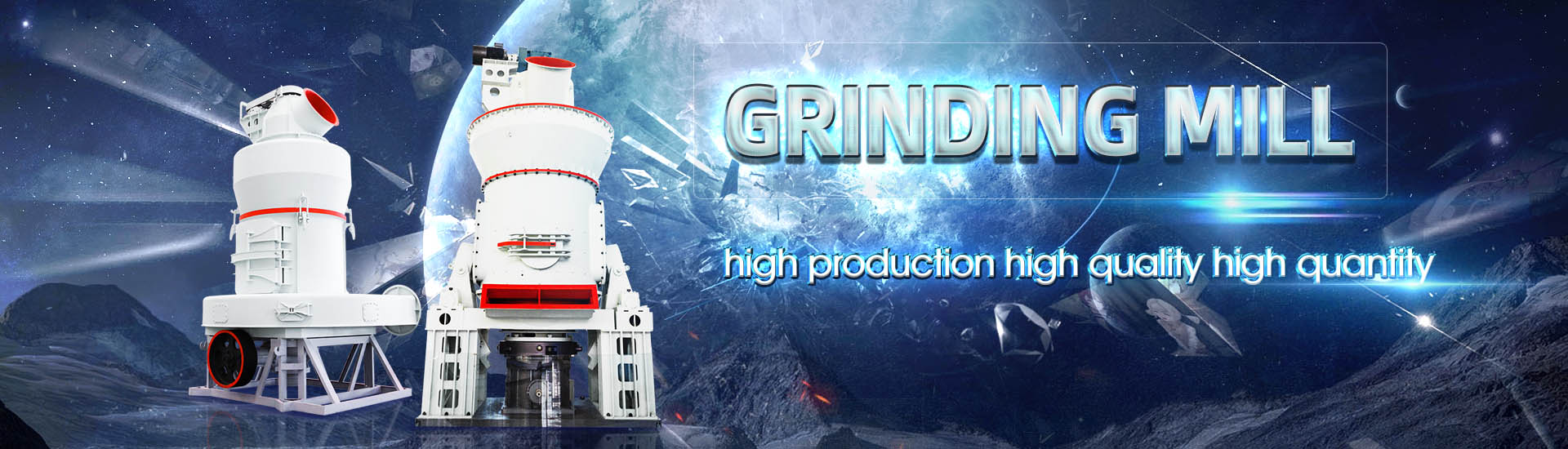
HOME→How to reduce the power consumption of the vertical mill How to reduce the power consumption of the vertical mill How to reduce the vertical mill Power consumption of mill
How to reduce the power consumption of the vertical mill How to reduce the power consumption of the vertical mill How to reduce the vertical mill Power consumption of mill
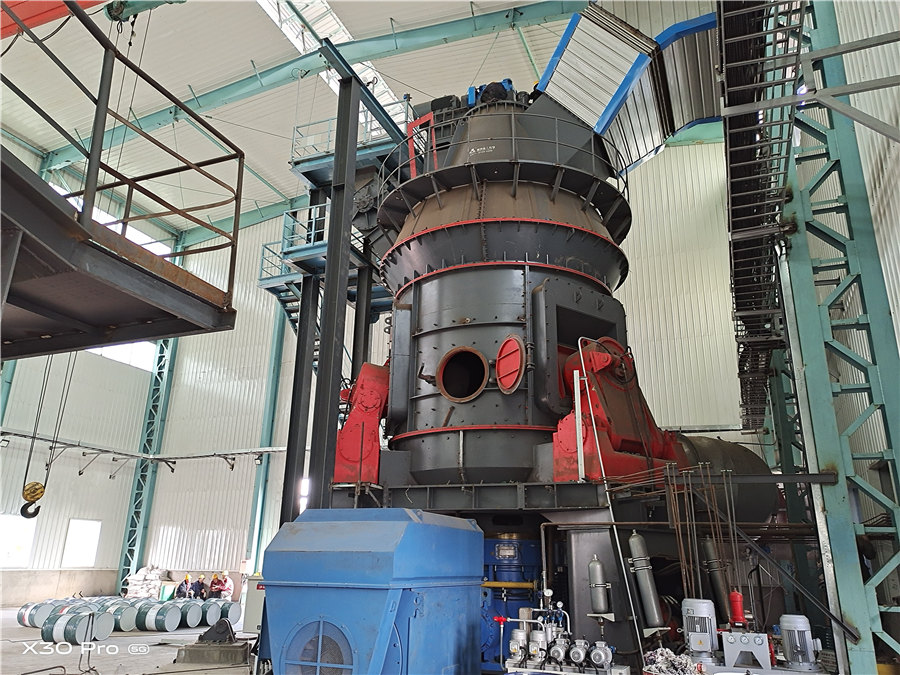
Modeling of energy consumption factors for an industrial cement
2022年5月9日 Generating such systems and assessing the VRM process operational parameters would help to optimize power consumption, improve maintenance, reduce environmental issues, and make the processFull Size Image Modeling of energy consumption factors for an industrial Full Size Image2024年1月15日 The performance of a vertical roller mill is analysed with CFD Adverse air circulation is detected through CFD simulations Design modifications were evaluated and Optimisation of the performance of a new vertical roller mill by The Vertical Roller Mill (VRM) reduces the power consumption for cement grinding approximately 3040% associated with other grinding mills The process variables in cement grinding process PROCESS CONTROL FOR CEMENT GRINDING IN VERTICAL
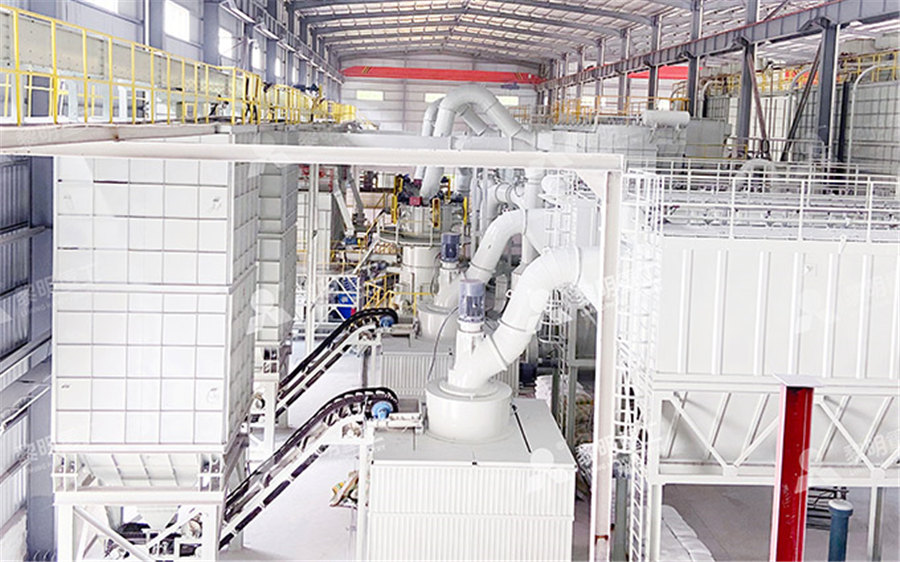
Four methods to reduce vertical mill power consumption on
The maximum load of the vertical mill system mainly comes from the main motor and the circulating air blower, which approximately takes up 70% power consumption So, the key of productivity and reduce power consumption In order to reduce the manufacturing costs for cement, it is very important to optimise the existing mill installations as far as the grinding PROCESS DIAGNOSTIC STUDIES FOR CEMENT MILL power consumption values As a rule, a lower specific power consumption of the mill system can be converted, in certain circumstances, to higher mill throughput during operation This is VERTICAL ROLLER MILLS A holistic VRM approach2022年5月9日 In the mid1990s, the vertical roller mill (VRM) was introduced to the cement industry to reduce this energy usage Besides lowering power consumption, VRMs may Modeling of energy consumption factors for an industrial cement
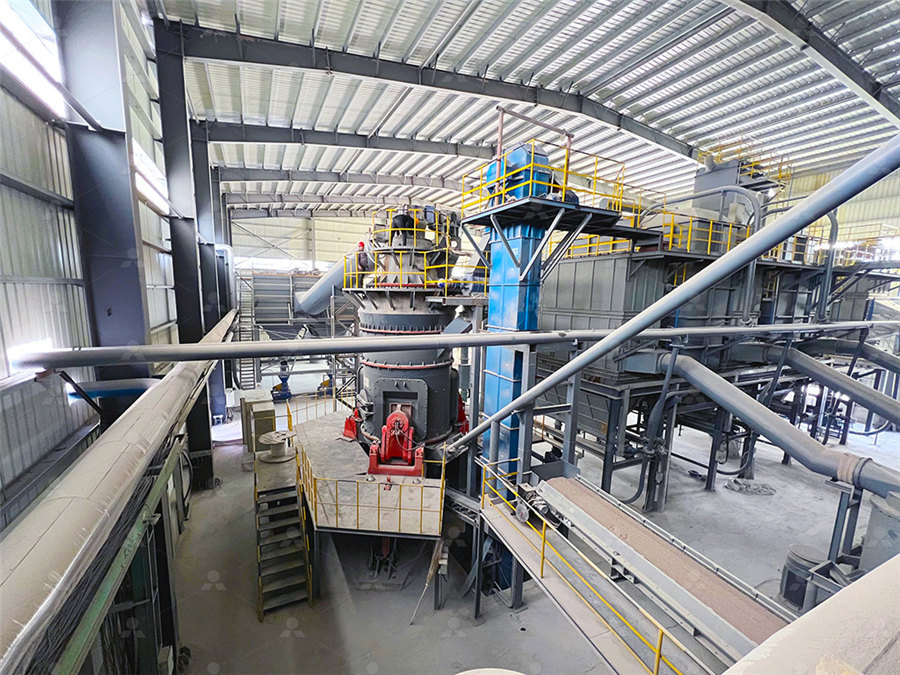
Analysis and Optimization of Grinding Performance of
2022年1月23日 This work concentrates on the energy consumption and grinding energy efficiency of a laboratory vertical roller mill (VRM) under various operating parameters For design of experiments (DOE), the response surface method 2021年2月1日 Literature showed that using VRM instead of a ball mill could reduce Zinc grinding power consumption from 2011 to 1111 kWh/t of raw materials (kWh/1000 kg) [14] In another A case study on energy and exergy analyses for an industrialscale Recently, the vertical roller mill having great grinding performance is widely applied to the raw material grinding process However, tube mill, which has about 30% poor grinding Vertical roller mill for raw Application p rocess materialsThe todate biggest mill size modular vertical roller mill 6700 C6 shows satisfactory results for cement and composite cement grinding This mill, installed in Northern Africa, is in operation Grinding Process Optimization Featuring Case Studies and
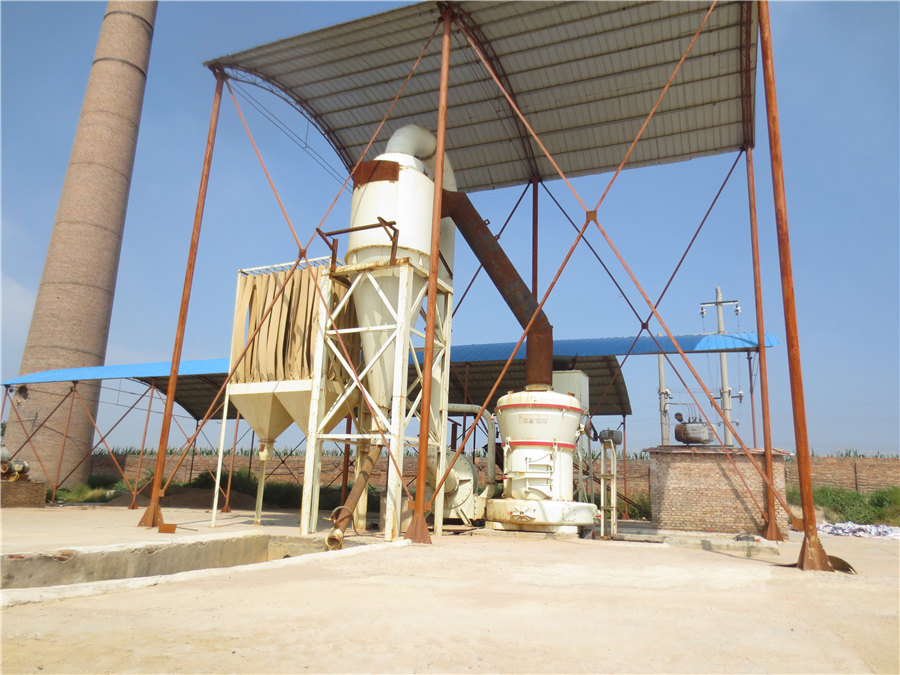
Modeling of energy consumption factors for an industrial cement
would help to optimize power consumption, improve maintenance, reduce environmental issues, and make the process sustainable A few investigations have been conducted to model VRM performance2016年7月23日 \$\begingroup\$ there are many peripherals that can be turned off to reduce power consumption, so having SPI enabled vs disabled will impact current consumption There are many resources online about making What is the best way to estimate the power 2020年9月21日 Measure power consumption directly from the socket The most reliable way is also the simplest way Buy a cheap watt hour meter, plug it into the socket between your wall and your server and you are golden This will always be the best way to measure power consumption because it will measure exactly what your server consumesHow to measure the power consumption of your backend service2019年11月14日 With the modern manufacturing industry evolving and advancing and amid a more energy conscious society, high energy demand in manufacturing—particularly in machining—has drawn more and more attention Accurate energy consumption modelling is critical to the improvement of energy efficiency in machining In the existing energy models of Energy consumption model for milling processes considering
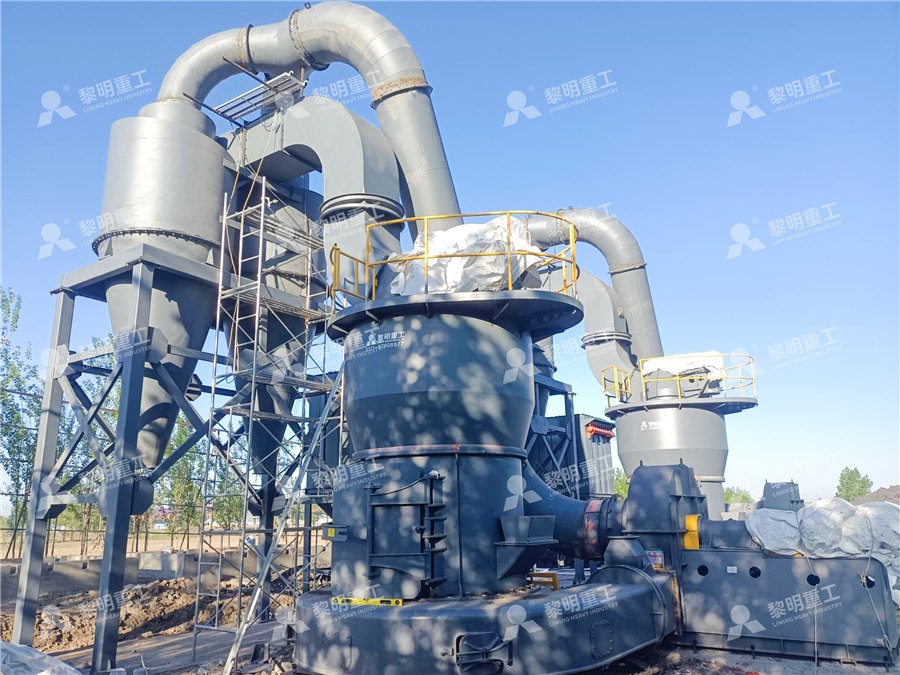
Performance Evaluation of Vertical Roller Mill in Cement
2017年9月11日 Used as a primary mill in existent plants, it can not only reduce energy consumption but also increase output However, its real advantage will lie in its use as an autonomous finish grinding mill2012年6月1日 In this study, the first and second law analysis of a raw mill is performed and certain measures are implemented in an existing raw mill in a cement factory in order to reduce the amount of energy consumption in grinding process The first and second law efficiencies of the raw mill are determined to be 615% and 164%, respectivelyReducing energy consumption of a raw mill in cement industry2015年6月19日 Ball Mill Motor/Power Sizing Calculation; Ball Mill Design/Sizing Calculator; The power required to grind a material from a given feed size to a given product size can be estimated by using the following equation: where: W = power consumption expressed in kWh/short to (HPhr/short ton = 134 kWh/short ton)Ball Mill Design/Power Calculation 911Metallurgist2022年6月24日 6 Energy consumption Under the same power condition, the grinding efficiency of the ball mill is low, and the energy consumption is high The vertical mill has high grinding efficiency and low energy consumption, and the power consumption is only 40%50% of the ball mill 7 Finished product qualityHow to choose between ball mill and vertical roller mill?
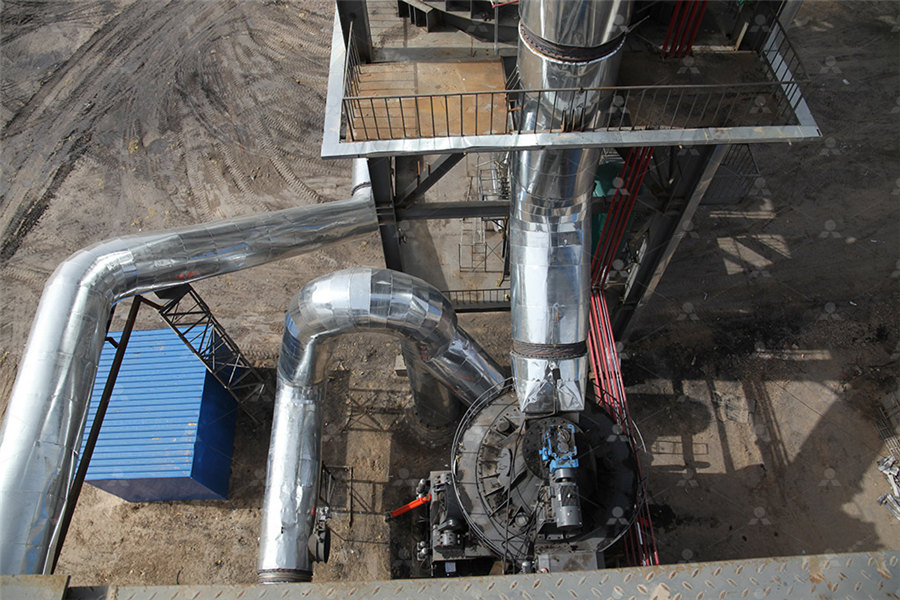
Optimisation of the performance of a new vertical roller mill by
2024年1月15日 Sun et al [9] carried out study of a roller mill (HRM 4800 by Hefei Zhong Ya, China) and analysed air flow patterns in the mill to improve the energy efficiency of the mill Shah et al [ 10 ] used modelling to optimise the performance of a coal pulveriser by studying the influence of variation in inlet vane angles on the collection efficiency of the powder and desired Table 3 Power Consumption Of Roller Press Grinding System Overall, we can conclude the three tables: After the longterm operation, although unit raw material grinding power consumption of the cement roller press grinding Comparison Of Vertical Roller Mill And Roller Press MillThe amount of feed in the mill can be tested by 3 methods: Grinding roller limit device clearance; The power of the mill (ie the main motor current); Metering of belt scales; If the layer is too thick, the following phenomena will occur: The How to Improve Grinding Efficiency of Vertical Roller 2017年1月17日 Excessive mill speeds caused more power consumption but resulted in reduced grinding rate Based on the simulation data, two scaleup models were proposed to predict power draw and grinding rateBreaking down energy consumption in industrial
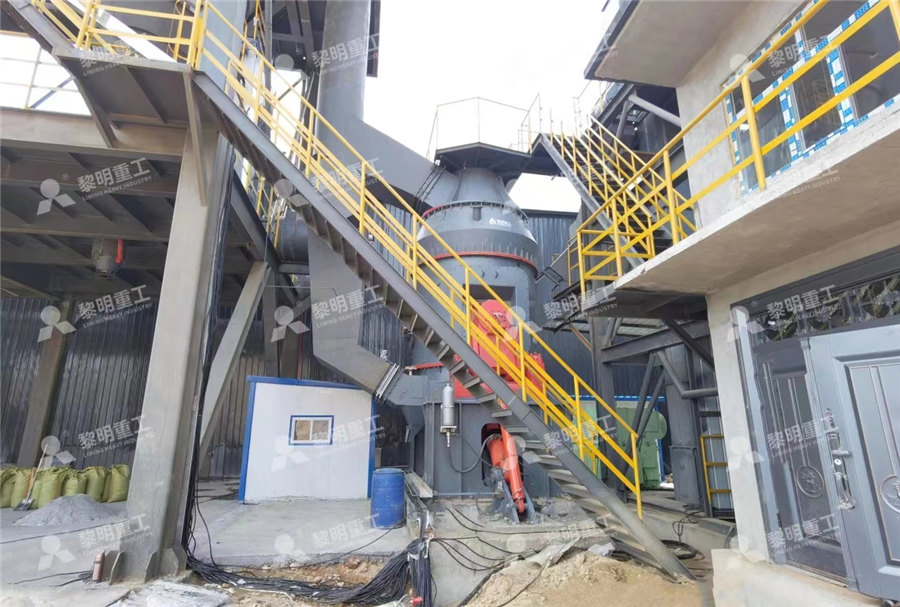
Review on vertical roller mill in cement industry its
2021年1月1日 Grinding Mill Vertical Roller Mill or Ball Mill: The reclaimed raw mix fed to Raw Mills, for drying and fine grinding of Raw meal for kiln feed: 4: Coal Grinding: Grinding Mill Vertical Roller Mill or Ball Mill: Coal is ground in Coal mill, which is a fuel for use in Kiln firing: 5: Pyro Section, Clikerization: In line calciner six stage The specific power consumption, product quality and other performance of the "OK" and "CK" vertical roller mills for cement grinding are briefly stated Hence, the enhancement in increasing the productivity of the vertical roller mill at Chichibu Onoda Cement Corporation (COCC) is introduced These include: (a) restoring a table liner and roller tires by hardfacing to reduce Productivity increase of the vertical roller mill for cement grinding2013年5月14日 And practices prove that the unit energy consumption of wet ball mill can reduce to some degree after adopting the rubber scaleboard, it usually can reduce 10% What's more, the service life of the rubber scaleboard is 2 or 3 times longer than the alloy scaleboardThe most remarkable thing is that besides reducing energy consumption, the rubber scaleboard can also How to Reduce the Energy Consumption of Ball Mill from 2016年10月5日 If you are thinking of saving on your electricity bill or looking to increase your laptop’s battery life, then you should make your PC use less power There are many ways you can reduce power consumption of your PC, and in this post we will list seven ways to reduce PC power usage Note: the ways listed below are meant for PCs running Windows 7 Ways to Reduce Your PC's Power Consumption Make Tech Easier
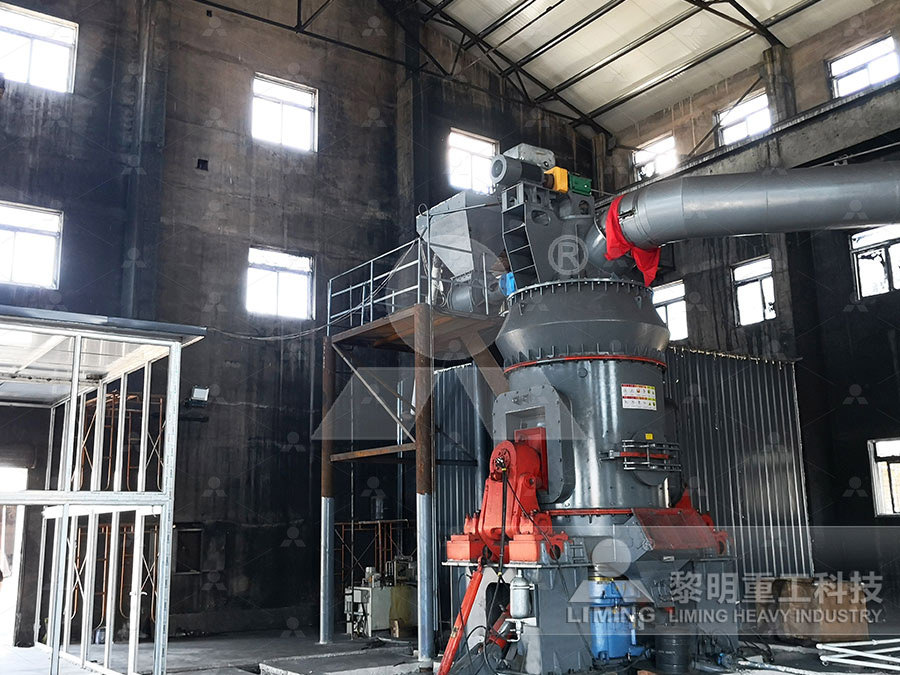
5 Ways to Improve the Ball Mill Efficiency FTM
2020年1月11日 This can reduce the energy consumption and the use cost of the ball mill To make the milling more efficient, we must first be acquainted with the factors They are mainly the ball mill structure, the rotation speed, the ball mill media, the lining plate, the material fed and the feeding speed, etc2019年11月23日 In How to Reduce Arduino Power Consumption, we looked at ways to reduce power consumption within the Arduino by changing hardware or modifying codeHowever, there are also ways to reduce the power consumption of an Arduino by adding some simple external circuits In this article, we design some external circuits to control the power flow to our How to Reduce Arduino Power Consumption Using External 2019年11月15日 Removing the power LED can shave 285mA of current in normal mode In sleep mode, without the LED, the power consumption of Arduino UNO is just 308uA Lowering the Voltage Supply to an Arduino One of the very easy ways to reduce the power consumption of the Arduino board is to lower the supply voltageHow to Reduce Arduino Power Consumption Maker Pro2021年1月29日 Specific Power consumption of Vertical Roller Cement Mill for preimprovement phase Data of last 6 Large feed size in any case will reduce the mill production rateIncrease productivity of vertical roller mill using seven
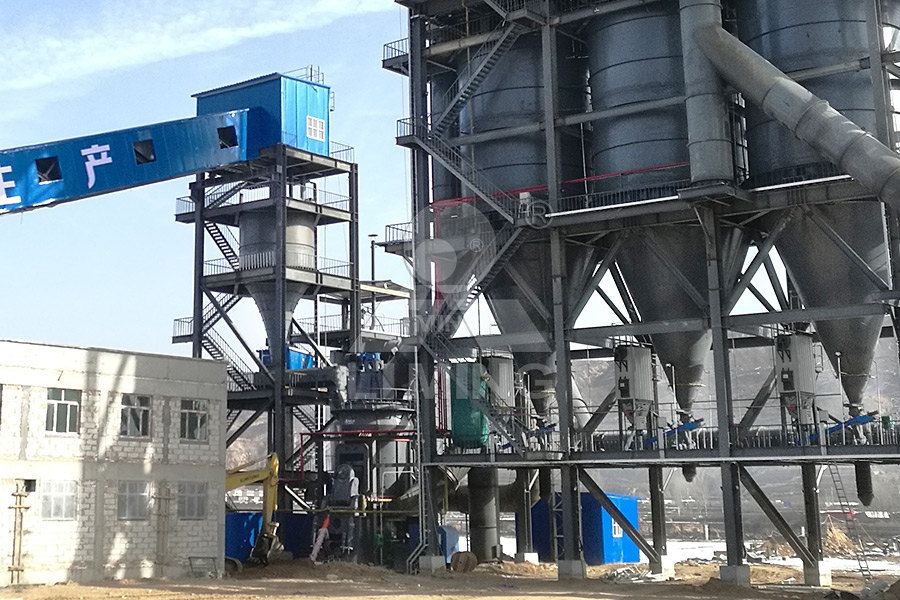
Reducing energy consumption of a raw mill in cement industry
2012年6月1日 Furthermore, the power consumption of the raw mill grinding process was reduced by 67 percent by using exterior hot gas, as suggested in an energy and exergy analysis of the mill by Atmaca Specific power consumption Metal ware rate Quality of the product If all the above mentioned parameters are optimized by experimentation on mills then mill output can be increased by 52 20% of its rated output and thereby reduce the specific energy consumption Addition ofOptimizing Electrical Energy Consumption In Cement Process 2015年2月16日 A typical comparison of three competing technologies is given in Table 1, demonstrating that an efficient ball mill/thirdgeneration separator, CKP/ball mill/thirdgeneration separator and vertical mill on a typical 4000Blaine limestone cement show little overall difference in energy consumptionBest energy consumption International Cement Review2023年8月22日 PoE Switch Power Consumption Explained The energy consumed per unit by a switch is an important factor for a buyer to know PoE switch power consumption differs not only based on its type and configuration but also on the IEEE standard for power consumption This standard is different for PoE, PoE+, and PoE++How to Reduce the Power Consumption of PoE Switches?
.jpg)
Power Consumption of Cement Manufacturing Plant
Nowadays, in the field of cement grinding system of the world cement industry, the major cement grinding equipments include loop flow ball mill, roller press, ball mill semifinishing system, and vertical mill system, in which ball mill and vertical mill are 2 major cement grinding systems in Cement Manufacturing Plants2020年8月12日 This study shows the performance of a currently running vertical roller coal mill (VRM) in an existing coalfired power plant In a power plant, the coal mill is the critical equipment, whose An investigation of performance characteristics and energetic 2022年5月9日 By initiating a CL for an industrial cement vertical roller mill (VRM), this study conducted a novel strategy to explore relationships between VRM monitored operational variables and their representative energy consumption factors (output temperature and motor power)Modeling of energy consumption factors for an industrial cement 2017年3月4日 The electric power consumption by this process run on ore mining and processing enterprises is variously estimated as a value from 5 to 20% of overall world electric powerSIZE REDUCTION BY GRINDING METHODS ResearchGate
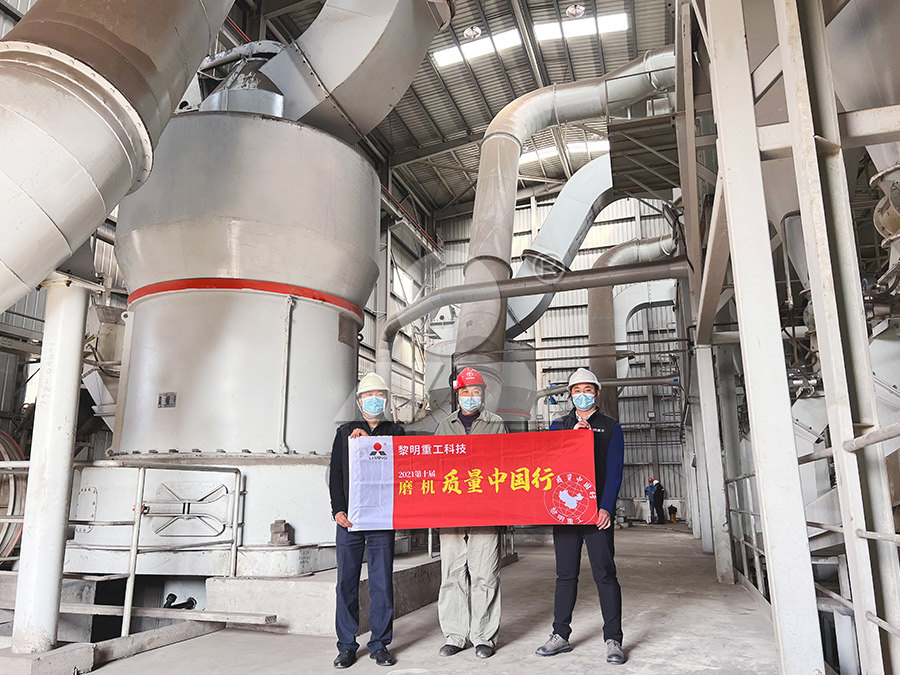
Charge behaviour and power consumption in ball mills:
2001年8月1日 Decreasing the fill level to 30% again increases the specific power consumption, (but by a smaller percentage than that of the last increase) The peak specific power consumption remains around 105% but continues to broaden For the 25% fill level the power curve is again translated higher by a smaller increment and again the peak broadensThe todate biggest mill size modular vertical roller mill 6700 C6 shows satisfactory results for cement and composite cement grinding This mill, installed in Northern Africa, is in operation Grinding Process Optimization Featuring Case Studies and would help to optimize power consumption, improve maintenance, reduce environmental issues, and make the process sustainable A few investigations have been conducted to model VRM performanceModeling of energy consumption factors for an industrial cement 2016年7月23日 \$\begingroup\$ there are many peripherals that can be turned off to reduce power consumption, so having SPI enabled vs disabled will impact current consumption There are many resources online about making What is the best way to estimate the power
.jpg)
How to measure the power consumption of your backend service
2020年9月21日 Measure power consumption directly from the socket The most reliable way is also the simplest way Buy a cheap watt hour meter, plug it into the socket between your wall and your server and you are golden This will always be the best way to measure power consumption because it will measure exactly what your server consumes2019年11月14日 With the modern manufacturing industry evolving and advancing and amid a more energy conscious society, high energy demand in manufacturing—particularly in machining—has drawn more and more attention Accurate energy consumption modelling is critical to the improvement of energy efficiency in machining In the existing energy models of Energy consumption model for milling processes considering 2017年9月11日 Used as a primary mill in existent plants, it can not only reduce energy consumption but also increase output However, its real advantage will lie in its use as an autonomous finish grinding millPerformance Evaluation of Vertical Roller Mill in Cement 2012年6月1日 In this study, the first and second law analysis of a raw mill is performed and certain measures are implemented in an existing raw mill in a cement factory in order to reduce the amount of energy consumption in grinding process The first and second law efficiencies of the raw mill are determined to be 615% and 164%, respectivelyReducing energy consumption of a raw mill in cement industry

Ball Mill Design/Power Calculation 911Metallurgist
2015年6月19日 Ball Mill Motor/Power Sizing Calculation; Ball Mill Design/Sizing Calculator; The power required to grind a material from a given feed size to a given product size can be estimated by using the following equation: where: W = power consumption expressed in kWh/short to (HPhr/short ton = 134 kWh/short ton)2022年6月24日 6 Energy consumption Under the same power condition, the grinding efficiency of the ball mill is low, and the energy consumption is high The vertical mill has high grinding efficiency and low energy consumption, and the power consumption is only 40%50% of the ball mill 7 Finished product qualityHow to choose between ball mill and vertical roller mill?2024年1月15日 Sun et al [9] carried out study of a roller mill (HRM 4800 by Hefei Zhong Ya, China) and analysed air flow patterns in the mill to improve the energy efficiency of the mill Shah et al [ 10 ] used modelling to optimise the performance of a coal pulveriser by studying the influence of variation in inlet vane angles on the collection efficiency of the powder and desired Optimisation of the performance of a new vertical roller mill by