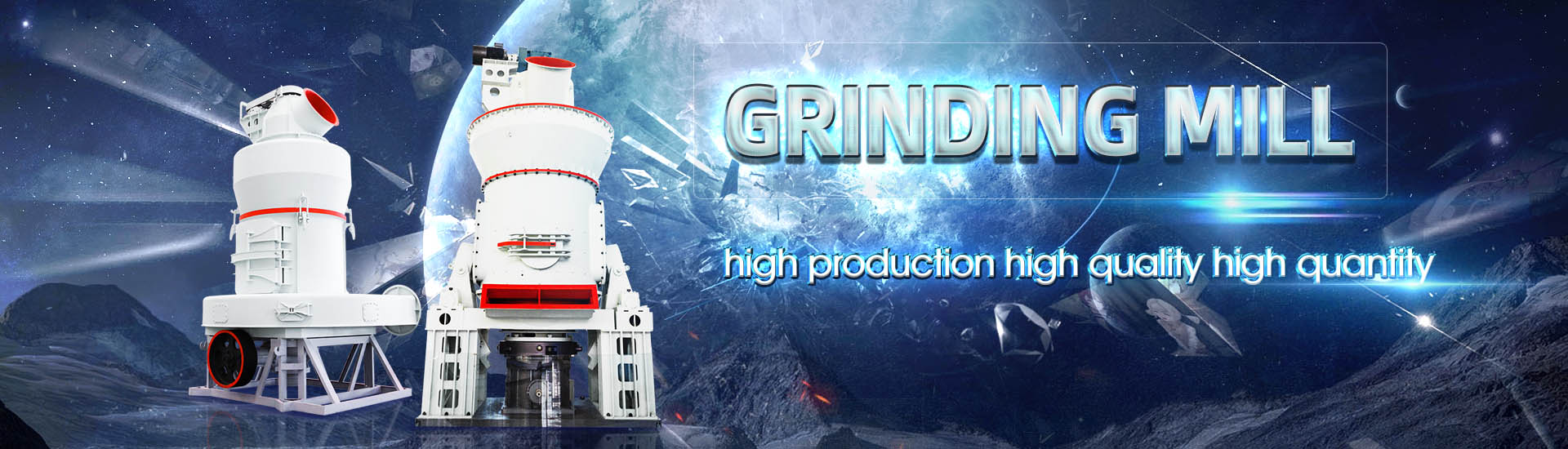
Processing aluminum ash, overhaul slag, aluminum electrolyte
.jpg)
Research Progress of Electrolytic Aluminum Overhaul Slag Disposal
2023年4月25日 This article analyzes and summarizes the composition and hazards of the overhaul slag and the current development status of domestic and international electrolytic Coal gangue is a byproduct of the production of coalassociated minerals, Review of Research on the Pr2024年2月1日 This study demonstrated the efficient leaching of Li from electrolytic aluminum slag under mild conditions, and this is a clean and feasible process for Li recovery It also Efficient lithium recovery from electrolytic aluminum slag via an 2023年8月1日 The dissolution behaviors of overhaul slag were fitted by a mass transfer model to obtain the dissolution parameters including dissolution capacity and dissolution rate This work Dissolution behavior of overhaul slag from aluminum reduction
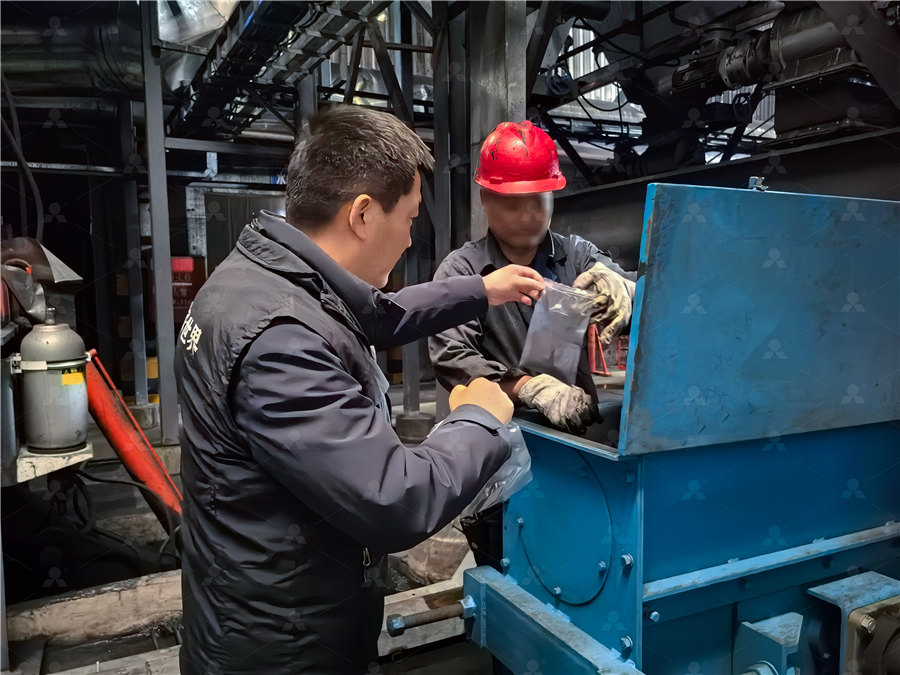
A novel approach for extracting lithium from overhaul slag by low
2024年2月1日 This process is easy to operate and highly controllable, achieving efficient separation and recovery of lithium, aluminum, and fluorine in the overhaul slag The research 2024年7月24日 The lithium was selectively recovered and enriched from spent aluminum electrolyte slag by using calcium salt roasting transformation followed by HBL121solvent extraction The new process realizes a high leaching Cleaner Process for the Selective Extraction of Lithium Aluminium ash and slag are produced from molten slag cooling in the electrolytic aluminium production process,the recycling and utilization of the electrolytic aluminium ash and slag is Recycling and Utilization of the Electrolytic Aluminium Ash and Slag2024年5月23日 Here, we review carbonrich solid wastes with focus on sources and hazards, detoxification, separation, recovery, recycling and disposal Treatment techniques include The recycling of carbonrich solid wastes from aluminum
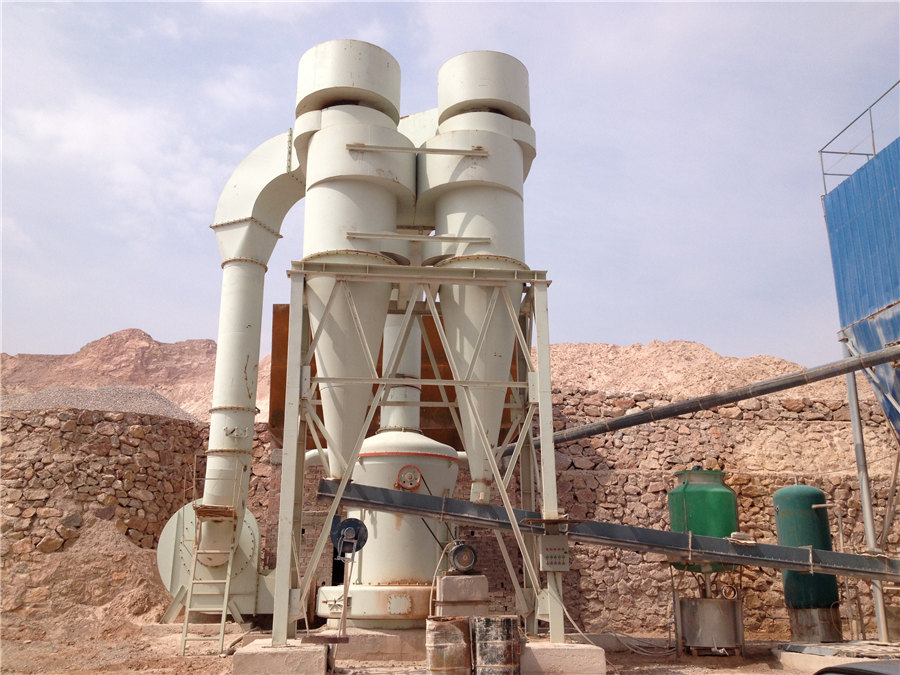
电解铝大修渣处置研究进展
2023年4月25日 This article analyzes and summarizes the composition and hazards of the overhaul slag and the current development status of domestic and international electrolytic aluminum overhaul slag disposal, and points out the 2024年1月1日 A novel approach for lithium recovery from waste lithiumcontaining aluminum electrolyte by a roastingleaching process Anode carbon residue is produced in the production Efficient lithium recovery from electrolytic aluminum slag via an This article analyzes and summarizes the composition and hazards of the overhaul slag and the current development status of domestic and international electrolytic aluminum overhaul slag disposal, and points out the development Research Progress of Electrolytic Aluminum Overhaul 2021年10月1日 A novel approach for lithium recovery from waste lithiumcontaining aluminum electrolyte by a roastingleaching the leaching toxicity was investigated The experimental results show that the best ratio of aluminum ash and calcium carbide slag is 1:9, the International Journal of Mineral Processing, Volume 160, 2017 A novel approach for lithium recovery from waste lithium
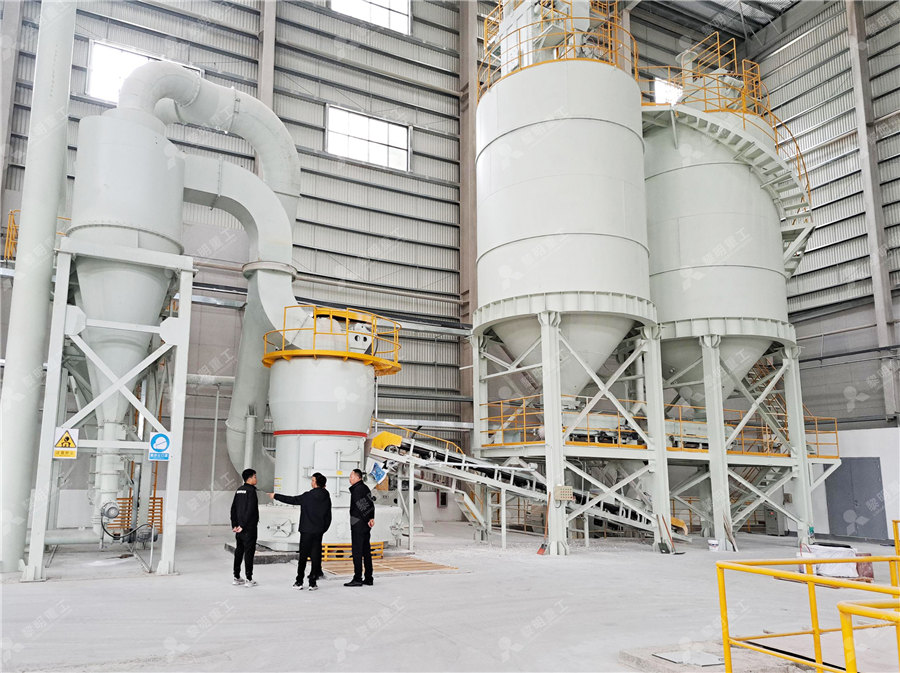
A novel approach for ultrasonic assisted organic acid leaching of
2023年10月1日 Currently, the green resource utilization in the aluminum electrolysis industry mainly focuses on the solid waste treatment of aluminum electrolysis tank overhaul slag, the resource utilization of waste cathodes, and the recovery of electrolytic tank waste heat There are few reports on lithium recovery from waste aluminum electrolytes [16,17]2023年10月1日 The main components of waste aluminum cryolite electrolyte are cryolite (Na 3 AlF 6), potassium cryolite (K 2 NaAlF 6), lithium cryolite (Na 2 LiAlF 6), fluorite (CaF 2), and approximately 2% carbon black (Wang et al, 2019)The main treatment methods of waste aluminum cryolite electrolyte can be divided into two categories: combined thermalwet Efficient extraction and recovery of lithium from waste aluminum The results showed that apart from the overhaul slag of electrolytic cell, unorganized flue gas and carbon slag were the key points of fluoride emission in electrolytic aluminum production The fluoride content of unorganized flue gas was 0374 kg/t per unit product, which was about 37 times of that of organized emissionsResearch on fluoride wholeprocess prevention and control in the 2024年7月24日 Spent aluminum electrolyte slag is a byproduct produced during the electrolysis of aluminum and contains elements such as F, Al, Na, and Li It is a toxic and harmful substance with a stable and complex structure As a consequence of fluorine pollution and low lithium recovery efficiency in the traditional hydro metallurgy process, a novel cleaner production Cleaner Process for the Selective Extraction of Lithium from Spent
.jpg)
The recycling of carbonrich solid wastes from aluminum
2024年5月23日 16 Million metric tons of spent carbon electrodes modify carbonrich solid wastes from aluminum electrolysis are produced annually, threatening ecosystems by cyanide and fluoride pollution Here, we review carbonrich solid wastes with focus on sources and hazards, detoxification, separation, recovery, recycling and disposal Treatment techniques CNA CN96A CN9A CNA CN A CN A CN A CN 9 A CN9 A CN 9A CN A CN A CN A Authority CN China Prior art keywords waste waste material silicon carbide treatment method recovery Prior art date Legal CNA Recovery treatment method of electrolytic aluminum ash During a longterm operation of the aluminum electrolysis cell, the molten salts continuously infiltrate and corrode the pot lining, resulting in a huge amount of hazardous waste after the overhaulElectrolytic cell spent lining Fig 2 Overhaul slags of the 2023年2月1日 Request PDF Industrial experimental research on coprocessing of spent refractory materials in aluminum electrolytic cell To realize the harmlessness, reduction and resource utilization of Industrial experimental research on coprocessing of spent
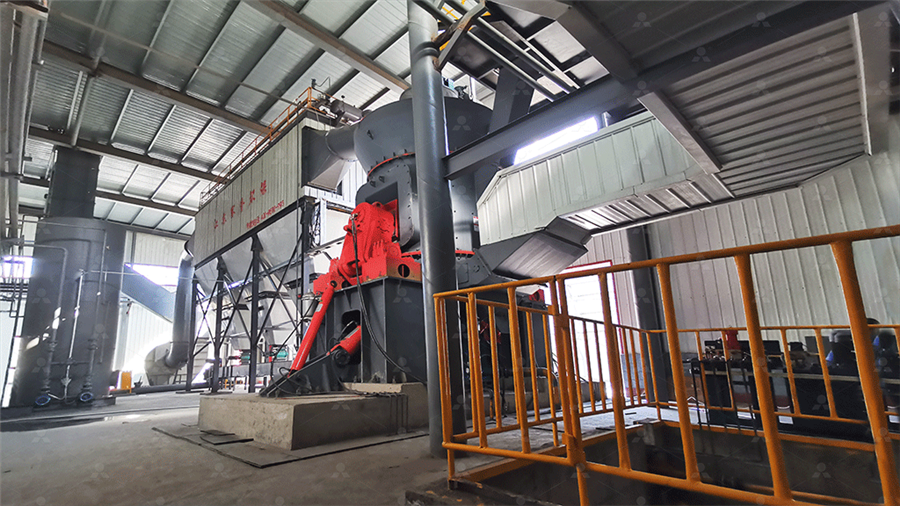
Aluminum Ash Processing Aluminum Ash Recovery Aluminum Ash
ALUMINUM ASH PROCESSING SYSTEM Processing capacity: 10,000200,000 t/a Processing materials: aluminum ash, aluminum slag, aluminum shavings and other hazardous waste Equipment configuration: rotary kiln, ball mill, dust collector and other equipment2021年1月23日 ZHAO L, SONG X K, LU Q Y, et al Analysis of total fluorine content in electrolytic aluminum overhaul slag[J] Environment and Sustainable Development, 2017, 42(04): 114115Process for stabilizing fluorine in electrolytic aluminum aluminum, heat treatment or cold treatment processes are generally used to recover the 10% to 30% of metallic aluminum contained in the aluminum slag The secondary aluminum dross is accounting for approximately 70% to 90% of the aluminum slag, which the metal aluminum content remained is generally less than 5%Technical Report International Aluminium2021年10月1日 To recover valuable elements such as lithium from waste aluminum electrolyte, Wu et al (2021) mixed Na 2 CO 3 with waste aluminum electrolyte and roasted them at 650 • C for 25 h, and Na 2 A novel approach for lithium recovery from waste lithium
.jpg)
Chemical Engineering and Processing Process Intensification
2023年10月1日 Crush and grind the waste aluminum electrolyte fine Fig 1 (b) shows the particle size analysis, and the results show that the average particle size of the treated aluminum electrolyte powder is 4528 μm Fig 1 (c) shows the XRD diagram, which shows that the waste aluminum electrolyte mainly comprises Na 3 AlF 6, CaF 2, LiF, K 2 NaAlF 6, and An efficient recycling process is developed to recover valuable materials from overhaul slag and reduce its harm to the ecological environment The high temperature sulfuric acid roasting water leaching technology is innovatively proposed to prepare Li2CO3 from overhaul slag Selective preparation of lithium carbonate from overhaul slag by 2024年2月1日 Overhaul slag, as one of the main hazardous solid wastes generated in the electrolytic aluminum, has high research value [12]The electrolytic cell lining is eroded by continuous chemical corrosion of hightemperature molten metal and salt, resulting in expansion and peeling off, leading to low production efficiency and degradation of performance [13]A novel approach for extracting lithium from overhaul slag by low 2020年12月1日 The rapid development of the electrolytic aluminum industry in China and the increasing demand for aluminum products have led to the development of many lowgrade bauxite mines with an average Li 2 O content of at least 058% (Wang et al, 2013)Due to the use of this lowgrade bauxite in the electrolytic aluminum process, the content of lithium in the Novel process for the extraction of lithium carbonate from spent
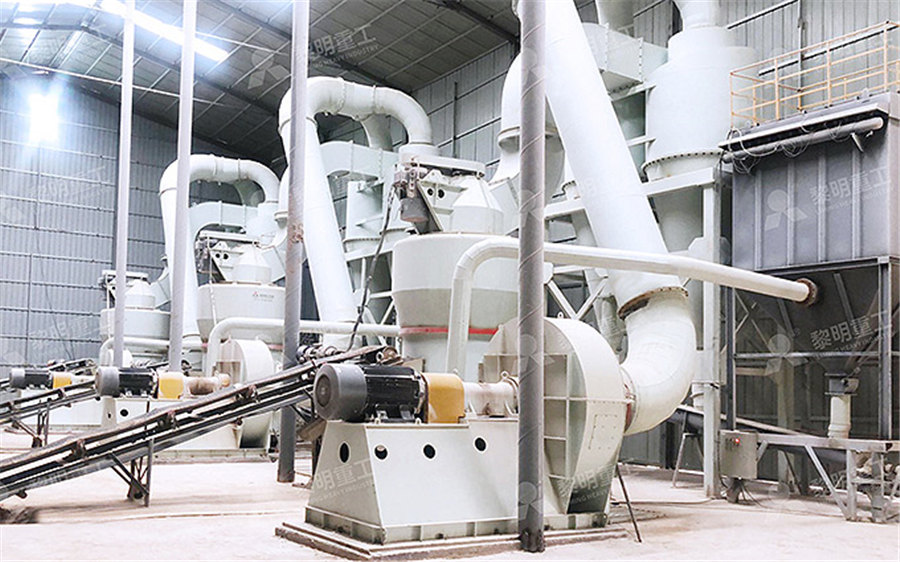
Electrolytic aluminum overhaul slag harmless technology
On August 2nd, China Nonferrous Metals Industry Association organized an expert meeting on scientific and technological achievements in Kunming, Yunnan Province, and completed the “electrolytic aluminum overhaul slag” jointly completed by Zhengzhou Hongyue Environmental Protection Technology Co, Ltd, Hunan Zhongda Metallurgical Design Co, Ltd and The present invention discloses a repair Slag sound processing method and system for reduction cell, the method comprising: 1) mixing the powder with the sulfuric acid residue overhaul, stirring to obtain a mixed slurry dip A; 2) mixing the slurry A heating, escape of hydrogen cyanide under negative pressure and the absorption with an alkaline solution to obtain a mixed slurry B; 3) Overhaul aluminum electrolytic tank Slag sound processing Download Citation On Aug 1, 2023, Jianping Yang and others published Dissolution behavior of overhaul slag from aluminum reduction cell in a cryolitebased molten salt system Find, read and Dissolution behavior of overhaul slag from aluminum reduction 2023年5月20日 Due to chemical corrosion and erosion by molten aluminum liquid and electrolyte, the carbon anode of the aluminum electrolytic cell would fall off into the electrolyte during the primary aluminum electrolysis process to produce spent anode carbon (SCA), which has been listed as one of the typical hazardous solid wastes in the National Hazardous Waste Regeneration of raw materials for aluminum electrolysis from
.jpg)
Research on the Coprocessing of Mixed Electrolytic Aluminum
electrolytic aluminum production process, including waste cathode carbon block, waste anode material Generally, electrolytic aluminum production enterprises will overhaul the electrolytic cell every five years, with a large amount of waste generated in this process Electrolytic aluminum scrap mainly contains NaF, Na 3 AlF 6, CaF 22023年5月20日 Due to chemical corrosion and erosion by molten aluminum liquid and electrolyte, the carbon anode of the aluminum electrolytic cell would fall off into the electrolyte during the primary aluminum electrolysis process to produce spent anode carbon (SCA), which has been listed as one of the typical hazardous solid wastes in the National Hazardous Waste Regeneration of raw materials for aluminum electrolysis from 2023年12月1日 Overhaul slag, as one of the hazardous wastes generated in the aluminum industry, which can pollute the environment and waste resources when arbitrarily stockpiled or landfilled Scientific and standardized recycling of overhaul slag with both valuable and pollutant characteristics can avoid environmental pollution, and greatly alleviate the global resource Harmless recovery and utilization of electrolytic aluminum spent 2024年2月1日 Overhaul slag, as one of the main hazardous solid wastes generated in the electrolytic aluminum, has high research value [12] The electrolytic cell lining is eroded by continuous chemical corrosion of hightemperature molten metal and salt, resulting in expansion and peeling off, leading to low production efficiency and degradation of performance [13]A novel approach for extracting lithium from overhaul slag by low
.jpg)
Assessing Environmental Impact of Aluminum Ash Disposal in
2024年6月4日 The main components of aluminum ash include single aluminum, aluminum oxide (Al 2 O 3), aluminum nitride (AlN), aluminum carbide (Al 4 C 3), fluoride and chlorinated salts, silicon, iron and other oxide (Kang et al 2022) Aluminum ash slag can be divided into primary aluminum ash and secondary aluminum ash according to the different degrees of 2022年10月10日 One of the main electrolytic aluminum production costs is the consumption of carbon anodes, and carbon anode slag is a common hazardous waste in the aluminum industryRecovery of carbon and cryolite from spent carbon anode slag of The electrolytic aluminum overhaul slag regeneration and recycling method comprises the following steps: (1) pulverizing the electrolytic aluminum overhaul residues; (2) adding water to leach under the condition of effectively discharging generated gas; (3) removing cyanogen from solid and liquid, (4) separating solid from liquid, (5) washing the solid, and recovering overhaul CNA Electrolytic aluminum overhaul slag, method With the rapid development of aluminium smelting industry in China, millions of tons of hazardous wastes such as carbon slag, overhaul slag and aluminum ash are generated every year In order to promote the refined management of hazardous wastes in China, an indepth research had been done, the current generation process link, pollution characteristics, utilization and Present situation of production, utilization and disposal of
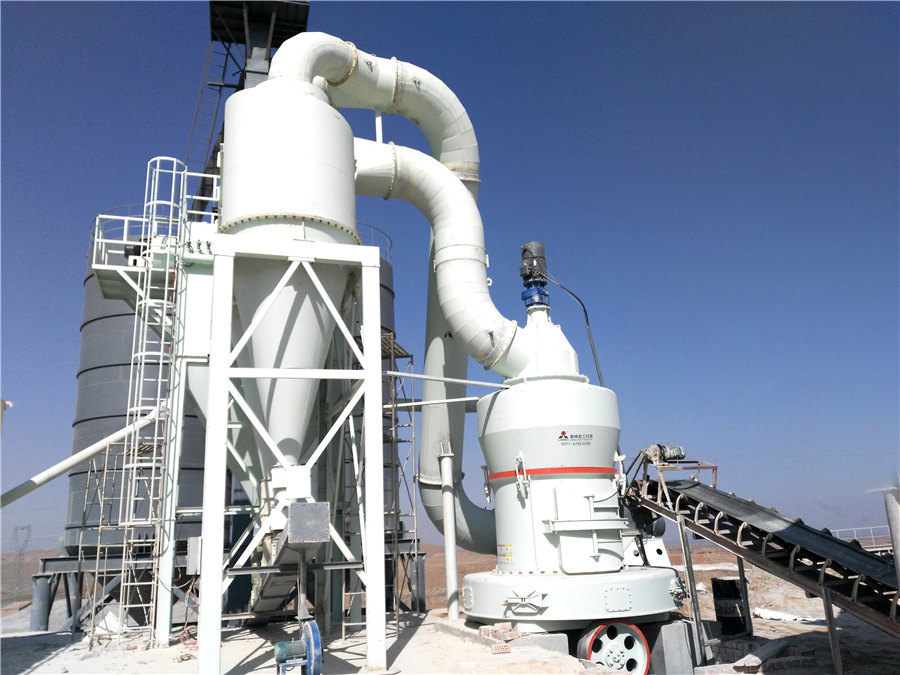
Selective extraction of lithium and solidified fluoride from overhaul
2024年10月1日 The overhaul slag utilized in the study was obtained from an electrolytic aluminum plant in Jiangxi, China The main chemical composition of the material was shown in Table 1 It can be seen that the content of Al, F, Li in overhaul slag were 1063 %, 2019 %, 159 %, respectively2021年10月1日 A novel approach for lithium recovery from waste lithiumcontaining aluminum electrolyte by a roastingleaching the leaching toxicity was investigated The experimental results show that the best ratio of aluminum ash and calcium carbide slag is 1:9, the International Journal of Mineral Processing, Volume 160, 2017 A novel approach for lithium recovery from waste lithium 2023年10月1日 Currently, the green resource utilization in the aluminum electrolysis industry mainly focuses on the solid waste treatment of aluminum electrolysis tank overhaul slag, the resource utilization of waste cathodes, and the recovery of electrolytic tank waste heat There are few reports on lithium recovery from waste aluminum electrolytes [16,17]A novel approach for ultrasonic assisted organic acid leaching of 2023年10月1日 The main components of waste aluminum cryolite electrolyte are cryolite (Na 3 AlF 6), potassium cryolite (K 2 NaAlF 6), lithium cryolite (Na 2 LiAlF 6), fluorite (CaF 2), and approximately 2% carbon black (Wang et al, 2019)The main treatment methods of waste aluminum cryolite electrolyte can be divided into two categories: combined thermalwet Efficient extraction and recovery of lithium from waste aluminum
.jpg)
Research on fluoride wholeprocess prevention and control in the
The results showed that apart from the overhaul slag of electrolytic cell, unorganized flue gas and carbon slag were the key points of fluoride emission in electrolytic aluminum production The fluoride content of unorganized flue gas was 0374 kg/t per unit product, which was about 37 times of that of organized emissions2024年7月24日 Spent aluminum electrolyte slag is a byproduct produced during the electrolysis of aluminum and contains elements such as F, Al, Na, and Li It is a toxic and harmful substance with a stable and complex structure As a consequence of fluorine pollution and low lithium recovery efficiency in the traditional hydro metallurgy process, a novel cleaner production Cleaner Process for the Selective Extraction of Lithium from Spent 2024年5月23日 16 Million metric tons of spent carbon electrodes modify carbonrich solid wastes from aluminum electrolysis are produced annually, threatening ecosystems by cyanide and fluoride pollution Here, we review carbonrich solid wastes with focus on sources and hazards, detoxification, separation, recovery, recycling and disposal Treatment techniques The recycling of carbonrich solid wastes from aluminum CNA CN96A CN9A CNA CN A CN A CN A CN 9 A CN9 A CN 9A CN A CN A CN A Authority CN China Prior art keywords waste waste material silicon carbide treatment method recovery Prior art date Legal CNA Recovery treatment method of electrolytic aluminum ash

Electrolytic cell spent lining Fig 2 Overhaul slags of the
During a longterm operation of the aluminum electrolysis cell, the molten salts continuously infiltrate and corrode the pot lining, resulting in a huge amount of hazardous waste after the overhaul2023年2月1日 Request PDF Industrial experimental research on coprocessing of spent refractory materials in aluminum electrolytic cell To realize the harmlessness, reduction and resource utilization of Industrial experimental research on coprocessing of spent ALUMINUM ASH PROCESSING SYSTEM Processing capacity: 10,000200,000 t/a Processing materials: aluminum ash, aluminum slag, aluminum shavings and other hazardous waste Equipment configuration: rotary kiln, ball mill, dust collector and other equipmentAluminum Ash Processing Aluminum Ash Recovery Aluminum Ash