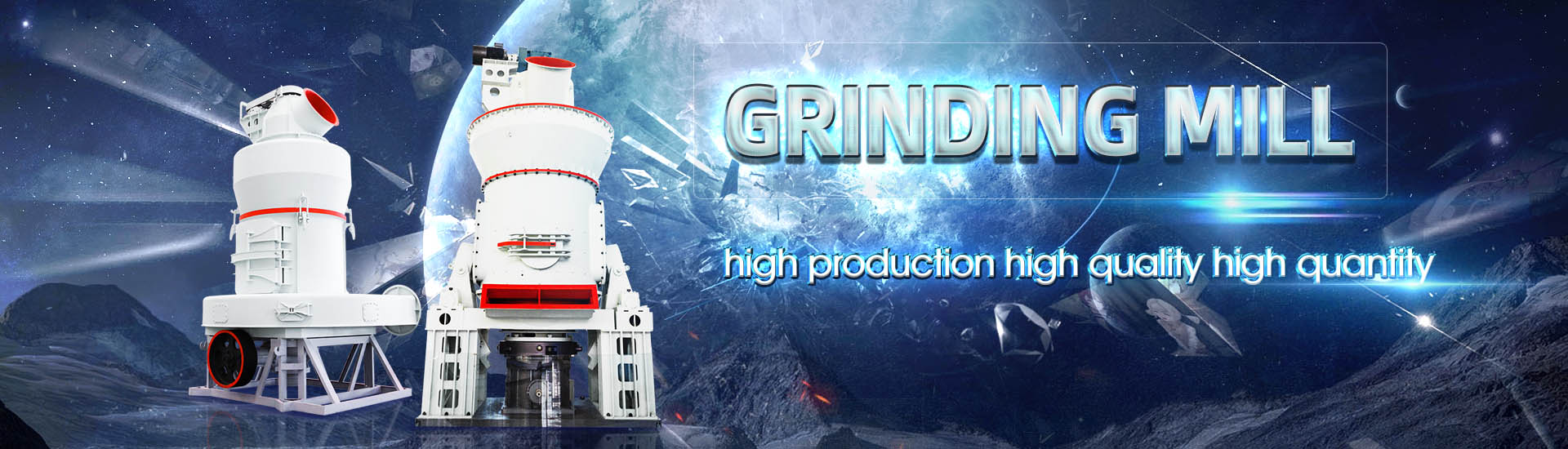
Ore mill rotor needs maintenance project statistics
.jpg)
Operational parameters affecting the vertical roller mill performance
2017年4月1日 Pilot plant test results with various ores showed that low energy consumption feature of vertical roller mills is applicable to the ore industry Grinding test results for zinc ore 2024年10月8日 This article presents an innovative predictive maintenance for grinding mills, aiming to enhance operational efficiency and minimize downtime Leveraging advancements Innovative predictive maintenance for mining grinding mills: from 2022年1月1日 The maintenance of industrial mining machines is a challenging process, especially in the case of critical assets, as it impact the hole process: for instance the grinding Predictive maintenance in mining industry: grinding mill case studypredictive maintenance from remote locations using machine learning, artificial intelligence (AI) and other techniques The company realised many years ago the importance ofExtracting potential ABB
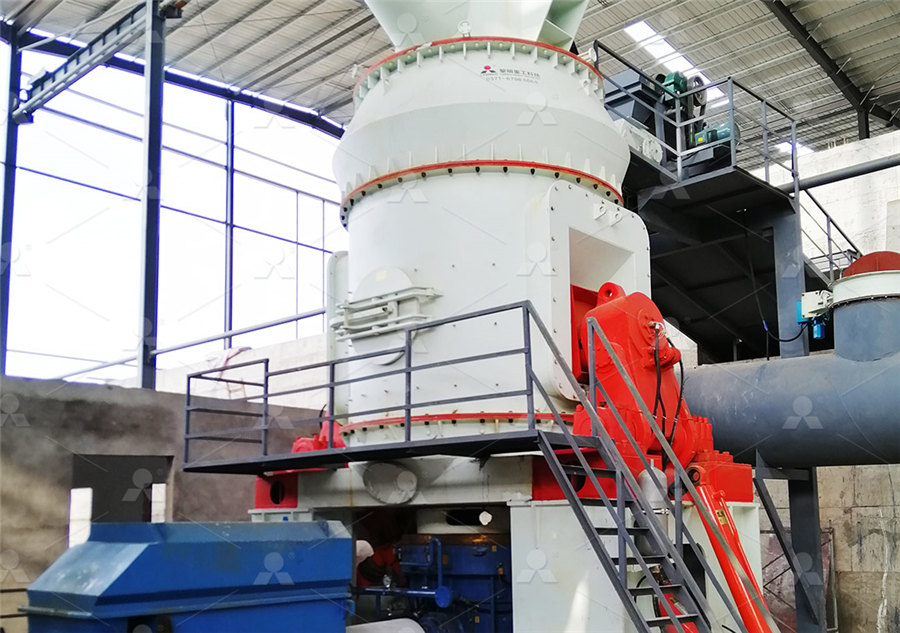
Smart monitoring of mining industry rotating machines : "Angular
Goal: The aim of this project is to implement a new monitoring strategy for ore mills in order to optimize maintenance actions The project addresses the problems of the noisy environmentWhether inching or creeping, you can dramatically shorten the mill’s maintenance time, and thereby significantly boost availability and mill productivity Operational reliability Lower costs SIMINE Gearless mill drives Siemens2014年2月1日 This paper provides a breakdown of operating costs in 63 mines by dividing them into three main categories: mining, milling, and general and administrative (G A) costs The Mine operating costs and the potential impacts of energy and The rotor life can also be maximised by increasing the media load in the mill and slowing the rotor speed down Once the maximum media fill level or an upper torque limit is reached, the mill Case story Grinding solutions Metso Outotec HIGmill increases

Model Based Monitoring of Dynamic Loads and Remaining Useful
2020年8月25日 System supports a database of maintenance actions and elements failures Reports are generated on overloading and RUL Typical elements of hot rolling mill: (a) Technologies for extraction and processing, including gearless mill drives (GMDs) and gearless conveyor drives (GCDs), help operators save energy and achieve greater throughput at large How digitalized gearless drive technology results in energy 2022年9月30日 Working with an experienced project partner will help organize your maintenance plan by conducting the necessary maintenance analysis needed Phoenix Industrial Group of Companies uses industryleading All You Need to Know About Pulp and Paper Mill SAG MILL TESTING AN OVERVIEW OF THE TEST PROCEDURES AVAILABLE TO CHARACTERIZE ORE GRINDABILITY AUTHOR: FO VERRET, G CHIASSON AND A MCKEN SGS KEYWORDS Comminution, grindability, grinding, SAG mill, AG mill, milling, HPGR, work index, pilot plant INTRODUCTION The resistance of ore samples to breakage (or hardness) is SAG Mill Testing Test Procedures to Characterize Ore
.jpg)
Gearless mill drives ABB
• 28 MW GMD for 42' SAG mill Whether it is size or an installation at the highest altitude (4600 masl), ABB’s GMDs are well positioned to contribute to the building of larger and ever more powerful mills — Leading the gearless mill drive evolution The ABB gearless mill drive (GMD) is the most powerful mill drive system available,2023年7月25日 How Often Should Roller Mill Maintenance Be Done? Roller mill maintenance will be unique for every operator and depend on the particular materials going through the machine When asked how often roller mill maintenance should be done, Josh replied, “That’s highly dependent on the abrasiveness of the material and the cleanliness of theMaterial Use Roller Mill Maintenance: What You Need to KnowThe main working part of the hammer mill is the rotor with the hammers The rotor consists of the main shaft, disc, pins and hammers The motor drives the rotor to rotate at high speed in the crushing chamber 50 mm ore enter the crushing chamber from the top inlet with water togetherGold Ore Processing Small Hammer MillThe real gold loss must be traceable if lost during mining operations, but if it cannot be located underground it can only be ascribed as apparent gold loss It is of vital importance that movement of ore from the source to the mill is understood to reduce ore Monitoring ore loss and dilution for minetomill integration in
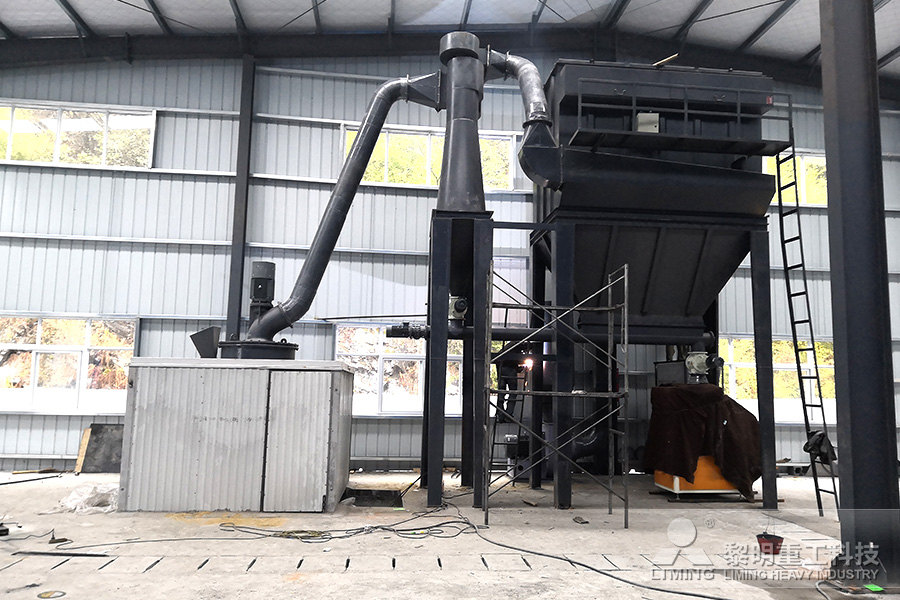
Sampling for Assaying 911Metallurgist
2015年12月10日 Sampling is the most important procedure in arriving at the value of an ore Improper sampling makes other procedures, including assaying, valueless, as the sample must truly represent the ore from which it is taken Before sampling, clean fresh faces must be exposed in order to prevent the possibility of salting2014年6月1日 Further, the long(er) lead times for mega projects need to be shortened Changes in process equipment are significant (ie bigger and fewer in the future) This includes the use of ever increasing float super cells (>600 m 3 and beyond), hybrid energy flotation, large SAGs, >3 m HPGRs, the better correlation of mineralogy with froth vision control, or better design of Ore characterization, process mineralogy and lab automation a International Journal of Engineering and Management Research eISSN: 22500758 pISSN: 23946962 Volume11, Issue2 (April 2021)Design and Analysis of Rotor Assembly of Hammer Mill Machine2019年12月23日 The rotor speed is obtained as 12891 rpm The major factors considered for the material selection are the mechanical properties, wear of materials, environmental properties, fabrication DEVELOPMENT OF A HORIZONTAL SHAFT HAMMER MILL CHAPTER
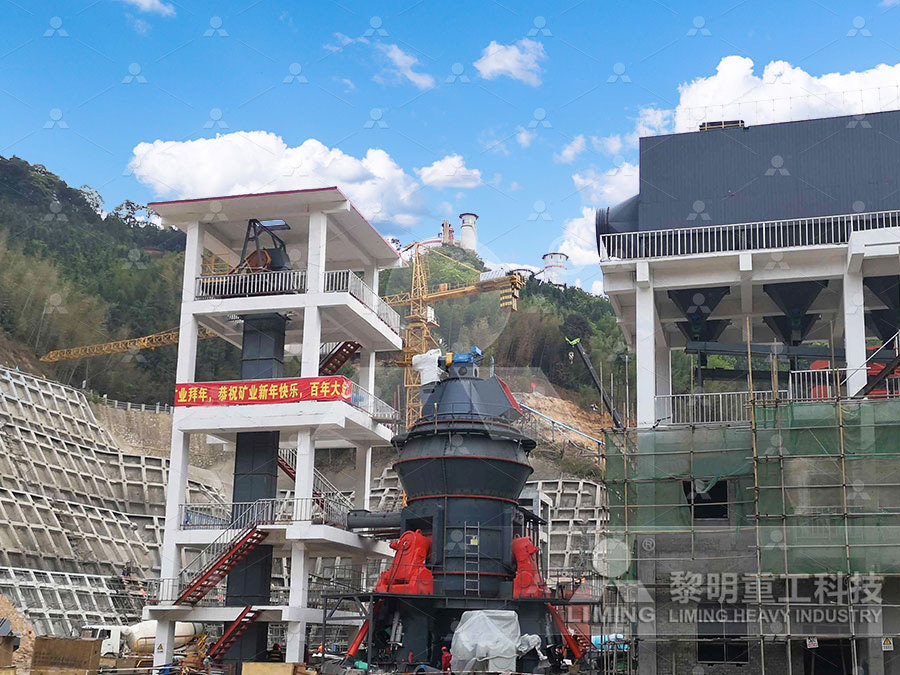
35 Latest Maintenance Statistics for 2024: Data,
2024年11月5日 Knowing what’s going on in the field can help reliability managers develop better preventive maintenance plans This also involves looking at what other maintenance executives are doing to improve their Not only does the vertical mill have a reduced footprint compared to horizontal mills of the same size, but the compact design is optimised to eliminate backpressure problems and remove the risk of bearing seal leakage With no need Vertical mills for fine grinding – FLS2015年9月11日 The mine is closed and now you need to know how to put the SAG or Large Ball Mill in care and maintenance does not have to be complicated to the point where you need bridge erection equipment for lifting a Mill Putting a Ball or SAG Mill on Care and MaintenanceThe project deals with the Manufacturing with Design and Analysis of Hammer Mill Machine and Rotor Assembly of Machine of Capacity of 200 (as in rock ore), Small size electric motors; and hammer mill machine rotor, etc In this project we used the Rolling Contact Bearing, named as UCP209 Bearing which is in the size type of mm, having Design and Analysis of Rotor Assembly of Hammer Mill Machine
[GYQ0R)ZQ]ESS4NJ.jpg)
Ore mill repair and maintenance YouTube
2023年4月4日 The mill is not allowed to refuel at will during normal operation To ensure production safety, if abnormal noise occurs in any part of the mill, 2021年3月23日 this typ e include rotor seizure or insul ation damage due to moisture from the wet ore The renovation cost of a single motor exceeds 25,000 USDEnergy Efficiency Analysis of Copper Ore Ball Mill Drive SystemsO serviço do Google, oferecido sem custo financeiro, traduz instantaneamente palavras, frases e páginas da Web do português para mais de cem outros idiomasGoogle Tradutor2016年7月1日 Employing a weatherproof cabin for rotor blade maintenance extends the annual maintenance period from 8 to 12 month and 3 to 24 hours a day One challenge for SMART is sealing the cabin top and Developing a climbing maintenance robot for tower and rotor
.jpg)
Recurrent Neural Networks for Predictive Maintenance of Mill
system for predictive maintenance based on sensor automated inputs Our subject was a device from Maritsa East 2 power plant – a mill fan The main sensor information we have access to is based on the vibration of the nearest to the mill rotor bearing block Our aim was to create a (nonlinear) model able to predictThe FEECO double rotor hammer mill is a super heavyduty mill adapted to do the toughest jobs with two sets of chain / bar links Our hammer mills reduce dry and semimoist materials with a minimum amount of fines and caking or plastering within the crusher They are ideal for granulated and pelletized materialsHammer Mills FEECO International IncDownload scientific diagram Isometric view of the new design of the hammer mill rotor with hammers in the shape of a circle section ( = 45°), designed in Solid Works from publication: A Isometric view of the new design of the hammer GMDs were selected for this project instead of ringgeared mill drives (RMD) The GMD solution eliminates several critical mechanical components that are used within a conventional mill drive system By mounting the rotor poles directly onto the mill flange, the mill itself becomes the rotor of a synchronous machineGearless mill drive (GMD) and digital services for Kinross ABB
.jpg)
(PDF) ORE SEPARATION BY SCREENING ResearchGate
2017年3月3日 Particle impact noise detection (PIND) test is a kind of reliability screening technique which is used to detect free particle in hermetical components and is specified in MILSTD883E method 20207Traditional ringgeared mill drives comprise a ringshaped gear that encircles the mill and drives it through one or two pinions followed by conventional motors GMDs mount rotor poles directly to the mill body and surround it with the stator ring, incorporating the mill itself into the motor The necessary torque is transmitted between the GMDExtracting potential ABB• 28 MW GMD for 42' SAG mill Whether it is size or an installation at the highest altitude (4600 masl), ABB’s GMDs are well positioned to contribute to the building of larger and ever more powerful mills — Leading the gearless mill drive evolution The ABB gearless mill drive (GMD) is the most powerful mill drive system available,Gearless mill drives ABBSmall footprint, expansive range of mill sizes Vertical arrangement means compact and efficient use of space From 200 to 125,000 Litres and 75kW to 12,500kW installed power We understand every ore is unique and can tailor a solution to best suit your needsSwiss Tower Mills Minerals AG
.jpg)
Double rotor hammer crusher mill Henan Double stage hammer
2024年1月6日 7 Reduced Wear: The dual rotor arrangement can help distribute wear more evenly across the hammers and other wear parts, potentially extending the overall lifespan of the crusher 8 Ease of Maintenance: Some double rotor hammer crushers are designed with features that make maintenance and replacement of wear parts more accessible, reducing 2023年2月15日 The removal of rotor 1 If the cross head part of the rotor or the inside of the bearing is damaged, the rotor needs to be taken out of the Raymond mill 2 Remove half of the grinding hood on the classifier, and remove the vibrating hammer and shovel supportRaymond Roller Mill PartsUltimate Guide Fote Machinerywear to the mill liners and ball consumption, as explained by a concentrator’s operation and maintenance supervisor in the US Furthermore, the mill’s direction of rotation can be simply changed with a switch, so that the wear on the liner is distributed equally at both sides Reduced wear of the liners prolongs the mill maintenance intervalsIncreasing availability through advanced Gearless Drive TechnologyA mill for comminution and separation of lump ore and subsequent recovery of relatively dense components of the ore, said mill including a stationary housing defining an ore reduction chamber therewithin, an impactor rotor drum rotatably mounted within said housing, said rotor drum supporting a plurality of circumferentially spaced ore breaker hammers and fixedly supporting USA Comminution/recovery ore mill Google Patents
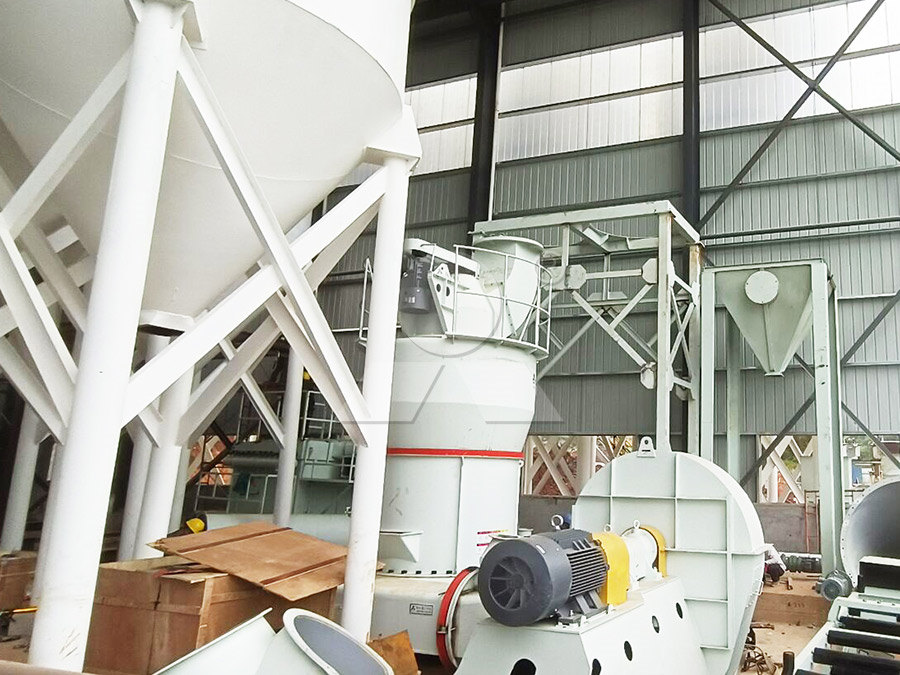
All You Need to Know About Pulp and Paper Mill
2022年9月30日 Working with an experienced project partner will help organize your maintenance plan by conducting the necessary maintenance analysis needed Phoenix Industrial Group of Companies uses industryleading SAG MILL TESTING AN OVERVIEW OF THE TEST PROCEDURES AVAILABLE TO CHARACTERIZE ORE GRINDABILITY AUTHOR: FO VERRET, G CHIASSON AND A MCKEN SGS KEYWORDS Comminution, grindability, grinding, SAG mill, AG mill, milling, HPGR, work index, pilot plant INTRODUCTION The resistance of ore samples to breakage (or hardness) is SAG Mill Testing Test Procedures to Characterize Ore • 28 MW GMD for 42' SAG mill Whether it is size or an installation at the highest altitude (4600 masl), ABB’s GMDs are well positioned to contribute to the building of larger and ever more powerful mills — Leading the gearless mill drive evolution The ABB gearless mill drive (GMD) is the most powerful mill drive system available,Gearless mill drives ABB2023年7月25日 How Often Should Roller Mill Maintenance Be Done? Roller mill maintenance will be unique for every operator and depend on the particular materials going through the machine When asked how often roller mill maintenance should be done, Josh replied, “That’s highly dependent on the abrasiveness of the material and the cleanliness of theMaterial Use Roller Mill Maintenance: What You Need to Know
.jpg)
Gold Ore Processing Small Hammer Mill
The main working part of the hammer mill is the rotor with the hammers The rotor consists of the main shaft, disc, pins and hammers The motor drives the rotor to rotate at high speed in the crushing chamber 50 mm ore enter the crushing chamber from the top inlet with water togetherThe real gold loss must be traceable if lost during mining operations, but if it cannot be located underground it can only be ascribed as apparent gold loss It is of vital importance that movement of ore from the source to the mill is understood to reduce ore Monitoring ore loss and dilution for minetomill integration in 2015年12月10日 Sampling is the most important procedure in arriving at the value of an ore Improper sampling makes other procedures, including assaying, valueless, as the sample must truly represent the ore from which it is taken Before sampling, clean fresh faces must be exposed in order to prevent the possibility of saltingSampling for Assaying 911Metallurgist2014年6月1日 Further, the long(er) lead times for mega projects need to be shortened Changes in process equipment are significant (ie bigger and fewer in the future) This includes the use of ever increasing float super cells (>600 m 3 and beyond), hybrid energy flotation, large SAGs, >3 m HPGRs, the better correlation of mineralogy with froth vision control, or better design of Ore characterization, process mineralogy and lab automation a

Design and Analysis of Rotor Assembly of Hammer Mill Machine
International Journal of Engineering and Management Research eISSN: 22500758 pISSN: 23946962 Volume11, Issue2 (April 2021)2019年12月23日 The rotor speed is obtained as 12891 rpm The major factors considered for the material selection are the mechanical properties, wear of materials, environmental properties, fabrication DEVELOPMENT OF A HORIZONTAL SHAFT HAMMER MILL CHAPTER