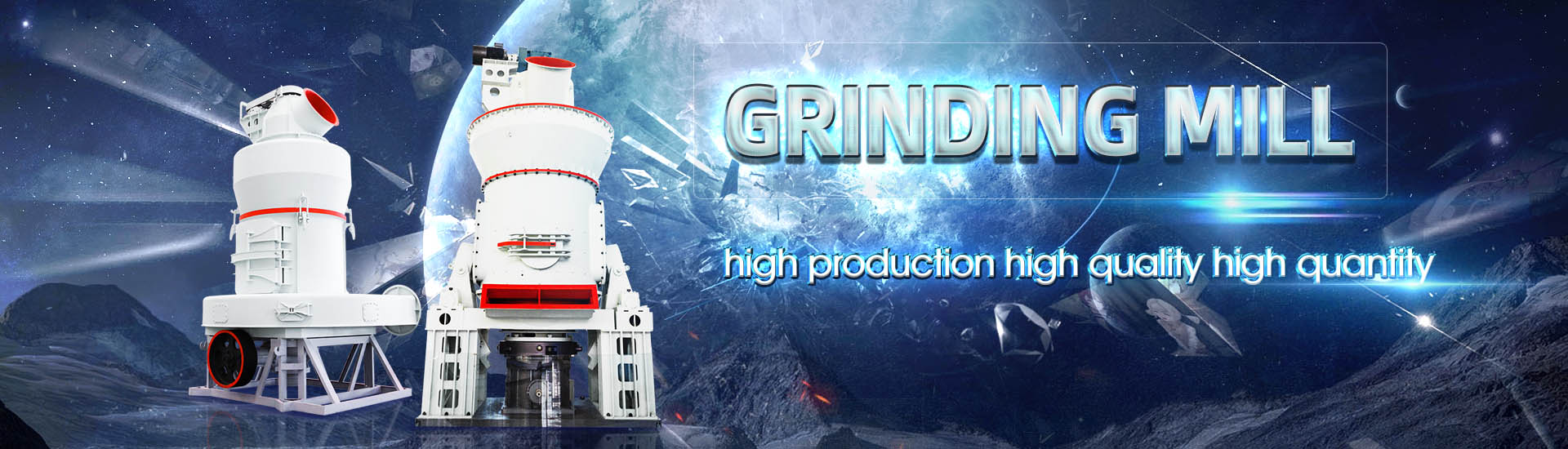
Dry is desulfurization process
.jpg)
Dry Flue Gas Desulfurisation Technology ScienceDirect
2000年7月31日 The primary dry FGD technologies employ either a spray drying process or a circulating fluid bed (CFB) process The spray drying process typically uses slaked lime (Ca(OH) 2 ) slurry as the reagent, while the CFB processes typically use dry hydrated lime (also Fluegas desulfurization processes can be classified as oncethrough or FlueGas DesulphurizationThe newly developed dry desulfurization processes including source/end control technologies and the various dry desulfurization materials including Calcium/Magnesium/Sodium/Carbonbased Recent advances in process and materials for dry desulfurization of 2022年1月15日 Through the purification technology of flue gas desulfurization, ultralow emissions of SO 2 flue gas in industrial flue gas can be achieved This article involves dry Summary of research progress on industrial flue gas
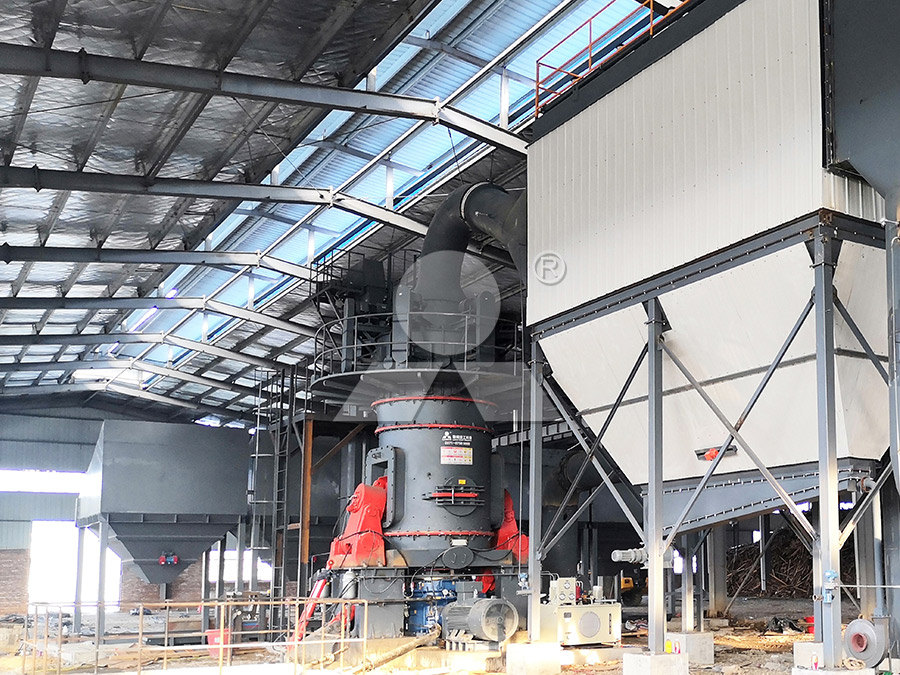
Air Pollution Control Technology Fact Sheet US EPA
Flue Gas Desulfurization Many wet systems reheat the flue gas downstream of the absorber to prevent corrosion caused by condensation inside the ducts and stack and reduce plume visibility2022年9月13日 In dry flue gas desulfurization (FGD) processes, SO 2 is combined with NO and O 2 to form sulfur trioxide, which is a chemical reaction that can significantly boost the adsorption Based on the above results, the An efficient calciumbased sorbent for flue gas dry 2023年7月29日 However, the dry desulfurization method exhibits significantly lower desulfurization efficiency compared to wet and semidry techniques, leading most enterprises Advances on resource utilization of semidry desulfurization ash 2024年6月1日 Calcium hydroxide (Ca (OH)2) finds widespread use in the petrochemical industry, particularly in flue gas desulfurization applications However, its conventional usage Recent advances in process and materials for dry desulfurization of
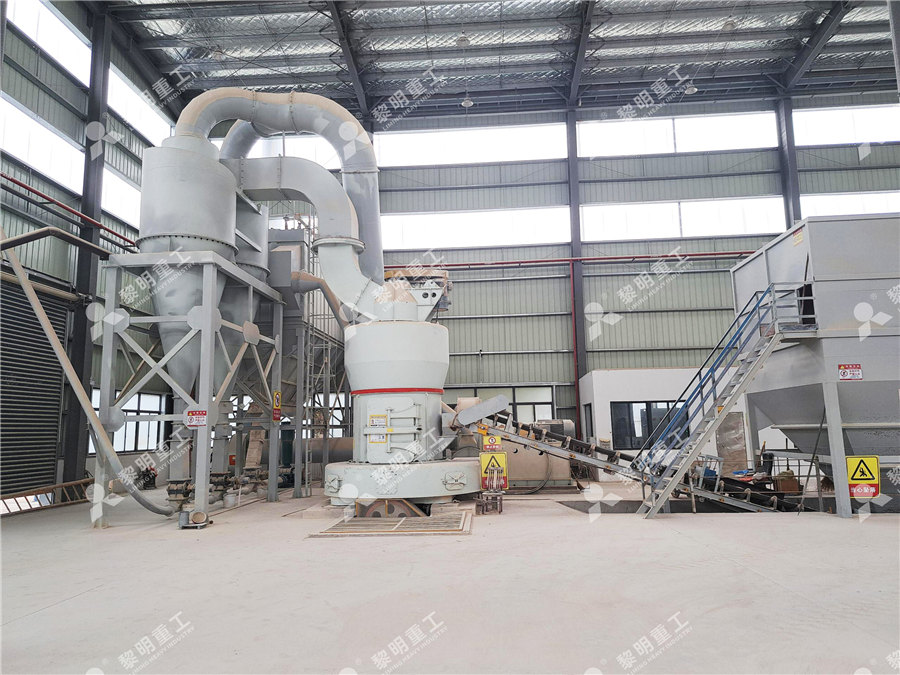
Flue Gas Desulfurization in a FixedBed Reactor: MildCondition
5 天之前 In quest of a substantial reduction in potentially toxic gas emissions into the air from industrial plants, dry flue gas desulfurization (FGD) systems offer several advantages, such as 2024年8月13日 Figure 3 below is a simplified process flow diagram for a dry sorbent injection (DSI) process, a typical dry FGD system The system is based on absorption of SO 2 from the Flue Gas Desulfurization: Detailed Process Overviewgas desulfurization (FGD) systems for controlling SO 2 emissions Our first coalfired spray dryer absorber (SDA) installations now have more than 35 years of operating history We are the exclusive North American licensee of GEA Process Engineering A/S, Denmark, for the GEA Niro SDA process The two companies also work together worldwide onSpray Dry Flue Gas Desulfurization Systems2024年8月13日 This blog post is the third in a threepart series that discusses flue gas desulfurization (FGD) The first post provides overviews of sulfur dioxide (SO 2) and emissions regulations, the FGD industry, and global FGD market trendsThe second post provides highlevel overviews of wet, semidry, and dry FGD technologies with respect to SO 2 capture Flue Gas Desulfurization: Detailed Process Overview
.jpg)
Desulfurization an overview ScienceDirect Topics
Numerous methods have been applied in the desulfurization process including wet scrubbing by means of slurry of alkaline sorbent, commonly lime or limestone, or seawater, spraydry scrubbing, SNO X desulfurization, etc Desulfurization efficiency and energy consumption during the process are two main factors when choosing the appropriate 2024年11月18日 Flue gas desulfurization gypsum (FGDG) is an industrial byproduct generated during the flue gas desulfurization process in coalfired power plants Flue gas desulfurization systems have been used to limit the release of sulfur dioxide from coalfired power plants since the late 1960s, but in the past decade the production of FGDG has drastically decreasedWhat is the Flue Gas Desulfurization Process?Desulfurization of flue gas from an amine process Abstract A method for disposing of excess sulfur dioxide in a flue gas from thermal oxidation of an acid gas stream including hydrogen sulfide recovered from a rich amine solution of an amine plant servicing at least one well head, includes cooling the flue gas to about 300 to about 650 degrees Fahrenheit, injecting a dry sorbent into Desulfurization of flue gas from an amine process US Patent 2022年1月15日 The semidry desulfurization ash is recycled to realize high valueadded production in the desulfurization process Semidry desulfurization technology has been continuously optimized and improved Wet desulfurization technology is a mature and widespread technology due to its high desulfurization rateSummary of research progress on industrial flue gas desulfurization
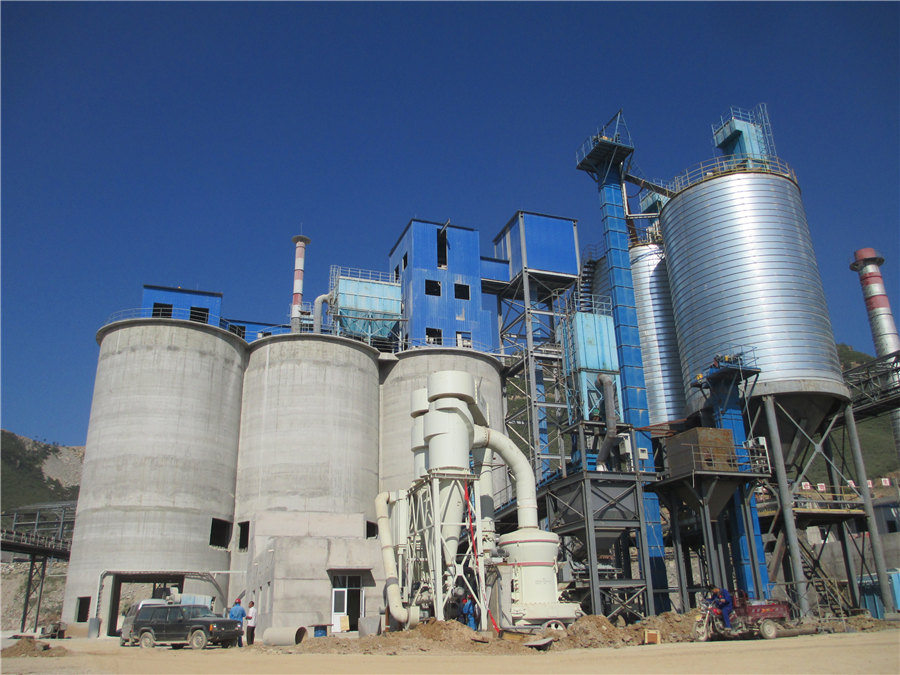
Recent advances in process and materials for dry desulfurization
In dry desulfurization process of flue gas, the selection of desulfurization agents is closely related to specific desulfurization processes and flue gas parameters Calciumbased, sodiumbased, magnesiumbased, and activated carbonbased materials all have unique properties2024年6月1日 Flue gas desulfurization process can be divided into wet, semidry and dry desulfurization process [[13], [14], [15]] Wet flue gas desulfurization process is the most mature and widely used desulfurization process However, the initial investment cost of the process is high, and it is easy to produce a large amount of secondary pollution Study on dry desulfurization performance of modified HNTsNumerous methods have been applied in the desulfurization process including wet scrubbing by means of slurry of alkaline sorbent, commonly lime or limestone, or seawater, spraydry scrubbing, SNO X desulfurization, etc Desulfurization efficiency and energy consumption during the process are two main factors when choosing the appropriate Desulphurisation an overview ScienceDirect Topics2024年10月1日 Given the low sulfur content in the lowtemperature sulfurous flue gas from hot blast stoves and rolling heating furnaces in steel plants, the economic viability of employing the wet FGD process is limited [4], [5] The dry fixedbed desulfurization process offers advantages such as low construction costs, stable operation, and minimal expenses Experimental study on the preparation of desulfurizer for low
.jpg)
An efficient calciumbased sorbent for flue gas dry
2022年9月13日 Abstract The development of sorbents for flue gas desulfurization in a dry mode is essential to control emission of sulfur dioxide Based on the novel concept of “treating waste with waste”, a lowcost and 2023年9月15日 The application of Dry Sorbent Injection (DSI) desulfurization with sodium bicarbonate was investigated to reduce SO 2 emission from power sector The sorbent was injected directly into the combustion chamber of the 29 MW th grate boiler, into a nonstandard area of high temperature (approximately 700 °C), while generally the DSI method is carried A novel approach to the dry desulfurization process by means of 2023年9月15日 The application of Dry Sorbent Injection (DSI) desulfurization with sodium bicarbonate was investigated to reduce SO 2 emission from power sector The sorbent was injected directly into the combustion chamber of the 29 MW th grate boiler, into a nonstandard area of high temperature (approximately 700 °C), while generally the DSI method is carried A novel approach to the dry desulfurization process by means of 2023年4月25日 The sodiumbased dry desulfurization process is a promising technology for flue gas desulfurization However, its industrial application still heavily relies on empirical experience In this study, a threedimensional numerical model was established for an industrial sodiumbased dry desulfurization process Numerical simulations were conducted to investigate the effects of Numerical Simulation on the SodiumBased Dry Desulfurization Process
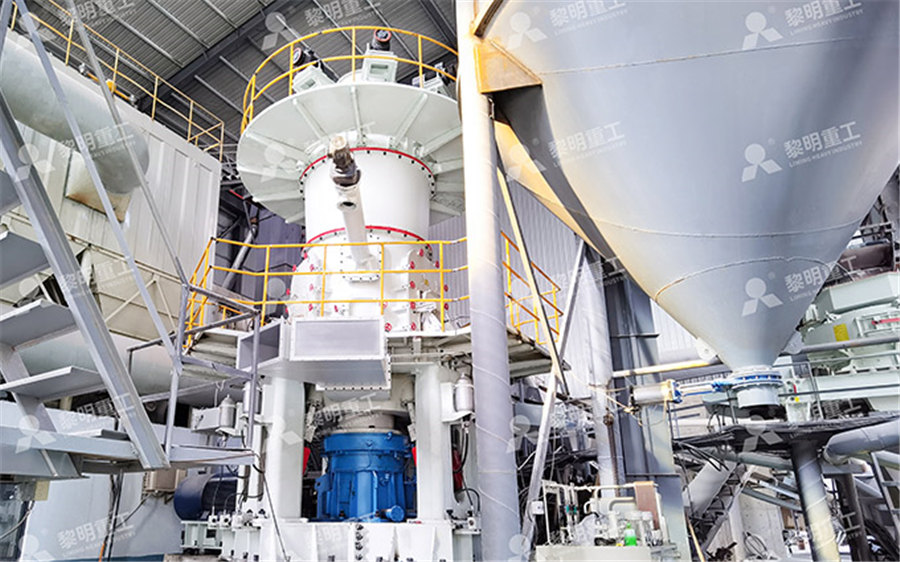
The Flue Gas Desulfurization Process Micronics Engineered
Flue Gas Desulfurization Processes The process of FGD is designed to absorb the sulfur dioxide in the flue gas before it is released This is accomplished through either a wet or a dry process Dry FGD In the process of dry scrubbing injection systems, lime is used as a reagent to react and remove gaseous pollutants2024年4月19日 4 flue gas injection semidry desulfurization process This method uses the flue between the boiler and the dust collector as the reactor for desulfurization, and does not need to add an additional absorption vessel, so that the process investment is greatly reduced, 4 Flue Gas Desulfurization Process You Should Never Miss2020年1月1日 In the formula, h is the enthalpy (J/kg) of q component The experimental data of Ma et al [7], [8], [9] for cylindrical spouted bed with conical base are used to validate the numerical model of water vaporization and semidry flue gas desulfurization process in a PPSB The bed and grid structures for the computational domain are illustrated in Fig 1, and the Numerical simulation of semidry flue gas desulfurization process limebased spraydry process, the overall S capture reaction is IMPLICATIONS Spraydry desulfurization was mainly investigated to date in connection with coalfired boilers, while in some European countries like Italy, there is a strong interest in carrying out a cheap desulfurization of flue gas from heavy oil combustionSprayDry Desulfurization of Flue Gas from Heavy Oil Combustion
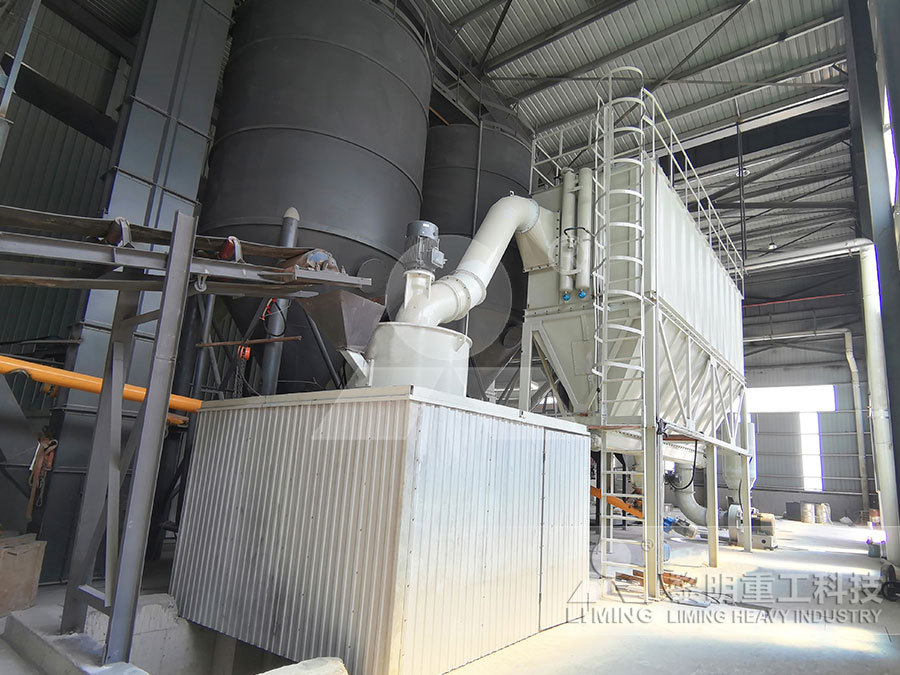
A new semidry desulfurization process using a powderparticle
2000年6月1日 A new semidry desulfurization process was tested in this study The process uses the socalled powderparticle spouted bed (PPSB) as the reactor in which coarse medium particles, usually silica sand of several hundred micrometers in size, are fluidized with hot flue gasA slurry of fine SO x sorbent, such as slaked lime or other alkaline powder, is continuously 2005年1月1日 A drydesulfurization process using Ca(OH)2/fly ash sorbent and a circulating fluidized bed (CFB) was developed Its aim was to achieve high SO2 removal efficiency without humidification and Novel DryDesulfurization Process Using Ca(OH) 2 /Fly2023年4月25日 The dry additive desulfurization process (DAP) is an appropriate approach for SOXreduction in power plants with small and medium capacity and for the retrofit of existing boilers with spatial Numerical Simulation on the SodiumBased Dry Desulfurization Process 2019年11月1日 A new semidry desulfurization process was tested in this study The process uses the socalled powderparticle spouted bed (PPSB) as the reactor in which coarse medium particles, Numerical simulation of semidry flue gas desulfurization process
.jpg)
FIRST OPERATING EXPERIENCE WITH A DRY FLUE GAS DESULFURIZATION
1986年1月1日 The dry FGDCFB process is explained Its main characteristics in particular, its simplicity and reliability, the high desulfurization efficiency without reheating the flue gas, the reduced space requirement, and the dry product have been highlightedThe authors also identify a number of important areas for future research, including reaction mechanisms, sorbent material, transport effects, modeling, and process development Dry Scrubbing Technologies for Flue Gas Desulfurization will appeal to both chemical and environmental engineers who examine different ways touse coal in a more Dry Scrubbing Technologies for Flue Gas DesulfurizationFluegas desulfurization (FGD) is a set of technologies used to remove sulfur dioxide (SO 2) from exhaust flue gases of fossilfuel power plants, Alstom presentation to UNECE on air pollution control (includes process flow diagram for dry, wet and seawater FGD)Fluegas desulfurization Wikipedia2023年7月29日 The semidry flue gas desulfurization ash (SFGDA) is an industrial waste generated by the semidry desulfurization process, and its resources have been continuously attracted attention Through the method of heat decomposition, the SFGDA decomposed into CaO and SO2 has emerged as a prominent research topic This paper summarizes various of Advances on resource utilization of semidry desulfurization ash
.jpg)
Biogas Desulphurisation: Which Technology is Best for your
2022年12月16日 Broadly there is dry desulfurization; For outlet requirements of less than 100 ppmv, the Iron Chelate desulfurization process can be followed by a dry desulfurization step which can bring hydrogen sulfide concentration down to ≤ 1999年7月9日 Development of New Desulfurization Agent Suitable for Dry Desulfurization Process at Low Temperature in China KAGAKU KOGAKU RONBUNSHU 2010, 36, 281287 DOI: 101252/kakoronbunshu36281 Yuzhong Li, Huiling Tong, Yuqun Zhuo, Yan Li, Changhe Chen, Xuchang Xu Feasibility study on High Calcium Utilization and Gypsum Formation for Dry Desulfurization 2024年2月21日 Dry desulfurization is a process used to remove or reduce sulfur compounds in flue gas without the use of liquid solvents Unlike wet desulfurization, which involves washing the flue gas with liquid absorbent solutions, dry desulfurization uses solid adsorbent materials or chemical reactors to capture and/or convert the sulfur compoundsDry flue gas desulfurization: sodium bicarbonate QuimidrogaThe semidry desulfurization process is simple, the overall cost is only 40%50% of the wet desulfurization process, and there are few rotating parts, which improves the reliability of the system and reduces the maintenance and repair costs 2.High desulfurization efficiency: FGD System for Sale Semidry Flue Gas Desulfurization
.jpg)
Spray Dry Flue Gas Desulfurization Systems
gas desulfurization (FGD) systems for controlling SO 2 emissions Our first coalfired spray dryer absorber (SDA) installations now have more than 35 years of operating history We are the exclusive North American licensee of GEA Process Engineering A/S, Denmark, for the GEA Niro SDA process The two companies also work together worldwide on2024年8月13日 This blog post is the third in a threepart series that discusses flue gas desulfurization (FGD) The first post provides overviews of sulfur dioxide (SO 2) and emissions regulations, the FGD industry, and global FGD market trendsThe second post provides highlevel overviews of wet, semidry, and dry FGD technologies with respect to SO 2 capture Flue Gas Desulfurization: Detailed Process OverviewNumerous methods have been applied in the desulfurization process including wet scrubbing by means of slurry of alkaline sorbent, commonly lime or limestone, or seawater, spraydry scrubbing, SNO X desulfurization, etc Desulfurization efficiency and energy consumption during the process are two main factors when choosing the appropriate Desulfurization an overview ScienceDirect Topics2024年11月18日 Flue gas desulfurization gypsum (FGDG) is an industrial byproduct generated during the flue gas desulfurization process in coalfired power plants Flue gas desulfurization systems have been used to limit the release of sulfur dioxide from coalfired power plants since the late 1960s, but in the past decade the production of FGDG has drastically decreasedWhat is the Flue Gas Desulfurization Process?
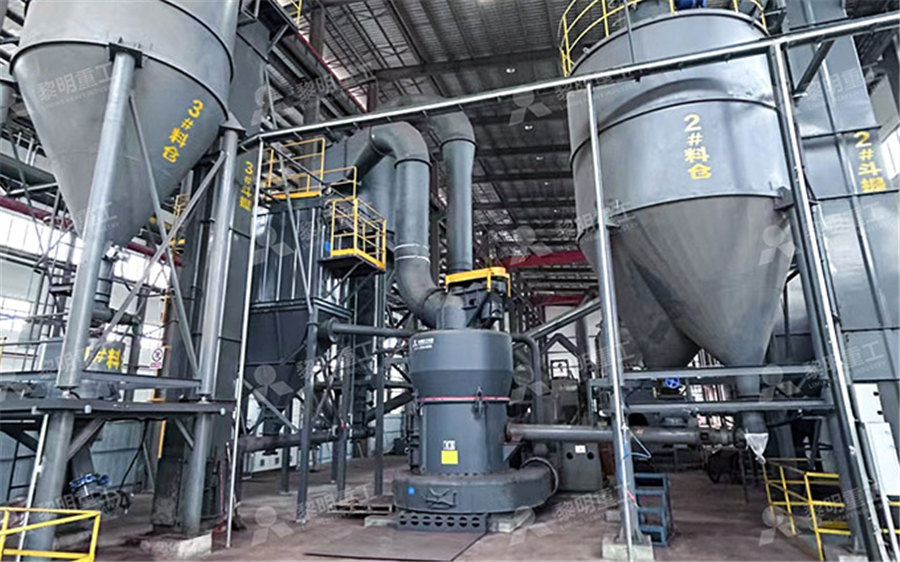
Desulfurization of flue gas from an amine process US Patent
Desulfurization of flue gas from an amine process Abstract A method for disposing of excess sulfur dioxide in a flue gas from thermal oxidation of an acid gas stream including hydrogen sulfide recovered from a rich amine solution of an amine plant servicing at least one well head, includes cooling the flue gas to about 300 to about 650 degrees Fahrenheit, injecting a dry sorbent into 2022年1月15日 The semidry desulfurization ash is recycled to realize high valueadded production in the desulfurization process Semidry desulfurization technology has been continuously optimized and improved Wet desulfurization technology is a mature and widespread technology due to its high desulfurization rateSummary of research progress on industrial flue gas desulfurization In dry desulfurization process of flue gas, the selection of desulfurization agents is closely related to specific desulfurization processes and flue gas parameters Calciumbased, sodiumbased, magnesiumbased, and activated carbonbased materials all have unique propertiesRecent advances in process and materials for dry desulfurization 2024年6月1日 Flue gas desulfurization process can be divided into wet, semidry and dry desulfurization process [[13], [14], [15]] Wet flue gas desulfurization process is the most mature and widely used desulfurization process However, the initial investment cost of the process is high, and it is easy to produce a large amount of secondary pollution Study on dry desulfurization performance of modified HNTs
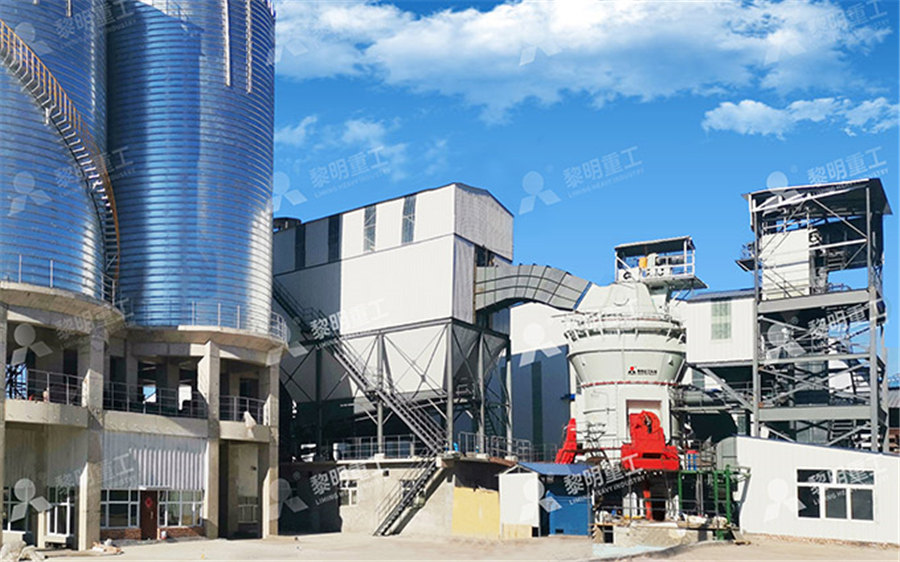
Desulphurisation an overview ScienceDirect Topics
Numerous methods have been applied in the desulfurization process including wet scrubbing by means of slurry of alkaline sorbent, commonly lime or limestone, or seawater, spraydry scrubbing, SNO X desulfurization, etc Desulfurization efficiency and energy consumption during the process are two main factors when choosing the appropriate 2024年10月1日 Given the low sulfur content in the lowtemperature sulfurous flue gas from hot blast stoves and rolling heating furnaces in steel plants, the economic viability of employing the wet FGD process is limited [4], [5] The dry fixedbed desulfurization process offers advantages such as low construction costs, stable operation, and minimal expenses Experimental study on the preparation of desulfurizer for low