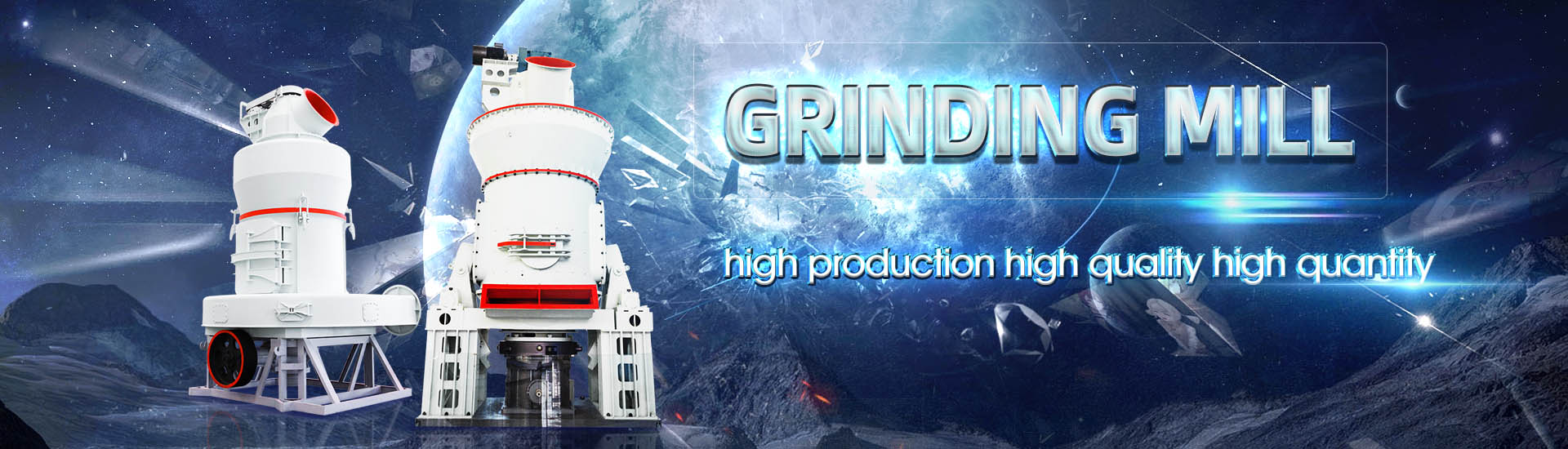
5cm ore mill
.jpg)
IsaMill™ Glencore Technology
IsaMill™ uses horizontal milling to secure better energy efficiency, product size and availability The IsaMill™ has realworld success in 143 metalliferous installations across 23 countries It’s Low height, small crane lifts and simple underfloor media system Large scale Low Installation CostCustomized grinding mill parts including heads, shells, trunnions and liners, main bearings, gears and pinions, and more! Metallic, PolyMet™, Megaliner™, Rubber and Orebed™ mill liners for Grinding mills for mining and minerals processing MetsoFind your ore mill easily amongst the 42 products from the leading brands (Fritsch GmbH, Retsch, Eriez, ) on DirectIndustry, the industry specialist for your professional purchasesOre mill, Ore grinding mill All industrial manufacturers
.jpg)
A Review of the Grinding Media in Ball Mills for Mineral Processing
2023年10月27日 Grinding media play an important role in the comminution of mineral ores in these mills This work reviews the application of balls in mineral processing as a function of the The wet ball mill is the key equipment for grinding mineral after the crush process It is mainly used in ore beneficiation plant Output Size: 0074089mm; Milling Capacity: 1600t/h; Learn Ball Mill Ball Grinding Mill SKEBall mill is the key equipment for secondary grinding after crushing And it is suitable for grinding all kinds of ores and other materials, no matter wet grinding or dry grindingSinogomine Industrial Technology Co,LtdBall mill machine priceBall milling is a grinding method that reduces the product into a controlled final grind and a uniform size, usually, manganese, iron, steel balls, or ceramic are used in the collision Ball Mill JXSC Mineral
.jpg)
Ultrafine Grinding and the IsaMill™ Technology
The IsaMill™ is a largescale energy efficient continuous grinding technology specifically developed for rugged metalliferrous applications Glencore Technology supplies the IsaMill™ Mill Type Overview Three types of mill design are common The Overflow Discharge mill is best suited for fine grinding to 75 – 106 microns; The Diaphram or Grate Discharge mill keeps coarse particles within the mill for additional AMIT 135: Lesson 7 Ball Mills Circuits – Mining SAG MILL TESTING AN OVERVIEW OF THE TEST PROCEDURES AVAILABLE TO CHARACTERIZE ORE GRINDABILITY AUTHOR: FO VERRET, G CHIASSON AND A MCKEN SGS KEYWORDS Comminution, grindability, grinding, SAG mill, AG mill, milling, HPGR, work index, pilot plant INTRODUCTION The resistance of ore samples to breakage (or hardness) is SAG Mill Testing Test Procedures to Characterize Ore Grindability2016年1月1日 For a rod mill–ball mill circuit, do not apply a mill diameter correction for the ball mill If the rod mill feed is produced by open circuit crushing, use a factor of 12 for the rod mill stage only If the rod mill feed is 80% passing 12 mm or less (eg from a closed circuit crusher) do not apply a rod mill efficiency factorSize Reduction and Energy Requirement ScienceDirect
.jpg)
The performance improvement of a fullscale autogenous mill by setting
2020年10月20日 One of the feed ore properties which can affect the grinding charge of an AG mill is particle size distribution Bergstedt and Fagremo (1977) studied the effect of feed size distribution on the performance of an AG during a series of pilot plant tests They reported that the ideal feed ore to an AG mill should have 10–15 wt% materials coarser than 100 mm Bouajila 2017年3月20日 Investigation on the particle size and shape of iron ore pellet feed using ball mill and HPGR 919 BROZEK, M, SUROWIAK, A, 2007, Effect of particle shape on jig separation efficiency,Physicochemical Problems of Mineral Processing Investigation the ball mill half filled with the grinding media of one inch steel balls counting 100 in number The open end of the mill was closed by clamping the lid tightly to the mill so that no leakage of the material takes place during grinding operation Then the mill was run for a period of 3 min and the reading of energy meter was notedStudies on Batch Grinding of Bauxite Ore in Ball Mill2020年10月18日 An iron ore concentrate sample was ground separately in a pilotscale HPGR mill in multiple passes and a dry opencircuit ball mill to increase the specific surface area of particlesThe effects of iron ore concentrate grinding methods (HPGR and
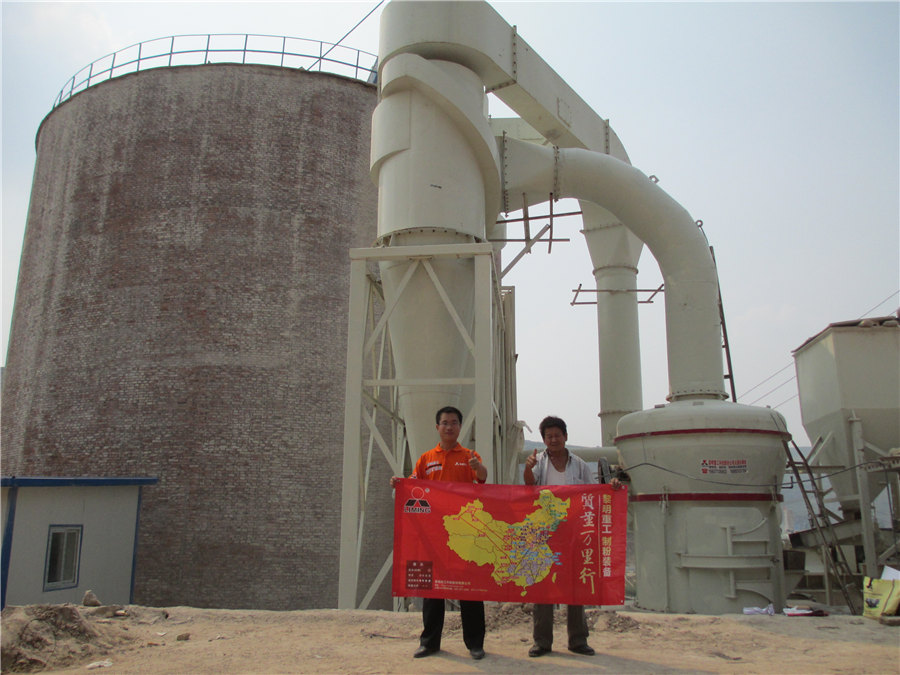
CM European Type Coarse Powder Mill
European Type Coarse Powder Mill is necessary equipment of medium and fine crushing work, Calcium carbonate crushing processing, gypsum crushing processing, power plant desulfurization, nonmetallic ore pulverizing, pulverized coal preparation Capacity: 10100T/H Input size: 30100mm Performance AdvantagesORE MILL Bar Grille, Warren, New Hampshire 1,606 likes 1 talking about this 1,133 were here Serving locallysourced food, craft beer, wine and cocktailsORE MILL Bar Grille Warren NH FacebookThe ore is continuously fed into the barrel of the rod mill The ore is crushed by a moving grinding medium and the product is expelled from the rod mill by a force of overflow and continuous feeding Then proceed to the next step It is generally used when product granularity 80% less than 20% to 05 mm is requiredRod Mill Ore MillForui MachineryThe grinding process was carried out in a cylindrical ball mill with a diameter and length of 186 cm and 215 cm, respectively, as well as a steel ball with a diameter of 25 cm and a weight of 100 grams/ball The optimum data for the grinding process OPTIMIZATION OF LATERITE ORE GRINDING PROCESS USING BALL MILL
.jpg)
Tubular Ball Mills ScienceDirect
2016年1月1日 A grate discharge mill of dimensions 412 m × 396 m was loaded to 40% of its volume with gold ore The mill drew 1095 kW power per tonne of balls To grind the ore to the liberation size the mill was run at 72% of the critical speed when charged with balls 64 mm in size and 79 t/m 3 density2023年2月23日 Varied types/geometries of stirred mills have been produced by different manufacturers, and the comparison task has been accomplished for some of the technologies, ie, Tower mill vs IsaMill(PDF) Performance Comparison of the Vertical and2015年6月16日 Weight and transfer ore to the ball mill Grind dry for 100 revolutions Empty the ball charge and ore through a coarse screen to separate the balls from the ore After mill and balls are swept clean, screen and ground ore through the mesh screen to be tested, using coarser protective screens if necessaryBond Grindability Test Procedure 911MetallurgistParticle Size Reduction and Enlargement JF RICHARDSON, JR BACKHURST, in Chemical Engineering (Fifth Edition), Volume 2, 2002 The rod mill In the rod mill, high carbon steel rods about 50 mm diameter and extending the whole length of the mill are used in place of ballsThis mill gives a very uniform fine product and power consumption is low, although it is not suitable Rod Mill an overview ScienceDirect Topics
.jpg)
AMIT 135: Lesson 5 Crushing – Mining Mill Operator Training
The purpose of the primary crusher is to reduce the ROM ore to a size amenable for feeding the secondary crusher or the SAG mill grinding circuit The ratio of reduction through a primary crusher can be up to about 8:1 Feed: ROM up to 15 m; Product: 300mm (for transport) to 200mm (for SAG mill) Feed Rate: 160 to 13,000 tphThe chromite ore, mill scale, and petroleum coke were dried in an oven at around 473K for 24h Then the materials were ground by a ball mill into various particle sizes (chromite ore: D 80¼147mm Direct Alloying Steel with Chromium by Briquettes Made from 2018年3月1日 This paper elaborates on the development of paste backfill using mill tailings generated during the processing of a uranium ore deposit hosted in dolomitic limestone(PDF) Mill tailings based composites as paste backfill in mines where Ω E is the energycorrected ball wear rate, g per kWh, d R is the diameter of the largest balls in the mill (the recharge size), mm, K d E is the linear wear rate of balls, µm per kWh t −1, Ai is the Bond abrasion index determined in a laboratory test (unitless), F 80 is the feed 80% passing size of the ore, µm, and pH is the water acid/base measurement of the mill pulpBall Mill an overview ScienceDirect Topics
.jpg)
Ball mill characteristics and test conditions Mill Diameter, D (cm
Download Table Ball mill characteristics and test conditions Mill Diameter, D (cm) 204 Length, L (cm) 166 Volume, V (cm 3 ) 5,423 Operational speed, Ν (rpm) 66 from publication 2013年8月3日 In Grinding, selecting (calculate) the correct or optimum ball size that allows for the best and optimum/ideal or target grind size to be achieved by your ball mill is an important thing for a Mineral Processing Engineer AKA Calculate and Select Ball Mill Ball Size for Optimum Gold Ore Ball Mill Manufacturer Coal Grinding Ball Mill And High Screw Classifier Production Line $11,60000 $12,30000 Min order: 1 set Easy Return Factory Supply Powder Grinding Machine Overflow Type Wet Gold Ore Ball Mill Machine For Africa $11,60000 $12,30000High Efficiency Gold Ore Grinding Ball Mill Machine Wet/dry ore grinding vibratory mill,vibration ball mill for mining industry No reviews yet Xinxiang First Vibration Machinery Factory Co, Ltd Custom manufacturer 12 yrs CNore grinding vibratory mill,vibration ball mill for mining industry
.jpg)
Ore Mill Bar Grille Restaurantji
2024年11月27日 Ore Mill Bar Grille is a popular destination for delicious food and warm hospitality The restaurant serves up mouthwatering dishes, including the acclaimed mac and cheese, falloffthebone ribs, and tender pulled pork and brisket The staff is friendly and attentive, with one server going above and beyond to impressThe average diameter of particles fed to the crusher was 200 mm and the SG of the ore was 28 Estimate: 1 the distance between the rolls, 2 the angle of nip, 3 the width of the rolls 62 Establish a relation between the diameter of roll and maximum size of ore when the reduction ratios were 20, 30 and 40 and nip angle was held at 15 Roll Diameter an overview ScienceDirect Topics2016年2月1日 The purpose of this study is to understand how ore loss and dilution affect the mine call factor, with the aim of subsequently improving the quality of ore mined and fed to the millMonitoring ore loss and dilution for minetomill integration in However, ore below the pay limit adds variation to the mill grade as increased mill throughput will be required to make up for the loss of gold, and that impacts on the recovery in the plant It is against these perspectives and findings of this study that the MCF should be seen as a method that identify the real problems underground and when these are addressed, the profitability of Monitoring ore loss and dilution for minetomill integration in
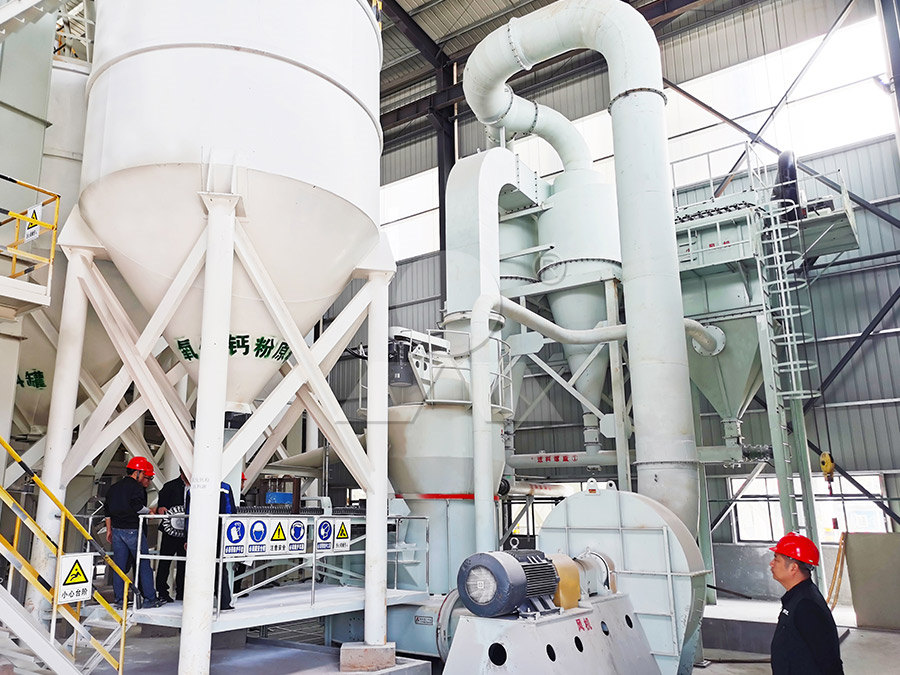
Treatment and water reuse of leadzinc sulphide ore mill wastewaters
2018年10月1日 Treatment and water reuse of leadzinc sulphide ore mill wastewaters by high rate dissolved air flotation Author links open overlay panel A Azevedo, HA Oliveira, J Rubio Show the most important high rate process in ore beneficiation, operates with high volume of water along the many ancillary operations, namely: grinding Ball mill = coarse particles (in the plant ball mill) grinding efficiency Ore grindability (in the lab ball mill) The units of "ball mill grinding efficiency" will be covered in detail in the first part of the module Alternatively, we can say that: Specific grinding rate = Ball mill x Ore grindabilityMODULE #5: FUNCTIONAL PERFOMANCE OF BALL MILLING2015年6月19日 The basic parameters used in ball mill design (power calculations), rod mill or any tumbling mill sizing are; material to be ground, characteristics, Bond Work Index, bulk density, specific density, desired mill tonnage capacity DTPH, operating % solids or pulp density, feed size as F80 and maximum ‘chunk size’, product size as P80 and maximum and finally the type of Ball Mill Design/Power Calculation 911MetallurgistMill Type Overview Three types of mill design are common The Overflow Discharge mill is best suited for fine grinding to 75 – 106 microns; The Diaphram or Grate Discharge mill keeps coarse particles within the mill for additional AMIT 135: Lesson 7 Ball Mills Circuits – Mining
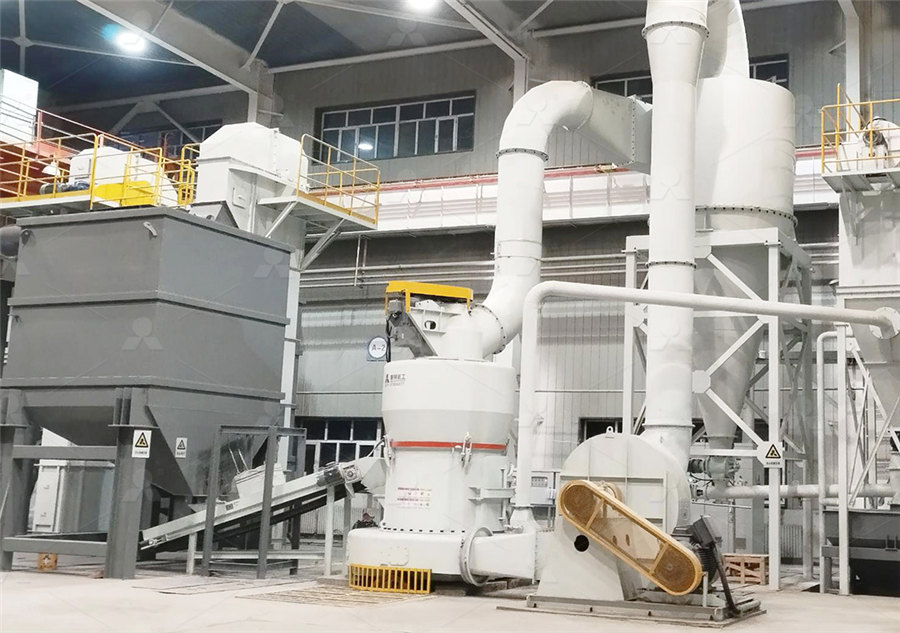
SAG Mill Testing Test Procedures to Characterize Ore Grindability
SAG MILL TESTING AN OVERVIEW OF THE TEST PROCEDURES AVAILABLE TO CHARACTERIZE ORE GRINDABILITY AUTHOR: FO VERRET, G CHIASSON AND A MCKEN SGS KEYWORDS Comminution, grindability, grinding, SAG mill, AG mill, milling, HPGR, work index, pilot plant INTRODUCTION The resistance of ore samples to breakage (or hardness) is 2016年1月1日 For a rod mill–ball mill circuit, do not apply a mill diameter correction for the ball mill If the rod mill feed is produced by open circuit crushing, use a factor of 12 for the rod mill stage only If the rod mill feed is 80% passing 12 mm or less (eg from a closed circuit crusher) do not apply a rod mill efficiency factorSize Reduction and Energy Requirement ScienceDirect2020年10月20日 One of the feed ore properties which can affect the grinding charge of an AG mill is particle size distribution Bergstedt and Fagremo (1977) studied the effect of feed size distribution on the performance of an AG during a series of pilot plant tests They reported that the ideal feed ore to an AG mill should have 10–15 wt% materials coarser than 100 mm Bouajila The performance improvement of a fullscale autogenous mill by setting 2017年3月20日 Investigation on the particle size and shape of iron ore pellet feed using ball mill and HPGR 919 BROZEK, M, SUROWIAK, A, 2007, Effect of particle shape on jig separation efficiency,Physicochemical Problems of Mineral Processing Investigation
.jpg)
Studies on Batch Grinding of Bauxite Ore in Ball Mill
the ball mill half filled with the grinding media of one inch steel balls counting 100 in number The open end of the mill was closed by clamping the lid tightly to the mill so that no leakage of the material takes place during grinding operation Then the mill was run for a period of 3 min and the reading of energy meter was noted2020年10月18日 An iron ore concentrate sample was ground separately in a pilotscale HPGR mill in multiple passes and a dry opencircuit ball mill to increase the specific surface area of particlesThe effects of iron ore concentrate grinding methods (HPGR and European Type Coarse Powder Mill is necessary equipment of medium and fine crushing work, Calcium carbonate crushing processing, gypsum crushing processing, power plant desulfurization, nonmetallic ore pulverizing, pulverized coal preparation Capacity: 10100T/H Input size: 30100mm Performance AdvantagesCM European Type Coarse Powder MillORE MILL Bar Grille, Warren, New Hampshire 1,606 likes 1 talking about this 1,133 were here Serving locallysourced food, craft beer, wine and cocktailsORE MILL Bar Grille Warren NH Facebook
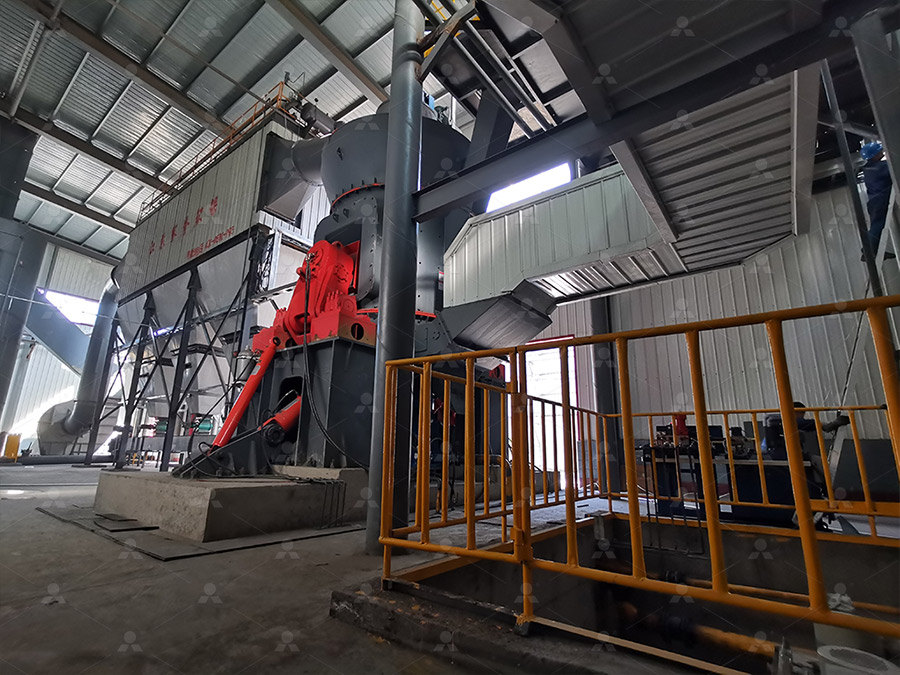
Rod Mill Ore MillForui Machinery
The ore is continuously fed into the barrel of the rod mill The ore is crushed by a moving grinding medium and the product is expelled from the rod mill by a force of overflow and continuous feeding Then proceed to the next step It is generally used when product granularity 80% less than 20% to 05 mm is required