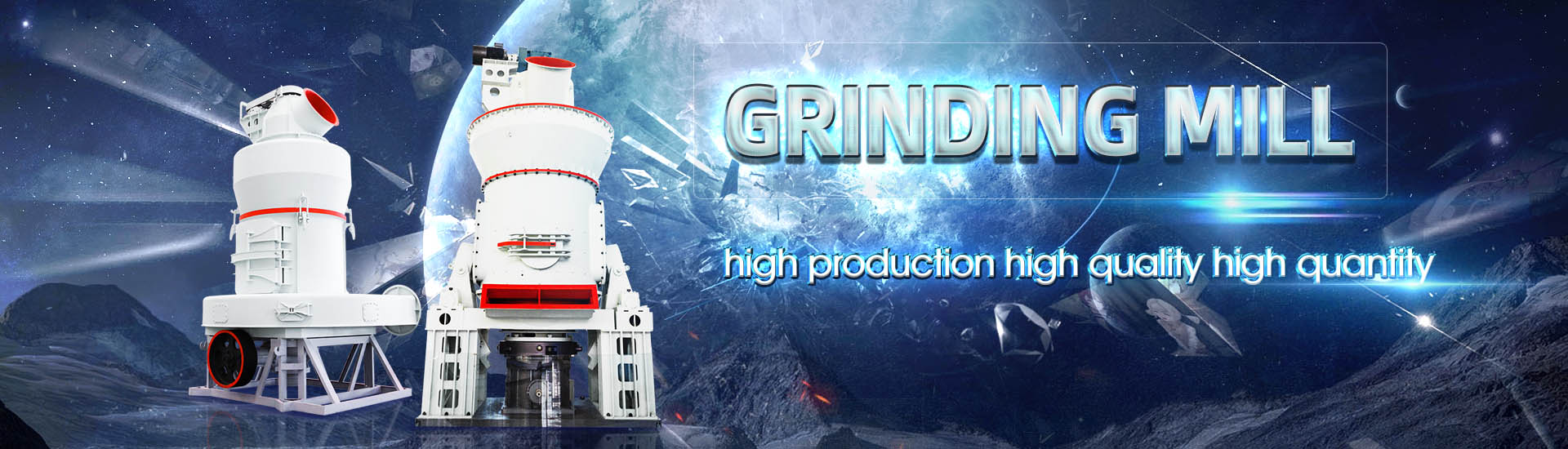
Vertical mill 130 process flow
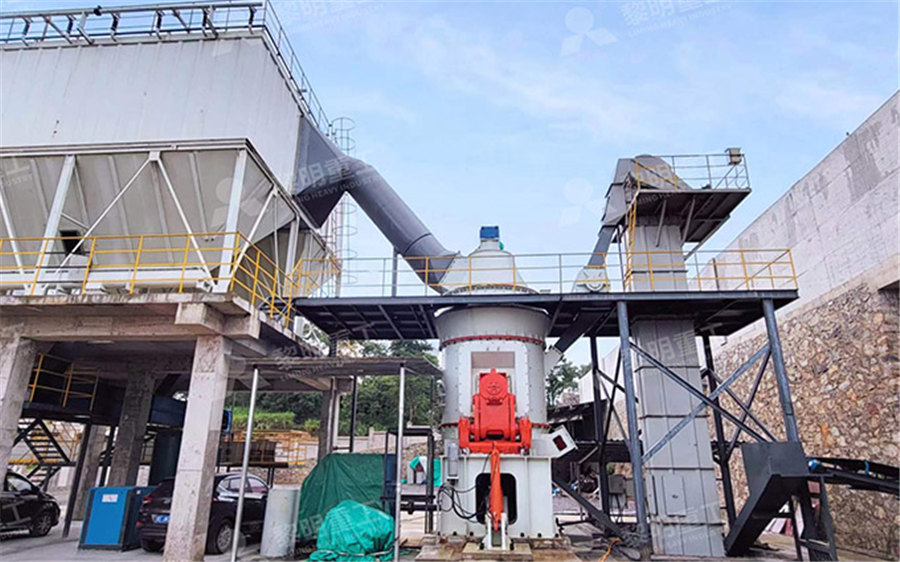
Vertical roller mill for raw Application p rocess materials
The conventional process gas flow of the mill grinding system generally consists of vertical 2017年9月11日 In this study, an extensive sampling study was carried out at vertical roller mill of ESCH Cement Plant in Luxemburg Samples were (PDF) Performance Evaluation of Vertical Roller Mill in Vertical roller mills are widely used for especially grinding of coal, cement raw materials, clinker Performance Evaluation of Vertical Roller Mill in Cement Grinding: The process flow of the sulfuric acid method lithium carbonate vertical roller mill production line is as follows: ① The spodumene or lepidolite ore is transformed and roasted, and after cooling, it is transported to the vertical roller mill for fine News Process Flow Of Lithium Carbonate Vertical
.jpg)
Drais Vertical Media Mill (DPM2206) – Detroit
Drais Buhler Type DCP Mega Vantis ACS 100 PUC Super Flow Vertical Media Perl Mill, Manufactured in 2007, 691 liter total volume of vessel, jacketed grinding chamber, 40 hp motor, maximum pressure rating for vessel is 3 bar or 45 psi, According to the requirements of construction waste treatment, the process flow of construction waste vertical mill is shown in the above figure: the construction waste particles (with a particle size of ≤ 20 mm) processed through sorting, Can Construction Waste Be Treated By Vertical Mill?FIGURE 4 Particle size distributions of collected samples (Survey 2) Bond work indices and breakage characteristics under compression were determinedPerformance Evaluation of Vertical Roller Mill in Cement Vertical roller mills (VRMs) require optimization of key process parameters to achieve maximum grinding capacity at minimum energy consumption Operators should continuously monitor parameters like product fineness, classifier speed, grinding force, air flow, and power usage to maintain optimal performance as feed materials change Relevant parameters that influence Docslide Net Optimization of Vertical Raw Mill Operation PDF
.jpg)
Optimization of Vertical Raw Mill Operation PDF
The document discusses optimization and operation of vertical roller mills (VRMs) Key points include: 1) Continuously monitor and adjust process parameters to find the optimum operating conditions of highest capacity and lowest power consumption 2) Relevant process parameters to monitor include product rate, fineness, classifier speed, grinding force, power consumption, air 130160: ≤2%: 2000: HLM42/4P: 3400: 160200: ≤2%: 2500: HLM44/4P: 3700: 190240: ≤2%: 3000: HLM45/4P: 3700: 240300: the qualified fine powder will flow out the mill and be collected by dust collector, This cycle is the whole process of grinding HLM vertical roller mill using standard modules to design and fabricate Best HLM Vertical Roller Mill Manufacturer and FactoryCLS Attritors – Stirred Vertical Ball Mill Lime Slaker The patented CLS Attritor Stirred Vertical Ball Mill Lime Slaker operates in continuous processing mode and has been used successfully in power generating plants for flue gas desulphurization (FGD) The Attritor will slake the lime as well as grind the inert grit, eliminating grit separation andVertical Ball Mill Vertical Media Mill Union ProcessVertical Mill PDF Free download as PDF File (pdf), Text File (txt) or read online for free The document provides instructions for preparing and starting a Loesche mill Key steps include: 1) Checking oil levels, filters, valves and equipment before start 2) Preheating the empty mill for 12 hours to prevent condensation, gradually increasing temperature while ensuring roller protectionVertical Mill PDF PDF Mill (Grinding) Scribd
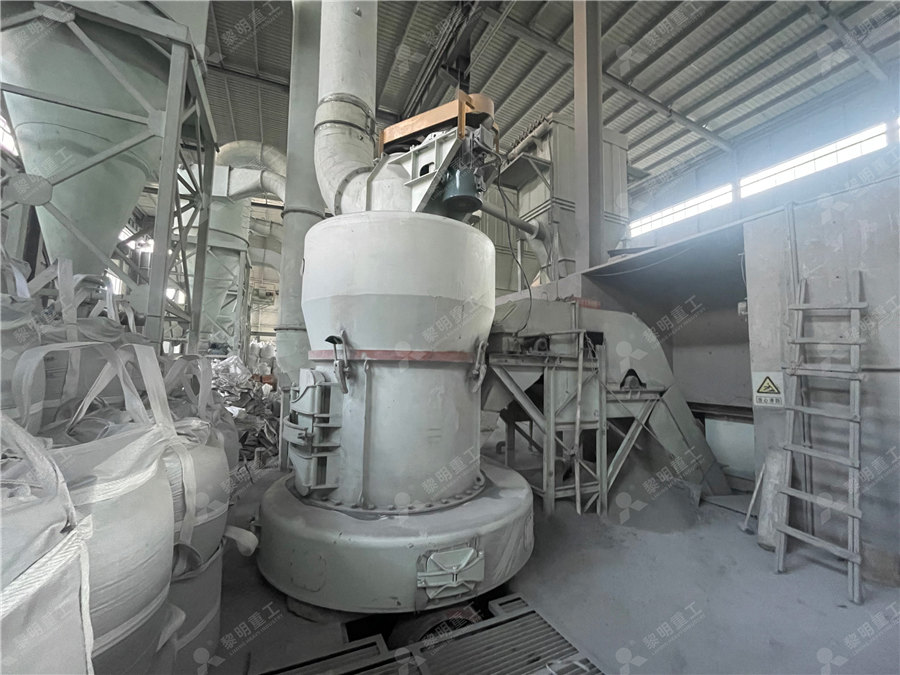
Cements ground in the vertical roller mill fulfil the
2013年3月1日 The mill provides the technical options to vary process parameters like airflow, mass flow, grinding force and classifier speed in a wide range and is equipped to analyze the internal circulating 2020年8月12日 This study shows the performance of a currently running vertical roller coal mill (VRM) in an existing coalfired power plant In a power plant, the coal mill is the critical equipment, whose An investigation of performance characteristics and 2009年1月31日 In another study, a simple matrix model was used for modelling the grinding process in a cement vertical roller mill (CKP), and multiple grinding cycles were taken into account to obtain the final Grinding process within vertical roller mills ResearchGateTherefore, it is critical for cement plant operations to increase the monitoring and control of a vertical raw mill energy process This technology has attracted the interest of the cement industry with its proven benefit Browse Preprints process flow sheets are created by connecting material and energy streams 130 08971 13684 Assessment of the thermodynamics efficiency of a cement vertical
.jpg)
Vertical Mill Calculations PDF Mill (Grinding) Nozzle
Vertical Mill Calculations Free download as Powerpoint Presentation (ppt / pptx), PDF File (pdf), Text File (txt) or view presentation slides online There are two main layouts for a vertical roller mill (VRM) system, with product collection in cyclones or a filter The power consumption of a VRM is calculated using factors like the specific grinding pressure, roller dimensions, Vertical Roller Mill Free download as PDF File (pdf), Text File (txt) or read online for free Vertical Roller Mill is designed to solve problems of low capacity and high consumption in traditional mills It uses a reliable structure and reasonable process flow that incorporates drying, milling, classifying, and elevating The Vertical Mill allows for high production of powders Vertical Roller Mill PDF Mill (Grinding) IndustriesIt moves to the edge of the mill due to centrifugal force and the grinding roller Shredded material overflows from the edge At the same time, wind from the nozzle ring speeds to the efficient separator It is with the vertical mill After the separator, meal returns to the mill wheel and grinds again The fine powder is ground with the air flowTable Roller Mill Vertical MillVertical Roll Mill Series Extreme industrial applications require reliable gear units all year round Gearboxes with longer bearing life, improved power density and increased product lifecycle are key factors in the decision making process David Brown Santasalo’s vertical roller mill series delivers power, durability and reliability even underVertical Roll Mill Series dbsantasalo
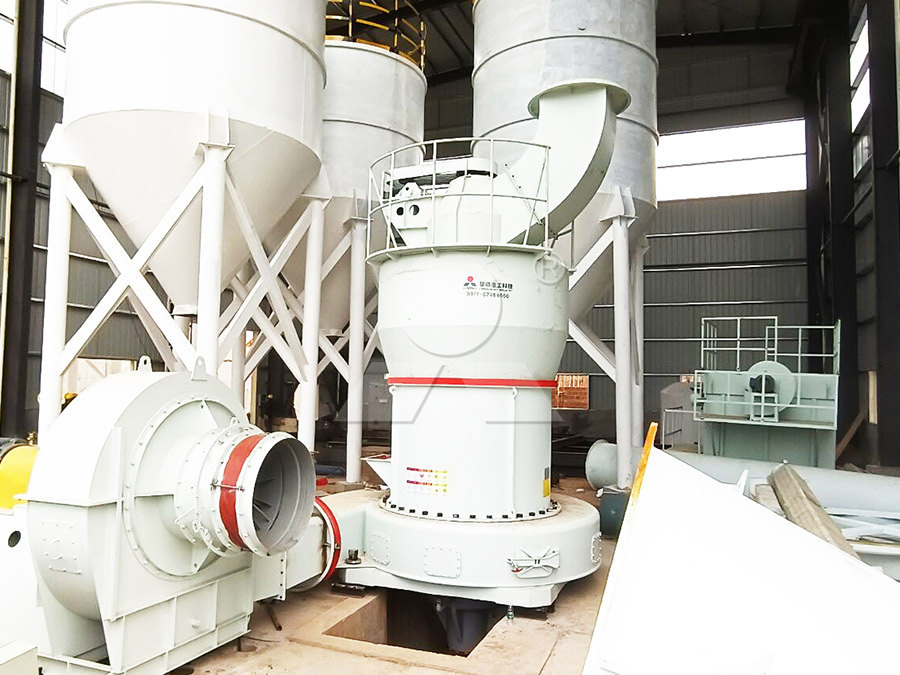
Treatment of olive mill wastewater in pilotscale vertical flow
2011年6月1日 Treatment of olive mill wastewater in pilotscale vertical flow constructed wetlands Author links open overlay panel Elissavet Herouvim a, The extraction process produces an aqueous phase formed by the water content of the fruit combined with the water used to wash and process the olives 130 g/d m 2, 15 g/d Download scientific diagram Technical specifications of vertical roller coal mill from publication: An investigation of performance characteristics and energetic efficiency of vertical roller Technical specifications of vertical roller coal millHD Process Supply vertical and inline colloid Mills The vertical colloid mill in the photo graph attached comes with Hopper, a recirculation function if required and an adjustable rotor stated gap in order to allow variation in the product output Colloid mills work on the rotorstator principle: a rotor turns at high speeds (1400 2800 RPM)Vertical Colloid Mill HD Process NZ Ltd Introduction to Vertical Roller Mill Free download as Powerpoint Presentation (ppt / pptx), PDF File (pdf), Text File (txt) or view presentation slides online This document provides an introduction to vertical roller mills for production optimization It discusses key aspects of vertical roller mills including: Vertical roller mills grind materials into an extremely fine Introduction To Vertical Roller Mill PDF Mill (Grinding
.jpg)
Comparing ball and vertical mills performance: An industrial case study
circuit) Therefore, the vertical mill showed performance significant better than the ball mills for the regrinding circuit of Germano concentrator II Its also possible to note in figure 7 that k from vertical mill decreased along the year, even reaching The mill provides the technical options to vary process parameters like airflow, mass flow, Operational experience from the United States’ first vertical mill for cement grinding In: Cement Industry Technical Conference IEEE, pp 241–249 Tamashige, T, Obana, H, Hamaguchi, M, 1991 Operational results of OK series roller millOperational parameters affecting the vertical roller mill grindability affects the capacity of grinding, type of mill and roller pressure The capacity of the mill is calculated Using G K * D 251 Where, G is capacity of the mill, K1 is roller mill coefficient and D is table diameter 2 PROCESS CONTROL OF VRM The conventional control system of VRM composed of field staff to adjust the few processPROCESS CONTROL FOR CEMENT GRINDING IN VERTICAL ROLLER MILL Download scientific diagram VERTICAL ROLLER MILL TECHNICAL DETAILS from publication: Grinding process optimization — Featuring case studies and operating results of the modular vertical roller VERTICAL ROLLER MILL TECHNICAL DETAILS ResearchGate
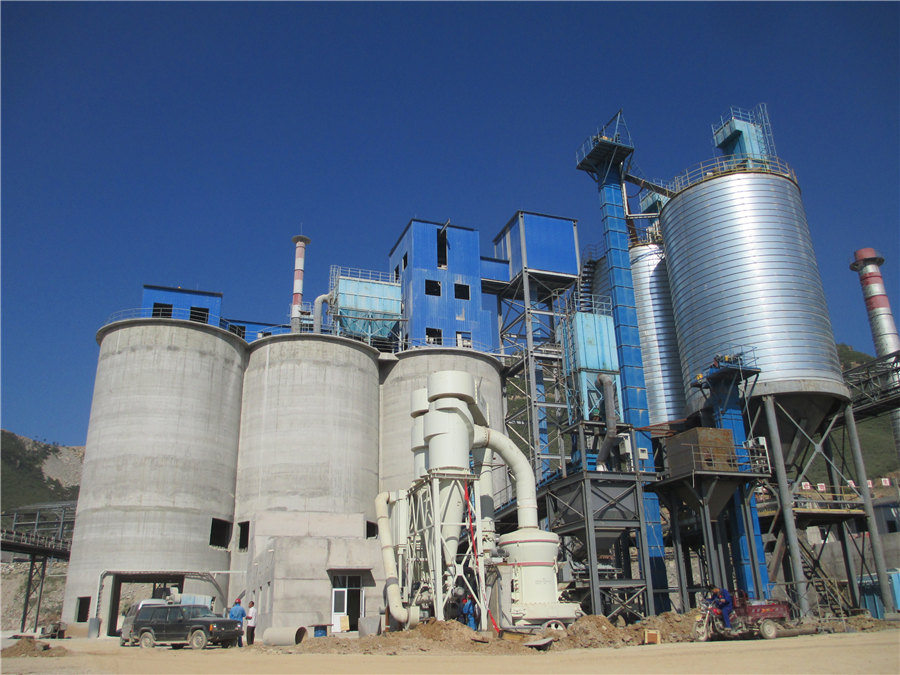
Important Operation Tips For Cement Vertical Mill
Vertical mill is a equipment that grinds materials by relative rolling of a the wearability and the moisture In the vertical grinding operation process, to form a stable material layer, it is required that the grinding (above 130 ° C), it will also cause damage to the equipment The dividing wheel in the lower part of The process flow of the sulfuric acid method lithium carbonate vertical roller mill production line is as follows: ① The spodumene or lepidolite ore is transformed and roasted, and after cooling, it is transported to the vertical roller mill for fine News Process Flow Of Lithium Carbonate Vertical Drais Buhler Type DCP Mega Vantis ACS 100 PUC Super Flow Vertical Media Perl Mill, Manufactured in 2007, 691 liter total volume of vessel, jacketed grinding chamber, 40 hp motor, maximum pressure rating for vessel is 3 bar or 45 psi, Drais Vertical Media Mill (DPM2206) – Detroit According to the requirements of construction waste treatment, the process flow of construction waste vertical mill is shown in the above figure: the construction waste particles (with a particle size of ≤ 20 mm) processed through sorting, Can Construction Waste Be Treated By Vertical Mill?
.jpg)
Performance Evaluation of Vertical Roller Mill in Cement
FIGURE 4 Particle size distributions of collected samples (Survey 2) Bond work indices and breakage characteristics under compression were determinedVertical roller mills (VRMs) require optimization of key process parameters to achieve maximum grinding capacity at minimum energy consumption Operators should continuously monitor parameters like product fineness, classifier speed, grinding force, air flow, and power usage to maintain optimal performance as feed materials change Relevant parameters that influence Docslide Net Optimization of Vertical Raw Mill Operation PDFThe document discusses optimization and operation of vertical roller mills (VRMs) Key points include: 1) Continuously monitor and adjust process parameters to find the optimum operating conditions of highest capacity and lowest power consumption 2) Relevant process parameters to monitor include product rate, fineness, classifier speed, grinding force, power consumption, air Optimization of Vertical Raw Mill Operation PDF130160: ≤2%: 2000: HLM42/4P: 3400: 160200: ≤2%: 2500: HLM44/4P: 3700: 190240: ≤2%: 3000: HLM45/4P: 3700: 240300: the qualified fine powder will flow out the mill and be collected by dust collector, This cycle is the whole process of grinding HLM vertical roller mill using standard modules to design and fabricate Best HLM Vertical Roller Mill Manufacturer and Factory
.jpg)
Vertical Ball Mill Vertical Media Mill Union Process
CLS Attritors – Stirred Vertical Ball Mill Lime Slaker The patented CLS Attritor Stirred Vertical Ball Mill Lime Slaker operates in continuous processing mode and has been used successfully in power generating plants for flue gas desulphurization (FGD) The Attritor will slake the lime as well as grind the inert grit, eliminating grit separation and