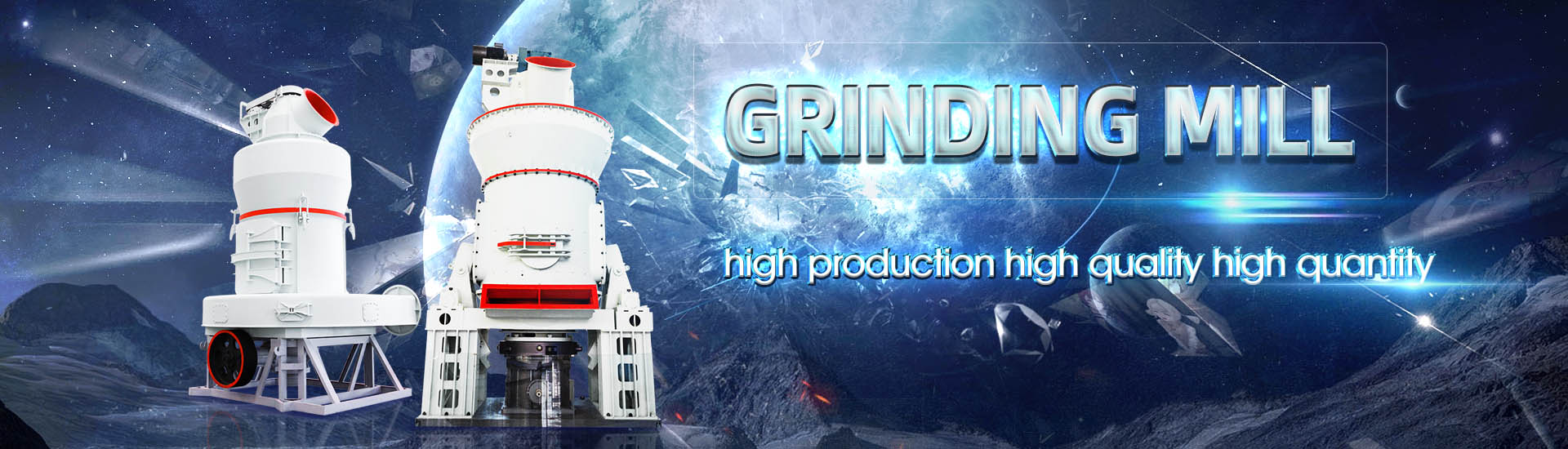
Ceramic ball mill, grinding media ratio
.jpg)
Ball Mill Success: A StepbyStep Guide to Choosing
2024年8月8日 Unlock the secrets to ball mill efficiency with our comprehensive guide on choosing the right grinding media Learn how material composition, size, shape, hardness, and cost impact your milling process and outcomes2023年4月23日 One of the most used tumbling mills is the ball mill This paper reviews different types of grinding media that have been developed and improved over the years and their properties Also(PDF) Grinding Media in Ball MillsA Review2023年10月27日 Grinding media play an important role in the comminution of mineral ores in these mills This work reviews the application of balls in mineral processing as a function of the A Review of the Grinding Media in Ball Mills for Mineral Processing Acceptable Way: measure the initial media level with a stick or mark somewhere visible Check the level periodically and fill when needed Alternative Way: passive maintenance: wait until How to Choose the Correct GRINDING MEDIA PCI Mag
.jpg)
PROCESSING OF CERAMIC POWDER USING HIGH ENERGY MILLING
kinetic energy of balls (grinding media) The milling balls are accelerated by the rotating rotor and collide with each other at a relative velocity up to 14 m/s A section view of the grinding unit is 2021年1月22日 Herein, an innovative approach for determining the grinding media system of ball mill based on grinding kinetics and linear superposition principle was proposed The An innovative approach for determining the grinding media 2022年11月1日 Recent research contends that ceramic balls significantly reduce energy consumption in industrial tumbling mills In this work, the binary media method is proposed to Can ceramic balls and steel balls be combined in an industrial 2024年1月18日 Research has shown that it saves 25% steel and 15% energy in consumption by adding a 25% volume ratio of pebbles instead of steel balls as the grinding media in the secondary grinding mill Ceramic balls are usually A Comparison of the FineGrinding Performance
CFB石灰石脱硫剂制备——磨机公众号12.8 推送案例(8)51.jpg)
The first attempt of applying ceramic balls in industrial tumbling
2022年4月1日 In this work, the binary media method is proposed to enhance ceramic ball grinding performance Specifically, when feed ore hardness is high and the ceramic ball 2024年1月31日 This paper introduces a novel method of combining media primarily using ceramic balls supplemented with an appropriate proportion of steel balls Three grinding media approaches, including the utilization of steel balls, Enhancing the Grinding Efficiency of a Magnetite 2023年11月24日 Although there are several types of grinding media, which include inert grinding media such as ceramic, zirconia, agate, and glass, this section is going to focus on cast iron and steel grinding media, together with their applicability in ball millsGrinding Media in Ball Mills for Mineral Processing2022年11月1日 Steel balls / Ceramic balls; Mass ratio Volume ratio Ball filling; 2:8: 1:87: 44%: An innovative approach for determining the grinding media system of ball mill based on grinding kinetics and linear superposition principle Powder Technol, 378 (2021), pp 172181Can ceramic balls and steel balls be combined in an
.jpg)
Milling Media: Factors for choosing milling media for
2020年11月2日 Agate milling media and agate planetary ball mill jars have been used in fields such as ceramics, electronics, light industry, paint, ink, medicine, food, geology, mining, chemical engineering MSE Supplies agate milling minerals Review A Review of the Grinding Media in Ball Mills for Mineral Processing Nyasha Matsanga 1, * , Willie Nheta 1 and Ngonidzashe Chimwani 2 1 2 * Mineral Processing and Technology Research Centre, Department of Metallurgy, University of Johannesburg, Doornfontein Campus, P O Box 17911, Johannesburg 2028, South Africa; Grinding Media in Ball MillsA Review Academia2022年4月1日 Compared with steel ball medium, ceramic ball medium has characteristics of good wear resistance, high hardness and low density, and thus can significantly reduce the consumption of grinding power and grinding media when applied in stirred mills [2,3] Moreover, ceramic ball medium can improve the flotation performance of nonferrous and noble The first attempt of applying ceramic balls in industrial tumbling mill 2016年1月1日 The performance of grinding media in a ball mill is also measured in terms of its wear rate Abrasive ores such as gold and copper produce high wear rates of about 120µm/hr [74] A comparison of wear rates of ball mill grinding media
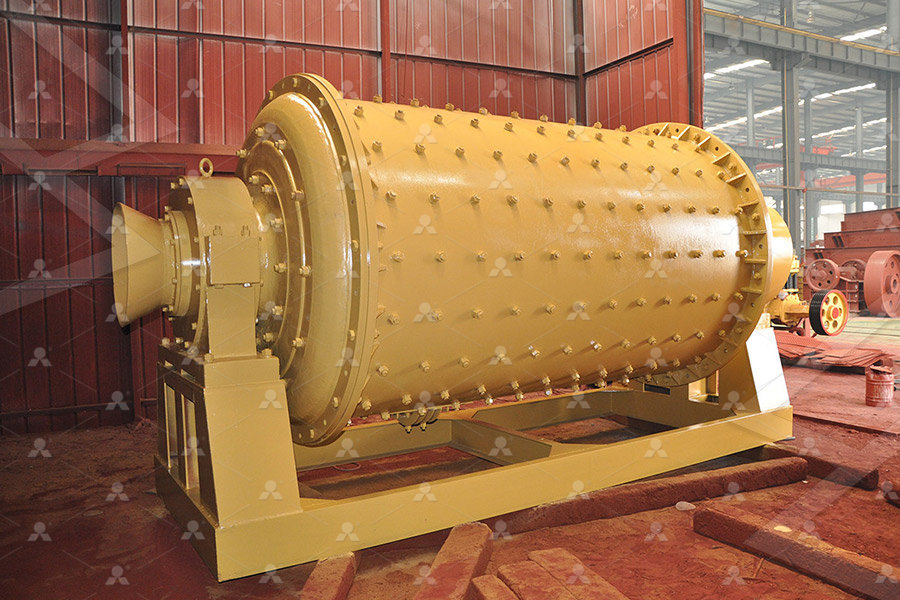
Zirconia Ceramic Grinding Media: Sintered Balls and Beads
Select larger sizes up to ∅70 mm for ball mills or use them to substitute high alumina grinding media Superior priceperformance ratio to other lowmedium density grinding medias MSE Supplies carries highquality ceramic grinding media to suit every application Find the right grinding media for your goals today, 2013年8月3日 In Grinding, selecting (calculate) the correct or optimum ball size that allows for the best and optimum/ideal or target grind size to be achieved by your ball mill is an important thing for a Mineral Processing Engineer AKA Metallurgist to do Often, the ball used in ball mills is oversize “just in case” Well, this safety factor can cost you much in recovery and/or mill liner Calculate and Select Ball Mill Ball Size for Optimum Grinding 2024年1月18日 Moreover, two models were developed to use ceramic balls instead of cylpebs as finegrinding media in the wet tumbling mill based on the ball size and the ratio of the total mass of cylpebs Cylpebs can be replaced by ceramic balls with 116–175 times the diameter of cylpebs, taking up only 76%–83% of the total weight of cylpebsA Comparison of the FineGrinding Performance between Ceramic grinding media are also suited for use in processes where mixing and dispersing effects play an important role In the majority of these grinding processes, steatite and alumina are the most common ceramic materials used for grinding balls and linings CeramTec generally manufactures its grinding balls and linings with steatiteCeramic Grinding Beads, Balls and Linings
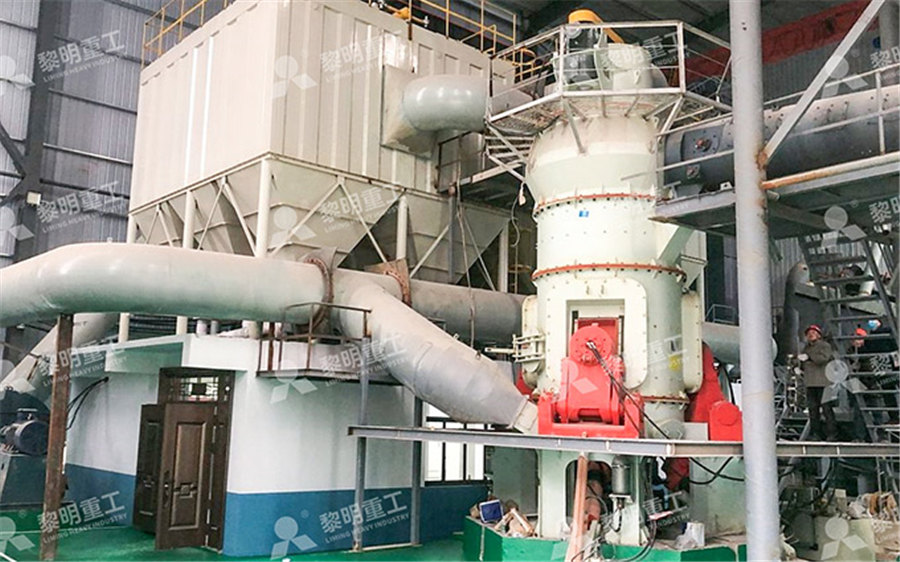
Energy conservation and consumption reduction in grinding
through ceramic media stirring mill: material ball ratio of 06, 3:2:5 media ratio stirring mill replacing twostage ball grinding provides a feasible solution for energy 2021年1月22日 Herein, an innovative approach for determining the grinding media system of ball mill based on grinding kinetics and linear superposition principle was proposed The optimal media ball size of −2 + 045 mm, −045 + 015 mm, and − 015 mm feeding samples were 40 mm, 30 mm, and 30 mm, respectivelyAn innovative approach for determining the grinding media 2024年1月31日 As can be seen from Table 7, the −0075 mm yield of the ceramic ball grinding (mill #7) product is the same as the −0075 mm yield of the steel ball grinding Media Filling Ratio: 40%: Grinding Time: 2 min, 4 min, 6 Enhancing the Grinding Efficiency of a Magnetite 2023年4月24日 Review Grinding Media in Ball MillsA Review Nyasha Matsanga 1,*, Willie Nheta 1 and Ngonidzashe Chimwani 2 1 Mineral Processing and Technology Research Centre, Department of Metallurgy, University of Johannesburg, POBOX 17011, Doornfontein 2028, South Africa; 2 Department of Mining Engineering, Florida Campus, Grinding Media in Ball MillsA Review Preprints
.jpg)
An innovative approach for determining the grinding media
2021年1月22日 Grinding operation is used extensively in the industry of beneficiation, metallurgy, chemical engineering, and electric power Assisted by the impact and abrasion between media (steel ball, steel rod, gravel, ceramic ball) and ore, the grinding operation reduces the particle size in the mill [[1], [2], [3]]To produce the qualified size and high liberation of Magotteaux Mining Grinding Media One Cast High Chrome is the best option when the situation requires optimal wear resistance against abrasion and corrosion Available in diameters of 054 inches, Magotteaux Mining Grinding Media One Cast High Chrome is appropriate for ball mills and tower mills, along with wet and dry ore applicationsGrinding Media MagotteauxThe benefits of Magotteaux ceramic grinding beads Magotteaux grinding media ceramic have an excellent price and performance ratio and help reduce wear and milling time due to the high density of the balls They also minimize the contamination of the raw materials and provide a stable process over timeCeramic grinding beads MagotteauxGrinding Media Grinding Balls Metallic Grinding Media NonMetallic Grinding Media Grinding media, (internally agitated ball mills) and DMQX horizontal media mills, Zirconium Oxide Balls (95% ZrO2) are the strongest, best wearing ceramic media for metalfree, pharmaceutical and food processing grinding These balls have a white, Grinding Media Union Process
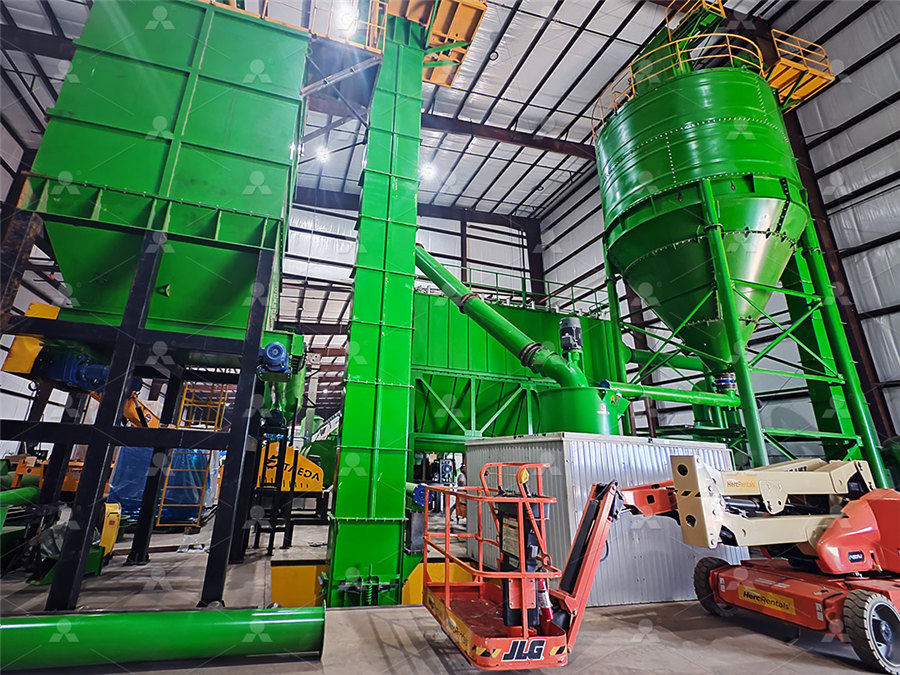
Energy conservation and consumption reduction in grinding
2023年11月1日 The research of ceramic media stirring mill instead of ball mill is beneficial to solve the problems of production efficiency and quality of the medium ratio (10 mm: 15 mm: 20 mm) was 3:2:5, while the material ball ratio, grinding concentration and stirring velocity were separately 06, 50% and 110 rpm The Magnesia Stabilized Zirconia grinding media mills twice as fast as equivalentlysized alumina media with only 1/2 the media weight loss US Stoneware has assembled the most extensive collection of specialty ceramic grinding medias anywhere The following chart identifies some of the more frequently requested materials Name Zirconia Grinding Media U S Stoneware2021年11月1日 The initial ratio of grading ball was 30 mm: 40 mm: 50 mm: 70 mm = 30: 20: 30: 20 It should be noted that the diameter of instrumented grinding media is 70 mm Rotation speed of cement ball mill was set to 80% The grinding time was 10 min for each experiment The grinding experiments were carried out according to Table 1Assessing load in ball mill using instrumented grinding media2022年1月1日 A pilotscale grinding technology of ceramic medium stirred mill was proposed in this study Based on the specific productivity and grinding efficiency, the appropriate grinding parameters were ascertained as follows: material ball ratio of 07, ceramic ball medium size ratio (10 mm: 15 mm: 20 mm = 3:2:5), stirring speed of 110 rpm, grinding concentration of 50%, Highefficiency and energyconservation grinding technology using
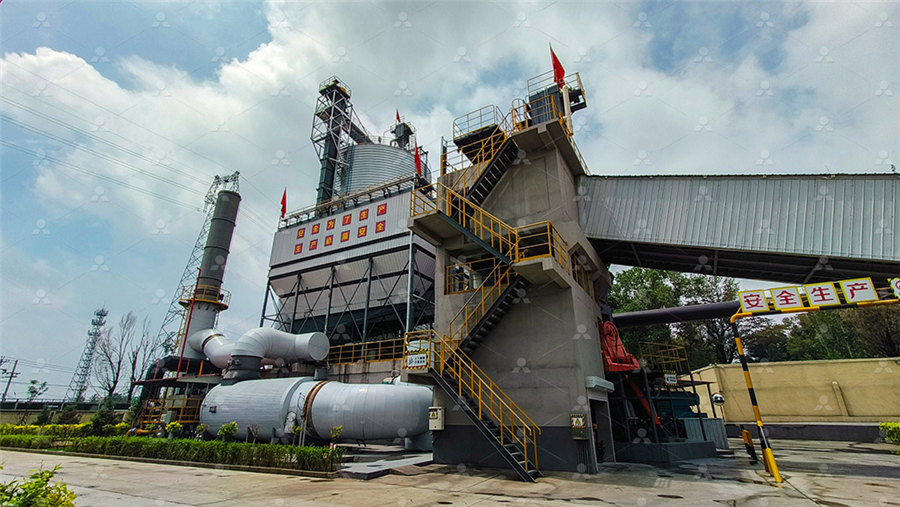
China Ceramic Grinding Media Manufacturers
Alumina Grinding Ball Alumina grinding ball is one ideal ball mill grinding media, it can keep the purity and improve the stability of grinded materialsIt is widely used in the grinding process of ceramics, electronic materials, cosmetics, food Lameck (2005) –The effects of grinding media shapes on ball mill performance (MSc thesis –University of Wits) Balls Worn Cylpebs balls Lameck’s work indicated that: • Higher torque (power draw) can be achieved with increased packing efficiency –particularly for worn ball media • At lower mill speeds, the cylpebs and new media drawRethinking Grinding Efficiency in Ball Mills2024年8月1日 Best Practices for Using Ball Mill Media When using ball mill media for black powder production, follow these best practices: Selection of Media: Choose the right type of media based on the material being ground Steel, ceramic, and lead media each have unique properties suitable for different applicationsEffective Ball Mill Media for Superior Black Powder Production2023年11月1日 This paper demonstrates the feasibility of using a ceramic medium stirring mill to reduce the energy consumption of grinding operations through an industrial verification experiment Compared with the original twostage ball milling process, the cost of grinding power consumption is significantly reduced by about 5016%, which provides a reference for the Energy conservation and consumption reduction in grinding
.jpg)
Grinding Media in Ball MillsA Review ResearchGate
grinding media system by ascertaining optimal media size, media proportion and material ball ratio According to Kelsall et al [17] changes in media (quantity, density, size, shape) change the Grinding Media Dan Taylor via Clayart: You need grinding media in a ballmill that has some tooth, like pebbles of porcelain Glass or steel is too smooth I use high fire, very dense porcelain balls of various sizes Industry says you should fill your mill jar half full of balls, half of which (by weight) are the largest, and two other sizes Ball Milling Glaze Mixing Preparation Glazy Ceramics WikiThere are three types of grinding media that are commonly used in ball mills: • steel and other metal balls; • metal cylindrical bodies called cylpebs; • ceramic balls with regular or high density Steel and other metal balls are the most frequently used grinding media with sizes of the balls ranging from 10 to 150 mm in diameter [30]Grinding in Ball Mills: Modeling and Process Control Sciendo2023年11月24日 Although there are several types of grinding media, which include inert grinding media such as ceramic, zirconia, agate, and glass, this section is going to focus on cast iron and steel grinding media, together with their applicability in ball millsGrinding Media in Ball Mills for Mineral Processing
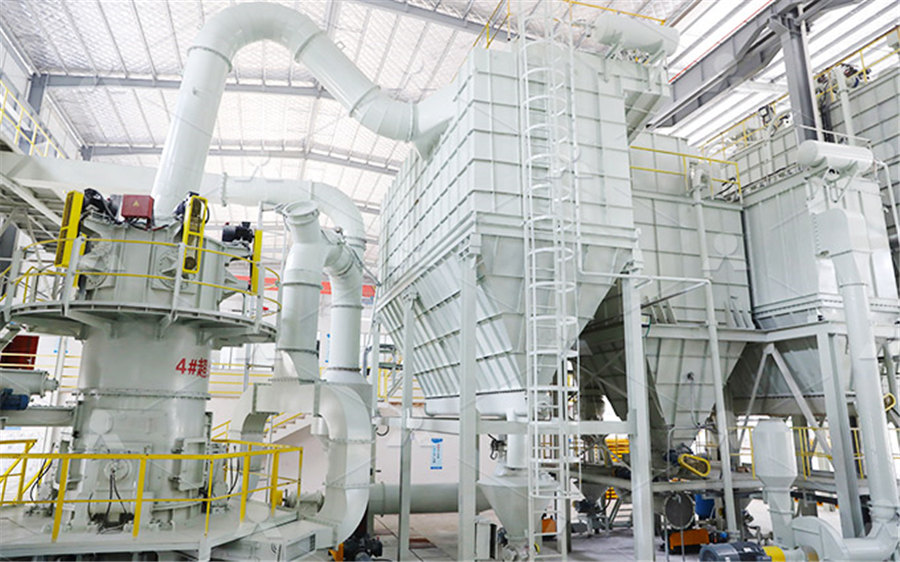
Can ceramic balls and steel balls be combined in an
2022年11月1日 Steel balls / Ceramic balls; Mass ratio Volume ratio Ball filling; 2:8: 1:87: 44%: An innovative approach for determining the grinding media system of ball mill based on grinding kinetics and linear superposition principle Powder Technol, 378 (2021), pp 1721812020年11月2日 Agate milling media and agate planetary ball mill jars have been used in fields such as ceramics, electronics, light industry, paint, ink, medicine, food, geology, mining, chemical engineering MSE Supplies agate milling Milling Media: Factors for choosing milling media for minerals Review A Review of the Grinding Media in Ball Mills for Mineral Processing Nyasha Matsanga 1, * , Willie Nheta 1 and Ngonidzashe Chimwani 2 1 2 * Mineral Processing and Technology Research Centre, Department of Metallurgy, University of Johannesburg, Doornfontein Campus, P O Box 17911, Johannesburg 2028, South Africa; Grinding Media in Ball MillsA Review Academia2022年4月1日 Compared with steel ball medium, ceramic ball medium has characteristics of good wear resistance, high hardness and low density, and thus can significantly reduce the consumption of grinding power and grinding media when applied in stirred mills [2,3] Moreover, ceramic ball medium can improve the flotation performance of nonferrous and noble The first attempt of applying ceramic balls in industrial tumbling mill
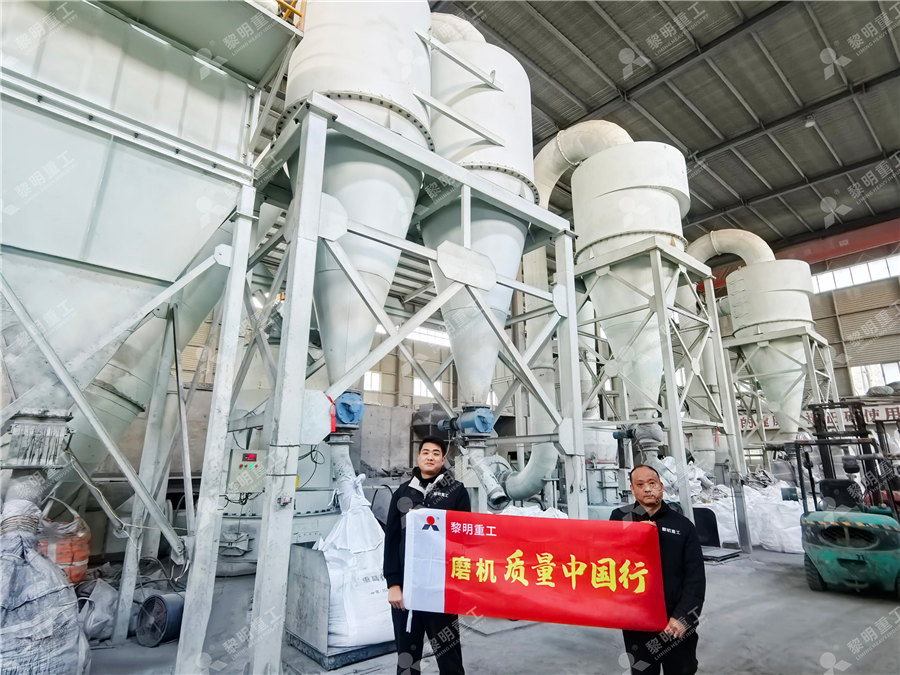
A comparison of wear rates of ball mill grinding media
2016年1月1日 The performance of grinding media in a ball mill is also measured in terms of its wear rate Abrasive ores such as gold and copper produce high wear rates of about 120µm/hr [74] Select larger sizes up to ∅70 mm for ball mills or use them to substitute high alumina grinding media Superior priceperformance ratio to other lowmedium density grinding medias MSE Supplies carries highquality ceramic grinding media to suit every application Find the right grinding media for your goals today, Zirconia Ceramic Grinding Media: Sintered Balls and Beads2013年8月3日 In Grinding, selecting (calculate) the correct or optimum ball size that allows for the best and optimum/ideal or target grind size to be achieved by your ball mill is an important thing for a Mineral Processing Engineer AKA Metallurgist to do Often, the ball used in ball mills is oversize “just in case” Well, this safety factor can cost you much in recovery and/or mill liner Calculate and Select Ball Mill Ball Size for Optimum Grinding 2024年1月18日 Moreover, two models were developed to use ceramic balls instead of cylpebs as finegrinding media in the wet tumbling mill based on the ball size and the ratio of the total mass of cylpebs Cylpebs can be replaced by ceramic balls with 116–175 times the diameter of cylpebs, taking up only 76%–83% of the total weight of cylpebsA Comparison of the FineGrinding Performance between
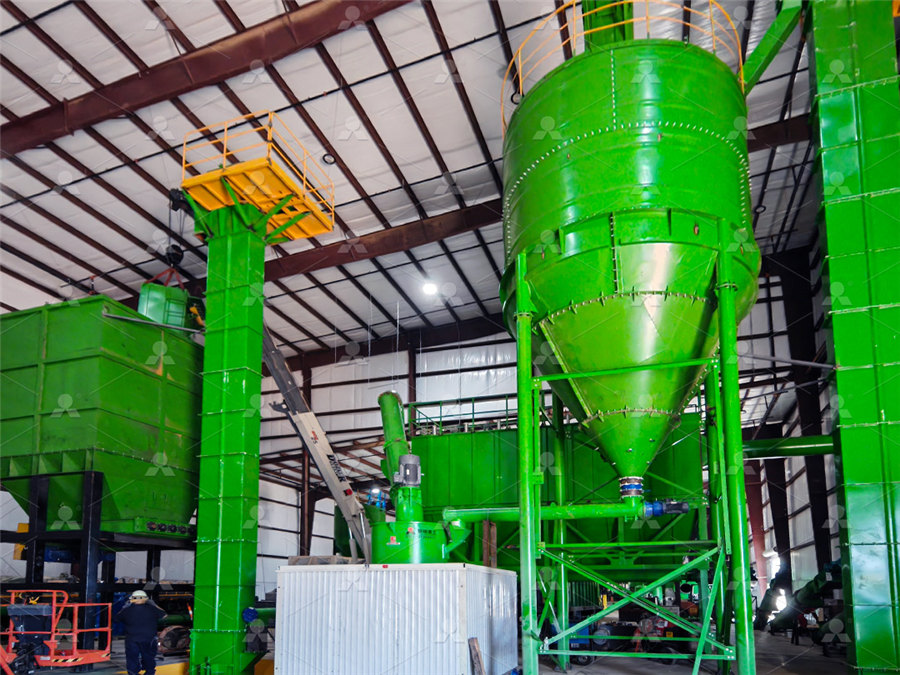
Ceramic Grinding Beads, Balls and Linings
Ceramic grinding media are also suited for use in processes where mixing and dispersing effects play an important role In the majority of these grinding processes, steatite and alumina are the most common ceramic materials used for grinding balls and linings CeramTec generally manufactures its grinding balls and linings with steatite