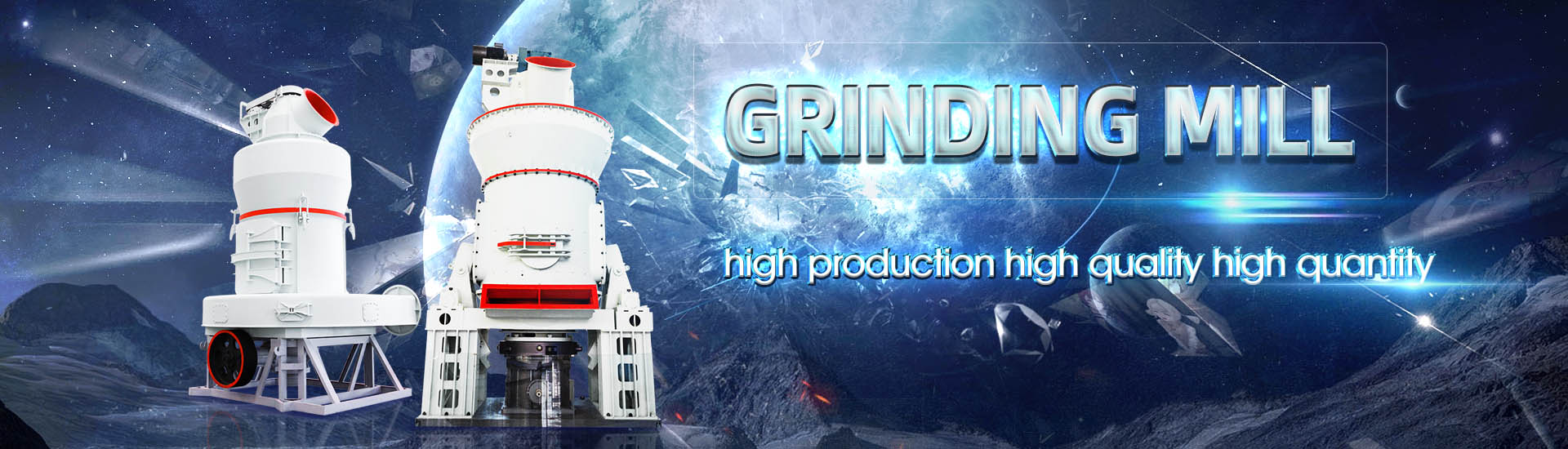
Highefficiency and energysaving ore mill picture

Process and Technology Solutions for Improving the Energy
1 天前 Download: Download highres image (173KB) Download: Download fullsize image; Figure 8 Case 1B; sensitivity analysis of CO 2 avoidance cost with respect to ee price at a 2022年1月1日 A pilotscale study of highefficiency and energysaving grinding technology using a special stirred mill with the ceramic medium was proposed in this studyHighefficiency and energyconservation grinding technology Energysaving ball mills are a cornerstone in mineral processing operations, designed to reduce energy consumption while maintaining or even enhancing processingThe Role of EnergySaving Ball Mills in Mineral Processing2021年11月1日 Through the new method, highenergy grinding was performed using a commercially available planetary mill on silicate materials such as limestone, feldspar, Highefficiency and energyconservation grinding technology
.jpg)
Energy Efficiency Analysis of Copper Ore Ball Mill Drive Systems
2021年3月23日 Milling is among the most energyconsuming technological stages of copper ore processing It is performed in mills, which are machines of high rotational masses The start of The highefficiency energy saving ore mill saves electricity, has low noise, and is particularly suitable for cement, silicate products, novel building materials, chemicalHighefficiency energy saving ore mill Google PatentsCeramic grinding, which in this paper is defined as a method of using ceramic materials as grinding media, is favored by many processing plants as an emerging highefficiency and Highefficiency and energyconservation grinding technology information on the technoeconomic aspects of suitable energyefficient technologies that can be adopted by DRI units SIMA members–major sponge iron producers and regional ENERGYEFFICIENT TECHNOLOGY OPTIONS FOR DIRECT
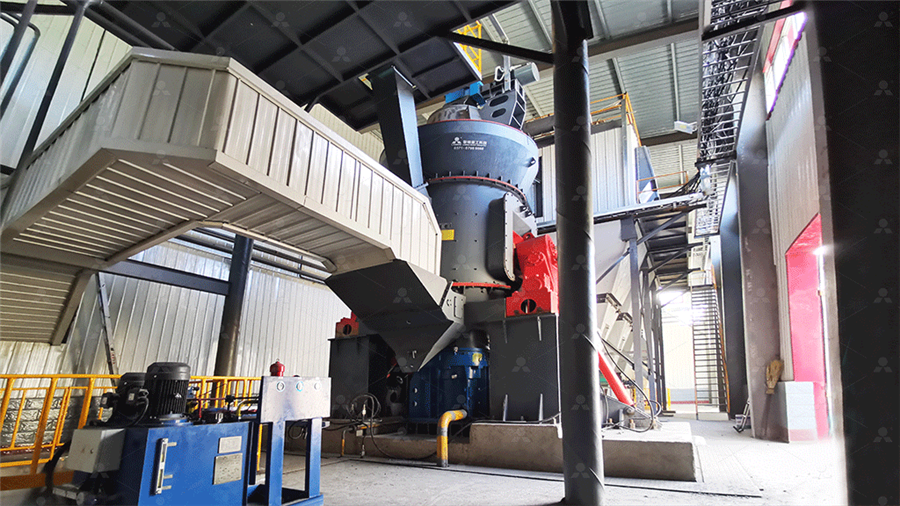
High Pressure Grinding Roll and Magnetic Separation for Energy
2024年5月31日 This study described the quest to improve grinding efficiency by adding a combined high pressure roller (HPGR) and magnetic separation process between threestage 2021年2月26日 Milling is among the most energyconsuming technological stages of copper ore processing It is performed in mills, which are machines of high rotational masses The start of a mill filled to capacity requires Energy Efficiency Analysis of Copper Ore Ball Mill By adjusting the gradation of the steel balls, the size and amount of the discharge fineness can be changed The highefficiency and energysaving ball mills produced by our company are all supported by rolling bearings instead of Energy Saving Ball Mill Hongji Mine MachineryThe lowcost highefficiency energysaving ore mill comprises a frame (1) The lowcost highefficiency energysaving ore mill is characterized in that the middle end of the frame (1) is connected with a clay semicircle (2); the upper end is connected with a seat and bearing (3), a seat and bearing (13), an adapter (4), a motor (5), an upper semicircle (6), a feed gate (7), a Lowcost highefficiency energysaving ore mill Google Patents
.jpg)
CNA High efficiency ore mill Google Patents
The invention discloses a highefficiency ore mill, which comprises a base, wherein an ore milling platform is welded on the base, convenient operation, time saving, low labor intensity and high production efficiency; when the energysaving ore mill works, 2023年12月1日 Multiobjective optimisation for energy saving and high efficiency production oriented multidirectional turning based on improved fireworks algorithm considering energy, CloudDPP for distributed process planning of millturn machining operations Robot Comput Integrated Manuf, 47 (2017), pp 7684Multiobjective optimisation for energy saving and high efficiency 3RZGHU 7HFKQRORJ\ , 1 Introduction Grinding operation is the last preparation stage before beneficiation In this stage, the material undergoes the combined action of impact andEnergy conservation and consumption reduction in grinding 2019年3月8日 IMPROVING THERMAL AND ELECTRIC ENERGY EFFICIENCY AT CEMENT PLANTS: 252 Replacing a Ball Mill with a Vertical Roller Mill, HighPressure Grinding Rolls, Besides the energysaving effect, IMPROVING THERMAL AND ELECTRIC ENERGY EFFICIENCY AT
.jpg)
(PDF) Energy Efficient Ball Mill Circuit – Equipment Sizing
2013年7月15日 The energy saving resulting from the replacement of cyclones with screens in a closed ball mill circuit was estimated to be in the range of 10 to 25% (Jankovic and Valery, 2012a) An analysis of theSBM Ore Ultrafine Grinding Mill Discharge fineness: 1503000 mesh Feed size: 20 mm Output: 120 T/H Product features: Safe and reliable, high efficiency and energy saving, low carbon and environmental protection, stable operation, wide range of SBM Ore Ultrafine Grinding MillBall Mills are widely used in the ceramic and mining industries, where the grinding process requires strict grain size control WEG developed an efficient solution for this applicEnergy Efficiency Solutions Ball Mill WEG2024年5月31日 This paper presents an industrial verification test, adding a high pressure grinding roll and magnetic separation operation after the thirdstage fine crushing operation to reduce the particle size of ball mill feed and improve the processing capacity of grinding operation The optimal process parameters of high pressure grinding roll and magnetic separation were High Pressure Grinding Roll and Magnetic Separation for Energy Saving
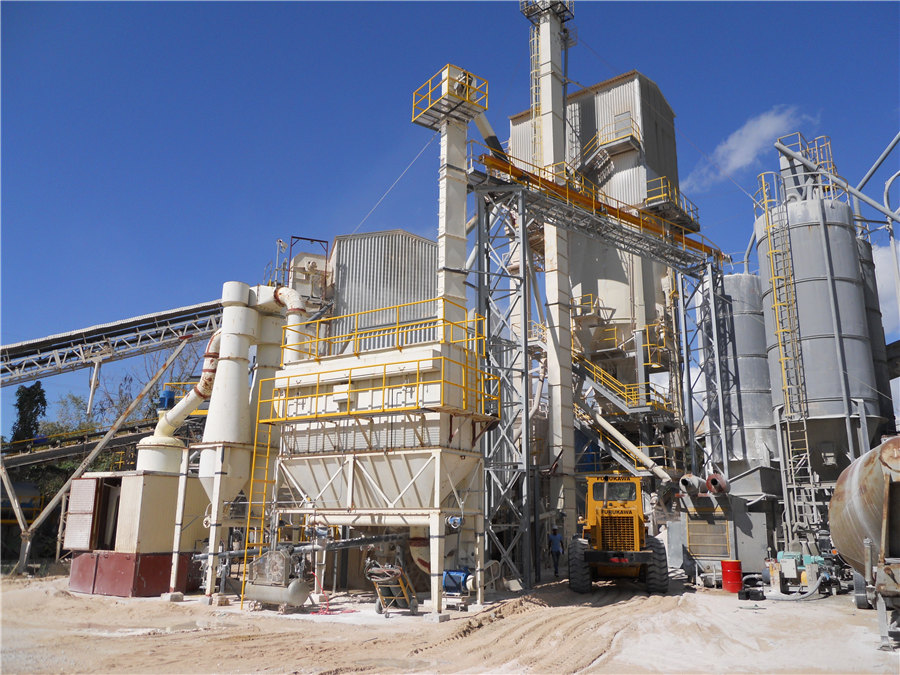
Energy Savings and Improved Recovery with Small Grinding Media
2002 Fe Ball Mill Regrind 26 mm Same Same Yes 2004 CuPb Ball Mill Regrind 5 mm 10% Same +56% 33% Same Yes 1 CuPbZn Ball Mill Secondary 8 mm 44% Same Same 2 AuCu Ball Mill Regrind 6 mm 30% Same Yes 3 CuMo VertiMill Regrind N/A 20% +25% Same 4 CuAu VertiMill Regrind N/A 60% Same Same 2022年1月1日 A pilotscale study of highefficiency and energysaving grinding technology using a special stirred mill with the ceramic medium was proposed in this study Impact of ball filling rate and stirrer tip speed on milling iron ore by wet stirred mill: analysis and prediction of the particle size distribution Powder Technol (2021)Highefficiency and energyconservation grinding technology using Therefore, any research effort that has the potential to reduce energy consumption while maximizing grinding efficiency is of great importance This Special Issue welcomes papers that highlight innovations and future trends in modeling grinding and technological ways to improve the grinding efficiency in ore/raw material beneficiationGrinding Modeling and Energy Efficiency in Ore/Raw Material The invention relates to a highefficiency energy saving ore mill which consists of a frame (1) The highefficiency energy saving ore mill is characterized in that the upper end of the frame (1) is connected with a bearing and seat (3) and a bearing and seat (15) which are connected by a concentric shaft (16), an adapter (5) is connected with a motor (4); and a concentric axle is Highefficiency energy saving ore mill
.jpg)
Integrative optimization for energy efficiency, CO2 reduction, and
Exploring measures for lowenergy consumption, lowCO 2 emission, and higheconomic benefit in the iron and steel industry is gaining increasing attention This study innovatively establishes a holistic approach that integrates energy consumption, CO 2 emission and economic benefit to optimize a typical steel mill After optimization, the energybenefit indicator has increased from of the energy requirements of HPGR and SAG mill circuits in hard ore applications by P Rosario*† and R Hall† Synopsis The application of high pressure grinding rolls (HPGR) has been growing in the mining industry for the last 10 to 15 years The major benefits supporting this trend are better energy efficiency,A structured approach to the evaluation of the energy The energysaving highefficient ore mill is characterized in that the milling barrel is provided with a gear, avoids repeated operation and has high work efficiency By aid of the conical sieve, the energysaving highefficient ore mill does not need a huge spiral classifier, Energysaving highefficient ore mill Google Patentsof the energy requirements of HPGR and SAG mill circuits in hard ore applications by P Rosario*† and R Hall† Synopsis The application of high pressure grinding rolls (HPGR) has been growing in the mining industry for the last 10 to 15 years The major benefits supporting this trend are better energy efficiency,A structured approach to the evaluation of the energy

A structured approach to the evaluation of the energy
of the energy requirements of HPGR and SAG mill circuits in hard ore applications by P Rosario*† and R Hall† Synopsis The application of high pressure grinding rolls (HPGR) has been growing in the mining industry for the last 10 to 15 years The major benefits supporting this trend are better energy efficiency,Figure 5 Startup of the LSPMSM SMH1732T motor with a filled ball mill after two hours of downtime: (a) active power, (b) current intensity, (c) voltage "Energy Efficiency Analysis of Copper Ore Ball Mill Drive Systems"Energy Efficiency Analysis of Copper Ore Ball Mill Drive Systems2023年2月23日 Replacing outdated motors on feed processing equipment with highefficiency motors and variable speed drives (VSD), which match input power to the operational requirements, holds vast potential for feed millers “Too 3 ways to improve feed mill energy efficiency2006年3月1日 Iron and steelmaking technologies in the USA have and will continue to evolve, resulting in a significantly changed industry by 2015 or compared to that of 10 years agoFinal Report on Energy Efficiency and Energy Savings in Recycling
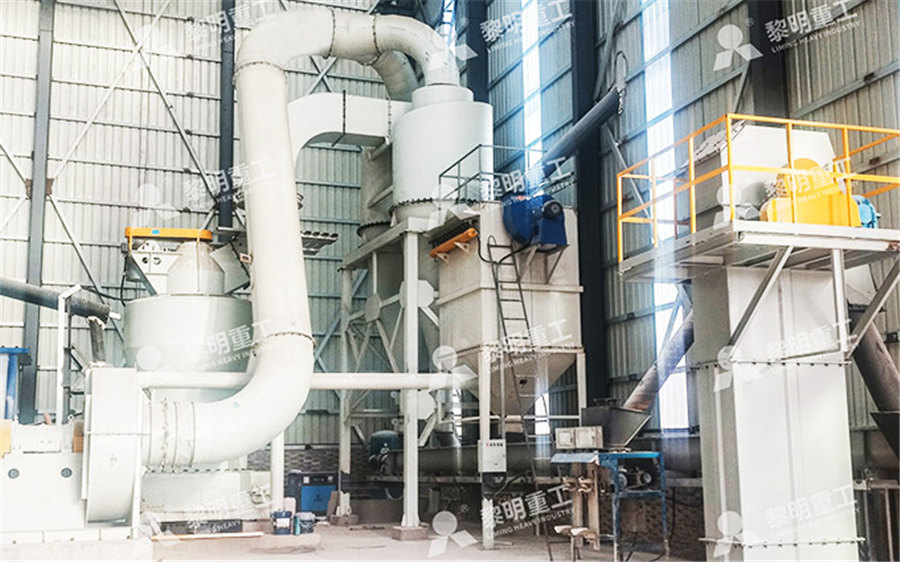
Energy saving and process optimization in a conventional hot strip mill
water savings was approx 20%, which allowed shutting off one of the three highpressure pumps Electrical energy saving amounts to 9,300,000* kWh/ year At the current energy costs this is equivalent to 000 TL 2,100,/ 641,700 EUR** Additional advantages are seen such as reduced material cooling and the lower wear of the2018年1月20日 The mapping relationship about tool path, machining efficiency, energy consumption and carbon emission is analyzed Selecting machining spacing, residual height and norepeated cutting as constraints, a multiobjective tool path optimization model based on machining efficiency, energy consumption, and carbon emission was established (2)Multiobjective optimization of tool path considering efficiency Milling is among the most energyconsuming technological stages of copper ore processing It is performed in mills, which are machines of high rotational masses The start of a mill filled to capacity requires appropriate solutions that mitigate the overloading One method for increasing the energy efficiency of ball mills is to optimize their drive systems This article looks at two Energy Efficiency Analysis of Copper Ore Ball Mill Drive Systems2022年6月29日 Gold ore wet pan mill have many years of history in beneficiation equipment, High efficiency and energy saving, high output, this product is used for the recovery of tailings in the iron ore process, so that the ore powder is not lost, How to use and maintain the gold ore wet pan mill
.jpg)
Multiobjective modeling and evaluation for energy saving and high
2024年5月1日 To reduce energy consumption, enhance production efficiency and perform superior product quality, the reference [16] proposes a new turning method called forwardandreverse multidirectional turning (MDT)The aforementioned challenges of UDT can be effectively addressed through the implementation of flexible multidirectional turning paths including both 2022年3月30日 All industries are facing increasing pressure to ensure that carbon emissions are reduced to help achieve the socalled 15 °C future This has led to most of the major mining companies committing to significant reductions in their operational carbon footprint – in many cases by up to 30–40% in the next 10–15 years and to place themselves in a netzero scope Helping to reduce mining industry carbon emissions: A stepby The nominal mill efficiency, at optimum speed, is 80 Mg/h The dimensions and the high mass of the rotating elements cause the drive system to be overloaded when the mill filled with copper ore is started For this reason, the mill is stopped only in Energy Efficiency Analysis of Copper Ore Ball Mill Drive Systems2021年2月26日 Milling is among the most energyconsuming technological stages of copper ore processing It is performed in mills, which are machines of high rotational masses The start of a mill filled to capacity requires Energy Efficiency Analysis of Copper Ore Ball Mill
.jpg)
Energy Saving Ball Mill Hongji Mine Machinery
By adjusting the gradation of the steel balls, the size and amount of the discharge fineness can be changed The highefficiency and energysaving ball mills produced by our company are all supported by rolling bearings instead of The lowcost highefficiency energysaving ore mill comprises a frame (1) The lowcost highefficiency energysaving ore mill is characterized in that the middle end of the frame (1) is connected with a clay semicircle (2); the upper end is connected with a seat and bearing (3), a seat and bearing (13), an adapter (4), a motor (5), an upper semicircle (6), a feed gate (7), a Lowcost highefficiency energysaving ore mill Google PatentsThe invention discloses a highefficiency ore mill, which comprises a base, wherein an ore milling platform is welded on the base, convenient operation, time saving, low labor intensity and high production efficiency; when the energysaving ore mill works, CNA High efficiency ore mill Google Patents2023年12月1日 Multiobjective optimisation for energy saving and high efficiency production oriented multidirectional turning based on improved fireworks algorithm considering energy, CloudDPP for distributed process planning of millturn machining operations Robot Comput Integrated Manuf, 47 (2017), pp 7684Multiobjective optimisation for energy saving and high efficiency
FYEFEPS2HDZ49G5Z0[B.jpg)
Energy conservation and consumption reduction in grinding
3RZGHU 7HFKQRORJ\ , 1 Introduction Grinding operation is the last preparation stage before beneficiation In this stage, the material undergoes the combined action of impact and2019年3月8日 IMPROVING THERMAL AND ELECTRIC ENERGY EFFICIENCY AT CEMENT PLANTS: 252 Replacing a Ball Mill with a Vertical Roller Mill, HighPressure Grinding Rolls, Besides the energysaving effect, IMPROVING THERMAL AND ELECTRIC ENERGY EFFICIENCY AT 2013年7月15日 The energy saving resulting from the replacement of cyclones with screens in a closed ball mill circuit was estimated to be in the range of 10 to 25% (Jankovic and Valery, 2012a) An analysis of the(PDF) Energy Efficient Ball Mill Circuit – Equipment Sizing SBM Ore Ultrafine Grinding Mill Discharge fineness: 1503000 mesh Feed size: 20 mm Output: 120 T/H Product features: Safe and reliable, high efficiency and energy saving, low carbon and environmental protection, stable operation, wide range of SBM Ore Ultrafine Grinding Mill
.jpg)
Energy Efficiency Solutions Ball Mill WEG
Ball Mills are widely used in the ceramic and mining industries, where the grinding process requires strict grain size control WEG developed an efficient solution for this applic