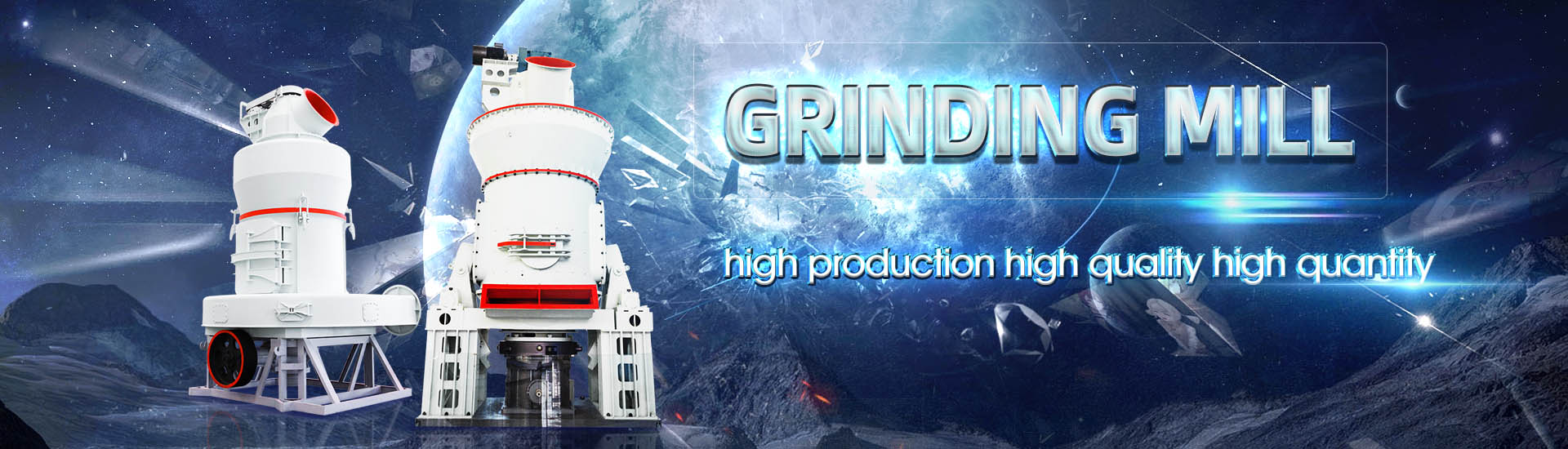
Tianjin Ruihua NdFeB rare earth ore grinding machine factory
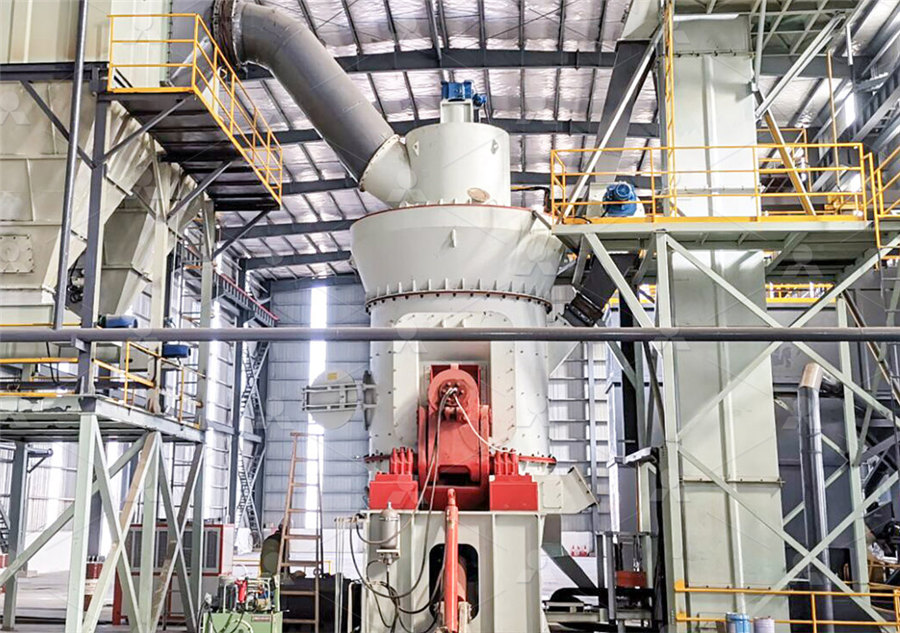
Separation and Recovery of Rare Earths and Iron from NdFeB
2023年9月30日 To address this issue, we conducted tests using a flash furnace to explore the lowtemperature reduction behavior of NdFeB magnet scraps under an H2 atmosphere based 2021年5月1日 Rare earths from the spent NdFeB magnet were selectively recovered by roasting with 3 times stoichiometric amount of NH 4 Cl at 300 °C temperature for 3 h and subsequent Energy efficient process for recovery of rare earths from spent 2015年6月14日 In this investigation, the possibility of a pyrometallurgical treatment of such grinding slurries should be determined Since REEs have a high oxygen affinity, the main Recovery of rare earth elements from NdFeB based grinding slurries2022年12月20日 The recovery by hydro processing of rare earth metals from NdFeB magnets has been widely studied, as well as the recovery by adsorptive processes that have gained Adsorption potential for the concentration and recovery of rare
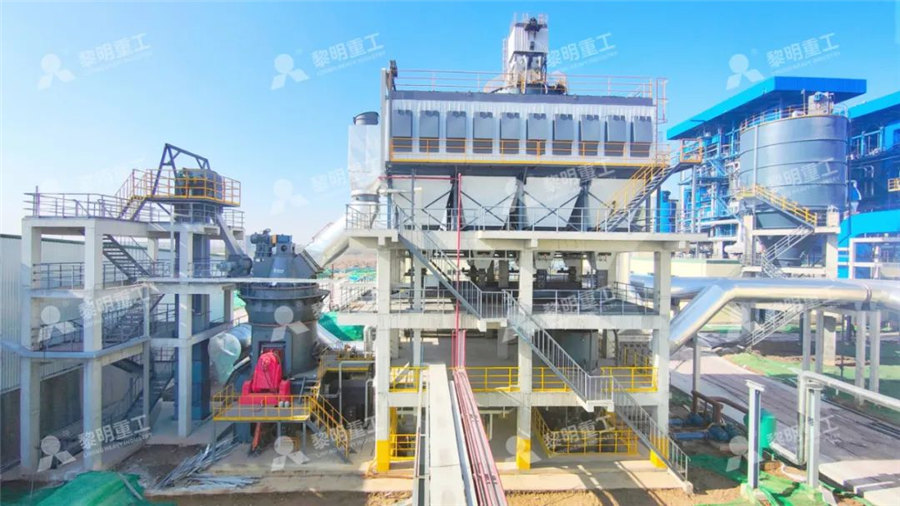
Selective Extraction of RareEarth Elements from NdFeB Magnets
2018年5月25日 Recycling rareearth elements (REEs) from NdFeB magnet waste is an important step toward building a sustainable REE supply chain In this study, we describe an 2021年10月1日 From the perspective of technological innovation, this paper defines the rare earth industry chain into three parts: the upstream mainly involves the extraction and smelting China's rare earth industry technological innovation structure and In this paper, a pyrometallurgical method was used to recover the rare earth elements from the NdFeB based magnet The NdFeB materials was firstly oxidized and then reduced in high RECOVERY OF RARE EARTH ELEMENTS FROM NDFEB MAGNET 2017年2月8日 A recent study has successfully demonstrated the selective sulfation of rare earths from NdFeB magnet scrap via sulfuric acid sulfation and selective decomposition, Selective Sulfation Roasting of Rare Earths from NdFeB Magnet
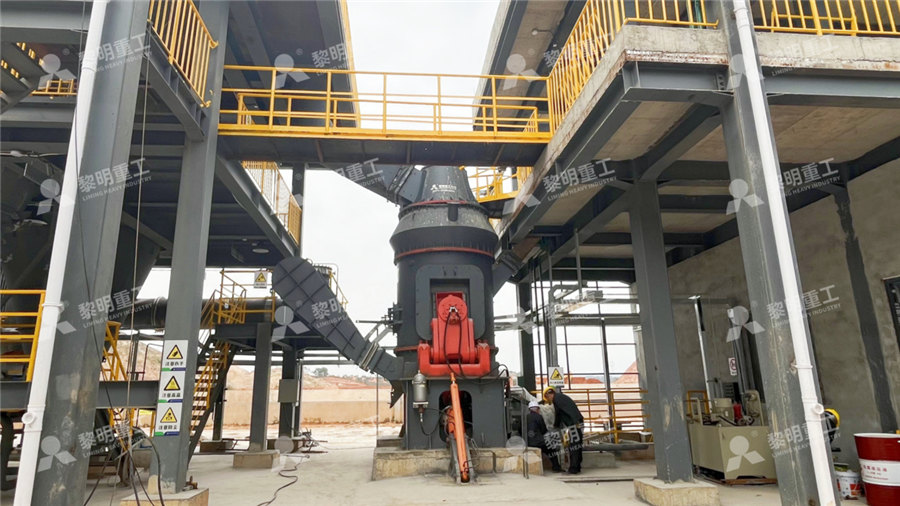
(PDF) Recovery of Rare Earth Elements from Spent
2022年9月27日 China's dominance in rare earth production and supply along with an increase in the available NdFeB magnets in the market [1], strongly motivates the recovery of rare earth elements from secondary 2021年8月1日 Acid leaching of Nd and Fe from roasted NdFeB magnet powders was studied in stirredtank and packedbed reactors The experimental data at sulfuric acid concentrations of 00210 mol/L and at 80 Selective Acid Leaching of Rare Earth Elements from Roasted NdFeB 5 Classifying – Dedusting of fine Powder mClass Highefficiency Fine Classifier ∙ The mClass Highefficiency Fine Classifier, equipped with the patented ConVor® classifier wheel, is suitable for an extremely fine classification (d 97 1 µm to 120 µm) with a closely defined sharpness of cutFine Grinding and Classifying of Rare Earth AlloysOre composition and detailed process data are listed in SI The beneficiation consists of different comminution steps followed by flotation All crushing and grinding To our knowledge so far the only two LCA studies on virgin NdFeB rare earth magnets are carried out by Sprecher et al6 and most recently by Arshi et al23 Sprecher (PDF) Lifecycle Assessment of NdFeB Magnet Production from Rare Earths
.jpg)
(PDF) Hydrometallurgical Recovery of Rare Earth Elements from NdFeB
2020年6月24日 Hydrometallurgical Recovery of Rare Earth Elements from NdFeB Permanent Magnet Scrap: A Review June 2020; prepared under the grinding and alkaline roasting treatments, 942%, 931%, 10% 2023年11月13日 A solvometallurgical process was developed to recover rareearth elements and cobalt from endoflife NdFeB magnets, using the ionic liquid (IL) trihexyltetradecylphosphonium trichloride ([P666,14 Recycling NdFeB Magnets and Rare Earth Fluorescent2021年6月1日 By expanding gravimetric separation to finegrained ore and to sediment systems (loess deposits, shallow to deep marine muds), the grain size of the tailings can be still in the medium silt to Life Cycle Assessment studies of rare earths production2018年2月1日 The hydrometallurgical process of recycling rare earths from NdFeB wastes generally includes calcination of wastes, dissolution of oxidized wastes, separation and extraction of rare earths [8][9 Recovery of rare earths from spent NdFeB magnets of wind
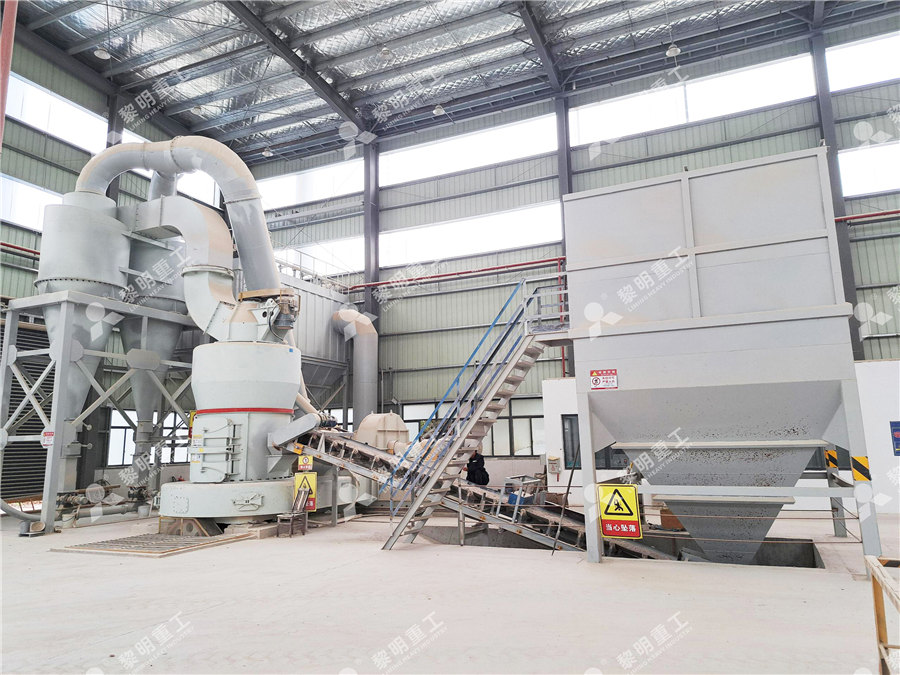
Sustainable Recycling of RareEarth Elements from NdFeB
2021年11月17日 Rare earth elements (REEs) are key materials for the development of renewable energy devices such as highpower magnets for wind turbines, electric vehicles, or fuel cells for hydrogen generation 2024年1月1日 Recent advances in electrochemical methods show promise for more sustainable recycling of rare earth elements (REEs) from endoflife NdFeB permanent magnets(PDF) Recent advances in electrochemical recovery of rare earth 2021年4月27日 NdFeB magnets are widely used in various applications including electric and hybrid vehicles, wind turbines, and computer hard drives They contain approximately 31–32 wt% Rare Earth Elements (PDF) NdFeB Magnets Recycling Process: An 2018年11月7日 A new recycling process for the extraction of rare earths from neodymium–iron–boron (NdFeB) magnet scrap is being developed, based on the direct extraction of rare earths from endoflife (PDF) An Exante LCA Study of Rare Earth Extraction
.jpg)
Energy efficient process for recovery of rare earths from spent NdFeB
2021年2月1日 The weight of NdFeB magnets, which have a life cycle of 1015 years in electric/hybrid cars and 2030 years in wind turbines, can reach 3040 g in electric/hybrid cars and 12 t in wind turbines 2023年12月14日 Material: NdFeB scrap Capacity: 40,000 tons/year Finished product particle size: 300 mesh Finished product use: rare earth materials Main equipment: MTW European version mill NdFeB Grinding Production Line Production Process The onsite raw materials are transported to the European version of the primary mill via a belt conveyor for grinding and NdFeB Powder Making Process Grinding Plant JXSC Mineral2023年3月1日 Rare earth elements are a nonrenewable strategic resource [1]However, undirected development in recent years has caused a serious waste of rare earth resources and irreversible damage to such resources, the supply gap of some rare earth elements is widening year by year [2]Recycling rare earth elements from urban or industrial waste is crucial to Recovery of highvalue rare earth elements from waste NdFeB by NdFeB permanent magnet scrap is regarded as an important secondary resource which contains rare earth elements (REEs) such as Nd, Pr and Dy Recovering these valuable REEs from the NdFeB permanent magnet scrap not only increases economic potential, but it also helps to reduce problems relating to disposal and the environment Hydrometallurgical routes are considered Hydrometallurgical Recovery of Rare Earth Elements from NdFeB
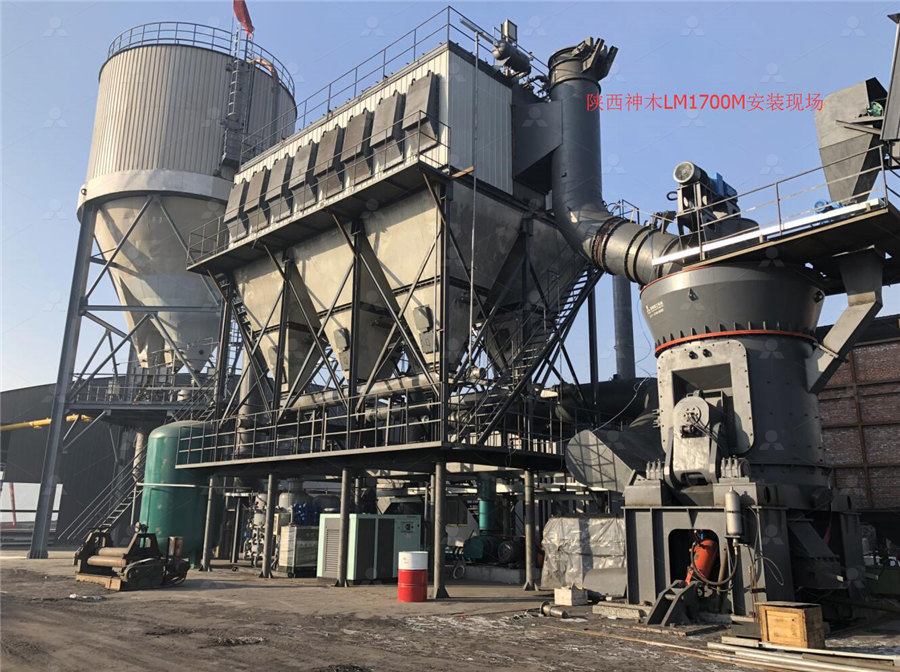
USA Rare Earth Acquires NdFeB Permanent Magnet Manufacturing Equipment
2020年4月10日 Industry sources estimate the global rare earth magnet market will nearly double by 2027 The equipment purchased by USA Rare Earth should provide most of what is needed to reestablish rare earth magnet production in the US and, with the addition of some readily available components, can produce at least 2,000 tons annually of rare earth 2017年2月8日 Kellogg diagram composed of superimposed (Nd Fe)O2SO2 diagrams at 750°C calculated using HSC 50 (21) [21] Selective Sulfation Roasting of Rare Earths from NdFeB Magnet 2023年6月22日 After mechanical pretreatment, the typical hydrometallurgical route of NdFeB magnet recycling starts with leaching in acidic solutions However, due to the high concentration of iron ions in the Recovery of Rare Earth Elements from the Leaching Solutions of 2023年9月30日 A sustainable separation concept for largescale recycling of NdFeB magnets under atmospheric pressure was developed by utilizing a combination of two separation concepts known from the literature Separation and Recovery of Rare Earths and Iron from NdFeB
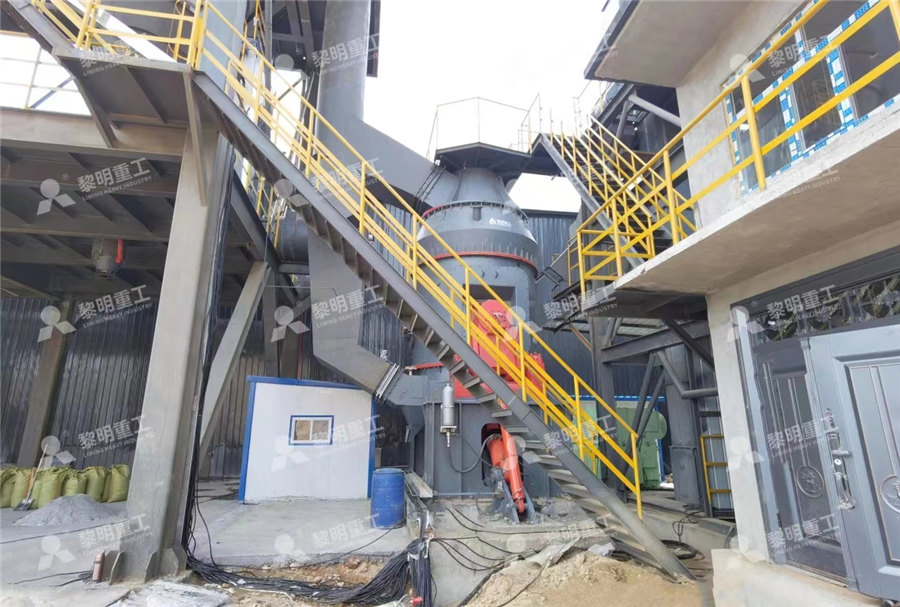
Aeriometallurgical Extraction of Rare Earth Elements from a NdFeB
2018年10月24日 Request PDF Aeriometallurgical Extraction of Rare Earth Elements from a NdFeB Magnet Utilizing Supercritical Fluids There is a global need for efficient and environmentally sustainable 2024年11月21日 All rareearth ores contain less than 10 percent REO and must be upgraded to about 60 percent in order to be processed further They are first ground to a powder and then separated from the other materials in the ore body by various standard processes that include magnetic and/or electrostatic separation and flotation In the case of Mountain Pass Rareearth element Processing Ores BritannicaIn recent decades, NdFeB permanent magnets have emerged as the preeminent rare earth materials, extensively utilized and comprising over 20 % of the global rare earth supply for their production [1], [2]The burgeoning new energy industry has significantly propelled the demand for the NdFeB permanent magnets, essential for generators and drive motors, particularly with the Selective leaching and recovery of rare earth from NdFeB waste 2020年3月1日 Spent NdFeB magnets are highly appealing secondary resources for rare earth elements (REEs), especially for Nd The goal of this study was to investigate electrochemical leaching of Fe and rare earths from NdFeB magnets with sulfuric and oxalic acids at different acid concentrations and current densities and reveal the mechanism of the leaching in varying Electrochemical leaching of rareearth elements from spent NdFeB
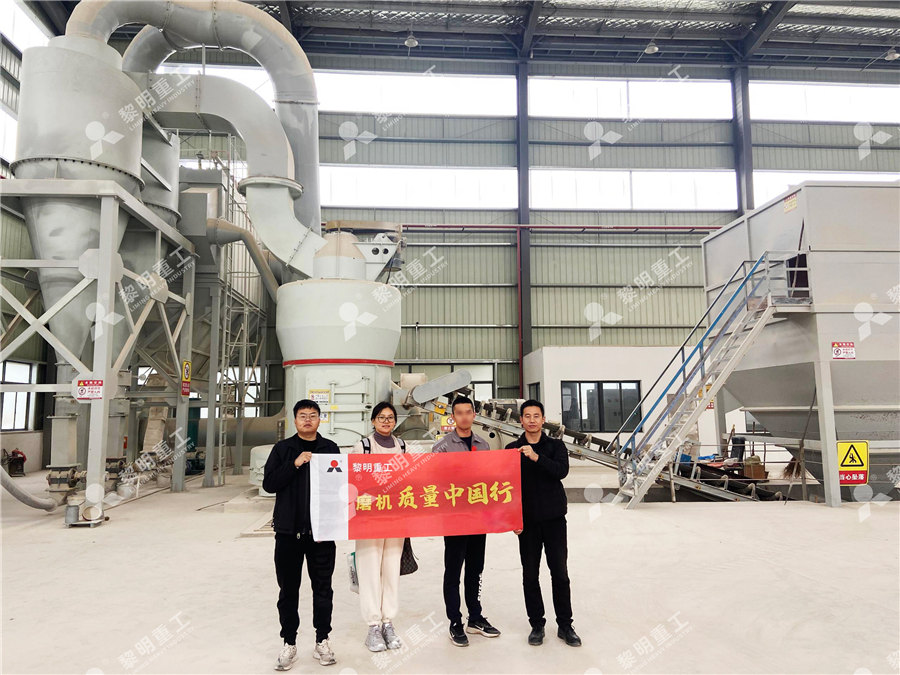
How Are Neodymium Magnets Made Ideal Magnet Solutions
Step #2 Ore Processing and Refining Next, the Rare Earth Ore is crushed and milled Then the ore goes through a flotation process where it is mixed with water and special reagents to separate the rare earth elements from the tailings Depending on the source of the ore, the concentrate may also undergo electrolytic refiningDechang Dalucao REE deposit is classified into a rare earth (bastnasite) deposit, and the minerals have been seriously weathered The rare earth minerals exist mainly in the form of bastnasite and parisite The rare earth minerals have a small monocrystal grain size and are interlocked with other minerals such as barite, fluorite, celestiteProcess mineralogy of Dalucao rare earth ore and design of 2021年12月10日 Recycling rare earth from ultrafine NdFeB waste by capturing fluorine ions in the wastewater and preparing into nanoscale neodynium oxyfluorideRecycling rare earth from ultrafine NdFeB waste by capturing 2023年12月12日 The mined ore will be processed through a circuit of crushing, grinding, floatation, tailings and handling with an output of up to 37,000 tons per year of rare earth concentrate at 27% TREO In Stage 2, a hydrometallurgical plant will be constructed which will process the concentrate from Yangibana into mixed rare earth carbonate (MREC) through a Hastings Targets Early 2025 for Start of Rare Earth Production in
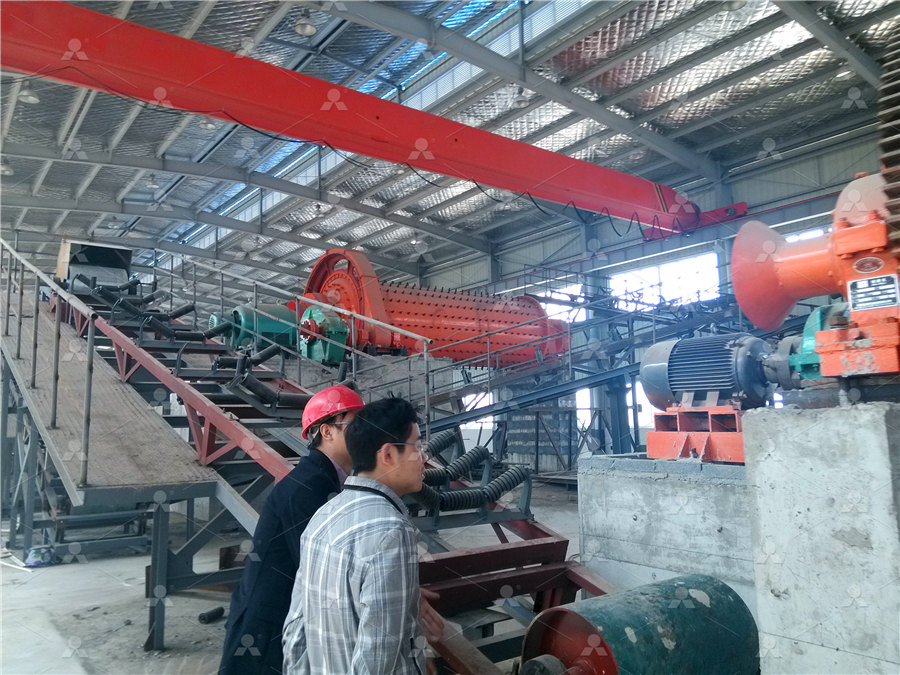
(PDF) Hydrometallurgical Recovery of Rare Earth Elements from NdFeB
About 20–30 wt% scrap is generated during the NdFeB magnets cutting and grinding processes, and 95% of those scraps can be [CrossRef] [PubMed] Dupont, D; Binnemans, K Recycling of rare earths from NdFeB magnets using a combined leaching/extraction system based on the acidity and thermomorphism of the ionic liquid [Hbet][Tf2 N the rareearth oxalate precipitation process, can be reused in the next selective leaching process In this way, a recycling process consuming only air, water, oxalic acid and electricity is From NdFeB magnets towards the rareearth oxides: a recycling 2022年9月27日 China's dominance in rare earth production and supply along with an increase in the available NdFeB magnets in the market [1], strongly motivates the recovery of rare earth elements from secondary (PDF) Recovery of Rare Earth Elements from Spent 2021年8月1日 Acid leaching of Nd and Fe from roasted NdFeB magnet powders was studied in stirredtank and packedbed reactors The experimental data at sulfuric acid concentrations of 00210 mol/L and at 80 Selective Acid Leaching of Rare Earth Elements from Roasted NdFeB
.jpg)
Fine Grinding and Classifying of Rare Earth Alloys
5 Classifying – Dedusting of fine Powder mClass Highefficiency Fine Classifier ∙ The mClass Highefficiency Fine Classifier, equipped with the patented ConVor® classifier wheel, is suitable for an extremely fine classification (d 97 1 µm to 120 µm) with a closely defined sharpness of cutOre composition and detailed process data are listed in SI The beneficiation consists of different comminution steps followed by flotation All crushing and grinding To our knowledge so far the only two LCA studies on virgin NdFeB rare earth magnets are carried out by Sprecher et al6 and most recently by Arshi et al23 Sprecher (PDF) Lifecycle Assessment of NdFeB Magnet Production from Rare Earths2020年6月24日 Hydrometallurgical Recovery of Rare Earth Elements from NdFeB Permanent Magnet Scrap: A Review June 2020; prepared under the grinding and alkaline roasting treatments, 942%, 931%, 10% (PDF) Hydrometallurgical Recovery of Rare Earth Elements from NdFeB 2023年11月13日 A solvometallurgical process was developed to recover rareearth elements and cobalt from endoflife NdFeB magnets, using the ionic liquid (IL) trihexyltetradecylphosphonium trichloride ([P666,14 Recycling NdFeB Magnets and Rare Earth Fluorescent
.jpg)
Life Cycle Assessment studies of rare earths production
2021年6月1日 By expanding gravimetric separation to finegrained ore and to sediment systems (loess deposits, shallow to deep marine muds), the grain size of the tailings can be still in the medium silt to 2018年2月1日 The hydrometallurgical process of recycling rare earths from NdFeB wastes generally includes calcination of wastes, dissolution of oxidized wastes, separation and extraction of rare earths [8][9 Recovery of rare earths from spent NdFeB magnets of wind 2021年11月17日 Rare earth elements (REEs) are key materials for the development of renewable energy devices such as highpower magnets for wind turbines, electric vehicles, or fuel cells for hydrogen generation Sustainable Recycling of RareEarth Elements from NdFeB 2024年1月1日 Recent advances in electrochemical methods show promise for more sustainable recycling of rare earth elements (REEs) from endoflife NdFeB permanent magnets(PDF) Recent advances in electrochemical recovery of rare earth