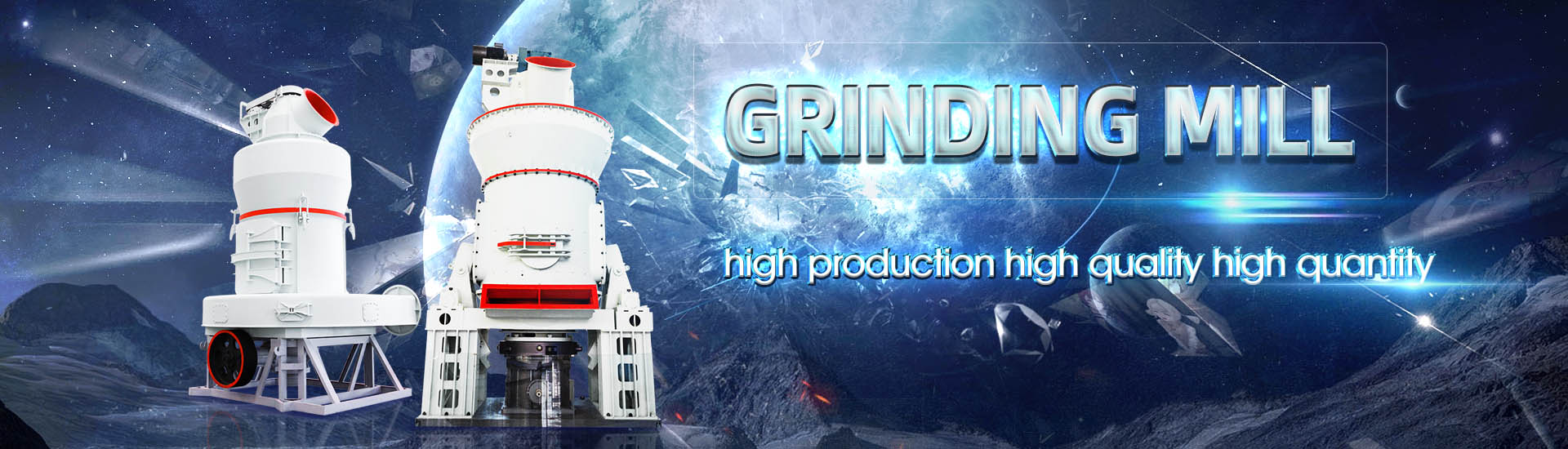
Highefficiency coal powder furnace design technology Technical plan
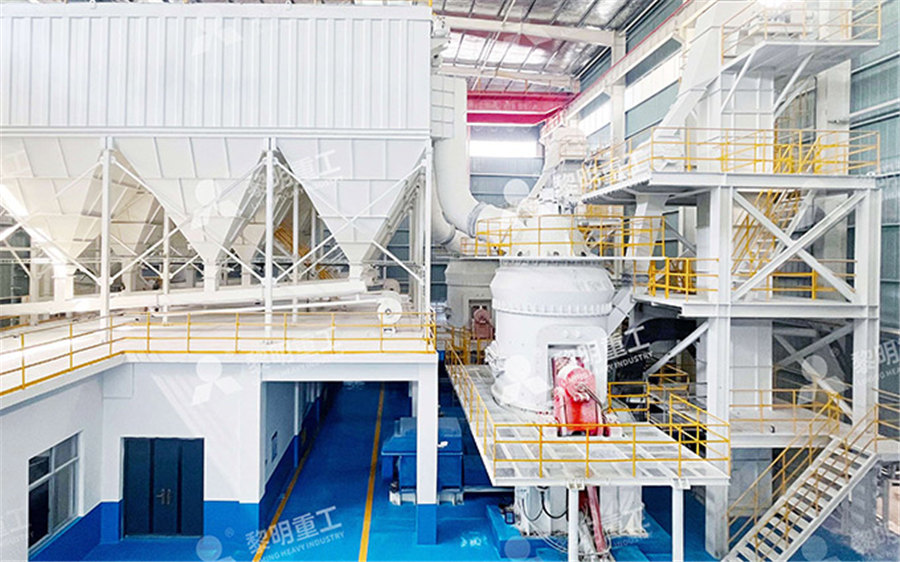
Advanced Development of Pulverized Coal Firing Technologies
Semianthracite coal and oil coke have higher heating values but are disadvantaged in their low ignitability due to their low volatile content This section outlines the new burners that we have PCC is the most commonly used technology in coalfired power plants and is based on many decades of experience The units operate close to atmospheric pressure which simplifies the Current design and construction of coalfired power plant ICSCPERFORMANCE AND COSTS – Technological development aims to increase the efficiency and decrease the investment cost and the emissions of coalfired power The generating efficiency CoalFired Power IEAETSAPThe HighEfficiency, LowEmissions CoalFired Power Generation Roadmap describes the steps necessary to adopt and further develop technologies to improve the efficiency of the global Technology Roadmap HighEfficiency, LowEmissions CoalFired
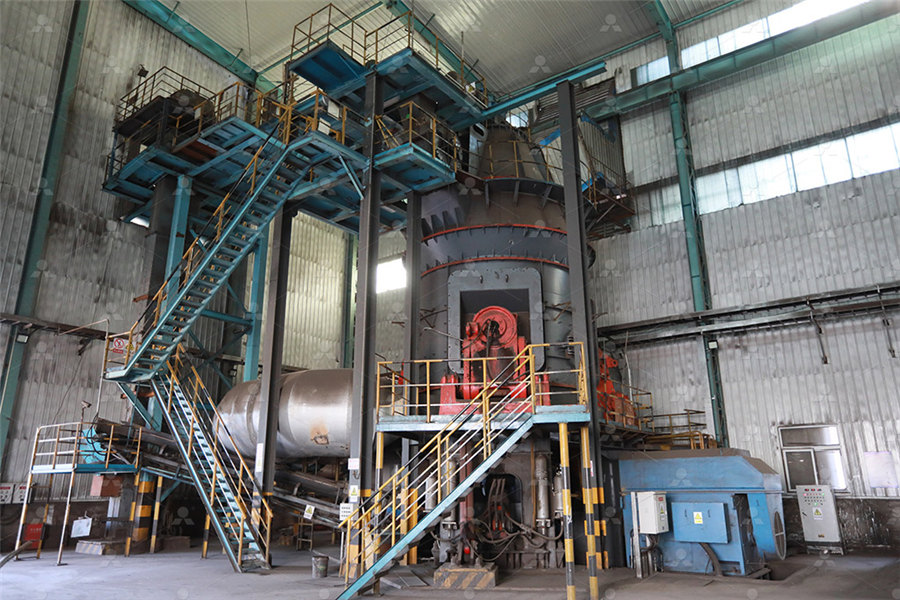
Continuous DeNOx Technology for Improved Flexibility and
2023年12月26日 It focuses on the assessment and optimization of continuous denitrification systems tailored for a 1000 MW ultrasupercritical pulverized coal boiler The extant Since coal amounts to about 25% of the annual power generation, it is necessary for countermeasures against global warming to take measures to limit CO2 emissions through Latest Technologies of High Efficient Coal Fired Thermal Power For a higher efficiency of the technology supercritical and ultrasupercritical coalfired technologies have been developed These technologies can combust pulverised coal and Pulverised Coal Combustion with higher efficiency Climate 2021年4月8日 Highefficiency, lowemissions (HELE) coalfired power plant technologies operate with a higher thermal efficiency of the steam cycle for coalfired power generation, A Review of the Numerical Modeling of Pulverized Coal
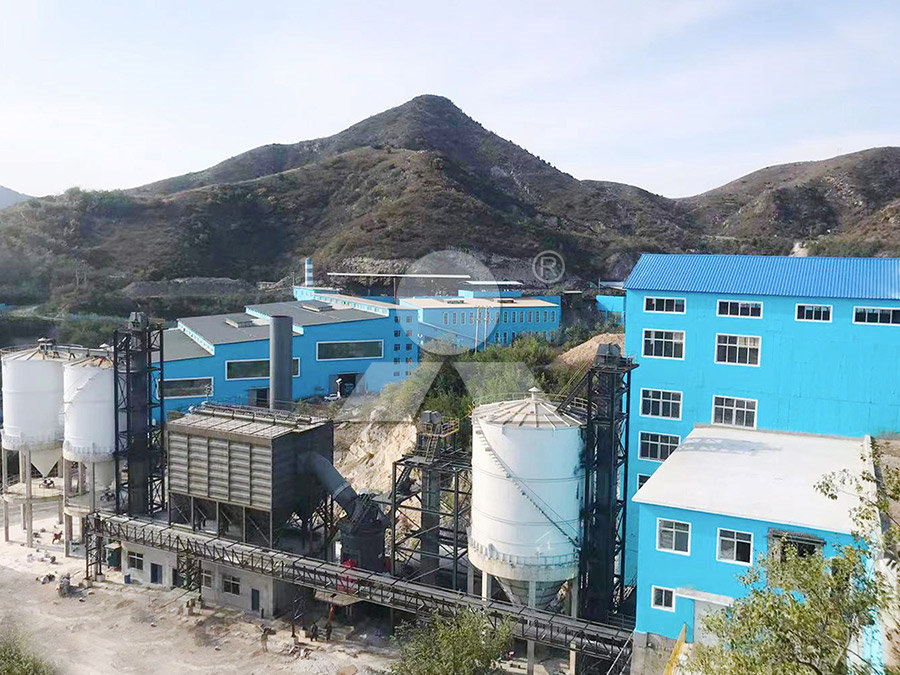
Highefficiency pulverized coal power generation using lowrank
2017年1月1日 In the present chapter, a review of state of the art technology in pulverized fuel fired power plants is presented Pulverized fuel firing is the mostly applicable firing technology Advancements in supercritical (SC), ultrasupercritical (USC), and advanced USC coalfired power plants have been achieved through the development of enhanced materials utilized in Comprehensive technical review of the highefficiency low on the supply of oxygen or air To improve the heat retention and the energy efficiency, a redesign of the coal fired furnace used in the rural foundries and selection of specified new lining materials were introduced Keywords Design and material selection, Coal fired furnace, Heat Loss, Energy efficiency 1320Evaluating the energy efficiency of rural foundry coal fired furnace 70 Metall Mater Eng Vol 25 (2) 2019 p 69104 Contents 1 Introduction 71 2 Development in BF Design and Measuring Systems 72 3 Development in Top Charging Materials 75 31 Active Nut Coke 76 MODERN BLAST FURNACE IRONMAKING TECHNOLOGY:
.jpg)
The Technology and Application of a New Type of Coal Water
2021年9月30日 In 2017, the new type of CWSfired CFB with high efficiency and clean combustion boiler technology was awarded the major energysaving achievement of Shandong Province [Shandong Government Office (2017) No 169]; In 2017, confirmed by the Ministry of Science and Technology, this technology has reached the domestic advanced level; In Nov Highly efficient coal powder combustion technology and the coal powder industrial boiler system have improved thermal efficiency of industrial boilers to over 90% Pollutant emissions of coalfired industrial boilers have reached ultralow emission standards Establishing UltraLow Emission Projects for Coal Fired Industrial BoilersGreen and LowCarbon Development and Utilization Technology of Coal 2023年12月26日 Continuous DeNOx Technology for Improved Flexibility and Reliability of 1000 MW CoalFired Power Plants: Engineering Design, Optimization, and Environmental Benefits December 2023 Processes 12(1):56(PDF) Continuous DeNOx Technology for Improved Flexibility and 2023年6月15日 Coalfired power generation is an important approach to supply energy [1]And Coalfired power stations supply over 70 % of the electricity in China [2]However, large amounts of pollutants (eg, particulate matter (PM), nitrogen oxides (NO x), and sulfur oxides (SO x)) are generated by combustion in coalfired boilersThus, flue gas purification systems are installed Integrated technology for dust removal and denitration of high
.jpg)
Numerical Study on Combustion Characteristics of Biogas
2024年4月23日 furnacebalanced ventilation, and natural circulation It features acompact enclosed πshaped layout supported by fully steel frame suspension structure The tangential combustion method offers several advantages such as effective flame distribution, high combustion efficiency,simple operation, and coal adaptability Hence, this furnace design 2019年7月2日 Expected technical issues and countermeasure at a high rate of PCI into the blast furnace [87] Figures available via license: Creative Commons Attribution 40 International Content may be Modern blast furnace ironmaking technology: potentials to 2018年11月19日 There is always an optimal particle size for a boiler, and thus the coal powder size measurement is critical to keep the high efficiency of the boiler and favorable dynamic performance of mills There are various particle sizing techniques commonly employed in practice, with some of them offline and others online [ 6 ]Digital holographic sizer for coal powder size IOPscience2024年11月1日 The carbon dioxide emissions from cement, highefficiency water reducers, and water are 0732, 072, and 0 kgCO 2 /kg, respectively The carbon dioxide emissions from natural sands and stones are 00417 kgCO 2 /kg, while the carbon dioxide emissions from fly ash and electric furnace steel slag powder are 00345 and 00442 kgCO 2 /kg Effect of electric furnace steel slag powder on the strength of
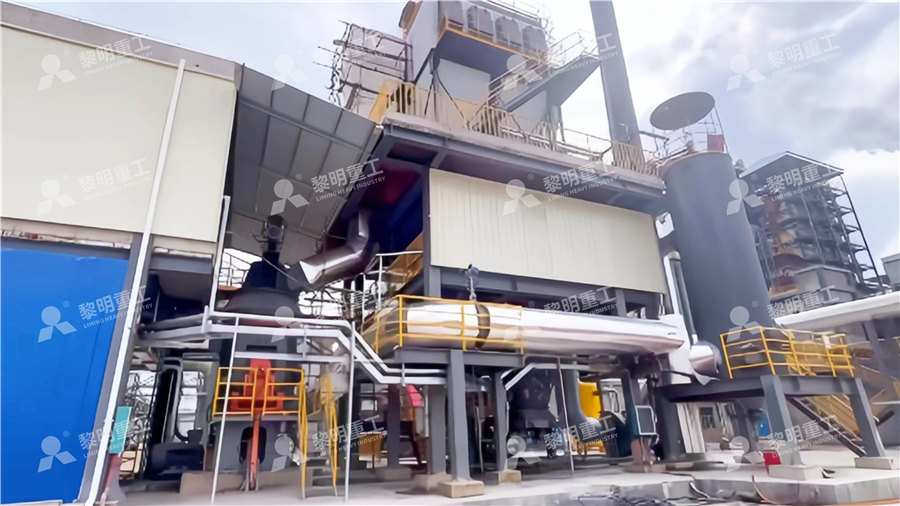
Development Tendency and Prospect of High Performance Coal
22 High efficiency power generation system A high efficiency power generation system can reduce CO 2 emission while producing the required electric power In Japan, the ultrasuper critical (USC) boiler has been introduced into operation and the steam condition has been gradually improved (Fig 5) For the greater im2020年10月15日 From the design, 000129m 3 /s volume of air supplied to the cupola furnace with an available volumetric capacity of 001378m 3 at the rate of 3296358W/m 2 produced an estimated melting heat of Design, Fabrication and Construction of Cupola The plasma ignition and tinyoil ignition techniques developed and applied in recent years can save lots of oil However, the combustion efficiency in the startup period is quite low (the burnout rate is about 50–65 %), and the soot with richer carbon is very likely to accumulate and cause severe accidents such as furnace explosion and burning of the SCR catalyst, the air preheater The High Efficiency and Clean Combustion of Coal Based onUpgrading and efficiency improvement in coalfired power plants 5 The efficiencies of coalfired plants will normally decrease over time as components suffer deterioration with age and use The losses that develop in the earlier part of the life of a plant are generally containable by employing good operating and maintenance practicesUpgrading and efficiency improvement in coalfired power plants
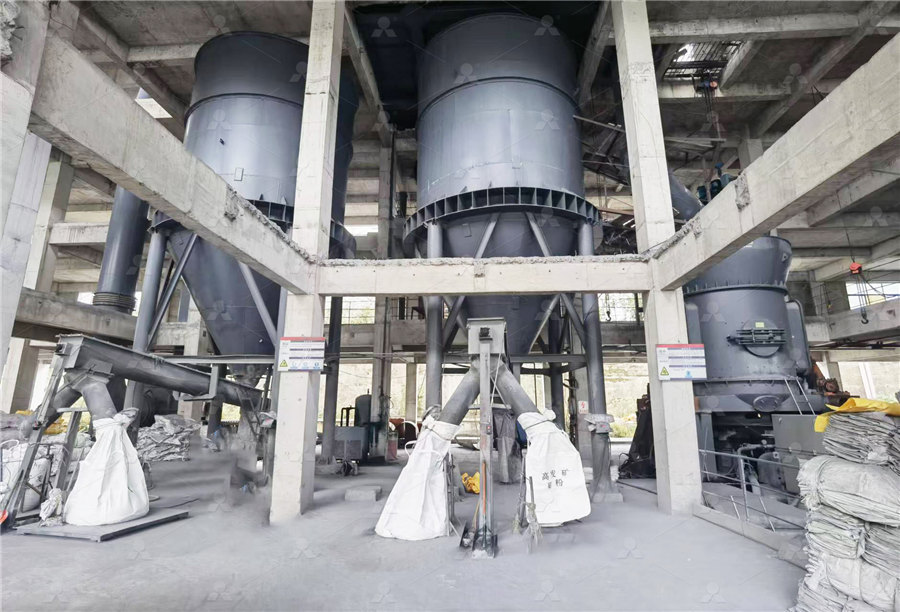
Blast furnace hydrogenrich metallurgyresearch on efficiency injection
2022年3月1日 The blast furnace (BF) ironmaking has irreplaceable technological advantages such as the simple process and high production efficiency, so the output of steel material produced by the blast furnaceconverter long process 2022年3月1日 Natural gas (NG) can replace part of pulverized coal (PC) in the blast furnace (BF) injection as the clean and highcalorific hydrogenrich energy, which can reduce environmental pollution and energy consumption in molten iron production In this work, the method of numerical simulation is used to first compare and analyze the differences of NG and Blast furnace hydrogenrich metallurgyresearch on efficiency injection 2021年4月20日 The designofexperiments matrix was prepared using the simplex–lattice design method with four independent variables (ie coal A and B and biomass A and B)Experimental Study and Design of Biomass CoFiring in a FullScale Coal Residential highefficiency wood and coal burning furnaces Explore the MF eSeries; P Series The Secret to High Efficiency Wood Furnace Performance the terms are often interchangeable – is a technology that has been around for more than 180 yearsThe Secret to High Efficiency Wood Furnace Performance
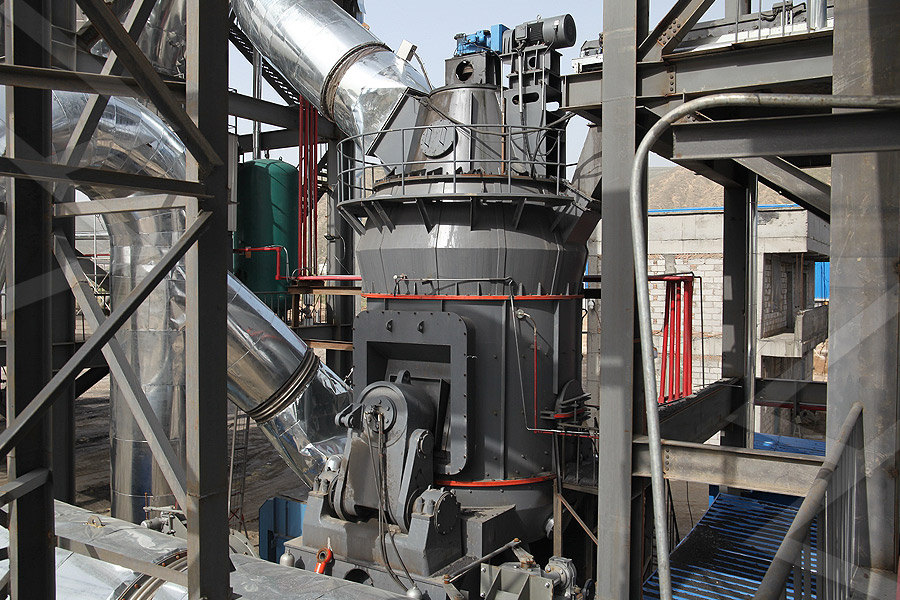
BLAST FURNACE TECHNOLOGY Paul Wurth
blast furnace technology 5 TECHNOLOG LEADERSHIP IN IRONMAKING – AVAILABLE HERE! blast furnace construction Modernisation 06 07 stockhouse charging systems 08 09 blast furnace top charging technology – the original 10 11 blast furnace Design: the blast furnace Proper, lining cooling 12 13 hot blast generation supply 14 年3月1日 Although there are many techniques for CO 2 mitigation, such as the integrated gasification combined cycle (IGCC) [6], OxyCombustion and CO 2 capture and Storage (CCS) [7], improving efficiency through steam parameter improvement is the best method to reduce CO 2 emissions from coalfired power plants Thus, ultrasupercritical (USC) technology, namely, China’s RD of advanced ultrasupercritical coalfired power 2023年6月14日 Ultrahigh power electric arc furnace technology requires not only the high level of main transformer power in device, but also the maximum allowable power state of electricity arc in furnace working, that is, the main transformer reaches full capacity and the electricity arc burns steadily, and during the smelting process the highest electricity arc power can be used as long UltraHigh Power Electric Arc Furnace Steelmaking2022年6月1日 Pulverised coal injection (PCI) into blast furnace (BF) is a dominant technology for partial coke replacement and lowering production cost, and high oxygen enrichment is a recent promising HMBCFD study of oxygenenriched pulverised coal
.jpg)
Continuous DeNOx Technology for Improved
2023年12月26日 This study endeavors to enhance the operational efficiency of extant coalfired power plants to mitigate the adverse environmental impact intrinsic to the prevalent utilization of coalfired power generation, which is Efficiency of high energy over conventional milling of granulated blast furnace slag powder to improve mechanical performance of slag cement paste Ahmed Bouaziz, Rabah Hamzaoui, Sofiane Guessasma, Ridha Lakhal, Djamel Achoura, Nordine Leklou PII: DOI: Reference: S00325910(16)308828 doi: 101016/jpowtec201612014 PTEC 12162 To appear in: Powder Efficiency of high energy over conventional milling of granulated 2023年6月15日 In these power plants, coal powder rather than coal blocks is often used to generate thermal energy because the pulverized coal could produce a higher combustion efficiency [6,7] Show abstract The hygroscopicity of coal powder is one of the crucial factors that determine its moisture content, which significantly affects its adhesion, flowability, charge Integrated technology for dust removal and denitration of high 2012年8月28日 The International Energy Agency's (IEA’s) December 2012 report “Technology Roadmap: HighEfficiency, LowEmissions CoalFired Power Generation” finds that in 2011, about 50% of new coalfired power plants used mostly supercritical and ultrasupercritical coal units, a share that doubled in the past decadeUltrasupercritical Plant an overview ScienceDirect Topics

Development of HighEfficiency Coal Gasification Technology:
2016年1月1日 Based on data from the Geological Agency of Indonesia (2011), Indonesia total reserves of coal approximate 28 Billion tons of very high (> 7100 kcal/kg) 231 Mt (Million tons), high (61007100 kcal Control Blast Furnace Pulverized Coal Injection to Increase PCI Rates Weiser, R / Braune, High efficiency production practice of a 100 t DC EBT EAF at Xing Cheng Steel Works Xu, Blast Furnace Bosh Design and Repairs van Laar, R J / Meijers, High Emissivity Coating Technology Improves Annealing Furnace EfficiencyIn the steelmaking industry, the ironmaking blast furnace (BF) plays a critical role in energy consumption and CO 2 emissions (Hu et al, 2019, Yu et al, 2021, Zhuo et al, 2021)To improve efficiency and reduce emissions, pulverized coal injection (PCI) technology is extensively employed in this process (Ishii, 2000, Shen et al, 2008) and biochar, a carbon–neutral solid Highfidelity modelling of unburnt coal flow in an industryscale Pulverised coal injection (PCI) into blast furnace (BF) is a dominant technology for partial coke replacement and lowering production cost, and high oxygen enrichment is a recent promising technology for further increasing coal combustion and thus increasing pulverised coal rate (PCR) and lowering emissions In this paper, a heat and mass balance (HMB) model and a three HMBCFD study of oxygenenriched pulverised coal combustion
.jpg)
Evaluating the energy efficiency of rural foundry coal fired furnace
on the supply of oxygen or air To improve the heat retention and the energy efficiency, a redesign of the coal fired furnace used in the rural foundries and selection of specified new lining materials were introduced Keywords Design and material selection, Coal fired furnace, Heat Loss, Energy efficiency Metall Mater Eng Vol 25 (2) 2019 p 69104 Contents 1 Introduction 71 2 Development in BF Design and Measuring Systems 72 3 Development in Top Charging Materials 75 31 Active Nut Coke 76 MODERN BLAST FURNACE IRONMAKING TECHNOLOGY: 2021年9月30日 In 2017, the new type of CWSfired CFB with high efficiency and clean combustion boiler technology was awarded the major energysaving achievement of Shandong Province [Shandong Government Office (2017) No 169]; In 2017, confirmed by the Ministry of Science and Technology, this technology has reached the domestic advanced level; In Nov The Technology and Application of a New Type of Coal WaterHighly efficient coal powder combustion technology and the coal powder industrial boiler system have improved thermal efficiency of industrial boilers to over 90% Pollutant emissions of coalfired industrial boilers have reached ultralow emission standards Establishing UltraLow Emission Projects for Coal Fired Industrial BoilersGreen and LowCarbon Development and Utilization Technology of Coal
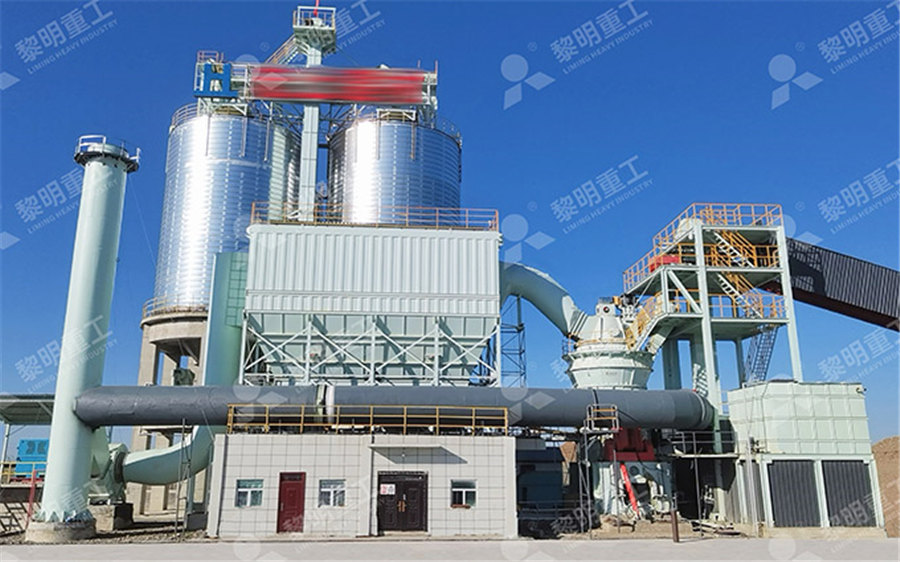
(PDF) Continuous DeNOx Technology for Improved Flexibility and
2023年12月26日 Continuous DeNOx Technology for Improved Flexibility and Reliability of 1000 MW CoalFired Power Plants: Engineering Design, Optimization, and Environmental Benefits December 2023 Processes 12(1):年6月15日 Coalfired power generation is an important approach to supply energy [1]And Coalfired power stations supply over 70 % of the electricity in China [2]However, large amounts of pollutants (eg, particulate matter (PM), nitrogen oxides (NO x), and sulfur oxides (SO x)) are generated by combustion in coalfired boilersThus, flue gas purification systems are installed Integrated technology for dust removal and denitration of high 2024年4月23日 furnacebalanced ventilation, and natural circulation It features acompact enclosed πshaped layout supported by fully steel frame suspension structure The tangential combustion method offers several advantages such as effective flame distribution, high combustion efficiency,simple operation, and coal adaptability Hence, this furnace design Numerical Study on Combustion Characteristics of Biogas 2019年7月2日 Expected technical issues and countermeasure at a high rate of PCI into the blast furnace [87] Figures available via license: Creative Commons Attribution 40 International Content may be Modern blast furnace ironmaking technology: potentials to
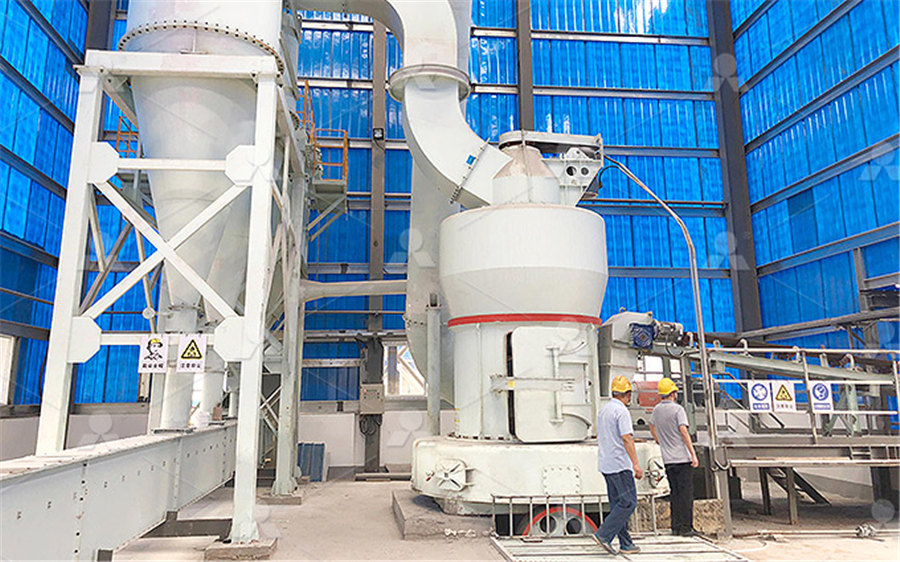
Digital holographic sizer for coal powder size IOPscience
2018年11月19日 There is always an optimal particle size for a boiler, and thus the coal powder size measurement is critical to keep the high efficiency of the boiler and favorable dynamic performance of mills There are various particle sizing techniques commonly employed in practice, with some of them offline and others online [ 6 ]2024年11月1日 The carbon dioxide emissions from cement, highefficiency water reducers, and water are 0732, 072, and 0 kgCO 2 /kg, respectively The carbon dioxide emissions from natural sands and stones are 00417 kgCO 2 /kg, while the carbon dioxide emissions from fly ash and electric furnace steel slag powder are 00345 and 00442 kgCO 2 /kg Effect of electric furnace steel slag powder on the strength of