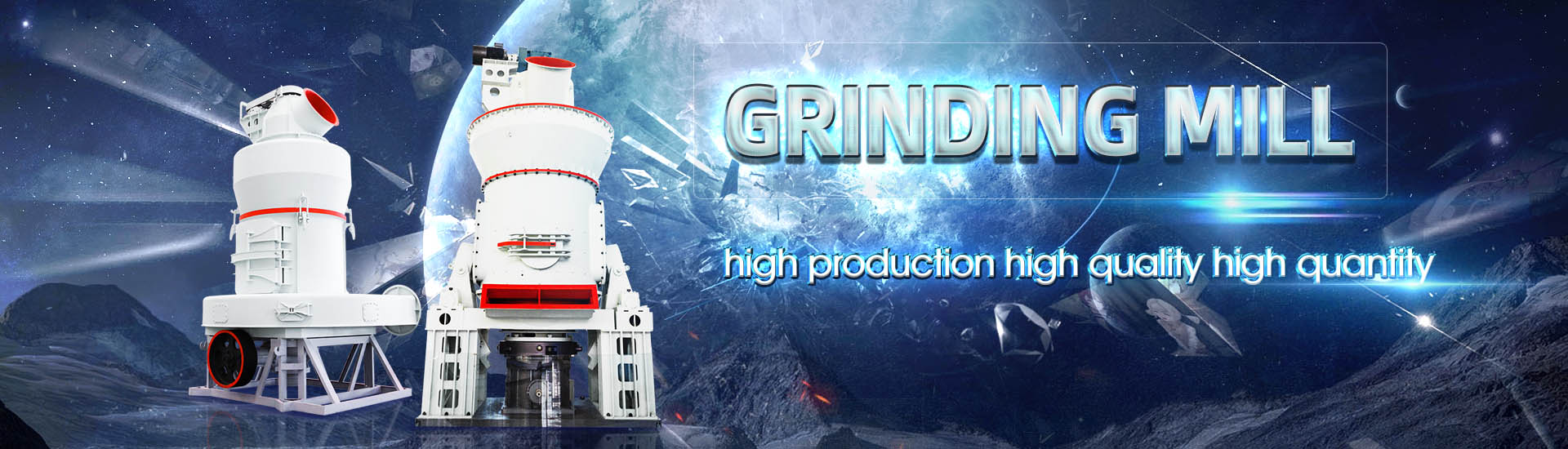
Processing process of refined iron oxide
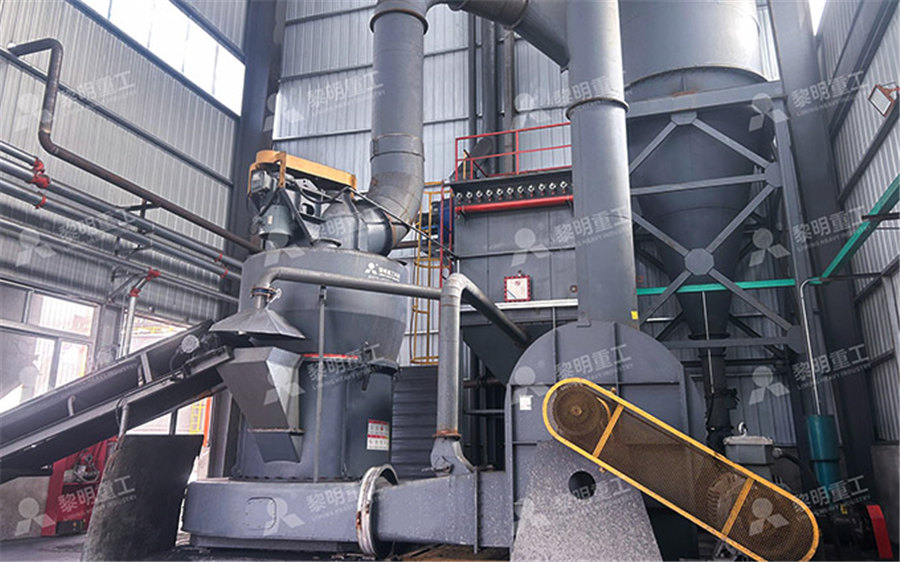
Iron Ore Processing: From Extraction to Manufacturing
2024年4月26日 Iron ore, a naturally occurring mineral composed primarily of iron oxides, is mined and processed to extract iron for various industrial applications This article provides a comprehensive overview of the iron ore Iron processing Ores, Smelting, Refining: Iron ores occur in igneous, metamorphic (transformed), or sedimentary rocks in a variety of geologic environments Most are sedimentary, but many have been changed by Iron processing Ores, Smelting, Refining BritannicaIron processing Smelting, Refining, Alloying: The primary objective of iron making is to release iron from chemical combination with oxygen, and, since the blast furnace is much the most efficient process, it receives the most attention Iron processing Smelting, Refining, Alloying Britannica2019年3月15日 In the paper are shown the history, processing and applications of hematite Hematite is an oxide of iron having the composition Fe2O3 Pure hematite, also called “red ore” contains 70% Fe(PDF) Hematite Processing and Applications
.jpg)
(PDF) An Overview of the ReductionSmelting Process
2022年8月23日 This study gave an overview of the reductionsmelting process as a third generational alternative for the modernday iron and steelmaking process whose hallmark is to mitigate theSeveral processes are used for extraction of same metal depending on occurrence and chemical requirements It takes multiple steps to extract the "important" element from the ore: First, the ore must be separated from 232: Principles of Extractive Metallurgy Chemistry 2024年1月1日 Ironmaking is the process of refining iron oxides in iron ores into metallic iron The earth’s crust is rich in iron, accounting for 42% of the total elements, ranking fourth With no Ironmaking SpringerLinkless energy to produce tonnes of hot metals and can reduce CO2 techniques in modern emissions reducersmelter to conventional steelmaking study The technology compared An Overview of the ReductionSmelting Process of Iron Oxides in
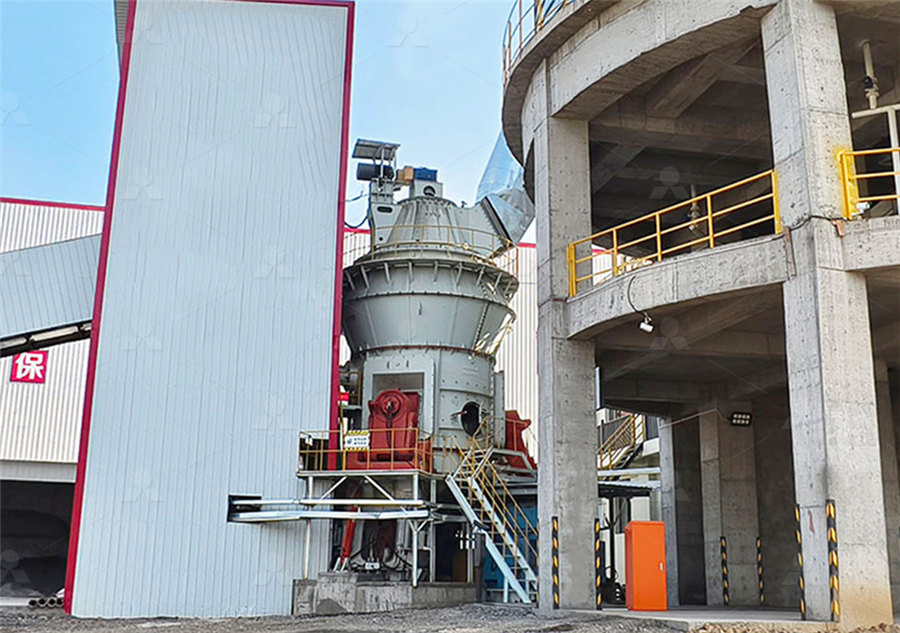
Iron Ore Processing, General
Making iron and steel from iron ore requires a long process of mining, crushing, separating, concentrating, mixing, agglomeration (sintering and pelletizing), and shipping to steel mills zinc processing, the extraction of zinc from its ores and the preparation of zinc metal or chemical compounds for use in various products Zinc (Zn) is a metallic element of hexagonal closepacked (hcp) crystal structure and a density of Zinc processing Extraction, Refining Uses Britannica2023年5月19日 The present invention is a method for refining iron oxide which is a byproduct of a zinc smelting process, the method comprising: a firing process for firing the iron oxide; a washing process for washing an iron oxide cake with a washing liquid, after the firing; and a step for providing iron oxide by filtering the washed iron oxide cake and refining sameWO/2023/ METHOD FOR PRODUCING HIGH QUALITY REFINED IRON OXIDE 2019年3月15日 In the paper are shown the history, processing and applications of hematite Hematite is an oxide of iron having the composition Fe2O3 Pure hematite, also called “red ore” contains 70% Fe(PDF) Hematite Processing and Applications
.jpg)
Copper Mining and Processing: Processing Copper Ores
Copper processing is a complicated process that begins with mining of the ore (less than 1% copper) and ends with sheets of 9999% pure copper called cathodes, which will ultimately be made into products for everyday useThe most common types of ore, copper oxide and copper sulfide, undergo two different processes, hydrometallurgy and pyrometallurgy, respectively, 2020年6月10日 224 Direct Reduction of Iron Oxide by Solid Carbon The direct reduction process of iron oxide by solid carbon is highly endothermic in nature and occurs when the molten slag flows over incandescent coke in the bosh region at a temperature above 1000 °C Therefore, the corresponding reaction can be written as follows:Iron and SteelMaking Process SpringerLinktitanium processing, the extraction of titanium from its ores and the preparation of titanium alloys or compounds for use in various products Titanium (Ti) is a soft, ductile, silvery gray metal with a melting point of 1,675 °C (3,047 °F) Owing to the formation on its surface of an oxide film that is relatively inert chemically, it has excellent corrosion resistance in most natural Titanium processing Technology, Methods, Facts Britannica2017年4月1日 A study of selective precipitation techniques used to recover refined iron oxide pigments for the production of paint from a The process used to form the synthetic AMD solution involves oxidation and alkaline addition to bring pH to a point that During final data processing, compositions were normalized to 100% A study of selective precipitation techniques used to recover refined
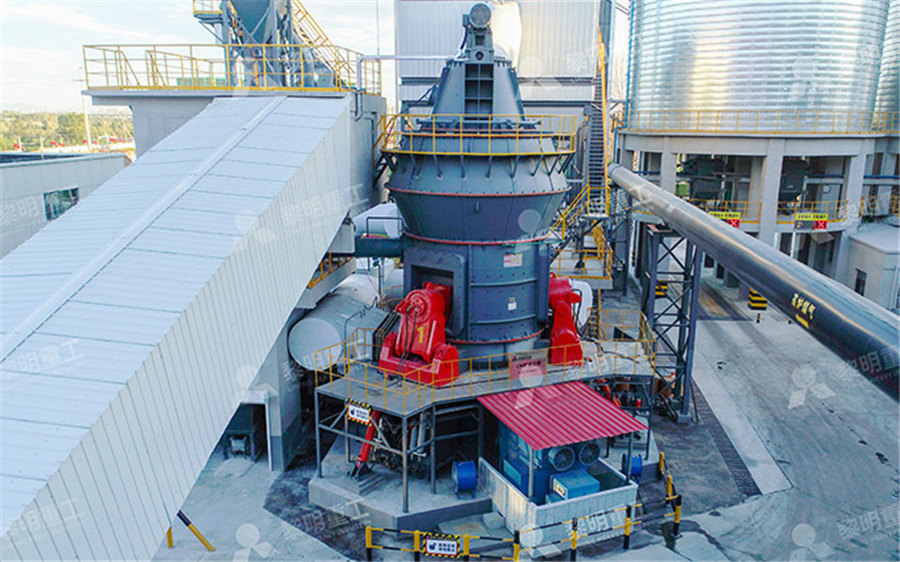
Nickel processing Extraction, Refining, Alloying Britannica
Nickel processing Extraction, Refining, Alloying: The extraction of nickel from ore follows much the same route as copper, and indeed, in a number of cases, similar processes and equipment are used The major differences in equipment are the use of highertemperature refractories and the increased cooling required to accommodate the higher operating temperatures in nickel Resource Recovery and Recycling from Metallurgical Wastes S Ramachandra Rao, in Waste Management Series, 2006 98 Production of Ceramic Tiles from Iron Ore Tailings Current practice of washing iron ore before it is processed for extractive metallurgical operation results in three products, coarse ore lumps with sizes in the range 1080 mm, which are directly charged Iron Ore Processing an overview ScienceDirect TopicsThe iron separated from the surrounding rock but never quite melted Instead, it formed a crusty slag which was removed by hammering This repeated heating and hammering process mixed oxygen with the iron oxide to produce iron, and removed the carbon from the metalHow iron is made material, manufacture, making, history, used molybdenum processing, preparation of the ore for use in various products Molybdenum (Mo) is a white platinumlike metal with a melting point of 2,610 °C (4,730 °F) In its pure state, it is tough and ductile and is characterized by moderate hardness, high thermal conductivity, high resistance to corrosion, and a low expansion coefficientWhen alloyed with other metals, molybdenum Molybdenum processing Extraction, Applications Uses
.jpg)
Silver processing Refining, Mining Uses Britannica
Silver processing, preparation of the ore for use in various products Silver has long been valued for its white metallic lustre, its ability to be readily worked, and its resistance to the corrosive effects of moisture and oxygen The lustre of the pure metal is due to its electron configuration,2021年10月15日 Raman spectrum was employed to evaluate the modifications of Cr 2 O 3 and Cr 2 O 3 +Fe 2 O 3 codoped on the glass network Raman profiles in the range of 3001250 cm−1 are illustrated in Fig 1, Fig 2A related work reports that the Raman profile of silicate glass is divided into two regions: namely, low and highfrequency regions [7]The lowfrequency Catalytic mechanism of iron oxide doping on the crystallization process Following the leaching of oxide ores, copper and cobalt are separated using solvent extraction, and a number of impurities, such as iron, zinc, manganese, etc, are removed prior to cobalt Overview of the main processing routes for cobalt extraction as 2023年4月5日 Recent Trends in the Technologies of the Direct Reduction and Smelting Process of Iron Ore/Iron Oxide in the Extraction of Iron and Steelmaking April 2023 DOI: 105772/intechopen(PDF) Recent Trends in the Technologies of the Direct
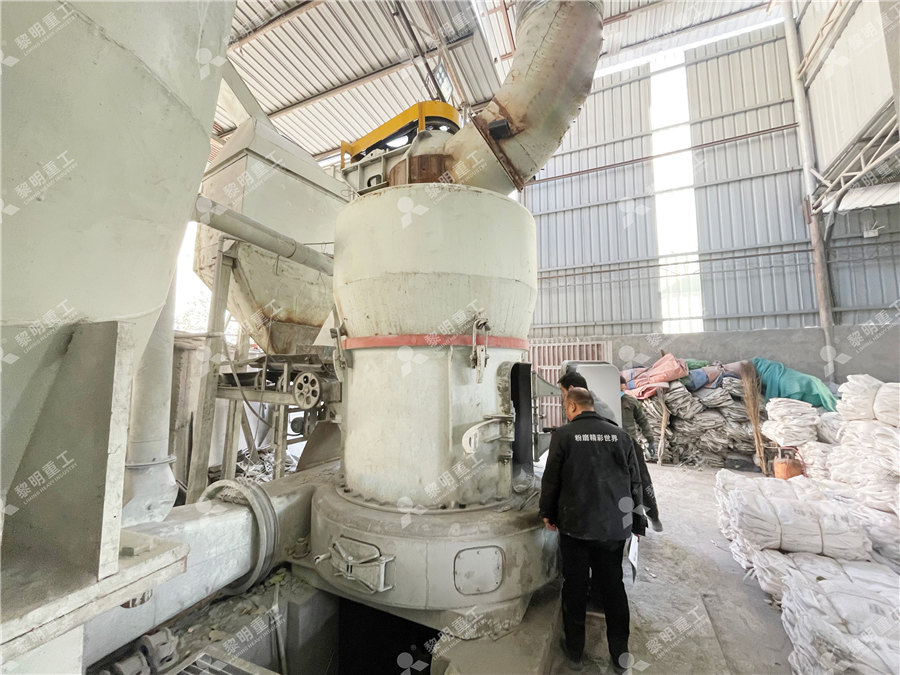
Gold processing Refining, Smelting Purifying Britannica
2024年11月14日 gold processing, preparation of the ore for use in various products For thousands of years the word gold has connoted something of beauty or value These images are derived from two properties of gold, its colour and its chemical stabilityThe colour of gold is due to the electronic structure of the gold atom, which absorbs electromagnetic radiation with 2003年8月1日 The three major end uses are derived from indium metal, its alloys and indium tin oxide (ITO) Indium is employed in the fabrication of germanium rectifiers, photo conductors, and thermistors (Economics of Indium, 1999)It can be evaporated onto glass and plated onto metal, thereby forming a mirror that is comparable to that made with silver but with greater resistance Processing of indium: a review ScienceDirect2008年1月1日 Finally, potential applications of supercritical fluid technology for the processing of iron oxide nanoparticles are presented workers and is known as RTDS 38,39,42,43 In this process, an ironProcessing of iron oxide nanoparticles by supercritical fluids2013年12月1日 Meanwhile, the production of nickel pig iron in China and India has been supplementing some of the refined nickel in stainless steel production, in the past 15 years (Widmer, 2009) Some of the methods stated above have processing cost advantages over others due to the credits generated from cobalt, copper and other metalsDirect extraction of nickel and iron from laterite ores using the
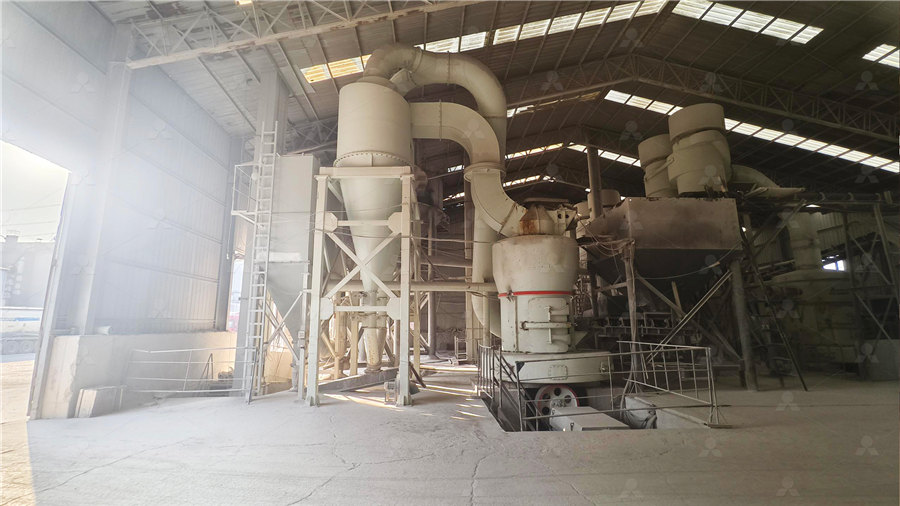
(PDF) i) Direct Reduced Iron: Production ResearchGate
2016年3月30日 In book: Encyclopedia of Iron, Steel, and Their Alloys (pppp 10821108) Chapter: i) Direct Reduced Iron: Production; Publisher: CRC Press, Taylor and Francis Group, New York2024年10月15日 It is known that the reactions in the hydrogenbased direct reduction of iron oxide can proceed in two or three stages, depending on the furnace temperature [] When the temperature is below 570 °C, direct reduction of Fe 2 O 3 → Fe 3 O 4 → metallic iron (Fe) takes place, regardless of the type of reducing gas At temperatures above 570 °C, Fe 3 O 4 → FeO Optimization of Hydrogen Utilization and Process Efficiency in the Niobium oxide (Nb 2 O 5) is generally the starting chemical for the production of other compounds, such as niobium chloride (NbCl 5), niobium carbide (NbC), or lithium niobate (LiNbO 3) Niobium metal is produced by the aluminothermic reduction of Niobium Extraction, Refining Production TICAluminum processing Ores, Refining, Alloying: Aluminum is the third most abundant element on Earth’s surface Only oxygen and silicon are more common Earth’s crust to a depth of 16 km (10 miles) contains 8 percent aluminum Aluminum processing Ores, Refining, Alloying
.jpg)
Production of Iron Oxide Nanoparticles by CoPrecipitation
2020年2月1日 Optimization studies were carried out in the production of γFe2O3 nanoparticles by using coprecipitation method Iron (II) chloride and iron (III) chloride were used as precursors which are dissolved in distilled water followed by centrifugation, drying and grinding process in order to obtain dried dark brown precipitated γFe2O3 powder2024年11月15日 uranium processing, preparation of the ore for use in various products Uranium (U), although very dense (191 grams per cubic centimetre), is a relatively weak, nonrefractory metal Indeed, the metallic properties of uranium appear to be intermediate between those of silver and other true metals and those of the nonmetallic elements, so that it is not Uranium processing Mining, Refining Enrichment Britannica12 The Open Mineral Processing Journal, 2009, 2, 1216 18748414/09 2009 Bentham Open Open Access Removal of Iron from Hard Zinc for Production of Refined Zinc MA Barakat* Central Metallurgical R D Institute, PO Box 87 Helwan 11421, Cairo, Egypt Abstract: RefiningRemoval of Iron from Hard Zinc for Production of Refined Zinc2020年3月19日 Iron Oxide Nanoparticle, maghemite (γFe2O3) has received great interest and extensively used in biomedical field Optimization studies were carried out in the production of γFe2O3 Production of Iron Oxide Nanoparticles by CoPrecipitation
.jpg)
(PDF) Processing and Characterization of Iron Oxide Nanoparticle
2023年3月21日 In this study iron oxide (Fe2O3) nanoparticle samples was prepared using mechanical grinding method The optical properties were studied using UVVis spectrophotometer within a range of 2001100nmFurnace Pig iron and refined iron ore pellets (briquetted iron) can also be used, and because his t method is economic at lower volumes these operations are called mini mills Plants that use Electric Arc Furnaces can be sited closer to the market Where market size permits, some degree of product specialisation is practised 12 Raw MaterialsThe Making of Iron Steel SEAISI2024年8月7日 The two main processing methods for laterite ores are smelting and HighPressure Acid Leaching (HPAL) Smelting is used primarily on saprolite ores to obtain an ironnickel alloy (ferronickel – FeNi, Nickel Pig Iron – NPI) while HPAL is used primarily to process limonite or for higherpurity end productsNickel industry Part 2 Processing nickel laterites and smeltingzinc processing, the extraction of zinc from its ores and the preparation of zinc metal or chemical compounds for use in various products Zinc (Zn) is a metallic element of hexagonal closepacked (hcp) crystal structure and a density of Zinc processing Extraction, Refining Uses Britannica
.jpg)
WO/2023/ METHOD FOR PRODUCING HIGH QUALITY REFINED IRON OXIDE
2023年5月19日 The present invention is a method for refining iron oxide which is a byproduct of a zinc smelting process, the method comprising: a firing process for firing the iron oxide; a washing process for washing an iron oxide cake with a washing liquid, after the firing; and a step for providing iron oxide by filtering the washed iron oxide cake and refining same2019年3月15日 In the paper are shown the history, processing and applications of hematite Hematite is an oxide of iron having the composition Fe2O3 Pure hematite, also called “red ore” contains 70% Fe(PDF) Hematite Processing and ApplicationsCopper processing is a complicated process that begins with mining of the ore (less than 1% copper) and ends with sheets of 9999% pure copper called cathodes, which will ultimately be made into products for everyday useThe most common types of ore, copper oxide and copper sulfide, undergo two different processes, hydrometallurgy and pyrometallurgy, respectively, Copper Mining and Processing: Processing Copper Ores2020年6月10日 224 Direct Reduction of Iron Oxide by Solid Carbon The direct reduction process of iron oxide by solid carbon is highly endothermic in nature and occurs when the molten slag flows over incandescent coke in the bosh region at a temperature above 1000 °C Therefore, the corresponding reaction can be written as follows:Iron and SteelMaking Process SpringerLink
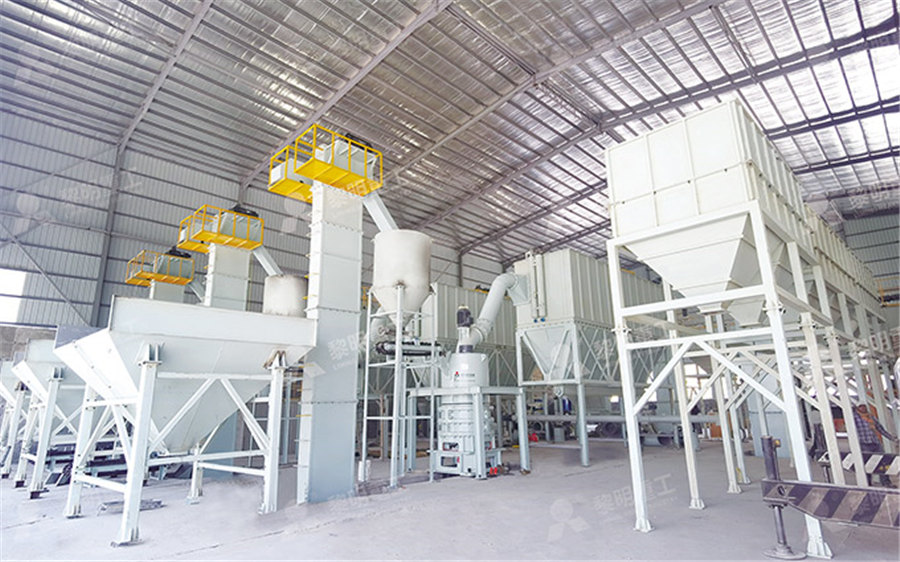
Titanium processing Technology, Methods, Facts Britannica
titanium processing, the extraction of titanium from its ores and the preparation of titanium alloys or compounds for use in various products Titanium (Ti) is a soft, ductile, silvery gray metal with a melting point of 1,675 °C (3,047 °F) Owing to the formation on its surface of an oxide film that is relatively inert chemically, it has excellent corrosion resistance in most natural 2017年4月1日 A study of selective precipitation techniques used to recover refined iron oxide pigments for the production of paint from a The process used to form the synthetic AMD solution involves oxidation and alkaline addition to bring pH to a point that During final data processing, compositions were normalized to 100% A study of selective precipitation techniques used to recover refined Nickel processing Extraction, Refining, Alloying: The extraction of nickel from ore follows much the same route as copper, and indeed, in a number of cases, similar processes and equipment are used The major differences in equipment are the use of highertemperature refractories and the increased cooling required to accommodate the higher operating temperatures in nickel Nickel processing Extraction, Refining, Alloying BritannicaResource Recovery and Recycling from Metallurgical Wastes S Ramachandra Rao, in Waste Management Series, 2006 98 Production of Ceramic Tiles from Iron Ore Tailings Current practice of washing iron ore before it is processed for extractive metallurgical operation results in three products, coarse ore lumps with sizes in the range 1080 mm, which are directly charged Iron Ore Processing an overview ScienceDirect Topics
.jpg)
How iron is made material, manufacture, making, history, used
The iron separated from the surrounding rock but never quite melted Instead, it formed a crusty slag which was removed by hammering This repeated heating and hammering process mixed oxygen with the iron oxide to produce iron, and removed the carbon from the metal