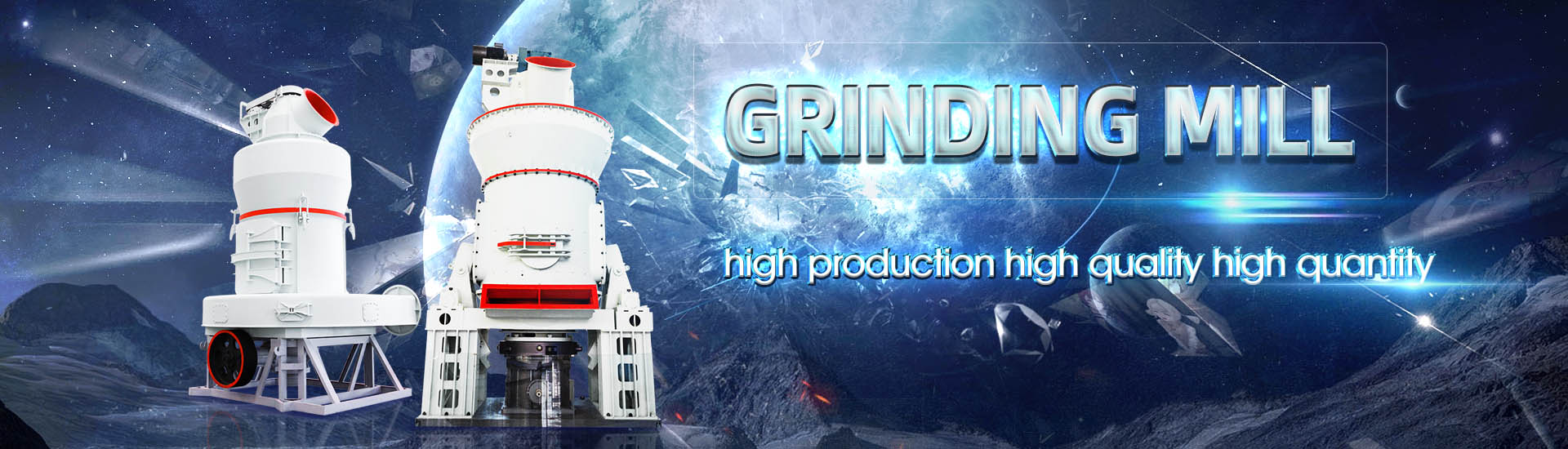
How to increase production by less hole blasting
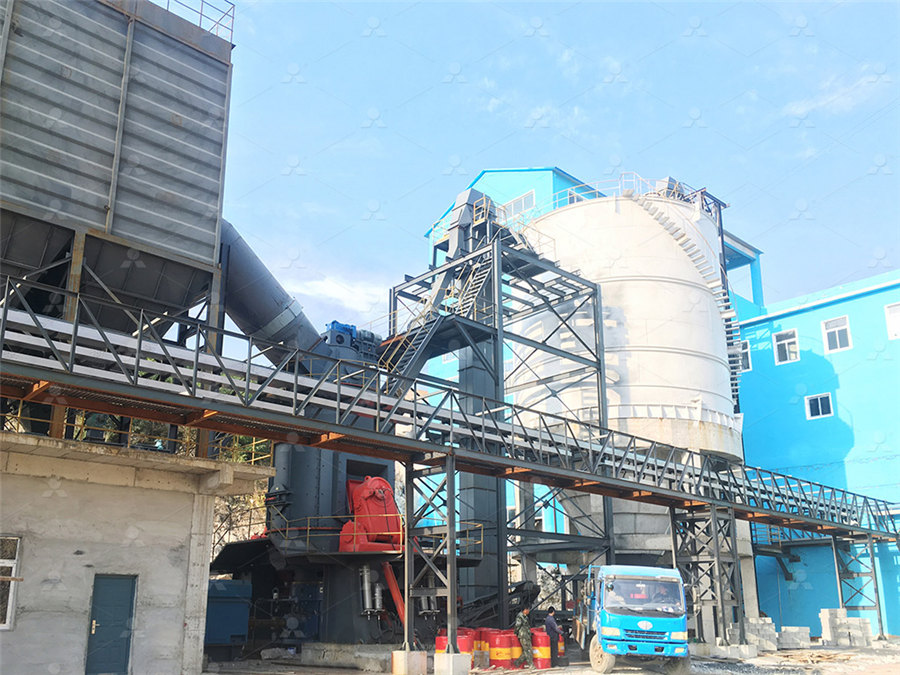
Optimization of the drillingandblasting process to improve
In most of the cases, the cheapest way to improve the fragmentation of the ore is by changing the drillingandblasting design parameters It of course increases the mining costs, but at the 2022年5月11日 Modifying parameters such as the firing sequence, drill diameter, hole spacing, burden, and explosive charge size, as well as decoupling the blast holes and even leaving Presplit blasting design to reduce costs and improve safety in 2021年10月22日 Optimal delay time can not only induce the seismic waves which produced by the adjacent holes interfered with each other to reduce the blasting vibration effect, at the Experimental Study on Vibration Reduction Technology of Holeby 2024年4月23日 Applying the novel proposed procedure for a cutcavity formation will increase the blasthole use coefficient and reduce the cost of drilling and blasting operations Moreover, the procedure may also be practical for Frontiers Using sectional blasting to improve the
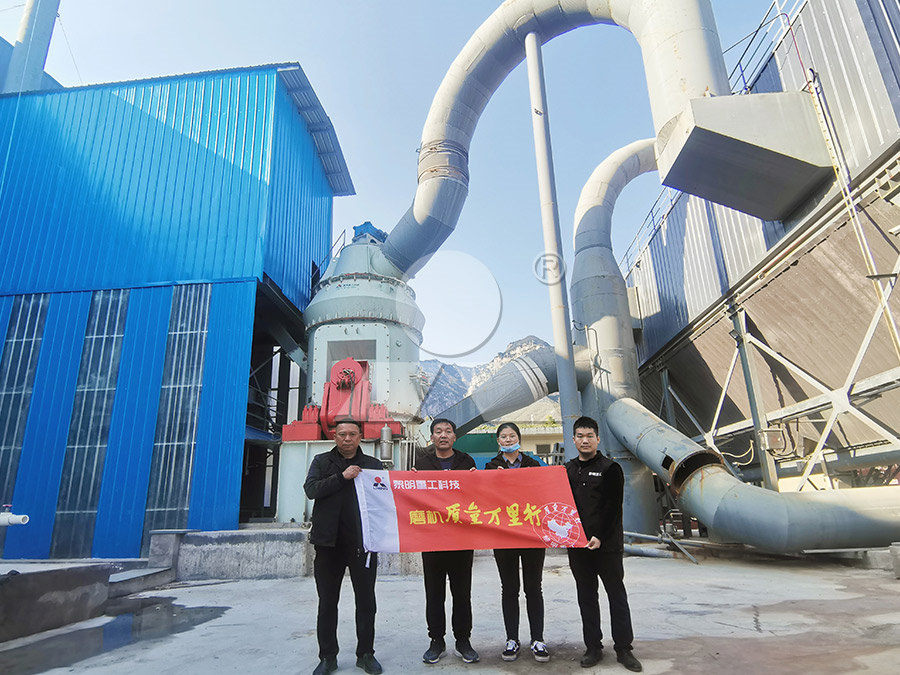
Reduction of Fragment Size from Mining to Mineral Processing: A
2022年10月4日 The main measures for achieving an optimum fragmentation by blasting are to increase the specific charge in blasting while avoiding misfires and to improve the energy 2018年11月1日 Bowa introduced a practical method in an open pit mine to optimize blasting design parameters such as bench height, drill hole diameter, spacing, etc [5] Tosun and Optimized design of drilling and blasting operations in open pit 2024年10月1日 Drilling and blasting techniques are employed in both surface and underground mining to optimize profitability and reduce production expenditures Obtaining the desired Enhancing blasting efficiency: A smart predictive model for cost 2021年10月13日 In engineering practice, the deep hole presplitting blasting permeability increasing technology can produce multiple cracks in the coal body of a low permeability coal Study on the technology of enhancing permeability by deep hole
G[R.jpg)
Research on Optimization of an OpenBench Deep
2024年4月22日 By enhancing the Gray Wolf algorithm, the parameters for step drilling and blasting are optimized, resulting in improved effectiveness for step blasting mining, as demonstrated through modeling and calculationPDF On Jun 9, 2008, Zongxian Zhang published Impact of rock blasting on mining engineering Find, read and cite all the research you need on ResearchGateImpact of rock blasting on mining engineering2009年12月17日 4 Sublevel stopping with Long Blast Holes: Demand for increased rate of production coupled with improvement in drilling technique has lead to the use of long hole blasting for ore extraction from Underground Metal Mines Blasting PPT SlideShare2023年10月24日 The fundamental principles of blasting are closely tied to hole diameter and burden, forming the foundation of the initial design process The following guide outlines the design process: Calculate the linear charge mass HighLevel Blast Design Basics ERG Industrial
.jpg)
Productivity Improvement in Underground Coal Mines A Case
2013年1月1日 The different mining operations in an underground coal mine include, dewatering, dressing and supporting of face, drilling of blast holes at the coal face, charging, stemming and blasting explosives at face, fume clearance after blasting, loading of coal at the face using loaders and conveying coal to the bunker by conveyor belts etc Productivity improvement through 30% in total explosives required for production blasting With the increased pressure on operators in large volume operations to reduce blasting costs, potential savings of this At the top (or "collar") of the hole, there is much less vertical constriction, so it follows that considerably less explosive energy isDESIGN AND APPLICATION OF AIR DECKS IN SURFACE BLASTING 2022年1月1日 The hole burden and spaci ng depend on the sensitivity o f the Explosiv e, the inclination of the misfired hole, and the diameter o f the hole 2 The relieving hole must be parall el to the Blasting Misfire: A Review of Causes, Economic Effect, Control and 2016年11月23日 For successful blasting, maximum hole deviation should not exceed 025 m (10″) Excavation via the long hole method starts by drilling the blastholes to the total whole length of the raise from the top level and later firing the blasts in stages from the bottomup with hanging charges Usually, a relief hole with larger diameter (100–200 mm Introduction to Underground Excavation by Drilling and Blasting
.jpg)
Blast design of production holes along with buffer row and pre
Download scientific diagram Blast design of production holes along with buffer row and presplit holes from publication: Controlled blasting for long term stability of pitwalls Controlled 2023年11月6日 As shown in Figs 16 and 17, for the level of transverse peak stress near the hollow hole, when L is small (L = 1 m, 15 m, 2 m), with the increase of insitu stress, the value of transverse peak Research on the damage characteristics of rock masses based on 2019年2月21日 About this fourpart series In 1963, Pit Quarry published a series of articles on the mechanics of blasting authored by Richard Ash, a longtime professor of mining engineering at the School of Mines Metallurgy at the University of MissouriRolla The content within each article was ahead of its time, putting forth cuttingedge concepts about the mechanics of rock Blasting mechanics: Blasting design standards #Site Title2019年2月1日 The PPV values are recorded during singlehole blasting conducted with a varying charge per delay at different distances The singlehole blasting will generate the vibration waves, where no superimposition of vibration waves will occur With the data of singlehole blasting conducted, regression is performed to find out the scaled distance Modified scaled distance regression analysis approach for
.jpg)
Study on the technology of enhancing permeability by deep hole
Introduction Coal seam gas predrainage technology is considered to be one of the most effective measures to prevent coal mine gas disasters 1 – 6However, with increasing mining depth, the gas pressure of the coal seam increases and the permeability decreases, which seriously affects the gas predrainage effect 7 – 9In engineering practice, the deep hole presplitting blasting fragmentation happen Therefore the distance of the blasting hole is uninformed by measuring it with tapes and marking With marked blasting hole make the Jumbo Drill Operator easier to drill The blasting hole distance is flexible due to the rock strength When the rock is stronger, the distance is narrower Figure 2The rock fragmentation control in long hole blasting – case study 2017年11月12日 Drone acquired data in the beginning of the blast design is rapidly being adopted throughout the mine and quarries blasting arena Some mines and quarries are looking at smart drills to get the complete information loop, to better enhance production and management in the complete blasting cycle Limited amount of data increases standard deviationThe trade secret to improving the loading of BlastHoletherefore produces less consistent fragmentation throughout the whole muckpile Of course, apart from the fragmentation effects, there is a practical reason that the primer should be placed at the bottom of the hole when singlepriming If the hole collapses during The ability to model explosive, blast hole and wholeofblast
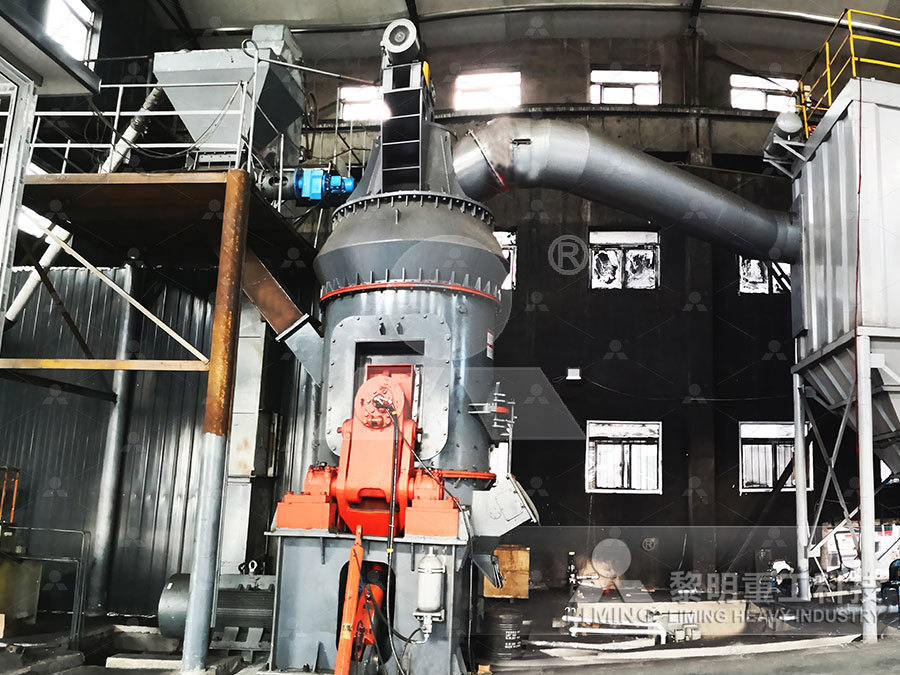
HowTo: Optimize Drilling and Blast Effectiveness Mining Digital
2020年5月17日 In the mining sector, drilling and blasting requires immense knowledge, experience and skill set It’s an art form that takes years to perfect Mining services company Sandvik Mining has launched new software to optimize drilling and blasting, making it easier for miners to streamline the processcally large, 76 127mm in diameter A less common alternative is to use “small hole” openings (several small holes instead of one or two large holes) Small hole opening make it possible to use the same bit size throughout the whole drilling pattern Experience proves that big hole openings give more reliable results than small hole 61 GENERAL2003年1月1日 This study aimed to investigate the blasting efficiency on different geological units in the blasting area using WipFrag fragmentation analyses and to suggest ways to increase of blasting efficiency(PDF) The Effects of Blasting on Crushing and Grinding2019年12月5日 The empty holes not only provide initial space for rock blasting but also convert the stress state around the rock as a free surface After the detonation of the charging hole, the shock wave generated by the explosion quickly attenuates into a stress wave []When the stress wave is transmitted to the empty hole, the reflection phenomenon will occur, leading to the Key Blasting Parameters for Deep‐Hole Excavation in an
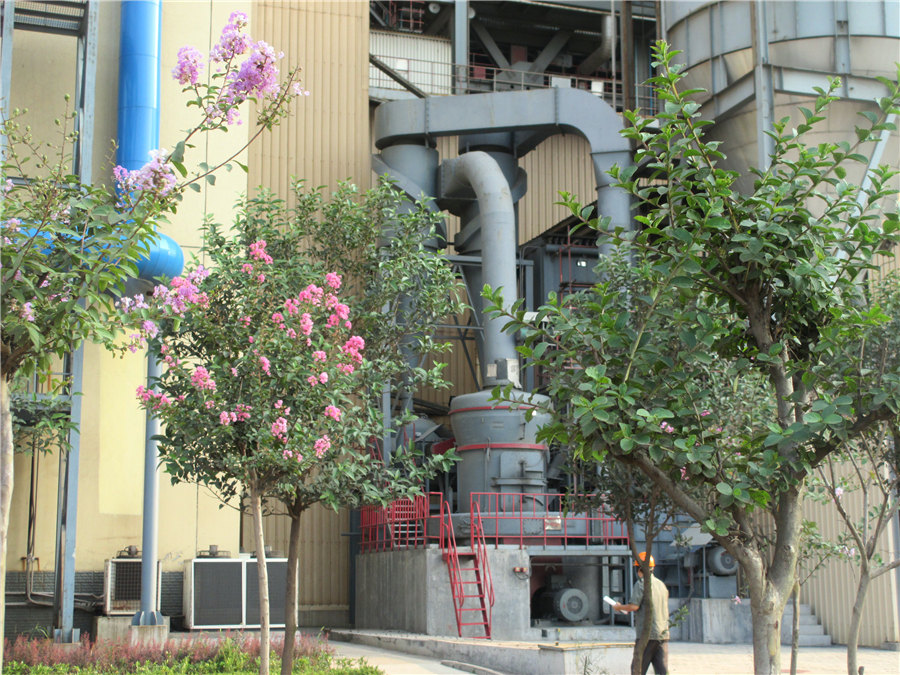
Fines and Dust Generation and Control in Rock Fragmentation by Blasting
Fines produced are less at larger burden of 35 mm and with increase in diameter thus increased decoupling and reducing role of tress waves Further test were carried out with wave trapping, by2016年10月13日 Suez Cement Drilling Calculation Descriptions Symbol Example • Max annual limestone production t 2,500,000 ton • Limestone density d 20 ton/m3 • Max annual limestone production m 1,250,000m3 • Burden × Advanced Drilling Blasting PPT SlideShare2024年1月31日 Some industries that utilise shot blasting in some of their processes are: Automotive – Body panels or engine parts that come through production are cleaned and the surfaces are smoothened through the shot Shot Blasting Explained Definition, Process Moreproduction for a singlehole blast, and creation of unnecessary vibrations This research was performed to eliminate these negative aspects of a signaturehole blast The material blasted consisted of a 22 g/cc density Georgetown limestone Multiple blasts were performed using a signature hole to precede the production blastVibration Reduction Through ProductionSignature Hole Blasting
.jpg)
Blasting and Explosives Quick Reference Guide 2010 Minnesota
Presplit blasting Spacing = Hole diameter x 12 Burden = 05 x production blast burden (B) Uncharged length at top = 10 x D Powder factor = 05kg per square metre of face Do not stem holes Fire all holes on the same delay, or in groups of ≥ 5 holes Smooth Blasting Spacing = 15 x Hole diameter (hard rock) 20 x Hole diameter (soft rock)2006年5月7日 The results indicate that the annual production of 23 minerals has increased by between 1 and 930 times since 1920, similar to the increase in the GDP per capita since 1960Applying fundamental principles of stress waves to production blasting According to [2], ring blasting, bench blasting and vertical crater retreat (VCR) are the three longhole blasting systems in underground operations In all, drilling operation is one of the critical stages of the overall excavation process with a major influence on the efficiency of the downstream processes such as blasting, scaling, loading, hauling and support operationsAn Analysis of Hole Deviation and its Effect on Production2021年10月13日 To reduce gas disasters in low permeability and high gas coal seams and improve gas predrainage efficiency, conventional deep hole presplitting blasting permeability increasing technology was Study on the technology of enhancing permeability by deep hole
.jpg)
Review of predicting the blastinduced ground vibrations to reduce
2020年7月1日 Drilling and blasting is one of the most economical and viable methods of excavation in the field of construction and mining across the globe (Gui et al, 2018)Compared with other technologies such as tunnel boring machines and roadheaders, blasting method is more flexible in dealing with engineering complications due to its advantages such as simple 2018年1月25日 Good Operating Practice Is Key to Mitigating the Problem By Mark S Kuhar E very mining operation has had to deal with damaged drill rods or stalled operations due to drillhole deviation While your choice of equipment can help, good operating practice is the most effective way to mitigate the problemHow To Reduce DrillHole Deviation Rock Products MagazinePDF On Jun 9, 2008, Zongxian Zhang published Impact of rock blasting on mining engineering Find, read and cite all the research you need on ResearchGateImpact of rock blasting on mining engineering2009年12月17日 4 Sublevel stopping with Long Blast Holes: Demand for increased rate of production coupled with improvement in drilling technique has lead to the use of long hole blasting for ore extraction from Underground Metal Mines Blasting PPT SlideShare
.jpg)
HighLevel Blast Design Basics ERG Industrial
2023年10月24日 The fundamental principles of blasting are closely tied to hole diameter and burden, forming the foundation of the initial design process The following guide outlines the design process: Calculate the linear charge mass 2013年1月1日 The different mining operations in an underground coal mine include, dewatering, dressing and supporting of face, drilling of blast holes at the coal face, charging, stemming and blasting explosives at face, fume clearance after blasting, loading of coal at the face using loaders and conveying coal to the bunker by conveyor belts etc Productivity improvement through Productivity Improvement in Underground Coal Mines A Case 30% in total explosives required for production blasting With the increased pressure on operators in large volume operations to reduce blasting costs, potential savings of this At the top (or "collar") of the hole, there is much less vertical constriction, so it follows that considerably less explosive energy isDESIGN AND APPLICATION OF AIR DECKS IN SURFACE BLASTING 2022年1月1日 The hole burden and spaci ng depend on the sensitivity o f the Explosiv e, the inclination of the misfired hole, and the diameter o f the hole 2 The relieving hole must be parall el to the Blasting Misfire: A Review of Causes, Economic Effect, Control and
.jpg)
Introduction to Underground Excavation by Drilling and Blasting
2016年11月23日 For successful blasting, maximum hole deviation should not exceed 025 m (10″) Excavation via the long hole method starts by drilling the blastholes to the total whole length of the raise from the top level and later firing the blasts in stages from the bottomup with hanging charges Usually, a relief hole with larger diameter (100–200 mm Download scientific diagram Blast design of production holes along with buffer row and presplit holes from publication: Controlled blasting for long term stability of pitwalls Controlled Blast design of production holes along with buffer row and pre 2023年11月6日 As shown in Figs 16 and 17, for the level of transverse peak stress near the hollow hole, when L is small (L = 1 m, 15 m, 2 m), with the increase of insitu stress, the value of transverse peak Research on the damage characteristics of rock masses based on 2019年2月21日 About this fourpart series In 1963, Pit Quarry published a series of articles on the mechanics of blasting authored by Richard Ash, a longtime professor of mining engineering at the School of Mines Metallurgy at the University of MissouriRolla The content within each article was ahead of its time, putting forth cuttingedge concepts about the mechanics of rock Blasting mechanics: Blasting design standards #Site Title