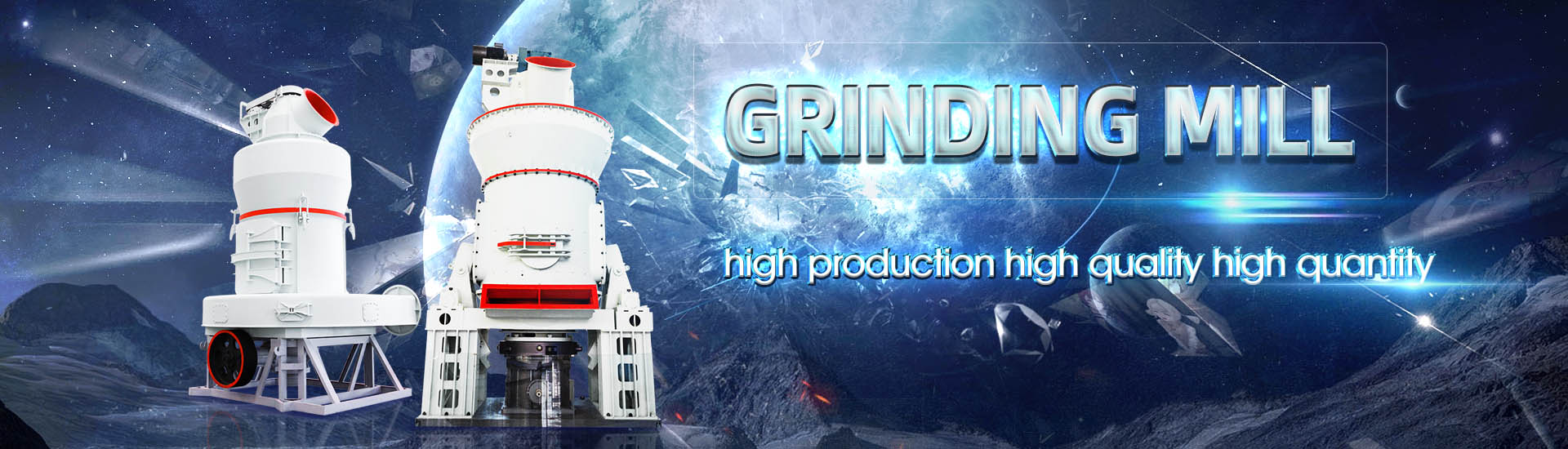
Efficient and energysaving crocodile ore mill

Energy conservation and consumption reduction in grinding
2023年11月1日 The development and application of new fine and ultrafine grinding equipment are particularly important As a new type of grinding equipment, the stirring mill has significant 2021年11月1日 Owing to their high energy efficiency, stirred mills are commonly used in the fine or ultrafine grinding of lowgrade and fine disseminated ores to enhance liberationHighefficiency and energyconservation grinding technology As a new type of grinding equipment, the stirring mill has significant advantages such as high energy efficiency, medium saving, simple installation, and easy operationEnergy conservation and consumption reduction in grinding 2022年1月1日 A pilotscale study of highefficiency and energysaving grinding technology using a special stirred mill with the ceramic medium was proposed in this studyHighefficiency and energyconservation grinding technology
.jpg)
The Role of EnergySaving Ball Mills in Mineral Processing
Energysaving ball mills are a cornerstone in mineral processing operations, designed to reduce energy consumption while maintaining or even enhancing processing efficiencyA high potential for energy savings resides in the introduction of certain crusher types that help to move the size distribution towards fine particles, the application of HPGR or chokefed cone Sustainable Processing of Mineral ResourcesSaving energy using gearless mill drives Using GMDs to power semiautogenous (SAG), ball and autogenous (AG) mills has been proven to provide improved throughput, reliability and Extracting potential ABBmajor benefits supporting this trend are better energy efficiency, improved grinding capacity, and higher metal recovery in downstream processes such as heap leaching and flotation In A structured approach to the evaluation of the energy
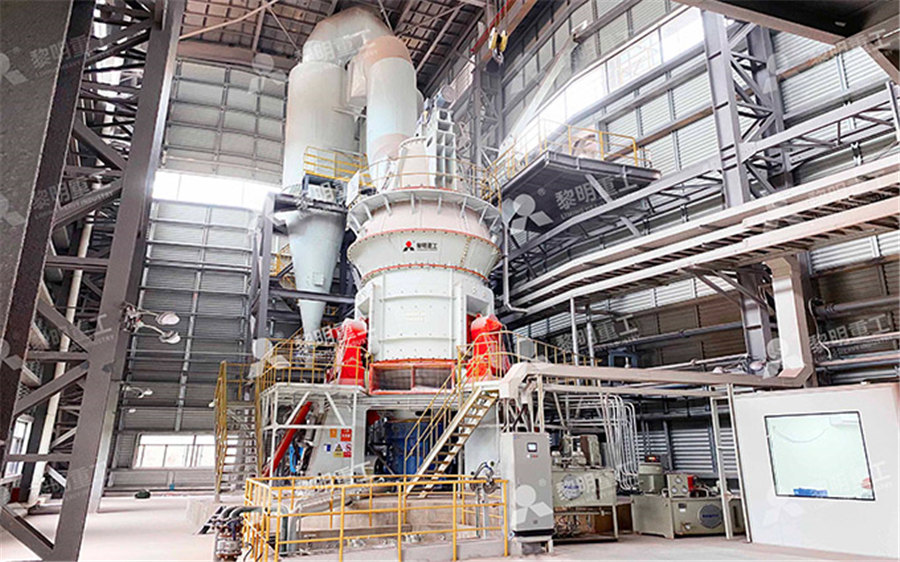
Breaking down energy consumption in industrial grinding mills
2017年1月17日 This paper reports the results of an investigation targeting two objectives: (1) characterising energy outputs in industrial grinding mill circuits, and (2) identifying the potential 2009年6月1日 It was found that the ball mill consumed 5467 kWh/t energy to reduce the F 80 feed size of 7222 lm to P 80 product size of 2754 lm while stirred mill consumed 3245 kWh/t of energy to produce Comparison of energy efficiency between ball mills and stirred the Energy Saving Compact Mini mill World electric steelmaking has increased from 595Mt in 1960 to 1,606Mt in 2013, an increase of 170% and, since their beginnings in the 1970s, a typical mini mill has increased its output from 050 to 30Mt/yr At the same time, market requirements for regional production using localMini mills, Micro mills, Nano mills and the Energy Saving Compact Mini millIn ball mills, energy savings vary from 10 per cent to 40 per cent compared to 25 mm media A regrind ball mill with a mix of small grinding media can be as energy effi cient as an Isa Mill charged with 25 and 35 mm beads In vertical stirred ENERGY SAVINGS AND TECHNOLOGY COMPARISON USING
.jpg)
How to Improve Working Efficiency of EnergySaving Grid Ball
2024年2月5日 Factors Affecting Ball Mill Efficiency 1 Physical properties of ore The physical properties such as hardness, particle size, and mud content of the ore have a significant impact on the 3RZGHU 7HFKQRORJ\ , 1 Introduction Grinding operation is the last preparation stage before beneficiation In this stage, the material undergoes the combined action of impact andEnergy conservation and consumption reduction in grinding 2024年8月23日 An energysaving ball mill is a kind of equipment specially used for grinding ore, stone, or other pared with traditional ball mills, energysaving ball mill reduces energy consumption and improve grinding efficiency by optimizing design and using a more efficient energy transmission systemEnergysaving Ball Mill VS Cement Ball Mill JXSC Mineral2020年4月10日 Bauxite grinding mill Parameters 【Mill model】: HC vertical pendulum mill 【Manufacturer】: Guilin HongCheng Mining Equipment Manufacture Co, Ltd 【Feeding granularity】: 2530mmThe Most Reliable and Efficient Bauxite Raymond Mill LinkedIn
.jpg)
EnergyEfficient Technologies in Cement Grinding
2016年10月5日 In this chapter an introduction of widely applied energyefficient grinding technologies in cement grinding and description of the operating principles of the related equip‐ ments and comparisons over each other in terms of grinding efficiency, specific energy consumption, production capacity and cement quality are given A case study per‐ formed on a The results show that grinding time is a significant factor affecting the particle size composition The suitable grinding concentration of Tongkeng ore and Gaofeng ore is 70% and 75%, respectively The effect of mill filling ratio on Gaofeng ore is not obvious The rotational rate has little effect on the grinding technical efficiencyGrinding Modeling and Energy Efficiency in Ore/Raw Material The GZM series conical ball mill is a new type of energysaving machine invented in Gold Capital of Zhao YuanAfter nearly 30 years of development,this ball mill has already played a leading role in the field of grindingIt has the following features:Efficient and EnergySaving Gzm Series Conical Ball Mill for 2019年6月1日 Energy Saving Measures in Textile Mill K Balachander, Coimbat ore, 2015 10 H W The working of proposed antenna is effective as well as efficient, and radiation is circularly polarized(PDF) Energy Saving Measures in Textile Mill
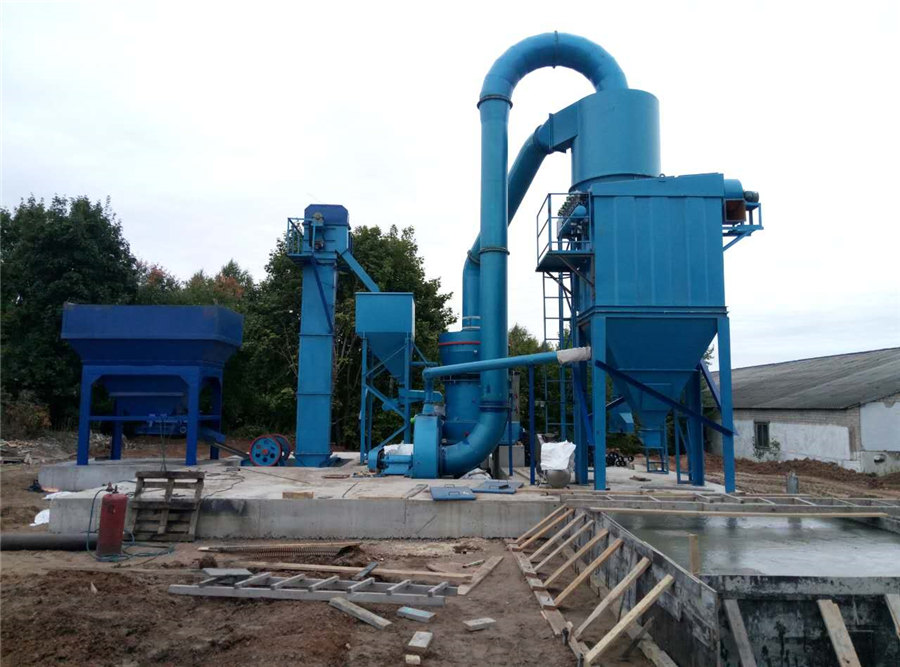
(PDF) Comparison of energy efficiency between ball mills and
The data show that the stirred mill has an advantage over the ball mill The energy saving of 25%, 37% and 27%, respectively, treating the three ore samples by using the stirred mill was realised On average, 30% energy saving can be expected Product size distributions of the two mills were compared in Fig 4the parameters of the mill In another approach, the energy efficiency of milling may be improved by adjusting the parameters of the comminuted material with the use of chemical additives or water Chemical additives may, however, have a negative environmental impact [22] Energy savings may also be found in the ball mill drive systemsEnergy Efficiency Analysis of Copper Ore Ball Mill Drive Systems2022年3月1日 energy savings are of the order of 15% overall (Parker et al, 2001, Koski et al, 2011, Kock et al, 2015 ) This energy saving is via a direct reductionHelping to reduce mining industry carbon emissions: A stepby 2023年1月1日 HPGR was found to be more energy saving advanced comminution equipment Therefore, PGE bearing lowgrade chromite ore needs an energyefficient grinding mill for the downstream beneficiation process 34 Comparison of Size reduction performance evaluation of HPGR/ball mill and
.jpg)
High Pressure Grinding Roll and Magnetic Separation for Energy Saving
2024年5月31日 This paper presents an industrial verification test, adding a high pressure grinding roll and magnetic separation operation after the thirdstage fine crushing operation to reduce the particle size of ball mill feed and improve the processing capacity of grinding operation The optimal process parameters of high pressure grinding roll and magnetic separation were As for the hard ore, use the shorthead cone crusher is much more economy that rod mill In consequence, no matter ball mill or rod mill, whatever we choose, we should according the specific situation to determine Product advantages 1 Save power The rod mill can save more than 40% power than the other machines in market 2High Efficient and Energy Saving Rod Mill2010年1月1日 Comparative high pressure grinding rolls (HPGR) and cone crusher pilotscale tests were conducted using Upper Group 2 (UG2) platinumbearing ore in order to determine the impact of microcracks in Efficiency, economics, energy and emissionsemerging criteria for 2022年1月1日 We have analytically derived a mathematical model of energysaving ore grinding by a ball mill with a threephase motion of grinding bodies, invariant to a change in the length of rods during wearOPTIMISATION OF ENERGY AND MATERIAL USE IN BALL MILLS WITH ENERGY
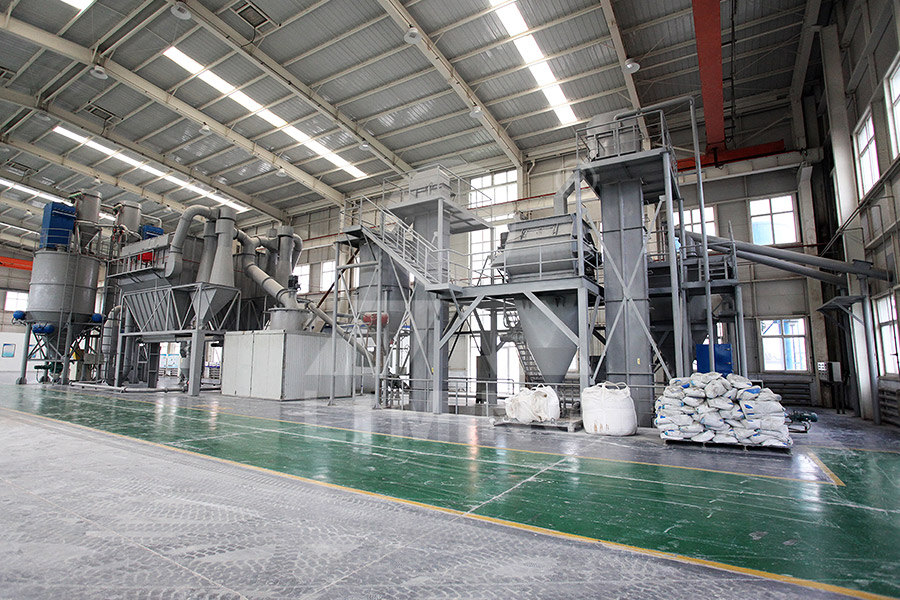
The Energy Saving Technology of Beneficiation of Iron Ore
The Coalition for Energy Efficient Comminution The Energy Saving Technology of Beneficiation of Iron Ore V V KARMAZIN, M A BIKBOV AND A A BIKBOV MAGNETIC AND ELECTRICAL SEPARATION, VOL 11 (4), PP 211224 ABSTRACTThe Coalition for Energy Efficient Comminution Energy Savings and Improved Recovery with Small Grinding Media In regrind application, a vertical stirred mill with small media (512 mm Millpebs) will require at least 62% less energy than a ball mill charged with 25 mm grinding mediaEnergy Savings and Improved Recovery with Small Grinding Mediaenergyefficient grinding technologies such as stirred mills in platinum concentrator circuits In addition to this, further energy gains can result, depending on how this technology is incorporated in a flowsheet For instance, in some cases a twostage stirred milling circuit will use energy more efficiently than a singlestage optionTECHNOLOGY SELECTION OF STIRRED MILLS FOR ENERGY 2022年9月1日 A small fraction of the mill input energy goes into breaking the ore particles while the majority is dissipated in the mill: energy loss through noise, heat and wear can be as high as 99 % (Adewuyi et al, 2020, Bouchard et al, 2016)Towards waterless operations from mine to mill ScienceDirect
.jpg)
CNA Efficient energysaving crushing and grinding
The invention relates to an efficient energysaving crushing and grinding process for stage grinding, which adopts a 'coarse crushing + singlestage semiautogenous grinding process + vertical stirring and grinding' process to replace the conventional stage crushing and grinding process; by adopting the longcylinder type customized semiautogenous mill, the ore grinding 2009年1月1日 This Energy Guide discusses energy efficiency practices and energyefficient technologies that can be implemented at the component, process, facility, and organizational levels(PDF) Energy Efficiency Improvement and Cost Saving Opportunities The invention provides an energysaving ore mill, comprising: the grinding outer box is provided with a box cover at the upper end, the grinding inner box is arranged in the grinding outer box, a plurality of groups of loop bars are uniformly arranged around and between the outer wall of the bottom of the grinding inner box and the inner wall of the bottom of the grinding outer box, CNA Energysaving ore mill Google PatentsFigure 3: Relationship between feed size (F80) and Bond efficiency factor (Huang et al, 2019) VERTICAL POWER MILL (VPM) – PRINCIPLE OF OPERATION Declining ore grades and more complex ore bodies, as well as waste management and global net zero initiatives, lead to a clear trend for high tonnage yet energy efficient grindingRECENT DEVELOPMENTS IN COARSE GRINDING USING VERTICAL
%3C1PGHL[2}HK_]YT.jpg)
Increasing Energy Efficiency and Productivity of the
2020年12月21日 Energy saving potential for various energyintensive processes in mining [3] 1 Btu (British thermal unit) ≈ 1055 Joule This measure suggests that a VSI can save 2–14% of the energy consumed in grinding, depending on the energy model used and the final product size This estimate is in agreement with an energy saving of 118% observed in an iron ore application where VSI’s were introduced as a crushing step preceding the grinding circuitEnergy considerations in compressive and impact crushing of rock2022年1月30日 (A) Evaluation of the energy consumption reduction ratio when an operating condition is varied, (B) evaluation of the reduction ratio of the parameter F300 when an operating condition is varied (PDF) Rod Mill Product Control and Its Relation to Energy 2009年6月1日 It was found that the ball mill consumed 5467 kWh/t energy to reduce the F 80 feed size of 7222 lm to P 80 product size of 2754 lm while stirred mill consumed 3245 kWh/t of energy to produce Comparison of energy efficiency between ball mills and stirred
.jpg)
Mini mills, Micro mills, Nano mills and the Energy Saving Compact Mini mill
the Energy Saving Compact Mini mill World electric steelmaking has increased from 595Mt in 1960 to 1,606Mt in 2013, an increase of 170% and, since their beginnings in the 1970s, a typical mini mill has increased its output from 050 to 30Mt/yr At the same time, market requirements for regional production using localIn ball mills, energy savings vary from 10 per cent to 40 per cent compared to 25 mm media A regrind ball mill with a mix of small grinding media can be as energy effi cient as an Isa Mill charged with 25 and 35 mm beads In vertical stirred ENERGY SAVINGS AND TECHNOLOGY COMPARISON USING 2024年2月5日 Factors Affecting Ball Mill Efficiency 1 Physical properties of ore The physical properties such as hardness, particle size, and mud content of the ore have a significant impact on the How to Improve Working Efficiency of EnergySaving Grid Ball 3RZGHU 7HFKQRORJ\ , 1 Introduction Grinding operation is the last preparation stage before beneficiation In this stage, the material undergoes the combined action of impact andEnergy conservation and consumption reduction in grinding
.jpg)
Energysaving Ball Mill VS Cement Ball Mill JXSC Mineral
2024年8月23日 An energysaving ball mill is a kind of equipment specially used for grinding ore, stone, or other pared with traditional ball mills, energysaving ball mill reduces energy consumption and improve grinding efficiency by optimizing design and using a more efficient energy transmission system2020年4月10日 Bauxite grinding mill Parameters 【Mill model】: HC vertical pendulum mill 【Manufacturer】: Guilin HongCheng Mining Equipment Manufacture Co, Ltd 【Feeding granularity】: 2530mmThe Most Reliable and Efficient Bauxite Raymond Mill LinkedIn2016年10月5日 In this chapter an introduction of widely applied energyefficient grinding technologies in cement grinding and description of the operating principles of the related equip‐ ments and comparisons over each other in terms of grinding efficiency, specific energy consumption, production capacity and cement quality are given A case study per‐ formed on a EnergyEfficient Technologies in Cement GrindingThe results show that grinding time is a significant factor affecting the particle size composition The suitable grinding concentration of Tongkeng ore and Gaofeng ore is 70% and 75%, respectively The effect of mill filling ratio on Gaofeng ore is not obvious The rotational rate has little effect on the grinding technical efficiencyGrinding Modeling and Energy Efficiency in Ore/Raw Material
.jpg)
Efficient and EnergySaving Gzm Series Conical Ball Mill for
The GZM series conical ball mill is a new type of energysaving machine invented in Gold Capital of Zhao YuanAfter nearly 30 years of development,this ball mill has already played a leading role in the field of grindingIt has the following features: