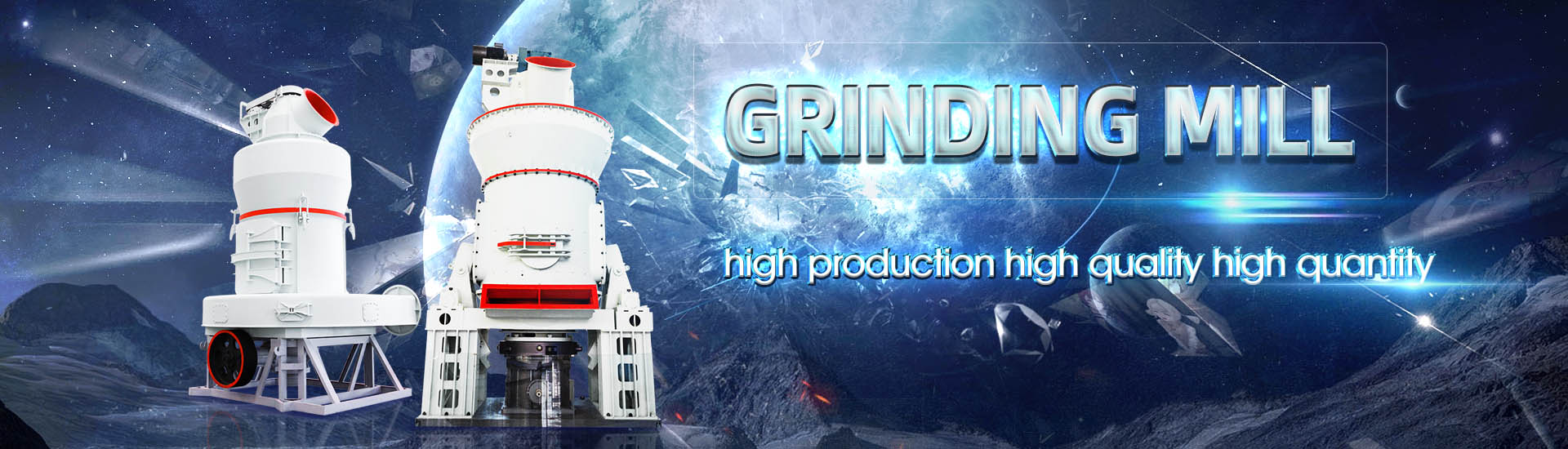
HOME→Square calcite Calculation of ball loading capacity of ball mill for stone ore powder processing equipment
Square calcite Calculation of ball loading capacity of ball mill for stone ore powder processing equipment
.jpg)
Ball Mill Design Calculations How To PDF PDF Scribd
The document provides information on how to calculate ball mill design and sizing parameters It includes a small ball mill capacity and sizing table, as well as details on ball mill design and power calculations The document advertises 2015年10月15日 Learn how to calculate the grinding capacity of your ball mill with 911 Metallurgist This guide provides essential formulas, insights, and tips to optimize your milling process and enhance production efficiencyCalculate Ball Mill Grinding Capacity 911Metallurgist2015年6月19日 Ball Mill Power Calculation Example #1 A wet grinding ball mill in closed circuit is to be fed 100 TPH of a material with a work index of 15 and a size distribution of 80% passing ¼ inch (6350 microns) The required product Ball Mill Design/Power Calculation 911Metallurgist2013年8月3日 In Grinding, selecting (calculate) the correct or optimum ball size that allows for the best and optimum/ideal or target grind size to be achieved Calculate and Select Ball Mill Ball Size for Optimum
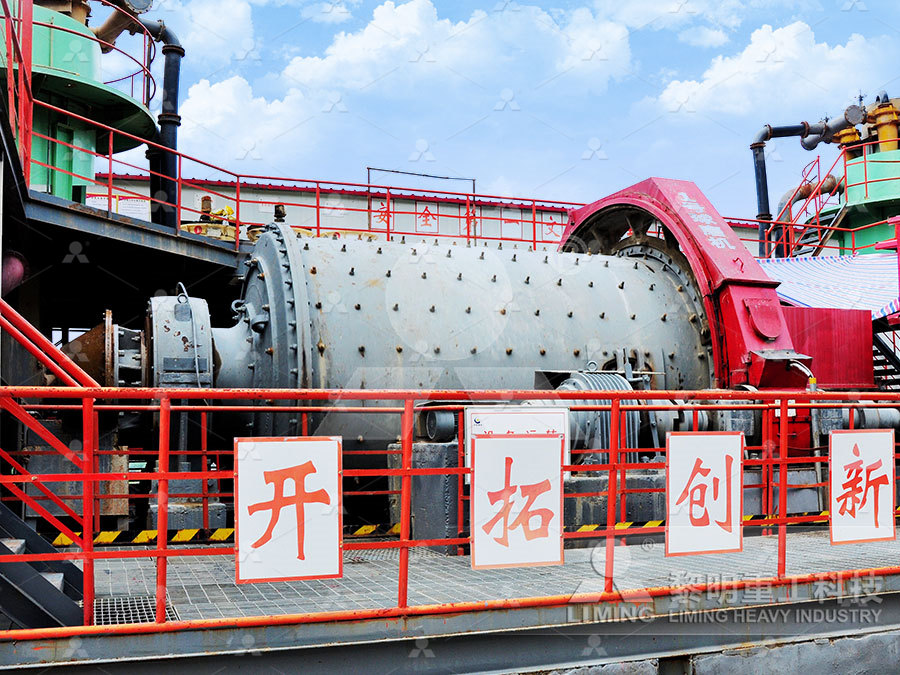
ball mill calculations, grinding media filling degree, ball size, mill
online live calculators for grinding calculations, Ball mill, tube mill, critical speed, Degree of filling balls, Arm of gravity, mill net and gross power2021年1月22日 Herein, an innovative approach for determining the grinding media system of ball mill based on grinding kinetics and linear superposition principle was proposed The Powder TechnologyThe document contains formulas and examples for calculating key performance metrics for ball mills used in cement production It includes formulas to calculate power consumption, production rate, specific power, circulation factor, Ball Mill Calculations PDF Mill (Grinding) ScribdGenerally, the milling of calcite is performed in a conventional tumbling mill or stirred ball mill in appropriate fine/ultrafine size ranges for obtaining the desired characteristics of the final Influences of operating parameters on dry ball mill performance
.jpg)
Ball Mill Calculations PDF PDF Industrial Processes
ballmillcalculationspdf Free download as PDF File (pdf), Text File (txt) or read online for free Scribd is the world's largest social reading and publishing site2022年1月1日 Design and simulation of gear box for stone crushing ball mill Author links open 55 mm and outer diameter of 75 mm against the speed of 343 rpm derived from the stage II speed reducer with static loading capacity of about 61 kN Motor used for the ball mill is taken from the calculations above and from the data Design and simulation of gear box for stone crushing ball mill2017年1月1日 Thus, the performance of an industrial ball mill can be adequately described using the orespecific breakage distribution function together with the systematic variation of the material transport Performance optimization of an industrial ball mill Talk with the Experts at Paul O Abbe® about your process requirements and Size Reduction and Dry Milling Equipment About Section 179; 6303503012 [ Ball Mill Loading Dry Milling Ball Mill Loading (dry Since mill Ball Mill Loading Dry Milling Paul O Abbe
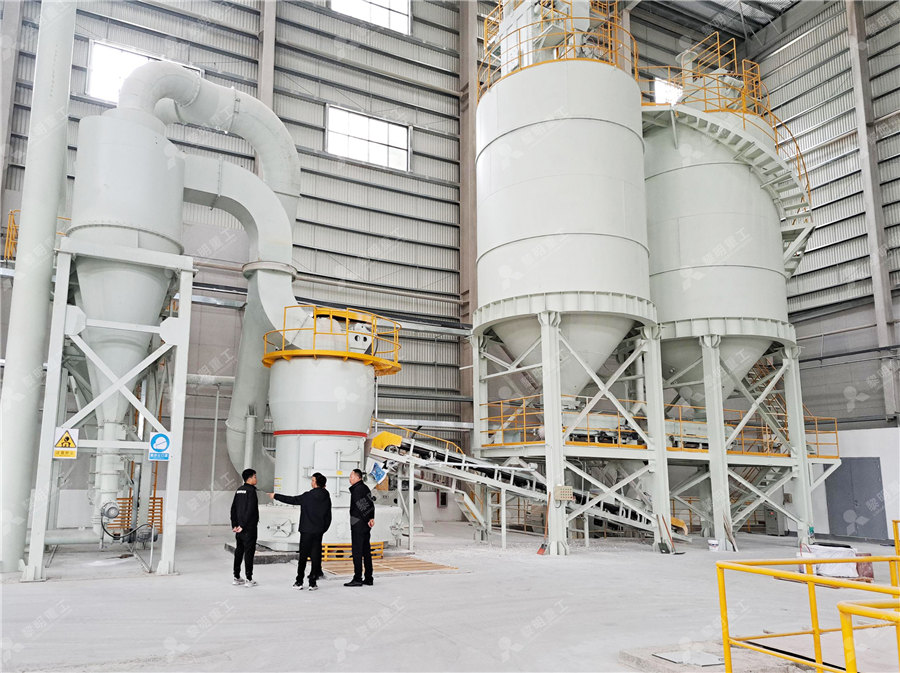
Ball Mill Grinding Process Handbook
Ball Mill Grinding Process Handbook Free download as PDF File (pdf), Text File (txt) or read online for free This document provides guidance on ball mill grinding processes It covers topics such as ball mill design including length to diameter ratios, percent loading, critical speed, and internals evaluation Methods for assessing ball charge, wear rates, and liner management are 2021年1月1日 In this paper, the design method of three chamber ball mill is introduced Comchambered with the design of Φ 35 × 13m threechamber ball mill, the design process of ball mill is described in (PDF) Design of Threechamber Ball Mill ResearchGate2022年1月1日 The effect of ball load composition, by varying the grinding media size distribution (eg alternatively by mixing four groups of 195, 38 mm; 195, 50 mm; 38, 50 mm and 195, 38, 50 mm), on the Effect of grinding media on the milling efficiency of a ball mill2016年12月12日 The basic parameters used in ball mill design (power calculations), rod mill or any tumbling mill sizing are; material to be ground, characteristics, Bond Work Index, bulk density, specific Ball Mill Design/Power Calculation LinkedIn
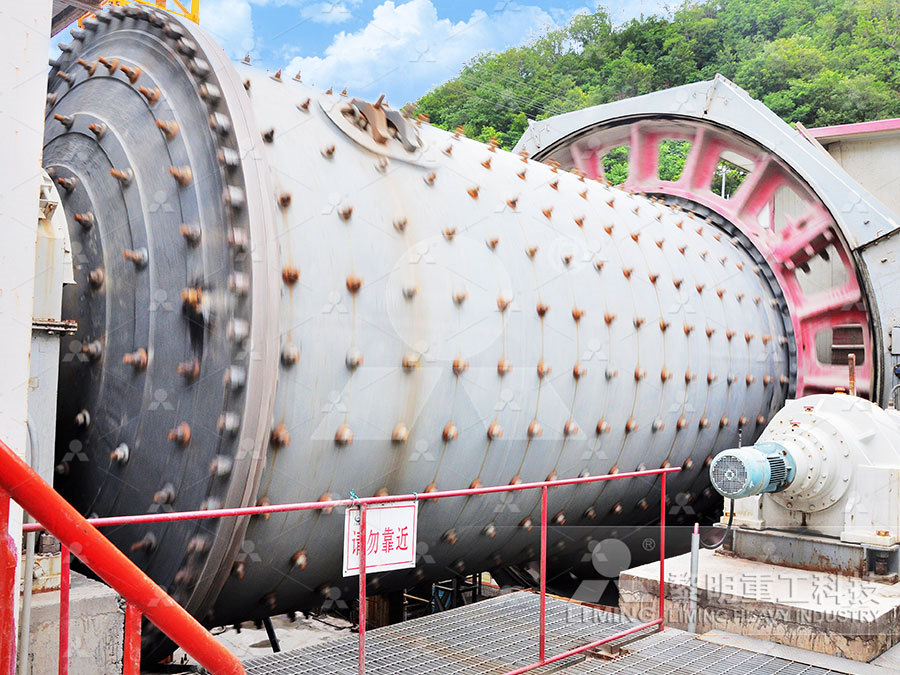
The Operation of a Ball Mill for Calcite Processing
The transmission system transfers rotational motion from an electric motor to the drum, ensuring continuous operation The loading and unloading mechanism allows for the easy addition and removal of calcite ore and grinding media The ball mill’s capacity, or the amount of calcite it can process per batch, depends on its size and design2015年6月19日 While the mill is stopped, the charge volume can be gotten by measuring the diameter inside the liners and the distance from the top of the charge to the top of the mill The % loading or change volume can then be read off the graph below or approximated from the equation and calculation: % Steel Charge Loading in Mill = 113 – 126 H/ DMill Steel Charge Volume Calculation 911MetallurgistBall Mill Degree of Filling Calculation Free download as Excel Spreadsheet (xls), PDF File (pdf), Text File (txt) or read online for free The document contains data on the relationship between charge level (q), degree of filling (h/D), and torque (a) for two different compartments in a mill It also includes calculations for various parameters like bulk density, charge quantity, Ball Mill Degree of Filling Calculation PDF Mill (Grinding2018年4月8日 Unlock the principles of ball mill design with 911 Metallurgist This guide offers detailed calculations and practical tips to ensure your mill is optimized for performance, efficiency, and effective mineral processingBall Mill Design Calculations How to
.jpg)
Calculation of the filling degree the ball mill with grinding media
For the ball mill efficient operation, it is necessary to constantly maintain the required loading level by the grinding media It is very important to correctly and accurately measure the grinding media quantity in the mill Measurements provided in the workedout mill (without crushed material) by measuring the following parameters (measurements provided at three points – mill power 2022年12月15日 It was found that the ball mill consumed 5467 kWh/t energy to reduce the F 80 feed size of 7222 lm to P 80 tests for PGE bearing chromite ore The ball mill of 315 Powder to ball loading Size reduction performance evaluation of HPGR/ball 2023年4月23日 loading ratio on a calcite ore, Cayirli [81] foun d out that as the ball charge increases, the mill’s energy input also in creases and gets to a maximum at 50% ball loading(PDF) Grinding Media in Ball MillsA Review ResearchGate2020年2月26日 Measurement results of two ball mills in a real ceramic manufacturing plant showed that the proposed calculation models could achieve an accuracy of more than 96% for predicting the ball mill Calculation method and its application for energy consumption of ball
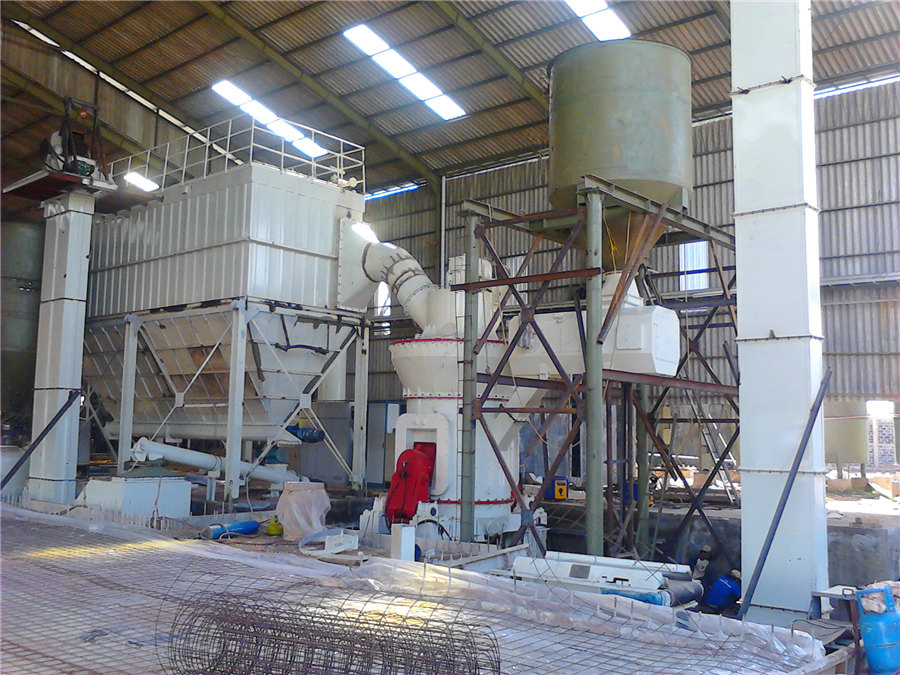
Calculate Top Ball Size of Grinding Media FRED C BOND
2015年9月6日 Although it was developed nearly 50 years ago, Bond‘s method is still useful for calculating necessary mill sizes and power consumption for ball and rod mills This paper discusses the basic development of the Bond method, the determination of the efficiency correction factors based on mill dimensions and feed characteristics, and the application of the Ball loader H65 Ball loader H85; Max lifting height: 6500 mm: 8500 mm: Belt width: 600 mm: 08 m/s: Belt speed: 08 m/s: 08 m/s: Weight: 57t: 65t: Ball loading capacity: 15 tph to 25 tph for a diameter from 10 to 100 mm: 15 tph to 25 tph for a diameter from 10 to 100 mmBall loader Magotteaux2010年3月10日 This project is to design and fabricate the mini ball mill that can grind the solid state of various type of materials into nanopowder The cylindrical jar is used as a mill that would rotate the (PDF) Optimization of mill performance by using online ball 2020年5月1日 The main aim of this study is to improve the processing capacity of the largescale ball mill Taking a Φ549 × 883 m ball mill as the research object, the reason for the low processing capacity of the ball mill was explored via process mineralogy, physicochemical analysis, workshop process investigation, and the power consumption methodEnhancing the capacity of largescale ball mill through process
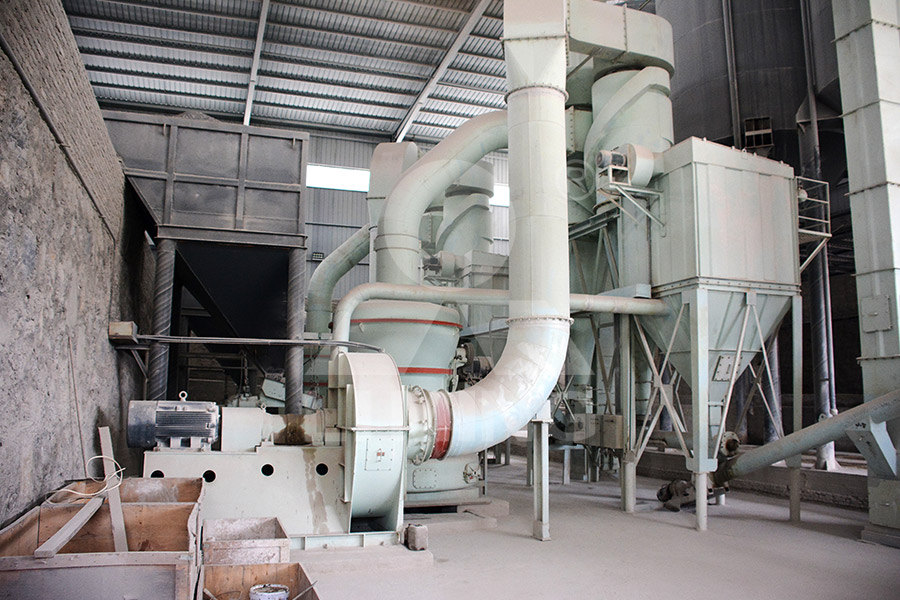
Classifying and Ball Mill Production Line ALPA Powder
Special design to ball mill which will be selected on the basis of hardness, grindability index of material to be ground, feed size, particle size and hourly capacity, customized to the liner Selection of grinding ball and rod can improve grinding efficiency farthest 2023年1月1日 A laboratory scale ball mill was used to conduct the grinding tests for PGE bearing chromite ore The ball mill of 315 mm diameter and 305 mm length as shown in Fig 3 (b) contained steel balls of a total weight of 28124 kg The characteristics of the mill used in the grinding studies and the test conditions are given in Table 1Size reduction performance evaluation of HPGR/ball mill and 2023年5月12日 Figure 2 shows an example of calculation of CM loading displacement in the first chamber of the mill 4 × 135 m, from which it follows that for each cycle CM loading makes a complex movement—along the axis of OУ this trajectory is an elongated ellipse (Fig 2a), the major axis of which coincides with the longitudinal axis of OУ crushing cylinder, and relative to Power Calculation of BallTube Mill Drives in the Construction 2012年12月1日 Optimization of inmill ball loading and slurry solids concentration in grinding of UG2 ores: A statistical experimental design approach(PDF) Optimization of inmill ball loading and slurry solids
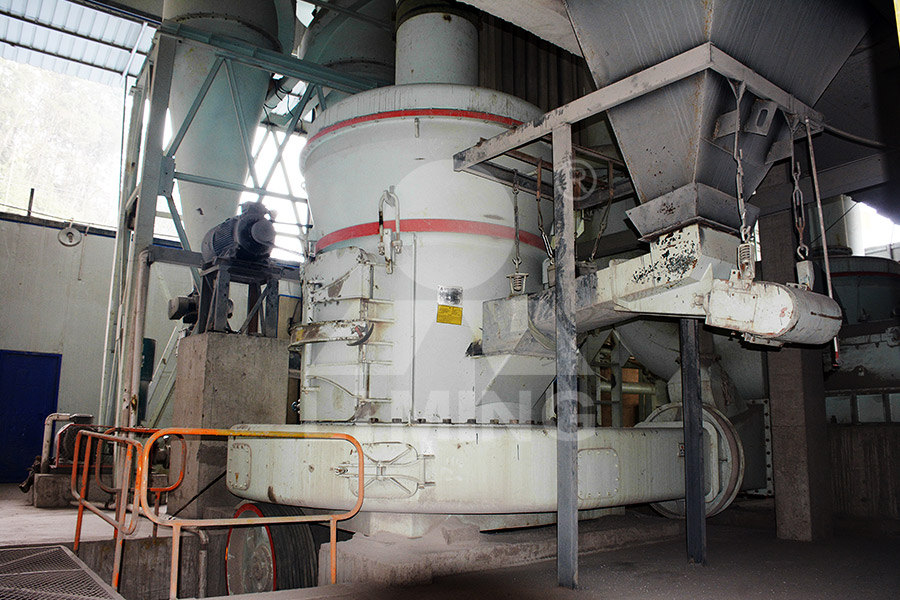
Ball Mill Loading Dry Milling Paul O Abbe
Talk with the Experts at Paul O Abbe® about your process requirements and Size Reduction and Dry Milling Equipment About Section 179; 6303503012 [ Ball Mill Loading Dry Milling Ball Mill Loading (dry Since mill diameter dictates performance and mill length only affects capacity, Slice Mills™ are used to develop or test 2021年1月22日 Where M (kg) represented the quality of loading ore; G (t) was the initial ball loading of the mill; V (m 3) represented the effective volume of ball mill; φ was the spacefilling factor; η (38%) represented the interspace among balls; χ was the material ball ratio; δ o (t/m 3) represented the bulk density of ore; δ b (t/m 3) was the bulk density of steel ballPowder Technology2014年10月27日 An experimental practice on the ultrafine wet grinding of calcite ore in a conventional batch ball mill is reported In this study, the effect of wet grinding conditions on the production of fine Wet Grindability of Calcite to UltraFine Sizes in Conventional Ball Millkey factors affecting mill throughput and grinding efficiency: mill speed, ball loading, and liner lifter face angle (angle between the lifter face in contact with a grinding ball and the lifter base) Its central hypothesis is that face angle drives a ball mill’s grinding efficiency and throughput independently of the type of liner usedA POWER BASED APPROACH FOR THE SELECTION AND COMPARISON OF BALL MILL
.jpg)
A comparison of wear rates of ball mill grinding media
2016年1月1日 The wear of balls used during a grinding process is considered one of the losses that cause an increase in the operating cost allocated to the ball mill [21]2013年8月3日 In Grinding, selecting (calculate) the correct or optimum ball size that allows for the best and optimum/ideal or target grind size to be achieved by your ball mill is an important thing for a Mineral Processing Engineer AKA Metallurgist to do Often, the ball used in ball mills is oversize “just in case” Well, this safety factor can cost you much in recovery and/or mill liner Calculate and Select Ball Mill Ball Size for Optimum Grinding 2023年8月2日 Phosphate ball mill steel ball loading capacity: The steel ball loading capacity of the phosphate ball mill is an important factor that directly affects the grinding effect Generally, the ball loading of the phosphate ball mill is around 40% of the cylinder volume, with a filling rate of about 35% during productionPhosphate ball mill working principle, structure, phosphate ball mill 2022年1月1日 Design and simulation of gear box for stone crushing ball mill Author links open 55 mm and outer diameter of 75 mm against the speed of 343 rpm derived from the stage II speed reducer with static loading capacity of about 61 kN Motor used for the ball mill is taken from the calculations above and from the data Design and simulation of gear box for stone crushing ball mill
.jpg)
Performance optimization of an industrial ball mill
2017年1月1日 Thus, the performance of an industrial ball mill can be adequately described using the orespecific breakage distribution function together with the systematic variation of the material transport Talk with the Experts at Paul O Abbe® about your process requirements and Size Reduction and Dry Milling Equipment About Section 179; 6303503012 [ Ball Mill Loading Dry Milling Ball Mill Loading (dry Since mill Ball Mill Loading Dry Milling Paul O AbbeBall Mill Grinding Process Handbook Free download as PDF File (pdf), Text File (txt) or read online for free This document provides guidance on ball mill grinding processes It covers topics such as ball mill design including length to diameter ratios, percent loading, critical speed, and internals evaluation Methods for assessing ball charge, wear rates, and liner management are Ball Mill Grinding Process Handbook2021年1月1日 In this paper, the design method of three chamber ball mill is introduced Comchambered with the design of Φ 35 × 13m threechamber ball mill, the design process of ball mill is described in (PDF) Design of Threechamber Ball Mill ResearchGate
.jpg)
Effect of grinding media on the milling efficiency of a ball mill
2022年1月1日 The effect of ball load composition, by varying the grinding media size distribution (eg alternatively by mixing four groups of 195, 38 mm; 195, 50 mm; 38, 50 mm and 195, 38, 50 mm), on the 2016年12月12日 The basic parameters used in ball mill design (power calculations), rod mill or any tumbling mill sizing are; material to be ground, characteristics, Bond Work Index, bulk density, specific Ball Mill Design/Power Calculation LinkedInThe transmission system transfers rotational motion from an electric motor to the drum, ensuring continuous operation The loading and unloading mechanism allows for the easy addition and removal of calcite ore and grinding media The ball mill’s capacity, or the amount of calcite it can process per batch, depends on its size and designThe Operation of a Ball Mill for Calcite Processing2015年6月19日 While the mill is stopped, the charge volume can be gotten by measuring the diameter inside the liners and the distance from the top of the charge to the top of the mill The % loading or change volume can then be read off the graph below or approximated from the equation and calculation: % Steel Charge Loading in Mill = 113 – 126 H/ DMill Steel Charge Volume Calculation 911Metallurgist
.jpg)
Ball Mill Degree of Filling Calculation PDF Mill (Grinding
Ball Mill Degree of Filling Calculation Free download as Excel Spreadsheet (xls), PDF File (pdf), Text File (txt) or read online for free The document contains data on the relationship between charge level (q), degree of filling (h/D), and torque (a) for two different compartments in a mill It also includes calculations for various parameters like bulk density, charge quantity,