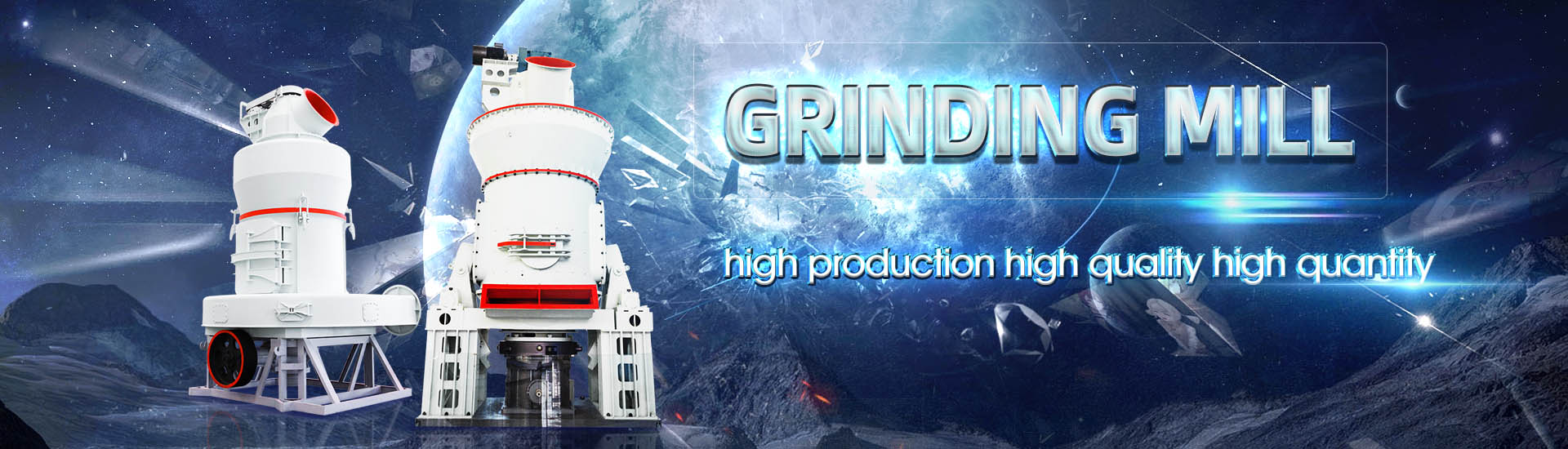
Ball mill 200 mesh silicon micropowder particle size distribution
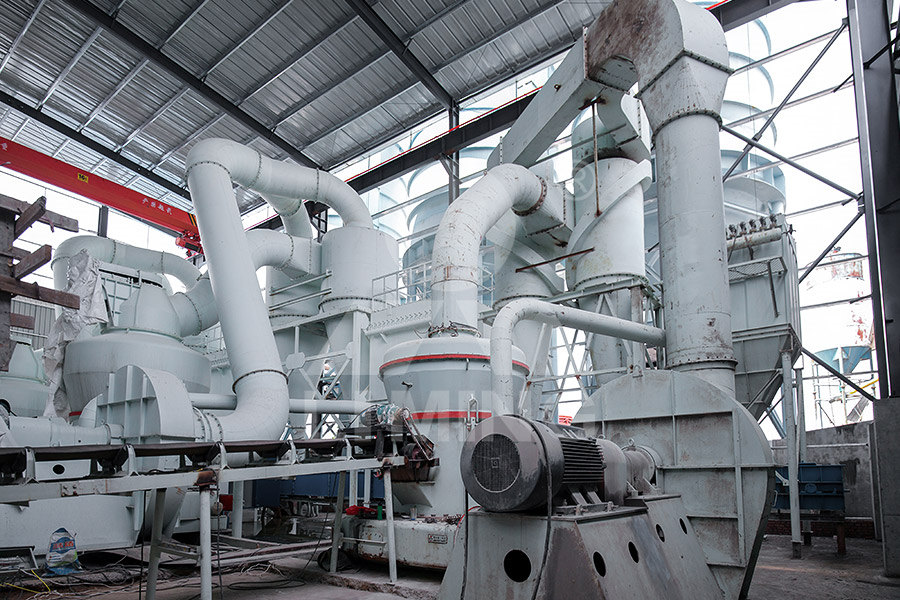
Effect of ball and feed particle size distribution on the milling
In this article, alternative forms of optimizing the milling efficiency of a laboratory scale ball mill by varying the grinding media size distribution and the feed material particle size distribution were2020年1月15日 In this study a metallurgical grade silicon quality was milled in a planetary ball mill and the properties of the powder were investigated as a function of grinding time, grinding Silicon Powder Properties Produced in a Planetary Ball Mill as a 2017年1月1日 In the dry ball milling operation, the specific breakage rate of particles has been found to vary significantly with the size distribution of the particulate materialEffect of size distribution of the particulate material on the specific 2020年10月1日 In our present investigation, we found that ballmilling technique can be used to tailor the microstructural parameters of milled Si sample where milling time can greatly Silicon Powder Properties Produced in a Planetary Ball Mill as a
.jpg)
Silicon Powder Properties Produced in a Planetary Ball Mill as a
In this study a metallurgical grade silicon quality was milled in a planetary ball mill and the properties of the powder were investigated as a function of grinding time, grinding bead size Highstrength aluminium alloy powders modified with different nanoparticles by ball milling (7075/TiC, 2024/CaB6, 6061/YSZ) have been investigated insitu during rapid solidification by Powder particle size distribution before and after the ball milling 2018年6月1日 In this article, alternative forms of optimizing the milling efficiency of a laboratory scale ball mill by varying the grinding media size distribution and the feed material particle size Effect of ball and feed particle size distribution on the milling 2015年11月1日 In this research, ball size distribution which is a function of makeup ball sizes was investigated to optimise the milling stage of a grinding circuit in order to maximise the Ball size distribution for the maximum production of a narrowly
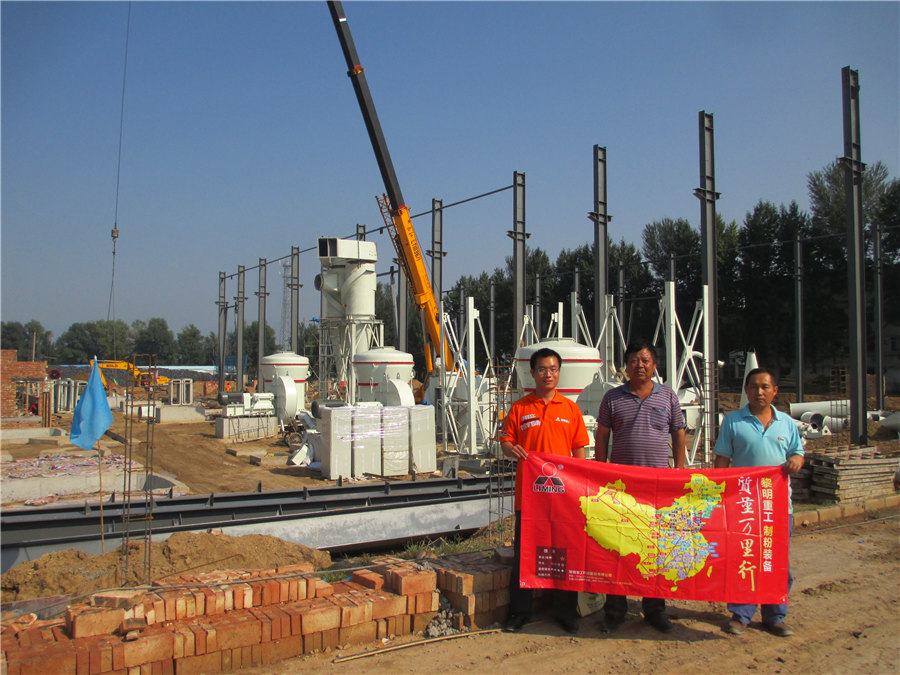
Effect of Ball Milling Conditions on the Microstructure and
Milling with a mixture of balls of two or three sizes was more effective in refining the raw powder than milling with balls of a single size A mixture of 3 mm and 5 mm diameter balls was the 2020年3月1日 Using 125 µm sieve mesh The particle size distribution was also investigated with results showing percentage particle retention of 8889%, 6226%, 4652%, 2730% and 932% for 0, 15, 30, 45, and Effects of ball milling on particle size distribution and measuring particle size before and after the process Particle size growth may be monitored during operations such as granulation or crystallization Determining the particle size of powders requiring mixing is common since materials with similar and A GUIDEBOOK TO PARTICLE SIZE ANALYSIS Horiba2020年7月2日 A comprehensive investigation was conducted to delineate the effect of ball size distribution, mill speed, and their interactions on power draw, charge motion, and balls segregation in a (PDF) Effects of Ball Size Distribution and Mill Speed and Their

Particle size distribution obtained from laser, IA and sieve
Download scientific diagram Particle size distribution obtained from laser, IA and sieve methods for ball mill (No 1, 5 samples) and HPGR (No 6, 10 samples) from publication: Physicochemical 2020年10月1日 The current study investigates the type of ratio for ball mill jars listed in Table 3 and [63,80,168,181,183] Different balltojar ratios can affect the milling kinetics, the size, and Silicon Powder Properties Produced in a Planetary Ball Mill as a 2022年4月21日 The integration of low speed in Program1 leads, with respect to the Reference program (Figure 5 a), to an increase in particle size and better particle size distribution (Figure 5 b) Thus, a higher mean particle area of 14,700 µm 2 (9500 µm 2 for the Reference program) is measured ( Figure 6 a)Influencing the Size and Shape of HighEnergy Ball Milled Particle The “M” Series fine grinders are designed to grind dry, freeflowing material down to 400 mesh with extremely tight particle size distribution This highly efficient machine ensures easy access to all internal areas and is perfect for heatsensitive materials, such Particle Size Reduction Solutions Prater Industries
.jpg)
The Vertical Mill Slag MicroPowders' Particle Size Distribution
In a grinding circuit with ball mill and classifier it is possible to obtain a fine classifier feed material, and hence a relatively wide particle size distribution of the classifier fines, by Download scientific diagram Particle size distribution of microcrystalline cellulose (MCC) powder (246 m) and suspension (216 m) from publication: Mechanisms of flocculation with poly Particle size distribution of microcrystalline cellulose (MCC) 2020年5月15日 However, the harmful effect of agglomeration on particle size reduction was not mentioned by Kohobhange et al [25], which reported that extensive size reductions and narrow particle size distributions can be achieved by ball milling undertaken in a dry ambience over a period of up to 360 h, Palaniandy et al [26] observed the creation of silica agglomerates in Evaluation of particle size reduction and agglomeration in dry 2023年11月1日 Statistical modeling approach of PBM such as the regression model indicates that the milling speed, milling time, and ball to powder weight ratio (BPR) significantly impact the crystallite size, lattice strain and mean particle size of the aluminum matrix [21]Some statistical models are based on the Taguchi method [22], [23], [24] to find the optimum milling Modeling the particle size of nanomaterials synthesized in a

Particle size distribution of the silicon 325 mesh
Download scientific diagram Particle size distribution of the silicon 325 mesh powder used in this study, obtained from the SEM image in Number of particles, n, = 502 from publication: An Ball Mill and Air Classifier Production Line; Pin Mill; a new material company produced 200kg per hour, particle size D100:10μm silicon micropowder ball milling and grading The production line of 40,000 tons per hour of super pure quartz ball grinding and grading with 325 mesh granularity is produced by a company in Guangdong; PROJECTS Lianyungang, a new material company produced 200kg per hour, particle senting the particle size distribution Flat and wide PSD curves represent uneven size distribution range while tall and narrow curves show more uniform particle size distribution The D 50 of BSC0is201mm,whilethoseofBSC2,BSC3,BSC4arecon rmed as 227 mm, 157 m, 135 m respectively, size decreasing in turn BSC0 and BSC2 have comparable D 50 Effect of particle size distribution on the electrochemical The transformation in particle micromorphology and size of Ag was carried out by planetary ball mill (QM1SP2) in a agate jar using agate balls of 2–6 mm diameter Figure 1 shows a schematic diagram of the planetary ball mill [6] During the preparation process of flake silver powders by planetary ball mill, every time the ball mill adoptsPreparation of microsize flake silver powder by planetary ball mill
.jpg)
Ball size distribution for the maximum production of a narrowly
2015年11月1日 Appreciating the role of ball charge and wear rate on ball size distribution and the complexity involved with controlling the ball size distribution parameter, Cho et al [1] incorporated the information that describes variation of the grinding kinetics with ball sizes and the ball wear kinetics into grinding model and investigated the effect of the makeup ball size on Since this is the amount that would pass through a hypothetical sieve of mesh size x, this type of particle size distribution is also called "percent passing Occasionally, the fractions are also summed starting from the largest particle size The resulting particle size distribution is a curve that drops from 100% to 0%Particle Size Distribution: Particle Analyzers MICROTRAC2020年10月1日 The particle size distribution was determined by Laser Diffraction (LD) using a Mastersizer 2000 (Malvern N Kotake, M Kuboki, S Kiya, Y Kanda, Influence of dry and wet grinding conditions on fineness and shape of particle size distribution of product in a ball mill, Adv Powder Technol 22 (1) (2011) 86–92 doi:101016/j Evolution of grinding energy and particle size during dry ball 2019年10月1日 Request PDF Wet and dry grinding of coal in a laboratoryscale ball mill: Particlesize distributions In this study, experimental data for wet and dryground coal samples under wet and dry Wet and dry grinding of coal in a laboratoryscale ball mill: Particle
.jpg)
A comparative study on a newly designed ball mill and the
2020年1月1日 The mill with lifter arrangement in the diaphragm segment provided a separation zone in the discharge end of the mill that helped lift the desired particle sizes from the mill; however, balls and coarse size particles cannot be picked to the separation zone, leading to a relatively a higher percentage of the desired particle size distribution discharge from the millIt is mainly suitable for micro powder processing of noninflammable and explosive brittle materials with medium and low hardness and Mohs hardness ≤6, such as calcite, limestone, dolomite, kaolin, bentonite, talc, mica, magnesite, Micro Powder Grinding Mill2023年6月27日 A key component of the grinding process in a ball mill is the ball size distribution (BSD), which controls the grinding efficiency, product size distribution, and media wear rate Higher rotational speeds and relatively small ball sizes produce finer BSDs, whereas lower speeds and significantly bigger balls produce coarser ones [ 71 , 110 , 148 , 149 , 150 ]Producing Metal Powder from Machining Chips Using Ball Milling PSD = Particle Size Distribution 2 1 Introduction The allimportant size reduction process, The ball mill is one of various sizereduction tools It is a crushing machine with a revolving drum that holds ceramic or metal balls or pebbles 100–200°C compared to commercial grades Powder Ball Milling: An energy balance approach to particle size
.jpg)
Effect of ball size and powder loading on the milling efficiency of
2013年12月1日 10 g of alumina powder (996%, CA5M, KC Corp, Youngam, Jeonnam, Korea) with average diameter of 60 μm (d 50) was loaded to a polyethylenebased bottle (approximately 60 mm in inner diameter and 250 ml in nominal volume) with 500 g of zirconia balls and 70 ml of distilled water The 500 g of balls reached approximately 50% of the bottle height regardless of 2020年1月15日 Mechanical milling is a promising route for production of submicron and nano sized silicon powders, but it is challenging to predict and control the product properties In this study a metallurgical grade silicon quality was milled in a planetary ball mill and the properties of the powder were investigated as a function of grinding time, grinding bead size (20 mm, 2 mm, Silicon Powder Properties Produced in a Planetary Ball Mill as a The tests conducted for ball mills [14], cylindrical mills [15,16], and hammer mills [1,17] showed that the particle size distribution curves vary depending on the process and design parameters of Particle size distribution of the feed after the grinding using the 2016年3月8日 Three particle size placements near largest particle size or top size, the approximate middle particle size or midpoint size, and the near smallest particle size or bottom size provide reasonable threepoint control within a PSD curve The primary control point of a three point control is one of these three pointsCurves Ahead: A Guide to Particle Size Distributions Powder
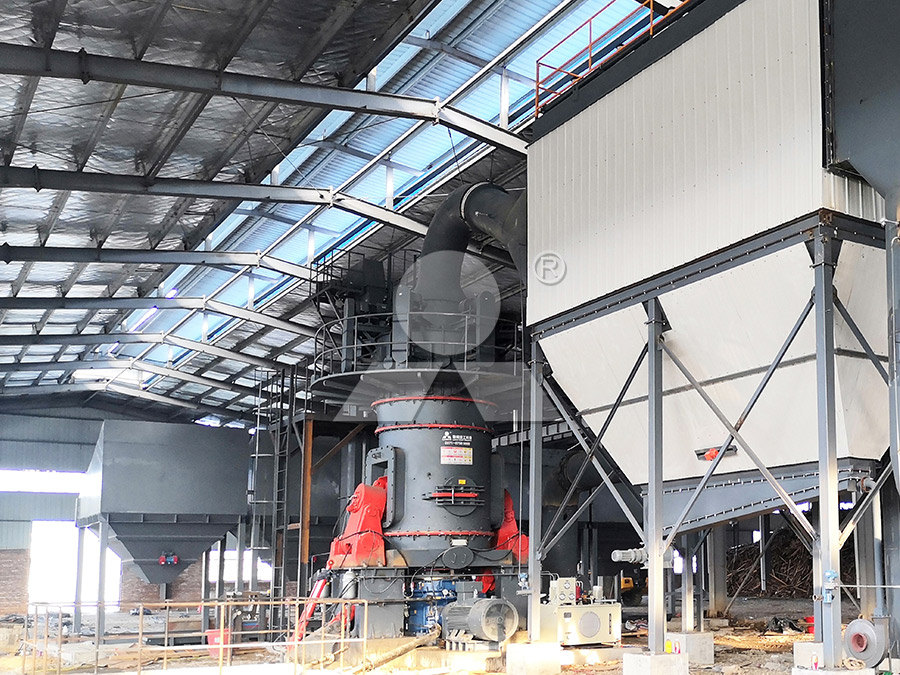
The design and optimization process of ball mill to reduce particle
2020年11月16日 Small particle size in the order of micrometer of event nanometer size is preferred The raw materials were ground from the big particle size to the smallest possible by using multistep grinding In the laboratory, the common method to be used as the ball mill This work aims to design a simple horizontal ball mill2020年11月16日 Request PDF The design and optimization process of ball mill to reduce particle size of calcium carbonate materials Particle size plays an important role in the designs of calcium carbonate The design and optimization process of ball mill to reduce particle 2020年3月1日 Using 125 µm sieve mesh The particle size distribution was also investigated with results showing percentage particle retention of 8889%, 6226%, 4652%, 2730% and 932% for 0, 15, 30, 45, and Effects of ball milling on particle size distribution and measuring particle size before and after the process Particle size growth may be monitored during operations such as granulation or crystallization Determining the particle size of powders requiring mixing is common since materials with similar and A GUIDEBOOK TO PARTICLE SIZE ANALYSIS Horiba
.jpg)
(PDF) Effects of Ball Size Distribution and Mill Speed and Their
2020年7月2日 A comprehensive investigation was conducted to delineate the effect of ball size distribution, mill speed, and their interactions on power draw, charge motion, and balls segregation in a Download scientific diagram Particle size distribution obtained from laser, IA and sieve methods for ball mill (No 1, 5 samples) and HPGR (No 6, 10 samples) from publication: Physicochemical Particle size distribution obtained from laser, IA and sieve 2020年10月1日 The current study investigates the type of ratio for ball mill jars listed in Table 3 and [63,80,168,181,183] Different balltojar ratios can affect the milling kinetics, the size, and Silicon Powder Properties Produced in a Planetary Ball Mill as a 2022年4月21日 The integration of low speed in Program1 leads, with respect to the Reference program (Figure 5 a), to an increase in particle size and better particle size distribution (Figure 5 b) Thus, a higher mean particle area of 14,700 µm 2 (9500 µm 2 for the Reference program) is measured ( Figure 6 a)Influencing the Size and Shape of HighEnergy Ball Milled Particle
.jpg)
Particle Size Reduction Solutions Prater Industries
The “M” Series fine grinders are designed to grind dry, freeflowing material down to 400 mesh with extremely tight particle size distribution This highly efficient machine ensures easy access to all internal areas and is perfect for heatsensitive materials, such In a grinding circuit with ball mill and classifier it is possible to obtain a fine classifier feed material, and hence a relatively wide particle size distribution of the classifier fines, by The Vertical Mill Slag MicroPowders' Particle Size Distribution Download scientific diagram Particle size distribution of microcrystalline cellulose (MCC) powder (246 m) and suspension (216 m) from publication: Mechanisms of flocculation with poly Particle size distribution of microcrystalline cellulose (MCC) 2020年5月15日 However, the harmful effect of agglomeration on particle size reduction was not mentioned by Kohobhange et al [25], which reported that extensive size reductions and narrow particle size distributions can be achieved by ball milling undertaken in a dry ambience over a period of up to 360 h, Palaniandy et al [26] observed the creation of silica agglomerates in Evaluation of particle size reduction and agglomeration in dry