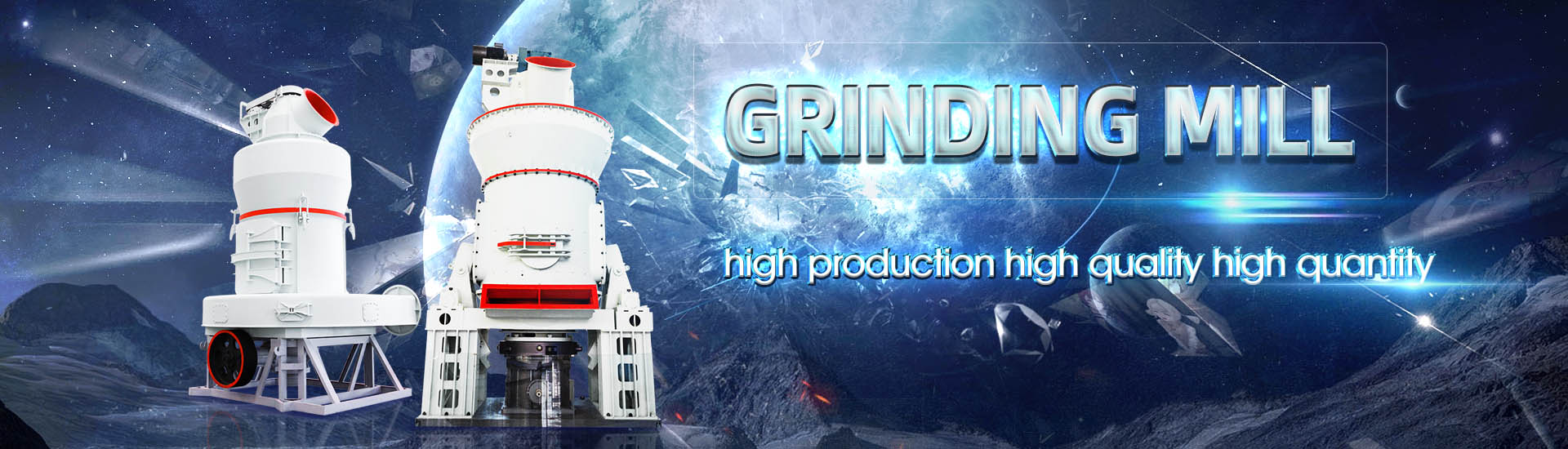
Cement plant raw material workshop
.jpg)
Cement plant operations workshops – Pertecnica Engineering
The Cement Plant Operations Workshops are designed to provide handson training and practical insights into the various aspects of cement plant operations These workshops cover the entire raw materials within the Indian cement sector It covers the various aspects of coprocessing, including international trends, waste regulation, types of AF/ARM, preprocessing, health and ALTERNATIVE FUELS AND ALTERNATIVE RAW MATERIALS UNIDOCement Manufacturing and Production Training: Training programs cover the entire cement production process, from raw material extraction and grinding to clinker production and cement Cement Industry Courses, Cement production training, Cement The Cement Plant Operations Handbook is a concise, practical guide to cement manufacturing and is the standard reference used by plant operations personnel worldwide Providing a The Cement Plant Operations Handbook International Cement
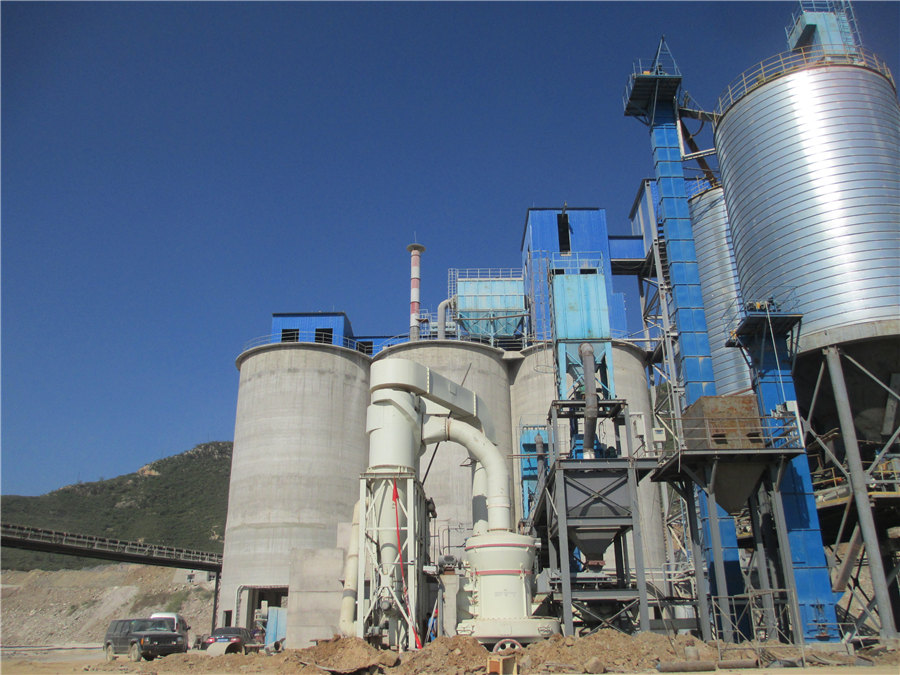
TECHNICAL WORKSHOP International Cement Review
In this threeday technical training workshop the progressive levels of cement manufacturing process optimisation will be explored, beginning with the raw materials and their preparation, The Seminar explores the critical elements of the various challenges faced by different cement plants around the world The Seminar covers the process, operation, and cement production of all the different departments in the CEMENT PROCESS TECHNOLOGY SEMINAR The workshop will aim to explain how that can be achieved Outline course programme Monday, 17 June Raw materials and their conversion into cement clinker, fuels and combustion n The TRAINING FOR CEMENT PLANT OPERATIONS STAFFProducing cement consumes both large quantities of raw materials and fuel, and produces substantial CO2 emissions The use of alternative fuels and raw materials in cement Guidelines for CoProcessing Fuels and Raw Materials in Cement
制粉项目-2023.11.17.jpg)
CEMENT GRINDING COURSE The Cement Institute
Throughout the course, the lectures are supplemented with exercises and case studies, allowing the participants to relate the course material to their cement grinding facility and, as a result understanding the changing needs of cement Cement production and concrete as building material The properties of concrete make it a primary building material where reliability and durability are required Depending on the application ~ Process characteristics of clinker and cement production SINTEF2014年1月29日 While in Europe, and especially in Germany, an average of around 60% of regular fuel is substituted by high quality alternative materials, which are carefully prepared and undergo quality control, the employment of such materials is developing much more slowly in other regions of the world Alternative fuels and raw materialsAlternative Fuels in Cement Production: Part One World CementRaw meal grinding is a vital link in the cement raw material preparation process also called roller mill, is another raw mill commonly used in cement plants Compared with the cement ball mill, it has a great difference in structure, a Raw Mill – Raw Mill In Cement Plant AGICO Cement
.jpg)
Cement Plant Raw materials INFINITY FOR
Bulk material handling is a major activity and bins for raw materials, intermediate products and finished cement must reliably provide controlled flows of materials upon demand The tonnages of material to be stored at various process 2022年7月4日 The raw materials which are used to manufacture cement at Shayona are limestone, clay, corrective (silica) sand and iron ore These ingredients, when heated at high temperatures form a rocklike Mining Activities, Cement Production Process and Quality ControlProduction scheme of a cement plant (typical) Raw Mill Fan ID Fan Kiln Exhaust Fan Clinker Cooler Fan Raw Material Clinker Cooler Rotary Kiln with 4 Stage Heat Exchanger Ball Mill with Triager and Cyclone Separator Gypsum, Other Materials Clinker Silo Cement Silo and Dispatch Raw Mill Silos Fuel Silo Storage and Homogenisation Storage and Fans in Cement Plants BrownleeMorrow Company2014年12月31日 Raw materials used in cement plants have a great influence on the investment for a cement plant as the design and selection of the handling equipment is based on their physical and chemical properties Effluent Treatment Plant (ETP) installed for mine’s workshop Treated water is reused in washing activityRaw material handling and storage Indian Cement Review

Preparation Of Cement Raw Material Cement Mill, Cement
The raw material production of cement plant can be classified into four steps: crushing, grinding, mixing and homogenizing Crushing: the limestone and other materials are crushed into small pieces by cement crusher, such as hammer crusher, Ball mill is a cylinder rotating at about 7080% of critical speed on two trunnions in white metal bearings or slide shoe bearings for large capacity mills Closed circuit ball mill with two compartments for coarse and fine grinding and a drying compartment with lifters are generally found in cement plants for raw material grindingRaw Material DryingGrinding Cement Plant OptimizationObjectives of the workshop 12 af/arm coprocessing 15 21 52 bringing solutions to waste producers in cement plants 37 53 Define procedure for sampling and analysis 38 training provided with respect to the use of alternative fuels and alternative raw materials within the Indian cement sector It covers the various aspects of co ALTERNATIVE FUELS AND ALTERNATIVE RAW MATERIALS2022年3月3日 Cement Raw Materials Grinding Process (Raw Mill System) English VersionRaw Mill System is a system for grinding raw materials in the form of raw materialsCement Raw Materials Grinding Process (Raw Mill System
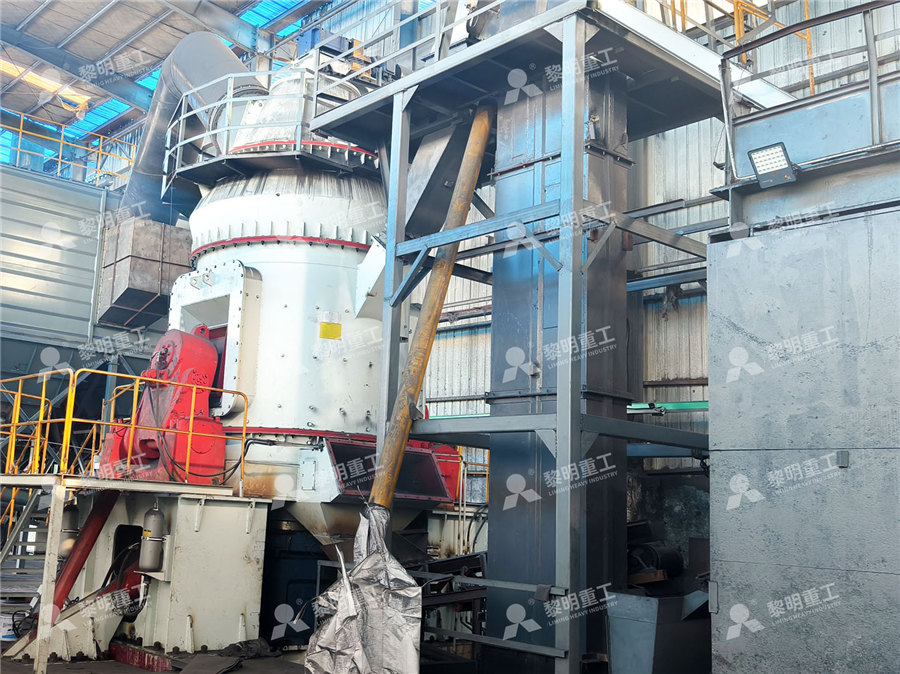
(PDF) Prediction of the Amount of Raw Material in an
2022年12月14日 The idea of this work is the development of a predictive model to predict the amount of raw material in a workshop in a cement factory based on the Deep Learning technique Long ShortTerm Memory 2014年6月29日 MVW, Session 5Quality Management (2010), in: Workshop Alternative Fuels Cement plants aggravate the critical challenges of including using alternative fuels and raw materials Use of alternative fuels in cement industrySlag powder is then conveyed to the cement grinding workshop using an air conveyor Cement Grinding Mill Equipped with 1 set of Φ1600×1500 roller press and Φ42×13m cement grinding equipment The cement raw materials are Clinker Plant – SBCCOCEMENTMill audit and axial sampling, raw material, and cement – Impact of material characteristics grindability – Drying and evaporative cooling – Mechanical and process description of the different types of presses – Separators, types and operation – Separator efficiency and particle size distribution – Workshop: Plant performance (mill operation improvement) – Maintenance CEMENT GRINDING COURSE The Cement Institute
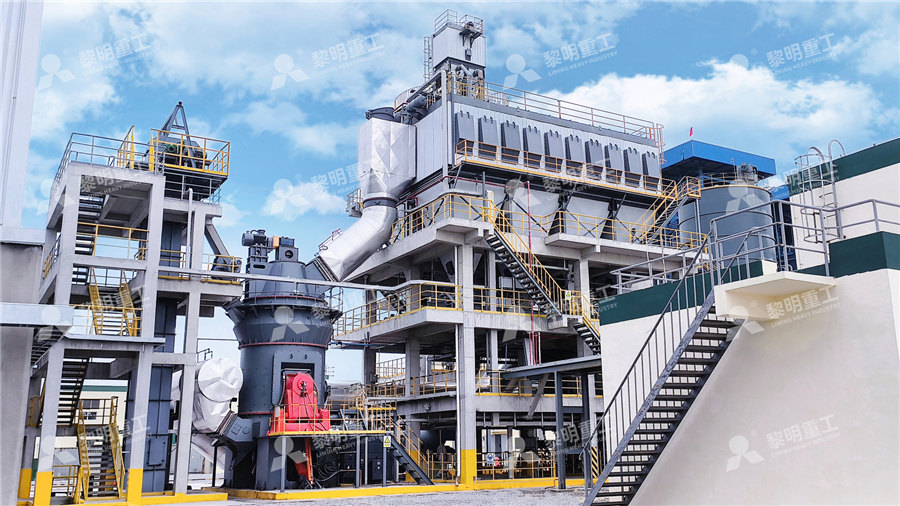
Cement Conveyor Belt Conveyor In Cement Plant AGICO
Cement conveyor refers to a belt conveyor in cement plant, which is necessary accessory equipment in the cement production line A belt conveyor is a kind of material handling equipment with strong adaptability, applied for conveying bulk density less than 167t / m³, it is mostly used for powder, granular, small lump materials, and bagged materials, such as sand, ore, coal, cement manufacture – 3 Portland cement in today’s world 2 Raw materials management system – 22 Concrete problems 16 1 Raw materials – 2 Raw mix – 3 Reserves – 4 Crushing – 5 Drying – 6 Preblending – 7 Storage and handling 3 Raw milling and blending 3 Computerised Maintenance Management Systems 30 1 Raw milling The Cement Plant Operations Handbook International Cement Cement is typically made from limestone and clay or shale These raw materials are extracted from the quarry crushed to a very fine powder and then blended in the correct proportions This blended raw material is called the 'raw feed' or 'kiln feed' and is heated in a rotary kiln where it reaches a temperature of about 1400 C to 1500 CCement manufacturing components of a cement plant Understanding CementRaw material: raw gypsum powder, special paper, modified starch, foamingagent, our workshop Onestop solution service Design Equipment Supply AGICO CEMENT supplies EPC projects for both cement plant and single cement plant equipment CONTACT INFO +86 s 19F, Gypsum Board Manufacturing Plant Plasterboard Production Line
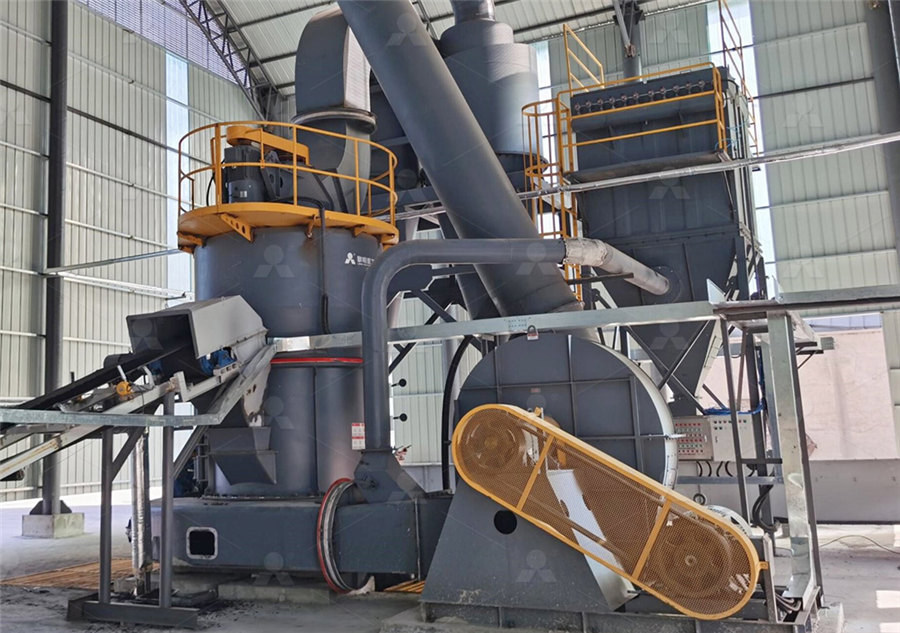
Raw Meal Suspension In Calciner INFINITY FOR CEMENT EQUIPMENT
Cement production starts in quarries where limestone and clay are mined and crushed Location of the crushers could be at the quarry or at the plant (largely is a function of haulage vs conveying costs) Already crushed raw materials are mixed in the correct proportions and stored in special stacker/reclaimer systems, where preblending is Raw materials Home About this site About cement About clinker List of plants Map of plants About Kilns Other technical advances Trends in innovation Sources Historical Texts Reference Essays Contact Site Map Descriptions of material types: Chalk: general Chalk: Thames Estuary Chalk: the Medway Swale Chalk: Cam Valley Middle Jurassic Cement Plants: Raw MaterialsIn recent decades, more than 250 polycom® highpressure grinding rolls have been commissioned in the cement industry as an integral part of a polysius® grinding plant in the current fiscal year alone thyssenkrupp has already polycom® HPGR cuttingedge technology in the Introduction Setting up a cement plant involves numerous components and stages, each contributing significantly to the overall cost This detailed guide will break down the costs associated with each component and stage of a cement The Comprehensive Guide to Cement Plant Costs: An
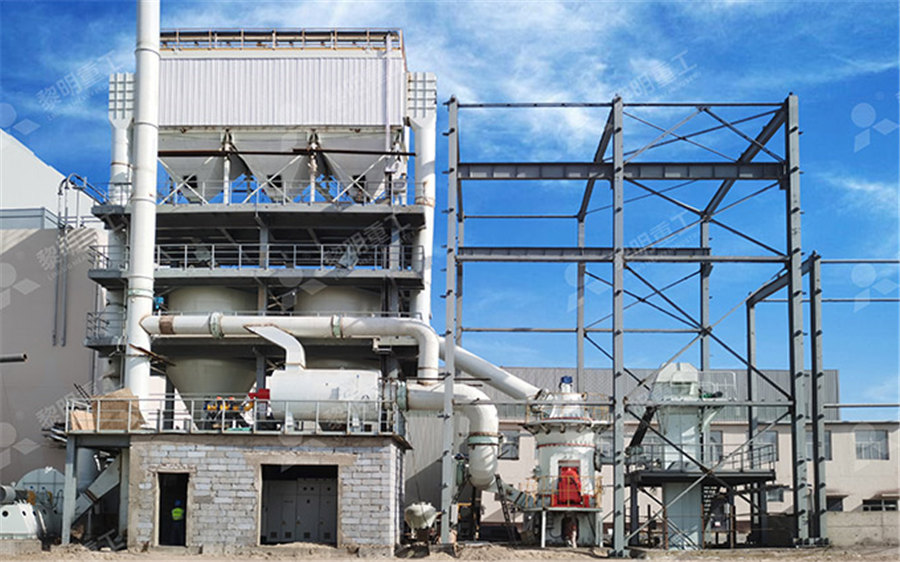
Raw Mill in Cement Plant Cement Manufacturing
Learn about the raw mill in cement plants and the basic raw materials used in cement manufacturing Discover our efficient cement manufacturing process Contact us for more info! Amrit Support About Amrit Support; Services; Where, G is another constant The majority of the kiln feed is limestone, which does not have to be finer than 125 µm If an argillaceous limestone (cement rock) is used, it may be possible to obtain good burnability at particle sizes considerably coarser than this (since the effective calcite grain size is smaller than the particle size)Every Thing you need to know about Raw Mix Design Vertical raw material grinding has been widely used in dry process cement plants The raw material preparation system of the 2 500 t/d cement production line can adopt the vertical mill with the disc diameter of 3 400 mm as the main grinding machineRaw Material Preparation in Cement Manufacturing Plant AGICOChina stacker and reclaimer manufacturer offers circular or rectangular stacker and reclaimer for bulk material handling system in cement plants customization design and competitive price Skip to content +86 s about blog contact EN ES RU Menu Menu Home; Cement Equipment Raw Material processing Stacker And Reclaimer Cement Plant Parts
.jpg)
Alternative fuels and raw materials INFINITY FOR CEMENT EQUIPMENT
Some of the cement plants have also set up integrated preprocessing plants in order to adopt the AFR strategy more effectively The interface of the waste management and recycling industry with cement plants along with the facilities required there is shown in Figure 43 (13)These alternative fuels and raw materials are typically byproducts of other industrial processes or waste materials that would otherwise be disposed of Source: CIF Survey, Status and prospects of coprocessing of waste in EU cement plants (Ecofys 2017), Portland Cement Association, Global Cement and Concrete Association, CembureauAlternative Fuels Raw Materials – Cement2022年10月3日 The halfday workshop aims at sharing international experiences in coprocessing of wastes in the cement industry, informing the industry of the results of the recent demonstration using nonrecyclable plastic wastes at the INSEE plant in Hon Chong, Kien Giang, and discussing the potential for future coprocessing in the Vietnamese cement WORKSHOP: “Coprocessing of alternative fuels and raw materials 2023年3月1日 Raw material is extracted from quarries that are usually close to the cement plant This raw material is composed mainly of limestone, as well as other assets as clay, shale, sand, iron ore, pozzolana and pyrrhotine The crusher is fed with specific raw material proportions calculated from material's mineral composition by the laboratoryEfficient machine learning model to predict fineness, in a vertical raw
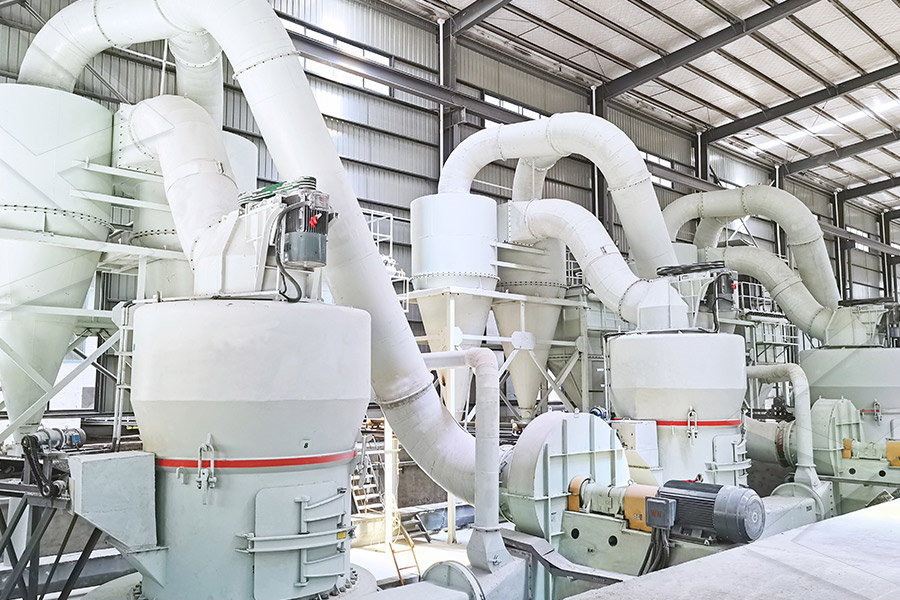
Alternative Fuels in Cement Production: Part One World Cement
2014年1月29日 While in Europe, and especially in Germany, an average of around 60% of regular fuel is substituted by high quality alternative materials, which are carefully prepared and undergo quality control, the employment of such materials is developing much more slowly in other regions of the world Alternative fuels and raw materialsRaw meal grinding is a vital link in the cement raw material preparation process also called roller mill, is another raw mill commonly used in cement plants Compared with the cement ball mill, it has a great difference in structure, a Raw Mill – Raw Mill In Cement Plant AGICO Cement Bulk material handling is a major activity and bins for raw materials, intermediate products and finished cement must reliably provide controlled flows of materials upon demand The tonnages of material to be stored at various process Cement Plant Raw materials INFINITY FOR 2022年7月4日 The raw materials which are used to manufacture cement at Shayona are limestone, clay, corrective (silica) sand and iron ore These ingredients, when heated at high temperatures form a rocklike Mining Activities, Cement Production Process and Quality Control
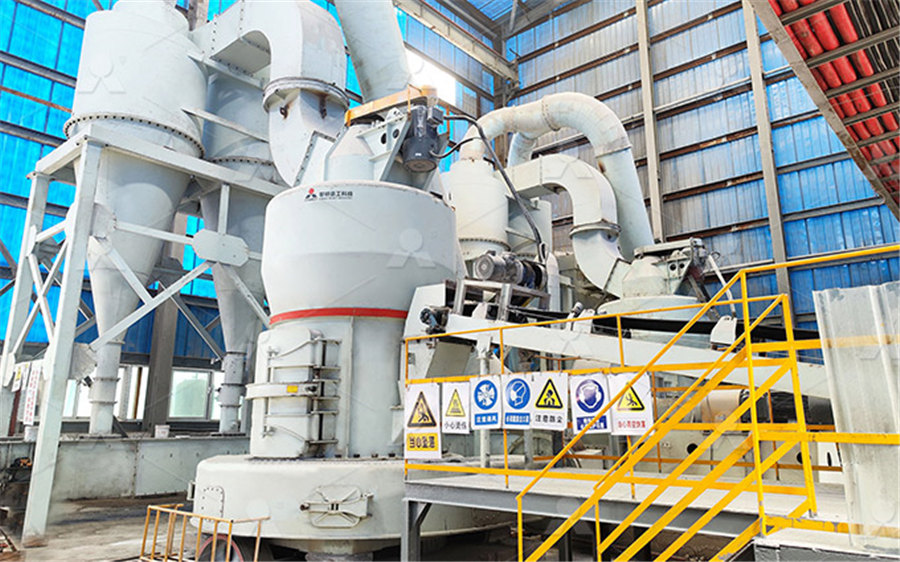
Fans in Cement Plants BrownleeMorrow Company
Production scheme of a cement plant (typical) Raw Mill Fan ID Fan Kiln Exhaust Fan Clinker Cooler Fan Raw Material Clinker Cooler Rotary Kiln with 4 Stage Heat Exchanger Ball Mill with Triager and Cyclone Separator Gypsum, Other Materials Clinker Silo Cement Silo and Dispatch Raw Mill Silos Fuel Silo Storage and Homogenisation Storage and 2014年12月31日 Raw materials used in cement plants have a great influence on the investment for a cement plant as the design and selection of the handling equipment is based on their physical and chemical properties Effluent Treatment Plant (ETP) installed for mine’s workshop Treated water is reused in washing activityRaw material handling and storage Indian Cement ReviewThe raw material production of cement plant can be classified into four steps: crushing, grinding, mixing and homogenizing Crushing: the limestone and other materials are crushed into small pieces by cement crusher, such as hammer crusher, Preparation Of Cement Raw Material Cement Mill, Cement Ball mill is a cylinder rotating at about 7080% of critical speed on two trunnions in white metal bearings or slide shoe bearings for large capacity mills Closed circuit ball mill with two compartments for coarse and fine grinding and a drying compartment with lifters are generally found in cement plants for raw material grindingRaw Material DryingGrinding Cement Plant Optimization
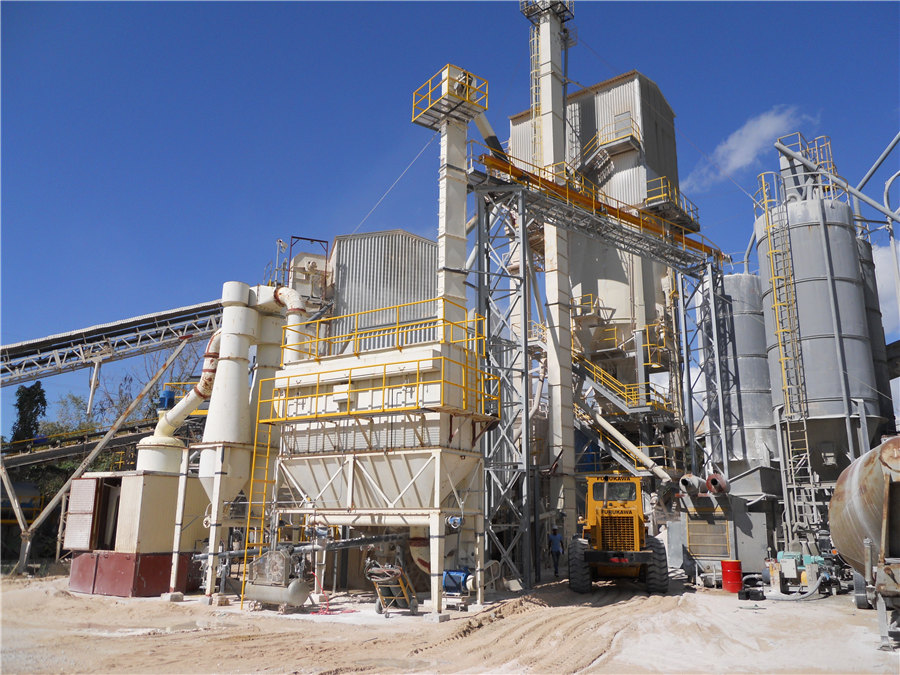
ALTERNATIVE FUELS AND ALTERNATIVE RAW MATERIALS
Objectives of the workshop 12 af/arm coprocessing 15 21 52 bringing solutions to waste producers in cement plants 37 53 Define procedure for sampling and analysis 38 training provided with respect to the use of alternative fuels and alternative raw materials within the Indian cement sector It covers the various aspects of co 2022年3月3日 Cement Raw Materials Grinding Process (Raw Mill System) English VersionRaw Mill System is a system for grinding raw materials in the form of raw materialsCement Raw Materials Grinding Process (Raw Mill System