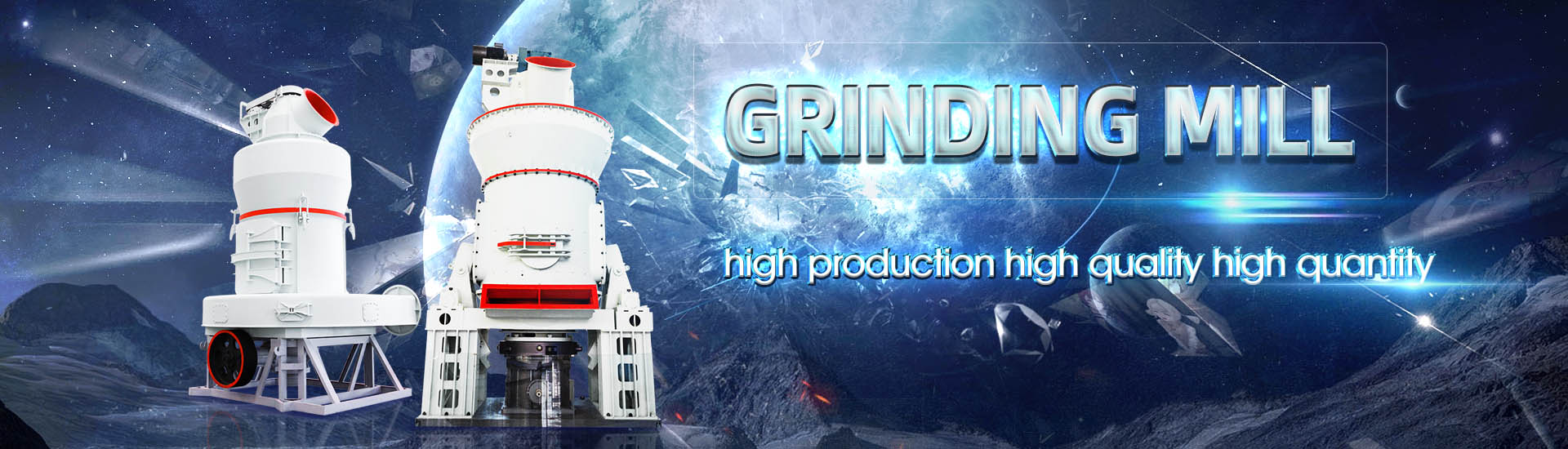
Limestone gypsum desulfurization equipment
.jpg)
Flue Gas Desulfurization (FGD) Plants Mitsubishi Power
The flue gas desulfurization (FGD) plant removes sulfur dioxides (SO 2) from flue gas produced by boilers, furnaces, and other sources Mitsubishi Power effectively contributes to the prevention of air pollution through its wet limestonegypsum FGD process and seawater FGD process, 2022年1月15日 Cui et al proposed a combination of limestonegypsum wet flue gas Summary of research progress on industrial flue gas Wet scrubbers are used in utilities, paper mills, and chemical plants to remove sulfur dioxide Lime / Limestone Wet Scrubbing System for Flue Gas DesulfurizationWet flue gas desulfurization plants from Steuler Equipment Engineering work using the limestone/gypsum process, as has been standard practice in largescale power stations for decades It is probably the most effective wet DeSO x plants/ flue gas desulfurization plants Steuler
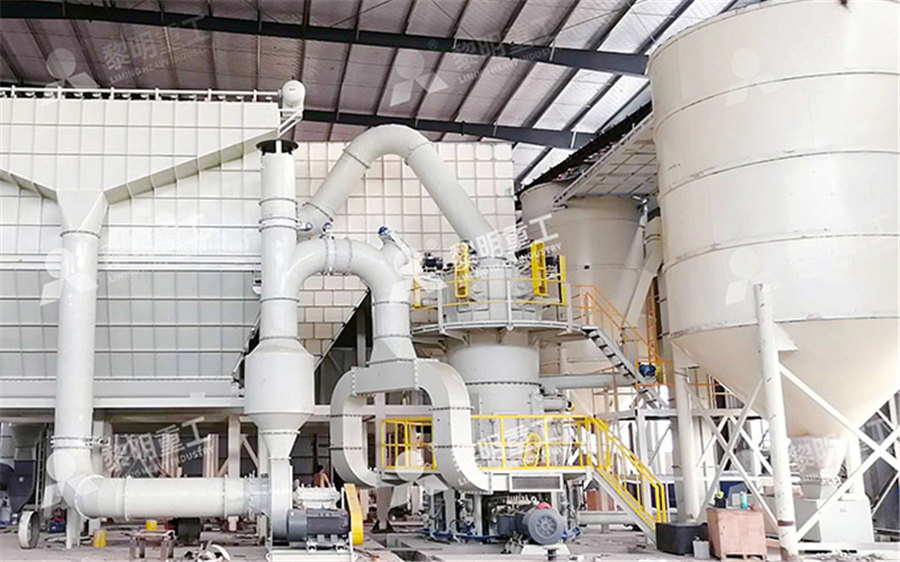
New LimestoneGypsum Flue Gas Desulfuization
2009年10月1日 In this study, a desulfurization experiment was performed in a bubbling reactor to investigate the effects of adding organic acids, such as 2011年1月14日 A novel type PCF device was developed for industrial application of wet FGD Flue gas desulphurization based on limestonegypsum with a Limestone with forced oxidation (LSFO) is a variation of the traditional wet scrubber (see Wet Flue Gas Desulfurization (FGD) ARCOR Epoxy2020年11月11日 Wet flue gas desulfurization was simulated to improve gypsum production Modeling of the wet flue gas desulfurization system to utilize low
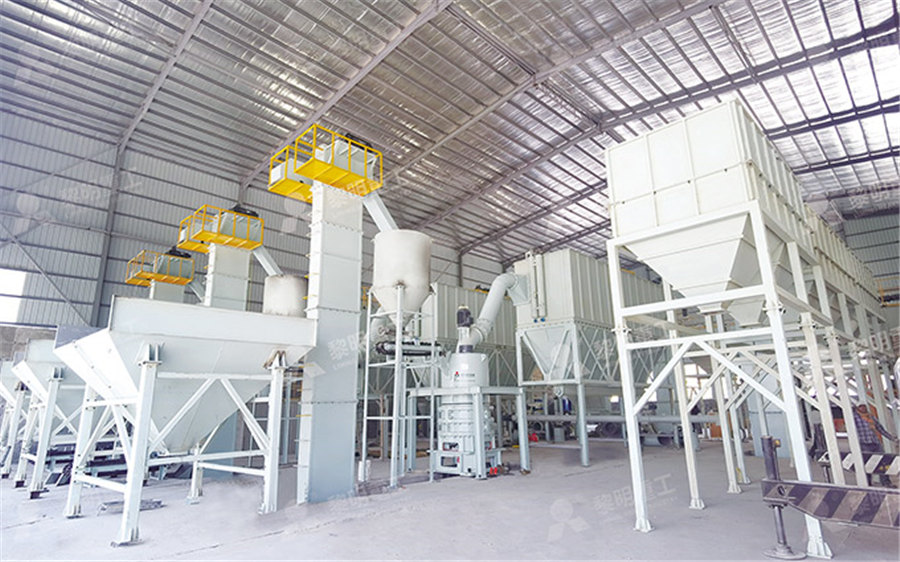
Enhancing the recovery of gypsum in limestonebased wet flue
2017年7月1日 As a dominant precursor of PM 25, SO 2 emitted from industrial process is The Flue Gas Desulfurization (FGD) plant is designed to remove sulfur dioxides (SO2) from flue gas that is produced by boilers, furnaces, and other sources Mitsubishi Power has developed a highly effective wet limestonegypsum FGD Flue Gas Desulfurization (FGD) Mitsubishi Power 2017年7月1日 Among the reasons for the success of the wet FGD system, there is the possibility of recovering a new product to be allocated on the market namely gypsum (He and Lee, 2014)In fact, the synthetic gypsum suitable for several applications such as wallboard manufacturing is the byproduct of the SO 2 scrubbing process for scrubbers using lime or Enhancing the recovery of gypsum in limestonebased wet flue 2015年7月27日 3 Flue Gas Desulfurization Technologies Flue gas desulfurization is an efficient method for the reduction of the sulfur dioxide emissions Citation 2 Many processes are available in the market, such as (a) wet scrubbers, (b) spray dry scrubbers, (c) sorbent injection, (d) regenerable processes, and (e) combined SO 2 /NO X removal processes The different flue Review of Design, Operating, and Financial Considerations in
.jpg)
Wet Flue Gas Desulfurization (FGD) ARCOR Epoxy
The final FGD waste is wallboardgrade gypsum Limestone Forced Oxidation FlueGas Desulfurization Process Note: FGD = fluegas desulfurization By controlling the gypsum quality in the dewatering step, a wallboardgrade gypsum can be produced The majority of scrubber installations in Europe and Japan generate gypsum for reusedesulfurization equipment By: WHD Plant and WL Mathay Flue gas desulfurization (FGD) is the removal of the sulfur oxides from gaseous products produced by the combustion of limestone/gypsum absorber towers constructed worldwide, use nickelcontaining alloys Further, Nickel containing materials in flue gas desulfurization equipmentPresently, wet limestonegypsum flue gas desulfurization (WFGD) technology is widely used in Chinese coal fired power plant WFGD is a mature desulfurization technology with high efficiency and wide availability, which can adapt to various kinds of coal and has low operation cost [2]CPFD SIMULATION AND EQUIPMENT DESIGN OF A NOVEL 2019年3月13日 Introduction Sulfur dioxide (SO 2) is one of the major pollutants contributing to frequent hazy weather in ChinaA large amount of SO 2 in the atmosphere comes from coal combustion As the amount of coal for power generation accounts for 45% of the total coal consumption in 2015 (National Bureau of Statistics [NBS] Citation 2017), the Chinese Full article: Modeling and optimization of wet flue gas desulfurization
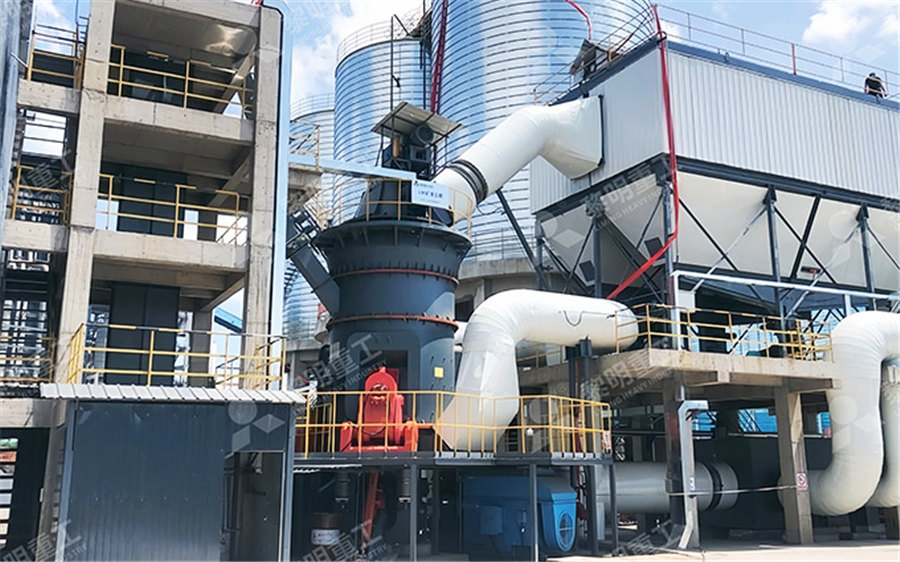
Desulfurization characteristics of limestone slurry with added
2023年3月15日 The equipment consisted of a bubbling reactor, gas supplier, and analytical apparatus New limestonegypsum flue gas desulfurization technology International Conference on Energy and Environment Technology, 2009 (2009), pp 7881, 101109/ICEET20094852021年11月1日 Flue gas desulfurized gypsum mainly comes from thermal power plants, smelters, and largeenterprise boilers, and contains industrial byproducts produced through a wet desulfurization combustion process, where SO 2 gas and lime slurry react under strong oxidation conditions The main component of this gypsum is calcium sulfate dihydrate, which also Production and resource utilization of flue gas desulfurized gypsum Plant in Chongqing introduced two sets of limestone (lime) – gypsum flue gas desulfurization equipment from Mitsubishi Heavy Industries in Japan, equipped with two 360MW generator sets, achieving a desulfurization efficiency of 95% and producing about 400,000 tons of gypsum byproducts annuallyAdvancement of Environmental Sustainability: A Comparative A flue gas desulfurization process capable of producing a high purity gypsum and also making equipment employed as minimum as possible is provided, which process comprises the steps of cooling and dedusting flue gas containing SO x ; contacting the cooled gas with a slurry containing limestone to remove SO x by absorption and also form CaSO 3 ; controlling the pH Limestonegypsum flue gas desulfurization process
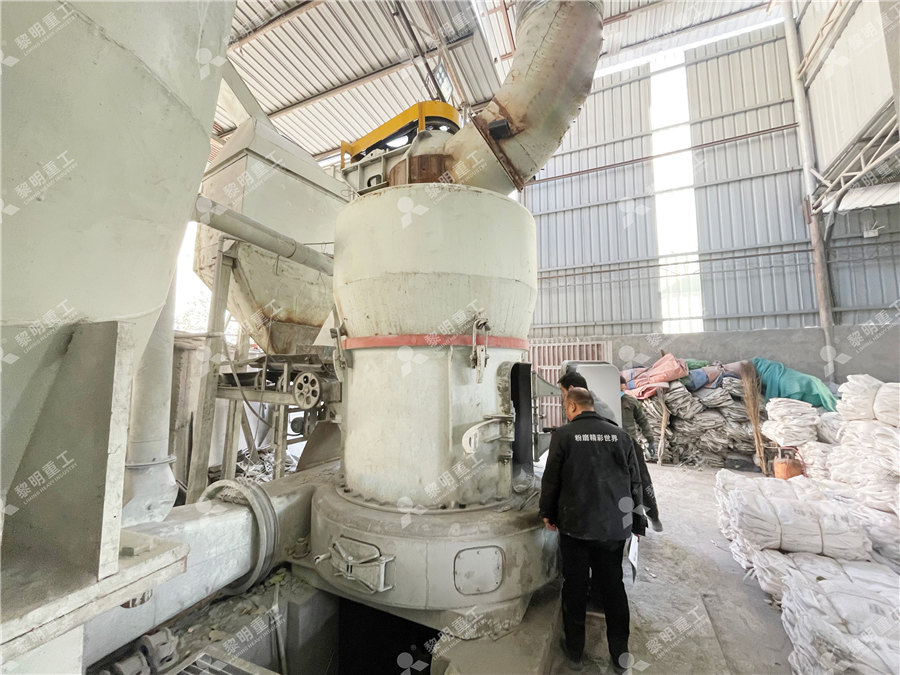
Corrosion evaluation of one wet desulfurization equipment –
2018年12月1日 This wet FGD unit was designed by IHI Corporation (Japan) with desulfurization efficiency over 96% for two pulverized coal boilers in that petrochemical company, and it mainly consisted of five systems including limestone preparation system, boiler air and gas system, absorption system, gypsum dewatering system, and waste water treatment system2020年11月11日 Wet flue gas desulfurization was simulated to improve gypsum production using lowgrade limestone Highgrade limestone with 94 wt% CaCO3 content is used for producing gypsum with 93 wt% purity, but owing to the resource depletion of highgrade limestone, lowgrade limestone should be replaced as an alternative However, lowgrade Modeling of the wet flue gas desulfurization system to utilize low 2019年8月9日 Physico chemical Pilot Study Of Wet Limestonegypsum Method For Flue Gas Desulfurization Wastewater Environmental Pollution and Public Health(EPPH) Special Track within iCBBE2012Study on Biological Treatment of Limestonegypsum FGD gypsum is a major gypsum resources in Germany, accounting for over 75% of the total production of gypsum[67] Japan FGD Gypsum Research and Application Status Japan is the world's first largescale application of FGD equipment countries, which uses wet limestonegypsum desulfurization unit more than 75% of total installed capacityAdvances in Utilization of Flue Gas Desulfurization Gypsum
.jpg)
New LimestoneGypsum Flue Gas Desulfuization Technology
PDF On Oct 1, 2009, Shengyu Liu and others published New LimestoneGypsum Flue Gas Desulfuization Technology Find, read and cite all the research you need on ResearchGate使用Reverso Context: In summary, since there is no ammonia byproduct in the Project, considering from the desulfurization process maturity, reliability and longterm stable operation, etc, this FSR tentatively adopts limestone gypsum desulfurization process,在英语中文情境中翻译"limestone gypsum desulfurization"limestone gypsum desulfurization翻译为中文例句英语 2019年3月30日 The maximum efficiency of wet limestonegypsum desulfurization can reach 99%, which basically ensures that the SO 2 concentration in the flue gas can meet the requirements of Chi na Air Pollutant(PDF) Progress of Desulfurization and Denitration Technology of At present, more than 90% of thermal power plants in China adopt limestone gypsum desulfurization technology, which has mature technology and low cost Both processes need limestone powder to absorb sulfur dioxide, Guilin HongCheng Mining Equipment Manufacture Co, Ltd Phone: 86;News Desulfurization Limestone Grinding Mill Sale Limestone
.jpg)
Lime / Limestone Wet Scrubbing System for Flue Gas Desulfurization
2) and limestone (CaCO 3) Rosemount Analytical pH equipment is used to control the feed rate of these chemicals PROCESS After fly ash removal, the flue gas (seen in Figure 1) is bubbled through the scrubber, and the slurry is added from aboveThe lime or limestone reacts with the SO 2 in the flue gas to create insoluble calcium sulfite (CaSO This article takes a 5000t/d clinker cement production line as an example to introduce the design scheme of limestonegypsum desulfurization CLIRIK believe that limestonegypsum desulfurization technology is very suitable for cement plants 1 and return to the absorption tower during operation of the equipment flushing water, Limestonegypsum Desulfurization Process in Cement Plant2024年3月20日 Desulfurization wastewater is industrial wastewater with a high salt content, high metal ions, and high hardness produced by flue gas desulfurization of the limestonegypsum method in coalfired power plants Current Status of Zero Liquid Discharge Technology for 2015年1月1日 In this paper, a concise model for wet limestone–gypsum flue gas desulfurization system with spray tower has been presented, aiming at the prediction of the absorption height in a spray tower The equations of droplet motion and mass balance were incorporated and developed to simulate the droplet movement, distribution and mass transfer of SO 2 in the absorption A concise algorithm for calculating absorption height in spray
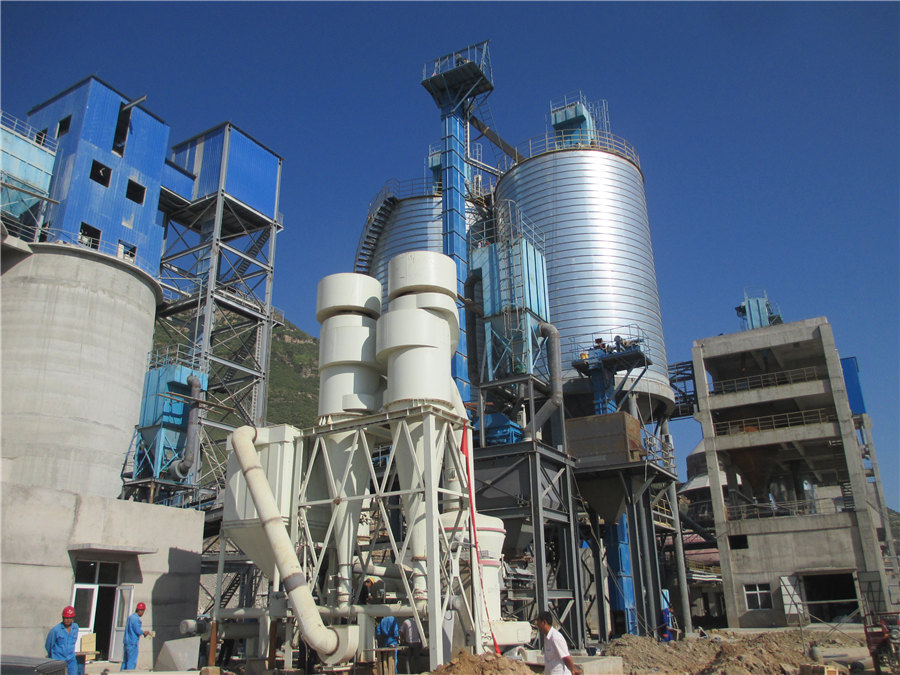
limestone gypsum desulfurization Translation into Chinese
Translations in context of "limestone gypsum desulfurization" in EnglishChinese from Reverso Context: In summary, since there is no ammonia byproduct in the Project, considering from the desulfurization process maturity, reliability and longterm stable operation, etc, this FSR tentatively adopts limestone gypsum desulfurization processThe selfadaptive efficient sieve plate dusting and desulfurization technology jointly developed by Zhejiang University and HBC Based on limestonegypsum WFGD technology, HBC add the adaptive sieve plate mass transfer component and reasonably reduce the height position of the partition plate, so as to form a stable and uniform liquid layerHarbin Electric Corporation2002年4月1日 A model of limestone/gypsum wet flue gas desulfurization system was set up based on the relationship between the energy consumption and the desulfurization features of these equipmentsOptimum Values of Process Parameters of the “Wet Limestone The invention discloses a limestonegypsum wetmethod flue gas desulfurization additive Components and corresponding mass percentage of the additive are as follows: highmolecular hydroxy acid salt 1525, organic synergist 6575, and inorganic dissolution accelerator 1015 The additive can effectively prevent scaling, promote the dissolution of limestone, and improve the Limestonegypsum wetmethod flue gas desulfurization additive
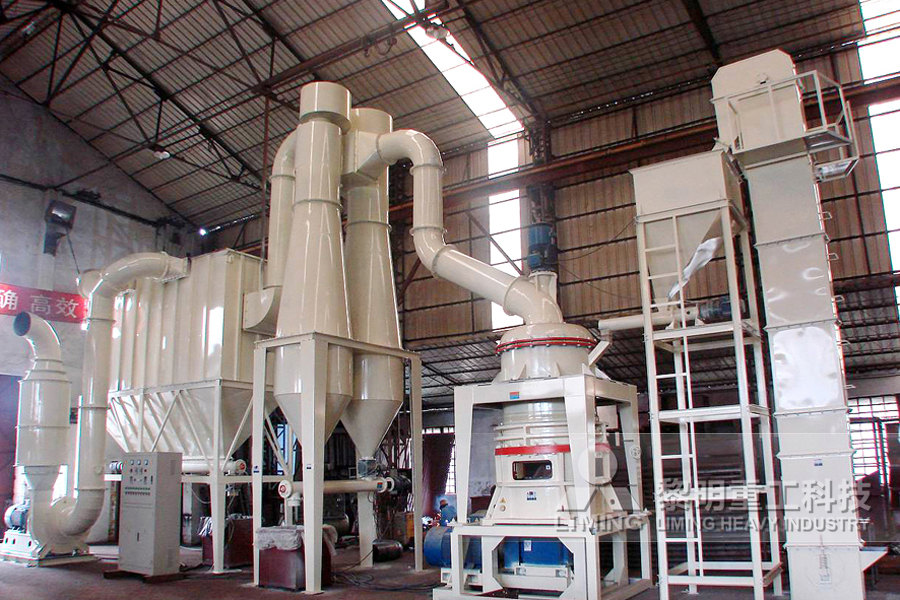
4 Flue Gas Desulfurization Process You Should Never Miss
2024年4月19日 Limestone gypsum wet flue gas desulfurization process 2 Magnesium oxide desulfurization process The basic principle of magnesium oxide desulfurization is similar to that of limestone (lime) method, that is, the SO2 in the flue gas is absorbed by magnesium oxide slurry, which mainly generates trihydrate and polyhydrate magnesium sulfite, and then generates Flue gas desulfurization plants, wet systems, gypsum dewatering, gypsum recovery, vacuum belt filters, environmental, coalfired power plant equipment, new technology for coalfired power plants ABSTRACT Recovering gypsum from flue gas desulfurization (FGD) plants is becoming more important as theCOMPARISON OF GYPSUM DEWATERING TECHNOLOGIES AT FLUE 2020年3月24日 The limestonegypsum method is a wet flue gas desulfurization technol ogy, it uses limestone or quicklime as the absorbent absorb and separate SO 2 and convert it into a stable substance, gypsum ItsResearch on Desulfurization and Denitration Technologies of 2024年2月1日 In the limestonegypsum WFGD system, the standard operating conditions were as follows: flue gas volume flow of 06 Nm 3 /h (where Nm 3 refers to a cubic meter at normal conditions of 27315 K and 101325 kPa), inlet flue gas temperature of 120 ℃, desulfurization solution temperature of 40 ℃, pH of desulfurization solution of 55, desulfurizing solution Formation and migration of soluble ions in condensable
.jpg)
Enhancing the recovery of gypsum in limestonebased wet flue
2017年7月1日 Among the reasons for the success of the wet FGD system, there is the possibility of recovering a new product to be allocated on the market namely gypsum (He and Lee, 2014)In fact, the synthetic gypsum suitable for several applications such as wallboard manufacturing is the byproduct of the SO 2 scrubbing process for scrubbers using lime or 2015年7月27日 3 Flue Gas Desulfurization Technologies Flue gas desulfurization is an efficient method for the reduction of the sulfur dioxide emissions Citation 2 Many processes are available in the market, such as (a) wet scrubbers, (b) spray dry scrubbers, (c) sorbent injection, (d) regenerable processes, and (e) combined SO 2 /NO X removal processes The different flue Review of Design, Operating, and Financial Considerations in The final FGD waste is wallboardgrade gypsum Limestone Forced Oxidation FlueGas Desulfurization Process Note: FGD = fluegas desulfurization By controlling the gypsum quality in the dewatering step, a wallboardgrade gypsum can be produced The majority of scrubber installations in Europe and Japan generate gypsum for reuseWet Flue Gas Desulfurization (FGD) ARCOR Epoxydesulfurization equipment By: WHD Plant and WL Mathay Flue gas desulfurization (FGD) is the removal of the sulfur oxides from gaseous products produced by the combustion of limestone/gypsum absorber towers constructed worldwide, use nickelcontaining alloys Further, Nickel containing materials in flue gas desulfurization equipment
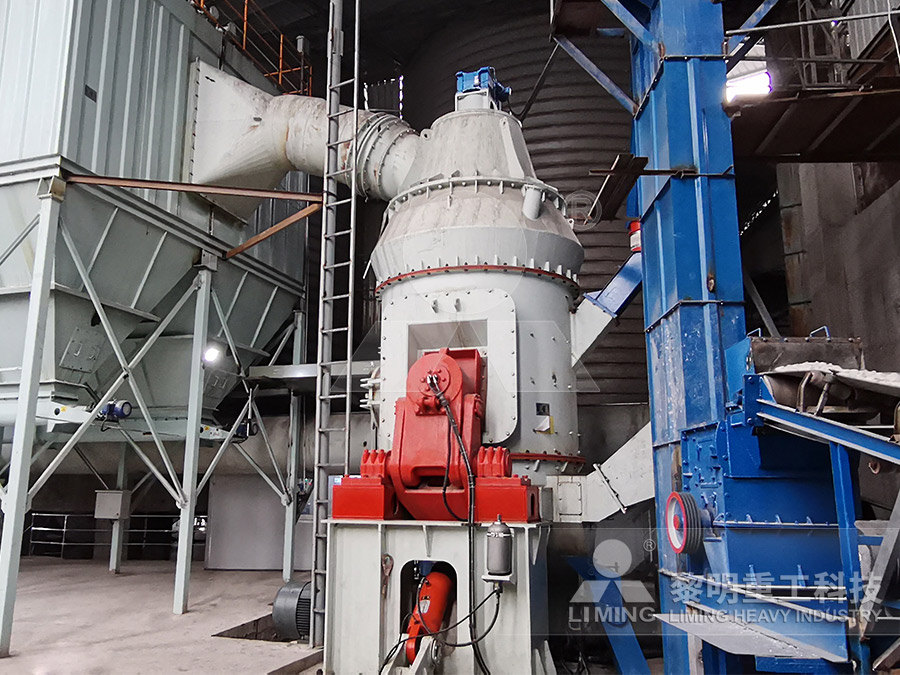
CPFD SIMULATION AND EQUIPMENT DESIGN OF A NOVEL
Presently, wet limestonegypsum flue gas desulfurization (WFGD) technology is widely used in Chinese coal fired power plant WFGD is a mature desulfurization technology with high efficiency and wide availability, which can adapt to various kinds of coal and has low operation cost [2]2019年3月13日 Introduction Sulfur dioxide (SO 2) is one of the major pollutants contributing to frequent hazy weather in ChinaA large amount of SO 2 in the atmosphere comes from coal combustion As the amount of coal for power generation accounts for 45% of the total coal consumption in 2015 (National Bureau of Statistics [NBS] Citation 2017), the Chinese Full article: Modeling and optimization of wet flue gas desulfurization 2023年3月15日 The equipment consisted of a bubbling reactor, gas supplier, and analytical apparatus New limestonegypsum flue gas desulfurization technology International Conference on Energy and Environment Technology, 2009 (2009), pp 7881, 101109/ICEET2009485Desulfurization characteristics of limestone slurry with added 2021年11月1日 Flue gas desulfurized gypsum mainly comes from thermal power plants, smelters, and largeenterprise boilers, and contains industrial byproducts produced through a wet desulfurization combustion process, where SO 2 gas and lime slurry react under strong oxidation conditions The main component of this gypsum is calcium sulfate dihydrate, which also Production and resource utilization of flue gas desulfurized gypsum
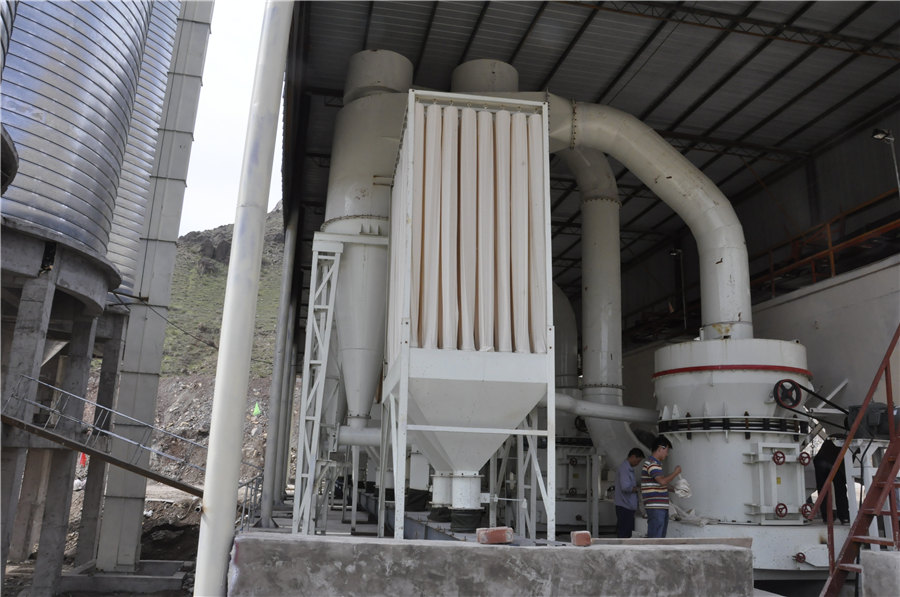
Advancement of Environmental Sustainability: A Comparative
Plant in Chongqing introduced two sets of limestone (lime) – gypsum flue gas desulfurization equipment from Mitsubishi Heavy Industries in Japan, equipped with two 360MW generator sets, achieving a desulfurization efficiency of 95% and producing about 400,000 tons of gypsum byproducts annuallyA flue gas desulfurization process capable of producing a high purity gypsum and also making equipment employed as minimum as possible is provided, which process comprises the steps of cooling and dedusting flue gas containing SO x ; contacting the cooled gas with a slurry containing limestone to remove SO x by absorption and also form CaSO 3 ; controlling the pH Limestonegypsum flue gas desulfurization process