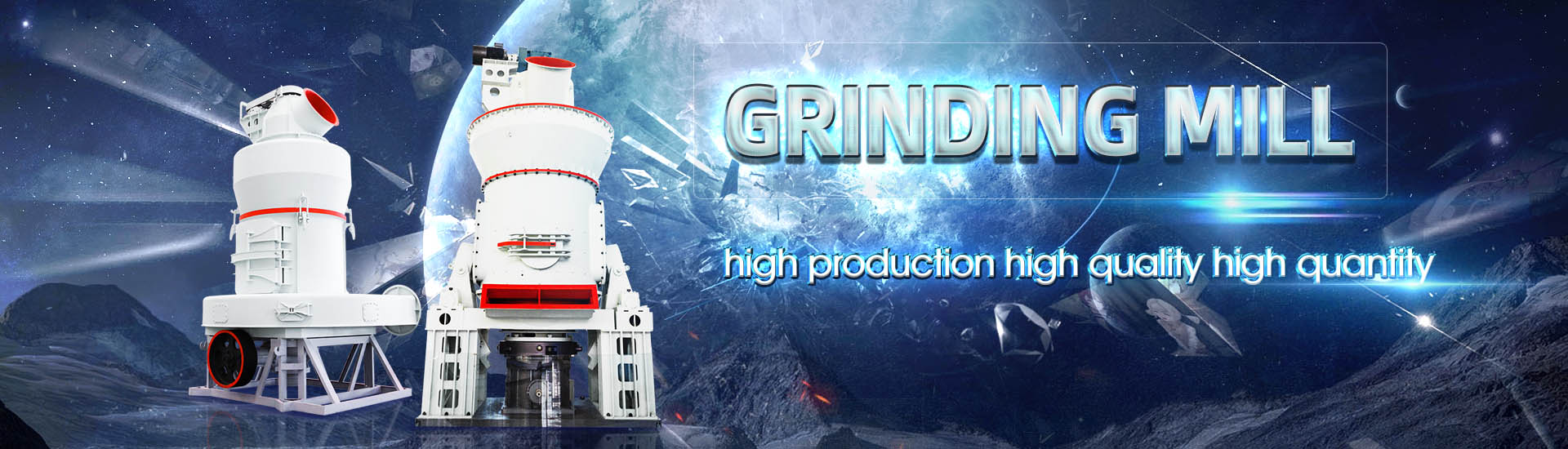
Design and construction of calcium powder plant
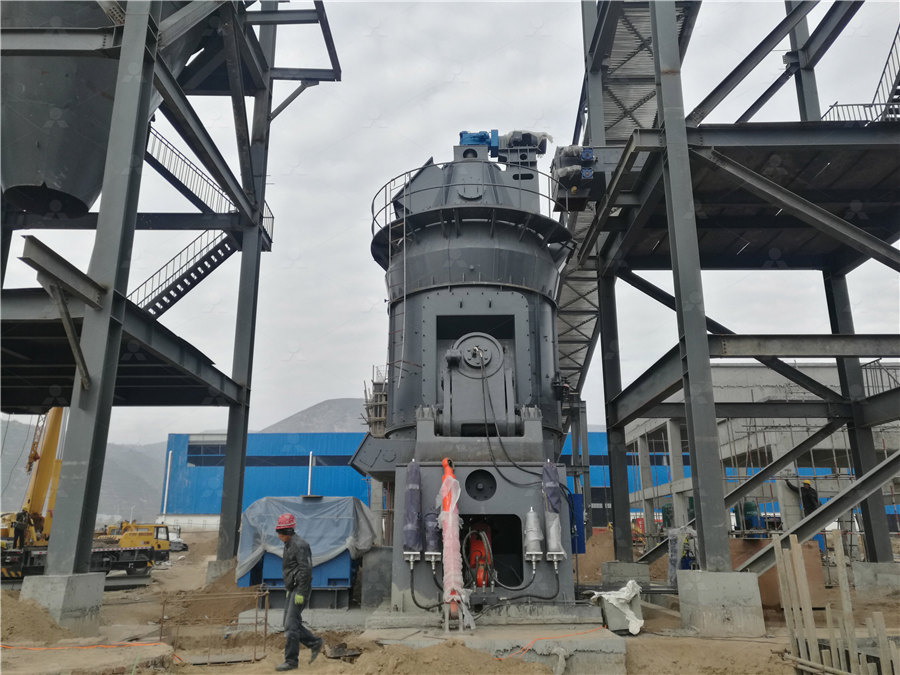
Calcium Powder Manufacturing Plant Project Report IMARC Group
IMARC Group’s report, titled “Calcium Powder Manufacturing Plant Project Report 2024: Industry Trends, Plant Setup, Machinery, Raw Materials, Investment Opportunities, Cost and Revenue” provides a complete roadmap for setting up a calcium powder manufacturing plantSIC, after years of developing technologies related to the production of lime and its byproducts with the technological support of two worldwide specialists of PCC, started to deal with the design and construction of plants for the PCC plants SIC Lime Società Impianti Calce SrlThe purpose of this study is to conceptually design a pilot plant for calcium chloride production by utilizing waste cockle shell as raw material Feasibility study willConceptual Production Plant of Calcium Chloride from Waste The report provides a complete roadmap for setting up an calcium powder manufacturing plantDetailed Project Report on Setting up a Calcium Powder
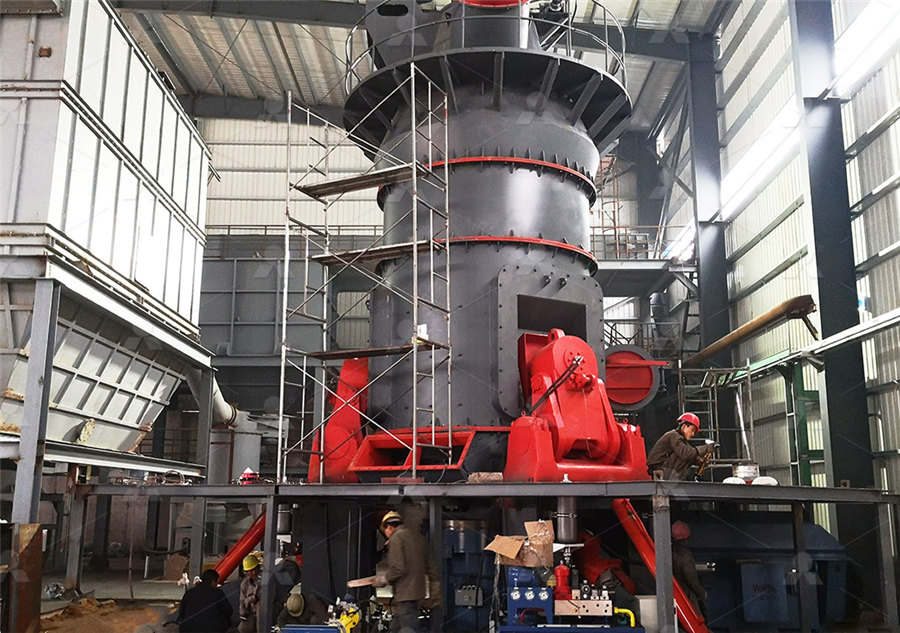
Calcium Carbonate Plant NUBERG EPC
The plant of Calcium Carbonate is built in the following steps: The first step is to Calcination / Burning of limestone in a vertical shaft lime kiln for quick lime and carbon dioxide gas This report deals with plant design of calcium chloride chemical powder known as calcium chloride dihydrate from limestone and acid chloride solution The synthesis process uses acid reaction by acidification which has pure 94% PLANT DESIGN REPORT OF CALCIUM CHLORIDE 2014年1月1日 Calcium looping (CaL) CO 2 capture process using calcium oxide as a regenerable solid sorbent has been under development at the Industrial Technology Research Design and Experimental Testing of a 19MWth Calcium Looping capture technologies, calcium looping appears promising due to its high thermal efficiency, technical feasibility at commercialscale, and low sorbent cost Calcium looping has now been Development of a Continuous Calcium Looping Process for CO2
.jpg)
Operation of a 25 KWth Calcium Looping Pilotplant with High
2017年10月25日 Calcium looping (CaL) is a postcombustion CO 2 capture technology that is suitable for retrofitting existing power plants The CaL process uses limestone as a cheap and 2022年8月1日 To guarantee a more balanced reaction pressure in the thermochemical heat storage, a multilayered reactor with multiple reacting zones was designed based on calcium Design and performance evaluation of multilayered reactor for 2019年7月25日 Among possible thermochemical systems, the CalciumLooping process, based on the multicycle calcinationcarbonation of CaCO 3, is a main candidate to be integrated as energy storage system within a scenario of massive deployment of Offdesign model of concentrating solar power plant with 2013年9月1日 [187] The benchscale experimental results were employed for design and construction of a 19 MWth pilot plant to capture CO2 from the flue gas of a cement manufacturing plant [188]Design and Experimental Investigation of Calcium Looping
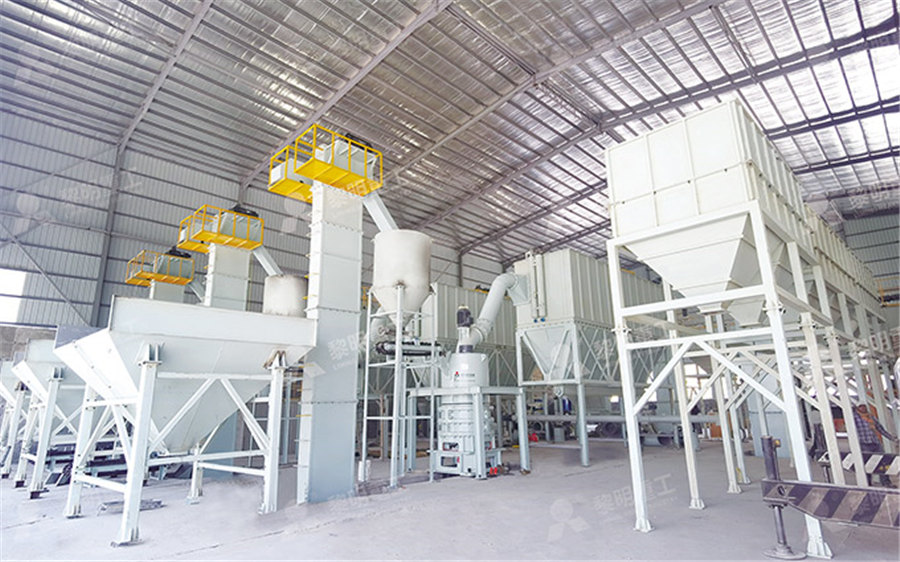
Design and Experimental Testing of a 19MWth
2014年12月31日 We describe here the design of a 1 MW th pilot plant to capture 70–95% of the CO2 contained in the flue gas from a 1/150 side stream emitted by an existing 50 MWe CFB power plantThe reduction in the construction of new generating plants in the late 1990s coupled with market liberalisation have led to the merger of some power construction companies and the collapse of others It is, hence, desirable to know which companies are presently involved in the construction of coalfired power plant and in what regions of the world they operateCurrent design and construction of coalfired power plant, The report examines onetime costs associated with the construction of a plant and the continuing costs associated with the daily operation of such a plant The analysis assumes a United Statesbased plant with a capacity of 25 kt of Calcium Hypochlorite per year and includes: * Capital Investment, broken down by:Calcium Hypochlorite from Slaked Lime and Cl2 (Sodium Method) 2013年2月19日 Calciumbased looping cycle offers reduced carbon capture energy penalty Chemical looping cycles ensures almost total decarbonisation rate of the fuel used Increasing energy efficiency and plant flexibility by H 2 and power cogeneration Energy integration techniques to optimise the overall plant energy efficiencyAssessment of calciumbased chemical looping options for
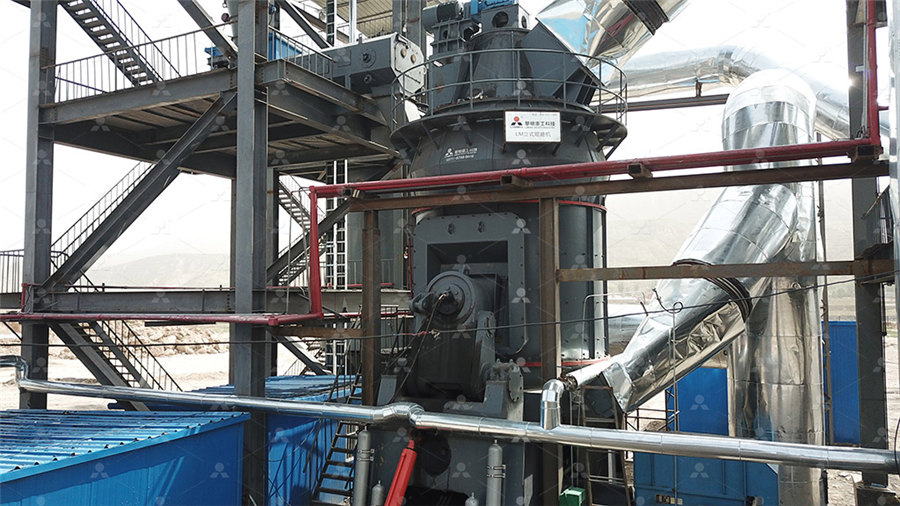
Design and construction application of concrete canvas for
2019年2月15日 The use of AFRP and 3D spacer fabric will inevitably lead to an increase in material costs; but significantly reduce both construction cost and curing cost, for instance, safe and easy to install due to the flexibility of CC, quick construction with very low labor cost, unnecessary extra moisture curing, unnecessary framework support, good adaptability to 2021年3月15日 Despite extensive indepth research into high calcium fly ash geopolymer concretes and a number of proposed methods to calculate the mix proportions, no universally applicable method to determine the mix proportions has been developed This paper uses an artificial neural network (ANN) machine learning toolbox in a MATLAB programming Novel Analytical Method for Mix Design and Performance Download scientific diagram CalciumLooping process principle from publication: Design and Experimental Testing of a 19MWth Calcium Looping Pilot Plant Calcium looping (CaL) CO2 capture CalciumLooping process principle Download Scientific DiagramReport Overview: IMARC Group’s report, titled “Calcium Hypochlorite Powder Manufacturing Plant Project Report 2024: Industry Trends, Plant Setup, Machinery, Raw Materials, Investment Opportunities, Cost and Revenue” provides a complete roadmap for setting up a calcium hypochlorite powder manufacturing plant It covers a comprehensive market overview to micro Calcium Hypochlorite Powder Manufacturing Plant Project Report
.jpg)
(PDF) Calcium Looping technology demonstration in
2020年10月22日 In this work, a Calcium Looping (CaL) configuration for cement plants using two interconnected circulating fluidized bed (CFB) reactors integrated into the clinker production process, is investigated2024年12月1日 SCC is among the many solutions for sustainable and highperformance construction materials It was invented in Japan in 1988 owing to many attributes such as workability, mechanical properties, and durability [1], [2], [3], [4]SCC is workable at the site without any form of mechanical compaction or vibration; hence, it flows under its own weight to Synergizing Portland Cement, highvolume fly ash and calcined calcium of calcium rich solution Construction of pilot plant also required research and design work on process equipment for small scale production quantities Now projects has moved to demo scale test phase In this thesis research will concentrate on upscaling the Slag2PCC pilot plant and streamlining the process work flow 12 Research taskConcept design for demonstration plant for production of 2011年3月1日 The applications of calcium looping cycle for fossil fuel power plants include the precombustion CO 2 capture and postcombustion CO 2 capture The precombustion CO 2 capture involves the zeroemission coal technology (ZEC) and HyPrRING process [5], [6], [7]The aim of these gasification processes is to produce hydrogenCO2 capture efficiency and energy requirement analysis of power plant
.jpg)
Operation of a 25 KWth Calcium Looping Pilotplant with High
2017年10月25日 Bidwe AR, Hawthorne C, Dieter H, Dominguez MA, Zieba M, Scheffknecht G Cold model hydrodynamic studies of a 200kWth dual fluidized bed pilot plant of calcium looping process for CO2 Capture Powder Technology 2014; 253:116–128 [Google Scholar] Chang MH, et al Design and experimental testing of a 19 MWth calcium looping pilot plantDairy Plant Design and Layout 7 Lesson 2 Importance of Dairy Plant Design 21 Introduction: Dairy Plant design, involves the estimation of capacity, process scheduling and proper layout so as to achieve the objective of handling milk at the least cost and greatest safetyDAIRY PLANT DESIGN AND LAYOUT AgriMoonCalcium Looping technology demonstration in industrial environment: the CLEANKER project and status of the CLEANKER pilot plant Martina Fantini1*, Maurizio Spinelli1, Francesco Magli2, and Stefano Calcium Looping technology demonstration in industrial 2017年7月1日 “In the first fluidized bed reactor, the absorber, a powder of burnt lime or calcium oxide (CaO), is contacted with the CO 2 in the power station exhaust to form calcium carbonate (CaCO 3)Researchers: Power Plant CarbonCapturing Calcium Carbonate
.jpg)
Integration of a coal fired power plant with calcium looping CO2
2022年2月1日 The CaL process was first proposed by Shimizu et al [8] for CO 2 capture that consists of two main reactors, a carbonator and a calcinerThe CO 2rich flue gas flows into the carbonator where CO 2 reacts with the CaO to form calcium carbonate (CaCO 3) at temperatures around 650 °CThe carbonation reaction releases great amount of highgrade heat that can be 2019年7月26日 Offdesign model of concentrating solar power plant with thermochemical energy storage based on calciumlooping(PDF) Offdesign model of concentrating solar power plant with Request PDF On Nov 1, 2024, Zheng Fang and others published Electrochemical recycling of recycled concrete powder: Selective recovery of calcium and silica to enable sustainable construction Electrochemical recycling of recycled concrete powder: Selective 2015年6月8日 This review indicates that the calcium looping integration resulted in the projected efficiency penalty of 26–79% points for the coalfired power plants and 91–114% points for the combined A review of developments in pilot plant testing and
.jpg)
Design and evaluation of alkaliactivated slagcalcined coal
2024年9月13日 This paper adjusts the proportion of slag (SG) and calcined coal gangue powder (CCGP), regulates the content of Na 2 O24SiO 2NaOHNa 2 CO 3 ternary activator components, and uses calcium carbonate whiskers (CW) instead of SG to prepare AAC with slow coagulation and shrinkage reduction2021年8月30日 These analyses reveal that the NGCC power plant integrated with double calcium looping unit captures 9132% of CO 2 with an energy penalty of 673% The proposed CO 2 capture and utilization integrated configurations have low electrical power output; however, the conversion of CO 2 to high energy density dimethyl ether (DME) product resulted in overall A novel calcium looping–integrated NGCC power plant 2018年4月15日 This research focuses on developing a mix design methodology for alkaliactivated high calcium fly ash concrete (AAHFAC) High calcium fly ash (FA) from Mae Moh power plant in northern Thailand A Mix Design Procedure for AlkaliActivated High Calcium Fly 2024年5月15日 Here, we evaluate a flexible natural gas power plant concept with the potential for negative emissions that integrates calcium looping, membrane and cryogenic CO 2 separation, and DAC Process optimization is performed to determine the design and scheduling of the process for different scenarios of carbon prices, fuel prices and electricity pricesOptimization of a combined power plant CO2 capture and direct
.jpg)
Caustic Soda, Chlorine, Chlor Alkali Plants EPC LSTK Supplier
Typical by products of chlor alkali and derivatives plant include caustic soda lye, caustic soda flakes, chlorine, calcium chloride, sodium hypochlorite, hydrogen peroxide, hydrochloric acid, stable bleaching powder and chlorinated paraffin wax (CPW) What we do in Chlor Alkali2014年7月3日 Usually the plant cash flow is presented as a cumulative flow over the life of the project As project life, 29 years was considered in this paper, 3 years for plant construction, 25 years operation and one final year for recovering the plant working capital The working capital is recovered at the end of the project life (29th year)Economic implications of pre and postcombustion calcium Chemical Plant Design and Construction Free download as PDF File (pdf), Text File (txt) or read online for free This document discusses the process of chemical plant design and construction It covers various stages of the process from initial feasibility studies and cost estimation, to preliminary design, contracting with engineering firms, detailed design, Chemical Plant Design and Construction2018年8月1日 Solar driven large scale uninterrupted power production can be accomplished with a combination of Concentrated Solar Power (CSP) plant and a Thermochemical Energy Storage (TCES) based on a Calcium Looping (CaL) process Thermal energy can be stored in the form of chemical energy due to calcination reaction and released back as thermal energy Design of an Integrated CSPCalcium Looping for Uninterrupted
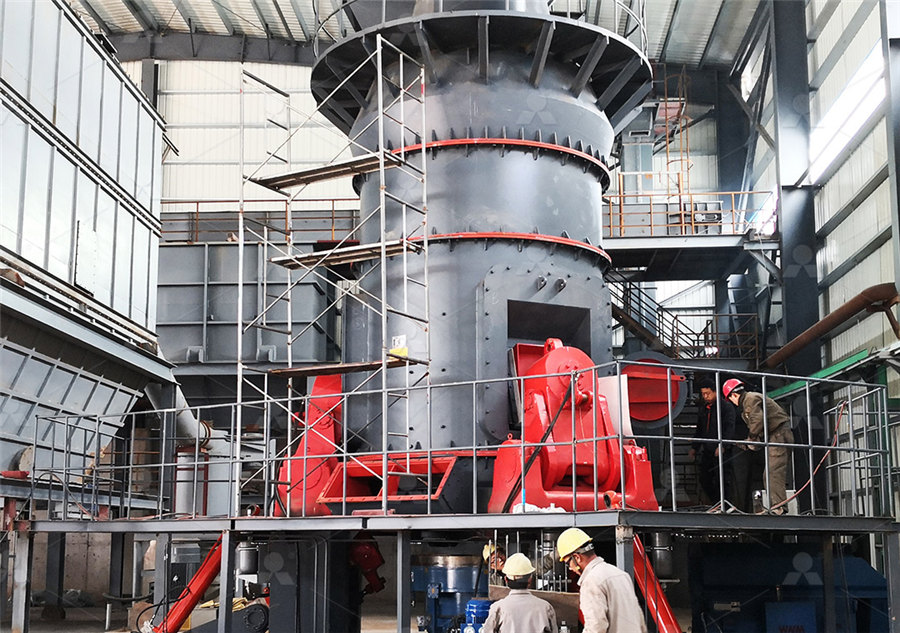
Offdesign model of concentrating solar power plant with
2019年7月25日 Among possible thermochemical systems, the CalciumLooping process, based on the multicycle calcinationcarbonation of CaCO 3, is a main candidate to be integrated as energy storage system within a scenario of massive deployment of 2013年9月1日 [187] The benchscale experimental results were employed for design and construction of a 19 MWth pilot plant to capture CO2 from the flue gas of a cement manufacturing plant [188]Design and Experimental Investigation of Calcium Looping 2014年12月31日 We describe here the design of a 1 MW th pilot plant to capture 70–95% of the CO2 contained in the flue gas from a 1/150 side stream emitted by an existing 50 MWe CFB power plantDesign and Experimental Testing of a 19MWth The reduction in the construction of new generating plants in the late 1990s coupled with market liberalisation have led to the merger of some power construction companies and the collapse of others It is, hence, desirable to know which companies are presently involved in the construction of coalfired power plant and in what regions of the world they operateCurrent design and construction of coalfired power plant,
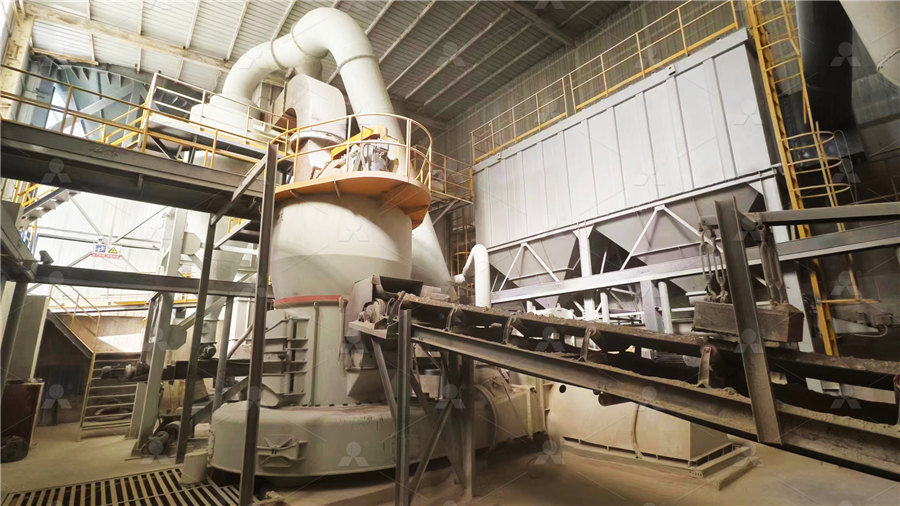
Calcium Hypochlorite from Slaked Lime and Cl2 (Sodium Method)
The report examines onetime costs associated with the construction of a plant and the continuing costs associated with the daily operation of such a plant The analysis assumes a United Statesbased plant with a capacity of 25 kt of Calcium Hypochlorite per year and includes: * Capital Investment, broken down by:2013年2月19日 Calciumbased looping cycle offers reduced carbon capture energy penalty Chemical looping cycles ensures almost total decarbonisation rate of the fuel used Increasing energy efficiency and plant flexibility by H 2 and power cogeneration Energy integration techniques to optimise the overall plant energy efficiencyAssessment of calciumbased chemical looping options for 2019年2月15日 The use of AFRP and 3D spacer fabric will inevitably lead to an increase in material costs; but significantly reduce both construction cost and curing cost, for instance, safe and easy to install due to the flexibility of CC, quick construction with very low labor cost, unnecessary extra moisture curing, unnecessary framework support, good adaptability to Design and construction application of concrete canvas for 2021年3月15日 Despite extensive indepth research into high calcium fly ash geopolymer concretes and a number of proposed methods to calculate the mix proportions, no universally applicable method to determine the mix proportions has been developed This paper uses an artificial neural network (ANN) machine learning toolbox in a MATLAB programming Novel Analytical Method for Mix Design and Performance
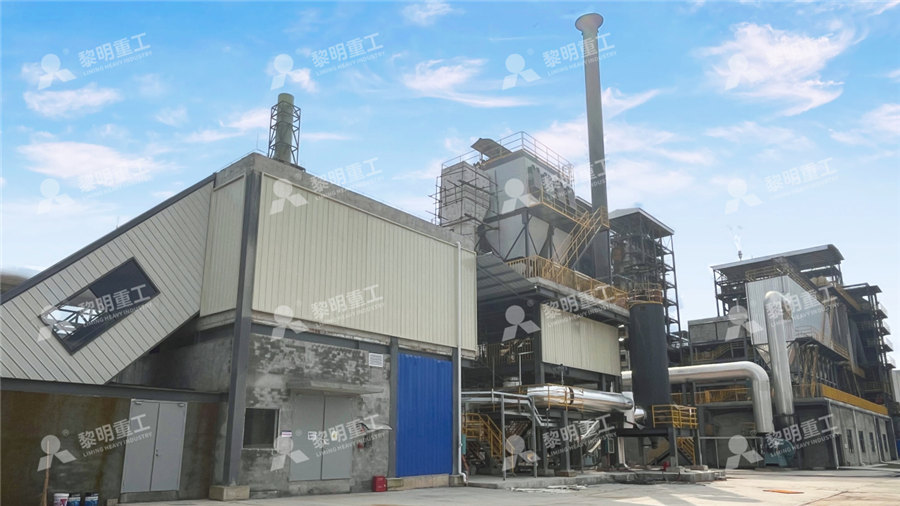
CalciumLooping process principle Download Scientific Diagram
Download scientific diagram CalciumLooping process principle from publication: Design and Experimental Testing of a 19MWth Calcium Looping Pilot Plant Calcium looping (CaL) CO2 capture Report Overview: IMARC Group’s report, titled “Calcium Hypochlorite Powder Manufacturing Plant Project Report 2024: Industry Trends, Plant Setup, Machinery, Raw Materials, Investment Opportunities, Cost and Revenue” provides a complete roadmap for setting up a calcium hypochlorite powder manufacturing plant It covers a comprehensive market overview to micro Calcium Hypochlorite Powder Manufacturing Plant Project Report