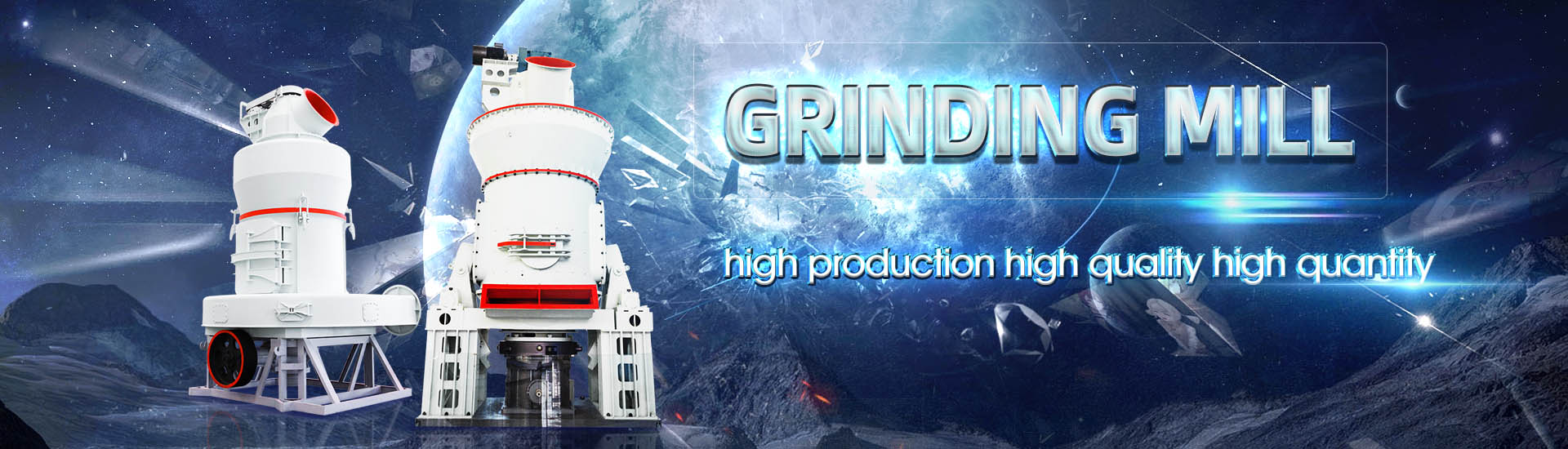
Ore powder mill should have reports
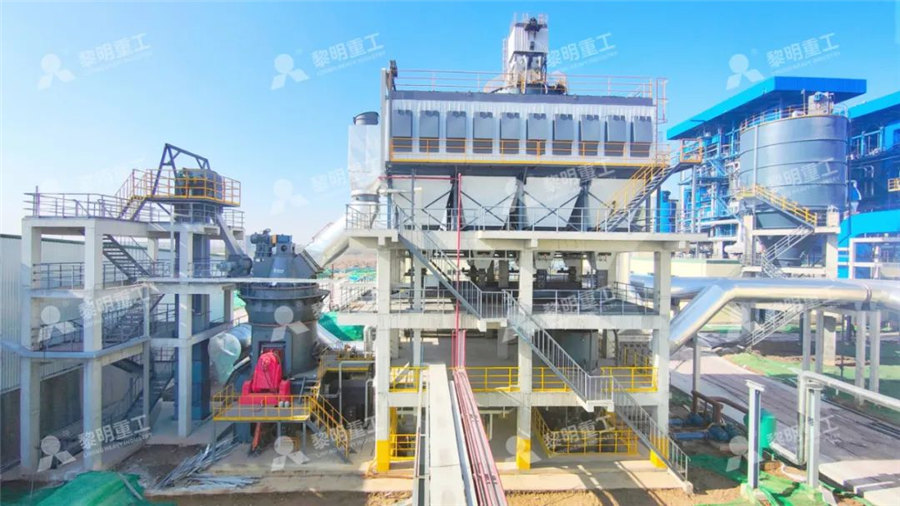
A Review of the Grinding Media in Ball Mills for Mineral Processing
2023年10月27日 Grinding media play an important role in the comminution of mineral ores in these mills This work reviews the application of balls in mineral processing as a function of the materials used to manufacture them and the mass loss, as influenced by three basic wear 2023年11月24日 Good grinding media should have high hardness, fracture toughness, wear resistance and corrosion resistance, but at the same time, should have adequate ductility to Grinding Media in Ball Mills for Mineral Processing2014年6月1日 Automation in mineralogical (and chemical) laboratories from sample preparation to analysis has been the baseline for these improvements This paper will highlight key Ore characterization, process mineralogy and lab automation a 2015年8月3日 The report provides an overview of all types of methods practiced in mineral processing These methods are adopted one after the other in sequence and also depending upon the ores processed No(PDF) Overview of Mineral Processing Methods
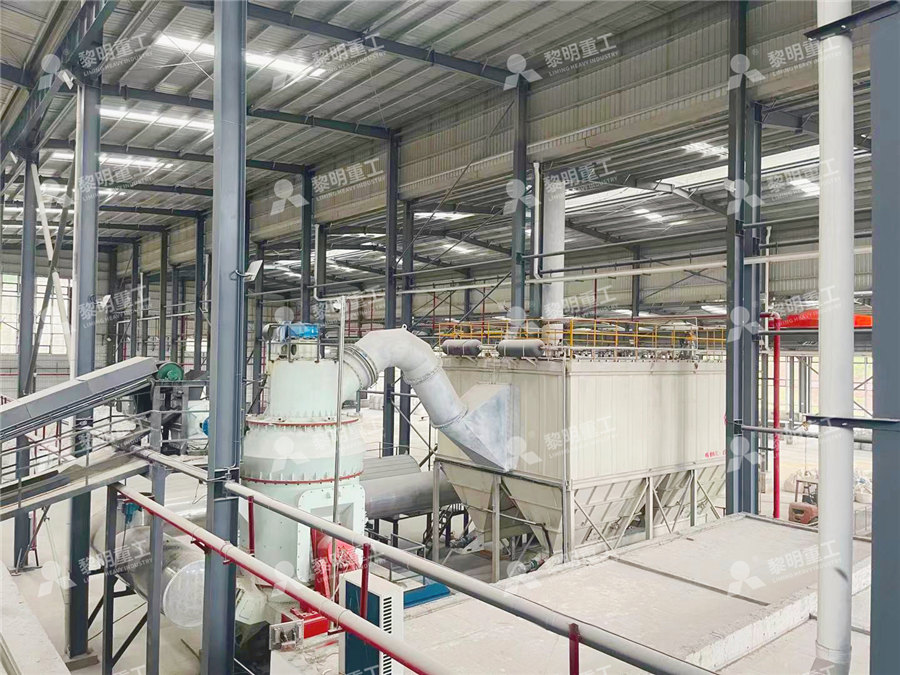
Grinding in Ball Mills: Modeling and Process Control ResearchGate
2012年6月1日 Ball mills can grind a wide range of materials, including metals, ceramics, and polymers, and can operate on a variety of scales, from laboratory to industrial (Monov et al 2023年4月24日 Various grinding media are used for milling in ball mills to achieve sufficient particle size reduction and mineral liberation for downstream separation processes Particle Grinding Media in Ball MillsA Review Preprints2020年12月3日 This study is conducted with the aim of investigating the efficiency of open and closedcircuit molybdenite ore comminution processes (primary and secondary mill, A process mineralogy approach to study the efficiency of milling Mill grinding efficiency is measured at the same time as CSE through circuit samplingFunctional performance analysis combines CSE and mill grinding efficiency to provide a measureable, Functional Performance of Ball Milling Circuits A Plant AusIMM
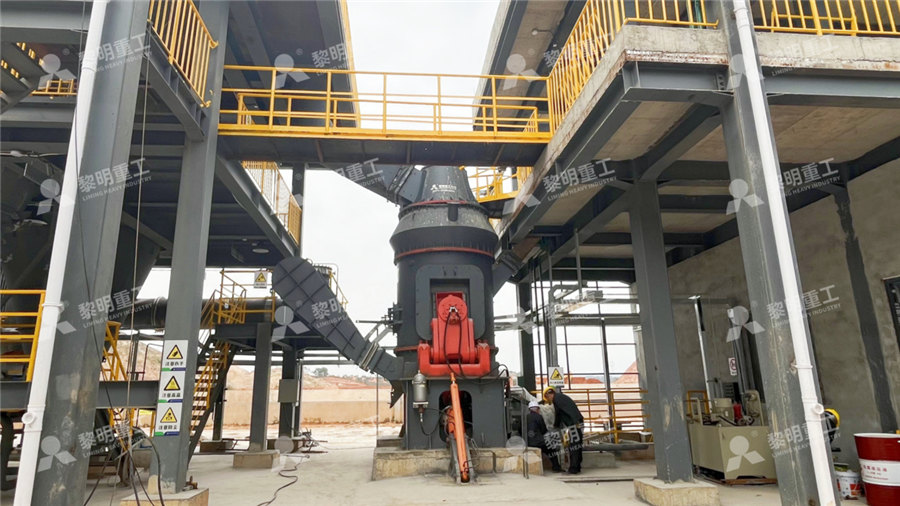
A Review of the Grinding Media in Ball Mills for Mineral
2023年10月27日 Grinding media play an important role in the comminution of mineral ores in these mills This work reviews the application of balls in mineral processing as a function of the materials used2014年10月15日 Dualenergy Xray transmission has been used to sort ore from different mines, and an analysis identifying the economic impact of these results is presented Significant Development of ore sorting and its impact on mineral processing 2023年10月27日 The ball mill is a rotating cylindrical vessel with grinding media inside, which is responsible for breaking the ore particles Grinding media play an important role in the comminution of mineral ores in these mills This work reviews the application of balls in mineral processing as a function of the materials used to manufacture them and the mass loss, as A Review of the Grinding Media in Ball Mills for Mineral Processing 2013年8月3日 In Grinding, selecting (calculate) the correct or optimum ball size that allows for the best and optimum/ideal or target grind size to be achieved by your ball mill is an important thing for a Mineral Processing Engineer AKA Calculate and Select Ball Mill Ball Size for Optimum
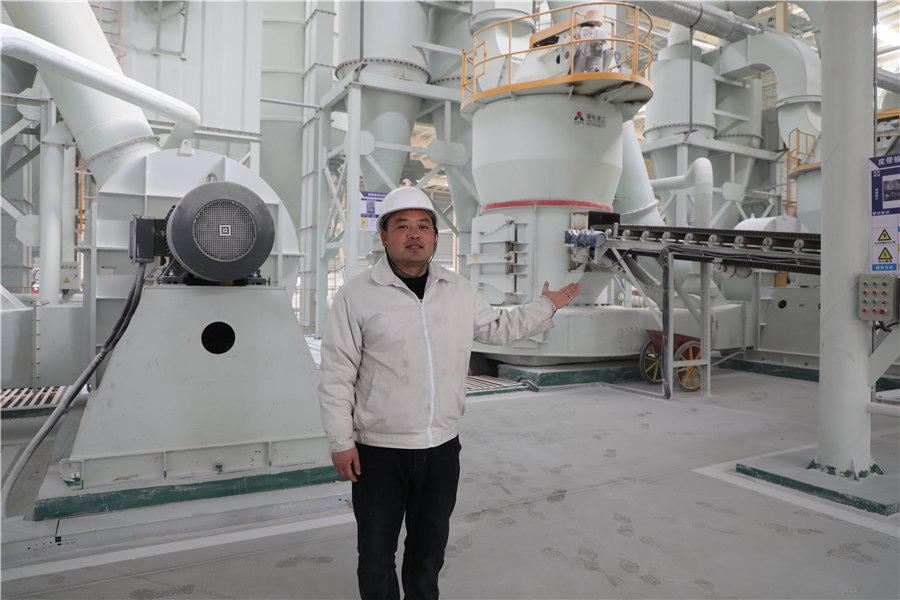
Laserassisted reduction of iron ore using aluminum powder
2023年3月15日 This study reports on the laserassisted reduction of iron ore waste using Al powder as a reducing agent Due to climate change and the global warming situation, it has become of paramount PDF On Jan 1, 2013, Jim Everett published Planning an Iron Ore Mine: From Exploration Data to Informed Mining Decisions Find, read and cite all the research you need on ResearchGate(PDF) Planning an Iron Ore Mine: From Exploration Data to able use of mill scale to mitigate the risk of groundwater and soil contamination as well as to recycle the iron values into mainstream industrial applications Several researchers have explored the possibility of utilizing mill scale in the iron ore sintering process as a partial replacement for iron ores [1, 12, 17–20]Evaluation of Quality Parameters and Mineralogy of Iron Ore HGM100A professional ultra fine powder grinder is the new type mining equipment for making micro powders, fine powders, which is widely applied in the industries of metallurgy, mining, chemistry, cement, construction, refractory materials, ceramics, and so on Final product fineness:3002500meshCapacity:0245t/hultra fine powder grinding mill Shanghai Clirik Machinery Co,
.jpg)
Towards waterless operations from mine to mill ScienceDirect
2022年9月1日 A conceptual diagram with considerations for selecting minetomill ore beneficiation technologies with lowwateruse or waterless focus 2 Since the powder factor in the model blasts was only 022 to 029 kg/m 3, Several reports have indicated that microwaveassisted grinding can improve the grindability of various The ball mill measured 0305 m in diameter and 0127 in length It was driven by an asynchronous motor rated with power close to 10 kW A schematic of the experimental laboratory ball mill used is shown in Fig 3 22 Sample preparation The coppercobalt ore used in the actual test work was obtained from the feed to theDetermination and scaleup of the milling parameters of a high 2021年11月3日 The amount of phosphate rock powder used as base fertilizer should be determined by the content of phosphate rock powder Reasonable and correct use of phosphate rock powder can not only increase the yield of crops and improve the quality of crops but also make the grains of cereal crops full, such as promoting the flowering and fruiting of cotton, Phosphate Mineral Powder Grinding Mill SBM Ultrafine Powder 2019年11月30日 There is a required ON and OFF grade split, that is, of the total ore tonnes produced or mined, 30% should be ON grade ore and 70% should be OFF grade ore, although it can change depending on the requirements of the iron ore mine for a certain period Table 1 indicates the grades of the ore that is mined in detail including contaminantsMine Planning and Optimisation Techniques Applied in an Iron Ore
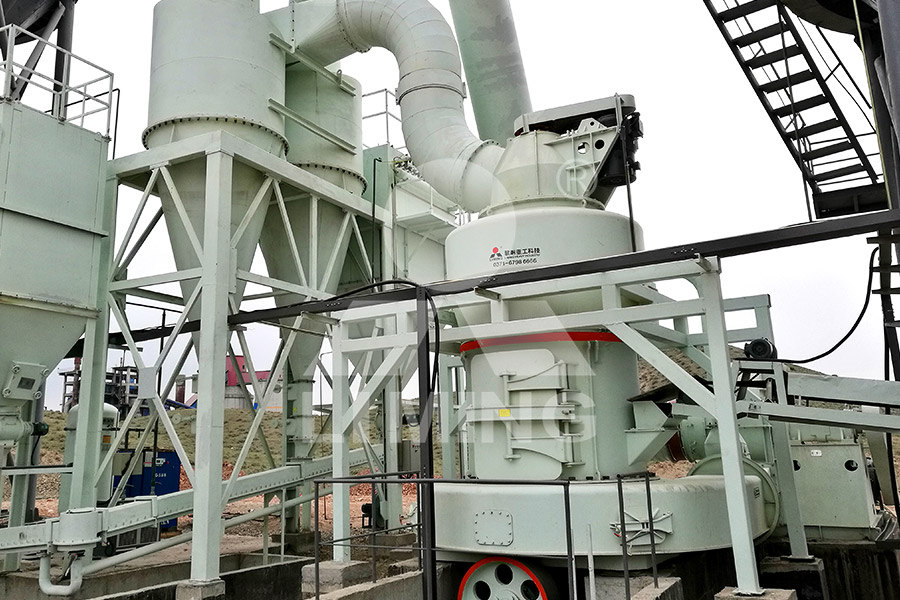
Compare and Understand Rod/Ball/Impact
2015年11月23日 Relation of Bond ball mill work index and rod mill work index The Bond rod mill and ball mill work indices are the most similar in size classes, both being fed material crushed to “relatively fine” sizes Both test are also 2022年5月23日 Grinding experiments were conducted in a laboratoryscale stirred mill on a lowgrade PGE bearing chromite ore HighPressure Grinding Rolls (HPGR) product of −1 mm was used as feed material to (PDF) Modeling and application of stirred mill for the coarse onto a discharge belt which conveys the ore to one of three coarse ore stockpiles ahead of the mill Both crushers have a hydraulic rock hammer to break oversize material in the crusher pocket For crusher operation, the apron feeder speed determines the throughput while the closesidesetting can be changed by raising orThe Importance of Primary Crushing in Mill Feed Size OptimizationPROJECT REPORT – PHASE I on ANALYSIS AND DESIGN OF BALL MILL FOUNDATION FOR TATA IRON ORE PELLET PLANT AT JAMSHEDPUR Submitted in partial fulfillment for the award of the degree of BACHELOR OF TECHNOLOGY in CIVIL ENGINEERING by MOHD ADEEL ANKIT GOYAL VIVEK BABU Under the (DOC) PROJECT REPORT – PHASE I ANALYSIS AND DESIGN OF BALL MILL
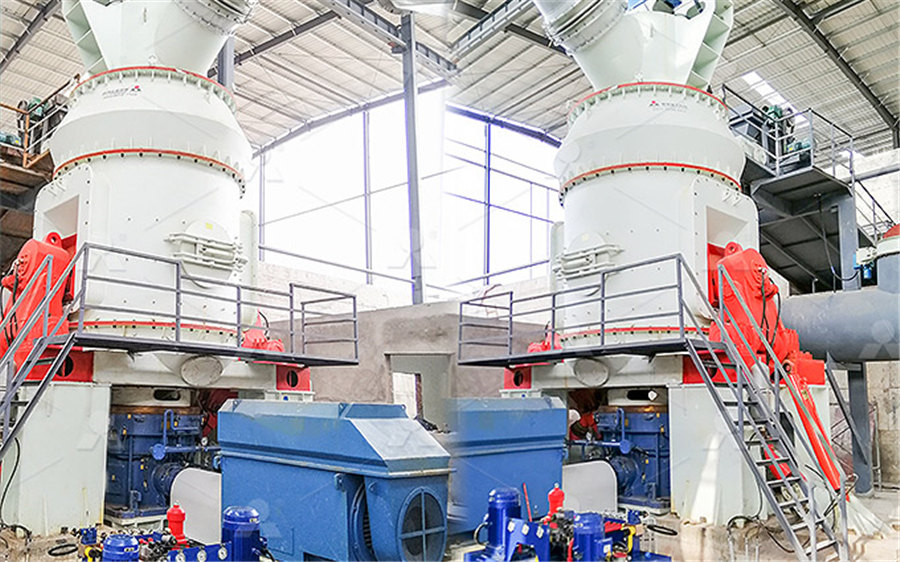
Morphology and Properties of Red Iron Ore Powder ResearchGate
2018年7月1日 Reduction of hematite pellets using H2CO mixtures with a wide range of H2/CO by molar (1:0, 3:1, 1:1, 1:3, and 0:1) at different reducing temperatures (1073, 1173, and 1273 K) was conducted in a Find your ore mill easily amongst the 42 products from the leading brands (Fritsch GmbH, Retsch, Eriez, ) on DirectIndustry, (endothermic) The powder is fed at subsonic speeds (approximately 50 m/s) into the Compare this product Remove from comparison tool See the other products Dec Group rotor mill HCP horizontal for ore ContactOre mill, Ore grinding mill All industrial manufacturers2022年12月15日 In the present study, size reduction experiments were performed on HighPressure Grinding Rolls (HPGR), ball mill and stirred mill of PGE bearing chromite oreSize reduction performance evaluation of HPGR/ball mill and 2023年10月17日 Factors for choosing a suitable ore powder grinding mill 1 Raw material characteristics: Different raw materials have different hardness, humidity and grinding and crushing properties, and the corresponding ore powder grinding mill needs to be selected to meet the processing requirements 2 Production capacity: Determine the required processing How to choose a suitable ore powder grinding mill?
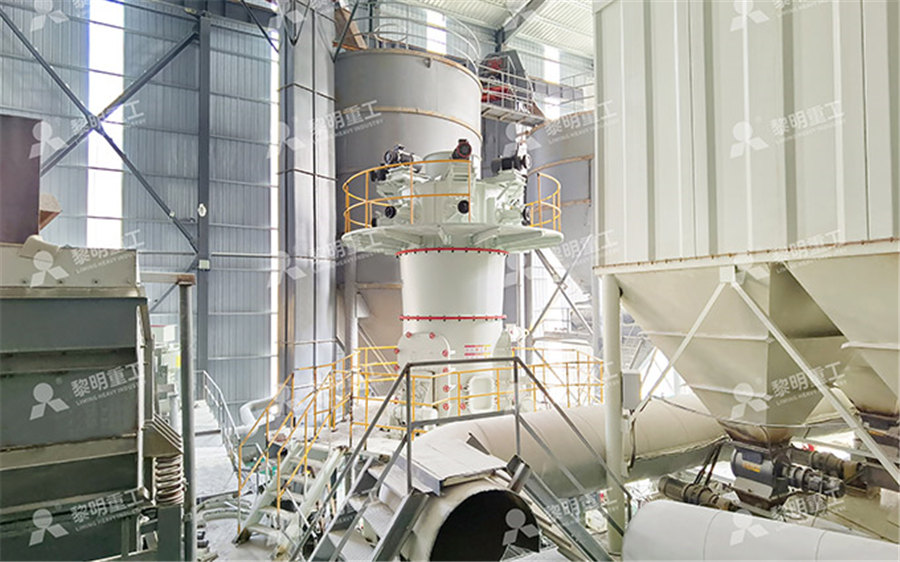
SBM Ore Ultrafine Grinding Mill
HGM ultrafine grinding mill can process nonmetallic ores with Mohs hardness less than 7 The equipment has stable operation, simple operation, long service life, low carbon and environmental protection There are 5 models of HGM ultrafine grinding mill, 2005年9月19日 Reconciliation at large iron ore operations is a complex and timeconsuming process Often the volume of data and the large range of different stakeholders makes the process almost impossibleIron Ore Mine Reconciliation—A Case Study From Sishen Iron Ore 2015年7月1日 This paper presents a fundamental study on the carbothermic reduction of chromite ore with the addition of mill scale, which forms the basis for designing an alloying precursor, “chromite ore Thermal Analysis Study on the Carbothermic 2022年11月24日 In order to reduce the sintering allocation scheme and lower the cost of allocation, two semilignite ores with similar properties and large price differences were selected for blending to achieve the purpose of Sintering Properties and Regression Analysis of
.jpg)
Advancements in ore powder production process equipment:
Here, we delve into the key components and technologies that make up the modern ore powder production process Key Components of Ore Powder Production Equipment: 1 Crushers The initial step in ore powder production is the reduction of ore size, which is accomplished by crushers Jaw crushers, cone crushers, and impact crushers are commonly 2016年3月30日 In book: Encyclopedia of Iron, Steel, and Their Alloys (pppp 10821108) Chapter: i) Direct Reduced Iron: Production; Publisher: CRC Press, Taylor and Francis Group, New York(PDF) i) Direct Reduced Iron: Production ResearchGateprocess stages, the ore is exposed to a number of heat cycles, which lead to material oxidation35 Therefore, the pellets and the iron ore fines mainly consist of hematite (Fe 2O 3) by the end of their manufacturing process In this study, iron ore powder fines, collected from the iron ore pelletization process, with a size range between 10 Laserassisted reduction of iron ore using aluminum powder DiVA2022年7月30日 Study on the Basic Characteristics of Iron Ore Powder with Different Particle Sizes Zezheng Li 1,2,3,4,5, Yifan Li 1,2,3,4,5, phase strengths of several iron ore powders commonly used in a steel mill with different particle sizes The experiment accurately analyzed the basic characteristic data of iron oreStudy on the Basic Characteristics of Iron Ore Powder with
.jpg)
Grinding Media in Ball Mills for Mineral Processing
2023年11月24日 Sometimes, the smaller balls do not have sufficient impact energy to break an ore particle; therefore, both media sizes are vital An optimal ball size range should provide sufficient energy to break coarse ore particles, but at the same time should not produce unnecessary ultrafine particlesIn the process of production and sales, micro powder grinding mill will encounter some common problems, how to improve the production efficiency of micro powder grinding mill, common problems in the use process and maintenance of the machine, etc, the daily maintenance of micro powder grinding mill is An important recurring task, which should be closely coordinated micro powder grinding mill ore deep processing technology2022年12月1日 The physical properties of iron ore concentrate, such as the morphology of particles, specific surface area, and particle size distribution, have a significant effect on the quality of green pellets [16], [17], [18] The grinding method and its associated parameters strongly affect the physical properties of the iron ore concentrateMechanism of magnetite iron ore concentrate morphology 2024年11月22日 Studies have demonstrated that IOT powder exhibits significant filling effects and pozzolanic reactivity For instance, UHPC containing 20 % IOT powder and 50 % IOTS achieves a remarkable compressive strength of 1456 MPa, with a concomitant reduction in the proportion of harmful pores (>100 nm) from 857 % to 609 % [38]Enhancing the properties of UHPC with recycled concrete powder
.jpg)
A Review of the Grinding Media in Ball Mills for Mineral Processing
2023年10月27日 The ball mill is a rotating cylindrical vessel with grinding media inside, which is responsible for breaking the ore particles Grinding media play an important role in the comminution of mineral ores in these mills This work reviews the application of balls in mineral processing as a function of the materials used to manufacture them and the mass loss, as 2013年8月3日 In Grinding, selecting (calculate) the correct or optimum ball size that allows for the best and optimum/ideal or target grind size to be achieved by your ball mill is an important thing for a Mineral Processing Engineer AKA Calculate and Select Ball Mill Ball Size for Optimum 2023年3月15日 This study reports on the laserassisted reduction of iron ore waste using Al powder as a reducing agent Due to climate change and the global warming situation, it has become of paramount Laserassisted reduction of iron ore using aluminum powderPDF On Jan 1, 2013, Jim Everett published Planning an Iron Ore Mine: From Exploration Data to Informed Mining Decisions Find, read and cite all the research you need on ResearchGate(PDF) Planning an Iron Ore Mine: From Exploration Data to
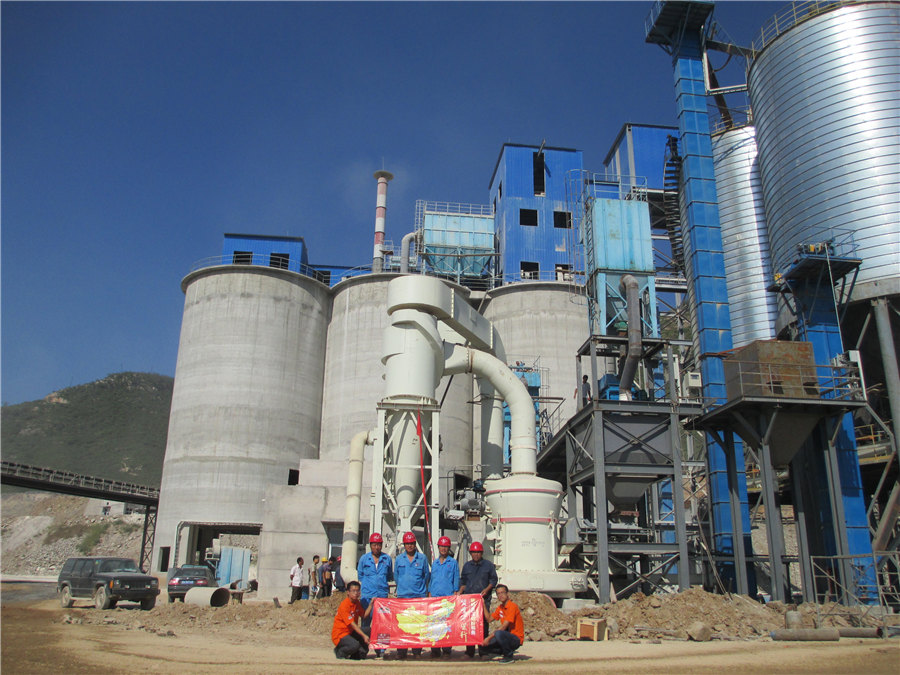
Evaluation of Quality Parameters and Mineralogy of Iron Ore
able use of mill scale to mitigate the risk of groundwater and soil contamination as well as to recycle the iron values into mainstream industrial applications Several researchers have explored the possibility of utilizing mill scale in the iron ore sintering process as a partial replacement for iron ores [1, 12, 17–20]HGM100A professional ultra fine powder grinder is the new type mining equipment for making micro powders, fine powders, which is widely applied in the industries of metallurgy, mining, chemistry, cement, construction, refractory materials, ceramics, and so on Final product fineness:3002500meshCapacity:0245t/hultra fine powder grinding mill Shanghai Clirik Machinery Co, 2022年9月1日 A conceptual diagram with considerations for selecting minetomill ore beneficiation technologies with lowwateruse or waterless focus 2 Since the powder factor in the model blasts was only 022 to 029 kg/m 3, Several reports have indicated that microwaveassisted grinding can improve the grindability of various Towards waterless operations from mine to mill ScienceDirectThe ball mill measured 0305 m in diameter and 0127 in length It was driven by an asynchronous motor rated with power close to 10 kW A schematic of the experimental laboratory ball mill used is shown in Fig 3 22 Sample preparation The coppercobalt ore used in the actual test work was obtained from the feed to theDetermination and scaleup of the milling parameters of a high
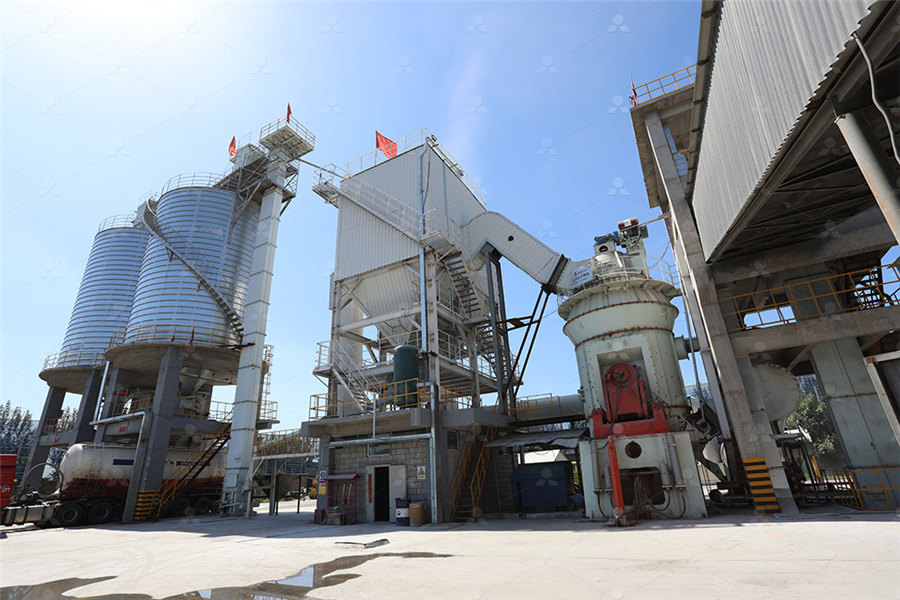
Phosphate Mineral Powder Grinding Mill SBM Ultrafine Powder
2021年11月3日 The amount of phosphate rock powder used as base fertilizer should be determined by the content of phosphate rock powder Reasonable and correct use of phosphate rock powder can not only increase the yield of crops and improve the quality of crops but also make the grains of cereal crops full, such as promoting the flowering and fruiting of cotton, 2019年11月30日 There is a required ON and OFF grade split, that is, of the total ore tonnes produced or mined, 30% should be ON grade ore and 70% should be OFF grade ore, although it can change depending on the requirements of the iron ore mine for a certain period Table 1 indicates the grades of the ore that is mined in detail including contaminantsMine Planning and Optimisation Techniques Applied in an Iron Ore