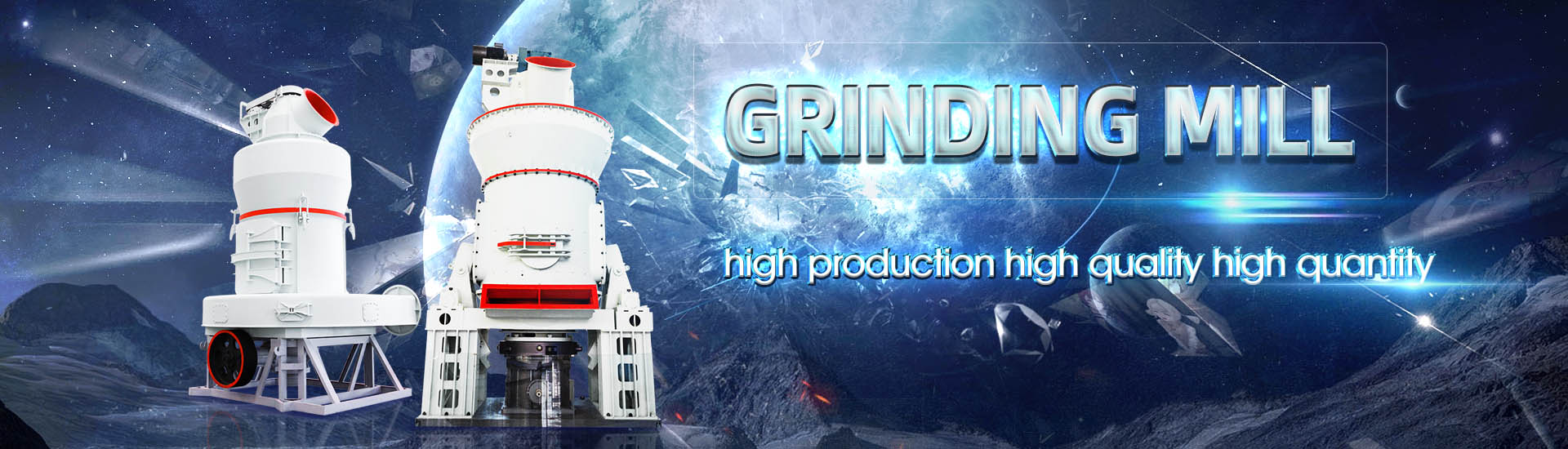
What is the crushing value requirement of high calcite ore powder
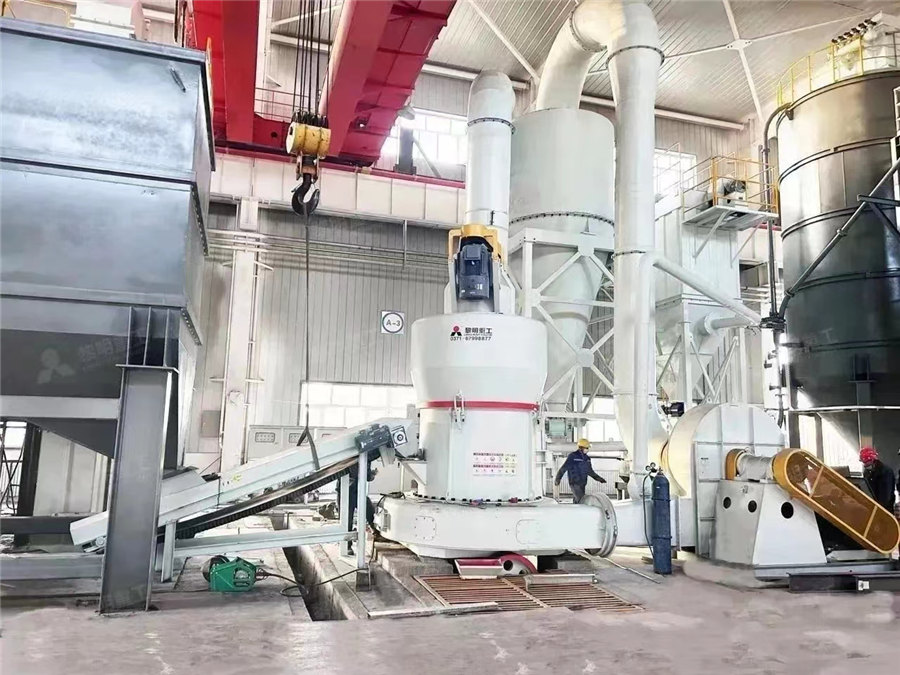
Calcite Mastery: From Hardness to Powder Processing Techniques
Calcite feedstock with a size of less than 400mm is uniformly fed into the vibrating feeder by the jaw crusher for initial coarse crushing treatment After preliminary coarse crushing, calcite is sent to an impact crusher or cone crusher via a belt conveyor for secondary fine crushing treatmentScreening plant will sieve and separate the crushed calcite powder The powder in suitable size will be send to grinding plant for fine powder, ultrafine powder production As the important Calcite Ore Crushing Solutions DSMAC2024年8月3日 Selecting highquality calcite ore as raw material is the first step in preparing ultrafine powder The quality of raw materials is directly related to the purity and performance Calcite ultrafine powder preparation process flowPhase one: raw material crushing Calcite blocks will be crushed to 15mm50mm by crusher Phase two: grinding Crushed calcite material will be sent to the storage hopper by the Calcite Grinding Mill Calcite Powder Processing Solution
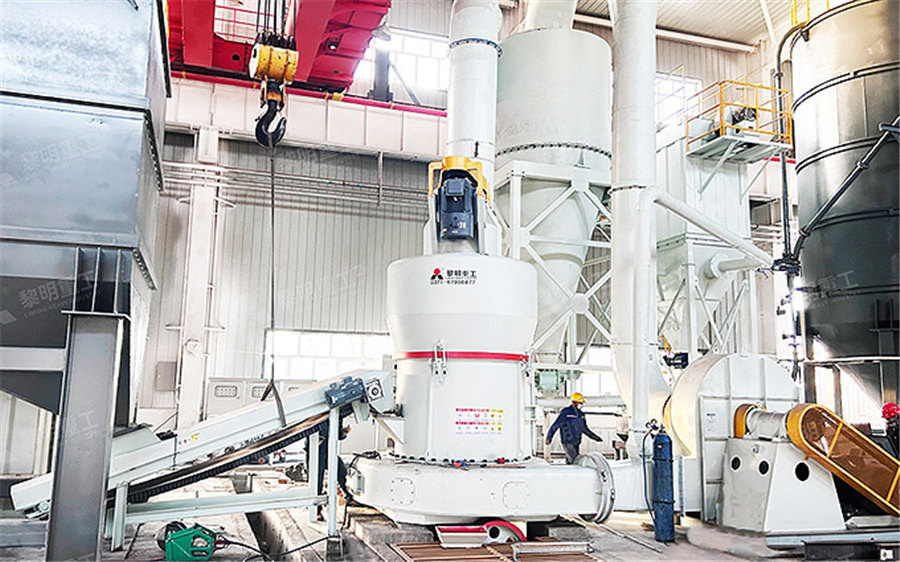
The effects on the grinding parameters of chemical, morphological
2022年1月1日 Generally, the most important factor used to the required scaleup of a grinder is usually the grindability value of that material, especially the Bond grindability Therefore, Crushing: Once extracted, the raw calcite is transported to a crushing facility The calcite is subjected to primary and secondary crushers to reduce its size to manageable piecesHow calcite is mined and processed2022年1月1日 The Bond and Hardgrove grindability values for the calciteAF (G bg = 3748 g/rev and HGI = 78) were found to be easier than the calciteBU (G bg = 1916 g/rev and HGI The effects on the grinding parameters of chemical, morphological 2023年5月12日 1 Crushing: Use a jaw crusher, roll crusher, and vibrating screen to form a twostageclosed circuit crushing system to crush the raw magnesite ore to 1mm 2 Calcination: Magnesite Ore Processing: Separation and Calcination
.jpg)
Purification of Highgrade Calcite Ore by Flotation with Springer
2018年9月17日 Cationic (Tallow1,3diaminopropane, Duomeen T) collector has been used in the purification of calcite by flotation with an aim of achieving calcite concentrate for its use in In the present study we propose some preliminary results on calcite powders produced by high energy grinding Nature and extent of calcitearagonite transformation and lattice defectXRD line profile analysis of calcite powders produced by high 2021年9月22日 The influence of intact rock properties on powder factor selection and the influence of powder factor selection on postblast conditions have also been discussedA Review on the Prediction and Assessment of 2022年12月27日 The production of calcite powder is mainly divided into four steps: crushing, grinding, grading and powder collection +29 The added value of the product is relatively high, but the energy consumption is relatively high the delivery is done by the miner The main requirements for calcite ore transportation are: How To Make Calcite Powder?
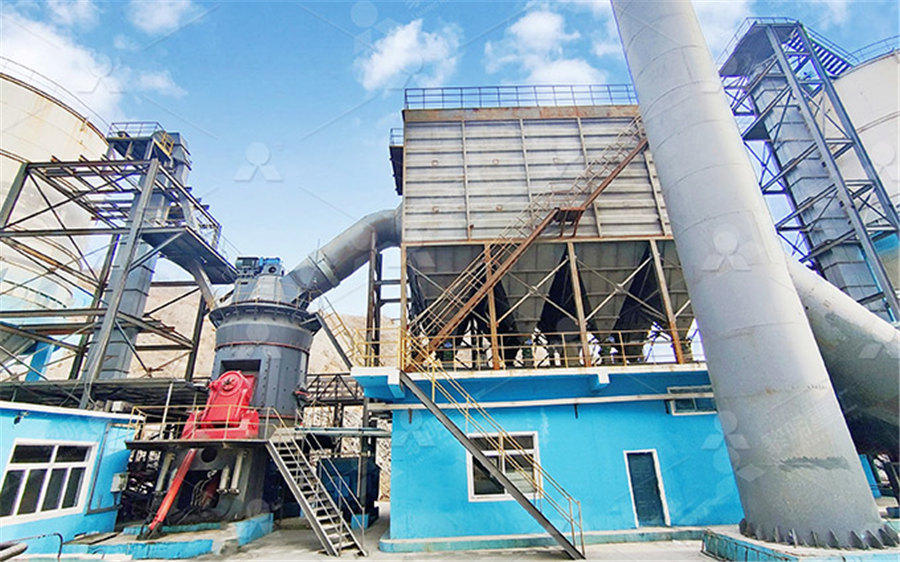
Calcite Ore Crushing Solutions DSMAC
Calcite powder is a natural form of calcium carbonate with extremely high whiteness, purity and free flowing in nature Calcite powder and coated calcite powder has a pivotal role in the modern industrial like plastic, paint, cosmetic, paper, PVC pipe etc 2023年2月15日 21 Fluoritecalcite type ore The fluoritecalcite type ore is mainly composed of fluorite and calcite (with a content of more than 30%) Under alkaline condition, calcite is easy to be floated But under acid condition, the flotation condition of calcite is greatly reduced4 Steps to Process Complex Lowgrade Fluorite OreIn the simplest terms, ore is a naturally occurring solid material from which a metal or valuable mineral can be extracted profitably An ore deposit could contain lead, gold, copper, or any other metal or mineral that has economic value The key point is that for a material to be considered ore, it must be economically viable to extract its componentsUnderstanding the Definition of Ore in Mining and Geology2014年3月1日 1 Introduction The pithead of Ouenza currently stored in stocks currently several thousand tons of iron ore poor These stocks have generated over the years, some negative effects on the environment of the region, these dumps can even be the main source of contamination of soil and surface water or groundwater or water remains a concern for most Study of Electrical Properties of Iron Ore in View of Electrostatic
.jpg)
(PDF) Extraction of Potassium from Feldspar by Roasting with
2021年12月3日 calcite ore was subjected to flotation experiments after comminution, and a calcite concen trate with low iron content was obtained in the first two flotation stages In the following4 天之前 Fluorspar mineral processing is a complex field that requires a variety of methods to extract and refine this valuable mineral One common type is gravity separation, which involves separating fluorspar from other minerals based on differences in densityThis method is costeffective and environmentally friendly, making it a popular choice in fluorspar processingFour Common Types Of Fluorspar Mineral Processing MethodsThe CLRM Enhanced Roller Mill adjusts for calcite powder from 80 to 500 mesh, ideal for materials under Mohs 6 It is energy efficient due to its high transparency, calcite is well suited for the production of materials such as glass, CLRM Enhanced Roller Mill is suitable for crushing 80425 mesh calcite fine powder, Calcite Mastery: From Hardness to Powder Processing Techniques2024年10月14日 Remark: For conversion from millimeter to mesh, please refer to mm to mesh Process 3: Calcinating dolomite rock The crushed dolomite is calcined in a rotary kiln, which is used for producing refractory materials, magnesium alloys, cement, etc Dolomite is calcined at 1500°C to obtain magnesiacalcium raw materials, such as dolomite sand, magnesiacalcium How to Process Dolomite Rock and What Is It Used for?
.jpg)
Correlation of crushing work index and dropweight
Ore hardness can be estimated using commercially available standard techniques such as the SAG Power Index (SPI), Bond Work Index (BWI), and JK Drop Weight (JKDW) tests (Bailey et al, 2009 2021年8月13日 The value of the width of the discharge port is S: Because the ore before and after crushing is different in size and shape, which reduces investment costs, has good grain shape and high neatness, and is favored by users Related Newsmore >> Bauma China 2024 Event Recap: Exploring What is the crushing ratio of the crusher?2022年1月1日 Turning to iron ore exports and imports, the tonnages are summarized in Table 11 for 2012 and 2018 (Australian Department of Industry, Science, Energy and Resources, 2021; US Geological Survey, 2020; United National Conference on Trade and Development (UNCTAD), 2021)As shown in Fig 13, China is the largest iron ore importing country and imported about Introduction: Overview of the global iron ore industry2018年11月1日 Since the production of mineral aggregates should ensure the standardized, highquality requirements of the final product, rockcrushing mechanisms should be investigated in a detailed manner(PDF) New testing methodology for the quantification of rock
.jpg)
Dolomite Crushing Process And Grinding Equipment
2024年3月12日 The equipment can form an independent and complete production system with strong systematicity, from the crushing, conveying, and powdermaking to the collection, storage, and packaging of finished products The grinding machine can process highquality powder with a mesh size of 325 to 3000, widely used in ultrafine crushing processing2019年9月24日 Although ore variability is frequently debated as a major source of uncertainty in process performance, most of the current ore testing methods do not capture this variability and plant designs Simulating the Impact of Ore Competence Variability on Process 2015年1月1日 Like other sintering processes, iron ore sintering converts iron ore fines of often − 8 mm sizing into larger agglomerates, namely, sinter, between 5 and 50 mm particle size, which possess the physical and metallurgical characteristics and gas permeability required for efficient blast furnace operationAs shown in Figure 141, iron ore sintering is carried out in three Iron ore sintering ScienceDirect2009年5月1日 The work index covering grinding in tumbling mills of coarse sizes is labelled M iaThe work index covering grinding of fine particles is labelled M ib M ia values are provided as a standard output from a SMC Test ® (Morrell, 2004a) whilst M ib values can be determined using the data generated by a conventional Bond ball mill work index test (M ib is NOT the Bond ball Predicting the overall specific energy requirement of crushing, high
.jpg)
Table of Bond Work Index by Minerals 911Metallurgist
2015年6月19日 This Table of Ball Mill Bond Work Index of Minerals is a summary as tested on 'around the world sample' You can find the SG of each mineral samples on thea Lump ore: a natural ore that is not selected by manual enrichment, with the grade of about 60% Since lump ore is raw ore, the proportion ores in blast furnace shouldn’t be too high, with a ratio of around 11% b Pellet: to produce a greenball with balanced viscosity and high intensity by adding certain water and binder to ore finesGeneral Introduction to Iron Ore I What is Iron Ore II founderfu2015年1月1日 Iron ore is the primary raw material from which metallic iron is extracted to make steel The rapid increase in crude steel production in the last decade has seen major expansions in world iron ore production from around 1 billion tonnes (Bt) in 2001 to over 29 Bt in 2012China is the largest iron oreproducing country, producing about 13 Bt in 2012, which accounts for Introduction: overview of the global iron ore industry2023年6月30日 Crushing is the first and most important stage in the preparation of raw materials for further processing The quality of the following processing stages (crushing, flotation,Modeling and Improving the Efficiency of Crushing
.jpg)
Predicting the overall specific energy requirement of crushing, high
takes the value of 119 x1 = P80 in microns of the circuit feed x2 = P80 in microns of the circuit product Mic = Crushing ore work index and is provided directly by SMC Test ® 223 HPGR Equation 1 for HPGRs is written as: (( 2 ) (1)) 3 4 2 1 f x f x Wh = K Mih x − x (8) where K3 = 10 for all HPGRs operating in closed circuit with a 2015年1月1日 However, the gradual increase in gangue minerals in iron ore fines in the last decade due to the depletion of highgrade iron ore resources has resulted in a considerable change in sinter chemistry, in particular alumina content and basicity (Lu et al, 2007)Quality requirements of iron ore for iron production2019年1月1日 Main properties of the processes of iron ore destruction in terms of its simultaneous effect by mechanical load and electric field of ultrahigh frequency have been studiedResearch into the crushing and grinding processes of iron ore Value dynamics: price drivers in the highgrade iron ore segment 6 Drivers of grade differentials 8 Direct charge premiums: lump pellet 9 Concentrates vs sinter fines differentials 10 Highgrade market dynamics in 2020 Looking forward: the future of the highgrade iron ore market 12 Current dynamics and shortterm outlookUnderstanding the highgrade iron ore market Pearl Gull Iron
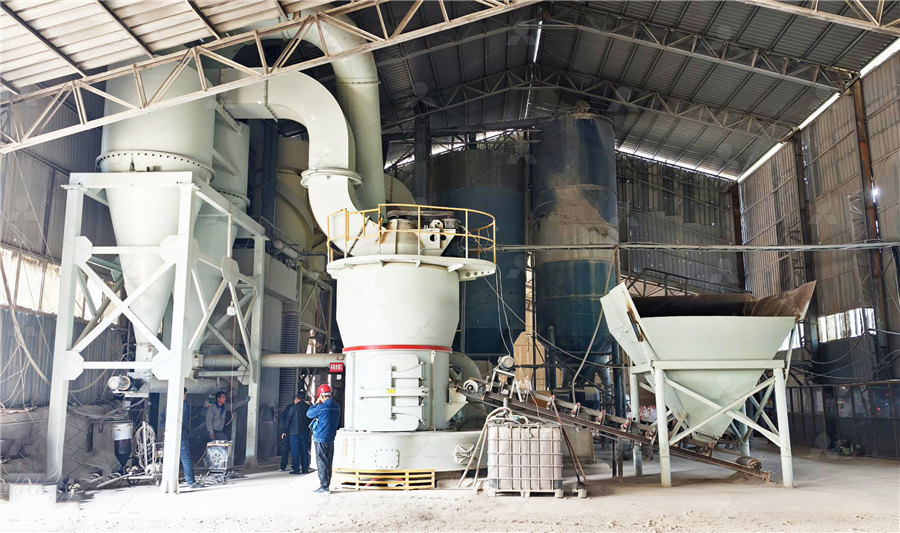
(PDF) The Effect of HPGR and Conventional Crushing on the
2023年10月10日 Comparative high pressure grinding rolls (HPGR) and cone crusher pilotscale tests were conducted using Upper Group 2 (UG2) platinumbearing ore in order to determine the impact of microcracks in 2023年5月12日 1 Crushing: Use a jaw crusher, roll crusher, and vibrating screen to form a twostageclosed circuit crushing system to crush the raw magnesite ore to 1mm 2 Calcination: Send the raw ore into a rotary kiln for calcination at a temperature of 700800°C for 1 hour 3 Crushing: Crush the calcined ore with a roll crusher 4 Screening:Magnesite Ore Processing: Separation and CalcinationWilliam Aspdin made what could be called ‘mesoPortland cement‘ (a mix of Portland cement and hydraulic lime)Isaac Charles Johnson further refined the production of ‘mesoPortland cement’ (middle stage of development), and claimed to be the real father of Portland cement In 1859, John Grant of the Metropolitan Board of Works, set out requirements for cement to be used in What is the manufacturing process of Portland Cement?2023年4月21日 Calcite processing involves various steps such as crushing, grinding, and classification The process is used to produce highquality calcite powder that is used in various industries such as construction, agriculture, and pharmaceuticals The process also involves the removal of impurities to ensure that the final product is of high purityCalcite Processing SBM Mill Crusher
.jpg)
A Review on the Prediction and Assessment of
2021年9月22日 The influence of intact rock properties on powder factor selection and the influence of powder factor selection on postblast conditions have also been discussed2022年12月27日 The production of calcite powder is mainly divided into four steps: crushing, grinding, grading and powder collection +29 The added value of the product is relatively high, but the energy consumption is relatively high the delivery is done by the miner The main requirements for calcite ore transportation are: How To Make Calcite Powder?Calcite powder is a natural form of calcium carbonate with extremely high whiteness, purity and free flowing in nature Calcite powder and coated calcite powder has a pivotal role in the modern industrial like plastic, paint, cosmetic, paper, PVC pipe etc Calcite Ore Crushing Solutions DSMAC2023年2月15日 21 Fluoritecalcite type ore The fluoritecalcite type ore is mainly composed of fluorite and calcite (with a content of more than 30%) Under alkaline condition, calcite is easy to be floated But under acid condition, the flotation condition of calcite is greatly reduced4 Steps to Process Complex Lowgrade Fluorite Ore
.jpg)
Understanding the Definition of Ore in Mining and Geology
In the simplest terms, ore is a naturally occurring solid material from which a metal or valuable mineral can be extracted profitably An ore deposit could contain lead, gold, copper, or any other metal or mineral that has economic value The key point is that for a material to be considered ore, it must be economically viable to extract its components2014年3月1日 1 Introduction The pithead of Ouenza currently stored in stocks currently several thousand tons of iron ore poor These stocks have generated over the years, some negative effects on the environment of the region, these dumps can even be the main source of contamination of soil and surface water or groundwater or water remains a concern for most Study of Electrical Properties of Iron Ore in View of Electrostatic 2021年12月3日 calcite ore was subjected to flotation experiments after comminution, and a calcite concen trate with low iron content was obtained in the first two flotation stages In the following(PDF) Extraction of Potassium from Feldspar by Roasting with 4 天之前 Fluorspar mineral processing is a complex field that requires a variety of methods to extract and refine this valuable mineral One common type is gravity separation, which involves separating fluorspar from other minerals based on differences in densityThis method is costeffective and environmentally friendly, making it a popular choice in fluorspar processingFour Common Types Of Fluorspar Mineral Processing Methods
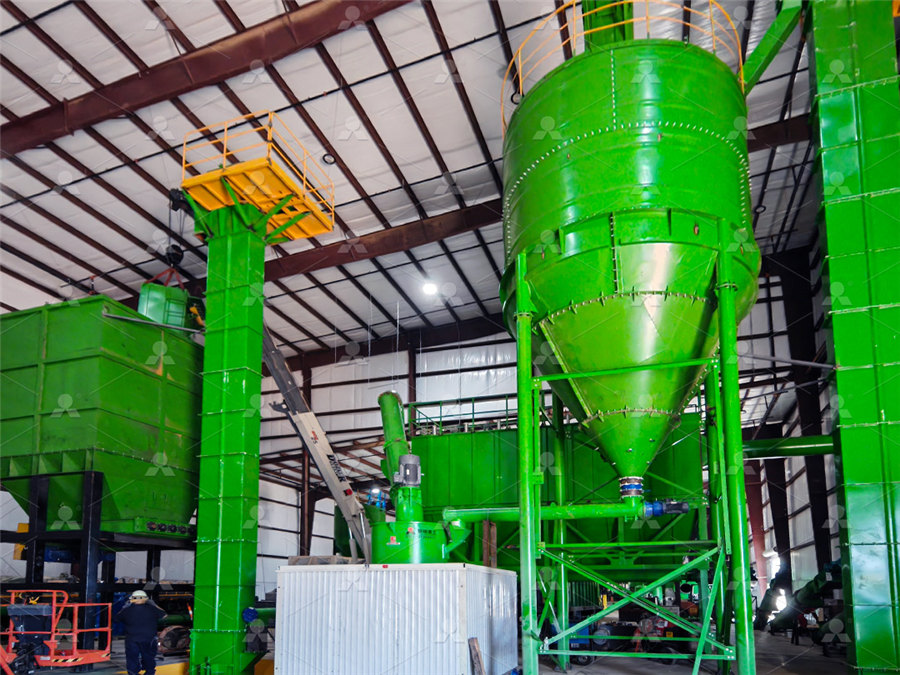
Calcite Mastery: From Hardness to Powder Processing Techniques
The CLRM Enhanced Roller Mill adjusts for calcite powder from 80 to 500 mesh, ideal for materials under Mohs 6 It is energy efficient due to its high transparency, calcite is well suited for the production of materials such as glass, CLRM Enhanced Roller Mill is suitable for crushing 80425 mesh calcite fine powder, 2024年10月14日 Remark: For conversion from millimeter to mesh, please refer to mm to mesh Process 3: Calcinating dolomite rock The crushed dolomite is calcined in a rotary kiln, which is used for producing refractory materials, magnesium alloys, cement, etc Dolomite is calcined at 1500°C to obtain magnesiacalcium raw materials, such as dolomite sand, magnesiacalcium How to Process Dolomite Rock and What Is It Used for?