this rolling machine and its grinding system have more advantages, like 50100% lower power consumption, and 100300% higher productivityPFG200180 Cement Roller Press
.jpg)
Grinding roller shell PDF SlideShare
2018年3月14日 They are made of high hardness ZG30Mn material in sizes from 320 tons to solve wear issues CHAENG produces customized grinding roller shells using CAE software and quality assurance testing Their roller shells 2018年7月1日 Among the industries, the nonmetallic industry was reported as the third largest energy user and accounted for about 12% of the global energy use [1]Within this portion, cement industry had the majority of the utilization with 85–12% [1], [2]US Energy Information Administration (EIA) [7] named cement industry as the most energy intensive among the Energy and cement quality optimization of a cement grinding circuit2021年7月1日 Stability in operation: Feeding material like fly ash, GGBS are fine in nature and they show a fineness below 3 mm hence where other grinding systems like vertical roller mills required water spray to form a grinding bed but in roller press when a premixing of fines with coarse material is made properly it can efficiently grind up to higher fineness [below 5 per cent Roller press:Efficient grinding solutions Indian Cement ReviewThe wheel hub is the core part of a vertical roller mill that performs grinding with the grinding rollers The quality of the wheel hub is essential for the normal operation of the grinding roller assembly The roller shell In the later period, each product is strictly 360° nondestructive inspected before leaving the factory Wood pattern Wheel Hub For Vertical Roller Mill Robust Cement Spares
.jpg)
Collaborative optimization decision making of cement grinding
2024年8月1日 Cement is a fundamental material in the construction industry, in which the growth of China’s sector has also stimulated consistent progress in the cement industry [1]With regard to cement production, the energy consumption of the grinding process accounts for 40% of the entire production process [2], [3]Additionally, the fineness of the grinding process directly Loesche VRMs in the Holcim Group 3 Grinding Systems and Cement Types 4 5 6 7 Holcim Approach to ensure high VRM Performance and Reliability Focus of Holcim and 06 Flacher Holcim Vertical Roller Mills For Clinker Grinding VDZ's quality surveillance organization underwent changes over the past decade to transition from nationally focused quality surveillance to internationally oriented quality assurance in line with harmonized European standards and regulations The organization certified around 540 cement and binder products from 64 plants in the reported period, maintaining its core function Quality Assurance of Cement PDFThe cement roller press is a type of material crushing machine which is often used in cement plants It usually works together with a ball mill to form a pregrinding or finalgrinding system for the grinding of raw materials, coal, and clinker Compared with the traditional tube mill and ball mill, the roller press has lower energy consumption and higher production efficiency, Hydraulic Roller Press AGICO Cement Plant
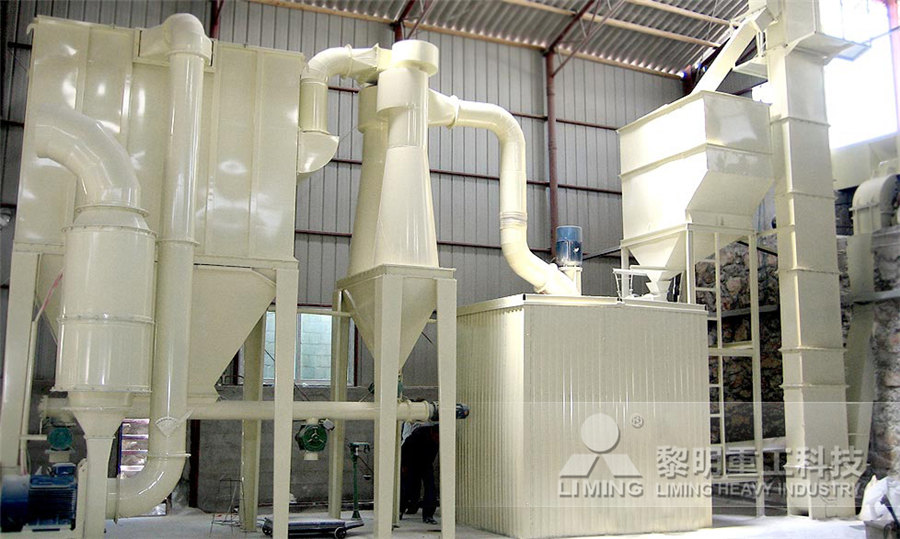
Efficient grinding unit selection impacts profitability Indian Cement
2022年8月10日 Depending on the quality of clinker and type of cement, blending material/gypsum are added in controlled proportion to produce a quality product to meet the prescribed quality as per given codes Optimum fineness needs to be found for the type of raw materials, coal, and clinker to avoid overgrinding, which comes with ‘excess energy’ 2016年10月5日 In this chapter an introduction of widely applied energyefficient grinding technologies in cement grinding and description of the operating principles of the related equip‐ ments and comparisons over each other in terms of grinding efficiency, specific energy consumption, production capacity and cement quality are given A case study per‐ formed on a EnergyEfficient Technologies in Cement Grinding