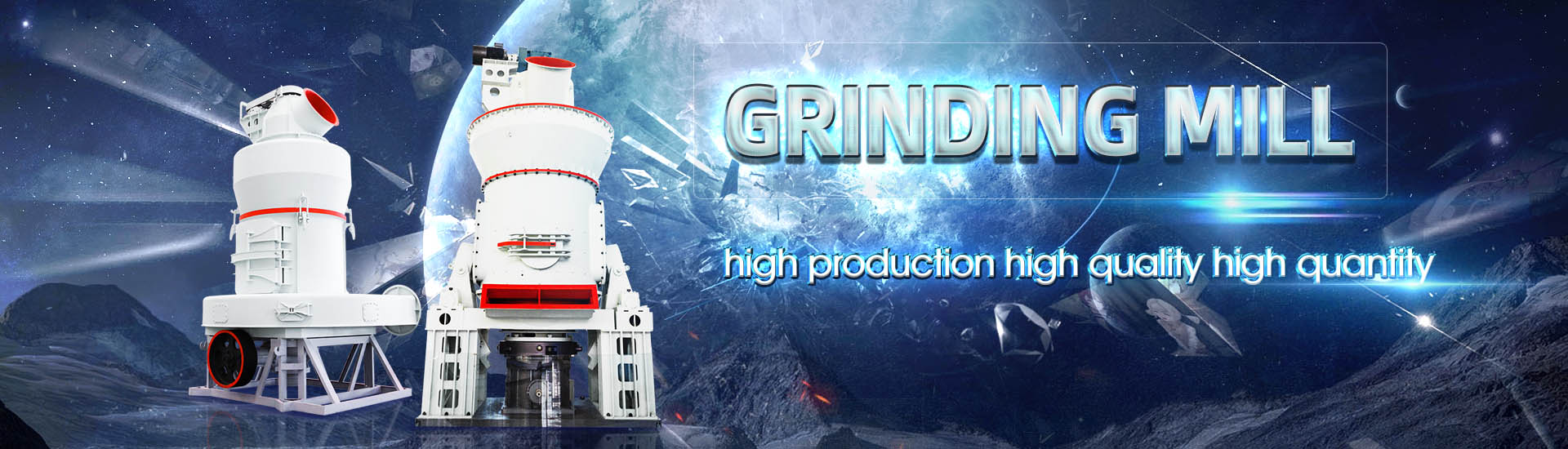
Limestone crusher smelting waste slag treatment technology
.jpg)
Limestone impact on properties, microstructure and CO
2024年10月10日 This study highlights the significant potential of utilizing blended blast 2023年2月8日 The novelty of the current work lies in improving a Vertical Aerated Rock Filter (VARF) using steel slag and limestone media to enhance the efficiency of a rock filter (RF) to eliminate total phosphorus (TP) from domestic Steel Slag and Limestone as a Rock Filter for 2022年11月1日 The Melting Reduction technology of Iron and Steel Waste Slag completely Life cycle assessment of melting reduction treatment for iron and 2021年11月3日 It is shown that the main advantage of the proposed HVG process is the A new technological approach to the granulation of slag melts of

Utilization and detoxification of gypsum sludge by replacing
To investigate the feasibility of replacing limestone with gypsum sludge for smelting slagging, 2023年3月6日 Recycled smelter slags can be used in both in situ and ex situ treatment However, their application has some limitations One of the challenges is how to handle spent slagRecycled Smelter Slags for In Situ and Ex Situ Water 2016年7月29日 They found that the combined use of burnt lime and a compound additive Slag Metallurgy and Metallurgical Waste Recycling JOMThis paper identifies the sources and hazards of ironbearing smelting slag, delves into Resource utilization strategy of Febearing smelting slag in China:
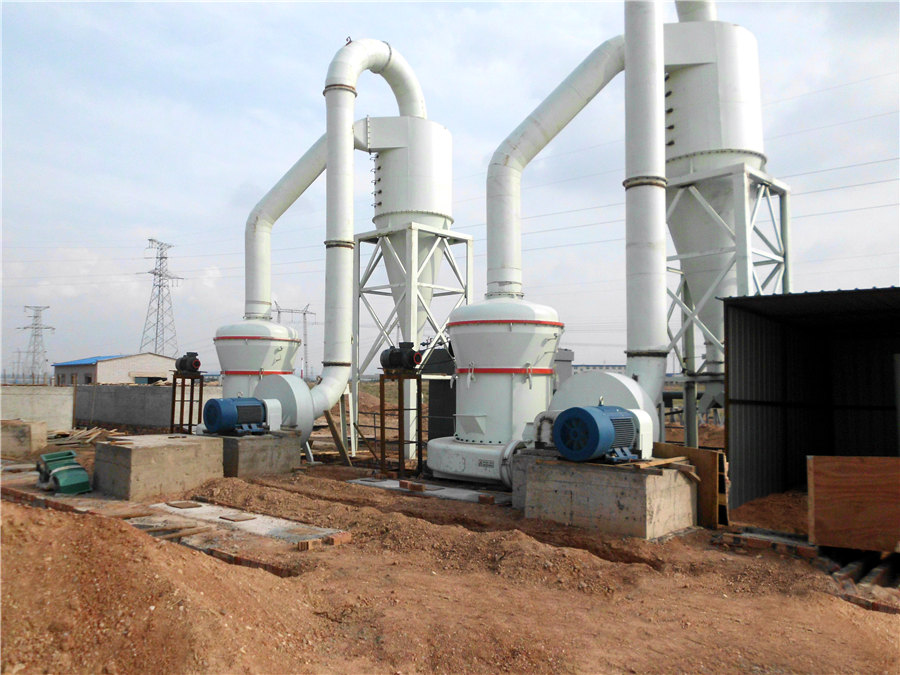
Magnesium Slag Generated by Reduction Smelting Using Pidgeon Process
2021年4月30日 As seen from the test results shown in Table 35, the fluorine in magnesium slag that is generated via the Pidgeon process seriously exceeds the standard limitThus, the slag cannot be landfilled directly because it will cause serious consequences Similarly, with reference to HJ/T2992007 “Solid wasteExtraction procedure for Leaching ToxicitySulfuric acid and 2013年7月1日 Steel slag is a byproduct discharged from the steelmaking process, which is characterized by abundant free calcium/magnesium oxide, low cementitious properties, and high contents of heavy metalsTreatment process and utilization technology of steel slag in 2019年5月23日 Li X, Hu JX, Li D (2011) Technical Characteristic and Application of Steel Slag Treatment Processes Gansu Metallurgy 33(6):44–48 Google Scholar Zeng JM, Cui HY, Xiang H (2008) Development of steel slag treatment technology Nanjing, Jiangsu Metallurgy 36(6):12–14 Google ScholarComprehensive Utilization Technology of Steel Slag2018年12月1日 Increasing concerns about environmental issues have led to more attention being paid to the recycling of mining wastes and smelting byproducts In the present study, the utilization of gold tailings, waste limestone, red mud, and ferronickel slag was investigated for producing continuous glass fibersTo verify the applicability of the downdrawing process, the Applicability of gold tailings, waste limestone, red mud, and
.jpg)
Highpurity recycling of hematite and Zn/Cu mixture from waste smelting
2020年6月3日 Introduction Smelting slag is a typical hazardous waste generated in the smelting and metallurgy industry 1, 2Slag contains high concentrations of heavy metals, such as Cu, Zn, Cr and Ni, which are harmful if released into the environment 3In China, smelting slag is disposed of as an environmental priority pollutant, wherein the slag is generally stabilized with cement 2024年10月10日 Utilizing industrial and urban solid wastes is crucial for developing lowcarbon cements This study proposes a novel method to integrate recycled glass and blast furnace slag (BFS) into alkaliactivated cements It also investigates the influence of pulverized limestone (LSP), as a readily available costefficient partial replacement for BFS The activators were Limestone impact on properties, microstructure and CO2018年6月28日 A novel process was proposed for the separation of Cu and As from Cusmelting waste acid (CSWA) This process includes three steps, namely, the oxidization of As via the addition of H2O2, the selective separation of Cu through the use of Na2S, and the removal of As via the synthesis of scorodite The CSWA was initially oxidized using H2O2 where the As(III) A Novel Process for the Treatment of CopperSmelting Waste Hazardous Waste and Their Disposal”, it was stated that granulated slag arising from the manufacture of iron and steel (B1200, Annex IX, List B) or in general most of slags fromIRON AND STEELMAKING SLAGS: ARE THEY HAZARDOUS WASTE

Application of dirtyacid wastewater treatment technology in
2024年2月14日 Dirtyacid wastewater (DW) originating from the nonferrous metal smelting industry is characterized by a high concentration of H 2 SO 4 and As During the chemical precipitation treatment, a significant volume of arseniccontaining slag is generated, leading to elevated treatment expenses2017年1月1日 Copper smelting slag is the largest solid waste produced in coppermaking process, and slow cooling beneficiation technology is the most widely used method in recovering remaining treasures from (PDF) Reductivesulfurizing smelting treatment of smelter slag 2021年2月26日 A potential industrial wastewaste cotreatment process was proposed and verified for the recovery of the valuable metals Co, Ni, and Cu from copper smelting slag by utilizing high temperature SO2 A potential industrial waste–waste cotreatment process of 2016年10月14日 Under the Al2O3FeOSiO2 ternary slag system, at a smelting temperature of 1450 °C, smelting time of 2 h, mass ratio of coke, pyrite, and CaO to waste catalysts of 16, 25, and 0%, respectively Cotreatment of waste smelting slags and gypsum wastes via
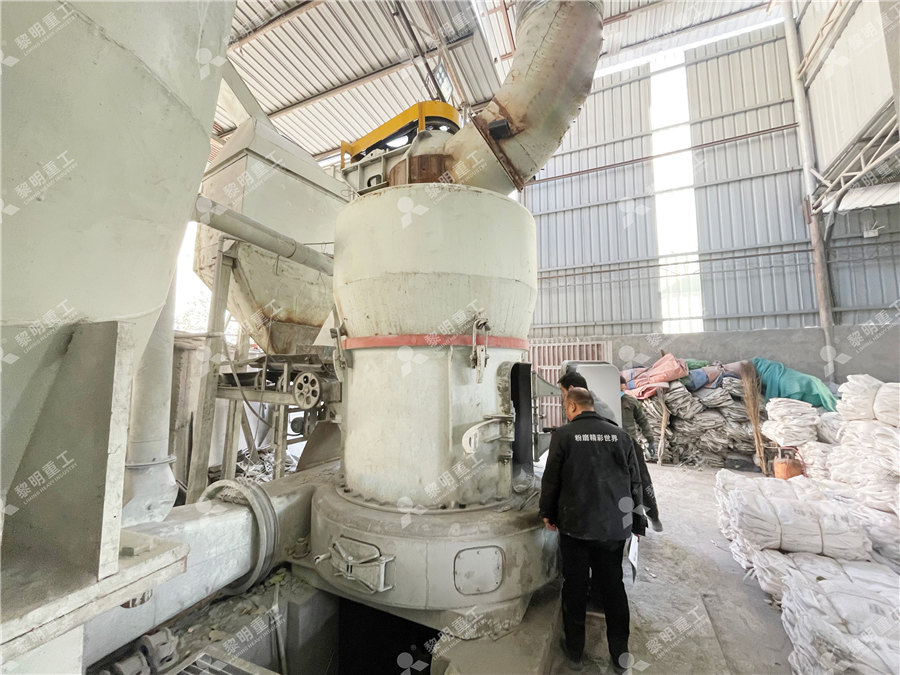
DEVELOPMENT OF TECHNOLOGY FOR RECYCLING COPPER SMELTING PRODUCTION WASTE
DEVELOPMENT OF TECHNOLOGY FOR RECYCLING COPPER SMELTING PRODUCTION WASTE 1251 Fig 1 Xray structural analysis of waste slag from the Balkhash copper smelting plant: ( ) Fe2SiO4 (fayalite); ( ) FeSiO3 (ferro silite); ( ) Fe(Ca)SiO3 (clinoferrite) Fig 2 Change in iron content in aqueous H2SO4 solution during mixi ng (vmix = 100 rpm) with slag having a silicate from waste glass Two waste glass based solid sodium silicates (SSWG) with moduli Ms=SiO 2 /Na 2 O of 1 and 15 were thermochemically synthesized following [27] Table 1 Chemical composition by Xray uorescence and surface area of BFS, LSP and waste glass *LOI = Loss on ignition Oxide (wt%) BFS LSP Waste glass CaO 4202 492 1092 SiOLimestone impact on properties, microstructure and CO22012年5月23日 Many researchers have attempted proposals to reuse waste materials as construction materials such as: household waste slag (Kouda 1996), marine sediments (Dubois et al 2009), residual lateritic (PDF) A new approach to the recycling of gold mine tailings Metals 2023, 13, 1768 2 of 21 stainless steel slag in China and the world were about 1021 million tons and 1943 million tons, respectively, while the yield of stainless steel dust reached about Valuable Recovery Technology and Resource Utilization of
.jpg)
Materials and Energy Balance of EWaste Smelting—An Industrial
2021年11月11日 The main results are as follows: (1) the optimized processing parameters in the NRT smelting practice were the Ewaste feeding rate of 595 t/h, oxidation smelting duration of 35 h, reduction 2017年1月15日 According to above tests, the optimum conditions for Cotreatment of waste smelting slags and gypsum waste via reductivesulfurizing smelting were obtained as follow: 12 wt% coke addition of smelter slag, 20 wt% sulfurizing agent CaSO 4 dosage, a smelting temperature of 1350 °C (1623 K), 3 h smelting durationCotreatment of waste smelting slags and gypsum wastes via Williams Patent Crusher is committed to designing and manufacturing the most durable and efficient limestone crusher machines on the market We’ve held that commitment for over 150 years Additionally, since the mid1980s, we’ve developed extensive experience in Circulating Fluidized Bed (CFB) technology and our limestone mills have proven themselves as an Limestone Mills Limestone Crushers Pulverizers Williams Crusher2023年1月1日 Although considerable effort has been done over a long period of time in the exploitation of industrial waste, ferrochrome slag has received surprisingly less investigationUtilization of steel slag waste as construction material: A review
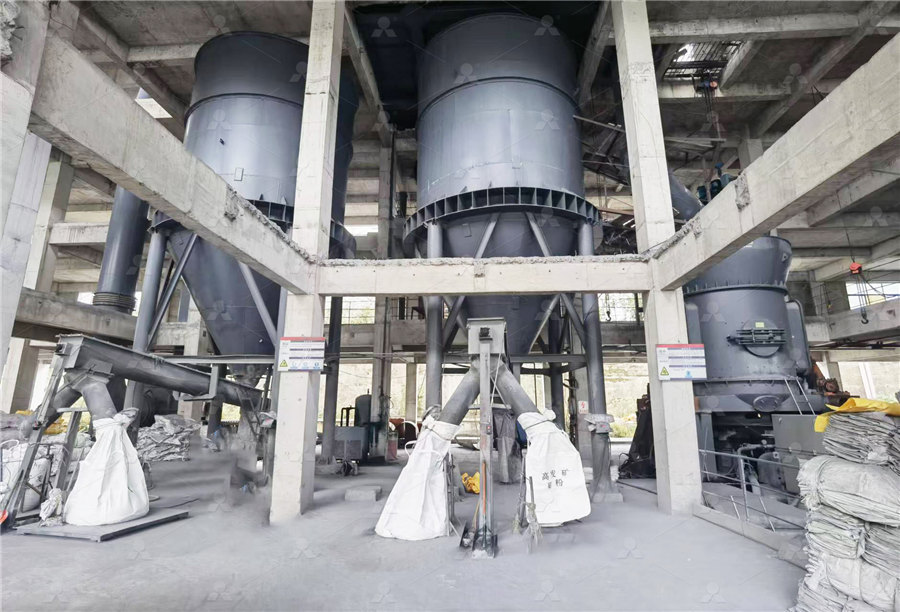
Highpurity recycling of hematite and Zn/Cu mixture from waste smelting
2020年6月3日 Smelting slag is a typical hazardous waste generated in the smelting and metallurgy industry 1,2Slag contains high concentrations of heavy metals, such as Cu, Zn, Cr and Ni, which are harmful if 2017年1月15日 Furthermore, phase compositions and microstructure of the initial smelter slag and smelting resultants after cotreatment with gypsum were characterized respectively by Xray Diffraction (XRD, Rigaku 3014, CuKαradiation, λ = 154 Å, Rigaku Co, Japan) and Scanning Electron Microscopy (SEM; FEI QUANTA 200; FEI, Eindhoven, The Netherlands Cotreatment of waste smelting slags and gypsum wastes via 2020年1月25日 The development trends of oxygen bottom blowing lead smelting technology are as follows: firstly, the technology is developing towards the direction of largescale production, energysaving and emission reduction, improving labor production efficiency; secondly, the technology is applied to treat various solid wastes comprehensively for achieving The Latest Development of Oxygen Bottom Blowing Lead Smelting Technology2021年12月1日 Generally, the processing was performed with similar assumptions than TSLS with PSC, but the tapping of matte and slag from the primary smelting furnace was done from separate tapholes Slag with iron to silica ratio 135 was transported to slow cooling while matte with 65% Cu was granulated Smelting slag was treated in a slag parison of environmental performance of modern copper smelting
.jpg)
OneStep Microcrystalline Glass Preparation Using Smelting Slag
2022年11月18日 The smelting slag obtained through iron collection from waste automobile threeway catalysts was used as a raw material to prepare microcrystalline glass through a onestep crystallization heat 2018年10月20日 A New Technology for Copper Slag Reduction to Get Molten Iron and Copper Matte Journal of Iron and Steel Research, International, Volume 22, Issue 5, Cotreatment of waste smelting slags and gypsum wastes via reductivesulfurizing smelting for valuable metals recovery Journal of Hazardous Materials, Volume 322, Green and efficient utilization of waste ferricoxide desulfurizer to Slag and slag handling currently represents a significant safety, environmental, operational, and financial concern for ferroalloy production With the majority of smelters producing slag/alloy mass ratio of 1015, slag handling and processing post tap hole represent a significant part of any operation Historically, slag treatments have Slag Atomising Technology: Unlocking Real ValueReuse Technology for Slag Generated from Municipal Solid Waste Melting Systems cooled slag by applying light crushing The benefits include simplification of equipment around the furnace than the air cooling method and eliminating the water treatment process required in the water granulation system 232 Adjusting physical propertiesReuse Technology for Slag Generated from Municipal Solid Waste
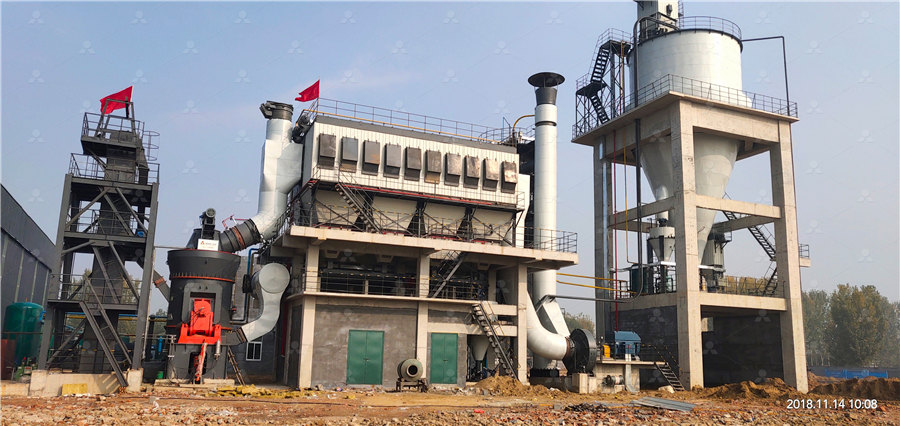
CONVERTER GAS AND WASTE WATER TREATMENT BY OGSYSTEM IN STEEL SMELTING
3 WASTE WATER TREATMENT AND REUSE TECHNOLOGY Solid waste is mud, blast furnace slag, converter slag, iron scale and refractory (Zhaowen, Lei Yuanlong 2008) steel industry contains different levels of heavy metals, for example, the waste water from steel smelting contains high concentrated Zn and Mn Besides, 2023年5月4日 Huigang, W Long, W Ben, P: Characteristics and research progress of steel slag primary treatment technology vol 20(13), 50255031 Science Technology and Engineering(2020) Treatment process Development of waste heat recovery technology from steel slag2021年4月30日 As seen from the test results shown in Table 35, the fluorine in magnesium slag that is generated via the Pidgeon process seriously exceeds the standard limitThus, the slag cannot be landfilled directly because it will cause serious consequences Similarly, with reference to HJ/T2992007 “Solid wasteExtraction procedure for Leaching ToxicitySulfuric acid and Magnesium Slag Generated by Reduction Smelting Using Pidgeon Process2013年7月1日 Steel slag is a byproduct discharged from the steelmaking process, which is characterized by abundant free calcium/magnesium oxide, low cementitious properties, and high contents of heavy metalsTreatment process and utilization technology of steel slag in
.jpg)
Comprehensive Utilization Technology of Steel Slag
2019年5月23日 Li X, Hu JX, Li D (2011) Technical Characteristic and Application of Steel Slag Treatment Processes Gansu Metallurgy 33(6):44–48 Google Scholar Zeng JM, Cui HY, Xiang H (2008) Development of steel slag treatment technology Nanjing, Jiangsu Metallurgy 36(6):12–14 Google Scholar2018年12月1日 Increasing concerns about environmental issues have led to more attention being paid to the recycling of mining wastes and smelting byproducts In the present study, the utilization of gold tailings, waste limestone, red mud, and ferronickel slag was investigated for producing continuous glass fibersTo verify the applicability of the downdrawing process, the Applicability of gold tailings, waste limestone, red mud, and 2020年6月3日 Introduction Smelting slag is a typical hazardous waste generated in the smelting and metallurgy industry 1, 2Slag contains high concentrations of heavy metals, such as Cu, Zn, Cr and Ni, which are harmful if released into the environment 3In China, smelting slag is disposed of as an environmental priority pollutant, wherein the slag is generally stabilized with cement Highpurity recycling of hematite and Zn/Cu mixture from waste smelting 2024年10月10日 Utilizing industrial and urban solid wastes is crucial for developing lowcarbon cements This study proposes a novel method to integrate recycled glass and blast furnace slag (BFS) into alkaliactivated cements It also investigates the influence of pulverized limestone (LSP), as a readily available costefficient partial replacement for BFS The activators were Limestone impact on properties, microstructure and CO
.jpg)
A Novel Process for the Treatment of CopperSmelting Waste
2018年6月28日 A novel process was proposed for the separation of Cu and As from Cusmelting waste acid (CSWA) This process includes three steps, namely, the oxidization of As via the addition of H2O2, the selective separation of Cu through the use of Na2S, and the removal of As via the synthesis of scorodite The CSWA was initially oxidized using H2O2 where the As(III) Hazardous Waste and Their Disposal”, it was stated that granulated slag arising from the manufacture of iron and steel (B1200, Annex IX, List B) or in general most of slags fromIRON AND STEELMAKING SLAGS: ARE THEY HAZARDOUS WASTE2024年2月14日 Dirtyacid wastewater (DW) originating from the nonferrous metal smelting industry is characterized by a high concentration of H 2 SO 4 and As During the chemical precipitation treatment, a significant volume of arseniccontaining slag is generated, leading to elevated treatment expensesApplication of dirtyacid wastewater treatment technology in 2017年1月1日 Copper smelting slag is the largest solid waste produced in coppermaking process, and slow cooling beneficiation technology is the most widely used method in recovering remaining treasures from (PDF) Reductivesulfurizing smelting treatment of smelter slag