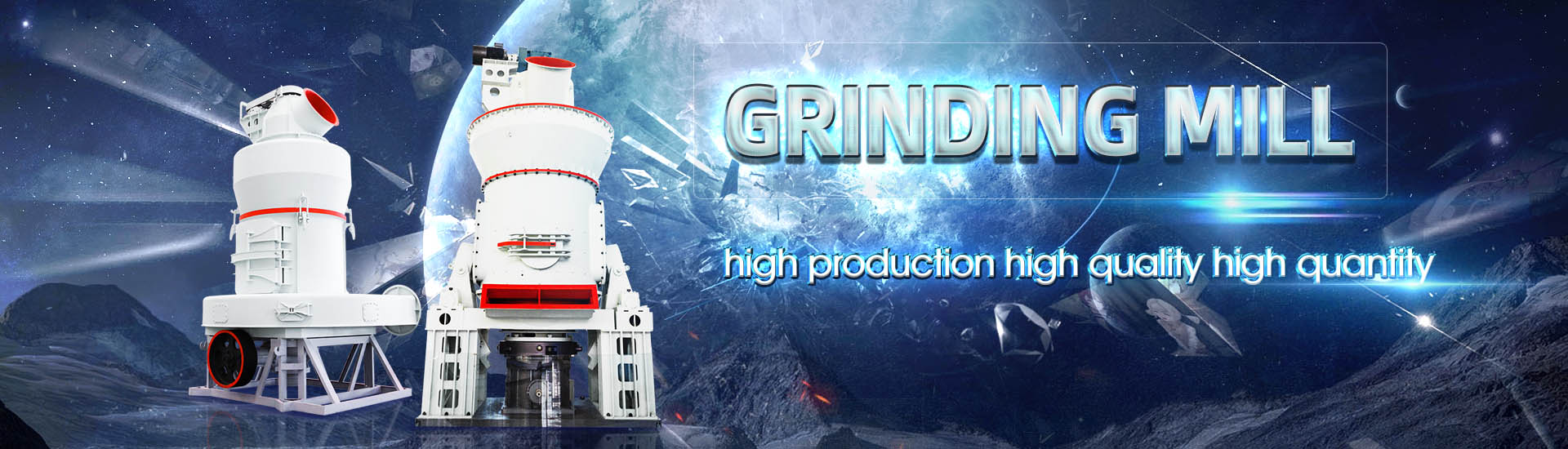
Coal mill end cover crack repair
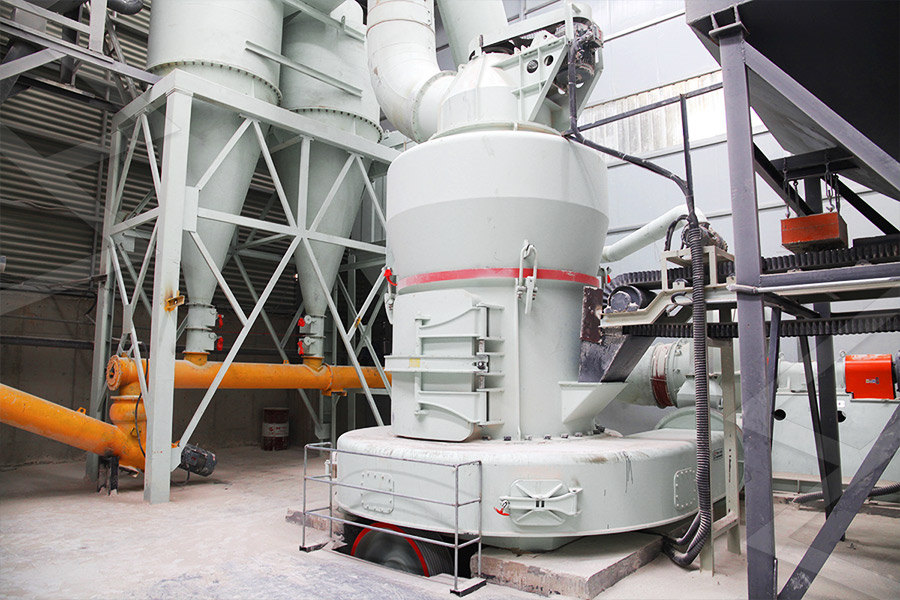
CNA Method for repairing feeding end cover of coal
The invention discloses a method for repairing a feeding end cover of a coal mill, which comprises the following steps: repairing the outer side of the damaged part, namely polishing theA repair method and feed end technology, applied in the field of coal mills, can solve the problems of coal mill downtime, economic losses, high replacement costs, etc, and achieve the effect of Coal mill feeding end cover repair method Eureka Patsnap提供MBS2736棒磨机出料端盖修复更换技术word文档在线阅读与免费下载,摘要:工艺与设备化工设计通讯 MBS2736棒磨机出料端盖修复更换技术 文档网The document outlines the steps for an overhaul procedure of a coal mill It involves 21 steps to remove, inspect, replace, and reinstall components Key steps include removing the mill cover, Overhaul Procedure For Coal Mill PDF Scribd
.jpg)
#1炉1E磨煤机磨辊辊套断裂原因分析及防范措施百度文库
Abstract: for the crack of grinder roll in the operation of one boiler coal mill in the power plant, by analyzed, we found the main reason in grinder roll of coal mill and put forwards to prevention 2024年3月25日 Here are some common issues with ball mill end covers and troubleshooting tips to resolve them: 1 Leakage Symptoms: Material or lubricant leakage is observed around the Troubleshooting Common Issues with Ball Mill End CoverAbstract: The cracks occurrence in outlet end cover of mill A of boiler No5 in a power plant was introduced Aiming at current situation, relevant emergency measures were adopted, the crack Treatment of cracks on end cover of mill and cover replace Atox Vertical Roller Mill, Maintenance and Repair Free download as Powerpoint Presentation (ppt), PDF File (pdf), Text File (txt) or view presentation slides online The document Atox Vertical Roller Mill, Maintenance and Repair
.jpg)
Crack Repair of Coal Mill Cylinder Manhole Door in 360 MW Unit
Semantic Scholar extracted view of "Crack Repair of Coal Mill Cylinder Manhole Door in 360 MW Unit" by Liu Xinju Skip to search form Skip to main content Skip to account menu Semantic 2015年8月1日 In this paper, a review of researches done on the mill control and methods employed for fault diagnosis of coal mills is provided, with the aim of improving performance Review of control and fault diagnosis methods applied to coal 2015年8月1日 Mill problems originate mainly due to poor controls or faults occurring within the milling system As discussed by GQ Fan and NW Rees [3], the control of mills remains very simple in most of the power plants due to the fact that the mill system is highly nonlinear with strong coupling among the variables and it is very difficult to measure some important Review of control and fault diagnosis methods applied to coal mills For any Emergency Industrial Repairs, please contact us for an initial survey/quotation Coal Mill Bearing Casting L3 Olympic House, Westminster Industrial Estate, Measham, Derbyshire, DE12 7DS Telephone: + 44 (0) 1530 : damaged cast iron components Cast Iron Welding Metal Stitching RepairsCast Iron Welding Metal Stitching Repairs
.jpg)
BALL MILL GIRTH GEAR PINION END COVER ASSEMBLY
OEM Manufacturer of BALL MILL GIRTH GEAR PINION END COVER ASSEMBLY Ball Mill Girth Gear Pinion and Trunnion Head Assembly in Ghaziabad Manufacturer and Supplier, Ball Mill Pinion Shaft Manufacturer For Industrial Piyali Group, Ghaziabad(India), Manufacturer of all types of grinding mill spares available for export from Ghaziabad, India and Cement Plant 2020年7月1日 The external surface of the coal mill shaft had been welded, and the poor welding process resulted in a large number of welding defects such as cracks, slag inclusions and lack of fusion in the Fracture failure analysis of coal mill shaft ResearchGateCement mill – Cracks in the mill ends This case of damage was investigated to decide if repairwelding is a sufficient solution when the ends of a cement mill start to crack and are in danger of breaking To ensure that the damage is repaired reliably, the cause of the damage must be investigated and weld seams examined carefullyCement mill – Cracks in the mill ends2020年11月26日 The WA Russia team initially started the repair using WA GAMMA 182E electrodes, as this gave better access to the base of the crack, which was difficult to weld using an automated process Once the base of the crack had been sufficiently welded with the GAMMA 182E electrodes, the team could continue with an automated process to rebuild, using both Kiln Tyre Repair – Facing the unknown Engineer Live
.jpg)
Mediumspeed coal mill wearresistant ceramic liner Composite
As an important pulverized coal preparation equipment, medium speed mill has been facing the test of wear since its birth According to statistics, about 80% of the parts that fail in medium speed grinding belong to the direct or indirect consequences caused by metal wearHow to Repair Ball Mill Inside Parts Repairing ball mill inside parts can be a challenging task, but it is essential to ensure the optimal functioning of the mill Here are some steps to repair the inside parts of a ball mill: Shutdown the mill: Before starting any repair work, it is crucial to shut down the mill and isolate it from the power What are the Components of Ball Mill Inside and How to Repair 2020年8月12日 This study shows the performance of a currently running vertical roller coal mill (VRM) in an existing coalfired power plant In a power plant, the coal mill is the critical equipment, whose An investigation of performance characteristics and energetic Coal Mill Free download as PDF File (pdf), Text File (txt) or view presentation slides online This dissertation examines technologies to enhance the maintenance performance of coal pulverizers through new technologies It presents the results of testing modifications to rotating throat assemblies, spider and guide wear plates, ball loading cylinders, classifier cones, and Coal Mill PDF Mill (Grinding) Industries
.jpg)
WOA2 Novel external flushing and Google Patents
The "Novel External Flushing and Lubrication of Top/Upper Bearing of Gear Box of Coal Mill Improved Filtration of Oil" consisting of externally filtered oil (16) sent via hose(s) (15) through hole(s) (17) provided in Upper Bearing Housing Cover (13) for FLUSHING of contaminants and LUBRICATING Top Bearing (9,10,11) by oil spray/streams (18, 19, 20), and the system Download scientific diagram 9 Crack at end of cover plate of Yellow Mill Pond Bridge propagating into web (Fisher 1984) from publication: Incorporation of Fatigue Detail Classification of Steel 9 Crack at end of cover plate of Yellow Mill Pond 2012年5月1日 Coal fired power plants are heavily used due to large and long lasting coal resources compared with oil or natural gas An important bottleneck in the operation of this particular kind of plants, however, is the coal pulverization process, which gives rise to slow takeup rates and frequent plant shutdowns (Rees Fan, 2003)In typical coal fired power plants, Derivation and validation of a coal mill model for controlThe invention relates to a pull rod sealing structure for a coal mill in a power plant and belongs to the technical field of industrial machinery The pull rod sealing structure comprises a pull rod, a front coneshaped cover body, a rear sealing seat and a middle sealing air cavity A ringshaped groove is formed in the inner side in the middle of the coneshaped cover body, and a ring CNA Pull rod sealing structure of loadvariable coal mill
.jpg)
Common faults and troubleshooting of linear vibrating screen for coal
2023年2月15日 Sometimes coal is unevenly distributed on the screen surface Vibrating screen troubleshooting: If there is no coal in the front section of the screen, adjust the eccentric blocks forward appropriately If there is no coal in the middle section, the mass of the eccentric block is too light and the amplitude cannot meet the requirementsThe raw coal is delivered to the feeding device of the coal mill, and at the same time the hot air with a temperature of about 300°C also enters the feeding device through the air inlet pipe, where the raw coal containing moisture starts to exchange heatHow To Maintain a Coal Pulverizer? (All You Need To Know)2021年5月12日 Babcock is helping to keep South Africa’s power going, following the award of a mill maintenance contract at a major power station Babcock’s diverse scope of work for the fiveyear contract covers the daytoday upkeep of the milling plant as well as outage repairs, quality and inventory support, and onsite training and upskilling of the surrounding local communitiesMill maintenance contract at power station awarded Energize2016年2月4日 Regular JB weld should work on the valve cover crack as it is rated for 550 degrees F, and I know the valve cover will NEVER even hit close to that, not even half of the 550 The extreme heat JB Weld is rated for 2400 degrees F, and is usually used on cracked exhaust manifolds and suchValve cover hairline crack epoxy BimmerFest BMW Forum
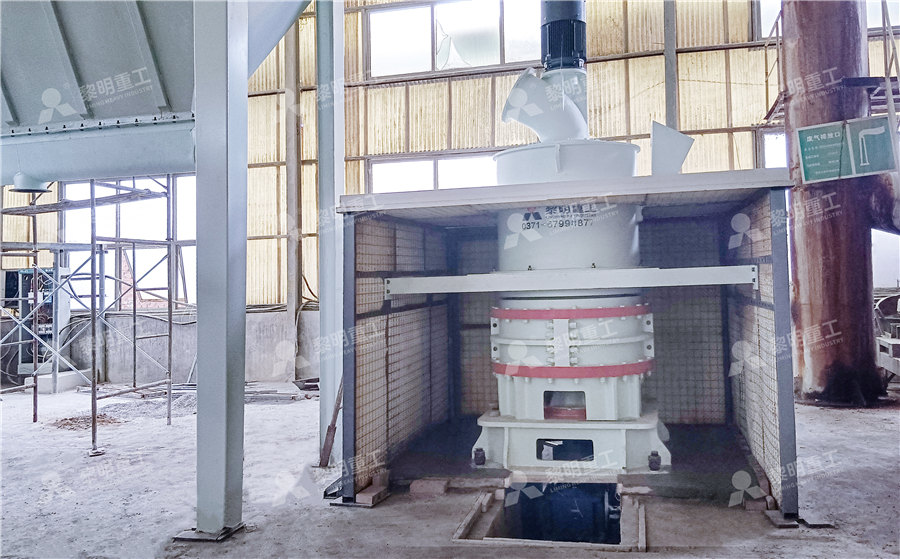
Coal Tar Enamel Repair Guide Bureau of Reclamation
various stages of coal tar enamel degradation and provides suggested maintenance options, with the goal of maximizing service life and minimizing coating maintenance costs It gives recommended procedures for proper surface preparation and application of 100% solids epoxy coating spot repairs to damaged areas of coal tar enamel2014年7月1日 Due to different characteristics of coal, types of coal mills are applied including ball mill, disk mill, roller mill, hammer swing sledge mill and fan mill [1] Among different types of coal mills, fan mill presents advantages of compact structure, less construction cost, less installed area and less electricity consumption, and is more applied in thermal power plants with brown Crack cause analysis of pulverizing wheel in fan mill of 600MW When the trunnion liner was removed there was evidence of slurry racing which had scalloped out areas of the mehanite mill end casting Also two cracks were found, each about one inch long, They had not attempted the repair of a ball mill prior to this mill although they had repaired cracks in a rotating kiln head of similar sizeRepair Ball Mill Discharge Trunnion Crack 911MetallurgistCement mill – Cracks in the mill ends This case of damage was investigated to decide if repairwelding is a sufficient solution when the ends of a cement mill start to crack and are in danger of breaking To ensure that the damage is repaired reliably, the cause of the damage must be investigated and weld seams examined carefullyCement mill – Cracks in the mill ends
.jpg)
Reliable Coal Pulverizers and Mills » Babcock Wilcox
Reliable coal pulverizer performance is essential for sustained fullload operation of today's power plants An effective pulverizer must be capable of handling a wide variety of coals and accommodating load swings in utility boilers as large 2023年4月22日 A simple and functional repair to prevent a crack from spreading on a cracked outboard cover / cowlingHow to repair a crack on an outboard cover The HillBilly ToolBox From the coal yard, the coal is transfer to the mill bunkers through conveyor belt The bunkers are sized for an effective capacity of twelve (12) hours at BMCR with design coal Each mill bunker has one hopper, connected to the feeders Mills operate when the bunker coal gate valves are opened, coal is allowed to flow to the gravimetric feedersAnalysis of the Coal Milling Operations to the Boiler Parameters2021年2月14日 Line 2 of a company's raw material mill is FLSmidthATOX50 roller mill, which was put into use in July 2007 There are three rollers, each roller is equipped with a pull rod head, as shown in Figure 1 The A end is connected with the piston rod of the hydraulic cylinder through the stretching rod, and the lifting of the grinding roller is completed through the hydraulic systemAnalysis and solution of crack of ATOX50 raw material mill tie rod
.jpg)
Cement mill – Cracks in the mill ends
Cement mill – Cracks in the mill ends This case of damage was investigated to decide if repairwelding is a sufficient solution when the ends of a cement mill start to crack and are in danger of breaking To ensure that the damage is repaired reliably, the cause of the damage must be investigated and weld seams examined carefullyCement mill – Cracks in the mill ends This case of damage was investigated to decide if repairwelding is a sufficient solution when the ends of a cement mill start to crack and are in danger of breaking To ensure that the damage is repaired reliably, the cause of the damage must be investigated and weld seams examined carefullyCement mill – Cracks in the mill ends2024年8月6日 In an integrated steel plant, the pulverized coal injection (PCI) mill plays an important role in providing pulverized coal to the blast furnace The main purpose of using PCI coal is to reduce the hot metal production cost through the utilization of noncoking coal and to extend the available coke oven life Any unplanned outage of the PCI mill leads to increase in Failure Analysis of Pulverized Coal Injection (PCI) Mill Grinding If the pulverized coal undergoes spontaneous heating and the coal mill is restarted with hot embers present, an explosion or fire is possible Although this does not happen often, the chances increase when a coal mill is frequently shut down and then restarted A coal mill system that goes down, particularly under load, must be treated with Coal Grinding Systems Safety Considerations PEC Consulting
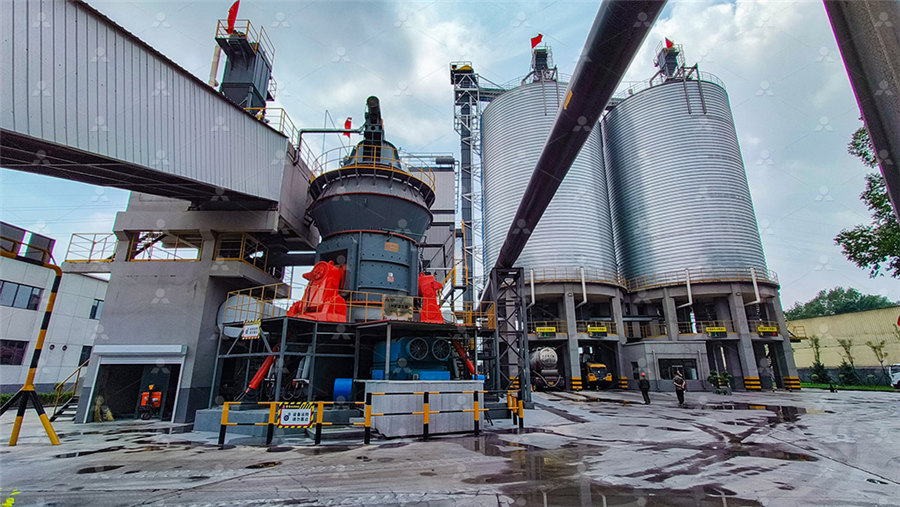
Review of control and fault diagnosis methods applied to coal mills
2015年8月1日 Mill problems originate mainly due to poor controls or faults occurring within the milling system As discussed by GQ Fan and NW Rees [3], the control of mills remains very simple in most of the power plants due to the fact that the mill system is highly nonlinear with strong coupling among the variables and it is very difficult to measure some important For any Emergency Industrial Repairs, please contact us for an initial survey/quotation Coal Mill Bearing Casting L3 Olympic House, Westminster Industrial Estate, Measham, Derbyshire, DE12 7DS Telephone: + 44 (0) 1530 : damaged cast iron components Cast Iron Welding Metal Stitching RepairsCast Iron Welding Metal Stitching RepairsOEM Manufacturer of BALL MILL GIRTH GEAR PINION END COVER ASSEMBLY Ball Mill Girth Gear Pinion and Trunnion Head Assembly in Ghaziabad Manufacturer and Supplier, Ball Mill Pinion Shaft Manufacturer For Industrial Piyali Group, Ghaziabad(India), Manufacturer of all types of grinding mill spares available for export from Ghaziabad, India and Cement Plant BALL MILL GIRTH GEAR PINION END COVER ASSEMBLY2020年7月1日 The external surface of the coal mill shaft had been welded, and the poor welding process resulted in a large number of welding defects such as cracks, slag inclusions and lack of fusion in the Fracture failure analysis of coal mill shaft ResearchGate
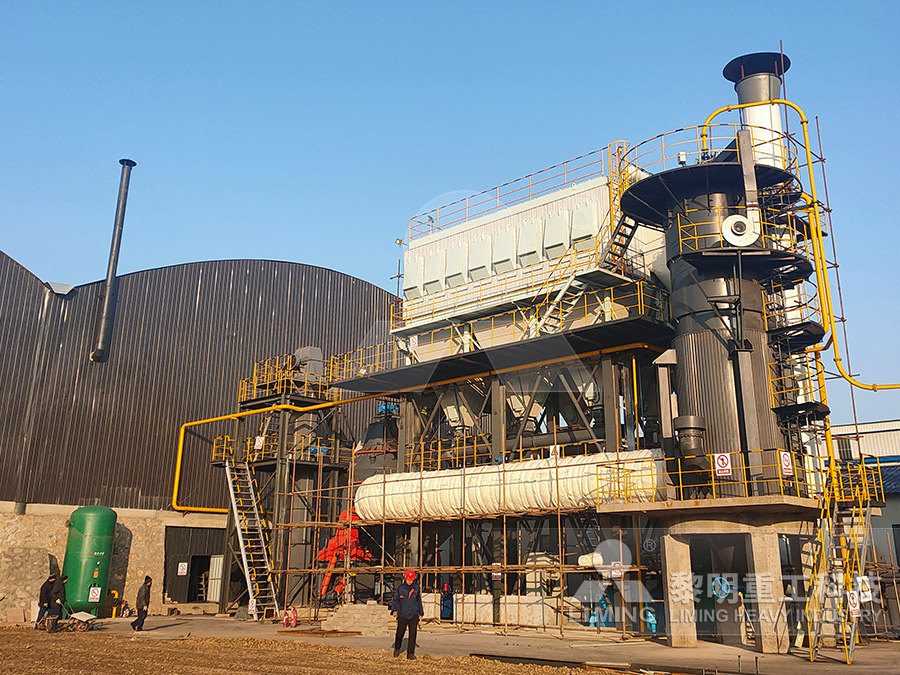
Cement mill – Cracks in the mill ends
Cement mill – Cracks in the mill ends This case of damage was investigated to decide if repairwelding is a sufficient solution when the ends of a cement mill start to crack and are in danger of breaking To ensure that the damage is repaired reliably, the cause of the damage must be investigated and weld seams examined carefully2020年11月26日 The WA Russia team initially started the repair using WA GAMMA 182E electrodes, as this gave better access to the base of the crack, which was difficult to weld using an automated process Once the base of the crack had been sufficiently welded with the GAMMA 182E electrodes, the team could continue with an automated process to rebuild, using both Kiln Tyre Repair – Facing the unknown Engineer LiveAs an important pulverized coal preparation equipment, medium speed mill has been facing the test of wear since its birth According to statistics, about 80% of the parts that fail in medium speed grinding belong to the direct or indirect consequences caused by metal wearMediumspeed coal mill wearresistant ceramic liner Composite How to Repair Ball Mill Inside Parts Repairing ball mill inside parts can be a challenging task, but it is essential to ensure the optimal functioning of the mill Here are some steps to repair the inside parts of a ball mill: Shutdown the mill: Before starting any repair work, it is crucial to shut down the mill and isolate it from the power What are the Components of Ball Mill Inside and How to Repair
.jpg)
An investigation of performance characteristics and energetic
2020年8月12日 This study shows the performance of a currently running vertical roller coal mill (VRM) in an existing coalfired power plant In a power plant, the coal mill is the critical equipment, whose Coal Mill Free download as PDF File (pdf), Text File (txt) or view presentation slides online This dissertation examines technologies to enhance the maintenance performance of coal pulverizers through new technologies It presents the results of testing modifications to rotating throat assemblies, spider and guide wear plates, ball loading cylinders, classifier cones, and Coal Mill PDF Mill (Grinding) Industries