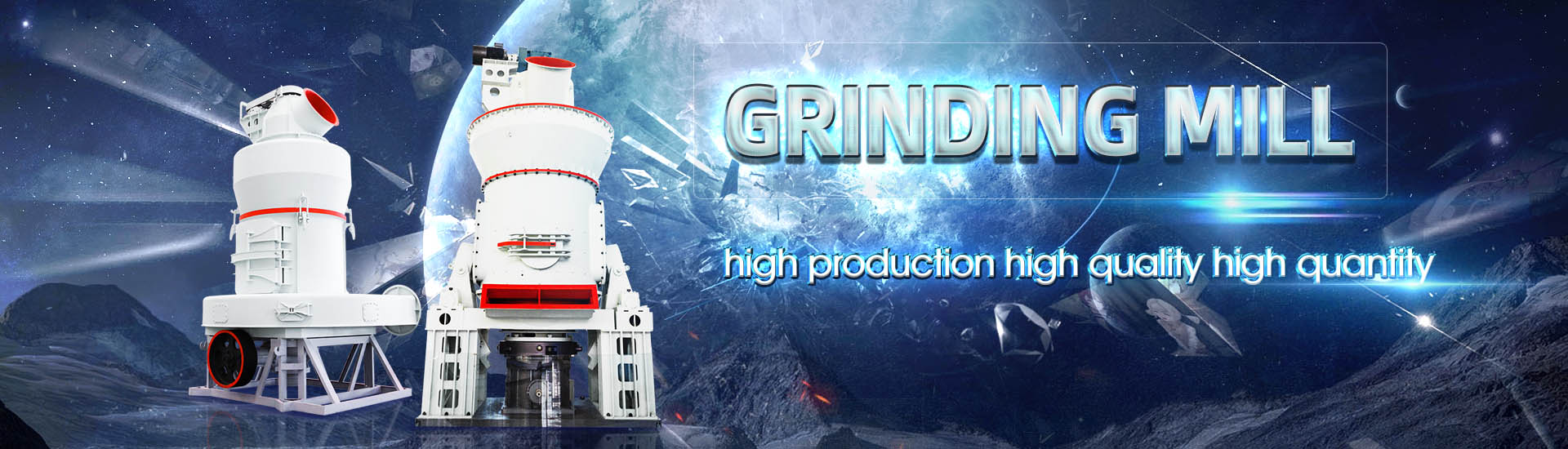
250T cement dry process line kiln opening process
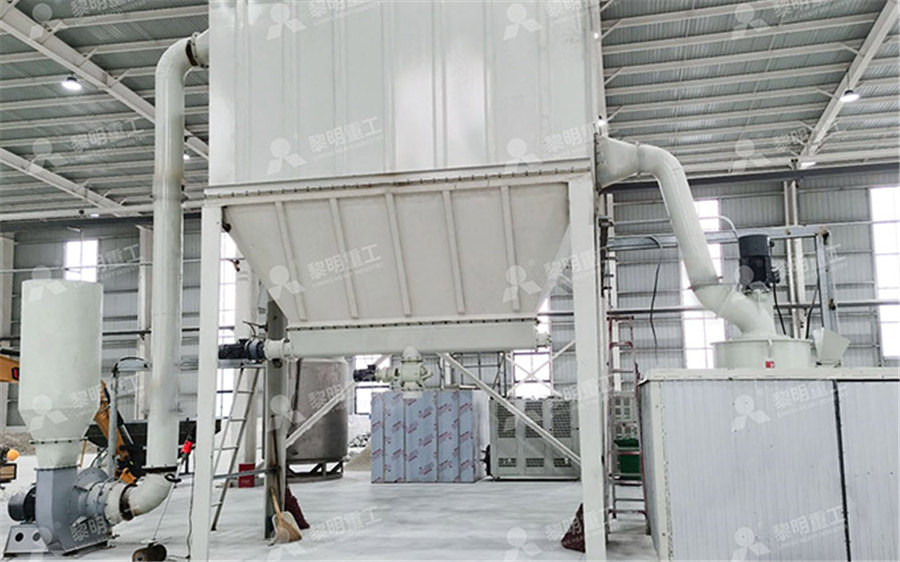
SOPKiln Start Up and Operation PDF Industrial
The document provides the standard operating procedure for starting up and operating a kiln at Anjani Portland Cement Limited It outlines 31 steps for kiln Three main stages in the cement production process exist: x Raw limestone processing, raw material mixing and milling; x Clinker production (as intermediary byproduct) from raw Advanced Control Schemes for Cement Fabrication Processes1 The document discusses different types of kiln systems used for burning cement clinker, including dry, semidry, semiwet, and wet processes 2 Key factors in selecting a kiln system Dinesh Agrawal: DryProcess PDF Cement Filtration ScribdClinker is ground to produce cement The three broad processes of cement manufacturing are: Raw milling — the preparation of the kiln feed Calcining and burning or clinkering — the The Cement Production Process
.jpg)
A comprehensive review on Advanced Process Control of cement
2023年1月1日 The cement kiln is one of the major energyintense processes that need efficient controllers to minimise fuel consumption, enhance clinker production, and improve cement The basic process in a cement production plant is burning a mixture of raw material containing Carbonates and Silicates in a kiln to produce solid oxides, clinker, which is then cooled and AI Kiln Solution For Optimized Control How To Reduce EnergyThe dry process cement production line is widely used in cement industry it is generally divided into the following processes: prehomogenization of raw materials, homogenization of raw Dry Process Of Cement Production 3005000TPD AGICO CEMENTduce cement in dry route is approximately half of the energy required to produce it through the wet process The most common way to manufacture Portland cement is through a dry process Chapter 4 Cement Manufacturing and Process Control
.jpg)
Cement Manufacturing and Process Control SpringerLink
2019年8月27日 The early manufacturing process of cement was through wet process , in which slurry, made of ground raw material and water, used to feed the rotary kiln But this process We provide a detailed configuration table of the Dry Process Cement Production Line and a description of the return on investmentDry Process Cement Production Line LCDRI CNDescription: The 2500t / d cement clinker production line adopts a new dry process, with an annual output of 775,000 tons of cement clinker and a total cement output of 105 million tons / yearA cement production line and auxiliary facilities from limestone crushing to cement packaging are constructed Specialties include raw materials, production technology, electrical and 2500TPD new type dry process cement clinker production lineAbstract The preheater system is an imperative part of the dry cement production line Besides its significant it represents the transition step from the wet to dry process for cement productionInfluence of bypass of kiln gases and calcinations degree in the
.jpg)
Kiln Cooler for Cement Rotary Kiln of Dry Process
In recent years, with the improvement of largescale cloth bag dust collecting technology in China, the long bag dust collector technology used in rotary kiln tail gas treatment of cement rotary kiln with dry process method is increasing day Other articles where dry process is discussed: cement: Manufacture of cement: are known as the wet, dry, and semidry processes and are so termed when the raw materials are ground wet and fed to the kiln as a slurry, ground dry and fed as a dry powder, or ground dry and then moistened to form nodules that are fed to theDry process cement Britannica2019年8月27日 The major raw materials used as a source of CaO for cement manufacturing are limestone, chalk, marl, etc These raw materials by virtue of their natural occurrence contains other mineral impurities eg, MgO, SiO 2, Al 2 O 3, Fe 2 O 3, alkali compounds, and sulfidesThese impurities play an important role to influence the cement manufacturing Cement Manufacturing and Process Control SpringerLink2014年6月10日 Evolution of the cement Process • Wet process easiest to control chemistry better for moist raw materials • Wet process high fuel requirements fuel needed to evaporate 30+% slurry water • Dry process kilns less fuel requirements • Preheater/Precalciner further enhance fuel efficiency allow for high production ratesCement manufacturing process PPT SlideShare
.jpg)
2500TPD new type dry process cement clinker production line
The 2500t / d cement clinker production line adopts a new dry process, with an annual output of 775,000 tons of cement clinker and a total cement output of 105 million tons / year Tel:+86513 Email: the case of dry process rawmilling, early plants preceded the raw mill with separate driers With the arrival of the new dry process in the 1950s, it was desirable to combine the drying and grinding processes It was also necessary run the mill in closed circuit, using a separatorCement Kilns: Size Reduction and Grinding2020年8月25日 Before you send inquiry Please provide us with project information as much as possible: For a complete project: the material availability, the required output capacity, the process technology, your budgetary and financing status, the estimated starting time, etc For singular machinery: the model, the capacity, your budgetary information, other requirements, etcCement Production Process Cement Manufacturing Process AGICO CEMENTDry Process Kiln Free download as PDF File (pdf), Text File (txt) or read online for free Dry process kiln systems Highly reliable Low emission levels Efficient energy utilizationDry Process Kiln PDF Heat Transfer Nature
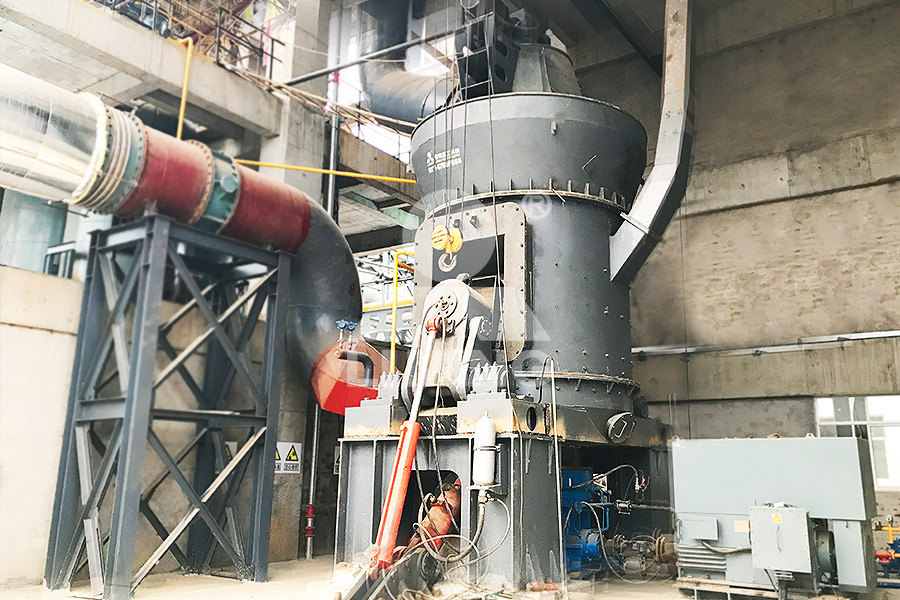
Dry Process Of Cement Manufacturing\Dry Process
Dry process cement kiln is a kind of rotary kiln which is mainly used in calcining cement clinker which made well use of waste heat in kiln tail Especially, when the beginning years of the 1970s, a new kiln production line with kiln Cement Dry Process Free download as Word Doc (doc / docx), PDF File (pdf), Text File (txt) or read online for free In the dry process, raw materials are crushed dry and fed into a grinding mill to produce a fine powder known as Cement Dry Process Download Free PDF ScribdDownload scientific diagram Rotary kiln firing process for new dry process cement technology from publication: Novel fCaO soft sensor for cement clinker based on integrated model of dual Rotary kiln firing process for new dry process cement technology Mixing and Blending for the manufacturing of cement Dry Process In the dry process of cement manufacturing, workers first mine and crush raw materials such as limestone, clay, and sand, then transport them to a grinding mill where they dry and reduce them to a fine powder They then store this dry powder, known as raw meal, in silosStepbyStep Guide to the Manufacturing of Cement PRACTICAL
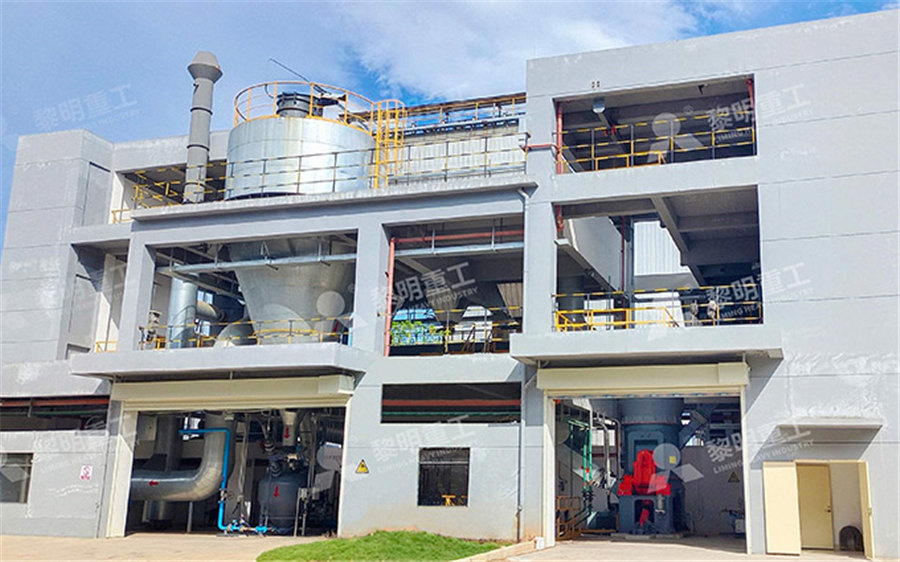
AI Kiln Solution For Optimized Control How To Reduce Energy
The basic process in a cement production plant is burning a mixture of raw material containing Carbonates and Silicates in a kiln to produce solid oxides, clinker, which is then cooled and milled to make the cement dust Fig 1 shows the structure of a rotary kiln with the most important variables used for control purposes in a simplified way [3]2021年11月1日 Energetic assessment of a precalcining rotary kiln in a cement plant using process simulator and neural networks November 2021 Alexandria Engineering Journal 61(1718)Energetic assessment of a precalcining rotary kiln in a cement In the rotary kiln process (Figure 2), raw material mixture is fed into the upper end of large cylindrical, refractorylined steel kiln that range from 60 to 300 meters long 7 and from over 30 to rotary Cement kiln (dry process with cyclonic preheaters)2015年10月1日 EM: After the restoration of Lithuania's independence, the adjustment to the market system meant that we didn't need to make as much cement The plant used just one line from the first plant and two from the second plant in the 1990s This was an inefficient setup and so in 2007 we decided to install a new dry process cement lineAkmenes Cementas: A new dry line for an independent cement producer
.jpg)
Dry Process Of Cement Manufacturing Dry Cement AGICO
The new dryprocess cement production line technology was developed in the 1950s, so far, the new dry process cement equipment rate of Japan, Cement kiln: the dry method cement kiln manufactured by AGICO has the characteristic of stable Ø Process control which involves raw materials moisture, raw meal chemistry and fineness, clinker free lime, degre e of calcination and volatiles contents of hot meal at the kiln inlet, proportioning of clinker and gypsum, and fineness of milled cementCement Plant OPERATIONS HANDBOOK For Dry Process Plants2015年3月2日 While the technology and requirements for valves needed for producing cement have not changed drastically in the last 20 years or so, efforts to make the process more environmentally friendly continue In many Valves in a Cement Slurry Line Valve Magazine2023年12月26日 As we all know, the dryprocess cement production line is commonly used in the cement industry The new type of dryprocess cement production process includes four main sections: Prehomogenization of raw 6 Cement Equipment For Dryprocess Cement
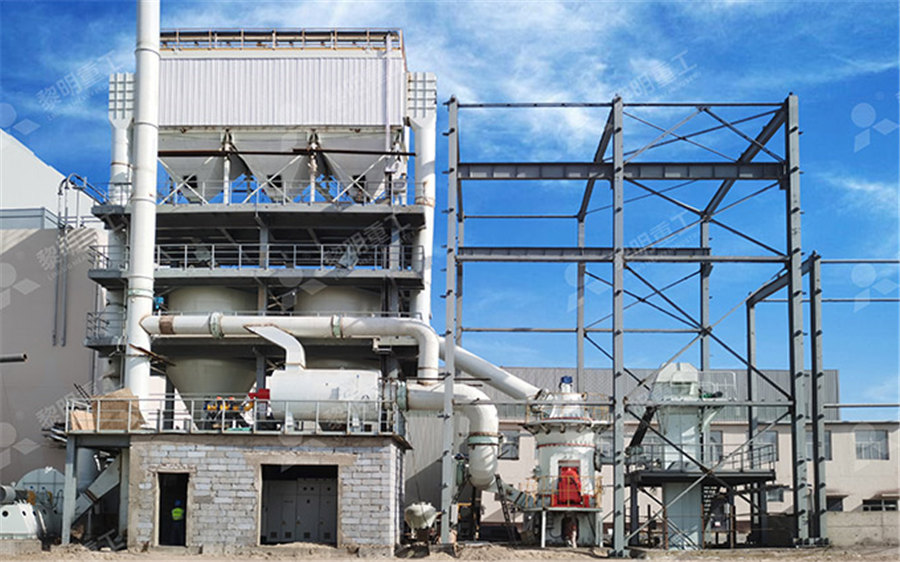
New dry process cement production line process
2019年8月26日 The new dryprocess cement production line technology was developed in the 1950s So far, in Japan, Germany and other developed countries, the production rate of new dryprocess cement clinker with Kiln Process Heat Consumption (kcal per kg clinker) Wet process with internals 14001500 Long dry process with internals 1100 1stage cyclone preheater 1000 2stage cyclone preheater 900 4stage cyclone preheater 800 4stage cyclone preheater plus calciner 750 5 stage preheater plus calciner plus high efficiency cooler 720The Cement Production Process2023年1月1日 Journal of Advanced Industrial Technology and Application ConditionBased Monitoring of Kiln Induced Draft Fan in A Dry Process Cement Plant for Efficient Utilization January 2023 DOI: 1030880 (PDF) Journal of Advanced Industrial Technology and Application In spite of the energetic advantage of the dry process in relation to wet process kilns a conversion to dry process is not always convenient for existing plants For some plants it does not make sense to change to a dry process because the raw materials are quarried out with more than 30 wt% moisture content In regions with relatively low Wet process rotary cement kilns: modeling and simulation
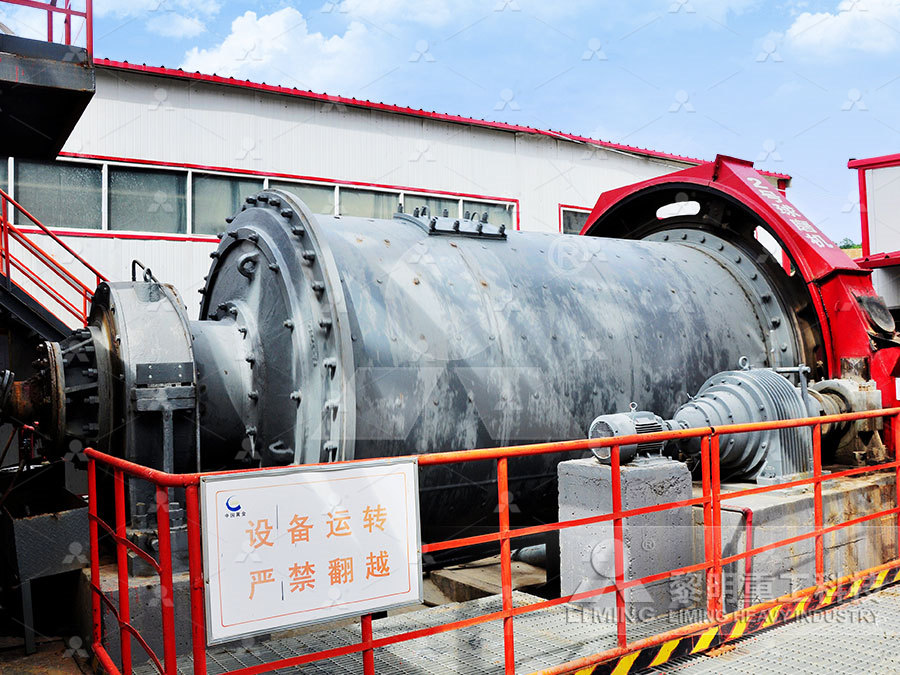
Cement manufacturing process PPT SlideShare
2016年1月29日 9 Wet process In the wet process, raw materials are crushed to a diameter of approximately 20 mm by a crusher and mixed in an appropriate ratio using an automatic weigher, Then, with water added thereto, the mixture is further made finer by a combined tube mill with adiameter of 2 to 35 m and a length of 10 to 14 m into slurry with a water content of 35 to 40%1975年1月1日 Cement manufacturing The St Lawrence Cement Co dry process plant Portland cement is produced by igniting a mixture of finely ground limestone, silica, alumina, and iron oxide (raw feed) The kiln discharge (clinker) is a chemically complex mixture of calcium silicates, aluminates and ferrites which, when ground and blended with 25% of calcium Experimental burning of used automotive crankcase oil in a dryprocess 2016年11月21日 While the technology and requirements for valves needed for producing cement have not changed drastically in the last 20 years or so, efforts to make the process more environmentally friendly continue In many modernized wet process plants, a slurry drier can be added to dry the slurry before entering the kiln, using waste heat from the kilnValves in a Cement Slurry Line Valve Magazine2006年3月17日 At the present time some 80% of the global cement clinker production is obtained from dry kiln processes However, there are still a several hundred wet process kilns in use (Eckert and Hand 2002; De Beus 1999)Modern dry process plants are a combination of a fourtofivestage cyclone preheater and a precalcination followed by a short rotary kilnWet process rotary cement kilns: modeling and simulation
.jpg)
2500TPD new type dry process cement clinker production line
Description: The 2500t / d cement clinker production line adopts a new dry process, with an annual output of 775,000 tons of cement clinker and a total cement output of 105 million tons / yearA cement production line and auxiliary facilities from limestone crushing to cement packaging are constructed Specialties include raw materials, production technology, electrical and Abstract The preheater system is an imperative part of the dry cement production line Besides its significant it represents the transition step from the wet to dry process for cement productionInfluence of bypass of kiln gases and calcinations degree in the In recent years, with the improvement of largescale cloth bag dust collecting technology in China, the long bag dust collector technology used in rotary kiln tail gas treatment of cement rotary kiln with dry process method is increasing day Kiln Cooler for Cement Rotary Kiln of Dry Process Other articles where dry process is discussed: cement: Manufacture of cement: are known as the wet, dry, and semidry processes and are so termed when the raw materials are ground wet and fed to the kiln as a slurry, ground dry and fed as a dry powder, or ground dry and then moistened to form nodules that are fed to theDry process cement Britannica

Cement Manufacturing and Process Control SpringerLink
2019年8月27日 The major raw materials used as a source of CaO for cement manufacturing are limestone, chalk, marl, etc These raw materials by virtue of their natural occurrence contains other mineral impurities eg, MgO, SiO 2, Al 2 O 3, Fe 2 O 3, alkali compounds, and sulfidesThese impurities play an important role to influence the cement manufacturing 2014年6月10日 Evolution of the cement Process • Wet process easiest to control chemistry better for moist raw materials • Wet process high fuel requirements fuel needed to evaporate 30+% slurry water • Dry process kilns less fuel requirements • Preheater/Precalciner further enhance fuel efficiency allow for high production ratesCement manufacturing process PPT SlideShareThe 2500t / d cement clinker production line adopts a new dry process, with an annual output of 775,000 tons of cement clinker and a total cement output of 105 million tons / year Tel:+86513 Email: 2500TPD new type dry process cement clinker production lineIn the case of dry process rawmilling, early plants preceded the raw mill with separate driers With the arrival of the new dry process in the 1950s, it was desirable to combine the drying and grinding processes It was also necessary run the mill in closed circuit, using a separatorCement Kilns: Size Reduction and Grinding
.jpg)
Cement Production Process Cement Manufacturing Process AGICO CEMENT
2020年8月25日 Before you send inquiry Please provide us with project information as much as possible: For a complete project: the material availability, the required output capacity, the process technology, your budgetary and financing status, the estimated starting time, etc For singular machinery: the model, the capacity, your budgetary information, other requirements, etcDry Process Kiln Free download as PDF File (pdf), Text File (txt) or read online for free Dry process kiln systems Highly reliable Low emission levels Efficient energy utilizationDry Process Kiln PDF Heat Transfer Nature