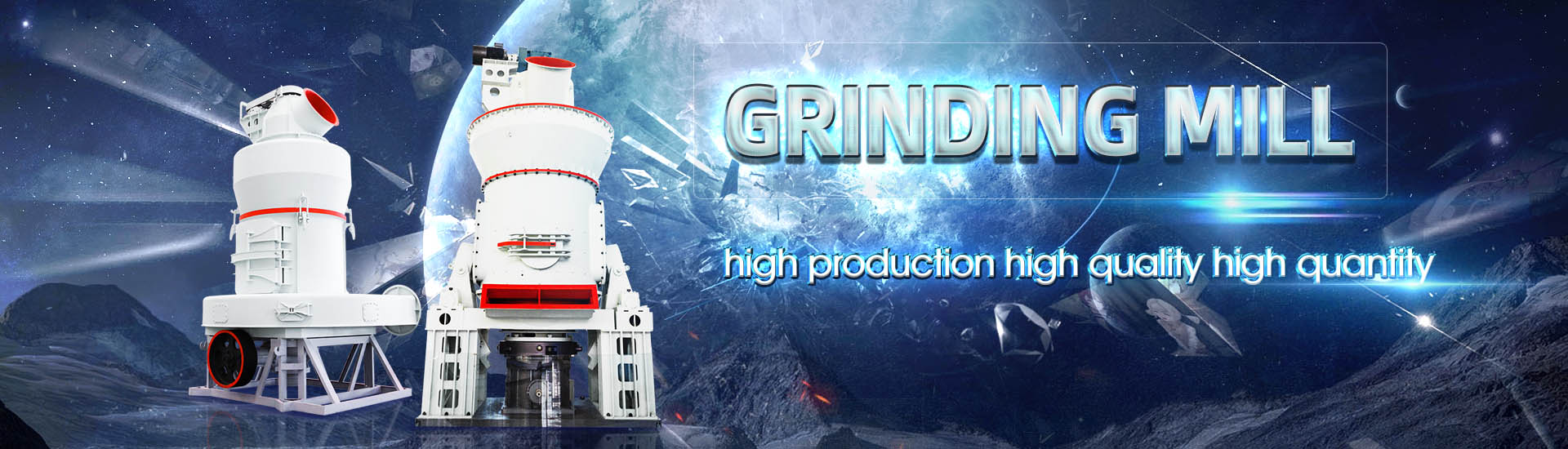
Aluminum ash, overhaul slag, aluminum electrolyte paste production process
.jpg)
Research Progress of Electrolytic Aluminum Overhaul Slag Disposal
2023年4月25日 This article analyzes and summarizes the composition and hazards of the overhaul slag and the current development status of domestic and international electrolytic Coal gangue is a byproduct of the production of coalassociated minerals, Review of Research on the Pr2023年8月1日 The main components of overhaul slag are aluminum and silicon oxides These components could be dissolved in the molten cryolitebased salt system (ie, electrolyte) in the Dissolution behavior of overhaul slag from aluminum reduction 2022年12月12日 In this paper, the first ultrahigh pressure contact molding technology was used to prepare highperformance building materials with aluminum ash and calcium carbide slag Comprehensive performance study of aluminum ash and calcium
.jpg)
Comprehensive performance study of aluminum ash and calcium
2022年12月12日 Aluminum ash is a large amount of industrial solid waste produced by the electrolytic aluminum industry, and calcium carbide slag is an alkaline industrial solid waste The invention discloses a treatment process of overhaul slag of an aluminum electrolytic cell, which comprises the following steps: sorting overhaul residues of an aluminumCNA Treatment process of aluminum electrolysis cell Aluminium ash and slag are produced from molten slag cooling in the electrolytic aluminium production process,the recycling and utilization of the electrolytic aluminium ash and slag is Recycling and Utilization of the Electrolytic Aluminium Ash and SlagDuring a longterm operation of the aluminum electrolysis cell, the molten salts continuously infiltrate and corrode the pot lining, resulting in a huge amount of hazardous waste after theElectrolytic cell spent lining Fig 2 Overhaul slags of the
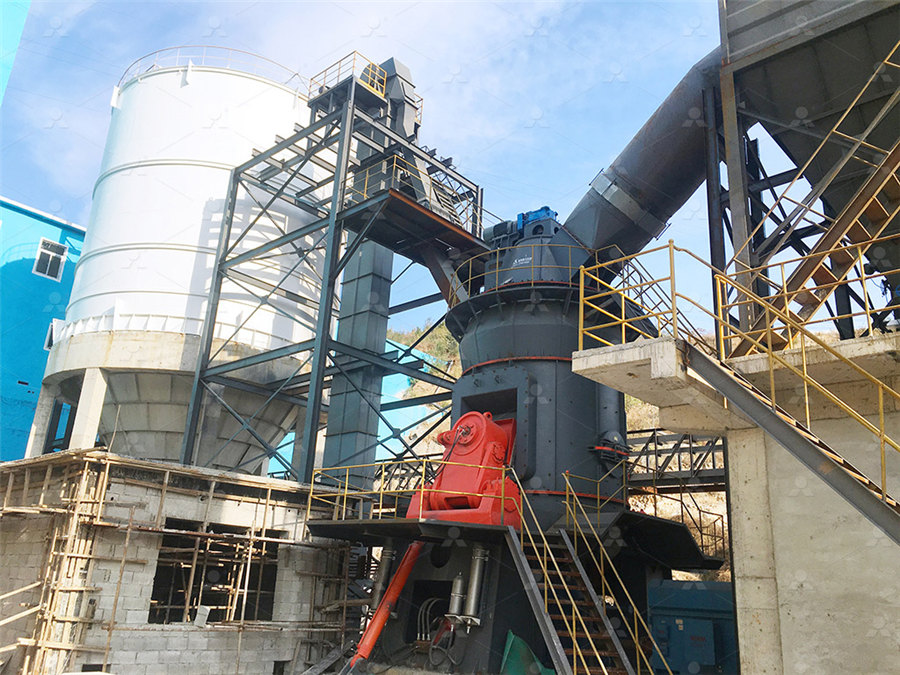
Cleaner Process for the Selective Extraction of Lithium
2024年7月24日 The lithium was selectively recovered and enriched from spent aluminum electrolyte slag by using calcium salt roasting transformation followed by HBL121solvent extraction The new process realizes a high leaching 2023年4月25日 This article analyzes and summarizes the composition and hazards of the overhaul slag and the current development status of domestic and international electrolytic aluminum overhaul slag disposal, and points out the 电解铝大修渣处置研究进展In this paper, the ultrahigh pressure contact molding technology is used for the first time to prepare highperformance building materials with aluminum ash and calcium carbide slag as Comprehensive performance study of aluminum ash and calcium The method comprises the following steps: 1) Obtaining electrolytic aluminum overhaul residues with fluorine content and pH exceeding the standard; obtaining nonstrong alkaline calciumcontaining material, wherein the content of free calcium is more than 4wt%, and the pH value is 4583; 2) Mixing and stirring a certain amount of crushed nonstrong alkaline calcium CNA Harmless electrolytic aluminum overhaul slag
.jpg)
电解铝大修渣处置研究进展
2023年4月25日 WU H Y, SU N, QIN J, et al Application process of molten iron desulfurization and electrolytic aluminum overhaul slag[C] Wuxi: Steelmaking Production New Process, New Technology, New Product Seminar, 2019 [4] 2021年10月1日 And all aluminum electrolysis production ensures that the cryolite ratio of aluminum electrolyte is below 30, and the electrolyte is called an acid electrolyte Based on publicly reported literature, LiF exists as Na 2 LiAlF 6 in the acid electrolyte, whereas LiF exists as its entity for cryolite ratio greater than or equal to 30 (Gao et al, 2002; Li, 2009, Zhang and A novel approach for lithium recovery from waste lithium Spent aluminum electrolyte slag is a byproduct produced during the electrolysis of aluminum and contains elements such as F, Al, Na, and Li It is a toxic and harmful substance with a stable and complex structure As a consequence of fluorine pollution and low lithium recovery efficiency in the traditional hydro metallurgy process, a novel cleaner production technology was developed Cleaner Process for the Selective Extraction of Lithium from Spent There has been increased interest in the United States in developing the technology to recover aluminum from nonbauxite sources stemming from a need to develop do1J1,estic aluminum sources!, 2 Several domestic sources of aluminum have been defined by the US Bureau of Mines,3 the types and approximate tonnages of these are listed in Table I Patterson and Dyni Chapter 2 Production and Processing of Aluminum 21 Extraction of Aluminum
.jpg)
Fluorineretaining agent for overhaul slag of aluminum
2020年1月2日 The invention discloses a fluorineretaining agent for overhaul slag of an aluminum electrolytic cell The fluorineretaining agent comprises the following components of, by mass, 80100 parts of calcium sulfate, 6080 parts of calcium oxide, 5070 parts of calcium hydroxide and 3060 parts of calcium chloride The invention further discloses a method for The invention discloses a treatment process of overhaul slag of an aluminum electrolytic cell, which comprises the following steps: sorting overhaul residues of an aluminum electrolytic cell to obtain carbonaceous waste and refractory waste, respectively crushing and ballmilling to obtain carbon powder and ceramic powder, mixing the carbon powder and the ceramic powder in CNA Treatment process of aluminum electrolysis cell overhaul As the main solid waste of the electrolytic aluminum industry, overhaul slag contains a large amount of hazardous substances, and how to treat it harmlessly and efficiently recover the valuable substances in it has become an urgent problem in the aluminum industry in recent years This article analyzes and summarizes the composition and hazards of the overhaul slag and Research Progress of Electrolytic Aluminum Overhaul Slag DisposalWith the rapid development of aluminium smelting industry in China, millions of tons of hazardous wastes such as carbon slag, overhaul slag and aluminum ash are generated every year In order to promote the refined management of hazardous wastes in China, an indepth research had been done, the current generation process link, pollution characteristics, utilization and Present situation of production, utilization and disposal of
.jpg)
(PDF) Aluminum Slag Separation Process Analysis Through a
2021年5月1日 Aluminum Slag Separation Process Analysis Through a 8% of the total energy needed to obtain primary aluminum by the electrolyte process production of aluminum via recycling is 2020年12月1日 A hydrometallurgical process was developed to extract lithium from a spent lithiumcontaining aluminum electrolyte, reduce the stacking of spent aluminum electrolyte, and recover the valuable elements In this study, we extracted lithium from an electrolyte using the following three steps: 1) leaching with HNO 3 − Al(NO 3) 3, 2) neutralizing the leachate Novel process for the extraction of lithium carbonate from spent The main components of aluminum ash include single aluminum, aluminum oxide (Al 2 O 3), aluminum nitride (AlN), aluminum carbide (Al 4 C 3), fluoride and chlorinated salts, silicon, iron and other oxide (Kang et al 2022) Aluminum ash slag can be divided into primary aluminum ash and secondary aluminum ash accordingAssessing Environmental Impact of Aluminum Ash Disposal in 2023年9月1日 Lithium (Li)bearing aluminum electrolyte slag is an inevitable byproduct of the aluminum industry, and improper disposal or stacking it may lead to potential environmental hazards This study employed hydrometallurgical Clean Process for Selective Recovery of Lithium
.jpg)
Assessing Environmental Impact of Aluminum Ash Disposal in
2024年6月4日 In the process of primary aluminum production, aluminum alloy processing and waste aluminum recycling, a large amount of aluminum ash will be produced, and every 1 t of molten metal aluminum produced by recycled aluminum can produce 8–15% of aluminum ash residue (Tsakiridis 2012; Meshram and Singh 2018)CNA CN96A CN9A CNA CN A CN A CN A CN 9 A CN9 A CN 9A CN A CN A CN A Authority CN China Prior art keywords waste waste material silicon carbide treatment method recovery Prior art date Legal CNA Recovery treatment method of electrolytic aluminum ash 2024年1月1日 Semantic Scholar extracted view of "Efficient lithium recovery from electrolytic aluminum slag via an environmentally and Jianming Gao and Fangqin Cheng}, journal={Journal of Cleaner Production recovery from waste lithiumcontaining aluminum electrolyte by a roastingleaching process Shaohua Wu W Tao +4 Efficient lithium recovery from electrolytic aluminum slag via an 2021年11月1日 PDF Aluminum slag ash commonly used as road and river embankments cement and the consolidation process in this study is the production of paving blocks When compared The Influence of Aluminum Slag Ash for Paving Block Production
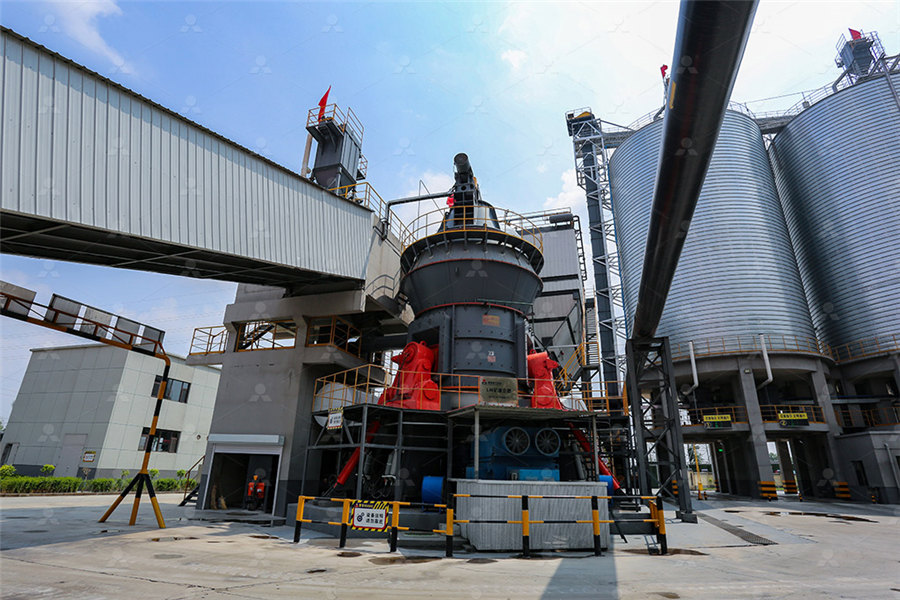
Technical Report International Aluminium
About 2 million tons of aluminum slag are generated during the process of primary aluminum smelting, fabrication and processing, and waste aluminum recycling in China The main components in the aluminum slag are metallic aluminum, alumina, aluminum nitride, fluoride salts, chloride salts, as well as the2014年5月1日 For many years, efforts have been made to find alternative smelting technologies to replace the centuriesold energyintensive HallHéroult process (Cochran, 2016;Kvande and Drablos, 2014)(PDF) The Aluminum Smelting Process and Innovative2021年7月30日 Due to Micron alumina's simple manufacturing process, the need for production equipment and technology is relatively mature, so the production cost of micron alumina is relatively low, and for the A Review of Secondary Aluminum Production and Its Byproducts On August 2nd, China Nonferrous Metals Industry Association organized an expert meeting on scientific and technological achievements in Kunming, Yunnan Province, and completed the "electrolytic aluminum overhaul slag" jointly Electrolytic aluminum overhaul slag harmless
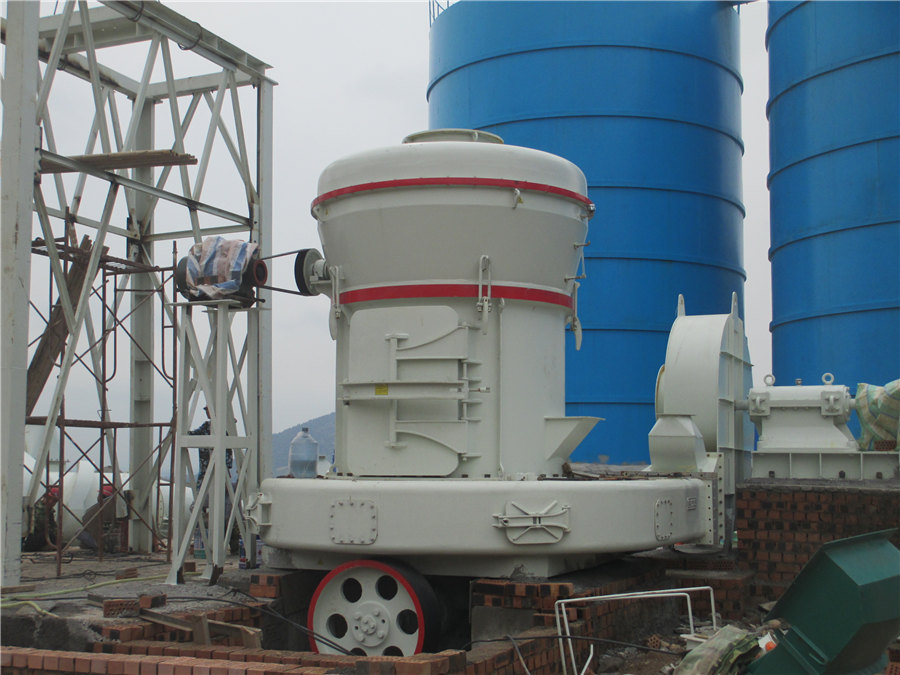
Regeneration of raw materials for aluminum electrolysis from
2023年5月20日 Due to chemical corrosion and erosion by molten aluminum liquid and electrolyte, the carbon anode of the aluminum electrolytic cell would fall off into the electrolyte during the primary aluminum electrolysis process to produce spent anode carbon (SCA), which has been listed as one of the typical hazardous solid wastes in the National Hazardous Waste 2024年2月1日 Efficient lithium recovery from electrolytic aluminum slag via an environmentally friendly process: Leaching behavior and mechanismEfficient lithium recovery from electrolytic aluminum slag via an 2022年2月25日 Industrial aluminium production is based on patents filed by Charles Martin Hall (1863–1914) in the USA in July 1886 [] and Paul Louis Toussaint Héroult (1863–1914) in France in April 1886 [] (Fig 2)Both developed similar principles to produce aluminium, namely, alumina (Al 2 O 3) dissolved in a cryolite (Na 3 AlF 6)based molten salt electrolyte, commonly called Aluminium production process: from Hall–Héroult to modern 1 process, invented in the 19th century, is by far the most important process used in the production of aluminum oxide from bauxite The process has been refined and improved since its inception Fig 22 shows that the production of alumina is a complex chemical process The aluChapter 2 Production and Processing of Aluminum The
.jpg)
Selective preparation of lithium carbonate from overhaul slag by
2024年5月1日 The reason is that the lithium content in the overhaul slag is relatively low, and the minimum amount of sulfuric acid is enough to completely transform the lithium compound into NaLi(SO 4) More aluminum compounds are converted to NaAl (SO 4) 2, when m(H 2 SO 4)/m(overhaul slag) increase from 10 to 14Electrolytic aluminum is an industry with high energy consumption and high pollution, and it faces many difficulties and challenges to realize intelligent control In order to solve the above problems, this paper expounds the current development status of intelligent control of electrolytic aluminum process, the composition of intelligent control optimization process system of electrolytic Optimization of Electrolytic Aluminum Production Process by 2024年6月29日 Aluminum electrolyte is a necessity for aluminum reduction cells; however, its stock is rising every year due to several factors, resulting in the accumulation of solid waste Currently, it has become a favorable material for the resources of lithium, potassium, and fluoride In this study, the calcification roasting–twostage leaching process was introduced to extract Stepwise extraction of lithium and potassium and recovery of 2023年10月1日 The aluminum electrolyte is the core part of the electrolytic production process of aluminum In contrast, lithiumrich aluminum electrolytes can cause problems such as reduced production temperature, decreased alumina solubility, increased precipitation at the bottom of the electrolytic cell, and poor stability in the aluminum electrolytic cell [ 7 , 8 ]Chemical Engineering and Processing Process Intensification

A Review of Secondary Aluminum Production and Its Byproducts
2021年7月30日 Secondary aluminum production is required for the conservation of the environment It can significantly reduce greenhouse gas emissions and energy consumption and reduce the consumption of alumina, a source of primary aluminum Secondary aluminum production requires sorting processes for the metal scrap before starting the refining process The method comprises the following steps: 1) Obtaining electrolytic aluminum overhaul residues with fluorine content and pH exceeding the standard; obtaining nonstrong alkaline calciumcontaining material, wherein the content of free calcium is more than 4wt%, and the pH value is 4583; 2) Mixing and stirring a certain amount of crushed nonstrong alkaline calcium CNA Harmless electrolytic aluminum overhaul slag 2023年4月25日 WU H Y, SU N, QIN J, et al Application process of molten iron desulfurization and electrolytic aluminum overhaul slag[C] Wuxi: Steelmaking Production New Process, New Technology, New Product Seminar, 2019 [4] 电解铝大修渣处置研究进展2021年10月1日 And all aluminum electrolysis production ensures that the cryolite ratio of aluminum electrolyte is below 30, and the electrolyte is called an acid electrolyte Based on publicly reported literature, LiF exists as Na 2 LiAlF 6 in the acid electrolyte, whereas LiF exists as its entity for cryolite ratio greater than or equal to 30 (Gao et al, 2002; Li, 2009, Zhang and A novel approach for lithium recovery from waste lithium
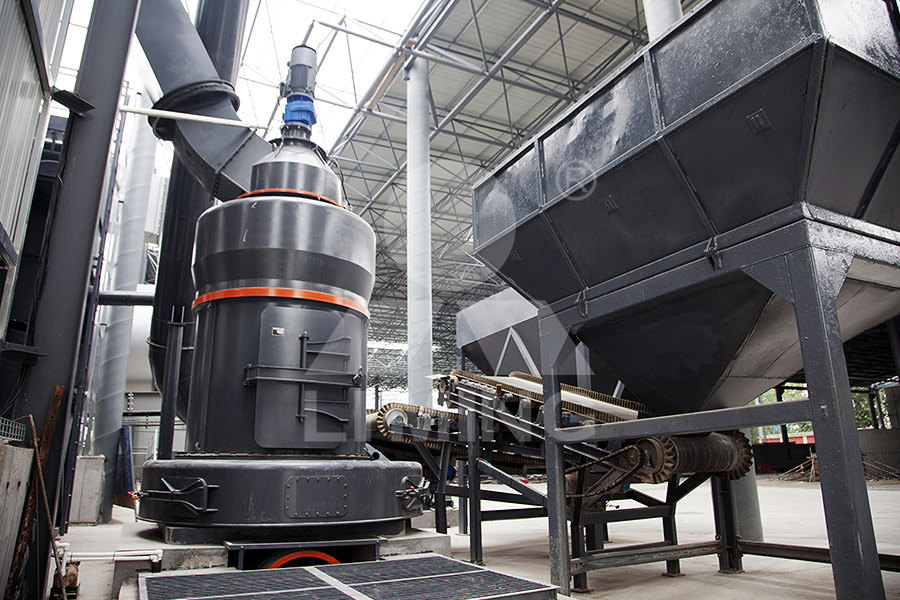
Cleaner Process for the Selective Extraction of Lithium from Spent
Spent aluminum electrolyte slag is a byproduct produced during the electrolysis of aluminum and contains elements such as F, Al, Na, and Li It is a toxic and harmful substance with a stable and complex structure As a consequence of fluorine pollution and low lithium recovery efficiency in the traditional hydro metallurgy process, a novel cleaner production technology was developed There has been increased interest in the United States in developing the technology to recover aluminum from nonbauxite sources stemming from a need to develop do1J1,estic aluminum sources!, 2 Several domestic sources of aluminum have been defined by the US Bureau of Mines,3 the types and approximate tonnages of these are listed in Table I Patterson and Dyni Chapter 2 Production and Processing of Aluminum 21 Extraction of Aluminum2020年1月2日 The invention discloses a fluorineretaining agent for overhaul slag of an aluminum electrolytic cell The fluorineretaining agent comprises the following components of, by mass, 80100 parts of calcium sulfate, 6080 parts of calcium oxide, 5070 parts of calcium hydroxide and 3060 parts of calcium chloride The invention further discloses a method for Fluorineretaining agent for overhaul slag of aluminum The invention discloses a treatment process of overhaul slag of an aluminum electrolytic cell, which comprises the following steps: sorting overhaul residues of an aluminum electrolytic cell to obtain carbonaceous waste and refractory waste, respectively crushing and ballmilling to obtain carbon powder and ceramic powder, mixing the carbon powder and the ceramic powder in CNA Treatment process of aluminum electrolysis cell overhaul
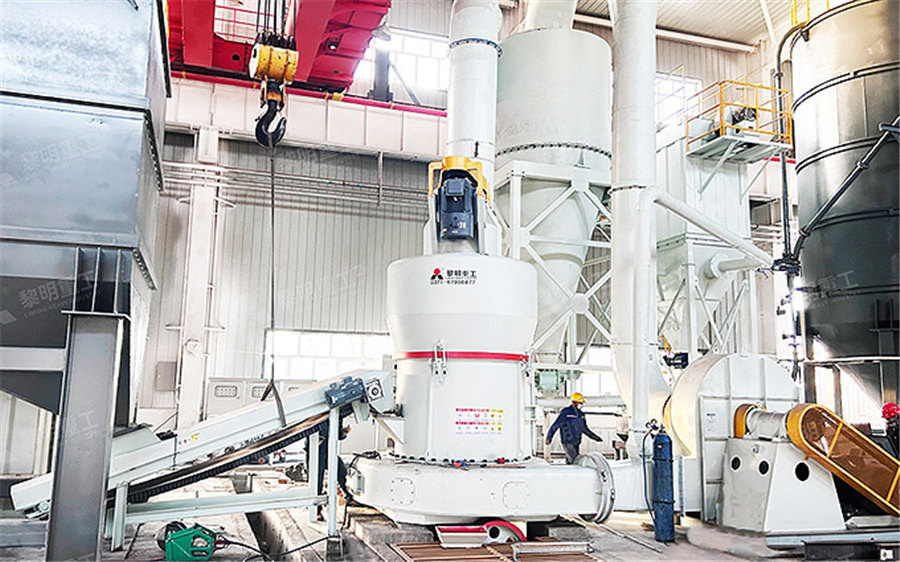
Research Progress of Electrolytic Aluminum Overhaul Slag Disposal
As the main solid waste of the electrolytic aluminum industry, overhaul slag contains a large amount of hazardous substances, and how to treat it harmlessly and efficiently recover the valuable substances in it has become an urgent problem in the aluminum industry in recent years This article analyzes and summarizes the composition and hazards of the overhaul slag and With the rapid development of aluminium smelting industry in China, millions of tons of hazardous wastes such as carbon slag, overhaul slag and aluminum ash are generated every year In order to promote the refined management of hazardous wastes in China, an indepth research had been done, the current generation process link, pollution characteristics, utilization and Present situation of production, utilization and disposal of 2021年5月1日 Aluminum Slag Separation Process Analysis Through a 8% of the total energy needed to obtain primary aluminum by the electrolyte process production of aluminum via recycling is (PDF) Aluminum Slag Separation Process Analysis Through a