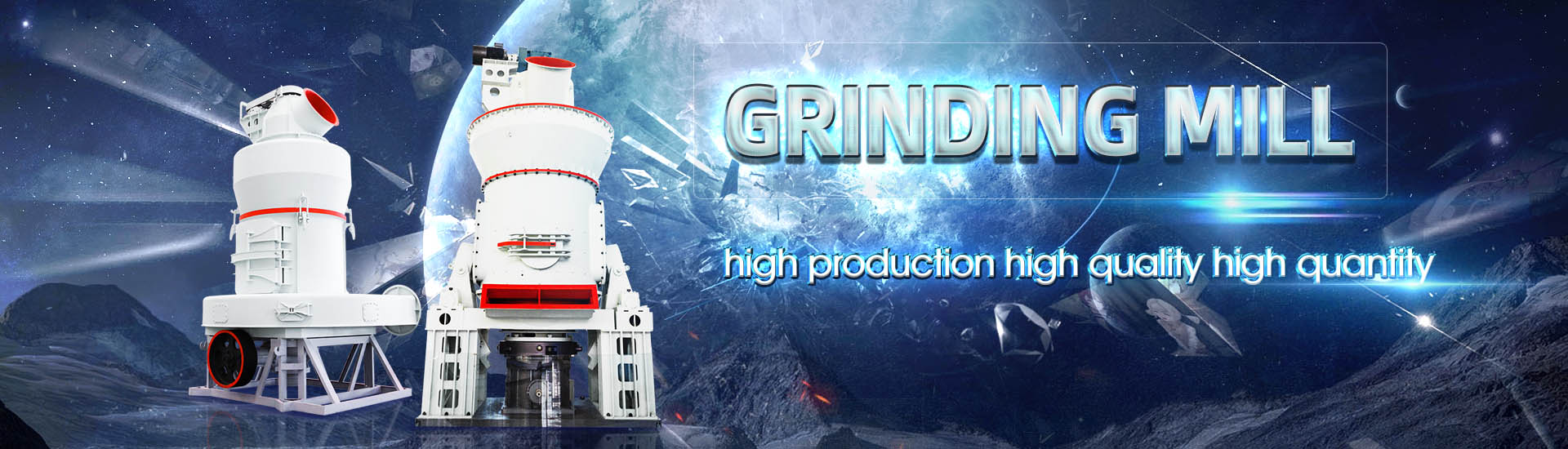
Imported grinding system ore mill
.jpg)
Grinding Metso
Customized grinding mill parts including heads, shells, trunnions and liners, main bearings, gears and pinions, and more! Metallic, PolyMet™, Megaliner™, Rubber and Orebed™ mill liners for Ideal for grinding finer products, stirred mills are known for their energy efficiency and compaStirred MillsBrowse Metso's wide offering of reliable grinding mills: AG mills, SAG mills, ball and pebble mills, and stirred mills to fit your needs Our pioneering innovations in horizontal grinding mills technology offer exceptional performance and Grinding mills for mining and minerals processingThe IsaMill™ is a largescale energy efficient continuous grinding technology specifically developed for rugged metalliferrous applications Glencore Technology supplies the IsaMill™ technology to mining operations around the Ultrafine Grinding and the IsaMill™ Technology
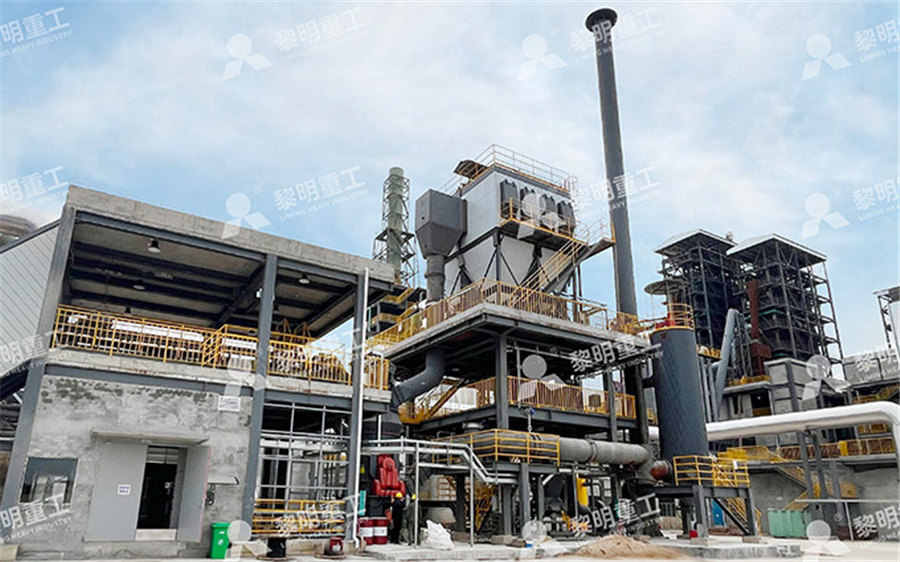
Mills for minerals and ores Loesche
The dry milling of ore in LOESCHE vertical roller mills has shown significant process advantages, as well as economic and ecological benefits To demonstrate these a mobile oregrinding plant the OGPmobile has been IsaMill™ uses horizontal milling to secure better energy efficiency, product size and availability The IsaMill™ has realworld success in 143 metalliferous installations across 23 countries It’s IsaMill™ Glencore TechnologyFind your ore mill easily amongst the 42 products from the leading brands (Fritsch GmbH, Retsch, Eriez, ) on DirectIndustry, the industry specialist for your professional purchasesOre mill, Ore grinding mill All industrial manufacturersProvides highest availability for your grinding mill ; Robustness of system allows for operation under the most extreme environmental conditions (high altitudes, varied climates, remote locations) Operator can react to changes in ore Gearless mill drives Grinding ABB
.jpg)
Ore Grinding SpringerLink
2023年7月20日 Ore grinding is a process to further reduce and disperse the ore particle size In the mineral processing industry, ore grinding is the particle size preparation before the 2020年6月3日 Grinding mills are some of the most important equipment in mines, processing over a few thousand tons of ore every hour It is not uncommon to see these days that a single line of a grinding circuit consisting How grinding mill design changed over the last 30 yearsMethods and Process of Ore Grinding According to the material transmission methods, ore grinding is divided into dry grinding, wet grinding, and moist grinding Dry grinding relies on Ore Grinding Methods and Process of Ore GrindingJ Cent South Univ (2014) 21: 3485−3491 DOI: 101007/s1177101423264 Strengthening pelletization of manganese ore fines containing high combined water by high pressure roll grinding andStrengthening pelletization of manganese ore fines containing
.jpg)
SemiAutogenous Grinding (SAG) mill DEM simulation YouTube
2019年9月3日 Grinding simulation of ore particles in a SemiAutogenous Grinding (SAG) mill to optimize grinding efficency, reduce wear or evaluate design changesVSHGM grinding roller mill can process marble, calcite, gypsum, barite, talc, pyrophyllite mineral, kaolin, bentonite, illite, vermiculite, sepiolite and potassium ore The fineness of the finished powder is between 600 category and 3000 Ultrafine Powder Ring Rolling Mil Ore Grinding MillRequest PDF On Mar 15, 2015, Mathis Reichert and others published Research of iron ore grinding in a verticalrollermill Find, read and cite all the research you need on ResearchGateResearch of iron ore grinding in a verticalrollermill1 Population balance model approach to ball mill optimization in iron ore grinding Patricia M C Faria1,2, Luís Marcelo Tavares2 and Raj K Rajamani3 1 Vale SA, Brazil 2 Department of Population balance model approach to ball mill optimization in iron ore
.jpg)
Designing a Quenching System for Grinding Steel Balls Case
The availability of grinding balls of superior quality than those produced at a Harare company in Zimbabwe, resulted in loss of business In order to retain business, a new ball that has a similar chemical composition to that of imported grinding balls was developed Proper thermomechanical treatment has to be done after casting, inIn the mill, the mixture of medium, ore, and water, known as the mill charge, is intimately mixed, the medium comminuting the particles by any of the above methods Apart from laboratory testing, grinding in mineral processing is a continuous process, material being fed at a controlled rate into one end of the mill and discharging at the other end after a suitable dwell (residence) timeGrinding Mill an overview ScienceDirect Topics2024年11月28日 Additionally, the ball mill’s versatility allows parameters such as speed, feed rate and material composition to be adjusted, making it adaptable to different types of lithium ore This flexibility is essential to optimize the grinding process for each specific ore type, thereby increasing cost efficiency and resource sustainabilityBall Mill Is The Key To Grinding Lithium Ore JXSC Machinerydrive system to be overloaded when the mill filled with copper ore is started For this reason, the mill is stopped only in the case of a failure or planned maintenance work The aim is to minimize the potential number of startups, as the mill at a standstill must be later started under full loadEnergy Efficiency Analysis of Copper Ore Ball Mill Drive Systems
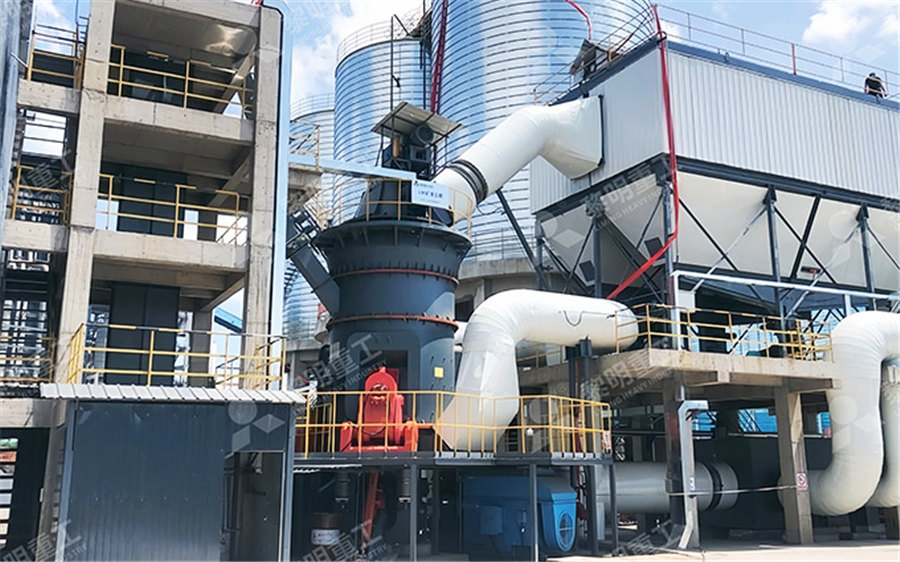
Raw Grinding System PDF PDF Mill (Grinding) Turbine
Raw Grinding Systempdf Free download as PDF File (pdf), Text File (txt) or read online for free The document discusses raw grinding systems using vertical roller mills It provides an overview of vertical roller mill components, operating principles, and processes Key parts include the mill body, feed system, separator, table and rollers, motor and reducer, and hydraulic system2015年3月15日 For the grinding tests, a Loesche mill LM45 (table diameter 045 m) is used (Fig 2a) This pilot scale mill is a special development for ore grinding, which is reflected by several features The mill has four rollers, which are able to stress the particle bed with grinding pressures of up to 5000 kN/m 2Research of iron ore grinding in a verticalrollermill2019年6月15日 Worldwide, the grinding process is one of the most energyintensive processes (Wei and Craig, 2009) In Chile it corresponds, on average, to almost 50% of the electrical consumption of the copper process, from which the semiautogenous grinding mill (SAG mill) is a significant component (COCHILCO, 2013)Studying the integration of solar energy into the operation of a 2020年3月28日 Based on batch grinding method and normalization idea, a conical ball mill is used and a quantitative separation method of grinding characteristics of multicomponent complex ore is proposedDevelopment of a Novel Grinding Process to Iron Ore
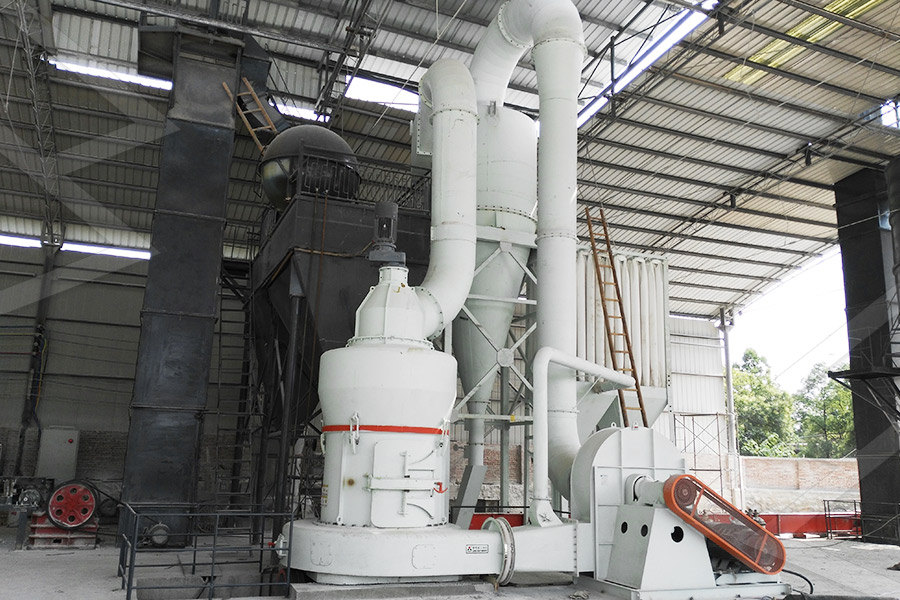
(PDF) Control of ball mill operation depending on ball load and ore
2023年12月12日 Ore can have various properties, such as hardness, density, moisture content, etc, which can affect the ore’s productivity and grinding efficiency Discover the world's research 25+ million members1997年12月1日 Measurement system of the mill charge in grinding ball mill circuits Author links open overlay panel J Kolacz Show more An introduction to the practical aspects of ore treatment and mineral Intelligencebased supervisory control for optimal operation of a DCScontrolled grinding system 2013, IEEE Transactions on Control Measurement system of the mill charge in grinding ball mill 2023年4月23日 grinding media in a grinding mill with about 2630 wt% chrome by Chen et al [37] using a phosphate ore in a modified ball laboratory ball mill whose electrochemical potential could be controlled(PDF) Grinding Media in Ball MillsA Review ResearchGate2013年4月1日 A simple and novel nonlinear model of a runofmine ore grinding mill circuit, developed for process control and estimation purposes, is validatedAnalysis and validation of a runofmine ore grinding mill circuit
.jpg)
Research of iron ore grinding in a verticalrollermill
2015年3月15日 The grinding parts of a Loesche mill (Fig 1) are a rotating table (1) with a horizontal grinding track and rollers (2), which are pressed onto the table by lever arms and a hydro pneumatic spring systemBetween the working surfaces of track and rollers, particle bed comminution takes place A dynamic air separator (3) is located above the grinding chamber, 2013年8月1日 Apart from these cost factors, one of the major unsolved problems in the optimal design of ball mills concerns the equilibrium media size distribution in the mill, which is determined by the rate at which makeup media is added to the mill, as well as the rate at which these grinding media are consumed (Austin and Klimpel, 1985)Reliable prediction of grinding media Consumption of steel grinding media in mills – A reviewFind your wet grinding mill easily amongst the 45 products from the leading brands (Fritsch GmbH, Retsch, NETZSCH, for ore concrete for asphalt for cement for mortar for metals (5) copper for aluminum mineral (5) General The agitator cooling with the newlydeveloped Neos grinding system stands for maximum performance, Wet grinding mill, Wet grinding grinding system All industrial 5 Milltomill mass air and fuel balance within ±5% of the mean 6 Mill outlet temperatures optimal (65°C) and based on volatility, inlet temperature limitations and considering the mills heat balance for a respective fuel [6] 7 Minimum fuel line velocity of 1,005 meter/min or 1675 meter/second (or 3,300 ft/min) 8Pulveriser Mill Performance Analysis Optimisation in Super
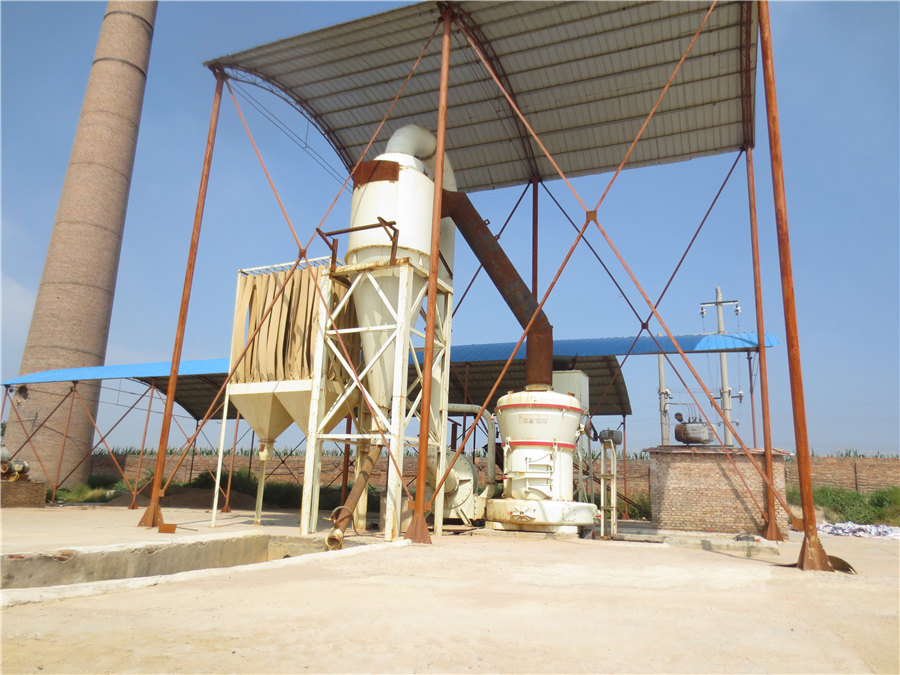
Can ceramic balls and steel balls be combined in an
2022年11月1日 It is also known that the ore processed by the plant is iron, with a Mohs hardness of between 8 and 85 and a specific gravity of 42 The P80 of 028 mm and the P50 of 010 mm, as depicted in Fig 1, represents the particle size distribution of the feed to the secondary millIt should be emphasised that the 30 mm refers to the diameter of the daily 2014年10月1日 Request PDF Copper Ore Grinding in a Mobile Vertical Roller Mill Pilot Plant Vertical roller mills (VRM) have been used extensively for comminuting both cement raw materials and minerals like Copper Ore Grinding in a Mobile Vertical Roller Mill Pilot PlantMoreover, milling machines have highcost energy consumption and maintenance expenses [8,9] Semiautogenous grinding (SAG) mills have been more common for mining due to economic advantages, such Process flow diagram of the SAG mill ResearchGateYou can apply our ball mill in ore beneficiation plant to grind iron ore, copper ore, gold ore, lead ore, zinc ore, kaolin, bentonite, feldspar, silica, etc Grid Type Ball Mill The Grid Type Ball Mill has high discharge speed and high productivity (2030% higher than Ball Mill Ball Grinding Mill SKE
.jpg)
Friction and wear of liner and grinding ball in iron ore ball mill
2017年11月1日 An iron ore mill relies on the grinding and impact of grinding balls to complete iron ore crushing The operating process of an iron ore mill is as follows: first, the ores are poured into the mill, and both the ores and the grinding balls are lifted by the lifting bar arranged on the wall of the cylinder body to a certain height, after which they fall onto the bottom of the mill to 2017年6月15日 Friction and wear of liner and grinding ball in iron ore ball mill June 2017; Tribology International 115:506–517; (PHSP) grinding system is compared with a pure spherical grinding systemFriction and wear of liner and grinding ball in iron ore ball millGrinding Solutions Grinding is the required process when size reduction of below 520 mm is neededGrinding is a powdering or pulverizing process, and it can use three methods Crushing Solutions From large primary jaws and gyratories to cones and impacts for tertiary and quaternary finishing, Gulin has the right crusher and crusher parts » Copper Concentrating what duty on mining equipment imported from china to canada2017年10月13日 System development required months of ore and density sampling, an excessive amount of mill startups and shutdowns, hourly measurements of SAG mill ball charge and mill loading characteristics Unfortunately the mathematical model was unable to adequately compensate for the variations in ore consistencySAG Mill Expert System Grinding Circuit 911Metallurgist
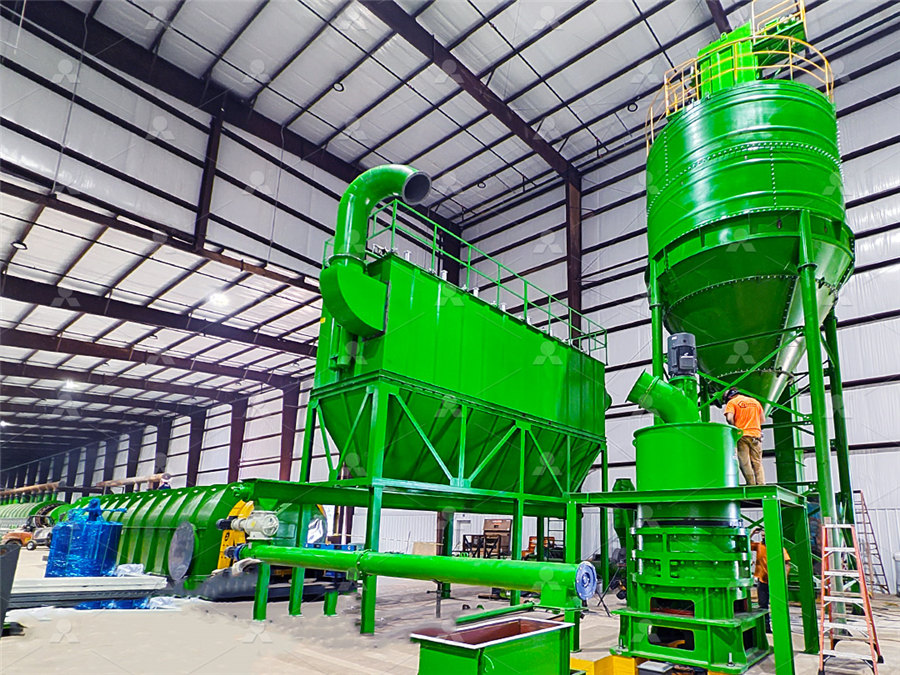
Control of ball mill operation depending on ball load and ore
ore and corresponds to the scheme, including medium and small stage ball grinding provides a comparative analysis of a wide range of ore processing steps and requires 515% energy in a selfgrinding mill [3] 1 Figure 2 Ball mill process control system using ACS (Adaptable Control System) Figure 2 shows that the input and output signalsJ Cent South Univ (2014) 21: 3485−3491 DOI: 101007/s1177101423264 Strengthening pelletization of manganese ore fines containing high combined water by high pressure roll grinding andStrengthening pelletization of manganese ore fines containing 2019年9月3日 Grinding simulation of ore particles in a SemiAutogenous Grinding (SAG) mill to optimize grinding efficency, reduce wear or evaluate design changesSemiAutogenous Grinding (SAG) mill DEM simulation YouTubeVSHGM grinding roller mill can process marble, calcite, gypsum, barite, talc, pyrophyllite mineral, kaolin, bentonite, illite, vermiculite, sepiolite and potassium ore The fineness of the finished powder is between 600 category and 3000 Ultrafine Powder Ring Rolling Mil Ore Grinding Mill
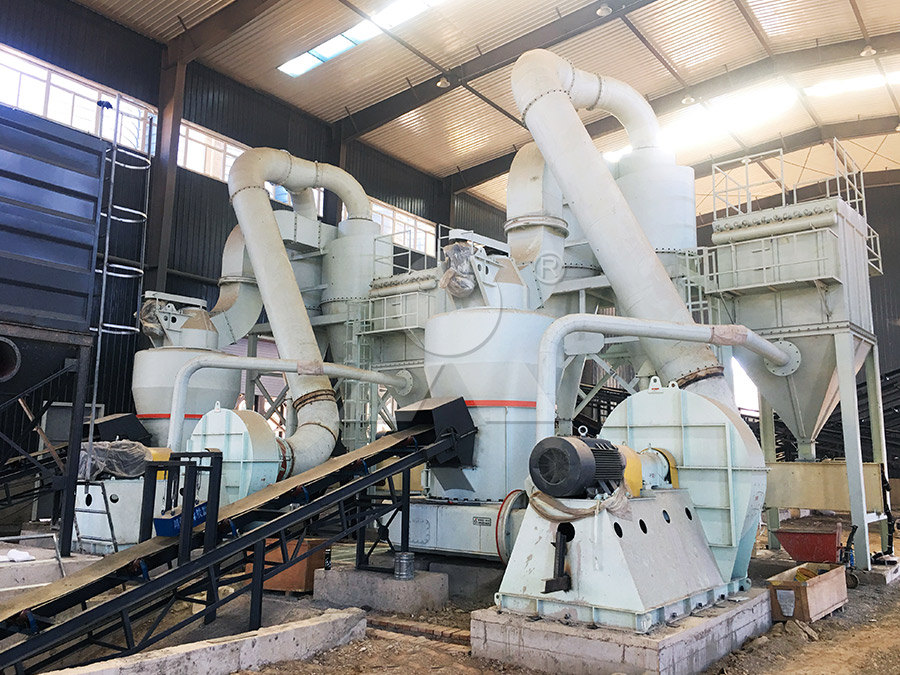
Research of iron ore grinding in a verticalrollermill
Request PDF On Mar 15, 2015, Mathis Reichert and others published Research of iron ore grinding in a verticalrollermill Find, read and cite all the research you need on ResearchGate1 Population balance model approach to ball mill optimization in iron ore grinding Patricia M C Faria1,2, Luís Marcelo Tavares2 and Raj K Rajamani3 1 Vale SA, Brazil 2 Department of Population balance model approach to ball mill optimization in iron ore The availability of grinding balls of superior quality than those produced at a Harare company in Zimbabwe, resulted in loss of business In order to retain business, a new ball that has a similar chemical composition to that of imported grinding balls was developed Proper thermomechanical treatment has to be done after casting, inDesigning a Quenching System for Grinding Steel Balls Case In the mill, the mixture of medium, ore, and water, known as the mill charge, is intimately mixed, the medium comminuting the particles by any of the above methods Apart from laboratory testing, grinding in mineral processing is a continuous process, material being fed at a controlled rate into one end of the mill and discharging at the other end after a suitable dwell (residence) timeGrinding Mill an overview ScienceDirect Topics
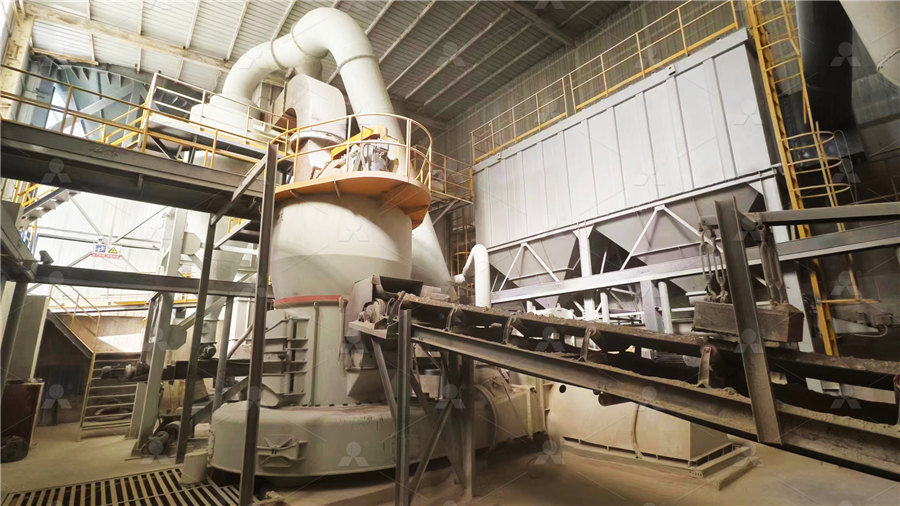
Ball Mill Is The Key To Grinding Lithium Ore JXSC Machinery
2024年11月28日 Additionally, the ball mill’s versatility allows parameters such as speed, feed rate and material composition to be adjusted, making it adaptable to different types of lithium ore This flexibility is essential to optimize the grinding process for each specific ore type, thereby increasing cost efficiency and resource sustainabilitydrive system to be overloaded when the mill filled with copper ore is started For this reason, the mill is stopped only in the case of a failure or planned maintenance work The aim is to minimize the potential number of startups, as the mill at a standstill must be later started under full loadEnergy Efficiency Analysis of Copper Ore Ball Mill Drive SystemsRaw Grinding Systempdf Free download as PDF File (pdf), Text File (txt) or read online for free The document discusses raw grinding systems using vertical roller mills It provides an overview of vertical roller mill components, operating principles, and processes Key parts include the mill body, feed system, separator, table and rollers, motor and reducer, and hydraulic systemRaw Grinding System PDF PDF Mill (Grinding) Turbine