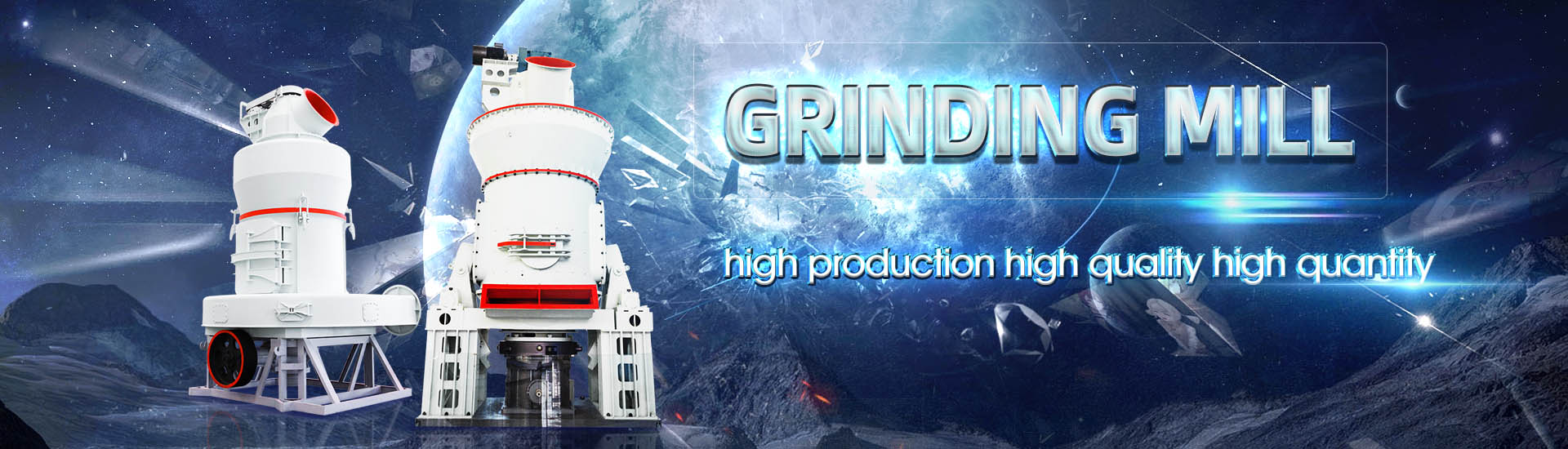
What is the ball consumption of calcite ore ball mill
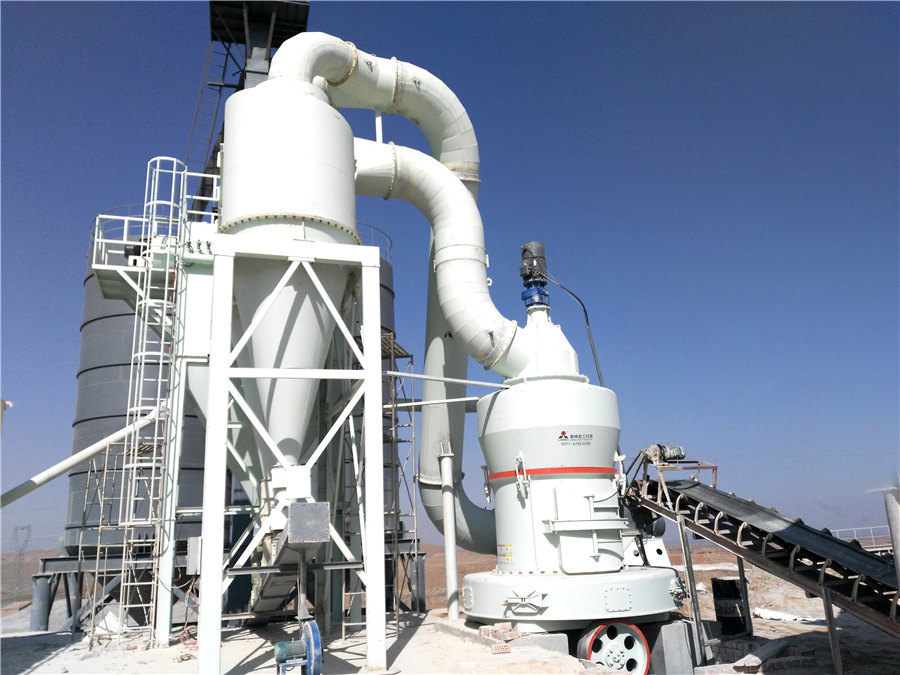
Calculate and Select Ball Mill Ball Size for Optimum
2013年8月3日 In Grinding, selecting (calculate) the correct or optimum ball size that allows for the best and optimum/ideal or target grind size to be achieved by your ball mill is an important thing for a Mineral Processing Engineer AKA 2015年7月29日 The outcomes indicate that the wet grinding technique in conventional ball mill for calcite ore is effective to obtain ultrafine size productsWet Grindability of Calcite to UltraFine Sizes in Conventional Ball 2023年10月27日 The optimal ball size distribution was 12 mm (40%), 20 mm (40%), 32 mm (10%), and 40 mm (10%) for dry finegrinding of calcite ore Finer ball loads were unable to A Review of the Grinding Media in Ball Mills for Mineral Processing 2023年4月23日 the grinding media reduces energy and material consumption in a ball mill Different performances are achieved when different sizes and shapes of grinding media are used [ 12 ](PDF) Grinding Media in Ball MillsA Review
.jpg)
Optimization of Wet Grinding Parameters of Calcite Ore in Stirred
energy consumption in comparison to other fine grinding machines [4–9] study is to influences of operating parameters such as stirrer speed (rpm), ball filling ratio (J), powder filling ratio (fc), 2023年12月12日 Ball mills are used for the second stage of ore grinding in mining operations by proportioning ore piles Controlling the operating conditions of ball mills is one of the key factors(PDF) Control of ball mill operation depending on ball 2014年10月27日 It was found that the ball mill consumed 5467 kWh/t energy to reduce the F 80 feed size of 7222 lm to P 80 product size of 2754 lm while stirred mill consumed 3245 kWh/t Wet Grindability of Calcite to UltraFine Sizes in Conventional Ball 2018年6月1日 In this article, alternative forms of optimizing the milling efficiency of a laboratory scale ball mill by varying the grinding media size distribution and the feed material particle size Effect of ball and feed particle size distribution on the milling
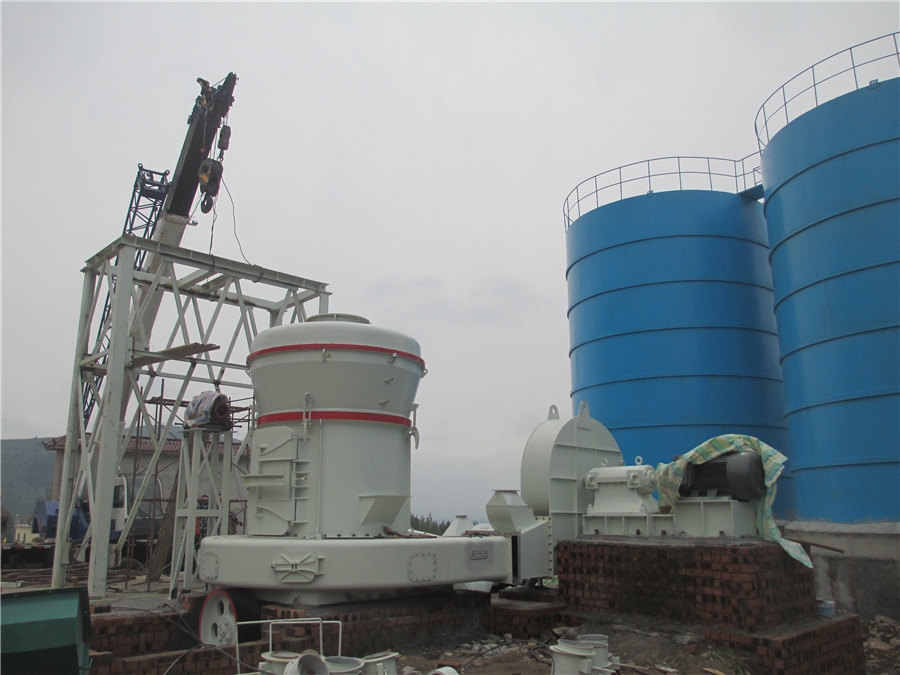
Ball Mill an overview ScienceDirect Topics
The ball milling process is carried out for approximately 100–150 h to obtain uniformsized fine powder In highenergy ball milling, vacuum or a specific gaseous atmosphere is maintained Optimization of Wet Grinding Parameters of Calcite Ore in Stirred Ball Mill Serkan ÇAYIRLI*1 1Niğde Ömer Halisdemir Üniversitesi, Mühendislik Fakültesi, Maden Mühendisliği Bölümü, Niğde Abstract This study focused on ultrafine grinding of calcite powder (CaCO 3) using a vertical stirred ball mill TheOptimization of Wet Grinding Parameters of Calcite Ore in Stirred Ball Mill2020年2月26日 Measurement results of two ball mills in a real ceramic manufacturing plant showed that the proposed calculation models could achieve an accuracy of more than 96% for predicting the ball mill Calculation method and its application for energy consumption of ball 2023年2月15日 After fully understanding the differences between ball mill and rod mill, it also lays the foundation for purchasing equipment and you can choose from the following: 1 By raw material Select a ball mill Ball mill is suitable for What Are the Differences between Ball Mill and Rod
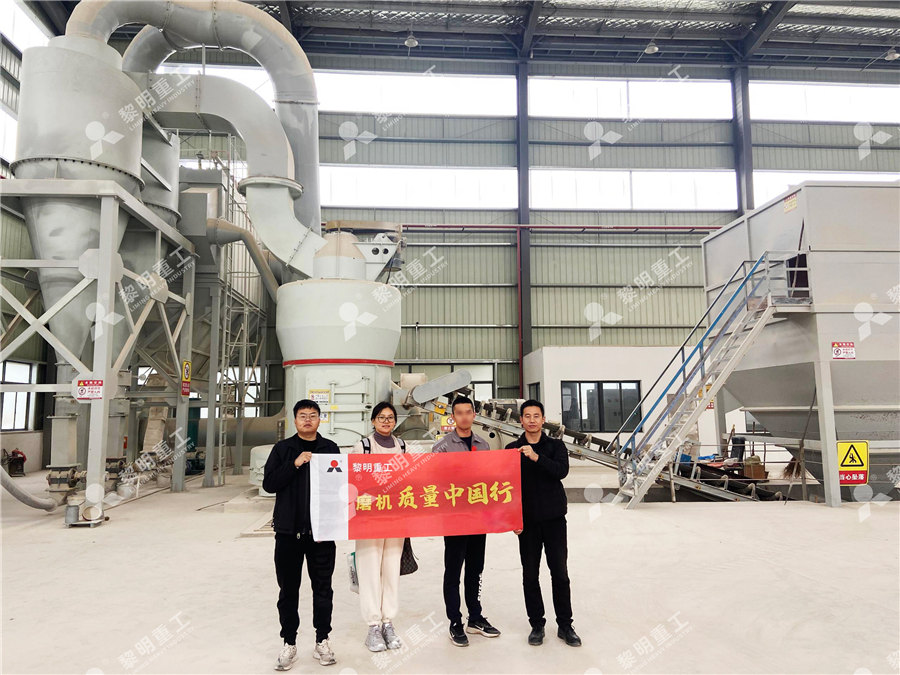
Effect of grinding aids on the grinding energy consumed during
DOI: 101016/JMINENG200909011 Corpus ID: ; Effect of grinding aids on the grinding energy consumed during grinding of calcite in a stirred ball mill @article{Choi2010EffectOG, title={Effect of grinding aids on the grinding energy consumed during grinding of calcite in a stirred ball mill}, author={H I Choi and W Lee and D Kim and 2010年1月1日 The structure and granularity of calcite were measured during dry grinding in a ball mill by Xray diffraction, Fourier transform infrared spectroscopy and laser diffraction, and its morphology was observed by a scanning electron microscopeEffect of grinding aids on the grinding energy consumed during grinding 2017年4月29日 In the previous discussion the fact was established that the work done by a ball when it strikes at the end of its parabolic path is proportional to its weight and velocity; then, since the velocity may be considered as constant for all the balls in the mill, the work done by a ball is proportional to its weight Since the amount of ore crushed varies as the work done upon it, it Grinding Media Wear Rate Calculation in Ball Mill2016年1月1日 The Ball Mill Abrasion (BMA) test was developed by the University of Queensland Materials Performance group to simulate the high stress abrasion conditions experienced in production ball millsA comparison of wear rates of ball mill grinding media
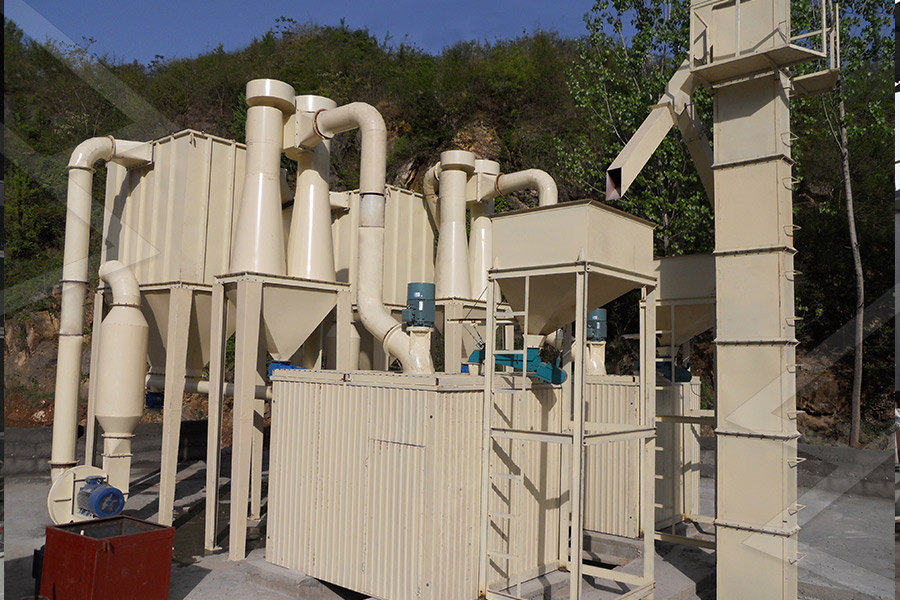
(PDF) Performance optimization of an industrial ball mill for
2017年1月1日 Thus, the performance of an industrial ball mill can be adequately described using the orespecific breakage distribution function together with the systematic variation of the material transport 2013年9月8日 SAG Ball consumption is “average” at 400 g/t while Ball Mill grinding media (3″ balls) usage in 550 g/t Yet, you add steel and nothing seems to happen, tonnage is not noticeably improved You need more tonnage and could actually use a larger/coarser transfer size from the SAG to Ball MillSAG Mill Ball Size Evaluator Evaluation Factors Calculate 2015年12月1日 Download Citation An experimental study on the ultrafine grinding of gypsum ore in a dry ball mill Gypsum is a crystalline form of hydrated calcium sulfate (CaSO42H20) generally used in An experimental study on the ultrafine grinding of gypsum ore in 2020年1月11日 Here the structure means the ratio of ball mill length to its diameter According to the industrial tests, the capacity varies with the ball mill types; Even from the same type of ball mill, the energy consumption and 5 Ways to Improve the Ball Mill Efficiency FTM
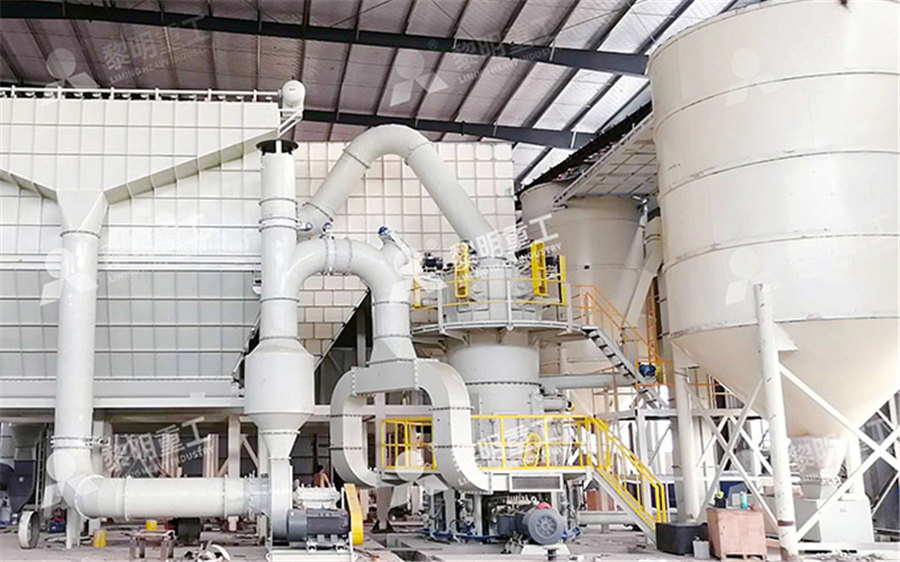
Influences of operating parameters on dry ball mill performance
Micronized calcite can be used both directly and in a coated form in the specified sectors Generally, the milling of calcite is performed in a conventional tumbling mill or stirred ball mill in appropriate fine/ultrafine size ranges for obtaining the desired characteristics of the final product2021年8月10日 Ball mill is one of the common equipment in mineral processing plants It is commonly used in the preparation stage to grind the ore to the required particle size Ball mill investment is large, and energy consumption What's the Price of Ball Mill? miningpedia2022年1月12日 Let's take a look at the difference between ultrafine vertical mill and ball mill +17 [ protected] language >Shibang Industry Technology Group Low energy consumption and large output The production of finished products of different specifications can realize rapid switching The products are highly What is the difference between vertical mill and ball mill?In the world of ore processing, ball mills are a common and essential tool The size of the steel balls used in these mills plays a crucial role in their effectiveness Ball mills are machines used in the mineral processing industry to grind materials into smaller particles These machines come in different sizes and shapes, but all have a cylindrical shell that contains the grinding media What is the size of balls used in ball mills?
.jpg)
Calculate and Select Ball Mill Ball Size for Optimum Grinding
2013年8月3日 In Grinding, selecting (calculate) the correct or optimum ball size that allows for the best and optimum/ideal or target grind size to be achieved by your ball mill is an important thing for a Mineral Processing Engineer AKA Metallurgist to do Often, the ball used in ball mills is oversize “just in case” Well, this safety factor can cost you much in recovery and/or mill liner 2019年8月14日 • Central discharge ball mill: the inlet of medium unloading ball mill is at both ends, and the outlet is in the middle of the ball mill 4 According to the ore discharge of ball mill: • Overflow ball mill: Discharge the ore through hollow shaft • Grid ball mill: Discharge the ore through the plaid plateThe Ultimate Guide to Ball Mills Miningpedia2023年12月12日 In addition, the ore properties are one of the important parameters for the optimal utilizing of the ball mill Ore can have various properties, such as hardness, density, moisture content, etc (PDF) Control of ball mill operation depending on ball load and ore This study focused on ultrafine grinding of calcite powder (CaCO3) using a vertical stirred ball mill The influences of various operating parameters such as stirrer speed (rpm), ball filling ratio (J), powder filling ratio (fc), solid ratio (wt%) and grinding time were studied under wet conditions The experiments were carried out in a batch mode of operation The experimental results were Optimization of Wet Grinding Parameters of Calcite Ore in Stirred Ball Mill
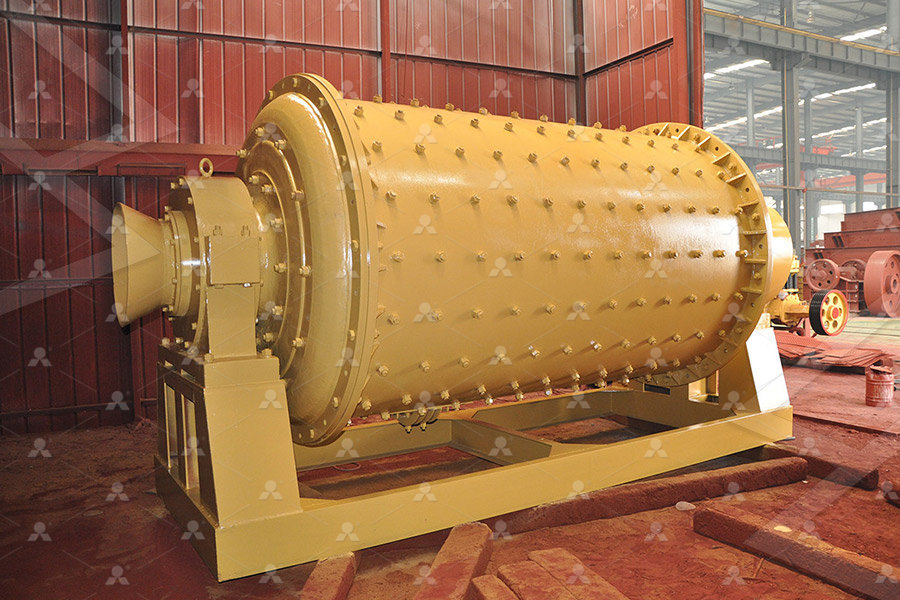
Effect of ball and feed particle size distribution on the milling
2018年2月1日 In another study to investigate ball size distribution on ball mill efficiency by Hlabangana et al [50] using the attainable region technique on a silica ore by dry milling, a threeball mix of 2010年1月31日 Request PDF Effect of grinding aids on the grinding energy consumed during grinding of calcite in a stirred ball mill A series of wetgrinding experiments has been carried out on inorganic Effect of grinding aids on the grinding energy consumed during grinding The ball impact energy on grain is proportional to the ball diameter to the third power: 3 E K 1 d b (3) The coefficient of proportionality K 1 directly depends on the mill diameter, ball mill loading, milling rate and the type of grinding (wet/dry) None of the characteristics of the material being ground have any influence on K 1THE OPTIMAL BALL DIAMETER IN A MILL 911 Metallurgist2023年1月8日 Particle size distributions of feed for calcite grinding by the stirred mill and ball mill (modified from [39,40] Mills used in this study (a) stirred mill [39], (b) ball mill [40] Figure 4(PDF) Comparison of Particle Shape, Surface Area, and
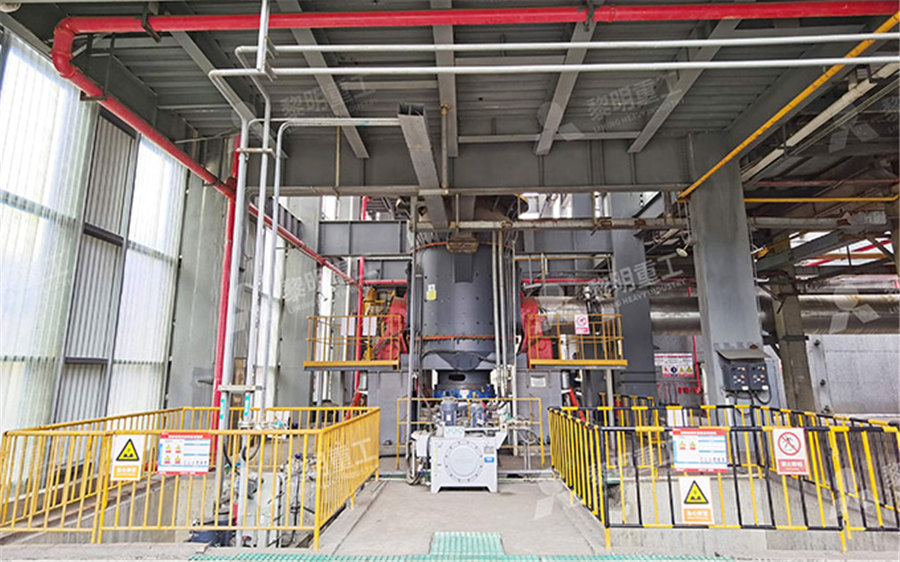
What is the Difference Between Tumbling Mill and Ball Mill?
However, they also have some disadvantages, such as high energy consumption and the need for a high degree of maintenance to keep them operating efficiently Ore Ball Mill; Ceramic Ball Mill; Continuous Ball Mill; Batch Ball Mill; Grate Ball Mill; Overflow Ball Mill; Wet Ball Mill; Dry Ball Mill; Small Ball Mill; Large Ball Mill;2023年10月27日 The ball mill is a rotating cylindrical vessel with grinding media inside, which is responsible for breaking the ore particles Grinding media play an important role in the comminution of mineral A Review of the Grinding Media in Ball Mills for Mineral Processing2023年4月28日 Reactive ball milling refers to the process of using a ball mill to cause chemical reactions that would not ordinarily occur at room temperature [6] Different mill types or alterations to milling parameters may lead to distinct reaction pathways for chemical reactions, and the milling time required to achieve the desired structure also varies depending on the mill Parametric study on four station ball mill for synthesis of ultrafine 2022年8月18日 1 Lithium ore grid ball mill In the lithium ore dressing plant, the grid ball mill is mainly responsible for the grinding of coarse minerals, and is mostly used in the firststage grinding operation Due to its special ore discharge plate design, the ball mill has a large ore discharge particle size and less blocking phenomenon 2 Lithium ore What are the commonly used lithium ore ball mill for lithium ore
.jpg)
SAG vs AG Mills: Understanding the Key Differences ball mills
SAG mills are often used in conjunction with a ball mill or pebble mill to achieve the desired grind size SAG mills are primarily used in AG mills also use a fraction of the energy needed for SAG mills to grind the same amount of ore Comparison of Power Consumption The power consumption of SAG and AG mills depends on several factors 1989年1月1日 This problem is considered in this paper and some solutions are put forward Experiments were made on copper ore, andesite and limestone, and it was found that the change of the mass passing a test screen G could be related to the aperture size P k of the screen by the formula: G=K 1 P kThe grindingproduct size, P, in a Bond ball mill, which is given by the Calculation of energy required for grinding in a ball millOptimization of Wet Grinding Parameters of Calcite Ore in Stirred Ball Mill Serkan ÇAYIRLI*1 1Niğde Ömer Halisdemir Üniversitesi, Mühendislik Fakültesi, Maden Mühendisliği Bölümü, Niğde Abstract This study focused on ultrafine grinding of calcite powder (CaCO 3) using a vertical stirred ball mill TheOptimization of Wet Grinding Parameters of Calcite Ore in Stirred Ball Mill2020年2月26日 Measurement results of two ball mills in a real ceramic manufacturing plant showed that the proposed calculation models could achieve an accuracy of more than 96% for predicting the ball mill Calculation method and its application for energy consumption of ball
.jpg)
What Are the Differences between Ball Mill and Rod
2023年2月15日 After fully understanding the differences between ball mill and rod mill, it also lays the foundation for purchasing equipment and you can choose from the following: 1 By raw material Select a ball mill Ball mill is suitable for DOI: 101016/JMINENG200909011 Corpus ID: ; Effect of grinding aids on the grinding energy consumed during grinding of calcite in a stirred ball mill @article{Choi2010EffectOG, title={Effect of grinding aids on the grinding energy consumed during grinding of calcite in a stirred ball mill}, author={H I Choi and W Lee and D Kim and Effect of grinding aids on the grinding energy consumed during 2010年1月1日 The structure and granularity of calcite were measured during dry grinding in a ball mill by Xray diffraction, Fourier transform infrared spectroscopy and laser diffraction, and its morphology was observed by a scanning electron microscopeEffect of grinding aids on the grinding energy consumed during grinding 2017年4月29日 In the previous discussion the fact was established that the work done by a ball when it strikes at the end of its parabolic path is proportional to its weight and velocity; then, since the velocity may be considered as constant for all the balls in the mill, the work done by a ball is proportional to its weight Since the amount of ore crushed varies as the work done upon it, it Grinding Media Wear Rate Calculation in Ball Mill
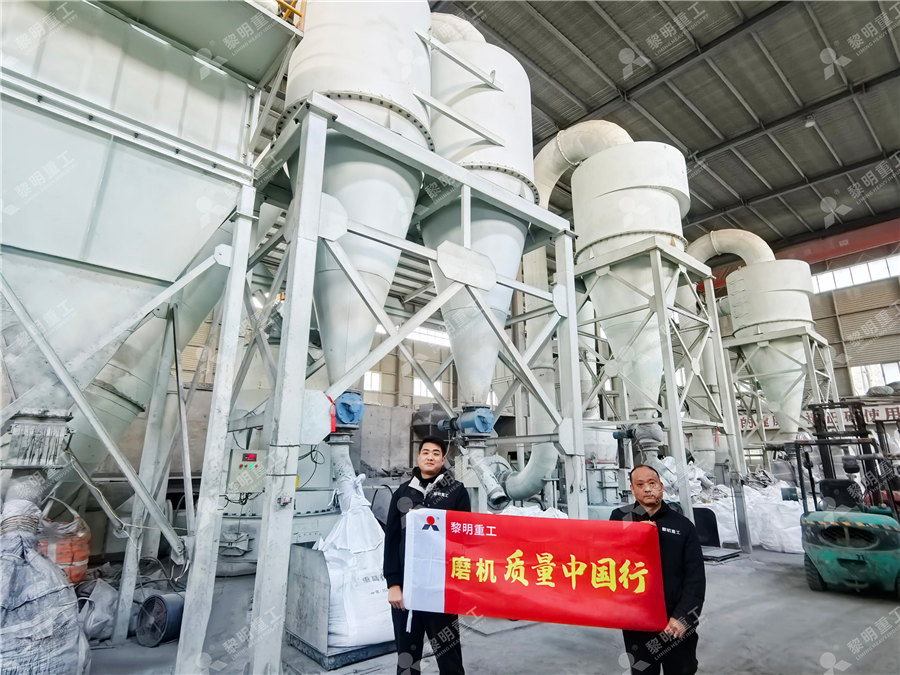
A comparison of wear rates of ball mill grinding media
2016年1月1日 The Ball Mill Abrasion (BMA) test was developed by the University of Queensland Materials Performance group to simulate the high stress abrasion conditions experienced in production ball mills2017年1月1日 Thus, the performance of an industrial ball mill can be adequately described using the orespecific breakage distribution function together with the systematic variation of the material transport (PDF) Performance optimization of an industrial ball mill for 2013年9月8日 SAG Ball consumption is “average” at 400 g/t while Ball Mill grinding media (3″ balls) usage in 550 g/t Yet, you add steel and nothing seems to happen, tonnage is not noticeably improved You need more tonnage and could actually use a larger/coarser transfer size from the SAG to Ball MillSAG Mill Ball Size Evaluator Evaluation Factors Calculate 2015年12月1日 Download Citation An experimental study on the ultrafine grinding of gypsum ore in a dry ball mill Gypsum is a crystalline form of hydrated calcium sulfate (CaSO42H20) generally used in An experimental study on the ultrafine grinding of gypsum ore in