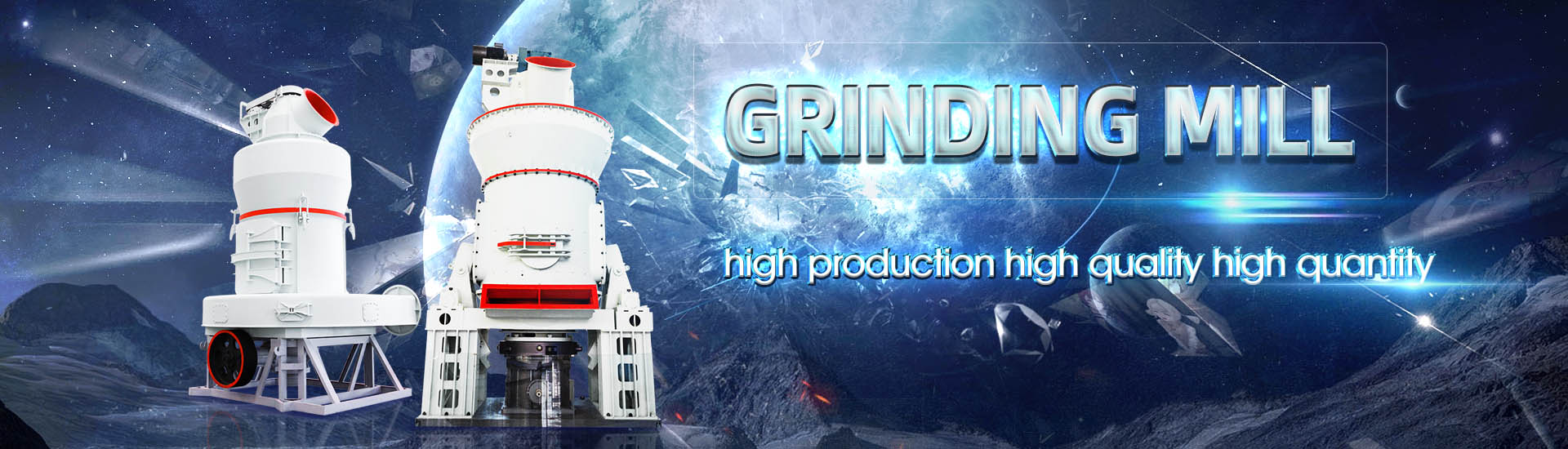
Mining dry grinding mill on the production line of reduced iron oxide powder grinding
.jpg)
Iron ore concentration process with grinding circuit, dry desliming
IRON ORE CONCENTRATION PROCESS WITH DRY GRINDING CIRCUIT, DRY DESLIMING AND MIXED (DRY AND WET) CONCENTRATION, according to the claim 7, wherein the 2024年4月26日 Iron ore, a naturally occurring mineral composed primarily of iron oxides, is mined and processed to extract iron for various industrial applications This article provides a Iron Ore Processing: From Extraction to Manufacturing Mining 2021年1月1日 The introductory section provides a brief overview of mill scale accumulation and disposal as a waste product become increasingly important This called for research and Overview on production of reduced iron powder from mill scale 2016年3月30日 Processes that produce iron by reduction of iron ore (in solid state) below the melting point are generally classified as DR processes Based on the types of reductant used, (PDF) i) Direct Reduced Iron: Production ResearchGate
.jpg)
Exploring LowGrade Iron Ore Beneficiation Techniques: A MDPI
2024年8月2日 This comprehensive review explores various beneficiation techniques for lowquality iron ore, focusing on conventional methods including comminution, froth flotation and 2023年4月5日 Direct Reduced Iron (DRI) is the product of the reduction of iron ores (lumps, pellets, or fines) in solidstate by gaseous or carbonaceous substances [22, 23] The reduction Recent Trends in the Technologies of the Direct Reduction and 2021年11月1日 The Höganäs method is considered the most effective method for producing reduced iron powder (RIP) However, this method does not remove impurities; therefore, high Preparation of reduced iron powder for powder metallurgy from Mill scale, a potential raw material for recycling from hot rolling mill operations is chosen and one step thermochemical reduction technique is employed to beneficiate the iron content in the Direct Reduction Recycling of Mill Scale Through Iron Powder
.jpg)
Development of a Novel Grinding Process to Iron Ore Pelletizing
2020年3月28日 Iron ore pellet production requires a fine mineral particle distribution to lead to good agglomerate densification, a smooth surface, and controlled growth in the pelletizing 2016年3月30日 In book: Encyclopedia of Iron, Steel, and Their Alloys (pppp 10821108) Chapter: i) Direct Reduced Iron: Production; Publisher: CRC Press, Taylor and Francis Group, New York(PDF) i) Direct Reduced Iron: Production2021年6月30日 In addition, although the behavior of iron reoxidation on the nanosurface of iron powder is quite different from the overall reoxidation behavior of iron powder, the intensity change trend of Fe 2+ (−7265 eV) (15293 → 23276), Fe 3 O 4 (−7108 eV) (15199 → 24099), Fe 2 O 3 (−7128 eV) (14566 → 22349) and Fe 2 O 3 (−7244 eV) (15813 → 24911) clearly shows that Novel insights into the reoxidation of direct reduced iron (DRI) Take the 2TPH capacity as example, our powder grinding mill machine can help customers get largeprofit every month Ultra fine powder grinding mill is our main product,not only can adapt to many kinds of material ,but also with high capacityWe can design you different capacity powder production line according to your capacity,materialGrinding Mill for Powder production line
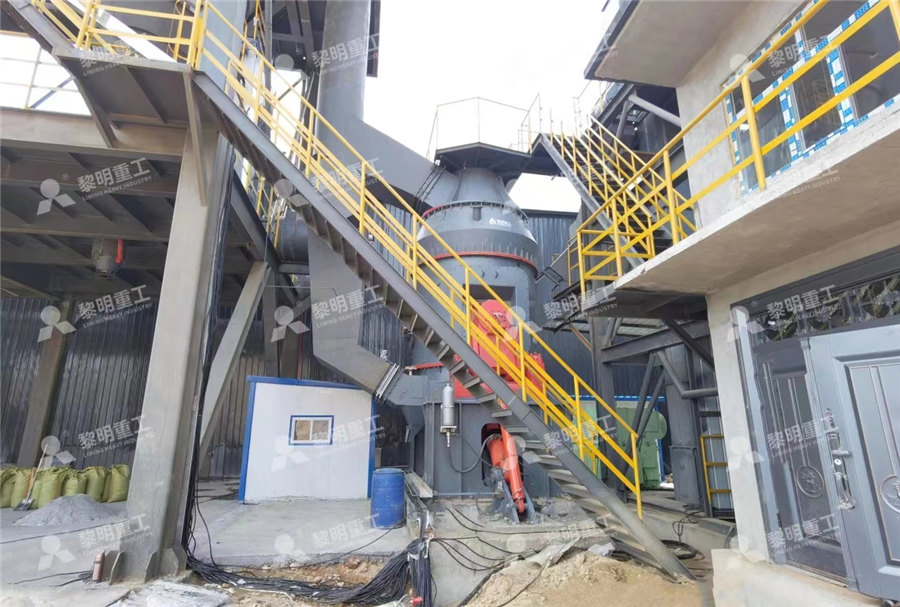
Ultrafine Grinding Mill, Micro Powder Grinding Mill Bellian Mining
The Ultrafine Grinding Mill, also known as a Micro Powder Grinding Mill or Ultra Fine Powder Grinding Machine, is a highefficiency and lowconsumption grinding mill that is widely used in the powder processing of various materials Bellian Mining Machinery offers a range of Ultrafine Grinding Mills, including the Ultrafine Vertical Mill and Fine Powder Mill Grinder, designed to Widely used in the mining, chemical, building materials, metallurgy, refractory, power plant desulfurization, highway, asphalt mixing station and other industries, powder grinding plant serves for the processing of nonflammable and nonexplosive mineral powder with less than 8 mohs hardness and no more than 6% humidity, such as limestone, feldspar, calcite, talc, barite, Powder Grinding Plant/ Powder Making Line/ Powder Production Line 2021年1月1日 Compared to traditional drymilling, wet grinding shows higher efficiency and can avoid dust generation Since most of IOTs are directly discharged into the river or exposed to rainwater, wet Different Effects of Wet and Dry Grinding on the Activation of Iron 2010年7月1日 Crushing and grinding processes have undergone significant changes over the last 20 years These adjustments have focused on lowering costs and increasing production and energy efficiency, mainly The Evolution of Crushing and Grinding: Changes in the Industry
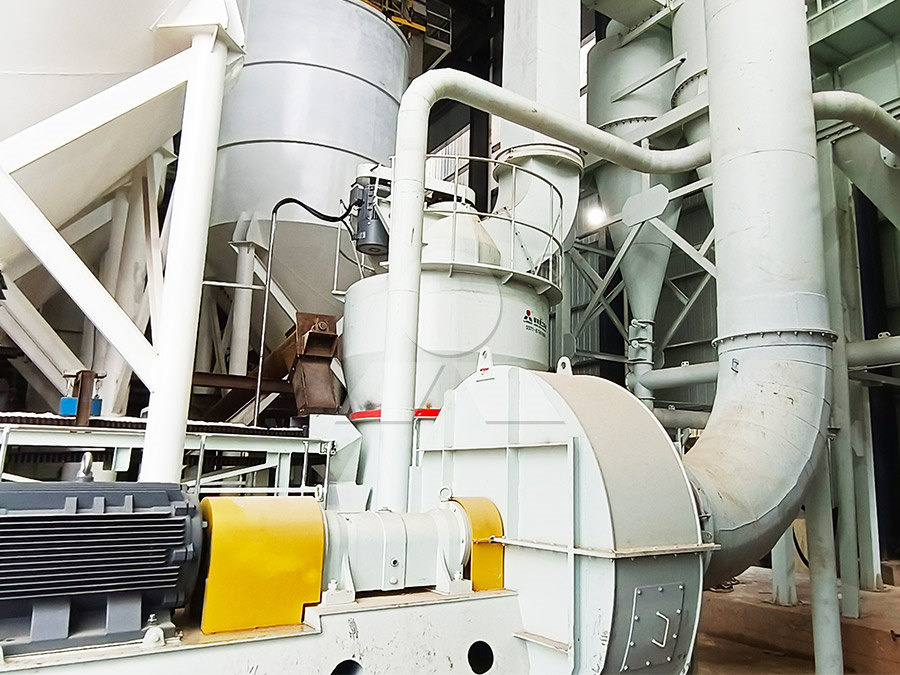
Preparation of iron oxide nanoparticles by mechanical milling
2011年1月1日 Additional requirements are given for the particle shape and surface properties of powders, dependent on the end usage or specific consumer requirements (Nakach et al, 2004) The aim of this study is to prepare iron oxide nanoparticles through dry milling using a planetary mill and to characterize the mill particles2023年8月1日 The inefficiency of grinding, especially in dry grinding, is generally explained by the slowing effect caused by fine particles This may originate from the particle regrowth or rebuilding from smaller particles as a result of either agglomeration, including van der Waal's forces, or direct briquetting, or ball coating in order to provide soft surfaces [1, 7, 16, 17]Effective role of grinding aids in the dry grinding performance of 2018年8月17日 Further, the grinding mills can be categorized into three major types — rod mills, ball mills, and SAG mills So, which one is for you? Well, the answer essentially lies in the feed size and the Grinding Mills — Types, Working Principle Applications2017年5月25日 An examination of the literature shows, however, that the actual difference between the results of wet and dry milling are often very large; for example the power to drive a tube mill in which a given material is being wet Dry Grinding VS Wet Grinding 911Metallurgist
.jpg)
(PDF) A comprehensive review on the grinding process:
June 2022; ARCHIVE Proceedings of the Institution of Mechanical Engineers Part C Journal of Mechanical Engineering Science 19891996 (vols 203210) 236(2):年8月29日 Shanghai Clirik Machinery Co, Ltd Is excellent ore mill supplier Our main products include ultrafine powder grinding mill, vertical roller mill, roller grinding mill, stone powder production equipment, Welcome to consultClirik Grinding Mill Clirik Enterprise Focuses On Also the Premier™ mills and Select™ mills come ready to be easily integrated with our mill reline equipment and full mining portfolio providing a onestopshop for your minerals processing needs! Premier™ horizontal grinding millsGrinding mills for mining and minerals processing Metso2020年9月20日 The inconsistencies of these studies may be explained by a study of Prziwara et al [54] on the impacts of grinding aids on the dry stirred milling of limestone: The authors found that the strategy of adding the grinding aid only influences the grinding result, if an early (or delayed) addition of chemicals influences the flow behavior of the product in such a way, that Grinding aids for dry fine grinding processes ScienceDirect
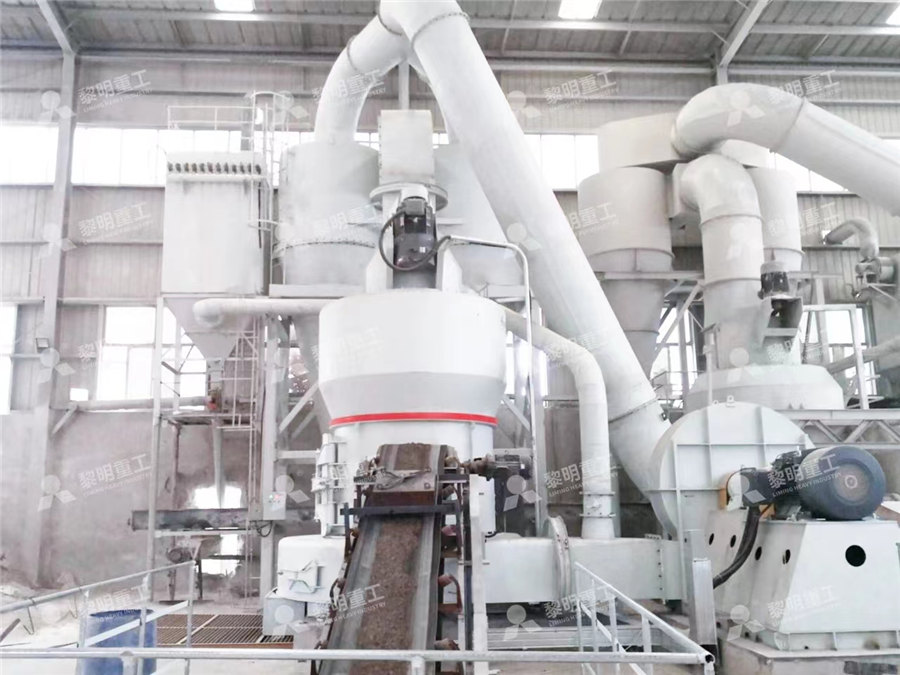
Production of powders for metal additive manufacturing
2022年4月1日 Metal powders are the starting point for a host of net and nearnet shape manufacturing processes, ranging from powder metallurgy to metal additive manufacturing (AM) [1], [2], [3]Powders for these applications are produced predominantly by atomization, which involves breakup of a molten metal stream into fine droplets via the use of impinging air or China Powder Grinding Mill wholesale Processing Object: Lithium Iron Phosphate, Ink, Alumina, Oxide Controlling Mode: Electric Control System Automatic Grade: Automatic Mineral Grinder Powder Production Line, Ultrafine Micron Calcite Grinding Mill Machine, Powder Grinding Mill MadeinChina2023年9月1日 There is no record of previous studies producing reduced iron from mill scale without agglomeration on a semiproduction scale However, in this research, it was observed that varying the rotation speed led to different crosssectional diameters of the produced spheroidal reduced iron As the RPM increased, the crosssectional diameters decreasedProduction of reduced iron from mill scale waste using tilting Mining Production Report Free download as Word Doc (doc / docx), PDF File (pdf), Text File (txt) or read online for free The document provides an overview of operations at Bulawayo Mining Company's reduction plant in March 2017 It details the multistage processes of crushing, milling, carboninpulp, elution, and tailings disposal used to extract gold from oreMining Production Report PDF Mill (Grinding) Pump
2FD{P}PC]854]XQ.jpg)
Different Effects of Wet and Dry Grinding on the Activation of Iron
DOI: 1032604/jrm2021 ARTICLE Different Effects of Wet and Dry Grinding on the Activation of Iron Ore Tailings Yingchun Yang 1, *, Liqing Chen 1 and Yuguang Mao 2 1 College of Engineering, Anhui Agricultural University, Hefei, , China 2 College of Civil Engineering, Hunan University, Changsha, , China * Corresponding Author: Yingchun Yang2022年8月13日 The grinding mill is the core of the entire production line The choice of grinding mill machine is related to the quality of the final ground calcium carbonate powder, so how to choose the right calcium carbonate grinding How to Choose a Calcium Carbonate Grinding Mill2019年9月1日 To select dry or wet grinding, the differences between their process conditions should be taken into consideration Transfer and motion of particles by air in case of dry grinding or water may significantly affect power draw and energy consumption of grinding circuits [5]Particularly, these energy differences become significant when considering that around 3% A comparative study on the effects of dry and wet grinding on 2020年7月1日 The term chemical additives or grinding aids (GAs) refers to any substance which results in increased grinding efficiency and reduction in power consumption when added to the mill charge (amounts not exceeding 025 wt% of the feed) during grinding [1], [2], [3]The use of grinding aids to increase mill throughput is quite common in the cement industry [2], [4], [5]A critical review on the mechanisms of chemical additives used in
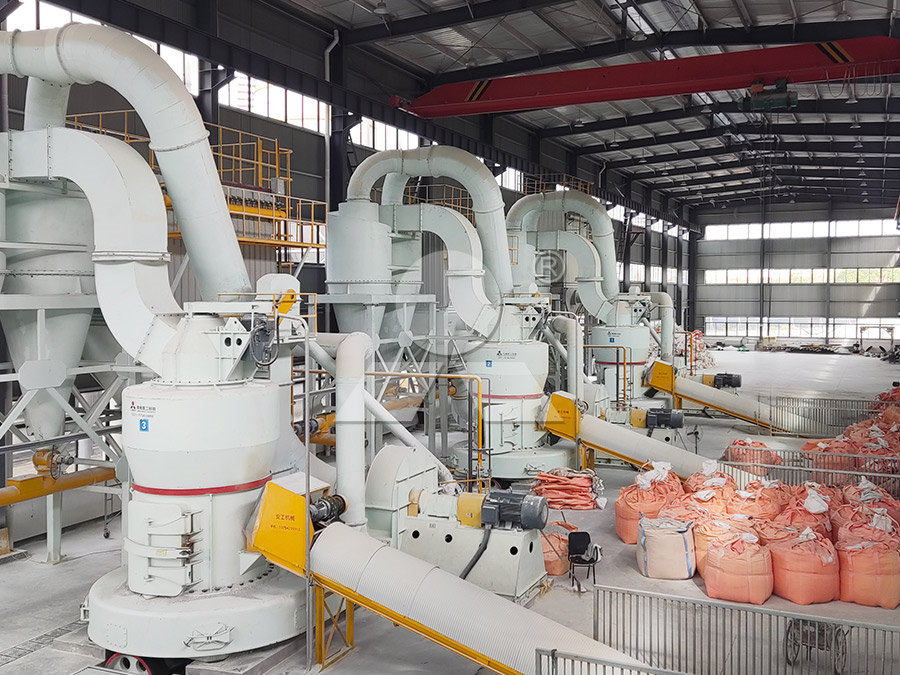
Preparation of reduced iron powder for powder metallurgy from
2021年11月1日 Analytical grade calcium oxide (CaO), analytical grade calcium sulfate dihydrate (CaSO 4), analytical grade anhydrous sodium carbonate (Na 2 CO 3), and analytical grade anhydrous sodium sulfate (Na 2 SO 4) were purchased from Sinopharm Chemical Reagent Co, LtdThe pyrite (FeS 2) used for the study was collected from Henan Province in China; its 2023年5月27日 Grinding process is to produce grade wise powder form from activated bentonite or natural bentonite Raymond mill is a popular bentonite grinding equipment Learn more about bentonite Raymond mill The particle size of bentonite powder can be adjusted within 80425 mesh to ensure that the finished bentonite powder can serve different industriesHow to Dry, Grind and Granulate Your Bentonite Clay?2020年10月1日 After some other processes, αFe 2 O 3 red powder particles byproduct of regeneration of spent pickling liquor in ARP in iron and steel industry should be ground up to pigment grade to convert it to a value added product, red iron oxide pigment In this study, grinding tests on αFe 2 O 3 red powder were performed using four different types of An investigation on optimum grinding system and conditions 2003年1月1日 Fine grinding of metalliferous ores has become increasingly important for the Australian mining industry, as many of the remaining orebodies are very finegrained and refractoryFINE GRINDING IN THE AUSTRALIAN MINING INDUSTRY
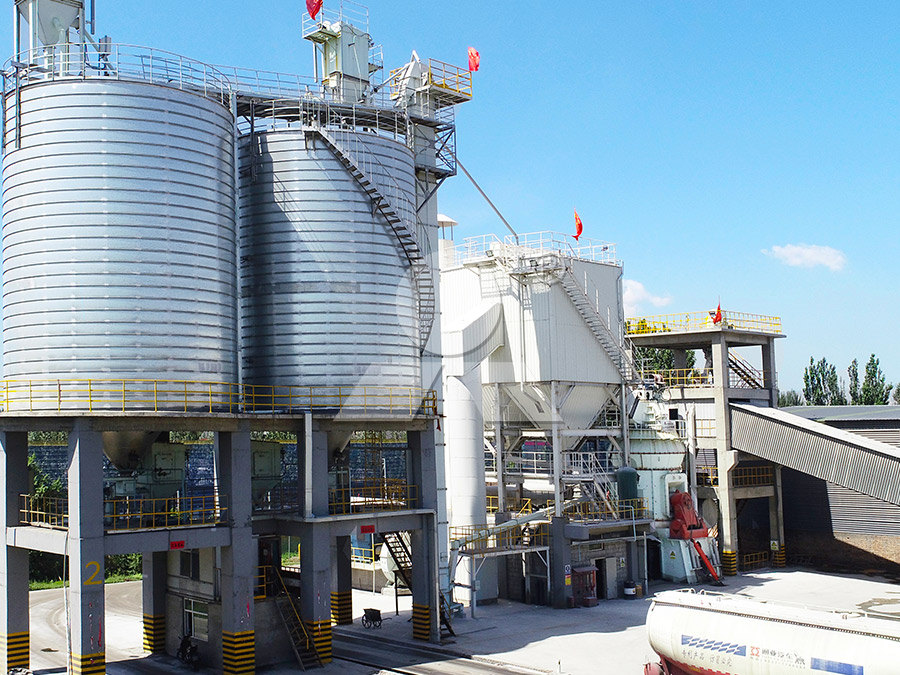
Grinding Metso
With over a century of experience, Metso designs and manufactures the most comprehensive line of grinding mills and entire grinding systems for mining companies around the world The comprehensive offering provides reliable and energy efficient technology and solutions across wet, dry, horizontal, and vertical grinding operations2020年1月1日 Also, the comparison between the methods of metal oxides powder production and their limitations and drawbacks will be stated Furthermore, choosing the right powder production method depends on the aims of the process and the type of materials (eg, hard, brittle, and ductile) that will be subjected to the processMechanical and physical methods for the metal oxide powders production 2019年1月30日 Mill power models have been used in a variety of ways in industrial practice since power directly equates to throughput and fineness of ground product We first start with HoggFuerstenau Power Model and show how this model successfully predicted the power draw of many grinding mills in several mining operations Then, we show how this model was on the The Evolution of Grinding Mill Power Models Mining, 2016年3月30日 In book: Encyclopedia of Iron, Steel, and Their Alloys (pppp 10821108) Chapter: i) Direct Reduced Iron: Production; Publisher: CRC Press, Taylor and Francis Group, New York(PDF) i) Direct Reduced Iron: Production

Novel insights into the reoxidation of direct reduced iron (DRI)
2021年6月30日 In addition, although the behavior of iron reoxidation on the nanosurface of iron powder is quite different from the overall reoxidation behavior of iron powder, the intensity change trend of Fe 2+ (−7265 eV) (15293 → 23276), Fe 3 O 4 (−7108 eV) (15199 → 24099), Fe 2 O 3 (−7128 eV) (14566 → 22349) and Fe 2 O 3 (−7244 eV) (15813 → 24911) clearly shows that Take the 2TPH capacity as example, our powder grinding mill machine can help customers get largeprofit every month Ultra fine powder grinding mill is our main product,not only can adapt to many kinds of material ,but also with high capacityWe can design you different capacity powder production line according to your capacity,materialGrinding Mill for Powder production lineThe Ultrafine Grinding Mill, also known as a Micro Powder Grinding Mill or Ultra Fine Powder Grinding Machine, is a highefficiency and lowconsumption grinding mill that is widely used in the powder processing of various materials Bellian Mining Machinery offers a range of Ultrafine Grinding Mills, including the Ultrafine Vertical Mill and Fine Powder Mill Grinder, designed to Ultrafine Grinding Mill, Micro Powder Grinding Mill Bellian Mining Widely used in the mining, chemical, building materials, metallurgy, refractory, power plant desulfurization, highway, asphalt mixing station and other industries, powder grinding plant serves for the processing of nonflammable and nonexplosive mineral powder with less than 8 mohs hardness and no more than 6% humidity, such as limestone, feldspar, calcite, talc, barite, Powder Grinding Plant/ Powder Making Line/ Powder Production Line
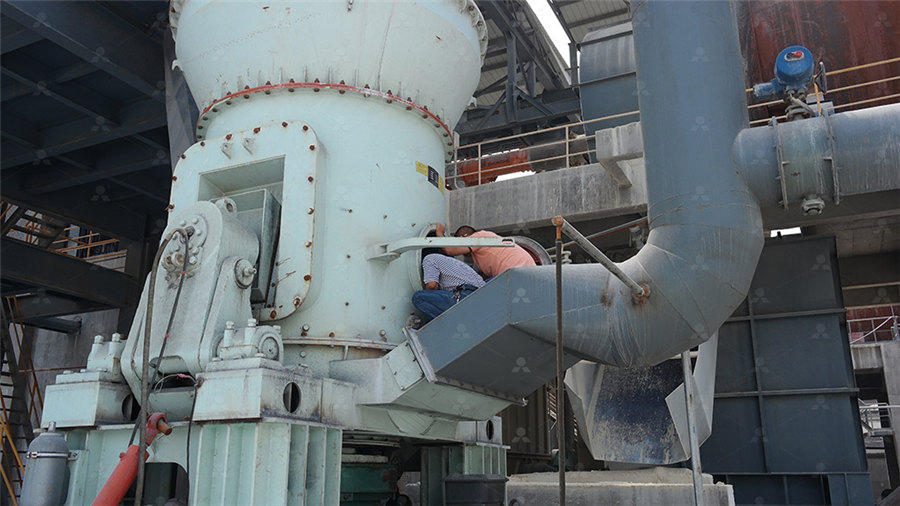
Different Effects of Wet and Dry Grinding on the Activation of Iron
2021年1月1日 Compared to traditional drymilling, wet grinding shows higher efficiency and can avoid dust generation Since most of IOTs are directly discharged into the river or exposed to rainwater, wet 2010年7月1日 Crushing and grinding processes have undergone significant changes over the last 20 years These adjustments have focused on lowering costs and increasing production and energy efficiency, mainly The Evolution of Crushing and Grinding: Changes in the Industry 2011年1月1日 Additional requirements are given for the particle shape and surface properties of powders, dependent on the end usage or specific consumer requirements (Nakach et al, 2004) The aim of this study is to prepare iron oxide nanoparticles through dry milling using a planetary mill and to characterize the mill particlesPreparation of iron oxide nanoparticles by mechanical milling2023年8月1日 The inefficiency of grinding, especially in dry grinding, is generally explained by the slowing effect caused by fine particles This may originate from the particle regrowth or rebuilding from smaller particles as a result of either agglomeration, including van der Waal's forces, or direct briquetting, or ball coating in order to provide soft surfaces [1, 7, 16, 17]Effective role of grinding aids in the dry grinding performance of
.jpg)
Grinding Mills — Types, Working Principle Applications
2018年8月17日 Further, the grinding mills can be categorized into three major types — rod mills, ball mills, and SAG mills So, which one is for you? Well, the answer essentially lies in the feed size and the