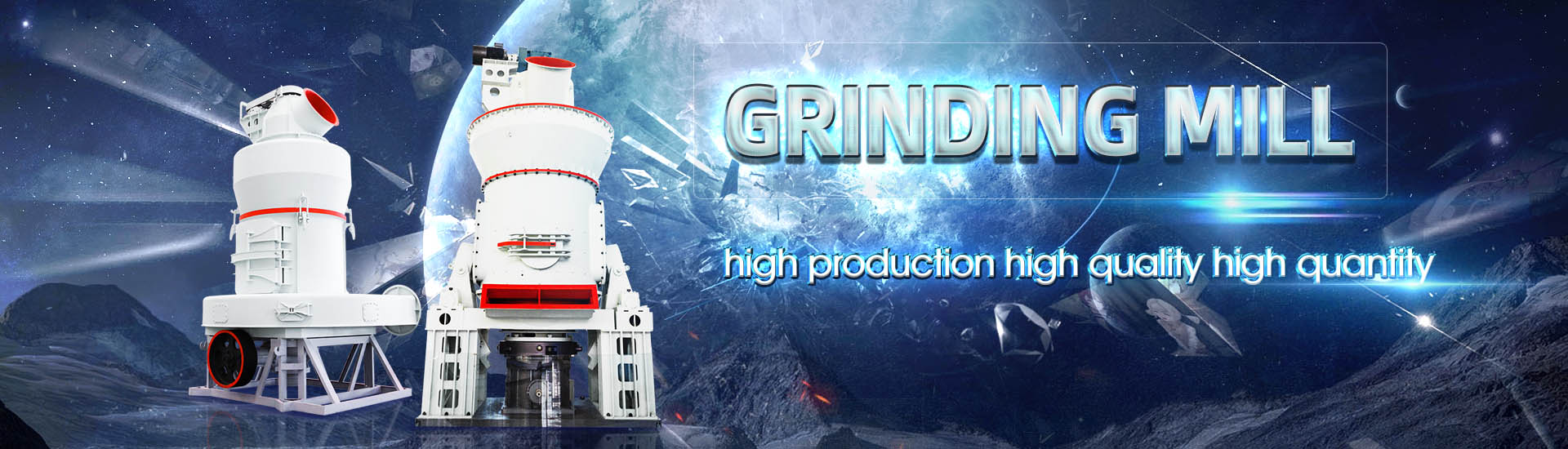
Grinding μm
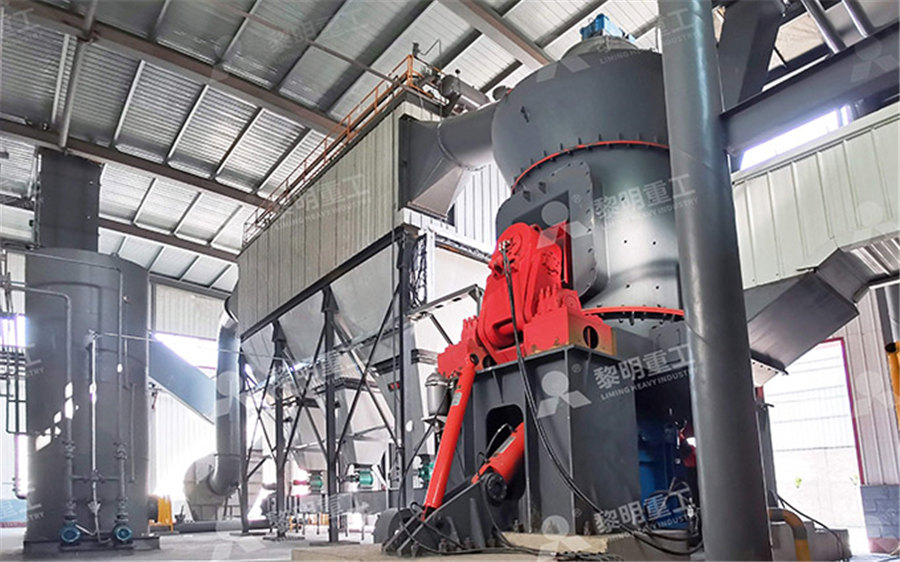
How Important is a Micron When Grinding Tools?
2023年3月30日 Highquality precision grinding machines can achieve microscopic tolerances and help manufacturers meet high customer requirements down to the μm As a manufacturer 2021年10月27日 Working in the machining and grinding world means grinding tools to around five microns’ tolerance for most highend cutting tools But just how tight is this tolerance? A How Important is a Micron in Cutting Tool Grinding?2021年1月1日 Contrary to the conventional (macro) grinding process, which is typically employed for grinding of simple components, the microgrinding offers a high degree of Modeling of microgrinding forces considering dressing 2023年3月24日 The results show that the use of small grit size grinding wheels allowed for effective removal of sapphire and they facilitated the production of ductile surfaces at the Evaluation of grinding characteristics for sapphire ultraprecision
.jpg)
High Efficiency Precision Grinding of Microstructured SiC Surface
2019年3月7日 Basing on precision grinding with conditioned and laser microstructured coarsegrained diamond grinding wheel, a novel high efficiency technique for microstructured 2023年12月21日 This research presents a multiscale model to capture the interaction state of the grainworkpiece by determining the transient stage of each individual grain based on the A multiscale model revealed in the grinding process and its 2019年5月18日 Microgrinding is a tool based mechanical micromachining process which is mostly applied to create and finish 3D microfeatures on hard and brittle materials such as A comprehensive review of microgrinding: emphasis on toolings 2023年3月27日 The rotating ultrasonicassisted grinding (RUAG) experiment of the conical grinding wheel generated the intermittent pitshaped microtexture on the surface of the Conical Grinding Wheel UltrasonicAssisted Grinding Micro

Effect of different grinding strategies on subsequent polishing
2024年2月28日 Two critical techniques in the manufacturing process of optical components made of hard and brittle materials are grinding and polishing Subsurface damage mainly occurs due to stresses and cracks generated when diamond abrasive grains cut the material during the grinding process [12]It is crucial to remove the grinding damage through subsequent polishing2024年12月1日 The aim of the present work was to investigate the diamond grinding of 0/90° continuous carbon fiber reinforced ZrB 2 in order to understand the influence of the process parameters (feed rate, cutting speed) on the material removal mechanisms and the surface topography The experiments were performed on a 0°/90° multiaxial reinforced C/ZrB 2 Influence of diamond grinding process on material removal 2014年7月1日 The thrust grinding force increased from 0 for each hole with an increase in the tool axial feed length The maximum grinding force during drilling one hole also increased with the number of drilled holes, reaching 02 N in drilling the fifth hole The increase in the maximum grinding force can be attributed to tool wearDrilling of microholes down to 10 μm in diameter using ultrasonic grinding2013年3月1日 Request PDF Energy Use of Fine Grinding in Mineral Processing Fine grinding, to P80 sizes as low as 7 μm, is becoming increasingly important as mines treat ores with smaller liberation sizesEnergy Use of Fine Grinding in Mineral Processing
.jpg)
How Important is a Micron When Grinding Tools?
2023年3月30日 This is also an economic factor because imprecise grinding processes lead to scrapped parts When grinding shank tools, it is important to minimize the runout – ie the deviation of one or more reference features from another reference point when the workpiece is rotated 360° around the reference axis2024年3月1日 The main influencing factors for grinding damage include abrasive grit size, grinding depth, workpiece feed speed, and wheel speed According to the research of Sabia et al [13], the grinding subsurface damage depth (SSD) of glass ceramics is proportional to 5 times the average abrasive grit sizeMa et al [14] found that the SSD of fused silica is 4–6 times the Optimization of grinding process for hard and brittle materials 2021年11月1日 The grinding wheel used was a vitrified diamond pin with a diameter of 2 mm, grainsize of 45 mm, at two different concentrations (C150 and C200) The grinding process was a peripheral, upgrinding operation with a width of 20 mm (Fig 2 c) Microgrinding was performed using grinding oil as a lubricant Download: Download highres image (799KB)The role of specific energy in microgrinding of titanium alloyA grinding mill is a device that breaks solid materials into smaller pieces by grinding, crushing, or cutting Such comminution is an important unit operation in many processes There are many different types of grinding mills and many types of materials processed in themGrinding Mills for reliable size reduction tasks RETSCH
.jpg)
Production of polymer particles below 5 μm by wet grinding
2012年9月1日 Polymeric microparticles that may be used in rapid prototyping processes typically are produced by either polymerization processes or cryogenic grinding in impact mills at liquid nitrogen temperature (− 196 °C) or by dry grinding at solid carbon dioxide temperature (− 78 °C)Within this account an alternative approach for the production of polymer particles is 2012年9月1日 Ghosh et al [8] modelled components of specific grinding energy in High Efficiency Deep Grinding (HEDG) process of steels They modelled components of specific grinding energy in terms of the semi apex angle of the single grit Grinding being complex and dynamic process, other parameters like wheel speed, depth of cut, feed rate and grain size Development of specific grinding energy model ScienceDirect2023年7月1日 Grinding is the most widely used highefficiency and lowcost finishing process in the manufacturing industry 1 During grinding, the interaction between the grinding wheel and workpiece generates grinding force at sliding, elastic/plastic deformation, and chipforming stages 2, 3 Grinding force is an important parameter to measure grinding performance, and it has a Analysis of grinding mechanics and improved grinding force 2014年7月1日 In order to reduce grinding force and thus prevent tool breakage, ultrasonic grinding was employed with the workpieces ultrasonically oscillated As a result, microholes down to 10 μm in diameter were successfully drilled They are the smallestdiameter holes drilled by grinding, to the best of our knowledgeDrilling of microholes down to 10 μm in diameter using ultrasonic grinding
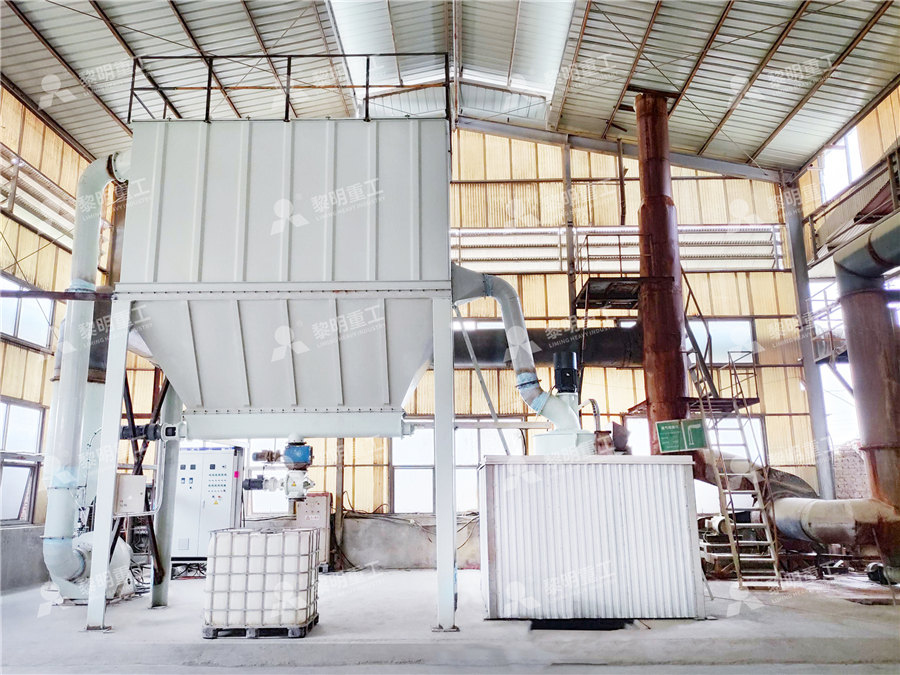
Effect of duration and type of grinding on the particle size
2023年10月1日 Wet grinding, on the other hand, seems to have less effect on the fineness of pumice than dry grinding Amongst the ground samples, large particles sized >100 μm are the most frequent in W feed, which are significantly rarer in the dry ground samples (Fig 9 e) Grinding for 3 h eliminated almost all particles sized >100 μm (Fig 9 d)2021年1月1日 The microgrinding tool acts as a cantilever beam where the end of the tool is firmly clamped in the tool holder The tool is subjected to a nonuniform cutting load at the end of the tool during the grinding process Since the grinding forces are applied in two different directions (tangential and normal), the tool deflects in both directionsModeling of microgrinding forces considering dressing parameters and 2023年10月15日 Conventional diamond grinding wheels present challenges such as poor selfsharpening and difficulties in achieving ductile domain machining when processing hard and brittle materials, reducing machining quality and efficiencyThis paper introduces a novel grinding wheel composed of porous diamond abrasive grains for better ultraprecision machiningGrain wear properties and grinding performance of porous 2012年1月11日 Mineral grinding oil was used as cooling lubricant In order to emphasize the fundamental chip formation mechanisms and their change along the engagement zone of the tool, the grinding tool and process parameters were deliberately chosen to achieve high average single grain thicknesses h cu,avTherefore, a cutting speed of v c = 5 m/s, a feedrate of v ft = 80 Chip formation in grinding: an experimental study

Drilling of Microholes Down to 10 ??m in Diameter Using Ultrasonic Grinding
2014年7月1日 Drilling by grinding is useful for fabricating holes in hard and brittle materials with high dimensional accuracy and low machining cost However, its application to microholes has been limited to 2024年6月1日 Before the grinding test, the grinding wheels were prepared during dressing and sharpening to eliminate the effects of wheel wear and runout After grinding, the surface morphology was obtained by ultradepth field microscopy (VHX100, Keyence, Osaka, Japan), and surface damage was observed with SEM (SUPRA 55, Zeiss, Oberkochen, Germany)Undeformed chip thickness models for precise vertical spindle 2021年7月1日 Grinding aids have been utilized in crushing PTFE Herein, four different soluble salts (NH 4 Cl, CO(NH 2) 2, NaCl, and Na 2 SO 4) are selected as grinding aids to achieve facile separation of the grinding aids and PTFE powder by a washing processEffect of grinding aids and process parameters on dry fine grinding 2017年4月1日 In summary, with a comparison to conventional grinding processes, grinding the hard and brittle microstructures still poses a more challenging task because of the following issues: (1) form deviation caused by chipping and fracturing on the edges of microstructures, (2) the rounded corners of microstructures resulting from the wheel manufacture/truing limitation Ultrasonic vibration assisted grinding of hard and brittle linear
.jpg)
Undeformed chip thickness with composite ultrasonic vibration
2024年3月1日 Grinding is essentially composed of each chip surrounded by two adjacent grains on the grinding wheel [16]Therefore, it is necessary to study the maximum undeformed chip thickness generated by a single grain (hereinafter using undeformed chip thickness for short) [17]By reasonably selecting the grinding parameters, the undeformed chip thickness less than 2017年5月1日 Grinding wheels with defined grain patterns have the advantage that the position of every grain is known Thus, deterministic structures can be manufactured, as the material removal of every grain is a priori known The manufactured structures applying this approach are composed by multiple single grain scratchesManufacturing of structured surfaces via grinding ScienceDirect2024年7月1日 Rough grinding produced a subsurface damage layer of 238 µm, due to the high hardness of the sapphire, wheel wear and the limited grinding efficiency of the D15 hybridbond wheel, the number of grinding passes in semifinish grinding is not sufficient to completely remove the subsurface damage layer produced by rough grindingResidual stress and subsurface damage in sapphire ultraprecision grinding2019年11月1日 Grinding with the laserstructured tool may allow more lateral cracks propagation compared to the nonstructured tools and more microcracks in the workpiecetool contact zone due to the intermittent cutting, easing the chipping mechanism and improves the cutting process with lowering the grinding forces [17]Laserassisted microgrinding of Si3N4 ScienceDirect
.jpg)
Evolution of Surface Roughness in Grinding and its Relationship
2013年12月31日 Grinding is a machining process specially indicated for finishing operations in hard materials, in order to obtain low surface roughness (Ra 01 mu m to 2 mu m) and tight tolerances2003年1月10日 Grinding is used as the most efficient and effective technique to finish ceramic workpieces As quality of advanced ceramics has dramatically improved with the modern manufacturing techniques, the bulk defects are significantly reduced in terms of Grinding induced damage in ceramics ScienceDirect2010年1月1日 Grinding fluids are used to reduce the friction between workpiece and grinding wheel and to conduct heat out of the grinding zone in order to avoid thermal damages of the workpiece surface Generally, in ultraprecision grinding small depths of cut and hence small grain contact lengths occurUltraprecision grinding ScienceDirect对于常见的厚度大于等于50㎛的晶圆,背面研磨有三个步骤:先是粗磨(Rough Grinding),再是精磨(Fine Grinding),两次研磨后切割并抛光晶圆。 此时,类似化学机械抛光(Chemical Mechanical Polishing,简称 CMP)一样,一般会在抛光垫和晶圆之间投入浆料(Slurry)和去离子水(Deionized Water)。背面研磨(Back Grinding)决定晶圆的厚度 知乎
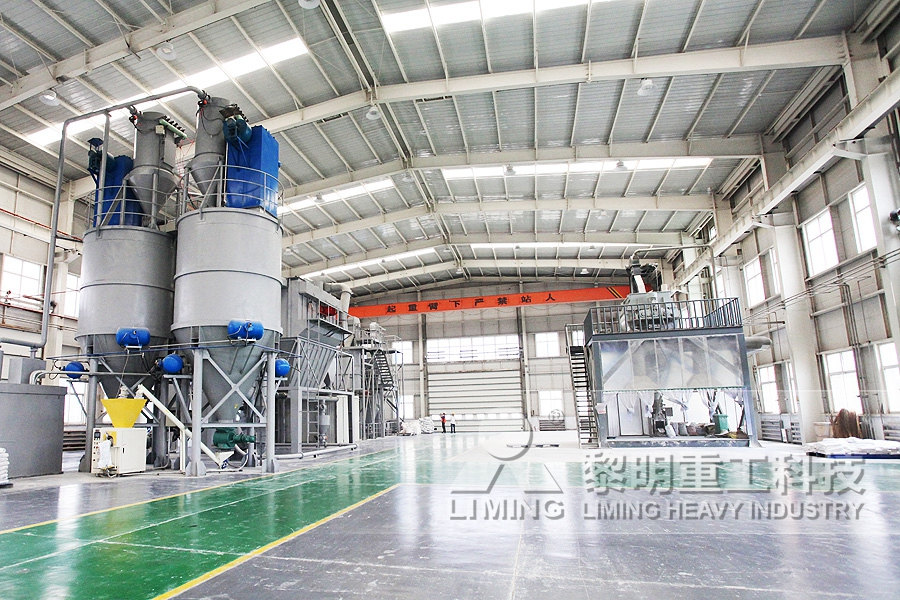
Evaluation of grinding characteristics for sapphire ultraprecision
2023年3月24日 Grinding characteristics in sapphire microslotgrinding included groove morphology, fracture behavior [11], brittleductile transformation [12] and subsurface damage [13], [14] were reported, and in particular, the model for the corresponding micro grinding tools [15], [16] were developed to reliable prediction of the grinding force2024年2月2日 In the grinding, the active abrasive grain quantity (AAGQ) and the undeformed chip thickness (UCT) are the key parameters for revealing the material removal mechanism 7, 8, 9 Due to the size different and random distribution characteristics of abrasive grains, only some outmost abrasive grains have the ability to remove the material Moreover, the value of UCT Evolution of undeformed chip thickness and grinding forces in grinding 2024年2月28日 Two critical techniques in the manufacturing process of optical components made of hard and brittle materials are grinding and polishing Subsurface damage mainly occurs due to stresses and cracks generated when diamond abrasive grains cut the material during the grinding process [12]It is crucial to remove the grinding damage through subsequent polishingEffect of different grinding strategies on subsequent polishing 2024年12月1日 The aim of the present work was to investigate the diamond grinding of 0/90° continuous carbon fiber reinforced ZrB 2 in order to understand the influence of the process parameters (feed rate, cutting speed) on the material removal mechanisms and the surface topography The experiments were performed on a 0°/90° multiaxial reinforced C/ZrB 2 Influence of diamond grinding process on material removal
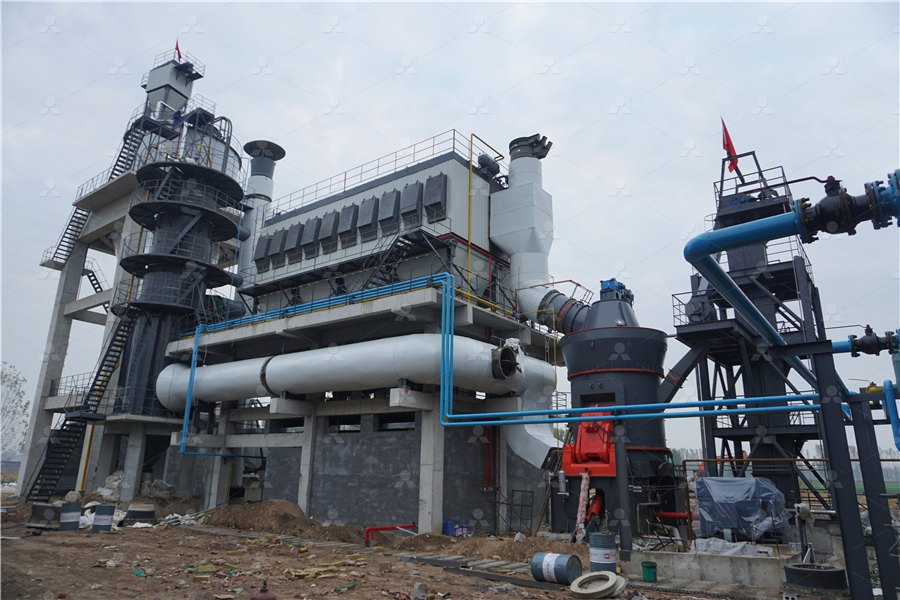
Drilling of microholes down to 10 μm in diameter using ultrasonic grinding
2014年7月1日 The thrust grinding force increased from 0 for each hole with an increase in the tool axial feed length The maximum grinding force during drilling one hole also increased with the number of drilled holes, reaching 02 N in drilling the fifth hole The increase in the maximum grinding force can be attributed to tool wear2013年3月1日 Request PDF Energy Use of Fine Grinding in Mineral Processing Fine grinding, to P80 sizes as low as 7 μm, is becoming increasingly important as mines treat ores with smaller liberation sizesEnergy Use of Fine Grinding in Mineral Processing2023年3月30日 This is also an economic factor because imprecise grinding processes lead to scrapped parts When grinding shank tools, it is important to minimize the runout – ie the deviation of one or more reference features from another reference point when the workpiece is rotated 360° around the reference axisHow Important is a Micron When Grinding Tools?2024年3月1日 The main influencing factors for grinding damage include abrasive grit size, grinding depth, workpiece feed speed, and wheel speed According to the research of Sabia et al [13], the grinding subsurface damage depth (SSD) of glass ceramics is proportional to 5 times the average abrasive grit sizeMa et al [14] found that the SSD of fused silica is 4–6 times the Optimization of grinding process for hard and brittle materials
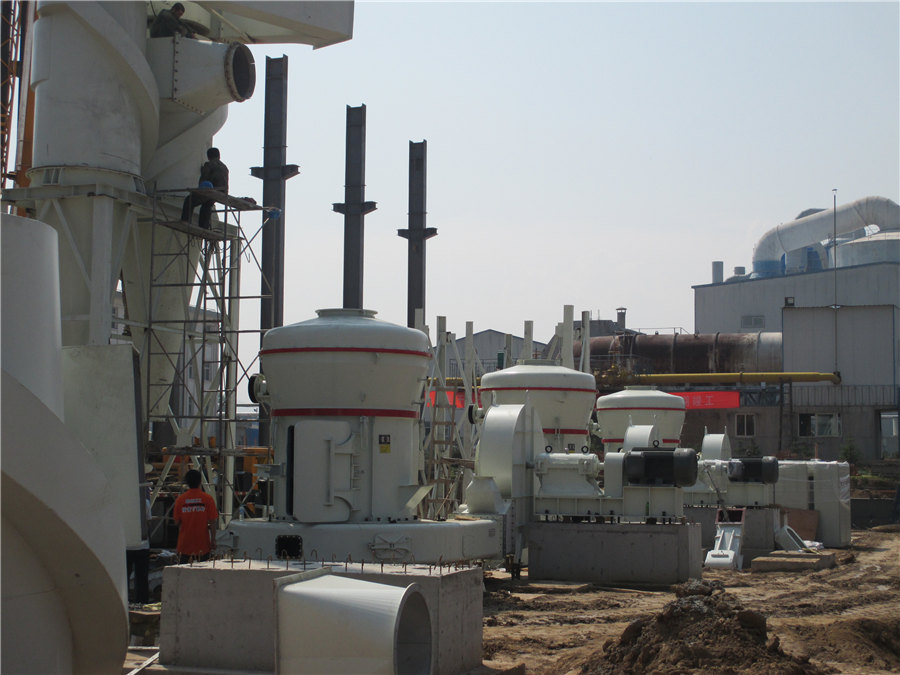
The role of specific energy in microgrinding of titanium alloy
2021年11月1日 The grinding wheel used was a vitrified diamond pin with a diameter of 2 mm, grainsize of 45 mm, at two different concentrations (C150 and C200) The grinding process was a peripheral, upgrinding operation with a width of 20 mm (Fig 2 c) Microgrinding was performed using grinding oil as a lubricant Download: Download highres image (799KB)A grinding mill is a device that breaks solid materials into smaller pieces by grinding, crushing, or cutting Such comminution is an important unit operation in many processes There are many different types of grinding mills and many types of materials processed in themGrinding Mills for reliable size reduction tasks RETSCH2012年9月1日 Polymeric microparticles that may be used in rapid prototyping processes typically are produced by either polymerization processes or cryogenic grinding in impact mills at liquid nitrogen temperature (− 196 °C) or by dry grinding at solid carbon dioxide temperature (− 78 °C)Within this account an alternative approach for the production of polymer particles is Production of polymer particles below 5 μm by wet grinding2012年9月1日 Ghosh et al [8] modelled components of specific grinding energy in High Efficiency Deep Grinding (HEDG) process of steels They modelled components of specific grinding energy in terms of the semi apex angle of the single grit Grinding being complex and dynamic process, other parameters like wheel speed, depth of cut, feed rate and grain size Development of specific grinding energy model ScienceDirect