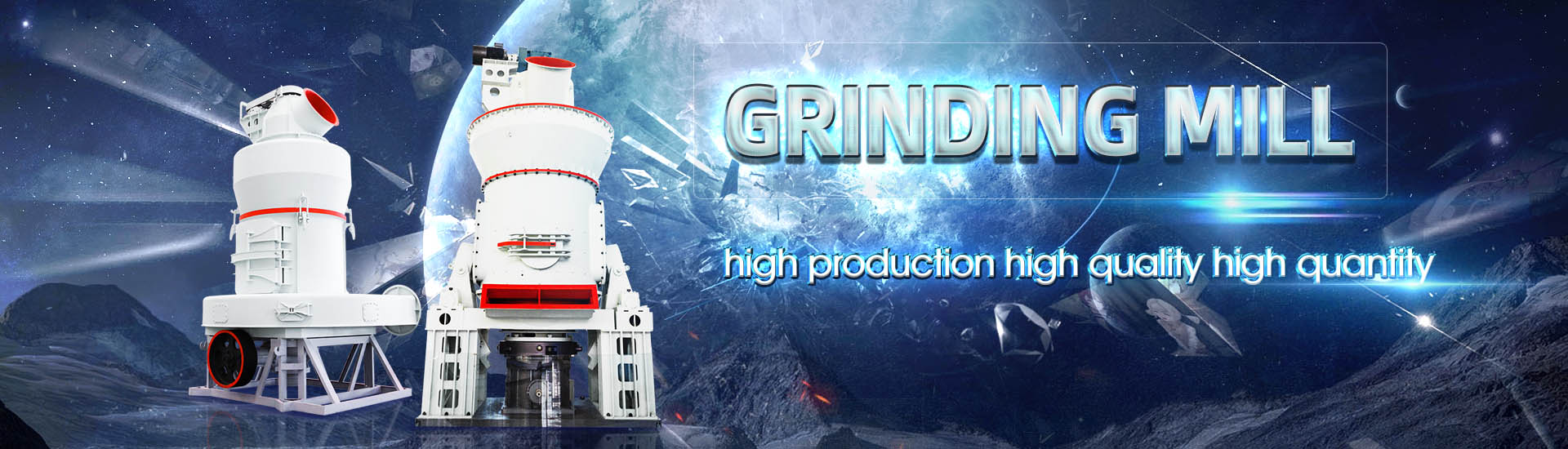
Coal to methanol process flow
.jpg)
Conceptual Design Development of CoaltoMethanol
2020年12月4日 In this study, we propose the conceptual design development of coaltomethanol process using captured CO 2 from the gasification plant by Figure 2 shows a typical coalbased methanol production process (MC), which can be divided into two subsystems: a fresh gas preparation subsystem (to produce fresh gas for methanolFlow diagram of coalbased methanol production2022年3月10日 The coaltomethanol (CTM) is an important technical route for methanol production The process suffers from high CO 2 emission and low energy efficiency due to the Novel coaltomethanol process with nearzero carbon emission 2008年5月2日 PDF Process simulation and engineering economics of a coal to methanol process via gasification Find, read and cite all the research you need on ResearchGate(PDF) Coal to methanol ResearchGate
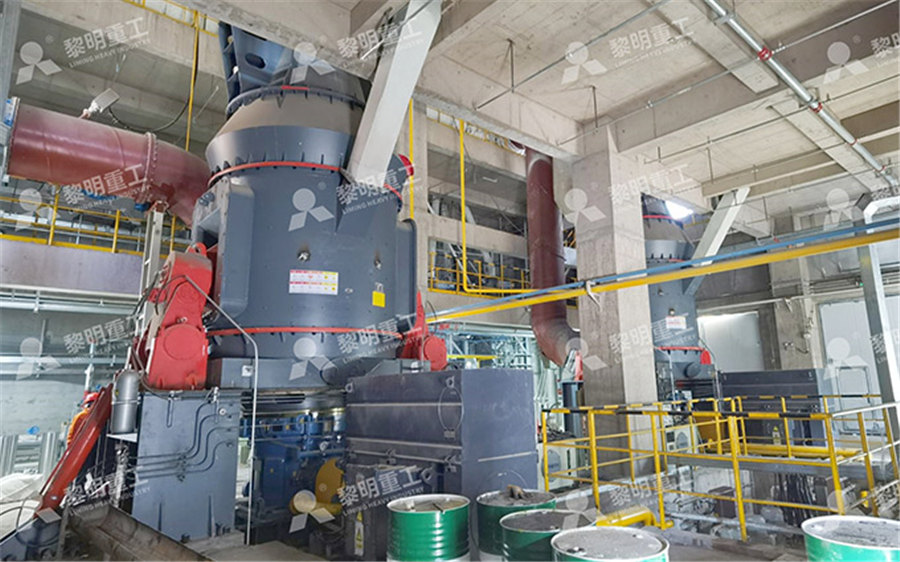
(PDF) Conceptual Design Development of CoalTo
2020年12月4日 In this study, we propose the conceptual design development of coaltomethanol process using captured CO2 from the gasification plant by implying process intensification The base case and2020年6月10日 A novel coaltomethanol process integrated with cokeoven gas chemical looping hydrogen and chemical looping air separation is designed and analysed to improve Highly efficient carbon utilization of coaltomethanol process 2022年9月15日 This study proposed a coal to methanol process assisted by the green hydrogen generated from three pathways of water electrolysis by wind, solar or windsolar hybrid power A multidimensional feasibility analysis of coal to methanol In this report we review entrained bed coal gasification technology using the Shell Coal Gasification Process (SCGP), integrated with the ICI/Synetix Low Pressure Methanol (LPM) Coal to Methanol SP Global
.jpg)
How to Produce Methanol from Coal SpringerLink
One of the many possible routes from coal to methanol is illustrated by a process flow diagram, and a material and energy balance is compiled for this typical example Coal Gasification: At the Crossroad Technological Factors What 2018年6月23日 This research aims to provide a preliminary design of a coal to methanol process via the gasification technology The plant capacity 5000 MT/day Plant economic feasibility, internal rate of(PDF) Coal to Methanol Conversion ResearchGate2023年9月15日 This paper takes the traditional coaltomethanol process (Process 1) as a case to implement direct and indirect electrification, and store renewable electricity in high energy–density methanol production to achieve longterm energy storage and overcome the impact of renewable energy volatility and intermittency on power gridDesign and analysis for chemical process electrification based on Apart from the production of chemicalgrade methanol, the book deals briefly also with fuel methanol production, i e with the production of alcohol mixes One of the many possible routes from coal to methanol is illustrated by a process flow How to Produce Methanol from Coal SpringerLink
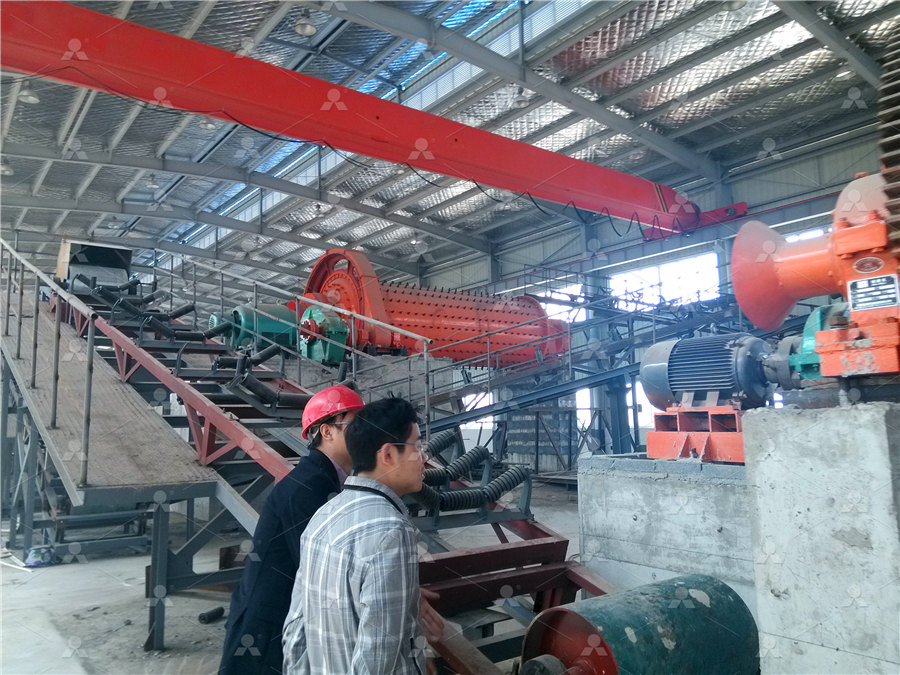
Final Design for CoaltoMethanol Process
The coaltomethanol process used for this project typically incorporates the following process operations, shown in Figure 1 Fig 1 Block diagram of coaltomethanol process First, coal is preprocessed by methods such as crushing, 2022年3月10日 The coaltomethanol (CTM) is an important technical route for methanol productionThe process suffers from high CO 2 emission and low energy efficiency due to the mismatch of H/C (hydrogentocarbon) ratio between raw coal and products Hydrogen production from renewable energy can be introduced into the system to meet the H/C ratio In this paper, Novel coaltomethanol process with nearzero carbon emission 2020年12月4日 Methanol is a clean fuel and an important feedstock for the petrochemical industry Conventionally, the coaltomethanol process generates a substantial amount of CO2 emissions with a low yield of (PDF) Conceptual Design Development of CoalToMethanol Process Download scientific diagram Simplified Methanol Synthesis Process Flow Diagram from publication: Preliminary Screening Technical and Economic Assessment of Synthesis Gas to Fuels and Chemicals Simplified Methanol Synthesis Process Flow Diagram
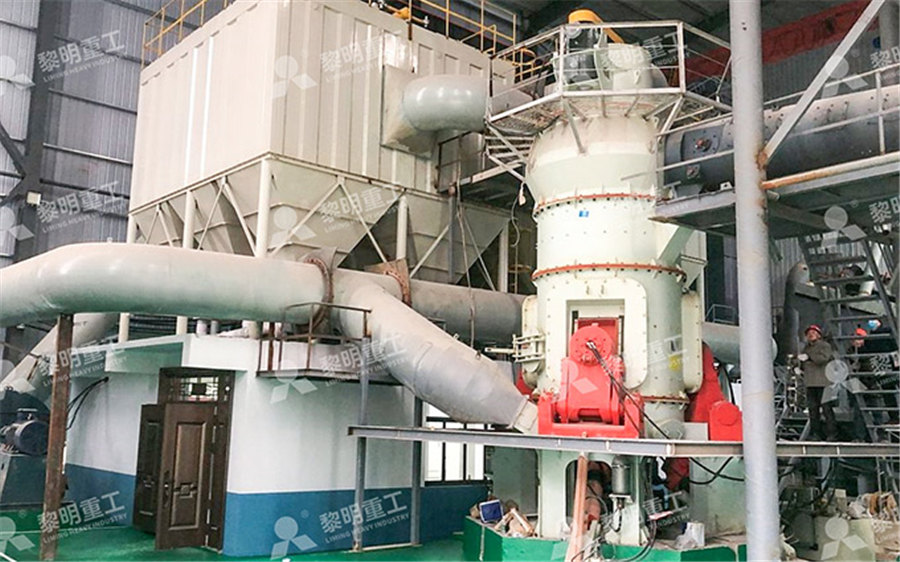
Baseline Analysis of Crude Methanol Production from Coal and
Exhibit 37 Simplified process flow diagram of coal to crude methanol 19 Exhibit 38 Simplified process flow diagram of natural gas to crude methanol 20 Exhibit 39 Coal drying process flow diagram Exhibit 322 Methanol synthesis process flow diagram 2021年8月1日 The conventional methanol process uses desulfurized natural gas as the main feedstock for synthesis gas production by using steam methane reforming Feasibility of power and methanol production by an entrainedflow coal gasification system Energy Fuels, 32 (7) (2018), pp 75957610 Crossref View in Scopus Google Scholar [33]CO2 utilization for methanol production; Part I: Process design 2024年1月27日 COAL TO OLEFINS (CTO) / METHANOL TO OLEFINS (MTO) — PROCESS FLOW DIAGRAMS 14 Process Flow Diagrams — Coal to Olefins (CTO) / Methanol to Olefins (MTO) Highpressure black water flashing valve Highpressure black water flashing valve Synthesis gas venting control valve Black water onoff valve Black water onoff valveProcess Flow Diagrams COAL TO OLEFINS (CTO) / METHANOL 2024年5月1日 The effluents from the reactor in the DMTE route are a mixture of ethanol, methanol, ethyl acetate, and methyl acetate In industrial practice, the process combinedly uses conventional and swingpressure distillation due to the presence of azeotropes [9] shown in Table 1Swingpressure configurations introduce extra columns, resulting in a largescale separation Process synthesis for the separation of coaltoethanol products
.jpg)
CoaltoMethanoltoOlefins: Processes and
Up to 60 MT/day of ethylene can optionally be recovered from the purge gas or used as fuel Methanol, both fresh and recycled (as recovered from aqueous streams), is the feed to the MTP unit Figure 12 (Lurgi, 2003; Wurzel, 2006) This study presents design considerations and an evaluation of a fullscale process chain for methanol and advanced dropin fuel production derived from lignite/solid recovered fuel (SRF) feedstock The plant concept consists of a Process Analysis and Design Considerations of a Low Figure 1 shows a simplified block flow diagram (BFD) of a methanol (MeOH) plant based on coal feedstock Syngas from the gasifier is cooled by generating high pressure (HP) steam in the high temperature (HT) gas cooling system before 1031 Methanol Plant Process ConfigurationsFig 5 Current impact of global natural and anthropogenic activities and of fossilbased methanol production over the commercial Cu–ZnO–Al 2 O 3 catalyst on the PBs, along with the performance of methanol processes using CO 2 captured from coal power plants and renewable hydrogen from various sources and the same catalystPlanttoplanet analysis of CO 2 based methanol processes
.jpg)
A full process optimization of methanol production integrated
2023年3月15日 At present, the coal to methanol process is very mature and has been widely used in industrial production In recent years, many researchers have improved the coal to methanol process, such as cogenerating electricity in the process [1], using green hydrogen to assist the coal to methanol process [2], and integrating the coal to methanol process with the 2023年9月15日 Process simulation and lifecycle analysis indicate that coal to methanol integrated with reverse water gas shift using coal to hydrogen (CTMRWGSCTH) and CTMRWGS with water electrolysis using wind energy process show relatively independent excellent technical and environmental performance, respectivelyDesign and analysis for chemical process electrification based on This document provides a final design for a coaltomethanol process that aims to produce 5000 MT/day of AA grade methanol from Montana subbituminous coal Key aspects of the design include using a Texaco entrainedflow gasifier to gasify the coal, Selexol solvent for acid gas removal from the syngas, water gas shift reactors to achieve a 2:1 H2:CO ratio for methanol Final Design For CoalToMethanol Process: Sheida Saeidi, Josh TechnoEconomic Analysis of Integrating CO2 Hydrogenation to Methanol Unit with Coal to Methanol Process for CO2 Reduction Jingpeng Zhang†, Zhengwen Li†, Zhihe Zhang†, Rong Liu‡, Bozhao Chu§, Binhang Yan†,* †Department of Chemical Engineering, Tsinghua University, Beijing , China ‡Huaneng Clean Energy Research Institute, Beijing , ChinaTechnoEconomic Analysis of Integrating CO2 Hydrogenation to
.jpg)
Process analysis of a novel coaltomethanol technology for
2023年3月26日 Coal chemical technology is crucial to China's clean and efficient coal usage and to guarantee the safety of its energy structure [1,2] The coal chemical process route uses largescale entrainedflow gasification technology to convert coal into CO and H 2, and through the transformation synthesis process, it is converted into highvalue chemicals [3]2024年9月30日 Zhou et al [41] conducted a systematic analysis of the integration of renewable energy with coal to methanol process for high product yield and low CO 2 emission and an excess of H 2 from the H 2 O electrolysis process Consequently, the methanol flow rate increases from 358760 kmol/h to 376629 kmol/h, A new pathway to integrate novel coaltomethanol system with 2016年9月15日 The chain from unexploited coal to methanol product is divided into four processes: coal mining, coal washing and selection, transport and methanol production Hereinto, detailed flow sheet of methanol production process is shown in Fig 4 Detailed description of the flow sheet will be declared in Section 35Carbon footprint evaluation of coaltomethanol chain with the 2018年1月1日 This chapter is an overview of not only common feedstocks used in the production processes for obtaining methanol (natural gases, CO 2, or char/biomass), but also of the historical production processes (such as the BASF process, also known as the “highpressure method,” and the ICI process, also known as the “lowpressure method”) and the most Methanol Production and Applications: An Overview

Substances and energy metabolism of green HydrogenAssisted/Coal
2024年1月5日 Within the oxygen flow networks of the CMOP and GHCMOP systems (Fig 5 (ef)), oxygen metabolism is observed solely in the coaltomethanol and methanoltoolefins processes No oxygen metabolism occurs in the subsequent units (RF1 to RF7, PD1, PD2, etc) following the COD unit2021年9月15日 The conventional coaltomethanol (CTM) process suffers from large CO 2 emission The additional hydrogen supplement to the CTM process can effectively improve the carbon utilization efficiency (GHSV), and SN on the molar flow of all components and methanol yield are illustrated in Fig 8 (a), (b), (c), and (d)Green hydrogen coupling with CO2 utilization of coaltomethanol 2020年6月10日 Methanol is an important feedstock of chemical engineering and energy source, and it is mainly produced by coal route in China The coaltomethanol suffers from serious CO 2 emissions and carbon resource waste since water gas shift is involved in this process to increase hydrogen content of syngas for meeting methanol synthesisA novel coaltomethanol process Highly efficient carbon utilization of coaltomethanol process 2016年8月15日 Coaltomethanol (CTM) is the main methanol production process in China Application of carbon capture and storage (CCS) technology in CTM is a possible way for CO 2 reduction However, the increase of energy consumption caused by CCS and related increase of Green House Gas footprint has to be minimisedA proposed coaltomethanol process with CO ScienceDirect
.jpg)
(PDF) Coal to Methanol Conversion ResearchGate
2018年6月23日 Entrained Flow Fuel T ype Solid Solid Solids or Liquids Fuel Size 5 50 mm Process simulation and engineering economics of a coal to methanol process via gasification View fulltextRegardless of the source of methanol, the MTP process keeps the same configuration up in China in 2010 and two more units followed in line (with a capacity of 470 kta propylene each), their feedstock is coalbased methanol The MTP® MATERIAL FLOWS (OPTIONAL) Energy in and Outputs explanation Material flows Current 2030 DME and METHANOL TO PROPYLENE PROCESS2019年1月26日 Methanol to olefins (MTO) represents a real paradigm shift as the whole process has been demonstrated to be a successful nonpetrochemical route, and the feedstock, methanol, is different from the (PDF) Methanoltoolefins process technology: current •500 MTPD of CO2 is recovered from the flue gas using MHI’s proprietary KS–1™ solvent and injected in synthesis loop for boosting Methanol production •The capacity of Methanol Plant has increased by 300 MTPD with addition of CO2 in synthesis gas mixture as excess H2 is available for the methanol reaction03 METHANOL PRODUCTION
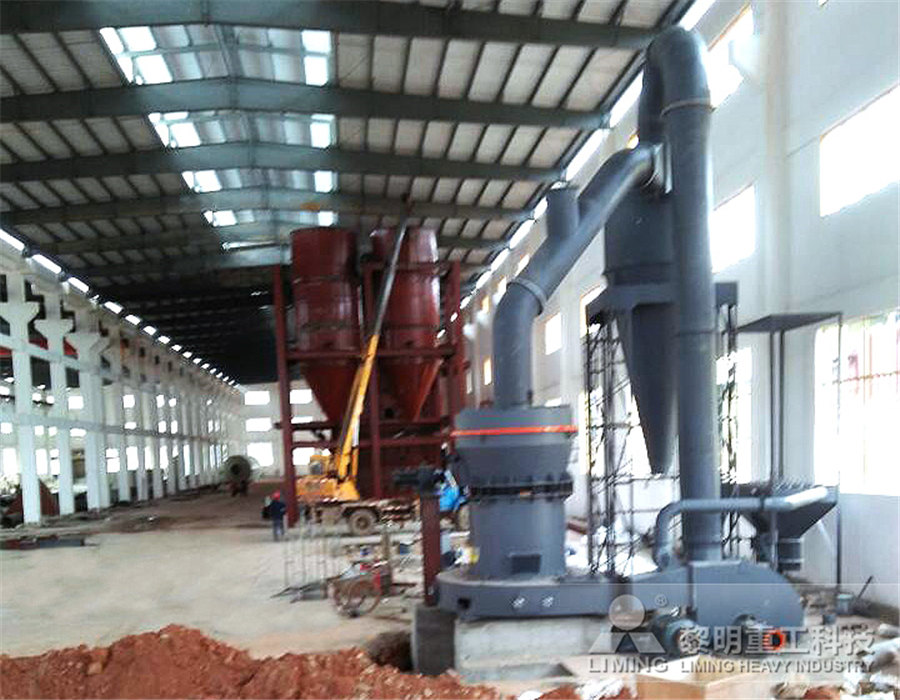
Design and analysis for chemical process electrification based on
2023年9月15日 This paper takes the traditional coaltomethanol process (Process 1) as a case to implement direct and indirect electrification, and store renewable electricity in high energy–density methanol production to achieve longterm energy storage and overcome the impact of renewable energy volatility and intermittency on power gridApart from the production of chemicalgrade methanol, the book deals briefly also with fuel methanol production, i e with the production of alcohol mixes One of the many possible routes from coal to methanol is illustrated by a process flow How to Produce Methanol from Coal SpringerLinkThe coaltomethanol process used for this project typically incorporates the following process operations, shown in Figure 1 Fig 1 Block diagram of coaltomethanol process First, coal is preprocessed by methods such as crushing, Final Design for CoaltoMethanol Process2022年3月10日 The coaltomethanol (CTM) is an important technical route for methanol productionThe process suffers from high CO 2 emission and low energy efficiency due to the mismatch of H/C (hydrogentocarbon) ratio between raw coal and products Hydrogen production from renewable energy can be introduced into the system to meet the H/C ratio In this paper, Novel coaltomethanol process with nearzero carbon emission
.jpg)
(PDF) Conceptual Design Development of CoalToMethanol Process
2020年12月4日 Methanol is a clean fuel and an important feedstock for the petrochemical industry Conventionally, the coaltomethanol process generates a substantial amount of CO2 emissions with a low yield of Download scientific diagram Simplified Methanol Synthesis Process Flow Diagram from publication: Preliminary Screening Technical and Economic Assessment of Synthesis Gas to Fuels and Chemicals Simplified Methanol Synthesis Process Flow DiagramExhibit 37 Simplified process flow diagram of coal to crude methanol 19 Exhibit 38 Simplified process flow diagram of natural gas to crude methanol 20 Exhibit 39 Coal drying process flow diagram Exhibit 322 Methanol synthesis process flow diagram Baseline Analysis of Crude Methanol Production from Coal and 2021年8月1日 The conventional methanol process uses desulfurized natural gas as the main feedstock for synthesis gas production by using steam methane reforming Feasibility of power and methanol production by an entrainedflow coal gasification system Energy Fuels, 32 (7) (2018), pp 75957610 Crossref View in Scopus Google Scholar [33]CO2 utilization for methanol production; Part I: Process design
.jpg)
Process Flow Diagrams COAL TO OLEFINS (CTO) / METHANOL
2024年1月27日 COAL TO OLEFINS (CTO) / METHANOL TO OLEFINS (MTO) — PROCESS FLOW DIAGRAMS 14 Process Flow Diagrams — Coal to Olefins (CTO) / Methanol to Olefins (MTO) Highpressure black water flashing valve Highpressure black water flashing valve Synthesis gas venting control valve Black water onoff valve Black water onoff valve2024年5月1日 The effluents from the reactor in the DMTE route are a mixture of ethanol, methanol, ethyl acetate, and methyl acetate In industrial practice, the process combinedly uses conventional and swingpressure distillation due to the presence of azeotropes [9] shown in Table 1Swingpressure configurations introduce extra columns, resulting in a largescale separation Process synthesis for the separation of coaltoethanol products