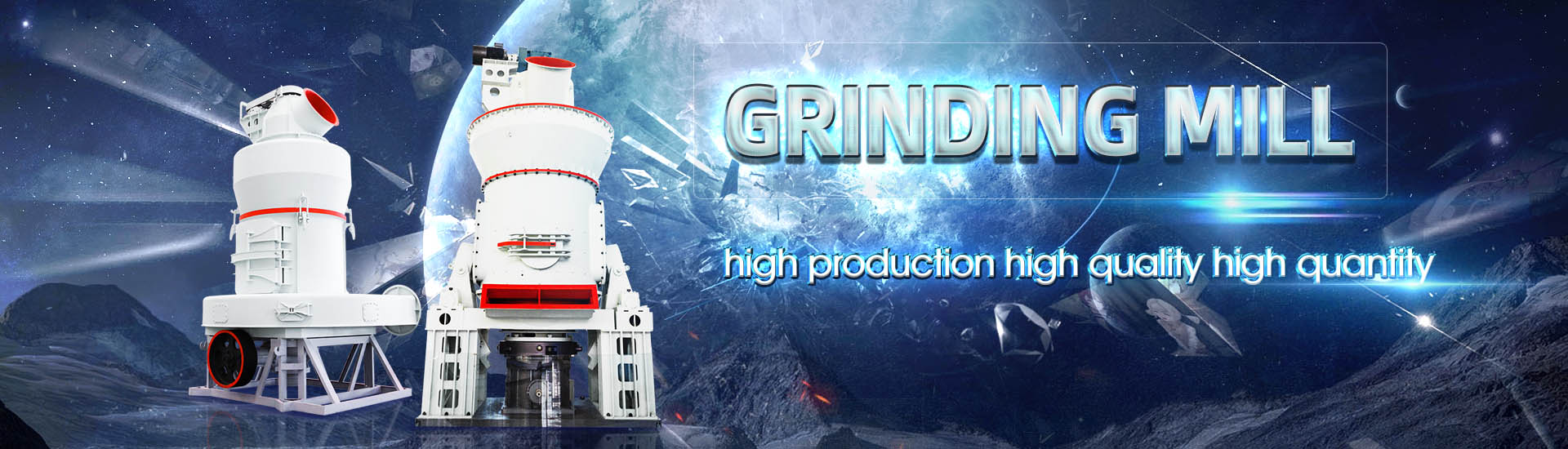
60 vertical mill working pressure
.jpg)
Operational parameters affecting the vertical roller mill performance
2016年9月1日 SHAP analyses highlighted that working pressure and input gas rate with positive relationships are the key factors influencing energy consumption eXtreme Gradient Boosting (XGBoost) as aworks were performed to investigate the influences of the design and operating parameters on vertical roller mill grinding performance In this context, systematic test plans have been INVESTIGATION OF EFFECT OF OPERATIONAL PARAMETERS ON 2017年4月1日 Working pressure is normalized with classifier rotor speed Vertical roller mills (VRM) have found applications mostly in cement grinding operations where they were used in Operational parameters affecting the vertical roller mill Vertical roller mills are adopted in 20 cement plants (44 mills) in Japan In the vertical roller mill which is widely used in the raw material grinding process, raw materials input grinding table Vertical roller mill for raw Application p rocess materials
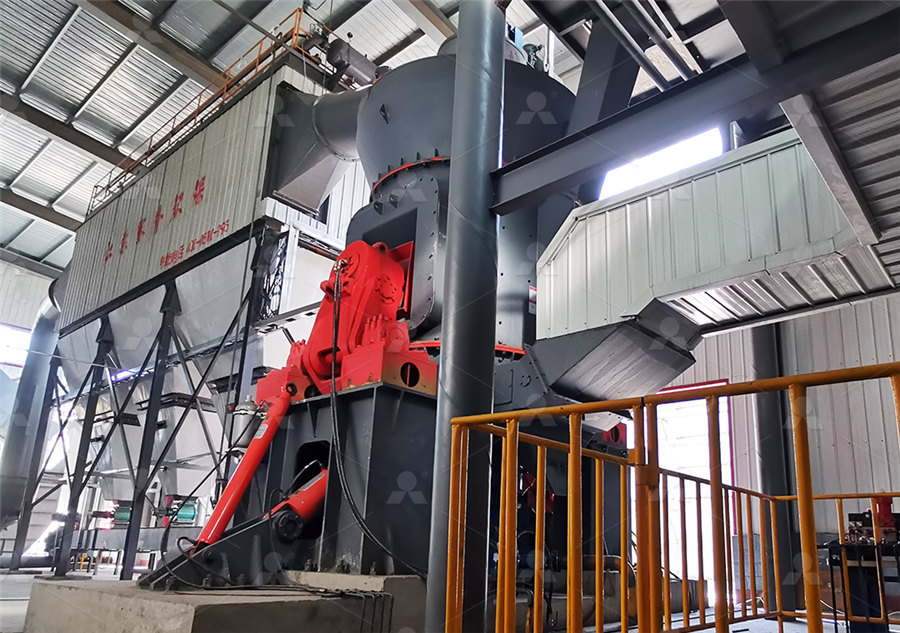
Vertical Mill Calculations PDF Mill (Grinding) Calorie Scribd
This document discusses the key components and calculations involved in the operation of a vertical mill It provides symbols and units for variables used in calculating mill power 2022年5月31日 Altun et al (2017) studied the effects of the working pressure of vertical grinding roller millstone on product mass flow rate and product size through industrial experiments and Analysis of vertical roller mill performance with changes in material Vertical Roller Mills Pressure Profile Draw Up Curve Influenced by: •Mill Inlet Pressure •Nozzle Ring Coverage •Classifier Speed •Dam Ring Height •Mill Load •Material Blockage in Hot Gas Optimization of VRM Operation RUCEMRU2017年4月1日 Working pressure is normalized with classifier rotor speed Vertical roller mills (VRM) have found applications mostly in cement grinding operations where they were used in Operational parameters affecting the vertical roller mill
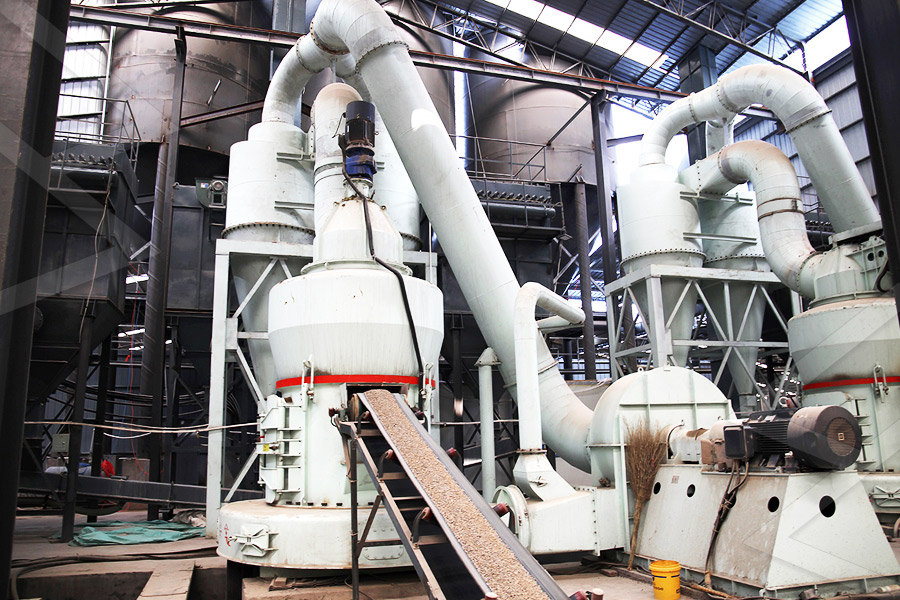
An investigation of performance characteristics and energetic
2020年8月12日 To understand the performance of a vertical roller coal mill, the real operational tests have been performed considering three different coal sources Obtained results indicate Understanding the working principle of vertical mills is crucial in maximizing their efficiency and performance in various industries By controlling parameters such as roller speed and feed Working principle and characteristics of vertical mill2022年5月9日 Modeling of energy consumption factors for an industrial cement vertical roller mill by SHAPXGBoost: SHAP analyses highlighted that working pressure and input gas rate with positive relationships are the key factors influencing energy consumption 60: 81: Maximum depth of trees: 16: 7: The minimum sum of instance weight Modeling of energy consumption factors for an industrial cement Ultrafine vertical mill is a highefficient industrial grinding mill, features: The fineness D97 of the finished powder produced can reach 3000 mesh, and the content of 2μm can reach up to 60% The product has high whiteness, narrow Ultrafine Vertical Mill
.jpg)
Hydraulic system vertical roller mill operation PDF
2015年3月25日 1 The working principle of the hydraulic system vertical roller mill The hydraulic system ofvertical mill is an important system, the main function ofthe hydraulic system is to break the grinding roller, which is when the 2022年10月1日 This study investigated a mathematical model for an industrialscale vertical roller mill Working Pressure (bar) 84–85 60 70 80 90 100 01 1 10 100 1000 10000(PDF) A cement Vertical Roller Mill modeling based onThe vertical grinding mill does not have the metal impact sound of the steel balls colliding with each other and the liner in the ball mill, so the noise is low, which is 2025dB lower than that of the ball mill In addition, the vertical mill adopts a fully enclosed system, the system works under negative pressure, no dust, and the environment Industrial Vertical Grinding MillJet mill: 5um powder can be produced, jet pulverization, the whiteness of the finished powder is the best Highend food grade finished powder Mechanically crushed, the powder has the highest fineness It is only suitable for highend or high valueadded powders High energy consumption and low output Ultrafine vertical grinding millCLUM Ultrafine Vertical Grinding Mill
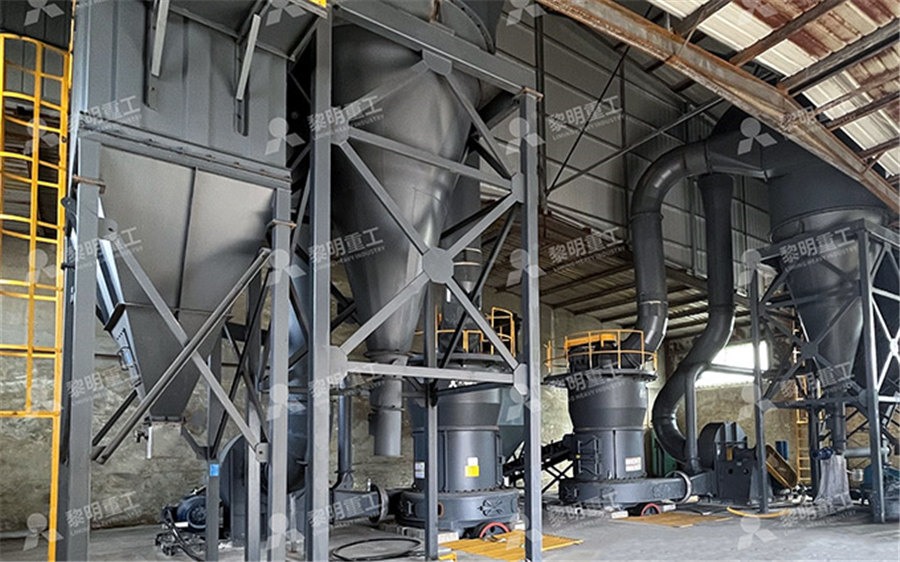
Limestone Ultrafine Vertical Mill
Limestone ultrafine vertical mill is a high quality ores material powder grinding mill +17 [ protected] Working Diameters (mm) 1400: 1600: 1700: Number of rollers (pieces) 3: 3: 3: Number of classifier (pieces) 6: 6: 6: Low vibration, low noise The equipment is sealed and works under negative pressure, no dust spilt, LM series vertical mill is a new type of milling equipment with advanced technology, LM series vertical mill is mainly composed of classifier, roller device, grinding disk device, pressure device, speed reducer, 5060: 90110: Main motor power(kw) 200250: 280315: 400450: 500560: 9001000: 18002000: 31503300: Models: LM80M: LM110M:LM series vertical mill6090: TRMR172: 1700: 220: 40: 2233: TRMR142: 1400: 150: 40: 1320: In a GGBS plant, higher roller pressure is adopted because the fineness requirement of the finished product is higher Working principle of VRM mill The vertical roller mill is composed of a frame, grinding table, grinding roller, VRM In Cement Plant Maximize Energy Saving CNBMSINOMA2013年5月15日 Vertical raw mill pradeep kumar calibrated bed depth monitors •Adjust the mill dam ring height to compensate for table wear •Match grinding pressure to mill throughput Nozzle ring velocity 45 – 60 m/s velocity above roller V = 15 Do to 25 Do Velocity through rotor vanes = 50 m/s Grinding bed thickness = 1 Vertical raw mill pradeep kumar PPT SlideShare
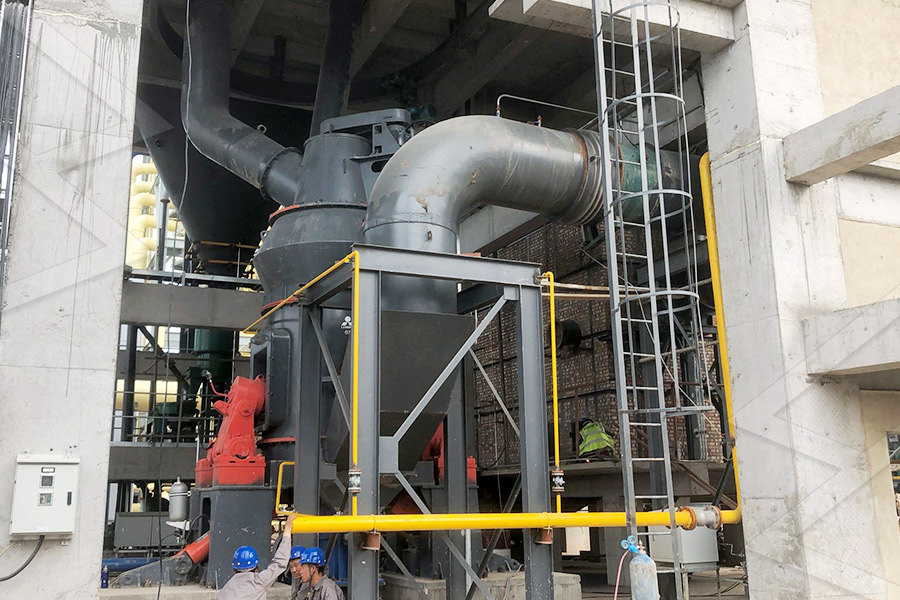
Prefinishing Mill Group
Prefinishing mill type: cantilever mill, rack number: 4 stands; Horizontal mill (2 stands), Vertical Looper (3 sets), vertical mill (2 stands), safety cover; Layout and transmission mode: horizontal vertical horizontal; HVHV, direct current Unloading roller working pressure: 60 MPa Roll cooling waterConsumption: 4x20 t/hThe basic working principle of a vertical mill involves the interaction of several key components At the core of the mill is a large vertical grinding table, which rotates at a controlled speed Above the grinding table, there are several rollers that apply pressure onto the material being groundIndepth understanding of the working principle of vertical millsAs the vertical roller mill works, the motor drives the reducer to rotate the dial, the raw material are delivered to the center of the dial from the air lock rotary feeder The material moves to the edge of the dial due to the effect of centrifugal force Best HLM Vertical Roller Mill Manufacturer and 1 The Structure and Working Principle of Vertical Mill 11 The Working Principle of Vertical Mill The material enters the vertical mill from the upper feed inlet, roller working pressure also very high all this cause relatively high yield and Power saving effect is obvious (2) Grinding process is simple and it can dry, Solid Edge’s Application in Vertical Mill Design Springer
.jpg)
(PDF) Performance Evaluation of Vertical Roller Mill in
2017年9月11日 In this study, an extensive sampling study was carried out at vertical roller mill of ESCH Cement Plant in Luxemburg Samples were collected from mill inside and around the circuit to evaluate the 2021年1月1日 Cement is an energyintensive industry in which more than 60% of the total electricity is used in grinding circuits and also bears most of the construction cost and working on to those causes by modifications Kaizens The wear rate in g/t is higher in the ball mill than in the vertical mill or highpressure roller, Review on vertical roller mill in cement industry its SBM high quality calcium carbonate ultrafine powder vertical mill is widely used in many fields +17 [ protected] Users can precisely control the working parameters of equipment such as grinding pressure and rotating speed Working Principle The ultrafine vertical mill is composed of several components, Calcium Carbonate Ultrafine Powder Vertical MillLimestone Powder Ultrafine Vertical Roller Mill Modle : CLUM Series Finished Size: 4003000 mesh Processing Ability: 3 – 45t/h Max Feeding Size: 10 mm M 1 Set Price: $ Range Of Application: Limestone, Calcium Carbonate, Talc, Limestone Powder Ultrafine Vertical Roller Mill
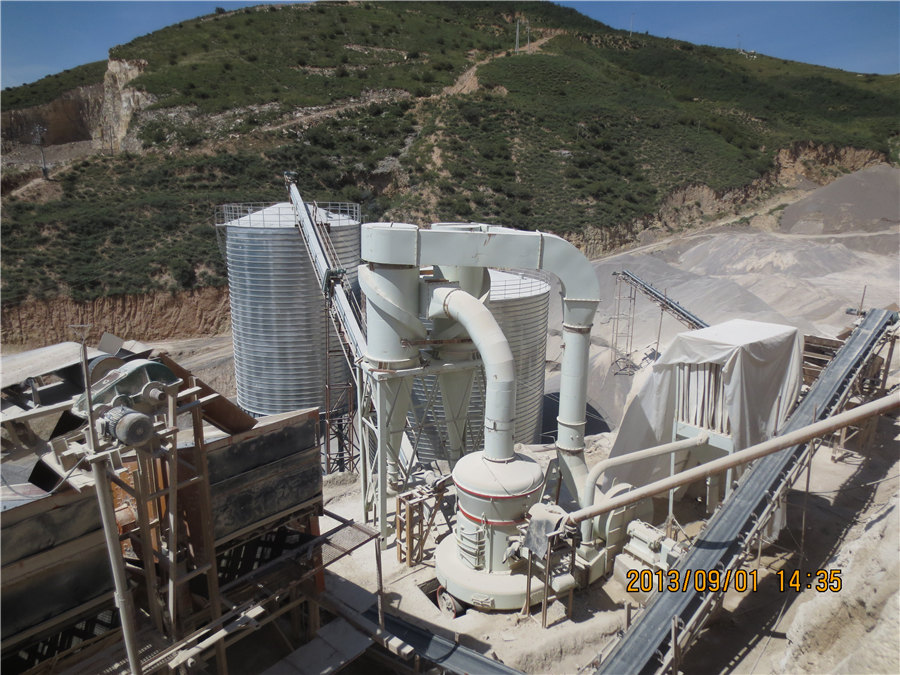
60" OLYMPIA V60L CNC VERTICAL BORING MILL WITH LIVE
Kick start your manufacturing with a used 2003 OLYMPIA V60, a topnotch CNC Vertical Boring Mill with Live Spindle Efficiently handles a max workpiece height of 62" under rail and turning diameter of 71" Benefit from its powerful main motor of 80 HP and live spindle horsepower of 25 HP Comes equipped with a Fanuc 18iTA CNC control with graphics, automatic tool changer 2017年4月1日 Classifier rotor speed and working pressure are effective parameters on product rate as indicated When the working pressure is normalized with the classifier rotor speed Fig 7 is obtained The graph shows that there is a steadily upward trend between the working pressure/classifier rotor speed and product rateOperational parameters affecting the vertical roller mill FIG 1 illustrates force displacement curves AD in such traditional counter pressure systems utilized in a roller mill Since the cushion effect is directly proportional to the counter pressure magnitude, as the cushion effect is increased, that is, as one goes from the system depicted in curve A toward the system depicted in curve D, the system stiffness, or steepness of the force Vertical roller mill with improved hydropneumatic loading systemBarite ultrafine vertical roller mill is an industrial vertical grinding mill that can grind nonmetallic ore into fine powder The mill has a high production capacity, high fine powder content, high degree of automation, convenient maintenance, long service life, environmental protection, and energysaving, and is an ideal equipment for largescale production of ultrafine powderBarite Ultrafine Vertical Roller Mill
.jpg)
60 Litre Vertical Pressure Vessel Anglian Pumping Services
60 Litre Vertical Pressure Vessel Next working day delivery is available for a £1500 + vat delivery charge Orders must be placed before 12 noon to qualify for next working day delivery Orders placed after 12 noon on Thursday but before Acer’s advanced Emill 5VK Head with inverter elctronic variable speed Machine provides large working table, 59″ x 114/5″ with extensive travel 47″ x 15″ It is the largest in its class! Machine can run both single and three phase 220V without using phase converter 12″ x 60″ New Acer EMill Vertical Mill Model 6VK Optional 12″ x 60″ New Acer EMill Vertical Mill Model 6VKAGICO vertical roller mills can be used as cement mills, raw mills, and slag mills AGICO also supplies vertical roller mill components and parts, we can customize machines according to customers’ needs Vertical roller mills (VRM) are a type of mainstream clinker grinding equipment in the cement manufacturing process Vertical roller mills are still newish []Vertical Roller Mill for Sale AGICO Cement PlantLM Series Vertical Roller Mill is used to pulverize materials, material can be pulverized into 80400Mesh with this mill Feed particle size : 070mm Production capacity : 4300 tons / hourLM Vertical Roller Mill, Vertical Mill Manufacturer
.jpg)
VRM Presentation PDF Mill (Grinding) Electric Motor
Vrm Presentation Free download as Powerpoint Presentation (ppt), PDF File (pdf), Text File (txt) or view presentation slides online The document describes a roller mill used in the cement industry It discusses the key components of a vertical roller mill including the grinding table, rollers, separator, and material flow It explains how the mill functions to grind materials Vertical Roller Mill Summary Free download as PDF File (pdf), Text File (txt) or view presentation slides online Ball mill vs vertical mill Operations Structure of a vertical mill Working Process Components Dam Ring Armour Ring Louver Ring Grinding Table Rollers Separators Maintenance Performance ImprovementVertical Roller Mill Summary PDF Mill (Grinding) ScribdIntroduction The LM Vertical Grinding Mill , launched by SMMVIK Machinery, integrates five functions of crushing, grinding, powder selection, drying and material conveyingIt is characterized by centralized technological process, small occupational area, low investment, high efficiency, energy conservation and environment protectionLM Vertical Grinding Mill SMMVIK Machinery2022年5月9日 Modeling of energy consumption factors for an industrial cement vertical roller mill by SHAPXGBoost: SHAP analyses highlighted that working pressure and input gas rate with positive relationships are the key factors influencing energy consumption 60: 81: Maximum depth of trees: 16: 7: The minimum sum of instance weight Modeling of energy consumption factors for an industrial cement
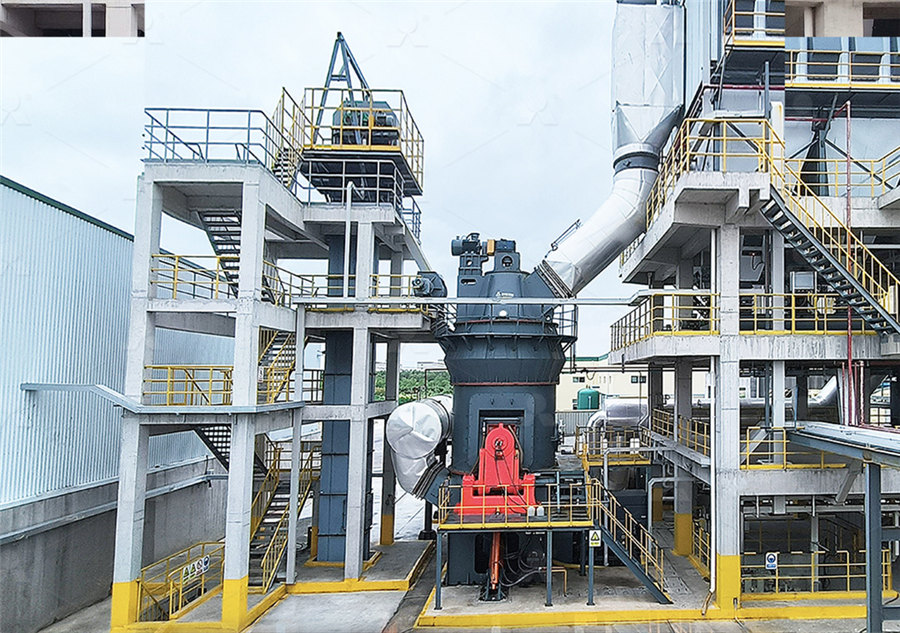
Ultrafine Vertical Mill
Ultrafine vertical mill is a highefficient industrial grinding mill, features: The fineness D97 of the finished powder produced can reach 3000 mesh, and the content of 2μm can reach up to 60% The product has high whiteness, narrow 2015年3月25日 1 The working principle of the hydraulic system vertical roller mill The hydraulic system ofvertical mill is an important system, the main function ofthe hydraulic system is to break the grinding roller, which is when the Hydraulic system vertical roller mill operation PDF2022年10月1日 This study investigated a mathematical model for an industrialscale vertical roller mill Working Pressure (bar) 84–85 60 70 80 90 100 01 1 10 100 1000 10000(PDF) A cement Vertical Roller Mill modeling based onThe vertical grinding mill does not have the metal impact sound of the steel balls colliding with each other and the liner in the ball mill, so the noise is low, which is 2025dB lower than that of the ball mill In addition, the vertical mill adopts a fully enclosed system, the system works under negative pressure, no dust, and the environment Industrial Vertical Grinding Mill

CLUM Ultrafine Vertical Grinding Mill
Jet mill: 5um powder can be produced, jet pulverization, the whiteness of the finished powder is the best Highend food grade finished powder Mechanically crushed, the powder has the highest fineness It is only suitable for highend or high valueadded powders High energy consumption and low output Ultrafine vertical grinding millLimestone ultrafine vertical mill is a high quality ores material powder grinding mill +17 [ protected] Working Diameters (mm) 1400: 1600: 1700: Number of rollers (pieces) 3: 3: 3: Number of classifier (pieces) 6: 6: 6: Low vibration, low noise The equipment is sealed and works under negative pressure, no dust spilt, Limestone Ultrafine Vertical MillLM series vertical mill is a new type of milling equipment with advanced technology, LM series vertical mill is mainly composed of classifier, roller device, grinding disk device, pressure device, speed reducer, 5060: 90110: Main motor power(kw) 200250: 280315: 400450: 500560: 9001000: 18002000: 31503300: Models: LM80M: LM110M:LM series vertical mill6090: TRMR172: 1700: 220: 40: 2233: TRMR142: 1400: 150: 40: 1320: In a GGBS plant, higher roller pressure is adopted because the fineness requirement of the finished product is higher Working principle of VRM mill The vertical roller mill is composed of a frame, grinding table, grinding roller, VRM In Cement Plant Maximize Energy Saving CNBMSINOMA
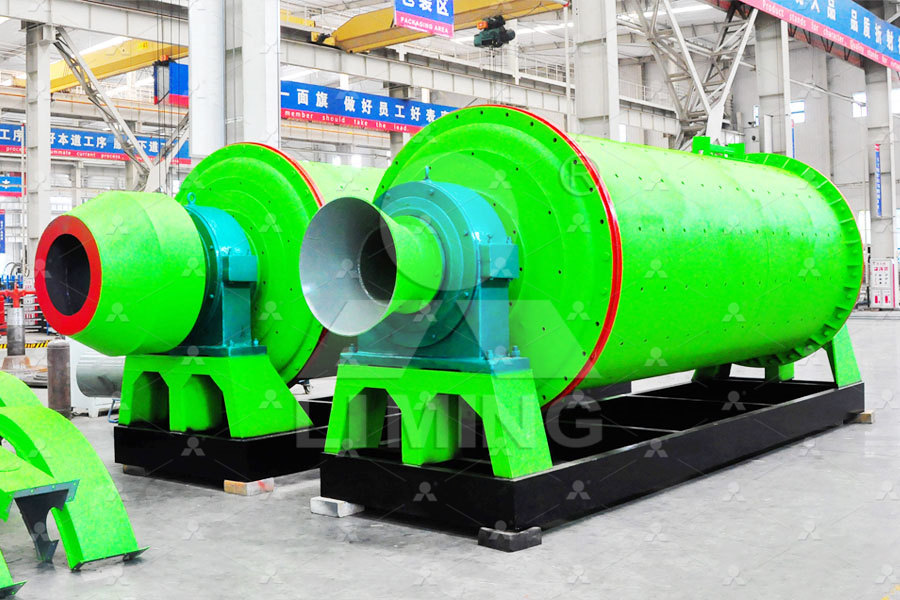
Vertical raw mill pradeep kumar PPT SlideShare
2013年5月15日 Vertical raw mill pradeep kumar calibrated bed depth monitors •Adjust the mill dam ring height to compensate for table wear •Match grinding pressure to mill throughput Nozzle ring velocity 45 – 60 m/s velocity above roller V = 15 Do to 25 Do Velocity through rotor vanes = 50 m/s Grinding bed thickness = 1