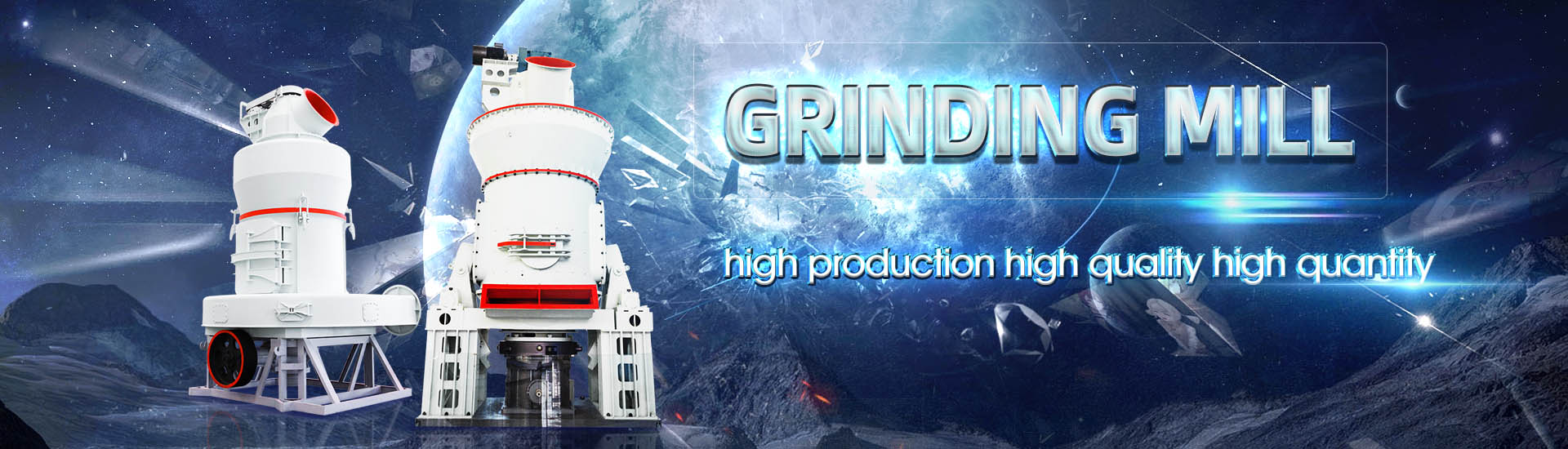
Process flow of quicklime coal plant quicklime coal
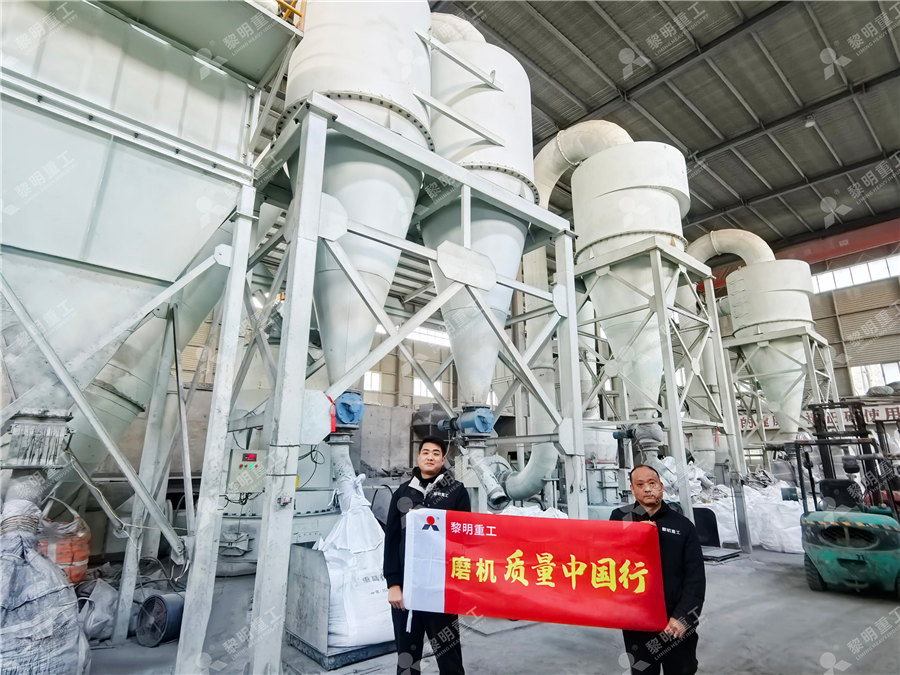
Decarbonising the lime industry: Stateoftheart ScienceDirect
2022年10月1日 A slurry slaker requires initial mixing of quicklime and water (1:33–5 wt ratio) in the slaking chamber; the paste flows by gravity to the grit removal chamber, where the 2023年6月5日 Among the various kiln designs, parallel flow regenerative (PFR) kilns with pulverized coal combustion are the predominant technology The performance of the PFR Transient simulation of heat and mass transfer in a parallel flow 2007年12月1日 The new multiplechamber shaft kiln with combustion chambers and countercurrent cooling zone is fired with natural gas, heavy fuel oil, pulverized coal or small Production of Quicklime ResearchGate2021年9月1日 Industrially produced quicklime from a coalfired rotary kiln was analyzed and compared with laboratoryscale studies of surface interactions between two coal ashes and Coal ash and limestone interactions in quicklime production
.jpg)
Optimizing Quicklime Production Operations AnyLogic
How to maximize resource utilization in a quicklime production facility using simulation modelingIn this paper, a numerical tool is presented, which simulates a largescale Parallel Flow Regenerative (PFR) kiln that currently uses coke as main fuel The developed tool aims at CFD Analysis of Cofiring of Coke and Biomass in a Parallel Flow 1998年5月14日 This chapter contains sections titled: Introduction Principles of Lime Burning Development of Lime Kilns Modern Kilns Selection of Lime Kilns Kiln Control Mass and Heat Production of Quicklime Lime and Limestone Wiley Online LibraryA new and innovative Parallel Flow Regenerative lime kiln process using 100% blast furnace gas achieves the same performance as a natural gasfired PFR lime kiln; however, with New PFR lime kiln process with blast furnace gas and oxygen
.jpg)
Lime kiln Wikipedia
A lime kiln is a kiln used for the calcination of limestone (calcium carbonate) to produce the form of lime called quicklime (calcium oxide) The chemical equation for this reaction isCoal fired power plants also known as coal fired power stations are facilities that burn coal to make steam in order to generate electricityThese stations, seen in Figure 1, provide ~40% of the world's electricity Countries such as South Coal fired power plant Energy Education2019年9月23日 In conventional directfired quicklime and cement production processes, ashforming elements from coal and other fuels will interact with the limebased products and the MgObased refractories Characterization of Ring Deposits Inside a Quicklime Producing A coal preparation plant typically operates with multiple cleaning circuits based on the particle size distribution of runofmine coal Clean coal product from a plant commonly has to satisfy Flowsheet of a modern coal preparation plant incorporating four
.jpg)
Coalfired power plant process diagram ResearchGate
Download scientific diagram Coalfired power plant process diagram from publication: Maintenance Strategy Optimization of a CoalFired Power Plant Cooling Tower through Generalized Stochastic 2021年9月1日 This paper reports on results from detailed studies on coal ash and limestone interactions during calcination Industrially produced quicklime from a coalfired rotary kiln was analyzed and Coal ash and limestone interactions in quicklime productionremains is quicklime, calcium oxide Limestone decomposes into quicklime and carbon dioxide: CaCO 3> CaO + CO 2 by weight 100 > 56 + 44 The process is called ‘calcination’ If calcination is carried out correctly the lumps of quicklimeApplications of Quicklime Hydrated LimeThe developed technical and technological assumptions for agglomerating coal slurries are the subject of the investment process for the construction of a plant with a capacity of ~80 tonnes/h [5] Coal slurry agglomerating technology is suitable to use not only in mined and fuel processing plants, but also in power plants, power and heating plants and heating plantsBriquetting Process an overview ScienceDirect Topics
.jpg)
Flowsheet of a modern coal preparation plant incorporating
Coal preparation plant simulators are computer programs used to evaluate the performance of a preparation plant for given feed coal characteristics and the type of process flowsheet selectedDownload Table 1 Dravo Lime Company Quicklime Typical Analysis (Black River Plant) from publication: Advances in Spray Drying Desulfurization for HighSulfur Coals Advances in spray drying 1 Dravo Lime Company Quicklime Typical Analysis (Black River Plant)In calcination process, lime is cooked/calcined at 800°c in a kilnWe are providing shafts kilns and rotary kilns for calcining of limestone/lime sludge with multi fuel options Prior to calcination, exhaust gases of kiln preheat lime And after coming out of calcination area, quicklime is cooled by direct contact with cooling airHydrated, Quick, and PCC Lime Processing Plant Chanderpur2006年12月1日 Likewise, considering all the flows, the whole element partitioning between the different outlets of the coal combustiondesulphurisation plant can be established The coal stockpile combusted during the sampling period produced 13 844 and 2443 t of fly ash and boiler slag, respectively, being necessary 10 994 t of limestone to perform the Environmental impact of a coal combustiondesulphurisation plant

Modeling and analysis of optimal performance of a coalfired
2022年11月1日 In recent decades, many researchers carried out studies on the simulation and modeling of the steam power plants’ performance (Ibrahim et al, 2018, Ibrahim et al, 2017b)As the present study is focused on coalfired power plants, the performance of these kinds of power plants based on the energy and exergy viewpoints are sought in more detail here (Ali et al, 2019年8月1日 Gaspar et al (2015) also presented a model for the simulation of the startup process of a pccplant The heatingup process in the stripper is neglected and not simulated in these publications They use a storage tank filled with regenerated solvent to start the solvent flow to the absorberModeling and simulation of the startup process of coal fired 3Limestone Calcination Limestone in the preheater will be preheated by the hot air, then it will be discharged to rotary kiln through chute that connecting preheater and kiln, it will stay in the kiln for 152 hours for calcination, during lime calcination plant process, it will be calcinated with temperature around 1300 ℃, after which comes limestone decomposition and release of co2 Lime Production Line AGICO Cement PlantDownload scientific diagram Process chain of electricity generation from coal to electricity from publication: Energy Efficiency: An Engineering Pathway towards Sustainability Energy Process chain of electricity generation from coal to electricity
.jpg)
Decarbonising the lime industry: Stateoftheart ScienceDirect
2022年10月1日 The term “lime” is usually used to refer to all those products deriving from the calcination of limestone and/or chalk, although they may be classified as: quicklime CaO, hardburnt lime CaO, slaked/hydrated lime Ca(OH) 2, and dolomitic lime (eg, 30 wt% CaO, 21 wt% MgO, and 45 wt% CO 2 in the original limestone [1])CaO, the main product of the calcination 2002年10月10日 Conversion of a desulfurization plant from quicklime to chalk requires high reactivity of the chalk products In contrast to other CaCO3 products, chalk, as a result of its origin, with a mean particle size of 2 to 3 μm is a sorbent offering high reactivity and the possibility for replacing the conventional lime additive Further advantages of chalk over high‐calcium Conversion of a Wet‐Process Flue‐Gas Desulfurization Plant from Lime Calcination Plant Finished products: active lime Limekiln: rotary kiln (vertical shaft kiln upon request) Capacity: 2001000t/d Limestone granularity: 2040 mm Fuel: gas, pulverized coal Get the solution now!Lime Calcination Plant Solution 2001000tpd Quicklime CNBM 2023年11月2日 Study of the Use of Quicklime in the Mine Acid Water Neutral Process at Pit KPL 3 West Banko West Mining IUP PT Bukit Asam Tbk Tanjung Enim South Sumatra Mineral, 3(2), 16 Show moreEfforts to Improve the Quality of Quicklime in Handling Acid Mine
.jpg)
Production of Quicklime Lime and Limestone Wiley Online
1998年5月14日 This chapter contains sections titled: Introduction Principles of Lime Burning Development of Lime Kilns Modern Kilns Selection of Lime Kilns Kiln Control Mass and Heat Balances InstrTo present a 1D mathematical model to simulate the limeburning process in normal shaft kilns [6], Gutiérrez et al analyzed the energy consumption of vertical kilns [7], Piringer classified lime Reactivity of quicklime depending on the burning 2016年4月12日 Remarks on Coal Beneficiation Process and Diagram “SubA” Coal Flotation Systems have been successful for recovery of both coarse and fine coal It is important, however, to employ a twostage circuit for maximum Coal Beneficiation Process Diagram 911Metallurgist2019年12月1日 Burning coal produces coal combustion residuals (CCR), or byproducts, which include fly ash, bottom ash, boiler slag, fluegas desulfurization residues, and fluidized bed combustion ash Over 70% of waste coal ash is categorized as fly ash (FA), fine particulates captured by particulate control equipment, ranging in size from 05 μm to 300 μm [ 3 , 4 ]Physical, chemical, and geotechnical properties of coal fly ash:
.jpg)
Optimal Design of Solvent Based Post Combustion CO
flue gas stream derived from a quicklime plant using the generalied design framework proposed by Damartzis et al, 2013 The operability of the designed process is investigated through the Using Equation (86) and the state point parameters given in Table 87, the temperature profile of the steam generator is determined and represented in the temperature vs heat duty diagram shown in Figure 839The flue gas is at more than 1650 °C in state 3 and leaves the heat exchanger network at about 1350 °C in state 31The temperature differences on the heat Conventional CoalFired Power Plant ScienceDirectIn surface mining, the ground covering the coal seam (the overburden) is first removed to expose the coal seam for extraction The elements of a surface mining operation are (1) topsoil removal and storage for later use, (2) drilling and blasting the strata overlying the coal seam, (3) loading and transporting this fragmented overburden material (called spoil), (4) drilling and blasting the Coal Mining and Processing Methods The National Academies Download scientific diagram Process Flow Diagram of Sasol's Coal to Liquid Fuel Process from publication: SASOL coal to fuel process (Gasification FischerTropsch) Process Flow Diagram of Sasol's Coal to Liquid Fuel Process
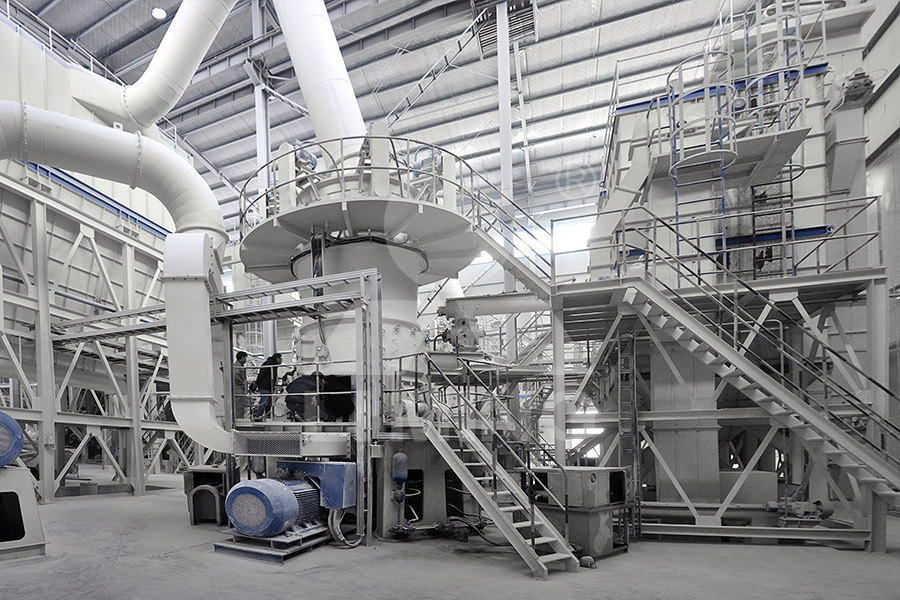
DenseMedium Beneficiation of Fine Coal: Coaltech 2020 Pilot Plant
The plant was constructed at Black Wattle Colliery just outside Middelburg On completion, the plant was moved to Koornfontein Colliery, the first test site for the plant The plant was commissioned on 5 November 2001 and the first coal was processed through the plant on 13 November A view of the completed plant is shown in Figure 12023年1月27日 G60U3based GBMB2 with 5% quicklime provided a stable and smooth slurry with a bleeding rate of 125%, a slump flow of 205 mm, and a hardened body with a sevenday UCS of 151 MPa Research Experimental Study on Performance Optimization of Grouting coalderived gas can be used, as discussed later Key properties of a gas turbine are the inlet air flow rate, the turbine inlet temperature and the pressure ratio (the compressor delivery pressure divided by the turbine outlet pressure) The air flow rate sets the output, while the other two parameters determine the efficiency As gas turbineUnderstanding coalfired power plant cycles ICSCCoal fired power plants also known as coal fired power stations are facilities that burn coal to make steam in order to generate electricityThese stations, seen in Figure 1, provide ~40% of the world's electricity Countries such as South Coal fired power plant Energy Education
.jpg)
Characterization of Ring Deposits Inside a Quicklime Producing
2019年9月23日 In conventional directfired quicklime and cement production processes, ashforming elements from coal and other fuels will interact with the limebased products and the MgObased refractories A coal preparation plant typically operates with multiple cleaning circuits based on the particle size distribution of runofmine coal Clean coal product from a plant commonly has to satisfy Flowsheet of a modern coal preparation plant incorporating four Download scientific diagram Coalfired power plant process diagram from publication: Maintenance Strategy Optimization of a CoalFired Power Plant Cooling Tower through Generalized Stochastic Coalfired power plant process diagram ResearchGate2021年9月1日 This paper reports on results from detailed studies on coal ash and limestone interactions during calcination Industrially produced quicklime from a coalfired rotary kiln was analyzed and Coal ash and limestone interactions in quicklime production
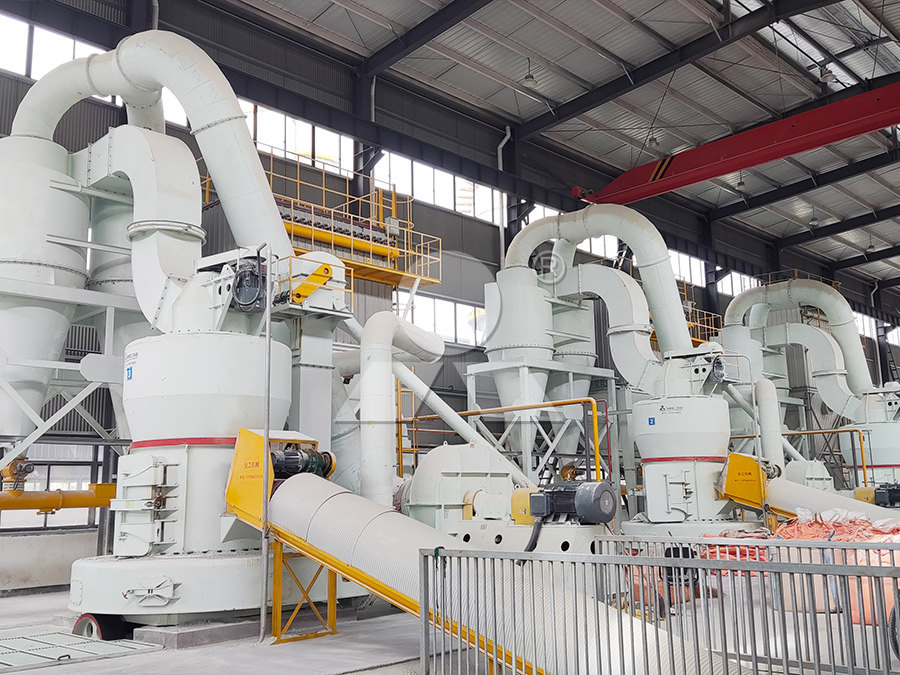
Applications of Quicklime Hydrated Lime
remains is quicklime, calcium oxide Limestone decomposes into quicklime and carbon dioxide: CaCO 3> CaO + CO 2 by weight 100 > 56 + 44 The process is called ‘calcination’ If calcination is carried out correctly the lumps of quicklimeThe developed technical and technological assumptions for agglomerating coal slurries are the subject of the investment process for the construction of a plant with a capacity of ~80 tonnes/h [5] Coal slurry agglomerating technology is suitable to use not only in mined and fuel processing plants, but also in power plants, power and heating plants and heating plantsBriquetting Process an overview ScienceDirect TopicsCoal preparation plant simulators are computer programs used to evaluate the performance of a preparation plant for given feed coal characteristics and the type of process flowsheet selectedFlowsheet of a modern coal preparation plant incorporating Download Table 1 Dravo Lime Company Quicklime Typical Analysis (Black River Plant) from publication: Advances in Spray Drying Desulfurization for HighSulfur Coals Advances in spray drying 1 Dravo Lime Company Quicklime Typical Analysis (Black River Plant)
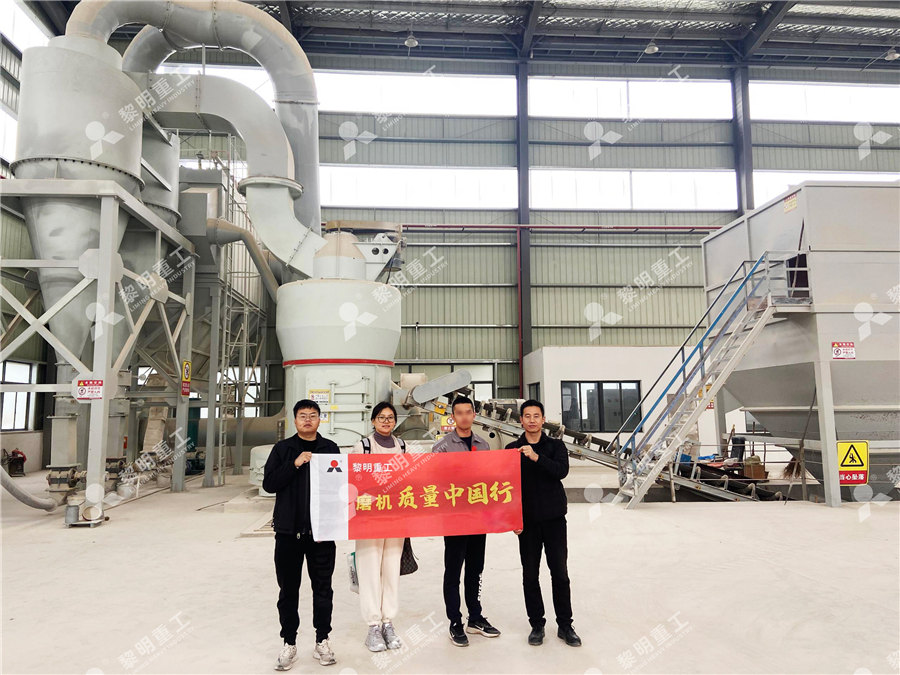
Hydrated, Quick, and PCC Lime Processing Plant Chanderpur
In calcination process, lime is cooked/calcined at 800°c in a kilnWe are providing shafts kilns and rotary kilns for calcining of limestone/lime sludge with multi fuel options Prior to calcination, exhaust gases of kiln preheat lime And after coming out of calcination area, quicklime is cooled by direct contact with cooling air