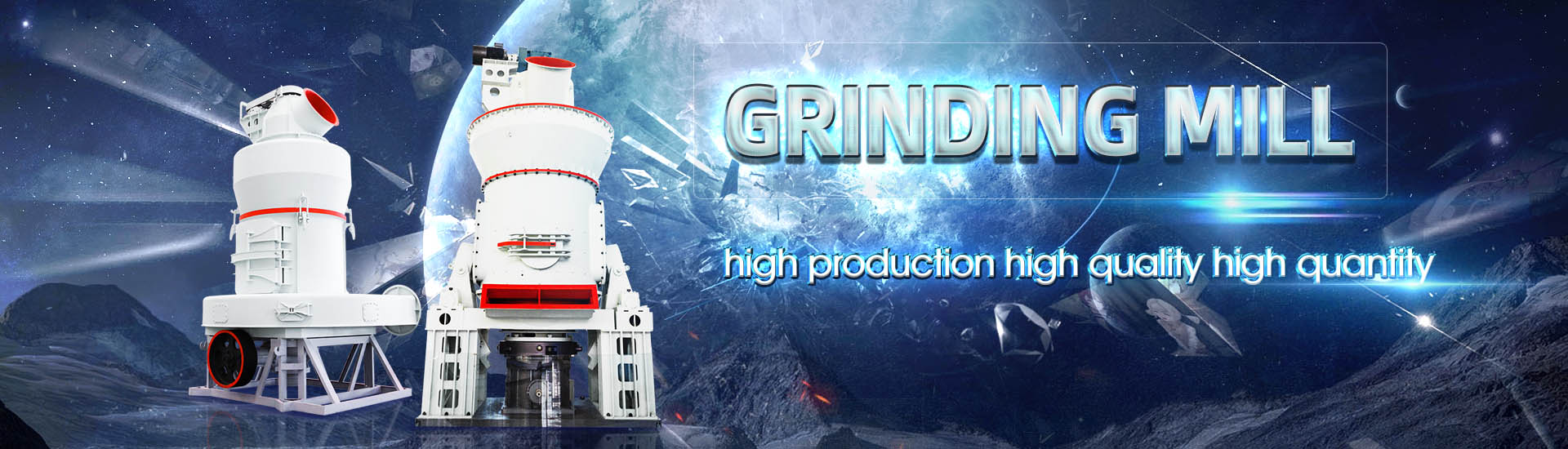
HOME→New steel micro powder composition New steel micro powder composition New steel micro powder composition
New steel micro powder composition New steel micro powder composition New steel micro powder composition
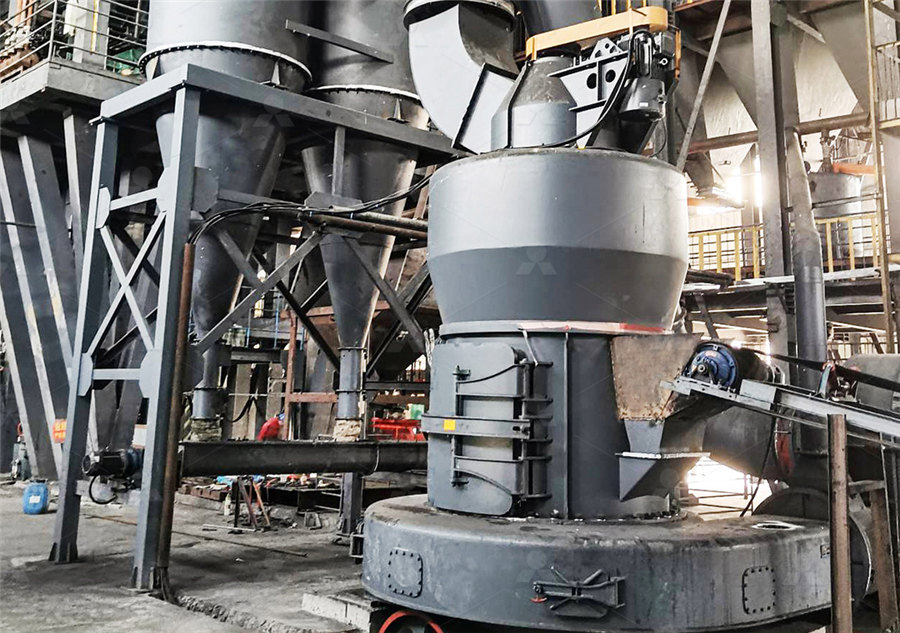
Powder metallurgy as a perfect technique for preparation of
2023年4月29日 In this essay, we will discuss the innovative and research value of powder metallurgy as a perfect technique for the preparation of Cu–TiO 2 composite by identifying their microstructure and2013年1月1日 A new method of developing lean powder metallurgy steels is proposed The microstructure of the steel is tailored by combining two different prealloyed steel grades(PDF) Tailoring the microstructure from the base powder: A new 2014年11月1日 Micropowder injection molding (μPIM) is a new technology that has potential in the mass production of microcomponents A bulk material of nanoparticles possesses The effect of nanosized stainless steel powder addition on 2024年4月11日 Here, we report a powdersize driven melt pool engineering approach, demonstrating facile and largescale control in the grain morphology by triggering a Powdersize driven facile microstructure control in powderfusion
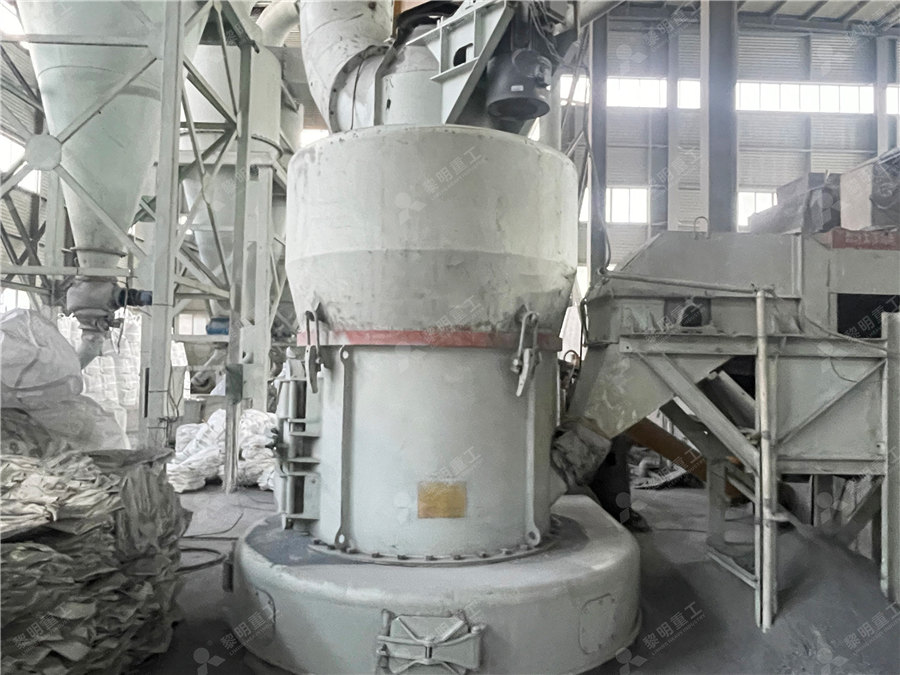
Development of a New Tooling Steel (L40) for Laser Powder Bed
2021年5月18日 In this study, the influence of particle size distribution and atomization process on the printability of a new tooling steel tailored for AM (L40), have been observed on a EOS 2021年4月15日 In the path of filling the gap in research, in this work, the production of a new type steel in the desired composition was manufactured by adding different proportions of Investigation of microstructure, mechanical and machinability 2023年3月27日 In the current study, nanopowder is blended to the conventionally used micrometresized wateratomised steel powder to evaluate its impact on sinteringFull article: Influence of iron nanopowder addition on the 2021年7月30日 Powder metallurgical processing techniques used to promote the formation of refined, homogeneous and contaminantfree structures, favouring improvements in ductility (PDF) News Trends in Powder Metallurgy: Microstructures,
.jpg)
Laser powder bed fusion of NiTiFe shape memory alloy via pre
2024年2月3日 In this work, the lowcost ternary NiTiFe shape memory alloy is fabricated by laser powder bed fusion (LPBF) technique via mechanically mixed prealloy NiTi powder and 2021年7月15日 The development of new materials for Additive Manufacturing (AM), especially for Laser Powder Bed Fusion (LPBF), is essential to reveal the full potential of AMprocessed Precise control of microstructure and mechanical properties of 2006年4月1日 Fig 2 shows green micro injection molded components made with conventional 316 L stainless steel feedstock The limitations of using conventional feedstock (mean particle size: 8 μm) are clearly visible as the components show defects and poor shape retention (rounded edges) For optimum performance, for example in terms of flow behavior or Micro powder injection moulding ScienceDirect2010年4月30日 The 316L stainless steel powder was uniformly distributed within the binder The 316L stainless steel micromixer was well replicated by micro powder injection molding The molded, debound and sintered micromixers had good shape retention, without visible defects, such as warpage, incomplete filling, crack, etcReplication and characterization of 316L stainless steel micro
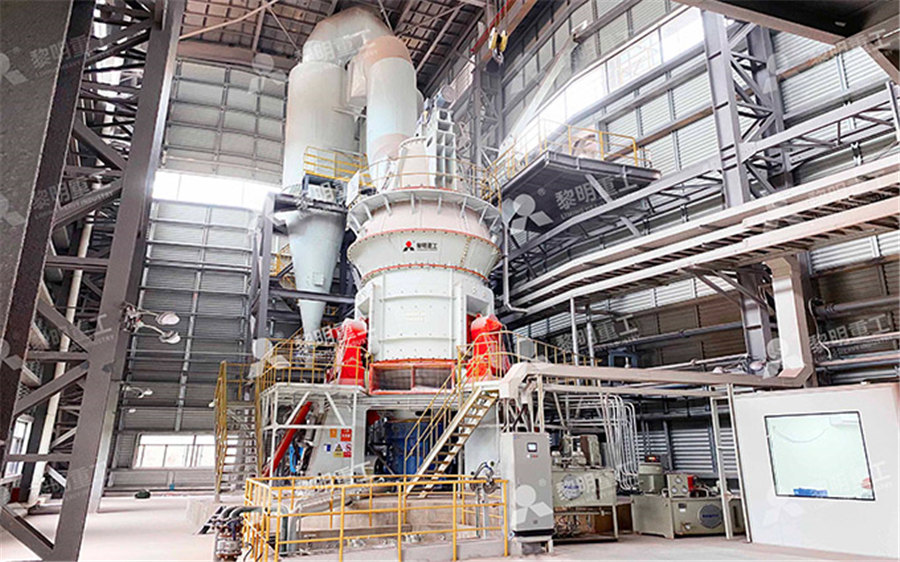
Process Parameters Used in Macro/Micro Powder Injection Molding
2020年6月3日 As can be seen in Table 1, stainless steel 316 L, 174PH, tungsten, and its alloys, titanium, and its alloys, nickelbased superalloys, yttriastabilized zirconia, alumina, and zirconiatoughened alumina have been mostly used by the researchers as materialsFrom Table 1, it can be said that the microsized powder particles received higher attention in the past 15 years 2008年10月15日 This paper presents an approach to fabricate 316L stainless steel micro parts with complex shapes using soft lithographical and powder metallurgical techniques The process includes production of high quality deep micro SU8 master moulds and their negative replicas in polydimethylsiloxane (PDMS)Fabrication of 316L stainless steel micro parts by softlithography 2016年12月1日 This might mean that the new powder Scorialit SPH C176/AlS9 used for the cast of C45 steel Ø170 mm billets, featuring very good quality of billets surfaces and muchOptimization of Chemical Composition of the Mould Powder Download Table Stainless steel(SS316L) powder characteristic from publication: Water Atomised Stainless Steel Powder for Micro Metal Injection Molding: Optimization of Rheological Properties Stainless steel (SS316L) powder characteristic Download Table
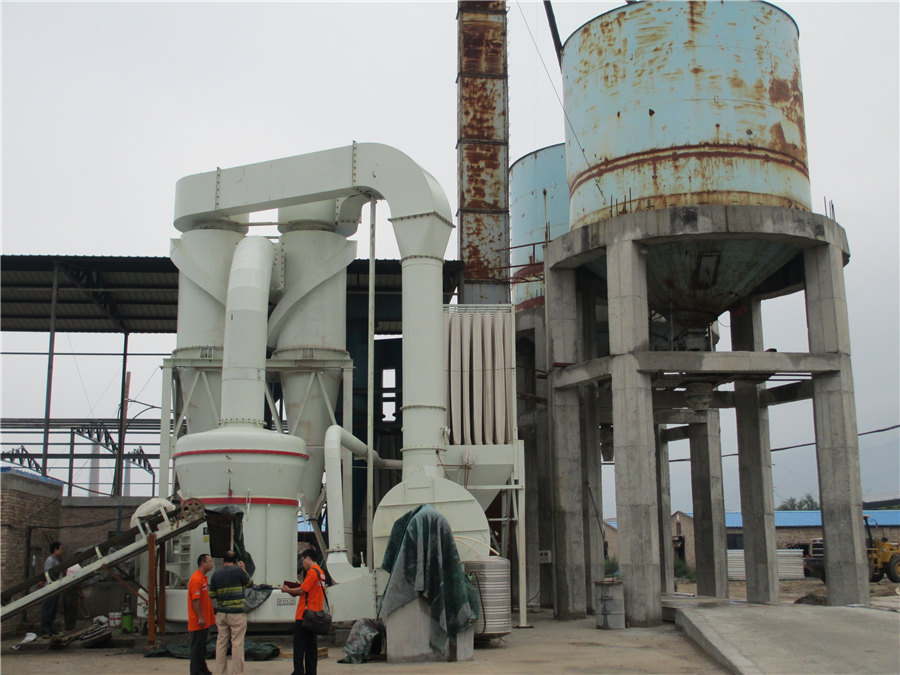
Triplex steel powder design to avoid hot cracking in laserpowder
2024年4月25日 However, a recent study on a high manganese triplex steel composition has revealed the occurrence of both hot cracking and micro segregation during rapid solidification in LPBF, highlighting potential processability issues of this family of high alloy steels2019年1月1日 Request PDF Laser metal deposition as repair technology for 316L stainless steel: Influence of feeding powder compositions on microstructure and mechanical properties Laser metal deposition Laser metal deposition as repair technology for 316L stainless steel Download Table Stainless steel powder chemical composition from publication: Water Atomised Stainless Steel Powder for Micro Metal Injection Molding: Optimization of Rheological Properties Stainless steel powder chemical composition Download Table2022年7月19日 Micro laser powder bed fusion (μLPBF) has been developed with the increasing demand of the high resolution for the lightweight structure [[1], [2], [3]]The major differences between μLPBF and conventional laser powder bed fusion (cLPBF) are the laser spot size, powder size, and the layer thicknessMicro laser powder bed fusion of stainless steel 316L: Cellular
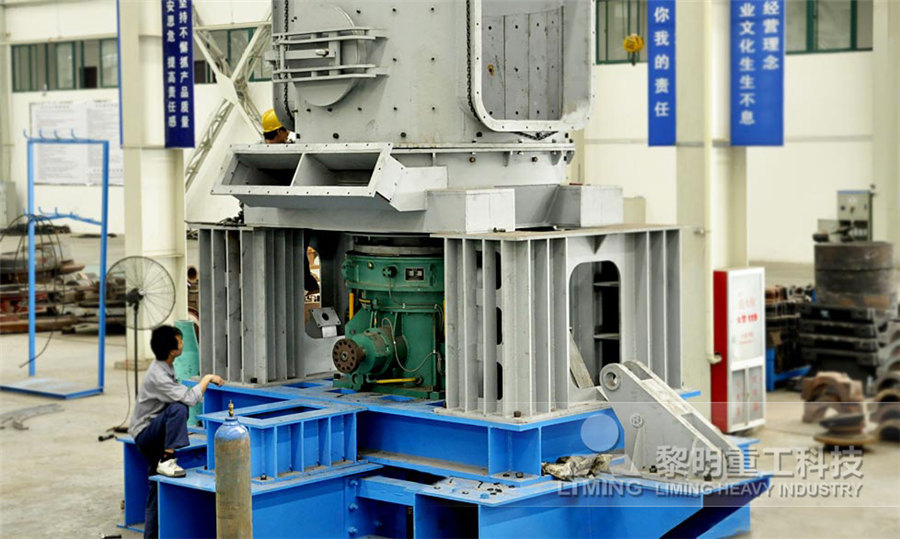
Nominal chemical compositions of powder metal steels
In this study, the unalloyed steel and microalloyed steel containing 015% Nb were produced by powder metallurgy and hot deformed to reduce the thickness by 40% and 75%2012年11月1日 The micro powder injection molding permits to get net shape components with complex geometry from polymers combined with ceramics, or metals The microMIM process open the way for functional microcomponents micromanufacturing in large batch for wide variety of markets due to the increasing demands in various applications fields, eg, sensors, medical Determination of critical and optimal powder loadings for Laser metal deposition was used to repair grooves on 20 mm thickness 316L stainless steel plates using two different 316L stainless steel commercial powders Fe015C118Cr015Mn02Ni0031P056Si005S (wt%) powder and Fe009C1705Cr12Mn1128Ni0019P046Si009S (wt%) powder Good comprehensive performance of fine metallurgical bonding with Laser metal deposition as repair technology for 316L stainless steel 2023年8月10日 A new grain refinement route for duplex stainless steels: Microduplex stainless steel matrix composites processed by laser powder bed fusion and the chemical composition of 2205 powder was listed in Table 1 In Fig 1 a, most of powder display a nearly spherical shape TiC particles ranging from 05 to 20 μm in size were used A new grain refinement route for duplex stainless steels: Micro
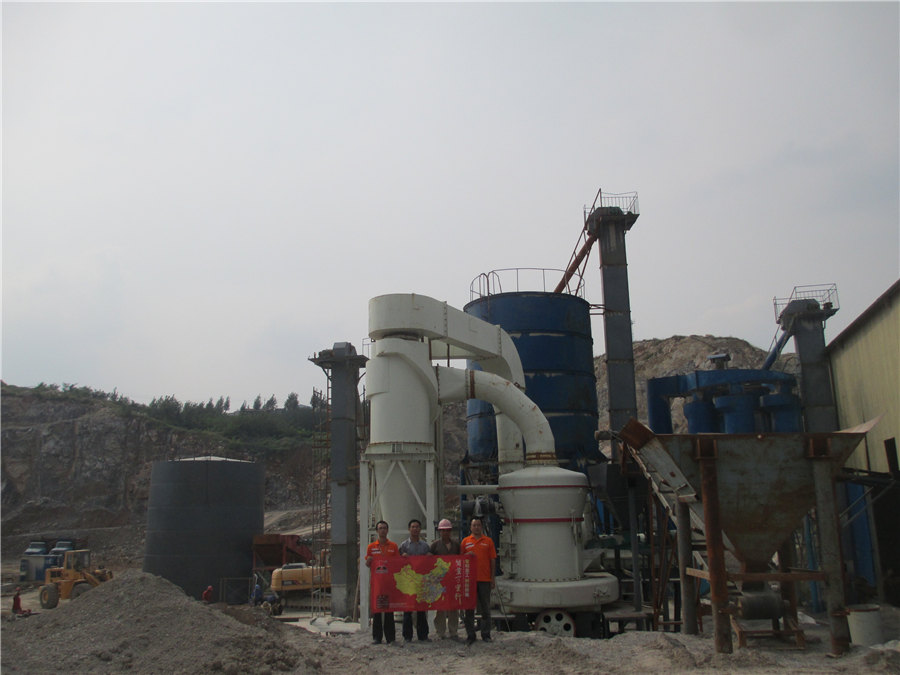
Introduction To The Way Of Steel Slag Recycling The Micropowder
Steel slag is one of the main solid wastes in steel plants, with considerable discharge The recycling of steel slag has become the focus of social attention The micropowder processing scheme using steel slag vertical roller mill can provide an effective way for the recycling of steel slag HCMilling(Guilin Hongcheng) provides customers with professional micropowder 2008年2月1日 In this research, gasatomized 316L stainless steel powders (Fe–17Cr–12Ni–25Mo–1Si–2Mn–003C–0045P–0003S) provided by Osprey Metals Ltd were used 316L powder has particle size distribution of D10 = 44 μm, D50 = 12 μm, D90 = 28 μmSpherical particles with 10 and 41 μm in mean diameter (Sunjin Chemical Co Ltd) made Production of microporous austenitic stainless steel by powder 21 Powders For the experiments, iron micropowder provided by BASF (Ludwigshafen, Germany) was used A detailed description of the materials used is listed in Table 1, along with SEM images and grainsize distribution plots, presented in Figure 1The grain size was measured using the laser diffraction method with Mastersizer 3000 (Malvern Instruments Ltd, Malvern, UK)Comparison between MicroPowder Injection Molding and 2022年7月19日 Micro laser powder bed fusion (μLPBF) enables the fabrication of the components with higher resolution and accuracy compared with conventional laser powder bed fusion (cLPBF) This study demonstrated the feasibility of fabricating materials with excellent mechanical properties due to the fine microstructures generated by μLPBF The near fully Micro laser powder bed fusion of stainless steel 316L: Cellular

Determination of critical and optimal powder loadings for
2012年11月1日 Adapted from powder injection molding (PIM), the microPIM technology satisfies the increasing demands for functionalization and miniaturization of microparts Research works in this area have been carried out through micro injection molding tests issued from mixtures consisting in 316L stainless steel fine powders with D 50 = 34 μm and different 2023年12月12日 Formation of two distinct cellular structures in 316L stainless steel fabricated by microlaser beam powderbedfusion Dayong An a Department of Plasticity Technology, School of Materials Science and Engineering, Shanghai Jiao Tong University, Shanghai, People’s Republic of China Correspondence mation of two distinct cellular structures in 316L stainless steel 2013年1月1日 Although powder metallurgy is a very modern technology, ferrous PM strictly speaking dates back more than 4000 years, since steel has been manufactured by a related technology – very similar to modern powder forging – right into the late middle ages, it being impossible to melt iron up until then 1 When the more productive blast furnace technology Advanced powder metallurgy steel alloys ScienceDirect2011年1月25日 It should be noted that the composition and the powder loading rate of the micronano powder feedstock used in this study were optimized based on our previous works on the mixing and molding Die Compaction and Sintering Behavior of Fe MicroNano Powder

PowderBased 3D Printing for the Fabrication of Device with Micro
2020年6月30日 2 PowderBased 3DPrinting Modalities and Their Resolution Powderbased 3Dprinting processes are very common in polymer 3D printing as well as in metal 3D printing [23,24,26]Figure 1 shows the schematic diagram for the classification of powderbased 3Dprinting processes Out of the seven 3Dprinting categories, powderbased 3Dprinting Download Table Chemical composition of 174 PH stainless steel powder from publication: The Effects of Powder Recycling on the Mechanical Properties of Additively Manufactured 174 PH Stainless Chemical composition of 174 PH stainless steel powder2023年8月10日 The employment of grain refinement approaches is regarded as a favorable strategy to increase mechanical properties of duplex stainless steels (DSSs) In this work, a new grain refinement route was successfully developed via laser powder bed fusion (LPBF) of microduplex stainless steel (SS) matrix composites along with a subsequent quenching processA new grain refinement route for duplex stainless steels: Micro 2002年9月30日 To overcome these drawbacks, micropowder injection molding (μPIM), a variant of powder injection molding (PIM), has been developed in recent years [4], [5] μPIM inherits the features of conventional PIM such as low production cost, shape complexity, applicability to many materials, good tolerance and good mechanical properties μPIM can be Micropowder injection molding ScienceDirect
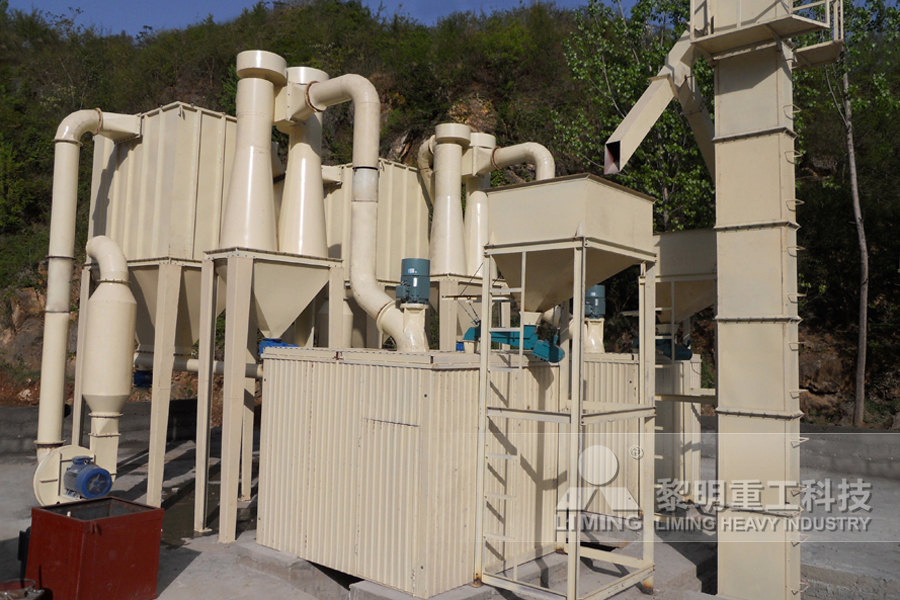
(PDF) Low temperature powder injection molding of iron micro
2012年9月1日 The feedstock consisted of 66 vol% powder and 34 vol% paraffinwax binder in which the powder composition was 75 vol% Fe micro powder (4 μm in average size) and 25 vol% nano powder (100 nm)3 micropowder or microporous corundum–spinel powder were selected to carry out the immersion tests with molten steel On the one hand, the higher surface roughness of the filter skeleton prepared from microporous raw materials increased the adsorption capacity of skeleton surface on inclusions in molten steel On the other hand, the higher Purification performance on molten steel of novel Al2O32022年1月10日 Commercial Metals Co said Jan 10 it plans to construct a state of the art "rebar centric" micro steel mill geographically situated to primarily serve regions in the eastern US Explore SP Global SP Global; CMC plans new steel micro mill to serve eastern US Metals Steel Platts World Steel Review Energy Transition CMC plans new steel micro mill to serve eastern US2021年1月15日 Both these powders satisfy the 95% theoretical density (TD) criterion after sintering at 900 °C, but other fine powders (eg, FeP) have to be admixed to increase the assintered hardness to minimum 92 HRB (>200 HV) [14,15,16]Therefore, the objective of the present work was to design and manufacture a lowalloy steel powder, which would combine A Newly Developed Easily Sinterable LowAlloy Steel Powder
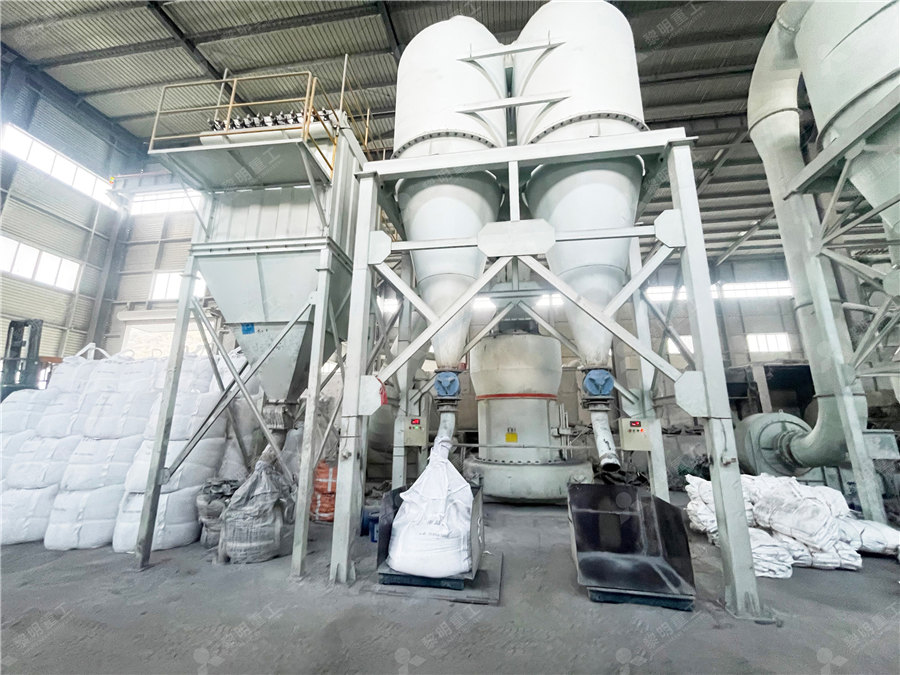
Micro powder injection moulding ScienceDirect
2006年4月1日 Fig 2 shows green micro injection molded components made with conventional 316 L stainless steel feedstock The limitations of using conventional feedstock (mean particle size: 8 μm) are clearly visible as the components show defects and poor shape retention (rounded edges) For optimum performance, for example in terms of flow behavior or 2010年4月30日 The 316L stainless steel powder was uniformly distributed within the binder The 316L stainless steel micromixer was well replicated by micro powder injection molding The molded, debound and sintered micromixers had good shape retention, without visible defects, such as warpage, incomplete filling, crack, etcReplication and characterization of 316L stainless steel micro 2020年6月3日 As can be seen in Table 1, stainless steel 316 L, 174PH, tungsten, and its alloys, titanium, and its alloys, nickelbased superalloys, yttriastabilized zirconia, alumina, and zirconiatoughened alumina have been mostly used by the researchers as materialsFrom Table 1, it can be said that the microsized powder particles received higher attention in the past 15 years Process Parameters Used in Macro/Micro Powder Injection Molding2008年10月15日 This paper presents an approach to fabricate 316L stainless steel micro parts with complex shapes using soft lithographical and powder metallurgical techniques The process includes production of high quality deep micro SU8 master moulds and their negative replicas in polydimethylsiloxane (PDMS)Fabrication of 316L stainless steel micro parts by softlithography

Optimization of Chemical Composition of the Mould Powder
2016年12月1日 This might mean that the new powder Scorialit SPH C176/AlS9 used for the cast of C45 steel Ø170 mm billets, featuring very good quality of billets surfaces and muchDownload Table Stainless steel(SS316L) powder characteristic from publication: Water Atomised Stainless Steel Powder for Micro Metal Injection Molding: Optimization of Rheological Properties Stainless steel (SS316L) powder characteristic Download Table2024年4月25日 However, a recent study on a high manganese triplex steel composition has revealed the occurrence of both hot cracking and micro segregation during rapid solidification in LPBF, highlighting potential processability issues of this family of high alloy steelsTriplex steel powder design to avoid hot cracking in laserpowder 2019年1月1日 Request PDF Laser metal deposition as repair technology for 316L stainless steel: Influence of feeding powder compositions on microstructure and mechanical properties Laser metal deposition Laser metal deposition as repair technology for 316L stainless steel
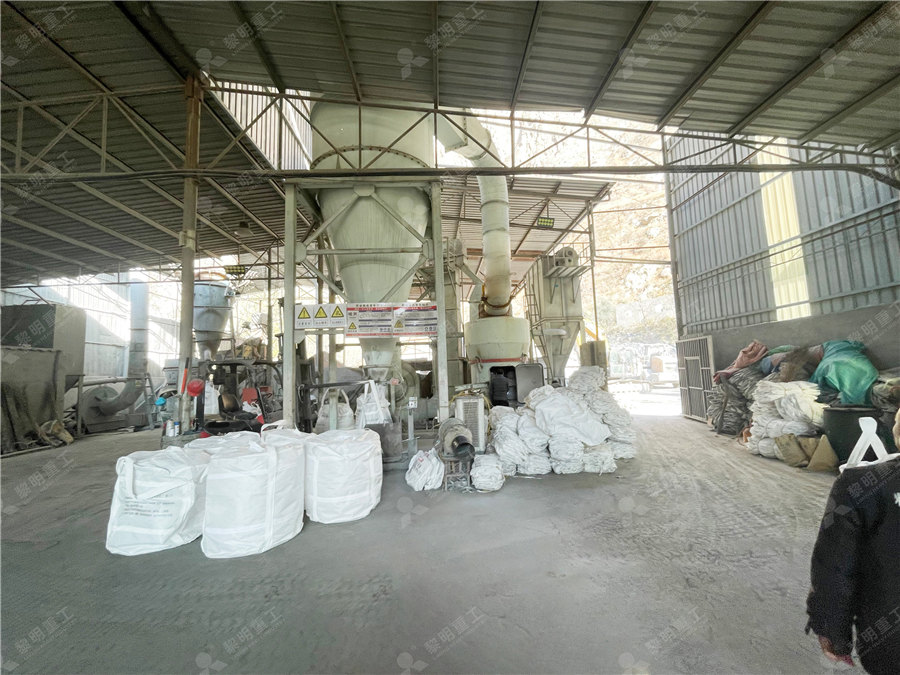
Stainless steel powder chemical composition Download Table
Download Table Stainless steel powder chemical composition from publication: Water Atomised Stainless Steel Powder for Micro Metal Injection Molding: Optimization of Rheological Properties 2022年7月19日 Micro laser powder bed fusion (μLPBF) has been developed with the increasing demand of the high resolution for the lightweight structure [[1], [2], [3]]The major differences between μLPBF and conventional laser powder bed fusion (cLPBF) are the laser spot size, powder size, and the layer thicknessMicro laser powder bed fusion of stainless steel 316L: Cellular