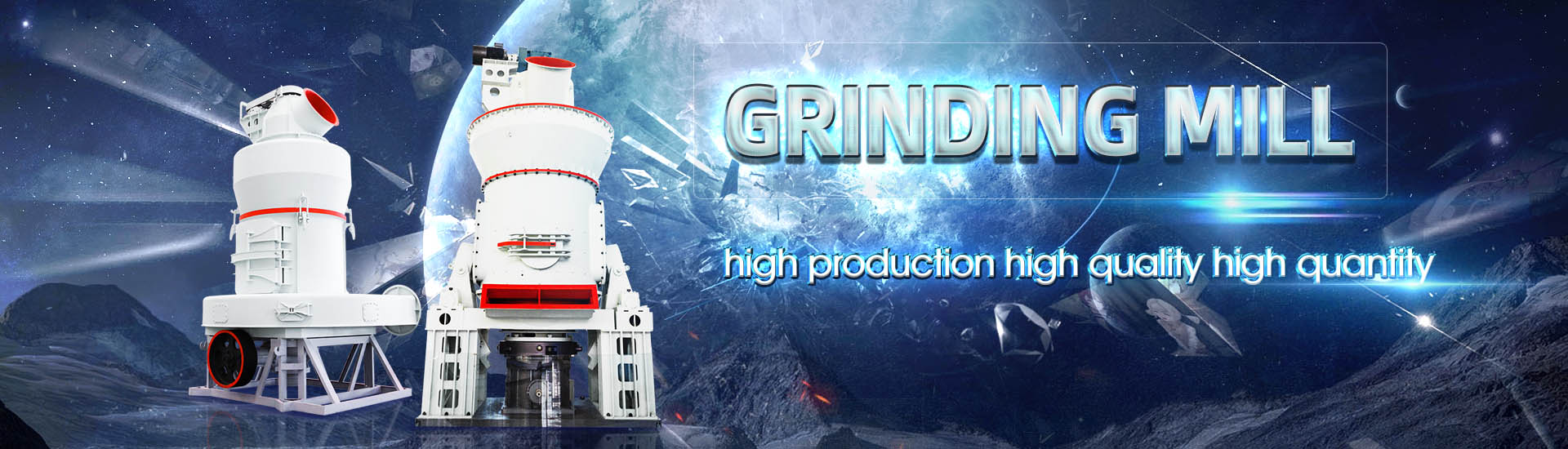
Blast furnace coal mill
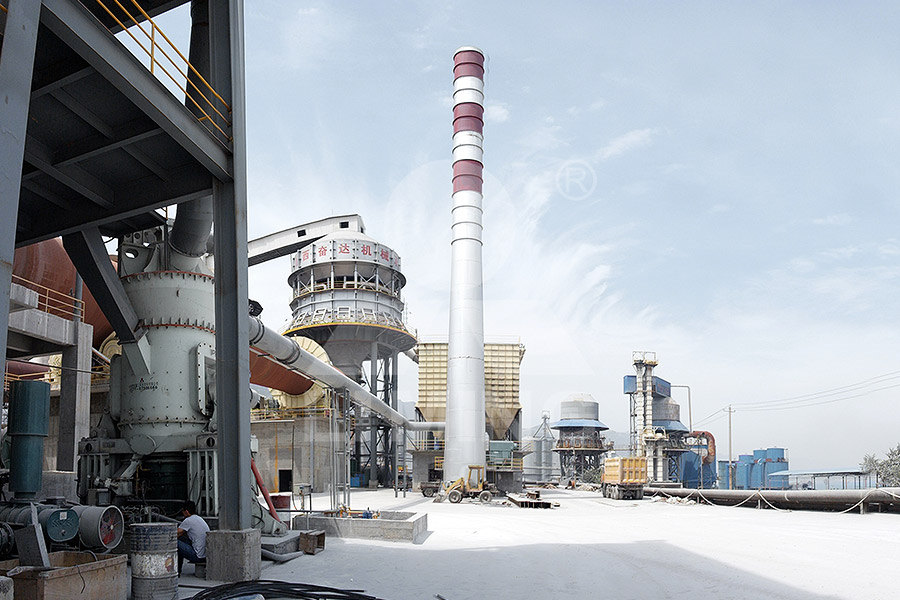
Impact of PCI Coal Quality on Blast Furnace Operations
Blast Furnace Operation The injected coal quality can influence the quality of the hot metal, stability of the blast furnace and top gas composition The ash from the injected can act as an The typical blast furnace gas composition in volume is N 2 = 5519%, CO = 2078%, CO 2 = 2127% and H 2 = 276% (Hou et al, 2011) The water content is removed by demisters Blast Furnace an overview ScienceDirect Topics2003年1月1日 Pulverized coal injection has assisted the steel industry to lower operating costs, extend coke oven life and lower greenhouse emissions As the understanding of the impact of quality of theImpact of PCI Coal Quality on Blast Furnace Operations The blast furnace uses coke, iron ore and limestone to produce pig iron Coal traditionally has been a key part of the cokemaking process The coal is crushed and ground into a powder and then charged into an oven where it is heated to Steel Production American Iron and Steel Institute
.jpg)
Use of PCI in blast furnaces ICSC
producers utilising PCI coal at higher consumption rates will drive the demand for PCI coal New BFs will be preferred over scrapbased minimills wherever steel demand is large, scrap is unavailable, iron ore and coal are available, and 2024年8月6日 In an integrated steel plant, the pulverized coal injection (PCI) mill plays an important role in providing pulverized coal to the blast furnace The main purpose of using PCI Failure Analysis of Pulverized Coal Injection (PCI) Mill Grinding 2015年7月1日 Coal injection in the blast furnace is understood to reduce the consumption of expensive coking coals, increase productivity, increase flexibility in operation, improve the Opportunities to improve the utilisation of granulated coals for The oxygen in the hot blast reacts with the coke and pulverized coal in the belly and bosh of the blast furnace (raceway) to form a mixture of carbon monoxide and nitrogen This gas mixture Blast Furnace Process an overview ScienceDirect Topics
.jpg)
Suitability of pulverised coal testing facilities for blast furnace
2019年1月20日 Identifying coals suitable for blast furnace injection has become increasingly important due to rising injection rates This review of traditional pulverised coal reactivity 2020年11月16日 The reheating furnace of the steel industry was evaluated in the present study, which uses the gas mixture from coke oven (COG), steelmaking process “LinzDonawitz” (LDG) and blast furnace (BFG)(PDF) REHEATING FURNACES IN THE STEEL INDUSTRY 2023年3月13日 Liberty began to pay for raw materials and transportation fees and has already supplied 40,000 mt of coal to the mill Serbia HBIS Serbia continued to operate one furnace after its blast furnace No 1, which has a Back in action: European mills restart idled blast HEADTOHEAD: Blast Furnace Vs Electric Arc Furnace Comparing Greenhouse Gas Emissions Intensity for Steelmaking The difference in inputs and processes between the BFBOF (extractive) and EAF (circular) How to Make Steel: Blast Furnace Vs Electric Arc
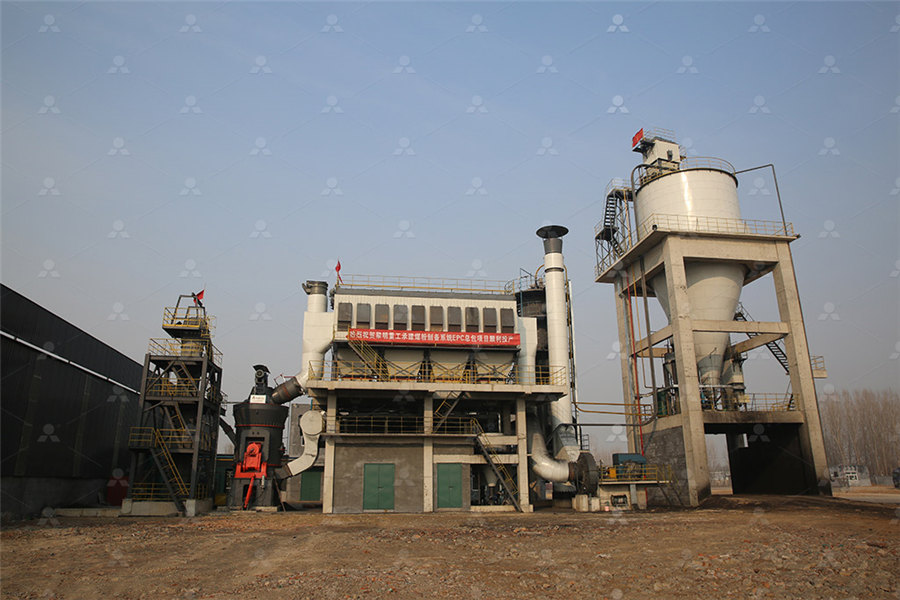
3A2 Pulverized Coal Injection for Blast Furnaces (PCI)
Steel works, blast furnace Coal dust ratio kg/t Coke ratio kg/t Reducing material ratio kg/t Tapping ratio t/d/m3 Maximum pulverized coal ratio (PCR) Minimum coke ratio (CR) Minimum reducing material ratio (RAR) Maximum tapping ratio 6/98 3/99 3/94 1/97 Fukuyama No 3 blast furnace Kobe No 3 blast furnace Oita No 1 blast furnace Nagoya No 1 Ciments Lafarge, France, as the first mill for grinding granulated blast furnace slag 1999 The first LM 562+2 was installed at Cementos Pacasmayo in Peru 2004 The 50th Loesche mill with 2+2 technology The springloaded roller grinding mill for grinding coal was intro duced by Loesche in the 1920’s Since the end of the 1930’s2 µm 5 µm LoescheLump ore, however, usually comprises a minor portion of the total ferrous feed Coal cannot be directly charged via the furnace top, it must first be transformed to coke Blast furnace gas is produced from the blast furnace in a steel mill This gas has 23% of carbon monoxide, 60% of nitrogen, and 14% of carbon dioxide The heating value is Blast Furnace an overview ScienceDirect Topicsare based on virgin raw materials, like oxydic iron ores and reductants like coal, oil HM ex blast furnace [ Mill t / y ] 0 20 40 60 80 100 120 DRI production [ Mill t / y ], BOF BOFNEW IRONMAKING TECHNOLOGIES: WILL THE DOMINANCE OF THE BLAST FURNACE
.jpg)
Global Steel Plant Tracker Global Energy Monitor
Iron and steel are typically produced through coalbased methods (blast furnace and basic oxygen furnace or open hearth furnace) or electricitybased production Details on blast furnace units at plants in the GSPT can be found in the Global Blast Furnace TrackerAccording to statistics, in 2021, China's annual energy consumption reached 524 billion tons of standard coal, of which coal resource consumption accounts for 560% of total energy consumption [2,3]Mass and energy balance in an integrated steel mill (baseline blast Global Blast Furnace Tracker The Global Blast Furnace Tracker (GBFT) is a worldwide dataset of blast furnace units It tracks each of the furnaces at iron and steel plants in GEM’s Global Steel Plant Tracker (GSPT), which includes plants with a crude iron or steel capacity of 500 thousand tonnes per annum (ttpa) or more, as well as those that have been proposed or under Global Blast Furnace Tracker Global Energy MonitorBlast Furnaces : 6 Nos 1 Blast furnaces of 1033 cum useful volum; 3 Blast furnaces each of 1719 cum useful volum; 1 Blast furnace of 2355cum useful volum; 1 Blast furnace of 4060 cum useful volume (BF 8 : MODEX Unit) Sintering Plants : 2 Nos SP2 : 3x75sqm hearth area and1x80sqm hearth areaFacilities SAIL
.jpg)
Pulverized Coal Injection Paul Wurth
Grinding and Drying of Coal in Inert Conditions Blast Furnace Gas Based Drying Blast Furnace Gas Based Drying, Dilution Air Drying energy supply based on blast furnace gas combustion Inert conditions produced by closed loop circulation of waste drying gas as a dilution gas for drying gas temperature control (self inertizing process)BLAST FURNACE MODELING An implementation of Rist and Meysson (1967) blast furnace process model was used to investigate the impact of PCI coal quality on the operation of a blast furnace This model examines: The fuel rate which closely relates to the heat balance in the lower part of the furnace and gas (indirect) reduction rate at the shaftImpact of PCI Coal Quality on Blast Furnace OperationsIn November 2011 Loesche GmbH obtained a contract for the first ever 4roller coal mill for the injection of pulverized coal into a blast furnace (PCI technology) The Loesche Mill Type LM 434 D has a capacity of 120 t/h and will be installed in the iron and steel plant of SSI Redcar in Great Britain This will be, together with the Loesche A coal mill for the injection of pulverized coal2024年8月30日 Algoma’s Electric Arc Furnace conversion project Modern blast furnaces use coke, or purified coal, to melt iron ore and create pig iron Oxygen is then injected into the furnace, to reduce the Algoma Steel is banking on a renaissance with its multimillion
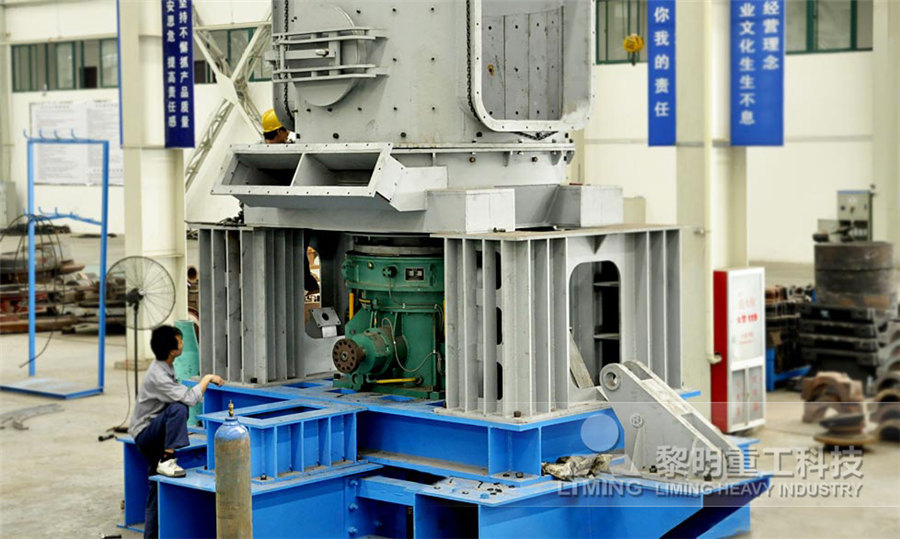
How 'Betsy' the blast furnace helped Pueblo become the `Steel
2020年8月30日 “The blast furnace was christened ’Betsy’ in honor of the superintendent’s daughter,” Miller explained “It was designed to yield 80 tons of iron daily, and the initial tap of 12 tons 2015年1月20日 In August of 2013, the Novolipetsk Metallurgical Combine (NLMK) began hot tests of a complex designed to prepare pulverizedcoal fuel (PCF) and inject it into its 3200m 3 blast furnace No 5 The working specifications for the complex were drawn up by the companies Lipetskii Gipromez and Metpromproekt with the use of base engineering done by the Paul Initial Results from the Use of PulverizedCoal Fuel in Blast Furnaces 2024年12月3日 Blast furnaces produce pig iron from iron ore by the reducing action of carbon (supplied as coke) at a high temperature in the presence of a fluxing agent such as limestoneIronmaking blast furnaces consist of several zones: a crucibleshaped hearth at the bottom of the furnace; an intermediate zone called a bosh between the hearth and the stack; a Blast furnace Definition, Temperature, Diagrams, Facts2024年11月25日 The oxygen blast furnace (OBF) process has been extensively studied theoretically because of the potentials of promising energy conservation and CO 2 emission reduction [74] This type may be the most suitable for use with CCS [73] The main blast furnace has of three levels; the reduction zone (523–973 K (250–700 °C; 482–1,292 °F)), slag Blast furnace WikiMili, The Best Wikipedia Reader
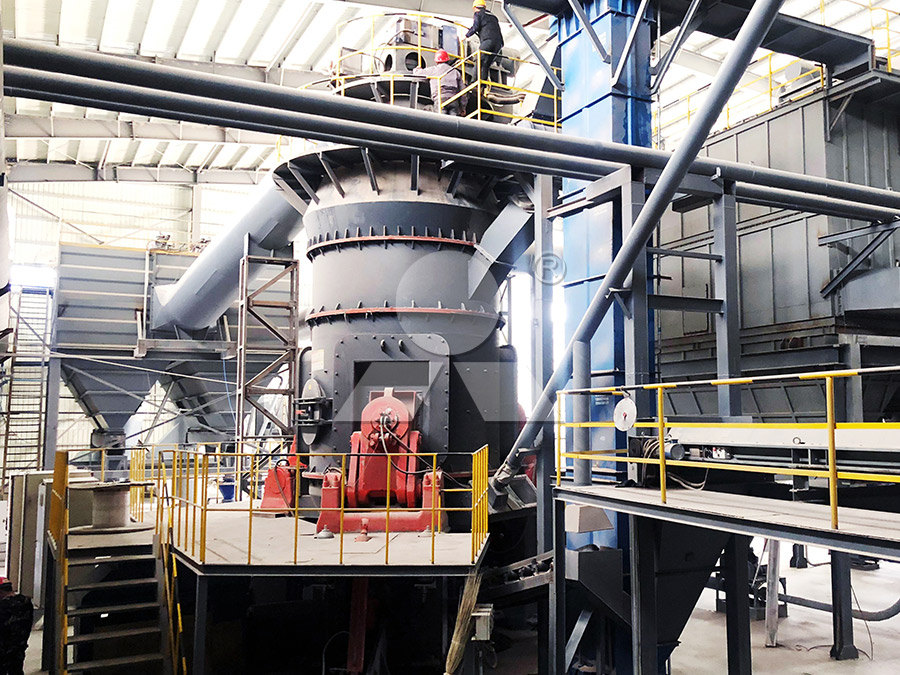
Pulverized Coal Injection of Blast Furnace Ironmaking
2024年1月1日 The blast furnace injection process system is mainly composed of raw coal storage and transportation system, dry gas preparation system, pulverized coal preparation system, pulverized coal conveying system, pulverized coal injection system, and gas supply system (Fig 1)There is also a computer control center to control the entire pulverized coal 2023年9月5日 High costs and environmental opposition have prevented the construction of blast furnaces at steel mills in the United States since 1980 ClevelandCliffs Inc CEO Lourenco Goncalves is on a Focus: Inside ClevelandCliffs' bid to keep US blast Before being utilized in blast furnaces, coal picked up from parks and properly mixed go through a distillation process that transform them into carbon coke, that are then used in blast furnace for the creation of cast iron from the iron Products EN Acciaierie d'ItaliaThe Blast furnace performs a similar function to the Smelter, although it cannot smelt the ores that the Smelter can The Blast furnace is used to process certain raw materials into Metal using Coal as fuel Materials that can be smelted are: Black metal scrap Flametal ore The Blast furnace uses approximately 1 Coal every 15 seconds as fuel It takes 30 seconds[1] to produce one bar of Blast furnace Valheim Wiki
.jpg)
Blast Furnace Islands Wiki
The blast furnace is a heating device used to convert iron into steel ingots Blast furnaces can be used to smelt iron ingots into steel ingots It has a total of 3 slots able to hold 50 items each — two slots on the top left for the item to be smelted, and one in the bottom row for fuel When powered with coal or petrified petroleum, the blast furnace will activate for approximately 20 blast furnace construction Modernisation 06 07 stockhouse charging systems 08 09 blast furnace top charging technology – the original 10 11 blast furnace Design: the blast furnace Proper, lining cooling 12 13 hot blast generation supply 14 15 Puvlesried c oal nIej ction 16 17 gas cleaning and energy recovery 18 19BLAST FURNACE TECHNOLOGY Paul Wurth2012年1月1日 Blast furnaces produce up to 53 mill t/y, A blast furnace model is used to calculate the decrease of coke rate under constant coal injection rate and constant coke consumption with New ironmaking technologies: Will the dominance of the blast furnace 2022年8月25日 The average compound growth rate for basic oxygen furnace (BOF) technology in Southeast Asia was 32% over 20112020, Seaisi said It forecasts a 25% rate over 20202026 But for electricarc furnace (EAF) technology, the growth rate was 5% over 20112020, and is expected to be 1% from 20202026Southeast Asia’s blast furnace capacity set for 25% growth
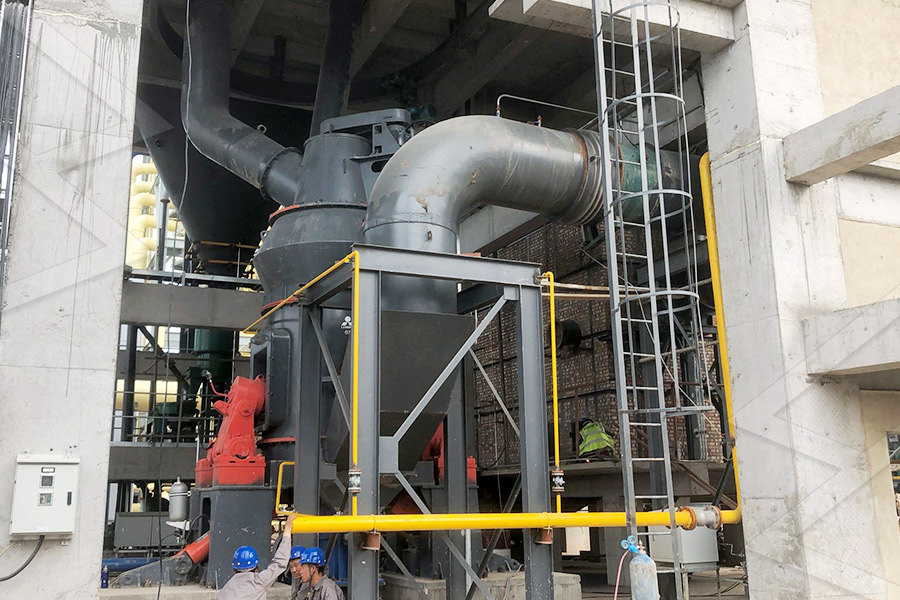
Wealden iron industry Wikipedia
Cast iron railings for St Paul's Cathedral, now in the Victoria Albert Museum The Wealden iron industry was located in the Weald of southeastern EnglandIt was formerly an important industry, producing a large proportion of the bar iron made in England in the 16th century and most British cannon until about 1770 Ironmaking in the Weald used ironstone from various clay beds, and Originally fueled by charcoal, the furnace with its thirtyfoot stack, produced approximately three to four tons of iron each day In the 1840′s, the Mill Creek Furnace was rebuilt to burn bituminous coal The Mill Creek Furnace went out of blast in the late 1840s or early 1850sHistoric Structures Sites – Mill Creek MetroParksRequest PDF On Jul 1, 2011, SS Hou and others published Firing blast furnace gas without support fuel in steel mill boilers Find, read and cite all the research you need on ResearchGateFiring blast furnace gas without support fuel in steel mill boilers2020年11月16日 The reheating furnace of the steel industry was evaluated in the present study, which uses the gas mixture from coke oven (COG), steelmaking process “LinzDonawitz” (LDG) and blast furnace (BFG)(PDF) REHEATING FURNACES IN THE STEEL INDUSTRY
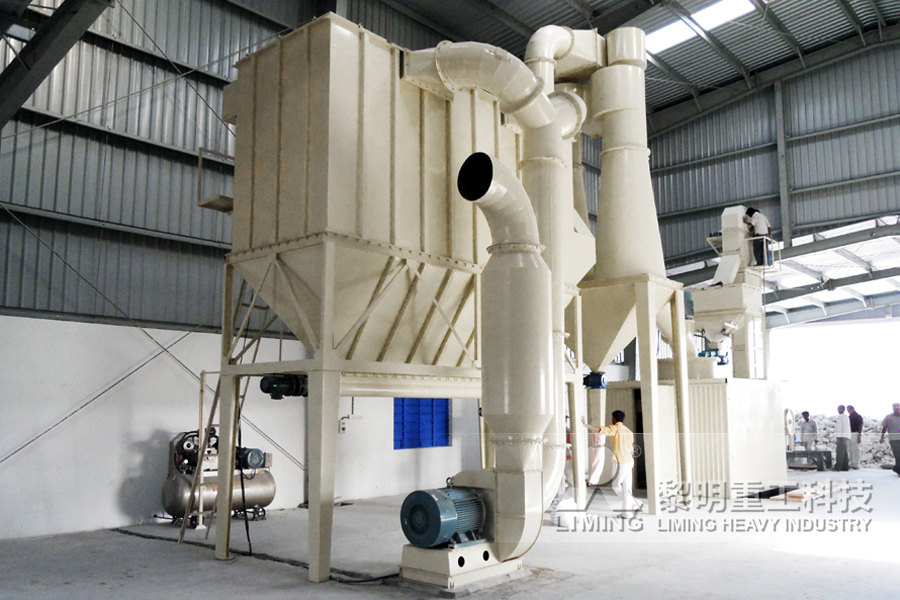
Back in action: European mills restart idled blast
2023年3月13日 Liberty began to pay for raw materials and transportation fees and has already supplied 40,000 mt of coal to the mill Serbia HBIS Serbia continued to operate one furnace after its blast furnace No 1, which has a HEADTOHEAD: Blast Furnace Vs Electric Arc Furnace Comparing Greenhouse Gas Emissions Intensity for Steelmaking The difference in inputs and processes between the BFBOF (extractive) and EAF (circular) How to Make Steel: Blast Furnace Vs Electric Arc Steel works, blast furnace Coal dust ratio kg/t Coke ratio kg/t Reducing material ratio kg/t Tapping ratio t/d/m3 Maximum pulverized coal ratio (PCR) Minimum coke ratio (CR) Minimum reducing material ratio (RAR) Maximum tapping ratio 6/98 3/99 3/94 1/97 Fukuyama No 3 blast furnace Kobe No 3 blast furnace Oita No 1 blast furnace Nagoya No 1 3A2 Pulverized Coal Injection for Blast Furnaces (PCI)Ciments Lafarge, France, as the first mill for grinding granulated blast furnace slag 1999 The first LM 562+2 was installed at Cementos Pacasmayo in Peru 2004 The 50th Loesche mill with 2+2 technology The springloaded roller grinding mill for grinding coal was intro duced by Loesche in the 1920’s Since the end of the 1930’s2 µm 5 µm Loesche
.jpg)
Blast Furnace an overview ScienceDirect Topics
Lump ore, however, usually comprises a minor portion of the total ferrous feed Coal cannot be directly charged via the furnace top, it must first be transformed to coke Blast furnace gas is produced from the blast furnace in a steel mill This gas has 23% of carbon monoxide, 60% of nitrogen, and 14% of carbon dioxide The heating value is are based on virgin raw materials, like oxydic iron ores and reductants like coal, oil HM ex blast furnace [ Mill t / y ] 0 20 40 60 80 100 120 DRI production [ Mill t / y ], BOF BOFNEW IRONMAKING TECHNOLOGIES: WILL THE DOMINANCE OF THE BLAST FURNACEIron and steel are typically produced through coalbased methods (blast furnace and basic oxygen furnace or open hearth furnace) or electricitybased production Details on blast furnace units at plants in the GSPT can be found in the Global Blast Furnace TrackerGlobal Steel Plant Tracker Global Energy MonitorAccording to statistics, in 2021, China's annual energy consumption reached 524 billion tons of standard coal, of which coal resource consumption accounts for 560% of total energy consumption [2,3]Mass and energy balance in an integrated steel mill (baseline blast
.jpg)
Global Blast Furnace Tracker Global Energy Monitor
Global Blast Furnace Tracker The Global Blast Furnace Tracker (GBFT) is a worldwide dataset of blast furnace units It tracks each of the furnaces at iron and steel plants in GEM’s Global Steel Plant Tracker (GSPT), which includes plants with a crude iron or steel capacity of 500 thousand tonnes per annum (ttpa) or more, as well as those that have been proposed or under