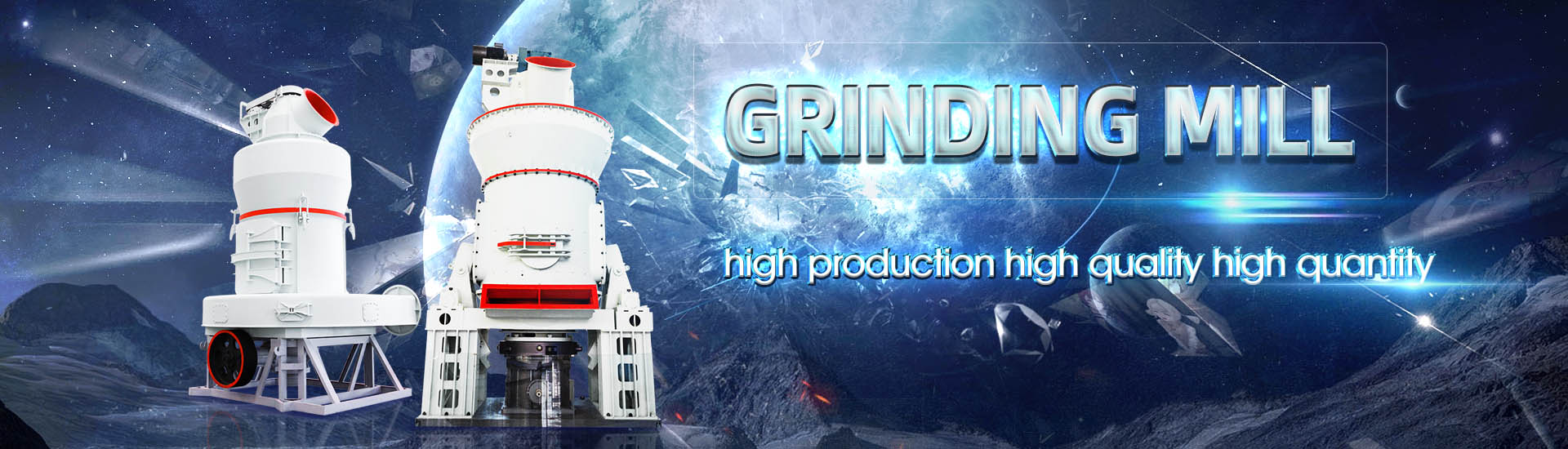
HOME→Limestone desulfurization wet ball mill limestone desulfurization wet ball mill limestone desulfurization wet ball mill
Limestone desulfurization wet ball mill limestone desulfurization wet ball mill limestone desulfurization wet ball mill
.jpg)
A Technical and Economic Comparison of Ball Mill Limestone
2021年10月13日 A Technical and Economic Comparison of Ball Mill Limestone Comminution Wet flue gas desulfurization (WFGD), using limestone with forced oxidation (LSFO), is a A Technical and Economic Comparison of Ball Mill Limestone 2017年7月1日 Desulfurization tests show greater performance in terms of gypsum production Enhancing the recovery of gypsum in limestonebased wet flue 2021年12月1日 Utilization of lowgrade limestone (LGL) in wet flue gas desulfurization Insights into the desulfurization mechanism of lowgrade
.jpg)
Summary of research progress on industrial flue gas
2022年1月15日 Cui et al proposed a combination of limestonegypsum wet flue gas 2021年10月13日 Wet flue gas desulfurization (WFGD), using limestone with forced oxidation A Technical and Economic Comparison of Ball Mill Limestone 2017年4月6日 As a dominant precursor of PM25, SO2 emitted from industrial process is now Enhancing the recovery of gypsum in limestonebased wet flue 2017年7月1日 In this paper, wet desulfurization system for a certain 600 MW coalfired power Enhancing the recovery of gypsum in limestonebased wet flue
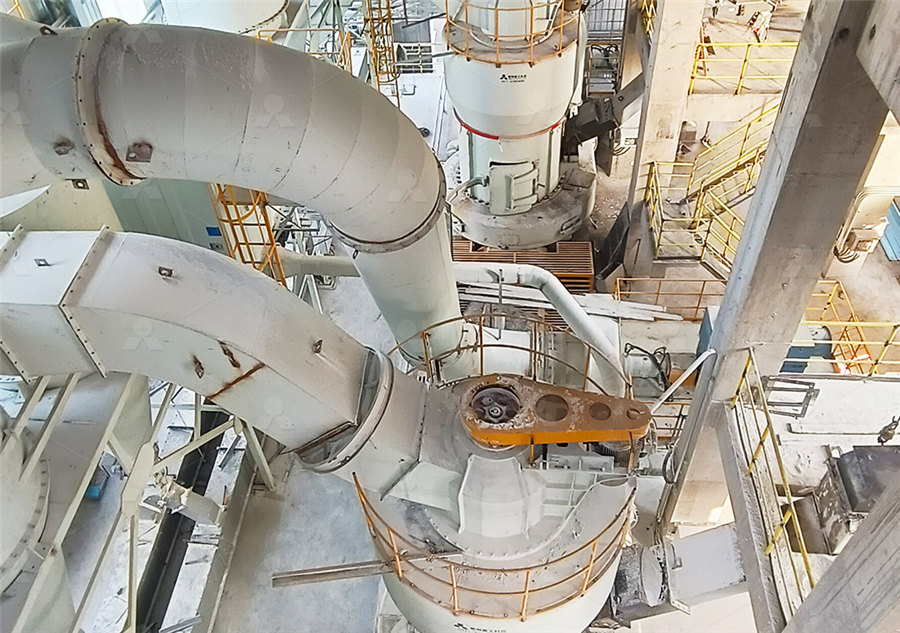
Modeling of the wet flue gas desulfurization system to utilize low
2020年11月11日 Wet flue gas desulfurization was simulated to improve gypsum production 2022年8月15日 Dualloop WFGD has better adaptability to flue gas desulfurization after Limestonebased dualloop wet flue gas desulfurization under ABSTRACT Wet flue gas desulfurization (WFGD), using limestone with forced oxidation (LSFO), is a common Flue gas desulfurization (FGD) process where limestone reacts with SO2 to produce gypsum (CaSO42H2O) In South Africa, Eskom’s Kusile Power Station utilizes conventional wet ball milling to grind highgrade limestone (96% CaCO3) to 95% passing 45 µm prior to use in A Technical and Economic Comparison of Ball Mill Limestone 2022年8月15日 Oxygenenriched combustion is the most promising CO 2 emission reduction technology for coal burning However, the sharp increase in CO 2 and SO 2 concentrations in flue gas after oxygenenriched combustion poses a new challenge to the subsequent wet flue gas desulfurization (WFGD) system In this study, limestonebased dualloop WFGD technology Limestonebased dualloop wet flue gas desulfurization under
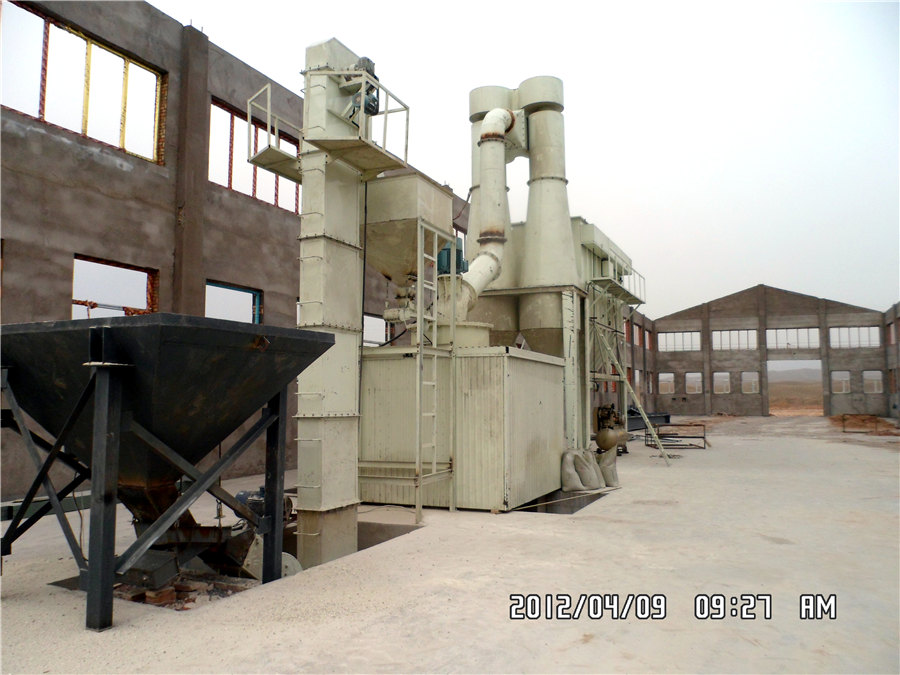
Enhancing the recovery of gypsum in limestonebased wet flue
2017年7月1日 Furthermore, Wang et al (2005) highlighted the systems commonly adopted for the grinding of limestone such as long drum or tube mill and the Hardings ball mill Generally, these ball mills consist of a rotating drum loaded with steel balls that crush the limestone by the action of the tumbling balls as the cylindrical chamber rotates, until 2002年4月1日 In this article the method of cost optimization of the “Wet Limestone Flue Gas Desulfurization System” is presented The optimization calculations include process and cost modelsOptimum Values of Process Parameters of the “Wet Limestone We bring forth a highly advanced Ball Mill, specifically engineered for both wet as well as dry cement grinding applications Classified depending on the circuit design, bearing, grinding type and drive, the selection is made on the basis of the product fineness, quality, and nature of raw material, site conditions and specific requirementsClosed and Open Circuits Ball Mill for Cement, Limestone, Iron ore5 天之前 Economy Ball Mill's wet grinding solutions utilize a ball mill with a rotating cylinder filled with grinding media and a slurry of limestone material and a fluid medium like water As the cylinder rotates, the grinding media cascades and crushing the limestone materials to the manufacturer’s desired sizeLimestone Size with Wet Grinding Economy Ball Mill

Wet Flue Gas Desulfurization (FGD) ARCOR Epoxy
Wet Flue Gas Desulfurization (FGD) In most developed countries, wet scrubber (fluegas desulfurization; FGD) technology is a wellestablished process for removing SO 2 Also, costs have been reduced significantly from 150200 $/KW in the 1980s to 70150 $/kW in the late 1990s Wet FGD Technology2021年10月10日 First, in the wet flue gas desulfurization process, the limestone is pulverized to an average size of 5–20 μm at wet ball mill (Córdoba, 2015) During stirring inside the limestone slurry storage tank, CaCO 3 in limestone was dissolved in water according to Equation (1) , based on Carletti et al (2017) Optimization of wet flue gas desulfurization system using recycled 2021年12月1日 Dissolution rate of limestone for wet flue gas desulfurization in the presence of sulfite J Hazard Mater, 168 (23) (2009), pp 10591064 View PDF View article View Particle size distribution and structural changes in limestone ground in planetary ball mill Int J Miner Process, 126 (2014), pp 4148 View PDF View article View Insights into the desulfurization mechanism of lowgrade limestone 2017年4月6日 The most common system for flue gas desulfurization (FGD) is the wet scrubbing process in which, the contact between the flue gases to be treated and an alkaline sorbent such limestone is realized Enhancing the recovery of gypsum in limestonebased wet flue
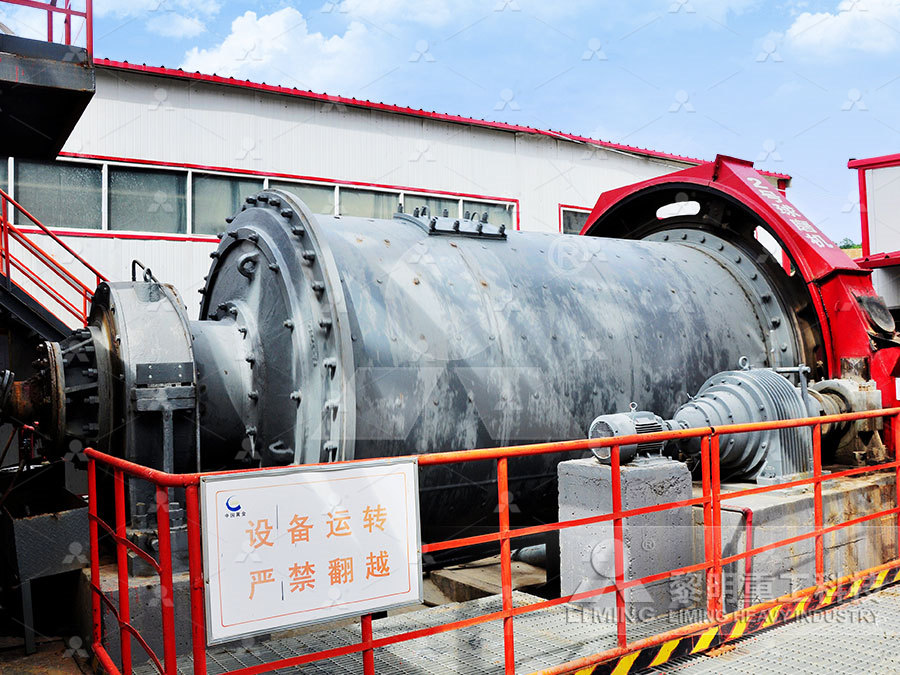
Flue Gas Desulfurization (FGD) Working Thermal
2021年4月11日 The reagent preparation system of flue gas desulfurization (FGD) includes a Wet ball mill and cyclone classifiers which produce a finely ground limestone slurry at 90% solids passing through 325 mesh One mill 2015年3月15日 According to the chemistry of the wet limestone desulphurisation process, in wet limestone FGD system with forced oxidation (Fig 1), limestone slurry is prepared in a closed ball mill (1) and pumped to the scrubber in controlled regime to maintain the pH of the scrubberStatus of Flue Gas Desulphurisation (FGD) systems from coal Wet Ball Mill Power Draw (Bond) For wet ball mills, Bond expressed power draw as a function of the total mass of media: Mill Dimension Design Ore: limestone; Throughput: 250 Tph; F80 = 10mm; P80 = 01mm; Calculate the AMIT 135: Lesson 7 Ball Mills Circuits – Mining 2021年10月13日 ABSTRACT Wet flue gas desulfurization (WFGD), using limestone with forced oxidation (LSFO), is a common Flue gas desulfurization (FGD) process where limestone reacts with SO2 to produce gypsum (CaSO42H2O) In South Africa, Eskom’s Kusile Power Station utilizes conventional wet ball milling to grind highgrade limestone (96% CaCO3) to 95% A Technical and Economic Comparison of Ball Mill Limestone
.jpg)
m/sbm limestone desulfurization ball millmd at main
Write better code with AI Code review Manage code changesChina Limestone Ball Mill wholesale Gold Stone Mining Lime Kaolin Ball Mill, Gold Copper Ore Wet Ball Mill, Limestone Powder Rotary Dry Ball Mills Machine Price US$ 8200098000 / Set 1 Set (MOQ) Baichy Heavy Industrial Machinery Co, LtdLimestone Ball Mill MadeinChina2020年11月11日 Wet flue gas desulfurization was simulated to improve gypsum production using lowgrade limestone Highgrade limestone with 94 wt% CaCO3 content is used for producing gypsum with 93 wt% purity, but owing to the resource depletion of highgrade limestone, lowgrade limestone should be replaced as an alternative However, lowgrade Modeling of the wet flue gas desulfurization system to utilize low Ball mill girth gear Rotary kiln thrust roller Ball mill trunnion Rotary kiln pinion Ball mill head Rotary kiln roller shaft Ball mill bearing bush Rotary kiln bearing housing Ball mill bearing housing ManufacturerFactory Rotary kiln spring plate ManufacturerFactory Ball mill transmission connection ManufacturerFactoryBall Mill Rotary Kiln Vertical Roller Mill Manufacturer Tongli

A Technical and Economic Comparison of Wet Milling versus Dry
work index of 12 kWh/t The limestone is stockpiled and conveyed to a feed preparation area where conventional wet ball milling (in closed circuit with a classifier cyclone cluster) is used to reduce the limestone particle size to 95% passing 45 2006年8月1日 A typical method of preparing limestone slurry is to grind the raw limestone with water in a ball mill This produces a suspended solution of fine limestone particles (slurry), which is then WetLimestone Scrubbing Fundamentals Power Engineering2021年2月1日 Compared with limestonebased wet flue gas desulfurization (WFGD), magnesiabased WFGD has many advantages, but it is not popular in China, due to the lack of good wastewater treatment schemesLimestoneGypsum Wet Flue Gas Desulfurization Abstract: In 2014 limestone desulfurization, denitrification latest technology 1 limestone slurry preparation system The limestone (particle size ≤20mm) into the discharge hopper, the feeder, bucket elevator to the inner limestone steel silo, and then by weighing feeder and belt conveyor to the mill made within a wet ball mill slurry, limestone slurry pumped to hydrocyclone after Limestone FGD New Technology
.jpg)
A simple realistic modeling of fullscale wet limestone FGD units
2010年12月1日 Nowadays, different desulfurization technologies are available to control SO 2 emission in coalfired power stations The most widespread is wet limestone flue gas desulfurization (WLFGD), which has undergone considerable development over the past 30 years in terms of SO 2 removal, efficiency, reliability, and costs Limestone is generally quite a bit Limestone Ball mill can devide into 2 types, wet ball mill and dry ball mill Ball mill is a mineral processing machine for milling the materials into powders after they are crushed It is widely applied to the production of cements, silicate products, building materials, fireproof materials, fertilizers, glass, ceramics as well as nonferrous and ferrous metal processing industriesLimestone Ball MillThe Gravimetric feeder feeds limestone to Wet ball mill system The Wet Ball Mill system consists of Wet Ball Mill, Wet Ball Mill Lubrication system, Mill circuit tank with an agitator, Mill circuit Pump, Mill Hydro cyclone, 3way distributor and accessories The Wet Ball Mill is the wet horizontal type The Process water is supplied to Wet TECHNICAL SPECIFICATION OF WET BALL MILL EQUIPMENTWet technologies represent the majority (87%) of desulphurization systems worldwide [60] due to their low operational costs, high removal efficiency, and CaCO 3 , which is used as an absorbentTypical limestone wet FGD system (adapted from Miller and
.jpg)
Ball mill simulation in wet grinding using a tumbling mill and its
2004年6月25日 A method for simulating the motion of balls in tumbling ball mill under wet condition is investigated The simulation method is based on the threedimensional discrete element method (DEM) and takes into account the effects of the presence of suspension, ie, drag force and buoyancy The impact energy on balls' collision, which enables us to provide Components of power plant: ball mill of FGD (Flue gas desulfurization) Components of power plant: Fluegas desulfurization FGD plant for removing SOx, big blue tank is absorber tank and other important component is GGH ie Gas to Gas heater its called wet FGD ball mill it can make 20 mm limestone into micron particlesComponents of Power Plant: Ball Mill of FGD (Flue Gas Desulfurization China Limestone Grinding Mill wholesale Machine Professional Mining Ore Gold Copper Lead Manganese Iron Slag Sliver Aluminum Limestone Gypsum Powder Grinding Wet and Dry Ball Mill Price US$ 500010000 / Piece 1 Piece (MOQ) Jiangxi Limestone Grinding Mill MadeinChinaThe structural design of the limestone ball mill is similar to the ordinary ball mill The main shaft uses a largediameter doublerow selfaligning rolling bearing, which reduces friction and energy consumption by 20% to 30%, making it highly efficient and energysavingLimestone Grinder AGICO Limestone Grinding Mill ball mill
.jpg)
A Technical and Economic Comparison of Ball Mill Limestone
ABSTRACT Wet flue gas desulfurization (WFGD), using limestone with forced oxidation (LSFO), is a common Flue gas desulfurization (FGD) process where limestone reacts with SO2 to produce gypsum (CaSO42H2O) In South Africa, Eskom’s Kusile Power Station utilizes conventional wet ball milling to grind highgrade limestone (96% CaCO3) to 95% passing 45 µm prior to use in 2022年8月15日 Oxygenenriched combustion is the most promising CO 2 emission reduction technology for coal burning However, the sharp increase in CO 2 and SO 2 concentrations in flue gas after oxygenenriched combustion poses a new challenge to the subsequent wet flue gas desulfurization (WFGD) system In this study, limestonebased dualloop WFGD technology Limestonebased dualloop wet flue gas desulfurization under 2017年7月1日 Furthermore, Wang et al (2005) highlighted the systems commonly adopted for the grinding of limestone such as long drum or tube mill and the Hardings ball mill Generally, these ball mills consist of a rotating drum loaded with steel balls that crush the limestone by the action of the tumbling balls as the cylindrical chamber rotates, until Enhancing the recovery of gypsum in limestonebased wet flue 2002年4月1日 In this article the method of cost optimization of the “Wet Limestone Flue Gas Desulfurization System” is presented The optimization calculations include process and cost modelsOptimum Values of Process Parameters of the “Wet Limestone
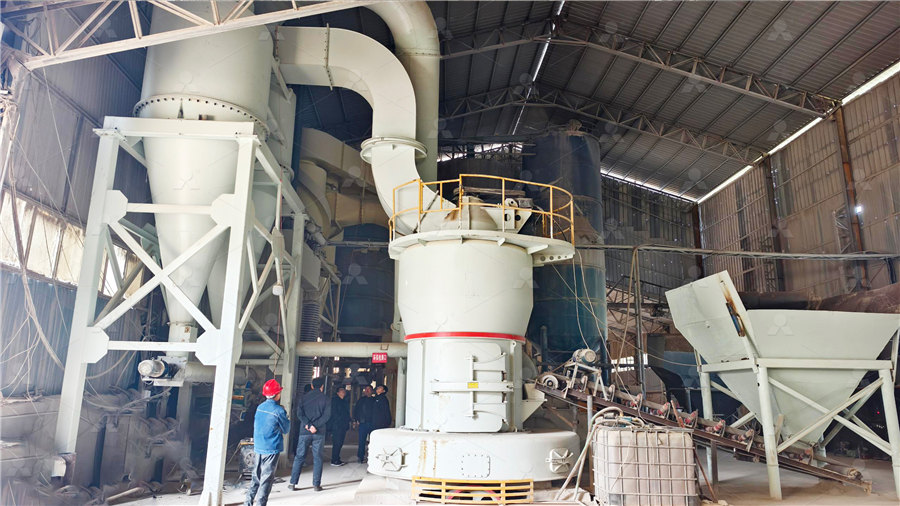
Closed and Open Circuits Ball Mill for Cement, Limestone, Iron ore
We bring forth a highly advanced Ball Mill, specifically engineered for both wet as well as dry cement grinding applications Classified depending on the circuit design, bearing, grinding type and drive, the selection is made on the basis of the product fineness, quality, and nature of raw material, site conditions and specific requirements5 天之前 Economy Ball Mill's wet grinding solutions utilize a ball mill with a rotating cylinder filled with grinding media and a slurry of limestone material and a fluid medium like water As the cylinder rotates, the grinding media cascades and crushing the limestone materials to the manufacturer’s desired sizeLimestone Size with Wet Grinding Economy Ball MillWet Flue Gas Desulfurization (FGD) In most developed countries, wet scrubber (fluegas desulfurization; FGD) technology is a wellestablished process for removing SO 2 Also, costs have been reduced significantly from 150200 $/KW in the 1980s to 70150 $/kW in the late 1990s Wet FGD TechnologyWet Flue Gas Desulfurization (FGD) ARCOR Epoxy2021年10月10日 First, in the wet flue gas desulfurization process, the limestone is pulverized to an average size of 5–20 μm at wet ball mill (Córdoba, 2015) During stirring inside the limestone slurry storage tank, CaCO 3 in limestone was dissolved in water according to Equation (1) , based on Carletti et al (2017) Optimization of wet flue gas desulfurization system using recycled
.jpg)
Insights into the desulfurization mechanism of lowgrade limestone
2021年12月1日 Dissolution rate of limestone for wet flue gas desulfurization in the presence of sulfite J Hazard Mater, 168 (23) (2009), pp 10591064 View PDF View article View Particle size distribution and structural changes in limestone ground in planetary ball mill Int J Miner Process, 126 (2014), pp 4148 View PDF View article View 2017年4月6日 The most common system for flue gas desulfurization (FGD) is the wet scrubbing process in which, the contact between the flue gases to be treated and an alkaline sorbent such limestone is realized Enhancing the recovery of gypsum in limestonebased wet flue