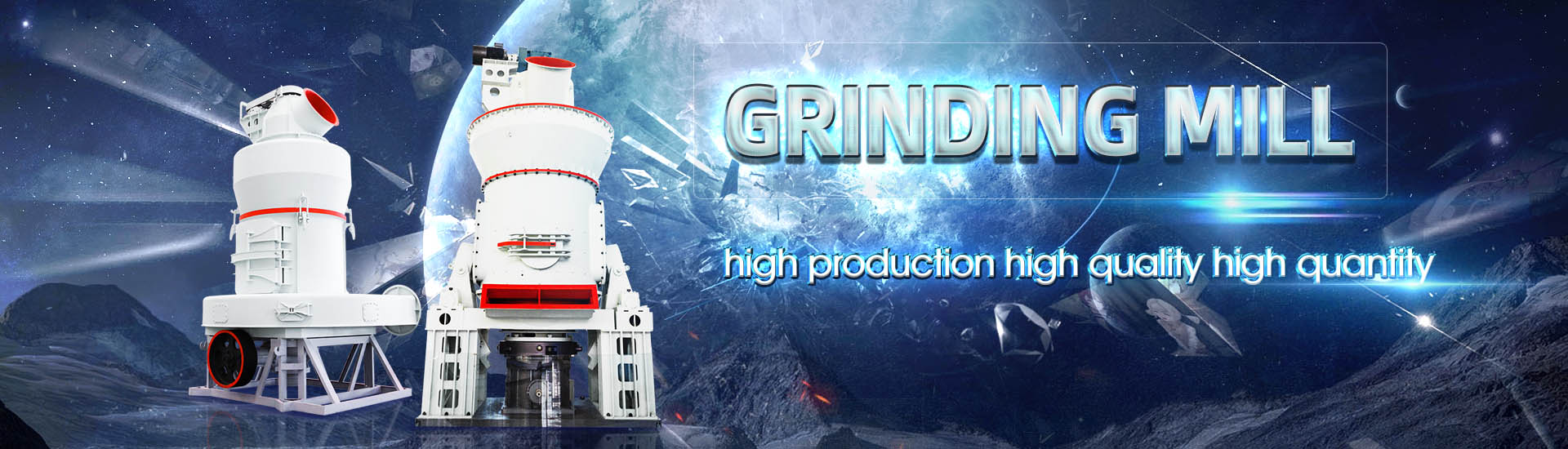
Coal grinding fineness control range and reasons
.jpg)
COAL GRINDING IMPS: more than meets the eye Gebr Pfeiffer
l control range is between 30100 per cent Partload operation may become necessary as a result of load variations in injectiontype grinding mills installed in power plants, changing fuel qualities and a grindability other2022年5月1日 This study investigated ultrafine coal grinding performance of four low to moderatecost grinding media in a laboratory stirred mill Kinetic grinding tests showed that Optimization of operating conditions on ultrafine coal grinding 2017年11月15日 A method for choosing the optimum fineness of coal in pulverisedfuel boilers is presented This method is based on economic criteria and takes into account variations of Optimisation of coal fineness in pulverisedfuel boilers2015年8月1日 Power plant performance and reliability is highly influenced by coal mills that grind, dry, and transport coal to the furnace This paper presents a review of the current state Review of control and fault diagnosis methods applied to coal
.jpg)
CONTRIBUTION TO DETERMINATION OF COAL GRINDABILITY
Hardgrove grindability index (HGI) is determining factor of energy consumption during grinding The HGI value is used for more detailed coal specification and is significant also for the design ABSTRACT: The paper describes the beneficial application of online coal flow measurement and control and online coal fineness measurement for optimization of the combustion process CPRI Online Coal Flow Balancing and Fineness Adjustmentthis dissertation was to investigate the effect of coal feedstock property variation on the vertical spindle coal pulverising mill’s performance to facilitate optimal plant performance Plant design Performance optimisation of vertical spindle coal pulverisersToday's coalfired utility boiler operation needs pulverizer designs to supply pulverized coal with required throughput and coal fineness, and also perform with lower specific power Coal Pulverizer Design Upgrades to Meet the Demands of Low
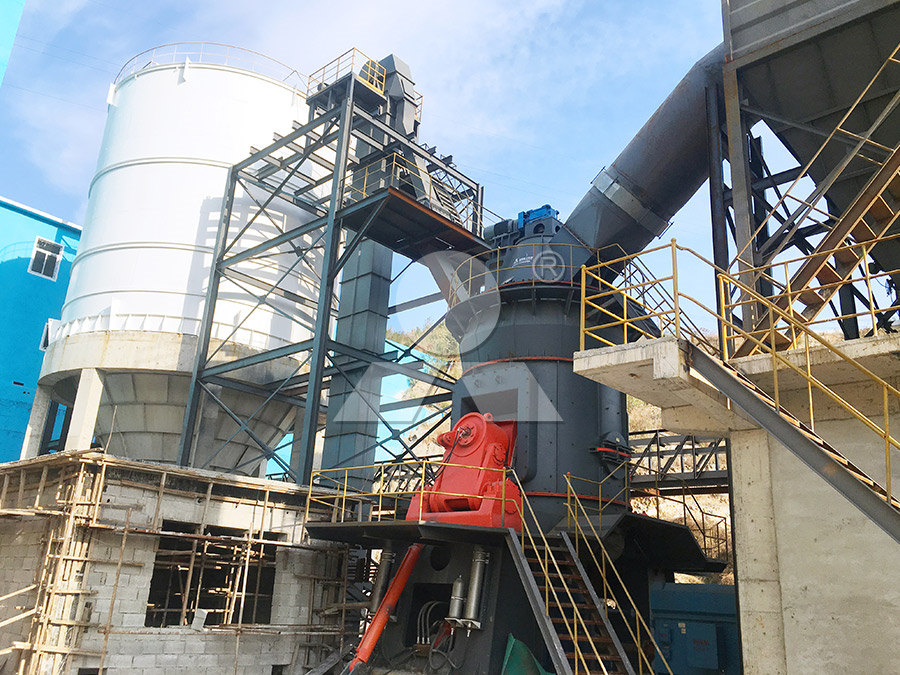
PowerGen 2008, Orlando, USA Online measurement of coal
Knowledge of the coal particle size distribution, coal mass flow and the air/fuel ratio inside the pipe is a prerequisite for optimal combustion and boiler performance Since combustion takes The rate of coal feed is normally determined automatically by a combustion control system, taking into account the MW demand on the unit, coal quality, and the number of pulverizer in service International Journal for Research in Engineering Application Online measurement of coal fineness and airfuel ratio inside the coal pipe Michael Schreiber, Michael Haug, Max Starke, The system measures particles in the range from 20 µm up to 4 mm and The direct cost of coal grinding is a function of the wear and tear of PowerGen 2008, Orlando, USA Online measurement of coal fineness fusion temperature of the coal Coal fineness also plays an important role in being able to utilize coals with elevated iron levels Many slagging problems associated with high sulfurlow fusion coals can be traced back to poor grinding (fineness) of the coal Large pyrite particles escape from the mill and do not completely oxidize in the flameCoping With Coal Quality Impacts on Power Plant Coal
.jpg)
Reprint from ZKG 3 Gebr Pfeiffer
2 Design features of MPS mills for coal grinding Depending on the material to be ground, through put rates of 5200 t/h can be achieved in a fineness range between 1% R0063 mm and 25 % R0090 mm Thus, the MPS coal grinding mill MPS 3070 Once normal coal flow is applied to the mill, a full mill test should be conducted This should include isokinetic coal sampling and dirty airflow measurements through each fuel line to determine air fuel balance and coal fineness Primary airflow “HotK” calibrations of the primary airflow measuring element should also be conductedThe Storm Approach to Coal Pulverizer OptimizationEffects of Grinding Process on Properties of Coal Bottom Ash 3 Besides that, Alkali silica reaction (ASR) is also a prominent issue in concrete, which could be minimized through introducing Effects of Grinding Process on the Properties of the Coal Bottom a sample of analysed material (product constant fineness method) or the granularity composition of final products is compared with the same consumption of grinding work (constant method of useful grinding work) Grindability determination methods based on constant fineness of grinding are labour and time demandingCONTRIBUTION TO DETERMINATION OF COAL GRINDABILITY USING HARDGROVE METHOD
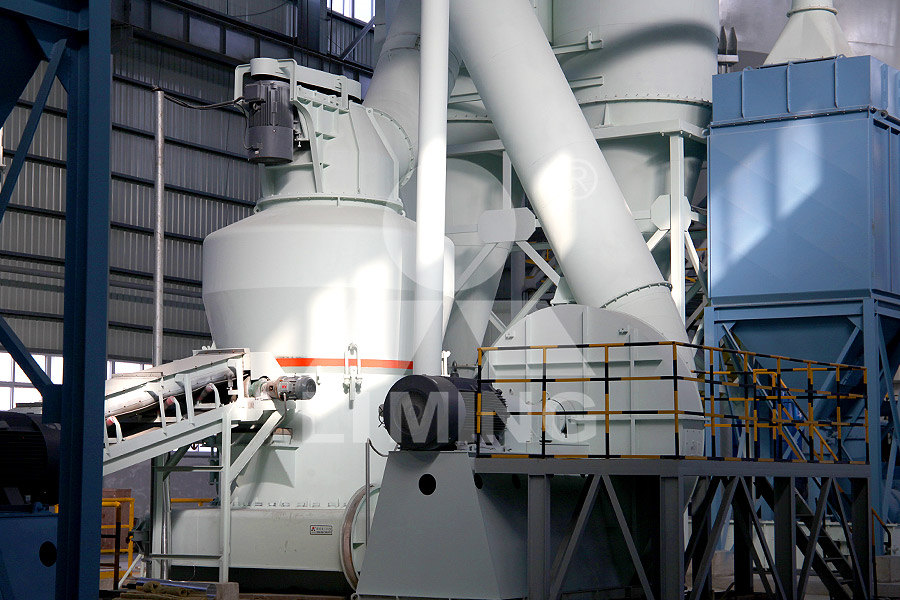
Review of control and fault diagnosis methods applied to coal
2015年8月1日 Mill problems originate mainly due to poor controls or faults occurring within the milling system As discussed by GQ Fan and NW Rees [3], the control of mills remains very simple in most of the power plants due to the fact that the mill system is highly nonlinear with strong coupling among the variables and it is very difficult to measure some important characteristics to better match the fineness with the furnace requirements Inherently, the rotational effects of the dynamic classifier and better fineness improve coal and air distribu tion to the coal pipes and to the burners Improved coal and air distribution allows operation at lower excess air, which results inPulverizer Fineness and Capacity Enhancements at Danskammer 2016年4月5日 In PFboilers, coal is pulverised in a mill (or pulveriser) before being entrained by primary combustion air to burners, to form a high temperature flame in the furnace of the boiler (1000–1600 °C) [2]The fineness of the coal powder, as well as the uniformity of the coal flow sent to each burner fed by the same mill, are crucial parameters to achieve an effective combustion Online monitoring of coal particle size and flow distribution in coal 132 Loesche Mills for Solid Fuels Coal Mill E 2016 Free download as PDF File (pdf), Text File (txt) or read online for free Loesche has been involved in processing solid fuels since 1925 Some key events include delivering their first coal mill in 1927 and introducing hydraulic systems in 1961 Their mills are distinguished by grinding without metal contact, suitability for 132 Loesche Mills For Solid Fuels Coal Mill E 2016
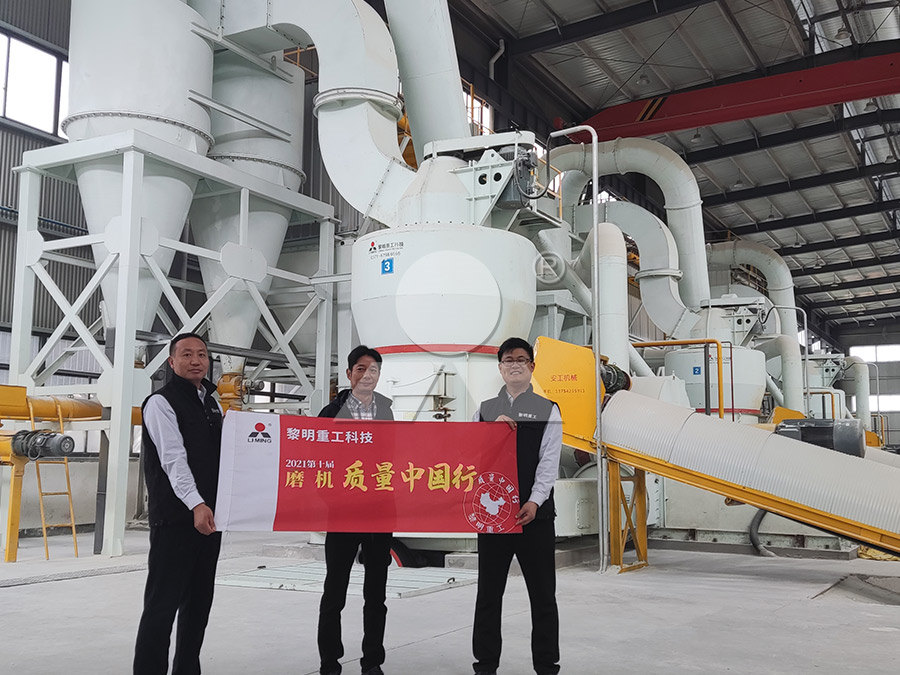
Cement Clinker Quality Control
Coal fines are usually prepared by air swept coal mill or vertical mill In order to produce highquality clinker, the fineness of coal fines should be controlled at about 12%, and its moisture content should be controlled within 10% The machines that are usually used to dry the coal fines are rotary dryers33 Coal Particulate Size and Fineness Figure 7 shows the coal fineness from the sampled particulates of the four PC pipes for the two elevations from mills 20 and 40 respectively According to plant requirements, more than 70% (by weight) of the pulverized coal should be smaller than 75 μmEffects of Mill Performance on Unburnt Carbon in Coalfired Boilers2010年1月1日 Advanced sensors and process control techniques to permit online measurement and subsequent control of the fuel/air flows in individual pipes, the flames of individual burners, and the optimised operation of fuel bunkers and pulverising mills have been regarded as a priority technological development by many leading power generation organisations and government Advanced monitoring and process control technology for coal 2020年1月1日 Coal has an important role in electricity generation worldwide According to data from the World Coal Association, coalfueled power plants currently provide 37% of the global electricity [1]In 2017, China's coalfired power generation accounted for 645% of the total power generation [2]Nearly 176 billion tons coal produced in China is used for generating electricity Wet and dry grinding of coal in a laboratoryscale ball mill:
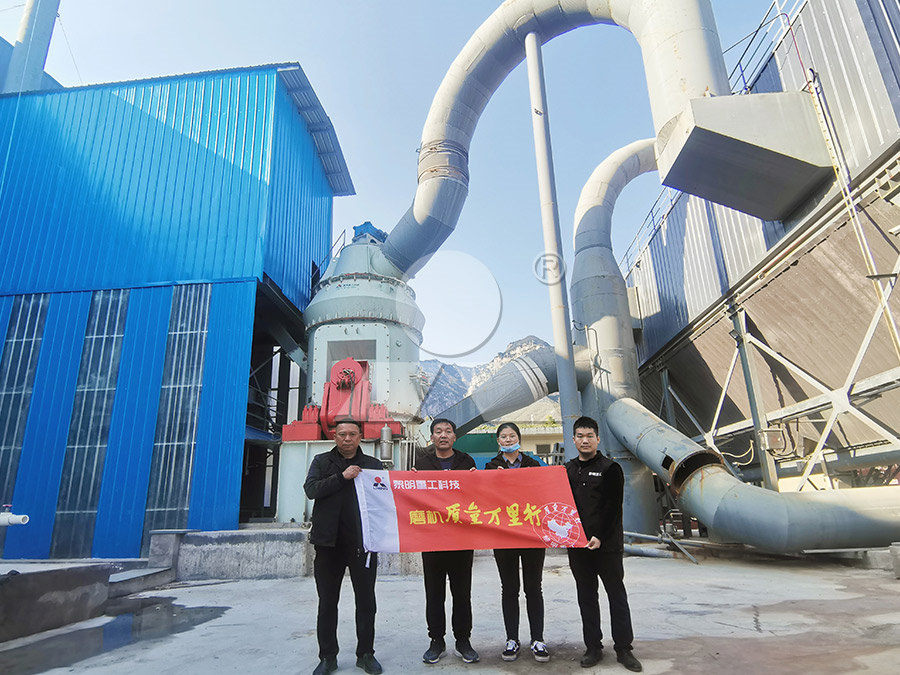
Optimization of operating conditions on ultrafine coal grinding
2022年5月1日 This study investigated ultrafine coal grinding performance of four low to moderatecost grinding media in a laboratory stirred mill Kinetic grinding tests showed that silica beads generated the finest product size with a P 80 of 59 μm from a feed size of 244 μm while having a specific energy (SE) input of 309 kWh/ton Nonetheless, the least energy In PC combustion, the coal is dried and is ground to a specified fineness, with a maximum particle size of 250–300 μm, depending on the reactivity of the coal Coal preparation, which involves feeding, drying, and grinding of the coal, and the pneumatic transport of the pulverized coal to the burners, is fully integrated with the boilerCoal Combustion an overview ScienceDirect Topics• Coal characteristics profoundly influence risk – Lower rank coals are generally more easily ignited inside the coal mill – High volatile matter and highly reactive coals encourage preignition inside the mill – Higher moisture content requires temperature extremes inside the millMill Inerting and Pulverizer/Mill Explosion Mitigation2019年2月28日 This study considered the different grinding periods ie 2, 10, 20, and 40hrs as to produce different particle fineness It was perceived through the laboratory findings that the more the Effects of Grinding Process on the Properties of the Coal Bottom
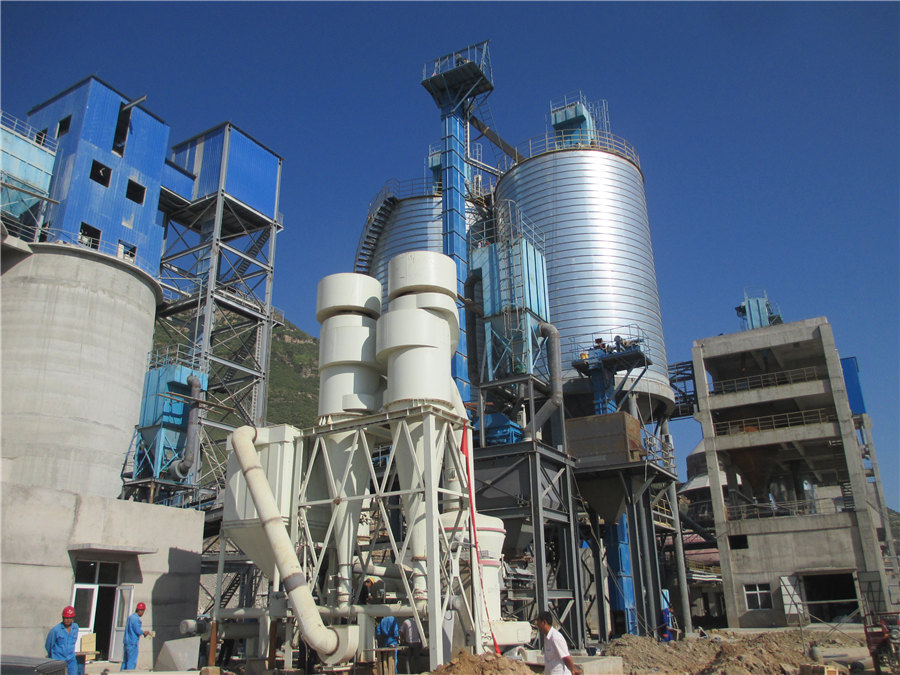
BHARAT HEAVY ELECTRICALS LIMITED
BHEL manufactures a complete range of Bowl Mill (Pulveriser) for all supercritical non supercritical thermal power plant applications Pulverisers are one of the major auxiliaries in a coal fired thermal power station They are used for grinding the raw coal, so that the pulverised product at desired fineness can fed to andUnder moderate grinding fineness, the cumulative yield of the −14 g/cm 3 density class concentrate was higher The crushing behavior of lowash coal and gangue is similar to that of the original samples in the range of 125–45 μm Coal and gangue show a crushing probability similar to that in the range of 125–45 μm size, Impact of grinding media shape on the dissociation continuous operation could be done in our palla the grinding can also be carried out at excess or negative pressure, as well as in an atmosphere of inert, protective or reaction gas Furthermore it is also applicable for cryogenic grinding Feed size 0– 15 mm (max 0– 30 mm) grinding fineness 10 µm (in airclassifier 3 µm)Coal MinErals proCessingSafe operation of coal grinding systems: Raw coal silo protection against fire and explosions Safe operation of coal grinding systems: Raw coal yard management The purchasing process for coal grinding systems needs changes Talk at a virtual seminar, November 2023 Accept the probability that the fire and explosion safety of your coal grinding system is nothing more than a mirageFire and explosion protection of coal grinding systems Where are
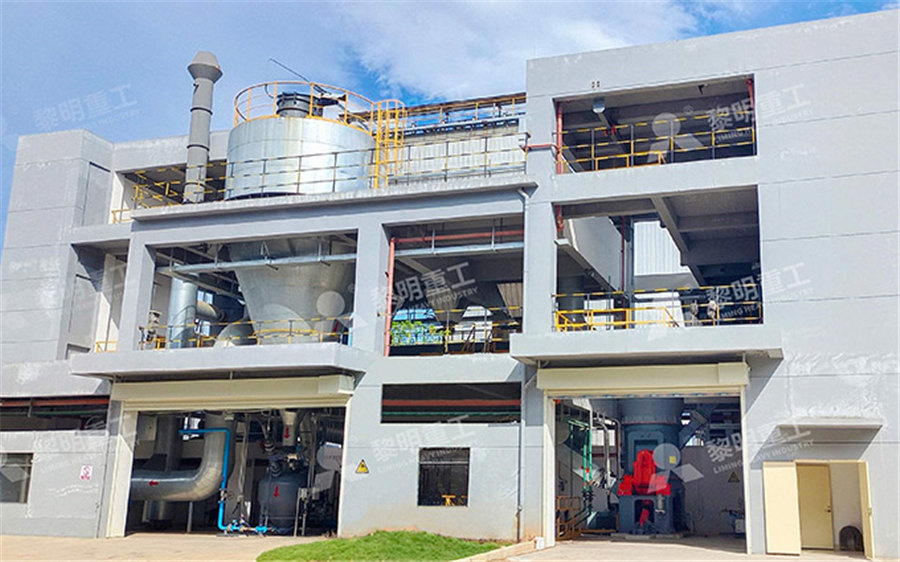
“Blueprint” Your Pulverizer for Improved Performance
Pulverizer throughput is determined by the coal fineness desired for a given coal However, compromising on coal fineness when your pulverizer isn’t up to snuff can increase NO x and cause many furnace problems Your least costly option for increasing pulverizer capacity is to pay careful attention2022年2月24日 Improving the efficiency of the coal grinding process in ball drum mills at thermal power values for coals range from 03 up to 0 The fineness of grinding and specific surface area of Improving the efficiency of the coal grinding process in ball drum 2020年8月12日 As one of the three major forces of coal mills, the grinding force exerts a significant impact on the working process of coal mills and parameters like mill current and outlet temperatureAn investigation of performance characteristics and energetic ensuring consistent fineness across the mill throughput range (see page 8) and have complete electrical control and instrumentation equipment solutions Loesche mills are relatively quiet in operation Key features • Individuallyguided, doubleacting hydraulically loaded grinding rollers improves roller response and control (see below)Loesche Grinding Technology for the Power Industry
.jpg)
Technique to Investigate Pulverizing and Abrasive Performance of Coals
2021年11月4日 Test methods for grindability and abrasion testing: Full scale ring and ball mill, Hardgrove mill [30,31], BCURAroll mill, Rotating electrode ball wear tester [32], Dropweight test machine [28 2022年8月11日 Finished grinding may consume 2550 kWh/t cement, depending on the feed material grindability, additives used, plant design and especially the required cement fineness The grinding process absorbs more energy due to the losses attributable to heat generated during grinding, friction wear, sound noise and vibrationBlended Cement Grinding: Energy Intake and FinenessDownload scientific diagram Product fineness t10 of mixtures for various grinding times from publication: Grinding Behaviors of Components in Heterogeneous Breakage of Coals of Different Ash Product fineness t10 of mixtures for various grinding timesOnline measurement of coal fineness and airfuel ratio inside the coal pipe Michael Schreiber, Michael Haug, Max Starke, The system measures particles in the range from 20 µm up to 4 mm and The direct cost of coal grinding is a function of the wear and tear of PowerGen 2008, Orlando, USA Online measurement of coal fineness

Coping With Coal Quality Impacts on Power Plant Coal
fusion temperature of the coal Coal fineness also plays an important role in being able to utilize coals with elevated iron levels Many slagging problems associated with high sulfurlow fusion coals can be traced back to poor grinding (fineness) of the coal Large pyrite particles escape from the mill and do not completely oxidize in the flame2 Design features of MPS mills for coal grinding Depending on the material to be ground, through put rates of 5200 t/h can be achieved in a fineness range between 1% R0063 mm and 25 % R0090 mm Thus, the MPS coal grinding mill MPS 3070 Reprint from ZKG 3 Gebr PfeifferOnce normal coal flow is applied to the mill, a full mill test should be conducted This should include isokinetic coal sampling and dirty airflow measurements through each fuel line to determine air fuel balance and coal fineness Primary airflow “HotK” calibrations of the primary airflow measuring element should also be conductedThe Storm Approach to Coal Pulverizer OptimizationEffects of Grinding Process on Properties of Coal Bottom Ash 3 Besides that, Alkali silica reaction (ASR) is also a prominent issue in concrete, which could be minimized through introducing Effects of Grinding Process on the Properties of the Coal Bottom
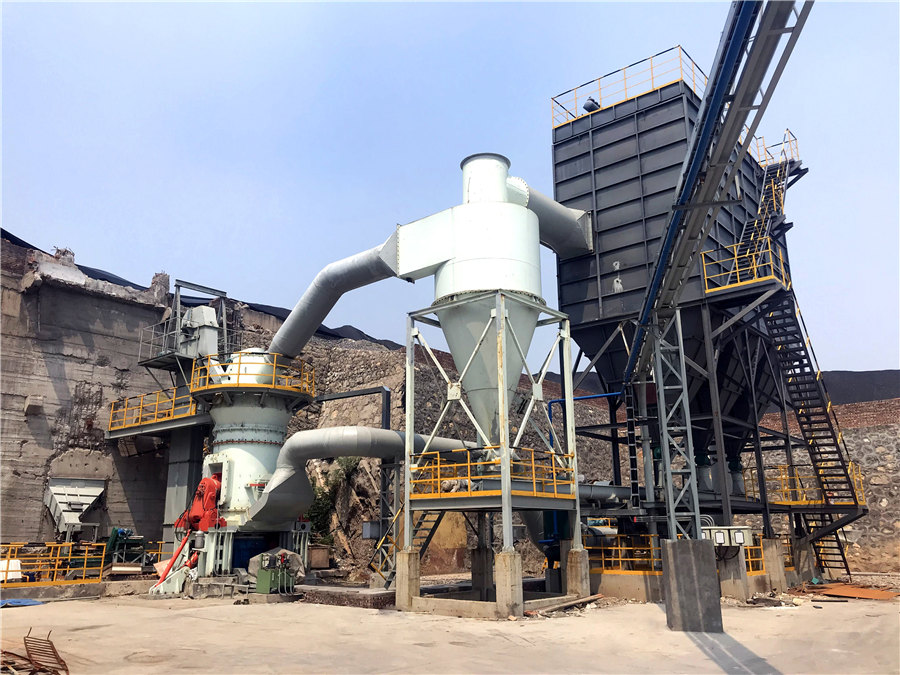
CONTRIBUTION TO DETERMINATION OF COAL GRINDABILITY USING HARDGROVE METHOD
a sample of analysed material (product constant fineness method) or the granularity composition of final products is compared with the same consumption of grinding work (constant method of useful grinding work) Grindability determination methods based on constant fineness of grinding are labour and time demanding2015年8月1日 Mill problems originate mainly due to poor controls or faults occurring within the milling system As discussed by GQ Fan and NW Rees [3], the control of mills remains very simple in most of the power plants due to the fact that the mill system is highly nonlinear with strong coupling among the variables and it is very difficult to measure some important Review of control and fault diagnosis methods applied to coal characteristics to better match the fineness with the furnace requirements Inherently, the rotational effects of the dynamic classifier and better fineness improve coal and air distribu tion to the coal pipes and to the burners Improved coal and air distribution allows operation at lower excess air, which results inPulverizer Fineness and Capacity Enhancements at Danskammer 2016年4月5日 In PFboilers, coal is pulverised in a mill (or pulveriser) before being entrained by primary combustion air to burners, to form a high temperature flame in the furnace of the boiler (1000–1600 °C) [2]The fineness of the coal powder, as well as the uniformity of the coal flow sent to each burner fed by the same mill, are crucial parameters to achieve an effective combustion Online monitoring of coal particle size and flow distribution in coal
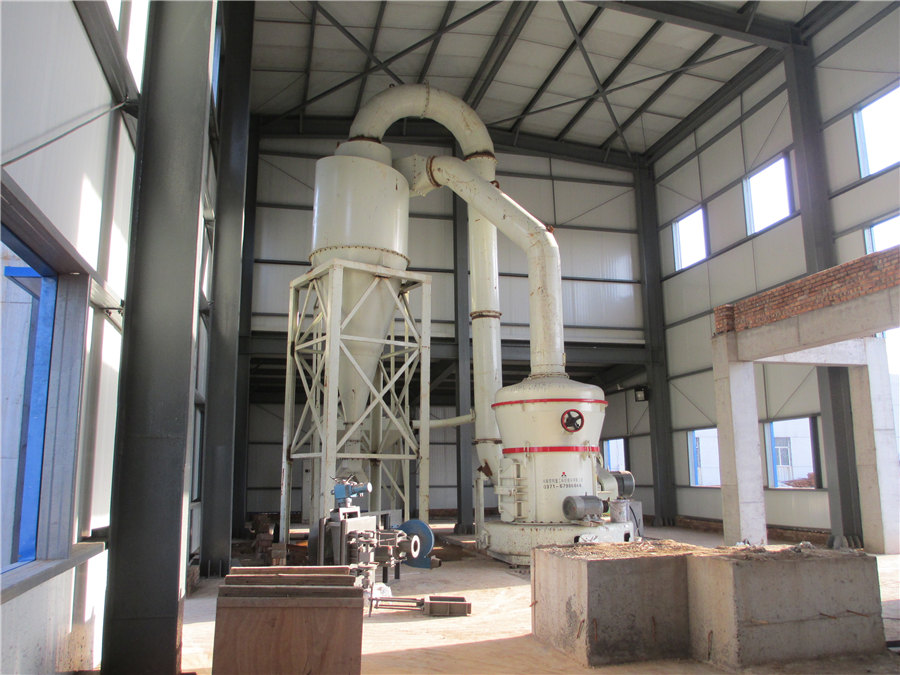
132 Loesche Mills For Solid Fuels Coal Mill E 2016
132 Loesche Mills for Solid Fuels Coal Mill E 2016 Free download as PDF File (pdf), Text File (txt) or read online for free Loesche has been involved in processing solid fuels since 1925 Some key events include delivering their first coal mill in 1927 and introducing hydraulic systems in 1961 Their mills are distinguished by grinding without metal contact, suitability for