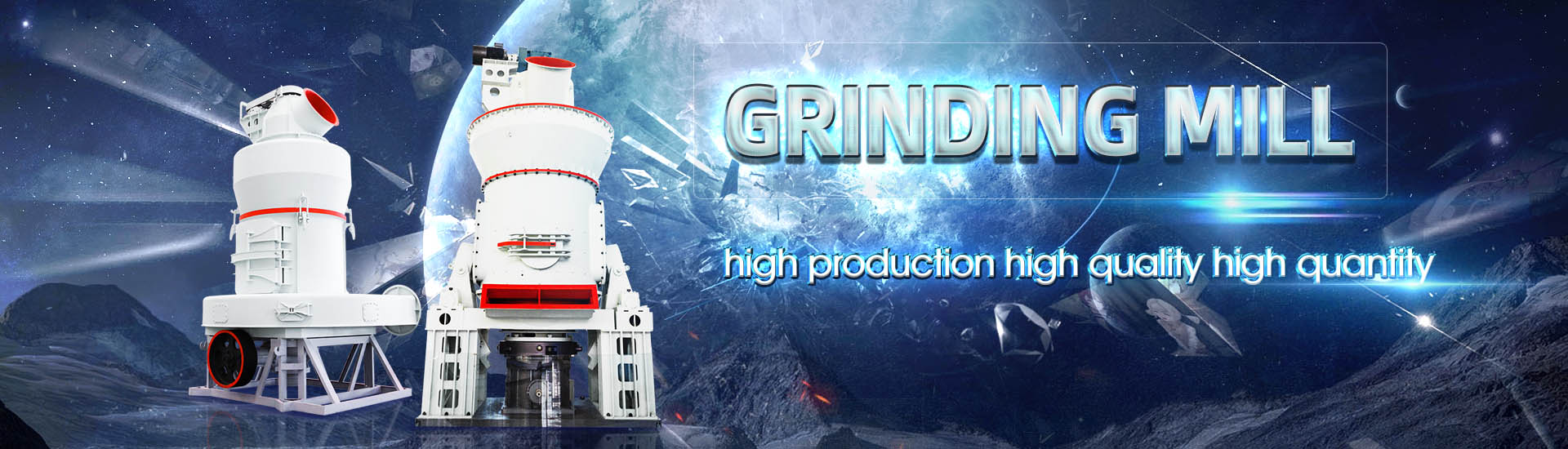
Preconditions for powder making process of alkaline furnace lining materials
.jpg)
Surface modification and functionalization of powder materials by
Unlike many other vaporphase deposition techniques, atomic layer deposition (ALD) is not a lineofsight dependent process ALD processes are based 展开2020年1月1日 Currently, gas atomization is the leading technology for producing metal powders for AM The feedstock material has three process steps such as melting, atomization and Atomization processes of metal powders for 3D printing2022年3月1日 The design of lightweight wear linings is crucial in terms of the energy and resource efficiency of industrial furnaces and quality of final products This review aims to Design, fabrication and properties of lightweight wear lining 2022年10月15日 In the scope of this work, the influence of three different powder producers of Ti6Al4V, on density, chemical composition, and mechanical properties of build samples, is Influence of powder production process and properties on
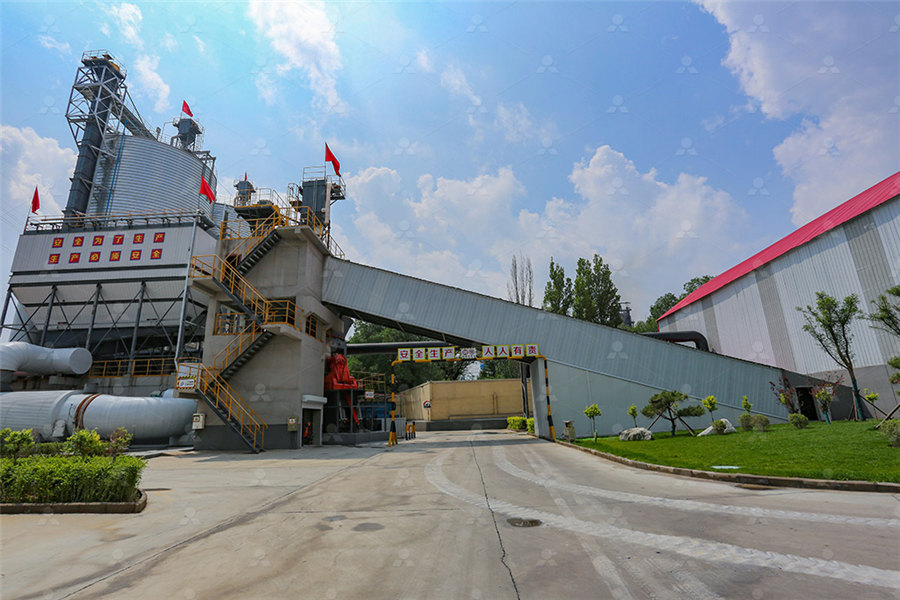
Innovative Refractory Technology for Coreless Induction Furnaces
This paper will discuss a completely new generation of refractories and address care of structural components, installation, sintering and optimal operation of coreless induction furnaces to 2019年11月10日 The typical approach for the fabrication of alkaliactivated foamed materials is borrowed from the procedure used in the cement industry, which consists of the addition to an Design of alkaliactivated aluminium powder foamed materials for The mechanism of insituformation of AlNi intermetallic lining layers during microchannel formation in nickel bodies by a powdermet allurgical process has been investigated Formation of AlNi Intermetallic Layers Lining Microchannels The technical indicators for quality of atomized powder are oxygen content and content of nonmetallic inclusions The former is mainly from surface oxidation of particles during atomization, Atomization Process to Produce Powder SpringerLink
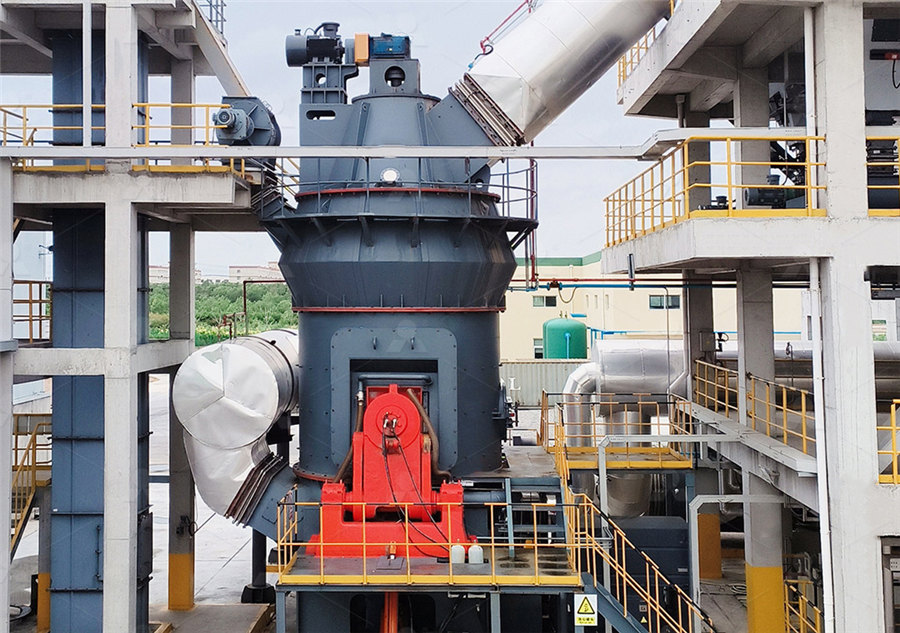
An impact of the ladle lining on the refining of reinforced steel
2019年9月12日 When refining steel by blowing powders, the ladle lining material plays a serious role The dependency graphs of the degree of desulfurization on the consumption of 2024年3月13日 The effect of lining materials (Al2O3 and Al2O3–MgOAl2O3) of ladle on evolution of nonmetallic inclusions in aluminumkilled (Alkilled) steel during ladle furnace (PDF) Effect of ladlelining materials on inclusion evolution in Al 2019年9月16日 For the lining of induction furnace, refractory materials are normally monolithic refractories made of dry powder which is required to be compacted with homogenous density Further, there are heat losses by Refractory Lining of Coreless Induction Furnace2005年11月30日 Typically, the refractory lining of a blast furnace consists of a combination of different refractory materials chosen for different portions of the furnace, as well as distinct process conditions Wear mechanism for blast furnace hearth refractory lining
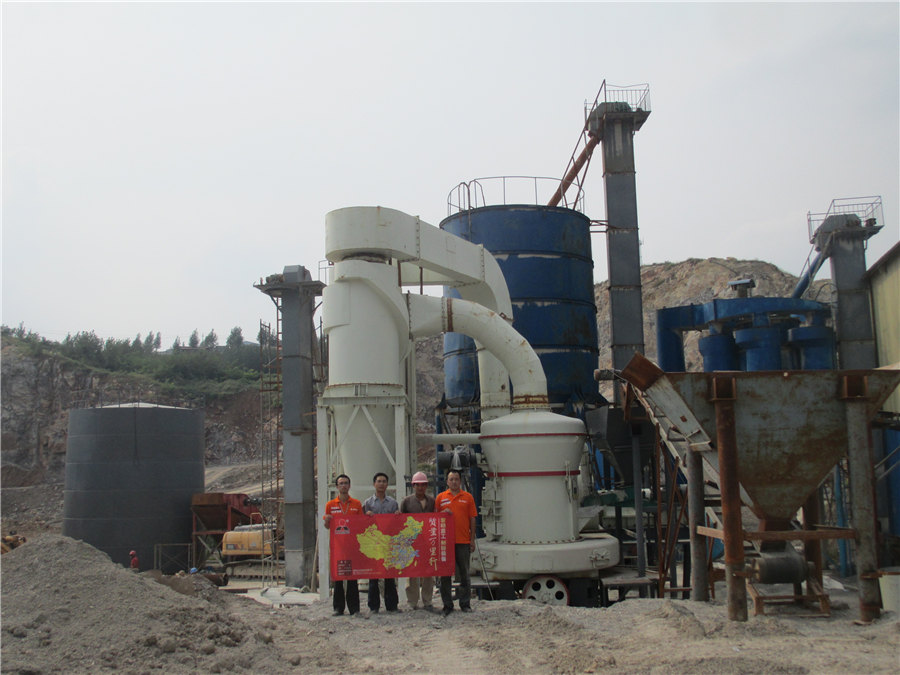
Historical overview of refractory lining in the blast
2022年6月30日 The majority of refractories used today are associated with the iron and steel industries Typically, the refractory lining of a blast furnace consists of a combination of different refractory 2016 D Ç î ñ Z r î ó Z î ì í ò U v } U Ì Z Z µ o ] U h 81 Table 4 Effect of K on CRI and CSR Sample Property (CRI/CSR) No Added K Medium K Content High K ContentEFFECT OF ALKALINE ELEMENTS ON COKE STRUCTURE UNDER BLAST FURNACE 2022年3月1日 Lightweight wear lining refractories are generally fabricated by replacing conventional dense aggregates with lightweight aggregates Several process routes, such as partial sintering, insitu decomposition, adding poreforming agent, direct foaming, and superplastic foaming, have been developed to fabricate lightweight aggregatesDesign, fabrication and properties of lightweight wear lining 2020年9月30日 Its role is not only the ladle for carrying molten steel in the traditional sense but also the core carrier of the refining process outside the furnace The choice of Refractory Materials for Ladle Lining is not only related to the life and cost of the ladle but also directly affects the output and cleanliness of molten steel Let’s look at Development of Refractory Materials for Ladle Lining
.jpg)
How to choose the refractory materials for the lining of medium
2022年7月8日 Alkaline furnace lining materials are dry ramming materials made of fused or highpurity magnesia, powder, aluminum magnesium spinel powder and sintering agent Its particle size distribution conforms to the theory of maximum bulk density, so dense and uniform heating furnace lining can be obtained through various knotting methodsDepending on the type of the furnace and the substance of the smelting, the thickness of the refractory lining is usually between 80mm300mm In certain applications, there may be two layers of refractory lining of different materials For example, the What is a Refractory Lining? Materials, Selection, and Types of These are incomparable to metal materials and organic polymer materials But compared with metal materials, it has low breaking strength and lack of ductility Compared with organic polymer materials, the density is higher and the manufacturing process is complicated The Forming of Silica Mullite Bricks In RS Factory Get Free QuoteWhy are Refractory Bricks Suitable for HighTemperature Furnace Lining?It is incorrect procedure to install the spout above the working lining (Reference Figure 4) which inhibits the free movement of the working lining and adds stress that results in cracks and metal penetration • C Coil Grout: o Must be smooth and concentric to allow the lining to expand and contract freely and avoid hangInnovative Refractory Technology for Coreless Induction Furnaces
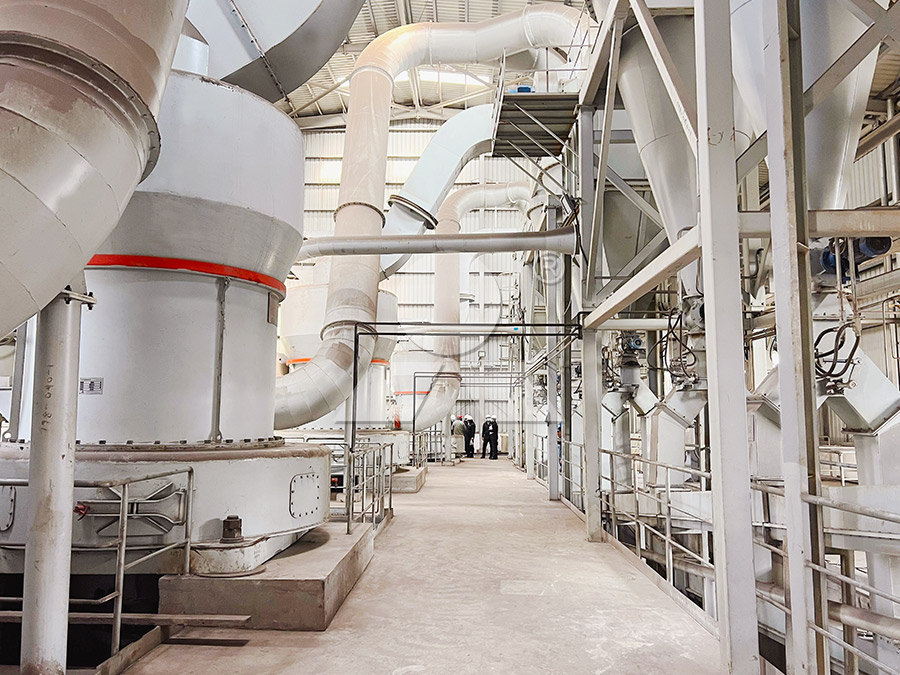
Formation of AlNi Intermetallic Layers Lining Microchannels
Division of Materials Science, Faculty of Engineering, Hokkaido University, Sapporo 060–8628, Japan The mechanism of insitu formation of AlNi intermetallic lining layers during microchannel formation in nickel bodies by a powdermetallurgical process has been investigatedThe furnace lining material comprises the following raw materials in parts by weight: 7590 parts of fused magnesia, 051 part of boric acid powder and 12 parts of fine silicon dioxide powder; when a slag line and the portion, above the slag line, of the furnace lining material are prepared, 615 parts of emery powder needs to be added; when the portion, below the slag line, of the Furnace lining material used for mediumfrequency induction furnace 2020年5月6日 Refractory Lining of the Electric Arc Furnace satyendra; May 6, 2020; 0 Comments ; AC EAF, DC EAF, EAF, EBT, Fettling, guniting, hearth, magnesite, Monolithic lining, roof, Taphole,; Refractory Lining of the Electric Refractory Lining of the Electric Arc Furnace – Some steel grades are only suitable for smelting in alkaline furnaces When smelting high manganese steel grades and alloys in an acid furnace, (MnO) will combine with SiO2 in the furnace lining to form a low melting point silicate, thus rapidly damaging the furnace liningInduction Furnace Steel Making Hani Metallurgy
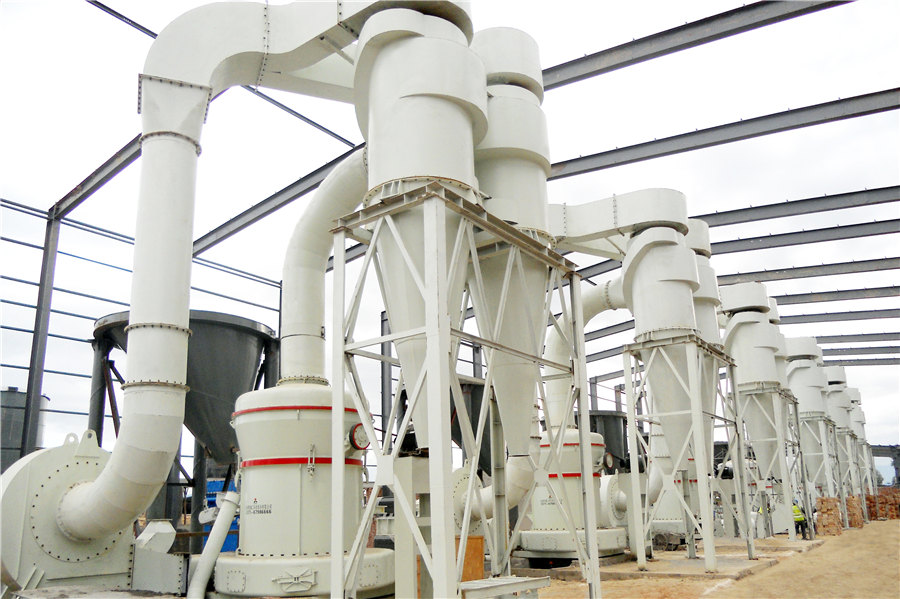
Integrated hydrometallurgical process for production of zinc from
DOI: 101016/S03043894(00)003058 Corpus ID: ; Integrated hydrometallurgical process for production of zinc from electric arc furnace dust in alkaline medium @article{Youcai2000IntegratedHP, title={Integrated hydrometallurgical process for production of zinc from electric arc furnace dust in alkaline medium}, author={Zhao Youcai and Robert R 2018年3月27日 Furnaces are most commonly used for melting of ferrous metals and its alloy materials Induction furnaces use electrical power so that they are more advantageous as no fuel is required(PDF) Review of Refractory Materials for Innovativeminor additives such as granite powder, alite cement, and black sand were manufactured The pellets of these materials with a varying additive percentage from 5 to 30% were prepared using hydraulic pressure The heattreated pellets were physically and mechanically characterized to ensure the brick properties suitable for furnace lining Manufacturing and Mechanical Characterization of FlyAsh which could cause a lining failure during restart Most of the lining shrinkage is caused by the contraction of the aluminum in cracks of the lining as aluminum has shrinkage greater than 6% [2] In the lining apart from hot metal contact area sills, door jambs and furnace door are the most vulnerable area to thermal shock The energy efficient Selection of Proper Refractory Materials for Energy Saving in
.jpg)
Fireclay refractory bricks used for the construction of furnace lining
These results were within the established refractory standards for fireclay of 170230 g/cm 3 (Amkpa et al 2017)The results were also comparable to those found in clays from other locations 2016年3月21日 With increasing demand of highquality clean steel, cleanliness is of paramount importance in steel production and casting Tundish plays an important role in controlling the continuously cast steel quality as it links a batch vessel, ladle, to a continuous casting mold Tundish is also the last vessel in which metal flows before solidifying in mold For controlling Tundish Technology for Casting Clean Steel: A Review2014年8月15日 Different types of BF refractories Different types of refractories which are used in blast furnace lining are described below Baked carbon blocks – Micro porous carbon block, semi graphitic carbon block, and micro porous Refractory lining of blast furnace – IspatGuruTip 1 Evaluate the furnace liner with IR thermography inspection — Infrared (IR) thermography scans are essential for evaluating the quality of the furnace lining Lining quality is critical to protect the steel from excess heat and limit heat Achieving Furnace Lining Efficiency Foundry
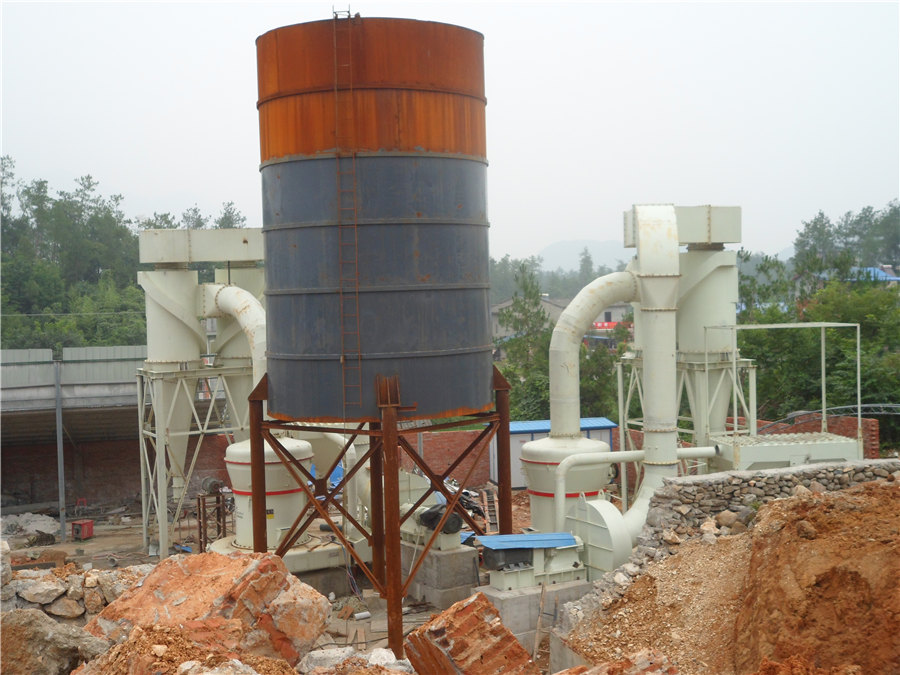
An impact of the ladle lining on the refining of reinforced steel
2019年9月12日 Dependence of desulfurization degree on the silicocalcium consumption in the dolomite lined ladles (1), schamotte (2), silicium oxide (3) (1,000 kg surface furnace slag): 1 dolomite lining; 2 As everyone knows, the desulfurization of Manufacture Of Iron And Steel By Melting process will be carried out under the strong condition of alkalescence, because acidity or neutral induction furnace melting are not suitable for making high basicity slag, therefore, the sweetening power of slag is very limitedBy the source of sulphur in the control raw material, the sulphur content in External desulfurizer for induction furnace and steelmaking furnace 2023年6月25日 This study investigated the synthesis of AgSnO2ZnO by powder metallurgy methods and their subsequent electrical contact behavior The pieces of AgSnO2ZnO were prepared by ball milling and hot Powder Metallurgy: Materials and Processing ResearchGate2013年3月28日 Refractory lining of a Basic Oxygen Furnace satyendra; March 28, 2013; 11 Comments ; charge pad, g carbon converte zones, gunning, slag coting, slag splashing,; Refractory lining of a Basic Oxygen Furnace The purpose of a refractory lining in a basic oxygen furnace (BOF) is to provide maximum furnace availability during operation of the converter in Refractory lining of a Basic Oxygen Furnace – IspatGuru
.jpg)
Preparation of geopolymers from alkaline thermally activated
2024年9月27日 Then, another richcalcium raw material was added to enhance the strength The low reactivity of raw materials like granite waste powder and burnt coal cinder can be improved by alkali thermal activation because the calcination of the raw materials and alkaline activators positively influences the reactivity of these raw materials2013年4月1日 Besides, the high generation of siderurgical waste (3040 kg/ton steel) includes dusts and sludges from blast furnace and Basic Oxygen Furnace, and the materials containing high Fe and carbon The cycle and effect of zinc in the blastfurnace process2022年11月29日 5 New process and new materials of furnace lining materials ① In the traditional lining materials, ultrafine powder (mostly in a few microns) can improve the corrosion resistance and thermal shock stability of lining materials, such as silicon powder, aluminum oxide powder, white corundum powder, spinel powder, etc ② Dry formingWhat are the types of lining materials for medium frequency 2020年1月21日 The use of manganesecontaining materials as part of the blastfurnace charge in case of the BF3 furnace (EMZ) resulted in a decrease of lining temperature on the lower furnace levels (bottom levels of furnace stack, belly and bosh) on average by 100 °C, while stabilizing the temperature distribution along the circumference (Fig 3), which provided a Experience of Using ManganeseContaining Materials in BlastFurnace
.jpg)
Refractory Lining of Coreless Induction Furnace
2019年9月16日 For the lining of induction furnace, refractory materials are normally monolithic refractories made of dry powder which is required to be compacted with homogenous density Further, there are heat losses by 2005年11月30日 Typically, the refractory lining of a blast furnace consists of a combination of different refractory materials chosen for different portions of the furnace, as well as distinct process conditions Wear mechanism for blast furnace hearth refractory lining2022年6月30日 The majority of refractories used today are associated with the iron and steel industries Typically, the refractory lining of a blast furnace consists of a combination of different refractory Historical overview of refractory lining in the blast 2016 D Ç î ñ Z r î ó Z î ì í ò U v } U Ì Z Z µ o ] U h 81 Table 4 Effect of K on CRI and CSR Sample Property (CRI/CSR) No Added K Medium K Content High K ContentEFFECT OF ALKALINE ELEMENTS ON COKE STRUCTURE UNDER BLAST FURNACE
.jpg)
Design, fabrication and properties of lightweight wear lining
2022年3月1日 Lightweight wear lining refractories are generally fabricated by replacing conventional dense aggregates with lightweight aggregates Several process routes, such as partial sintering, insitu decomposition, adding poreforming agent, direct foaming, and superplastic foaming, have been developed to fabricate lightweight aggregates2020年9月30日 Its role is not only the ladle for carrying molten steel in the traditional sense but also the core carrier of the refining process outside the furnace The choice of Refractory Materials for Ladle Lining is not only related to the life and cost of the ladle but also directly affects the output and cleanliness of molten steel Let’s look at Development of Refractory Materials for Ladle Lining2022年7月8日 Alkaline furnace lining materials are dry ramming materials made of fused or highpurity magnesia, powder, aluminum magnesium spinel powder and sintering agent Its particle size distribution conforms to the theory of maximum bulk density, so dense and uniform heating furnace lining can be obtained through various knotting methodsHow to choose the refractory materials for the lining of medium Depending on the type of the furnace and the substance of the smelting, the thickness of the refractory lining is usually between 80mm300mm In certain applications, there may be two layers of refractory lining of different materials For example, the What is a Refractory Lining? Materials, Selection, and Types of
.jpg)
Why are Refractory Bricks Suitable for HighTemperature Furnace Lining?
These are incomparable to metal materials and organic polymer materials But compared with metal materials, it has low breaking strength and lack of ductility Compared with organic polymer materials, the density is higher and the manufacturing process is complicated The Forming of Silica Mullite Bricks In RS Factory Get Free QuoteIt is incorrect procedure to install the spout above the working lining (Reference Figure 4) which inhibits the free movement of the working lining and adds stress that results in cracks and metal penetration • C Coil Grout: o Must be smooth and concentric to allow the lining to expand and contract freely and avoid hangInnovative Refractory Technology for Coreless Induction Furnaces