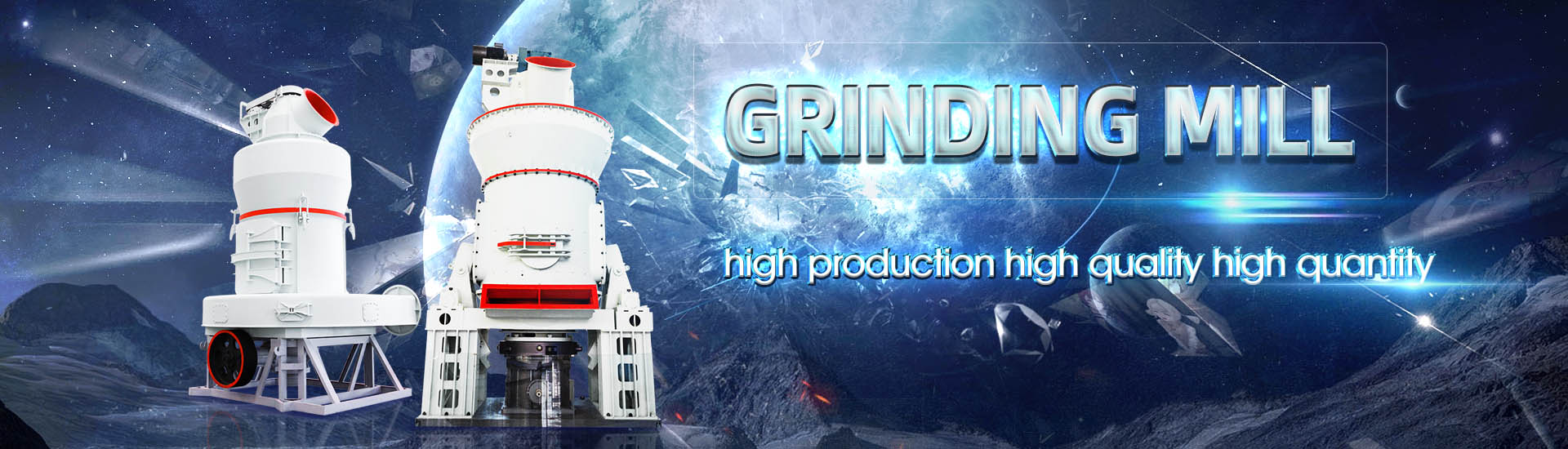
Investment cost of cement raw material grinding equipment

The Comprehensive Guide to Cement Plant Costs: An
This detailed guide will break down the costs associated with each component and stage of a cement factory, from raw material preparation to final packaging and distribution Additionally, we will compare the costs of using Chinese and 2024年5月31日 The raw material storage area of the cement grinding plant needs the following equipment: Stacker and reclaimer: the system is used to handle raw materials and put them in How much dose it cost to start a cement grinding plant?2024年4月4日 Raw material costs typically account for around 2025% of the overall cost (Cement Equipment) Efficient sourcing and management of raw materials can help minimize Unveiling Cement Manufacturing Plant Costs Osum2023年12月28日 In the realm of cement production, the ball mill is a crucial equipment for grinding raw materials and clinker This article delves into the factors influencing the cost of a ball mill cost for 100ton cement plant LinkedIn

Installed cost comparison for cement grinding systems
2004年5月25日 According to the cost breakdown provided by Terembula (2004) and Conroy (1998) for new and upgraded cement plants in USA, purchase cost of the equipment for each ide range of equipment from raw material handling to final product packaging, serves as the backbone of cement production It includes crushers for size reduction of ra materials,Technical Evaluation and Financial Analysis of a Retro tting To be competitive, Production Units need to optimize operations to the maximum possible level so as to lower overall operating costs without having to make major capital investments The cost Optimizing Operating Costs to Improve Profitability in A Cement Raw material cost accounts for around 2025 per cent of the cost of sales of cement players Limestone accounts for a major share of this cost Cement plants are generally located near limestone quarries as limestone cannot be The four major costs associated with cement production
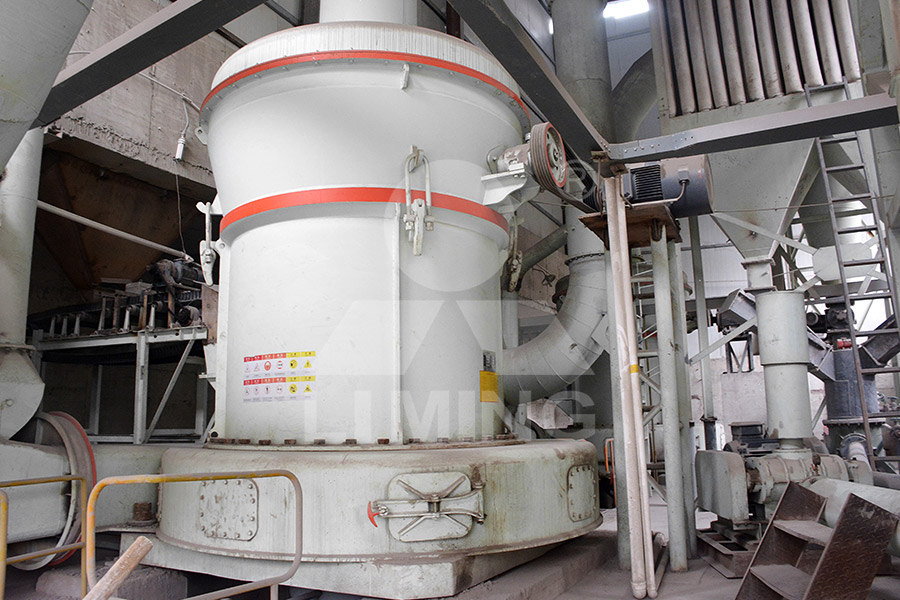
What Are the Major Operating Costs of Cement Plants?
2024年12月1日 1 Raw Materials Costs The cost of raw materials is often the largest expense and can account for approximately 3040% of total cement production expenses This includes Introduction Setting up a cement plant involves numerous components and stages, each contributing significantly to the overall cost This detailed guide will break down the costs associated with each component and stage of a cement The Comprehensive Guide to Cement Plant Costs: An 2024年4月4日 Raw Material Costs Raw material costs constitute another significant component of the total cost of sales in cement production Limestone, the primary raw material, is a major cost factor Other materials, such as fly ash and slag, are often used as additives in the production of blended cementUnveiling Cement Manufacturing Plant Costs OsumThe economic considerations arise from the fact that the costs of raw materials and fuels comprise as much as 50% of the total Storing, metering and conveying solid secondary fuel—Design basis and equipment, Cement Alternative fuels and raw materials INFINITY FOR
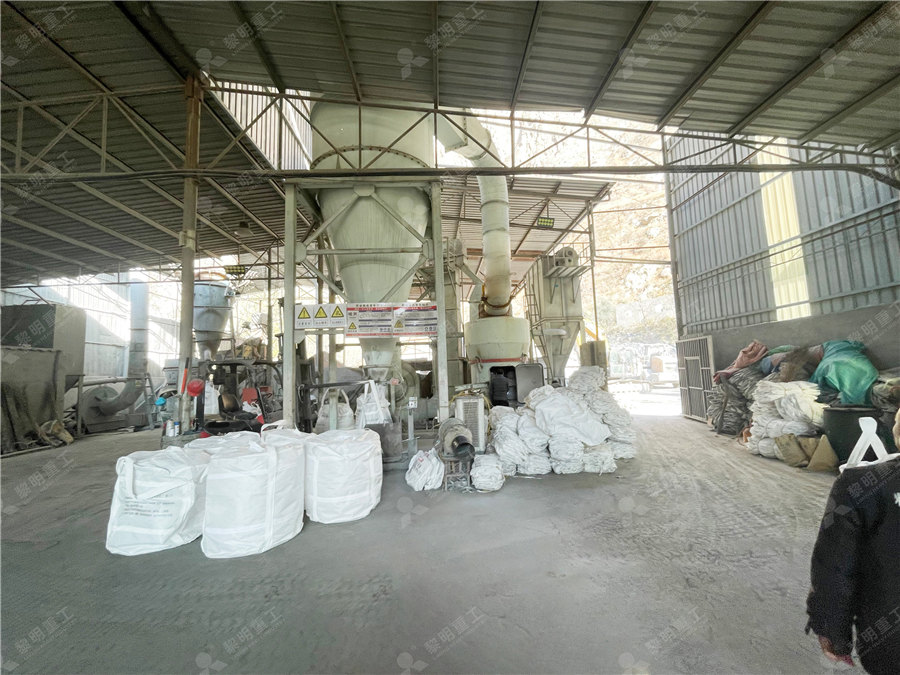
Everything you need to know about clinker/cement Grinding
Relative investment costs global net wear rate of 11 [g/kWh] (Stephane) Gross wear rate 15 g/kWh (my estimate) Wear rate is the same for raw material and cement Different for slurry grinding The [%] of free silica at mill feed for raw material grinding Moisture content of the mill fresh feed Above or below 2 [%H2O] An intermediary storage of the raw material is necessary since the material flow has to be divided up after the primary crusher and the secondary crushers should be loaded The jaw crusher should be mentioned as alternative to the primary gyratory crusher However, its use for cement raw materials is advantageous only under very special conditionsEverything you need to know about Crushers in Cement industryGrinding mills are mainly used to grind the clinker and raw materials in the cement plant It is also called cement grinding equipment or cement mill AGICO provides the cement ball mill, rod mill, cement vertical and repair, thus reducing the investment cost and improving the production efficiency Ultrafine Grinding Mill>> Air Swept Grinding Mill Grinding Equipment Cement Mill AGICOThe principal raw materials for cement manufacturing are: Limestone; Silica chemical corrosion which can be occurred as a result of the chemical reaction between the corrosive gases and equipment The raw materials and fuel are counted as the major sources Low investment cost; Disadvantages Limited raw meal homogenizing compared to Cement Manufacturing Process INFINITY FOR CEMENT EQUIPMENT
.jpg)
The Cement Plant Operations Handbook International Cement
cement manufacture – 3 Portland cement in today’s world 2 Raw materials management system – 22 Concrete problems 16 1 Raw materials – 2 Raw mix – 3 Reserves – 4 Crushing – 5 Drying – 6 Preblending – 7 Storage and handling 3 Raw milling and blending 3 Computerised Maintenance Management Systems 30 1 Raw milling 2022年10月13日 The grinding plant is friendly to new investors since the recovery of cost is quicker than the cement plant It has many advantages over the cement plant The total cost for land, raw material, equipment, civil engineering, and the energy consumption is lessDifferences Between Grinding Plant Cement PlantRaw material prehomogenization is a vital step in cement production that directly influences product quality, energy efficiency, and operational costs By using the right prehomogenization techniques, investing in automation, and adopting best practices, cement plants can achieve consistent, highquality outputsRaw Material PreHomogenization: Ensuring Consistent Cement Typically, cement plants are built in close proximity to raw material extraction sites, which helps to minimize transportation costs Cement production includes the following stages: • Extraction of raw materials and their delivery to the Construction of cement plants under an EPC contract
.jpg)
Comparison Of Cement Vertical Roller Mill And Roller
Table 3 Power Consumption Of Roller Press Grinding System Overall, we can conclude the three tables: After the longterm operation, although unit raw material grinding power consumption of the cement roller press grinding In 1998, Arizona Portland cement (Rillito, Arizona) installed a roller mill for raw material grinding increasing throughput, flexibility, raw meal fineness and reducing electricity consumption (De Hayes, 1999) In North America, it is Everything you need to know about Energy Efficiency Brundick, H, “Drying and grinding of extremely moist cement raw materials in the Loesche mill,” ZKG International, No2, 1998, pages 6471Brundick, Horst, and Schäfer, HeinzUllrich, “Loesche mills for clinker grinding,” Asian Cement and Construction Everything you need to know about cement Materials Preparation and Raw 2019年10月11日 AGICO Cement is a cement grinding plant manufacturer, we'd like to helps you learn more about cement grinding plant and cement grinding machines Skip to content +86 Cement Grinding Plant Overview Cement Grinding Unit AGICO Cement
.jpg)
Cement Factory Cost Cement Plant Cost AGICO Cement Plant
How to minimize the dry method cement plant cost is a crucial issue for many cement enterprises The cement factory cost reduction method can be discussed from site selection, All of these principles will help us to save unnecessary investment Cement Equipment Selection Raw Material Grinding Cement GrindingGenerally, the investment cost of gas pipe lines amortize within 3 5 years On the other hand, with gas pipe lines, the cement industry depends only on one supplier The cost of a coal preparation department of a cement plant amounts to about 15 Fuels in the cement industry INFINITY FOR CEMENT EQUIPMENT2022年8月10日 Raw material grinding: to improve raw meal burning behavior, clinker quality, and kiln output, including thermal energy requirement; Coal grinding: better combustion of fuels, improves the flame property, and avoids CO2 generation, including improved burning process; Cement grinding: cement hydration, strength development, and water demandEfficient grinding unit selection impacts profitability Indian Cement A Vertical Roller Mill (VRM) is an advanced and efficient grinding machine commonly used in the cement industry for grinding raw materials and clinker VRMs have become increasingly popular due to their ability to produce finer products with lower energy consumption compared to traditional ball mills Advantages of Vertical Roller Mills:Vertical roller mill vs ball mill for cement grinding: Comparison
.jpg)
CEMENT GRINDING SYSTEMS INFINITY FOR CEMENT EQUIPMENT
The final manufacturing stage at a cement plant is the grinding of cement clinker from the kiln, mixed with 45% gypsum and possible additives, into the final product, cement In a modern cement plant the total consumption of electrical energy is about 100 kWh/t The cement grinding process accounts for approx 40% if this energy consumptionA complete modular mobile cement grinding plant includes raw material supply, material dosing, cement mill, cement silo, cement packing, etc elements Module 1: Dosing and conveying system Module 2: Mill, separator, and filter Module Modular Mobile Cement Grinding Plant Up To 2020年5月14日 The cement factory cost is based on changing factors like size, location, labor, raw materials, and current real estate trends, which make it impossible to nail down a perfectly accurate, onesizefitsall answerHow Much Does It Cost To Start A Cement Plant?Learning outcomes An emphasis on the understanding of the milling technology system: Gas flow, advantage and disadvantage in the Raw mill and Cement mill installations – Grindability concept and the effects of intergrinding materials of CEMENT GRINDING COURSE The Cement Institute

How to Start a Cement Factory: A Comprehensive Guide
History of the Cement Industry; Current Global Cement Market; Key Players in the Industry; Future Trends and Forecasts; Chapter 2: Understanding Cement Composition and Types of Cement; Raw Materials Required for Cement Production; Cement Manufacturing Process Mining and Preparation of Raw Materials; Raw Material Grinding; Preheating and Report Overview: IMARC Group’s report titled “Cement Manufacturing Plant Project Report 2024: Industry Trends, Plant Setup, Machinery, Raw Materials, Investment Opportunities, Cost and Revenue” provides a complete roadmap for setting up a cement manufacturing plant It covers a comprehensive market overview to microlevel information such as unit operations involved, Cement Manufacturing Plant Report 2024: Setup and Cost2024年6月18日 This study helps to understand the homogenization process of raw materials by equipment in cement production and provides certain reference the equipment investment and maintenance costs are Excluding the effect of grinding, the raw meal processed by the ball mill under gradation conditions with a higher proportion of Evaluation and Analysis of Cement Raw Meal Homogenization These differences between cement grinding and grinding of raw materials made it a serious challenge but may even be taken into consideration in relation to new installations that are included in a twophase investment the corresponding figure will be 010015 EUR per ton of cement Costs of equipment and civil works The total specific Cement grinding Vertical roller mills VS ball mills
.jpg)
Cement plant design under EPC contract ESFC Investment Group
The stage of preparing raw materials for cement production involves crushing the material, which is then dried for use in dry cement production or further grinding for a wet process Even with the use of modern technologies, the production of 1 kilogram of cement requires processing about 15 kilograms of mineral raw materialsRoll presses are also used in, particularly in upgrading existing ball mill circuits as pregrinders to increase production or to reduce specific power consumption in grinding operation Ball mills for cement raw material and coal equipped with a drying compartment adequately air swept with hot gas (2535M/sec above the ball charge), can Raw Material DryingGrinding Cement Plant Optimization2023年3月27日 For example, a smallscale cement plant with a production capacity of 50,000 tons per annum can cost around N300 million, while a largescale plant with a capacity of 2 million tons per annum can The cost of setting up a cement factory in Nigeria LinkedInIntroduction Setting up a cement plant involves numerous components and stages, each contributing significantly to the overall cost This detailed guide will break down the costs associated with each component and stage of a cement The Comprehensive Guide to Cement Plant Costs: An
.jpg)
Unveiling Cement Manufacturing Plant Costs Osum
2024年4月4日 Raw Material Costs Raw material costs constitute another significant component of the total cost of sales in cement production Limestone, the primary raw material, is a major cost factor Other materials, such as fly ash and slag, are often used as additives in the production of blended cementThe economic considerations arise from the fact that the costs of raw materials and fuels comprise as much as 50% of the total Storing, metering and conveying solid secondary fuel—Design basis and equipment, Cement Alternative fuels and raw materials INFINITY FOR Relative investment costs global net wear rate of 11 [g/kWh] (Stephane) Gross wear rate 15 g/kWh (my estimate) Wear rate is the same for raw material and cement Different for slurry grinding The [%] of free silica at mill feed for raw material grinding Moisture content of the mill fresh feed Above or below 2 [%H2O] Everything you need to know about clinker/cement GrindingAn intermediary storage of the raw material is necessary since the material flow has to be divided up after the primary crusher and the secondary crushers should be loaded The jaw crusher should be mentioned as alternative to the primary gyratory crusher However, its use for cement raw materials is advantageous only under very special conditionsEverything you need to know about Crushers in Cement industry
.jpg)
Grinding Mill Grinding Equipment Cement Mill AGICO
Grinding mills are mainly used to grind the clinker and raw materials in the cement plant It is also called cement grinding equipment or cement mill AGICO provides the cement ball mill, rod mill, cement vertical and repair, thus reducing the investment cost and improving the production efficiency Ultrafine Grinding Mill>> Air Swept The principal raw materials for cement manufacturing are: Limestone; Silica chemical corrosion which can be occurred as a result of the chemical reaction between the corrosive gases and equipment The raw materials and fuel are counted as the major sources Low investment cost; Disadvantages Limited raw meal homogenizing compared to Cement Manufacturing Process INFINITY FOR CEMENT EQUIPMENTcement manufacture – 3 Portland cement in today’s world 2 Raw materials management system – 22 Concrete problems 16 1 Raw materials – 2 Raw mix – 3 Reserves – 4 Crushing – 5 Drying – 6 Preblending – 7 Storage and handling 3 Raw milling and blending 3 Computerised Maintenance Management Systems 30 1 Raw milling The Cement Plant Operations Handbook International Cement 2022年10月13日 The grinding plant is friendly to new investors since the recovery of cost is quicker than the cement plant It has many advantages over the cement plant The total cost for land, raw material, equipment, civil engineering, and the energy consumption is lessDifferences Between Grinding Plant Cement Plant
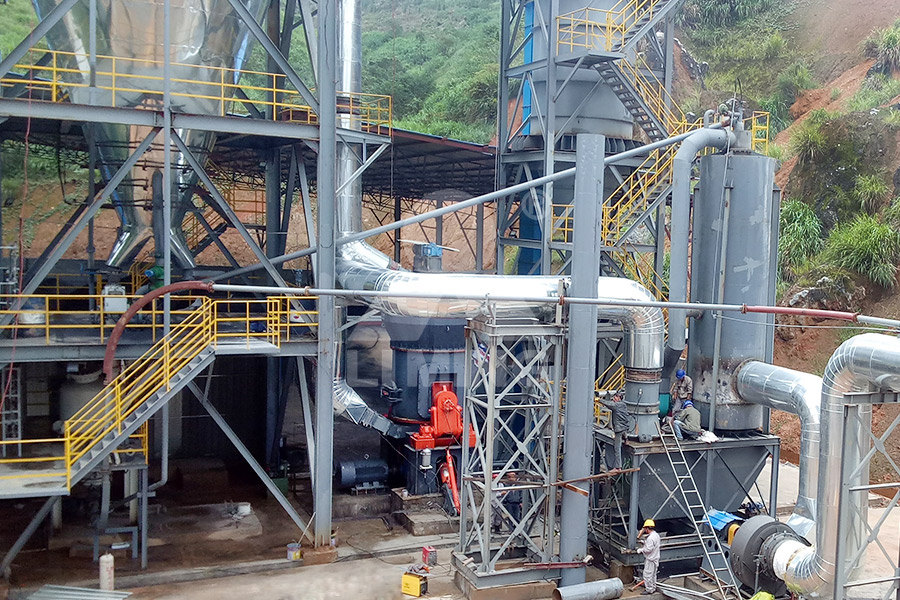
Raw Material PreHomogenization: Ensuring Consistent Cement
Raw material prehomogenization is a vital step in cement production that directly influences product quality, energy efficiency, and operational costs By using the right prehomogenization techniques, investing in automation, and adopting best practices, cement plants can achieve consistent, highquality outputs