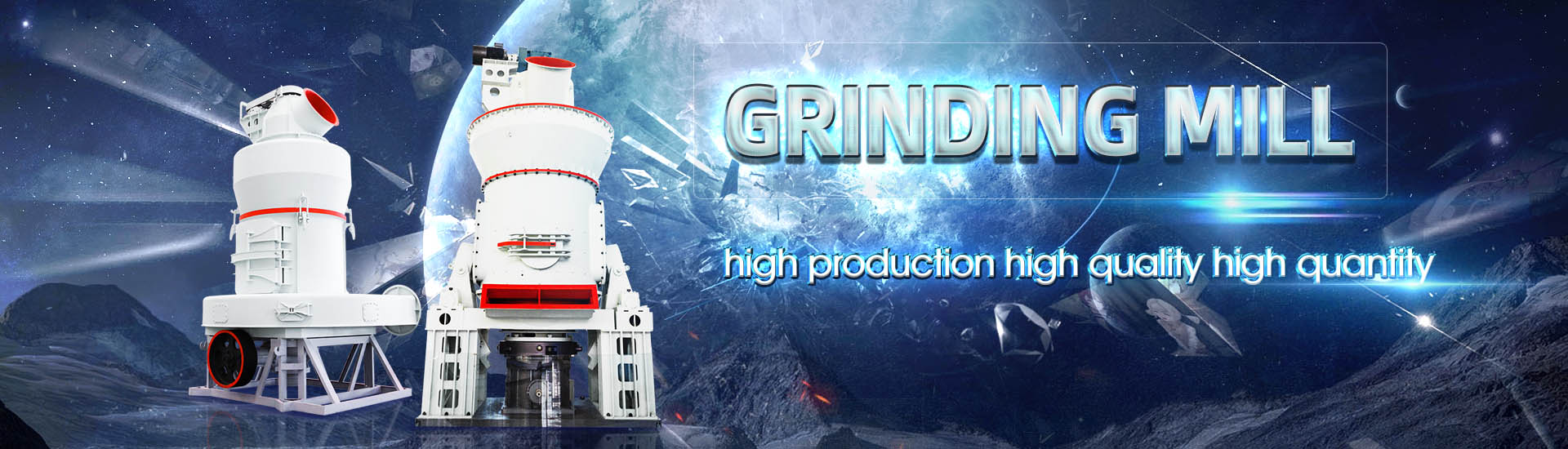
Consumption of steel balls for coal mill in power plant
.jpg)
Coal mill pulverizer in thermal power plants PPT
2012年11月17日 The document discusses coal mill/pulverizers used in thermal power plants It describes how pulverized coal is dried, ground, circulated, and classified within the mill to produce a fine powder that is then transported to 2020年6月29日 The key types of coal pulverizers tube/ball mills, vertical spindle mills, and impact mills are outlined Performance indicators for mills include meeting load, achieving fineness, minimizing current/rejects, and classifications and working of mills in a power plant2007年9月10日 A Brazilian power plant consumes mineral coal with high ash contents to feed four turbines to generate 450 MW Four ball mills, 42 m in diameter, are fed with crushed coal Maximizing wear resistance of balls for grinding of coal2013年8月1日 Consumption of grinding media in mills is an economically important problem Current understanding of factors influencing wear loss of steel balls in mills is reviewed Consumption of steel grinding media in mills – A review
.jpg)
Optimization and transformation of 300MV units steel ball coal
2019年11月7日 Comprehensive treatment,we should have a test on the 300 MV unit steel ball coal and safe operation 1 Introduction consumes a large amount of metal, and the initial In order to determine the basis for charging steel balls for the ball mills in thermal power plants during the normal operation,ensure the relative stability of pulverizing capacity of ball mills, 火电厂磨煤机钢球装载量与电机电流的关系分析Pulverized Coal System of Steel Ball Mill for 300MW Unit In modern pulverized coal boilers, pulverizing system has become an indispensable part of theOptimization and transformation of 300MV units steel ball coal 2010年4月1日 In this paper, we preliminarily focus on the optimization operation for ball mill pulverizing system in power plant The nonlinear model of electric consumption is built based A study on a new algorithm to optimize ball mill system based on
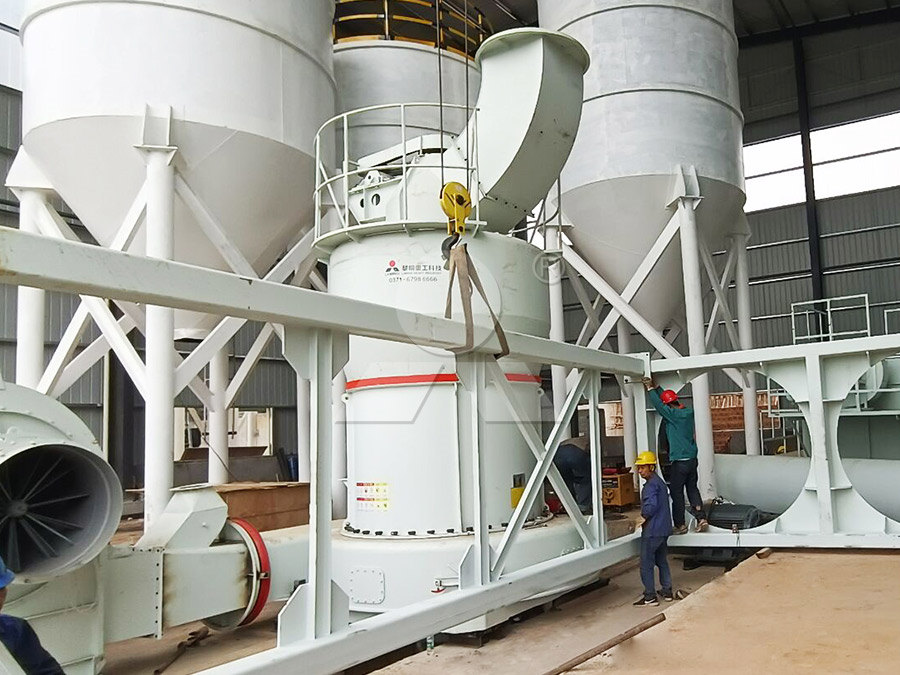
Improving the efficiency of the coal grinding process in ball drum
2022年2月24日 The study reveals that the lowest specific energy consumption is achieved when the relative rotational speed of the mill is between 081 and 087; the weighted average 2019年10月1日 Cause Analysis of Congested Pulverized Coal Dropping of Pulverized Coal Feeder in Storage Pulverizing System and Solutions; Quantitative characterization of Optimization and transformation of 300MV units steel ball coal IOP Publishing % %% )Optimization and transformation of 300MV units steel ball coal mill that coal based generation/consumption as well as coal despatch varies during the course of the year Further, Genco/IPP of which any power plant maintains average coal stock during the preceding month in the range of 65% to 85% of the mandatory coal stock prescribed in the norms of that month; ANDREVISED COAL STOCKING NORMS FOR COAL BASED THERMAL POWER
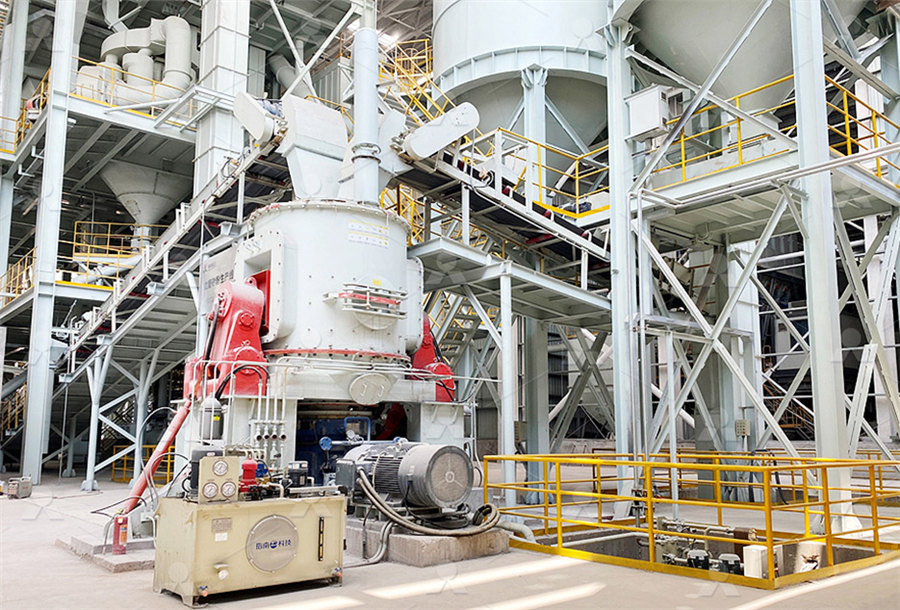
A Comparison of Three Types of Coal Pulverizers Babcock Power
The Ball Tube Mill (BTM) is a cylindrical lowspeed grinding mill It consists of a steel barrel, lined with cast abrasionresistant liners and partially filled with hardened steel balls Coal and preheated primary air enter one or both ends of the mill from a crusher/dryer or feeder As the mill rotates, the balls cascade and2014年10月1日 To investigate the characteristics of coal particle collisions on steel surface, and the power consumption of the mill will increase to a limit that the mill cannot handle Distribution of the coal flow in the millduct system of the As Pontes Power Plant using CFD modelling Fuel Processing Technology, 106 (2013), Numerical and experimental analysis of pulverized coal mill Total power consumption for grinding circuit as a whole is also less by about 30% compared to closed circuit ball mill in spite of higher fan power Feed size can be as large as 75 to 100 mm Feed size can be as large as 5% of roller diameterCoal Grinding Cement Plant OptimizationSteel is produced via two main routes: the blast furnacebasic oxygen furnace (BFBOF) route and electric arc furnace (EAF) route Variations and combinations of production routes also exist The BFBOF route produces steel using raw materials such as iron ore, coal, limestone and steel scrap About 75% of steel is produced using the BFBOF routeFact sheet Energy use in the steel industry

A Study on 500 MW Coal Fired Boiler Unit’s Bowl Mill
1inch steel balls A weighted upper race is placed on the coal sample and the steel balls and the ball mill is made to rotate for 50 revolutions The crushed coal samples are then removed and sieved The quantity of the crushed coal passing through 200 mesh (75 µm) is weighed and the HGI is derived from the empirical equation: HGI = 693W +13Coal ball mill is mainly used in coal power plant or mineral calcining system Skip to content Home; Product Center; Ball Mill Parts Menu Toggle Ball Mill Shell; Ball Mill and the grinding chamber is rotated to bring up the grinding media steel balls and throw them off After being ground for a period of time, the coal is turned into a Coal Ball Mill Grinding for Different Kinds of Pulverized Coal2022年2月8日 High wear rates were observed when using forged highcarbon steel ballsA pilotplant ball mill, with a 001m3 chamber, was used to perform wear tests, comparing the original ball material and Study of steel ball recharge and consumption in a wet cement Bowl Mill has long been recognized as the most advantageous design of the coal pulverisers and include low initial cost, low maintenance cost, removal of tramp iron, low power consumption, easy maintenance, wide range output, quiet operation The basic features of Bowl Mill (Puveriser) supplied by BHEL are:BHARAT HEAVY ELECTRICALS LIMITED
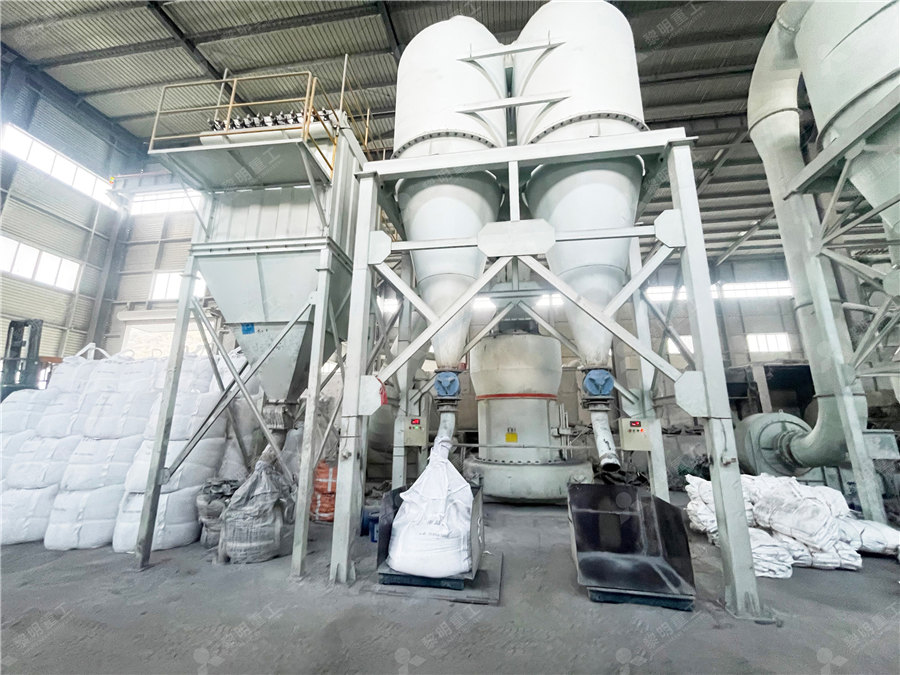
Double inlet outlet ball mill Geckointech
Coal feeder sends coal into drop pipe Coal falls down to screw conveyor and gets pushed into cylinder of ball mill Inside, steel balls will grind coal into fine particles Hot primary air enters cylinder through hollow pipe at two ends of Its coal mills are designed to minimize emissions and meet strict environmental regulations Efficient grinding processes reduce coal consumption and prevent coal wastage, contributing to a more sustainable power generation process Market Impact: Bellian Machinery's coal mills have made a significant impact in the thermal power industryCoal Mill in Thermal Power Plant: Enhancing Efficiency and High chromium steel balls for ball mill is widely used in cement plant, power plant, metallurgy industry, mining industry, glass work, etc High chromium steel balls are featured with high hardness, low abrasion loss, good toughness, low Steel balls for ball mill Geckointech2022年2月24日 The study reveals that the lowest specific energy consumption is achieved when the relative rotational speed of the mill is between 081 and 087; the weighted average diameter of the balls ranges Improving the efficiency of the coal grinding process in ball drum
.jpg)
Calculation method and its application for energy consumption
2020年2月26日 Calculation method and its application for energy consumption of ball mills in ceramic industry based on power feature deployment2022年12月30日 The coal is feed into the coal mill through a central inlet pipe, where it is pulverized by a series of large balls made of steel, which are mounted on a rotating horizontal shaftHow does a coal mill work? LinkedInThe energy consumption in steel plants is however, gradually reducing because of technological upgradation, utilisation of waste heats, use of better quality inputs, etc The Government/ Ministry of Steel, through various schemes and regulations, is facilitating reduction in energy consumption and emission of environment pollution in steel plantsEnergy Environment Management in Steel SectorCompared with the vertical roller mill, the advantages of airswept ball mill are strong adaptability to raw coal quality, simple operation and low investment cost; the disadvantages are high power consumption and high noise Vertical Roller Mill Vertical Roller Coal Mill Vertical roller mill is a popular pulverized coal mill in recent yearsCoal Mill in Cement Plant Vertical Roller Mill AirSwept Ball Mill
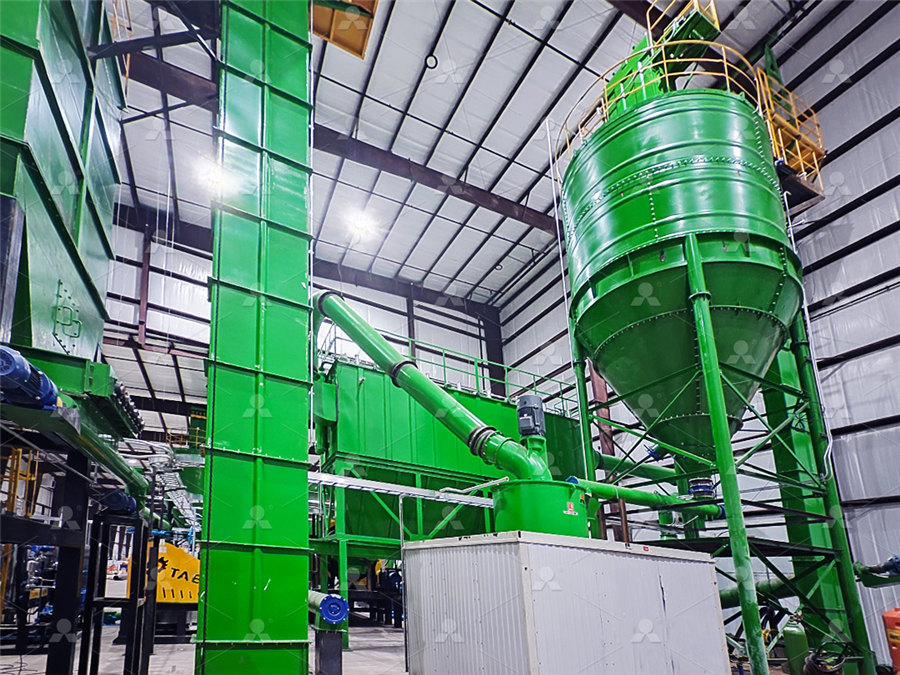
Coal Pulverizer – Power Plant Pall Corporation
The four most common coal pulverizers types are: BallTube Mills This type of mill consists of a rotating tube filled with cast alloy balls Coal is introduced through two hollow trunnions on each side of the tube As the tube rotates, the balls tumble onto the coal, crushing and pulverizing it Process 63 (2001) 79–114 97 Fig 7 Ža Dependence of the specific power consumption vs mill speed curve on the lifter shape for face angles between 858 and 2258 The fill level here is 40% Žb Change in specific power consumption with face lifter angle throughout the lifter life cycle for the rotation rates N s 70%, 80%, 90% and 100%Charge behaviour and power consumption in ball mills: 2002年4月1日 Abstract The pulverized coal systems with tube mills are widely used in coal fired power plants As there are many controlled variables and disturbances in this system, and startup and shutdown of the system is frequent and the dynamic characteristic of the controlled plant is also extraordinary, the automatic control system for this kind of pulverized coal system is not A study of control strategy for the bin system with tube mill in the Investigation on Classification Efficiency for CoalFired Power Plant 1543 Journal of Engineering Science and Technology June 2020, Vol 15(3) 1 the major percentage of coal consumption was for power generation purposes Recently, and hub coal mill with a power generation capacity of 700 MW(e) using Pipit (061)INVESTIGATION ON CLASSIFICATION EFFICIENCY FOR COALFIRED POWER PLANT
.jpg)
A REVIEW ON ENERGY EFFICIENCY OF STEEL
2020年2月24日 The Indian iron and steel sector's energy consumption of 66 GCal per of coal with 1821% ash and 22C6% volatile matter as against 320 NmJ per Integration with Captive Power Plant Figure 3 Changes in coal power plants and status of new coal power projects by halfyear period The perceived need for more coalfired capacity is also leading to a slowdown or even reversal of plant retirements For example, 2 x 300MW units of Huaneng Liancheng power plant and 2 X 330MW units of Datang Gansu Gangu power plant had been shut Chinaʼs power and steel industries continue to invest in coal 2013年8月1日 Furthermore, it is worth mentioning that the application of ceramic balls in tumbling mill is exceedingly economic, given that the power consumption of the tumbling mill has been reduced by 385% Consumption of steel grinding media in mills – A review2017年11月15日 The work is based on tests of pulverisers of a 650 t/h pulverized fuel boiler (OP 650) in a Polish power plant On the basis of these studies, relationships were derived between the fineness of the produced pulverized fuel and operating parameters, the efficiency of the boiler and parameters of the milling system, eg, energy consumption of the mill and its fanOptimisation of coal fineness in pulverisedfuel boilers
.jpg)
Pulveriser Mill Performance Analysis Optimisation in Super
in the mining or coal processing operations Fig3 Mill fuel piping connections to furnace II COAL MILL SPECIFICATIONS PERFORMANCE ANALYSIS Typical Coal Pulveriser Mill Details in 660 MW SuperCritical [3] Unit is as given in table Table No 1 Table1 Coal mill Type Bowl Type Mediumspeed Coal mill Number of Mills 6set/ boiler2015年5月23日 Fig 1 Types of fuel energies used in steel plant Other form of energy used in steel plants After fuel energy, electricity constitute the next highest consumption of energy in the integrated steel plant The electricity may be produced in captive power plant, or may be produced from waste energy or may be purchased from public utility companiesTypes of Energy used in a Steel Plants and Energy Conservation2014年7月1日 Pulverizing system is the main energyconsumption equipment in coalfired power plant, so it is of great significance to study energysaving and optimization of pulverizing systemEnergy Consumption Analysis of Pulverizing System in CoalFired Power Plant2015年11月1日 Several possible objective functions can be – minimizing the power consumption, maximizing the coal feed rate, achieving the desired fineness, minimizing the costs, minimizing the startup time, etc Intelligent expert system (KBOSS) for power plant coal mill supervision and control Control Eng Pract, 5 (1997), pp 101108A unified thermomechanical model for coal mill operation
.jpg)
Optimization and transformation of 300MV units steel ball coal mill
IOP Publishing % %% )that coal based generation/consumption as well as coal despatch varies during the course of the year Further, Genco/IPP of which any power plant maintains average coal stock during the preceding month in the range of 65% to 85% of the mandatory coal stock prescribed in the norms of that month; ANDREVISED COAL STOCKING NORMS FOR COAL BASED THERMAL POWER The Ball Tube Mill (BTM) is a cylindrical lowspeed grinding mill It consists of a steel barrel, lined with cast abrasionresistant liners and partially filled with hardened steel balls Coal and preheated primary air enter one or both ends of the mill from a crusher/dryer or feeder As the mill rotates, the balls cascade andA Comparison of Three Types of Coal Pulverizers Babcock Power2014年10月1日 To investigate the characteristics of coal particle collisions on steel surface, and the power consumption of the mill will increase to a limit that the mill cannot handle Distribution of the coal flow in the millduct system of the As Pontes Power Plant using CFD modelling Fuel Processing Technology, 106 (2013), Numerical and experimental analysis of pulverized coal mill
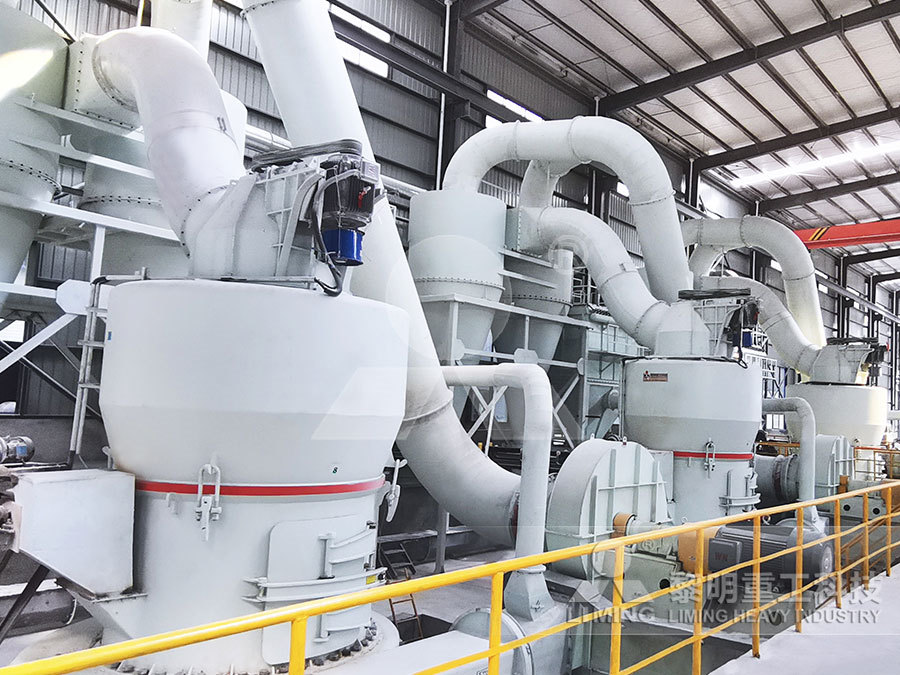
Coal Grinding Cement Plant Optimization
Total power consumption for grinding circuit as a whole is also less by about 30% compared to closed circuit ball mill in spite of higher fan power Feed size can be as large as 75 to 100 mm Feed size can be as large as 5% of roller diameterSteel is produced via two main routes: the blast furnacebasic oxygen furnace (BFBOF) route and electric arc furnace (EAF) route Variations and combinations of production routes also exist The BFBOF route produces steel using raw materials such as iron ore, coal, limestone and steel scrap About 75% of steel is produced using the BFBOF routeFact sheet Energy use in the steel industry1inch steel balls A weighted upper race is placed on the coal sample and the steel balls and the ball mill is made to rotate for 50 revolutions The crushed coal samples are then removed and sieved The quantity of the crushed coal passing through 200 mesh (75 µm) is weighed and the HGI is derived from the empirical equation: HGI = 693W +13A Study on 500 MW Coal Fired Boiler Unit’s Bowl Mill Coal ball mill is mainly used in coal power plant or mineral calcining system Skip to content Home; Product Center; Ball Mill Parts Menu Toggle Ball Mill Shell; Ball Mill and the grinding chamber is rotated to bring up the grinding media steel balls and throw them off After being ground for a period of time, the coal is turned into a Coal Ball Mill Grinding for Different Kinds of Pulverized Coal
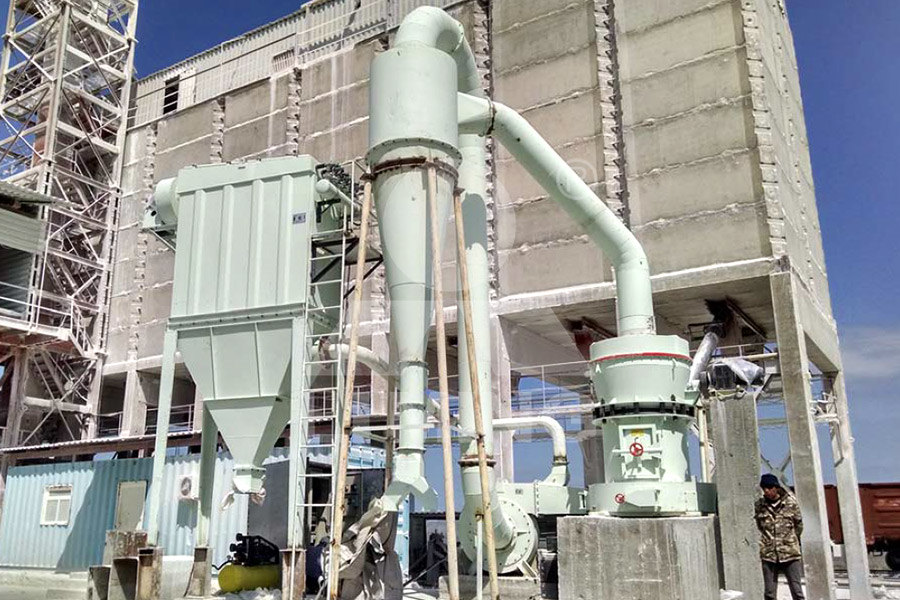
Study of steel ball recharge and consumption in a wet cement
2022年2月8日 High wear rates were observed when using forged highcarbon steel ballsA pilotplant ball mill, with a 001m3 chamber, was used to perform wear tests, comparing the original ball material and Bowl Mill has long been recognized as the most advantageous design of the coal pulverisers and include low initial cost, low maintenance cost, removal of tramp iron, low power consumption, easy maintenance, wide range output, quiet operation The basic features of Bowl Mill (Puveriser) supplied by BHEL are:BHARAT HEAVY ELECTRICALS LIMITED