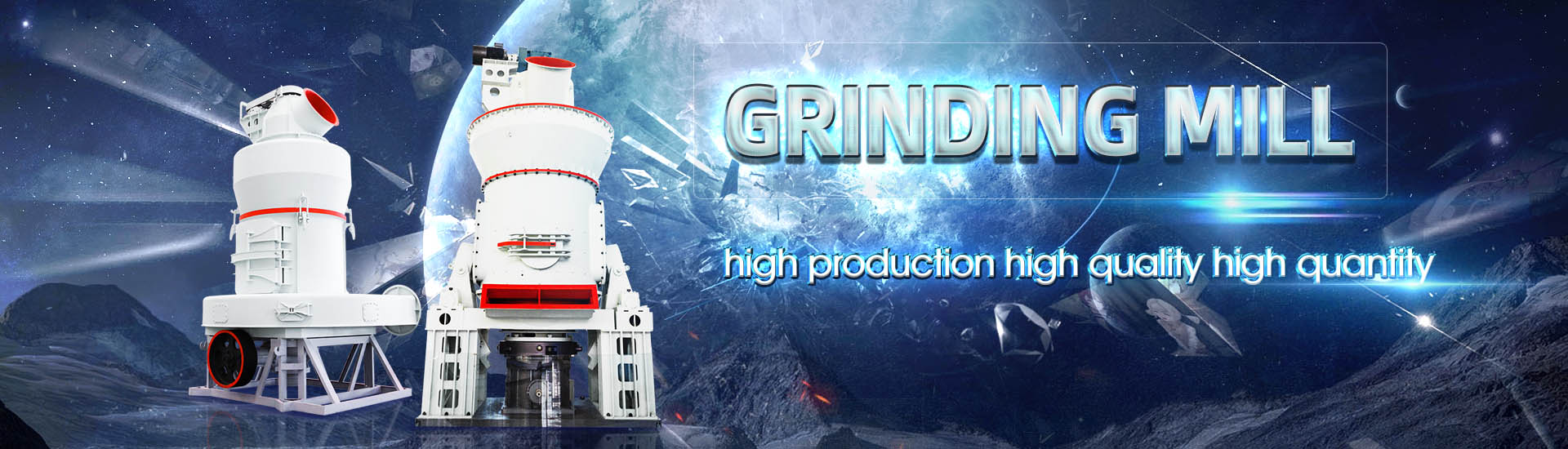
1414 silica mill parameters
.jpg)
Process Parameters Optimization of Silica Sand
2014年2月26日 Experiments are designed using Taguchi method to find the optimum parameters for silica sand nanoparticles production using low speed 2019年3月1日 The three main parameters applied in this study are Ball to Powder weight Ratio (BPR), time milling process, and rotational speed (rpm) The materials used in the study was Parameter Optimization of Ball Milling Process for Silica2019年12月13日 Parameter Optimization of Ball Milling Process for Silica Sand Tailing To cite this article: Sukanto et al 2019 IOP Conf Ser: Mater Sci Eng 494 View the article PAPER OPEN ACCESS Parameter Optimization of Ball Milling 2019年3月29日 Ball milling process was conducted by a planetary type ball mill with WC milling balls and vial at constant parameters like rotating speed, time, BalltoPowder ratio and Process Control(PDF) Parameter Optimization of Ball Milling Process
.jpg)
Comparative Study on Improving the Ball Mill Process Parameters
2021年2月19日 The optimum process parameters setting concluded that balls to powder weight ratio are 20:1, the optimum ball mill working capacity is 2 L while the optimum speed of the ball In this paper, the grinding of dry silica sand in a batch type planetary ball mill is reported The effects of various technical parameters, such as ball size and density of ball material, The Mechanism and Grinding Limit of Planetary Ball Millingt J If the reaction temperature approaches the melting point of silica ≈ 1700 °C or silicon 1414 °C, then significant effects on the morphology can be expected The large quantity of heat A review of magnesiothermic reduction of silica to porous silicon A laboratorycontrolled milling process of silica sand was carried out using aluminum oxide balls of three different sizes The ball wear kinetic equations were experimentally obtained from the Generalized mathematical model applied to a silica sand
.jpg)
The influence of processing parameters on morphology and
2018年8月1日 Many important parameters should be taken into consideration while performing wet ball milling For example, the liquidtopowder ratio (LPR), ie, the solids loading, the type 2017年5月14日 The silica (SiO2) nanoparticles were synthesized from colloidal silica via thermos mechanical route method using ball mill The parameters, which are affecting the CHARACTERIZATION OF SILICA NANOPARTICLES SYNTHESIZED 2017年5月14日 The silica (SiO2) nanoparticles were synthesized from colloidal silica via thermos mechanical route method using ball mill The parameters, which are affecting the milling process has been CHARACTERIZATION OF SILICA NANOPARTICLES The optimum process parameters setting concluded that balls to powder weight ratio are 20:1, the optimum ball mill working capacity is 2 L while the optimum speed of the ball mill is 105 rpm Using SEM characterization, the improved particles Comparative Study on Improving the Ball Mill Process Parameters
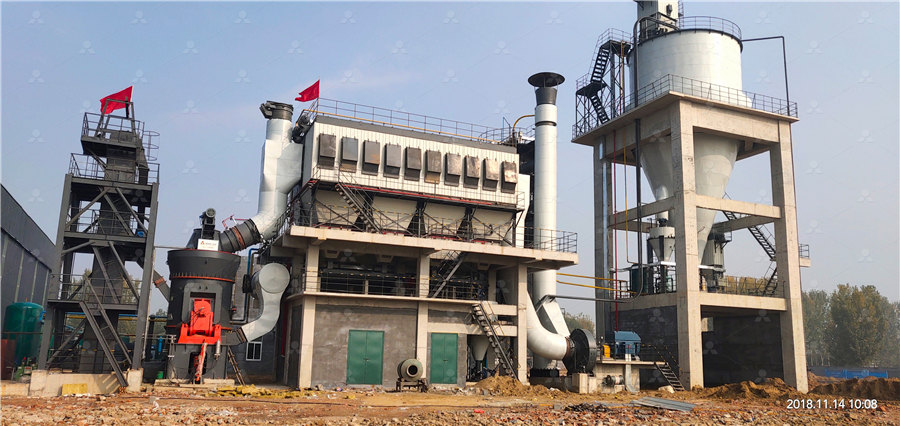
An investigation on the effects of the ball filling on the breakage
2016年7月1日 The chemical properties of the natural amorphous silica sample used experimentally were presented in Table 1The SiO 2 content of the amorphous silica appeared very high (about 90%), on the other hand, the quantities of alkali metal (Na 2 O, K 2 O), the oxide components of alkaline earth metals (CaO, MgO) and sulfur (SO 3) contents were lowIts PDF On Oct 8, 2019, Zhang Chong and others published Development of a Cutting Force Prediction Model for Silica/Phenolic Composite in Millgrinding Find, read and cite all the research you (PDF) Development of a Cutting Force Prediction Model for Silica Download Table Shape parameters of silica particles of ball mill products with 250+212 particle sizes and flotation test for each 10 seconds from publication: Shape parameters of silica particles of ball mill products with 2019年12月13日 Parameter Optimization of Ball Milling Process for Silica Sand Tailing To cite this article: Sukanto et al 2019 IOP Conf Ser: Mater Sci Eng 494 View the article online for updates and enhancements This content was downloaded from IP address 2074613217 on 13/12/2019 at 11:24PAPER OPEN ACCESS Parameter Optimization of Ball Milling
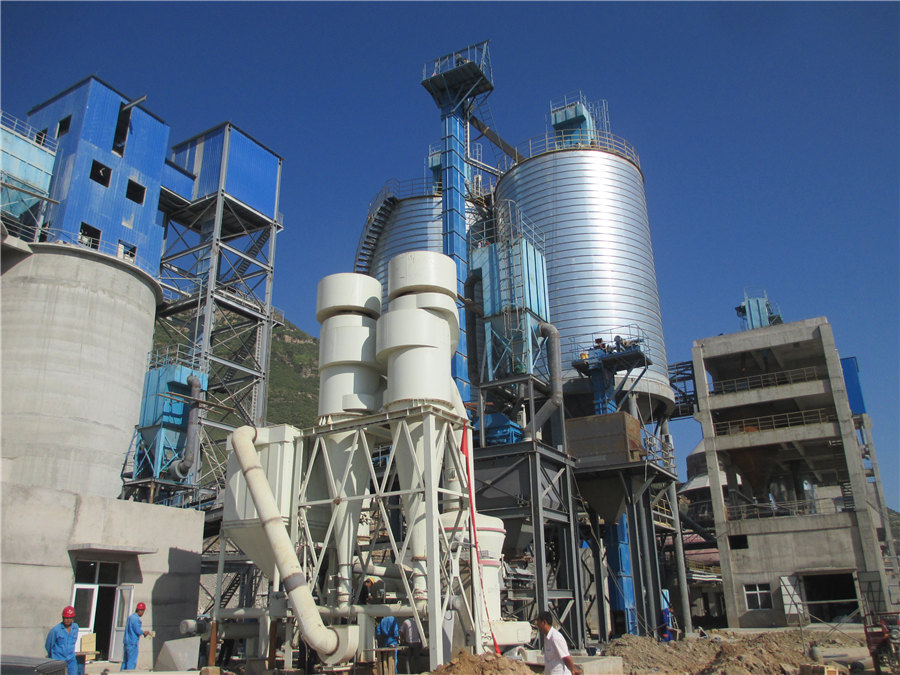
OPTIMIZATION OF MILLING PARAMETERS OF PLANETARY BALL MILL
2018年11月1日 Silica nanoparticles were synthesized from rice husk ash at room temperature by using a high energy planetary ball mill The milling time and mill rotational speed were varied at four levelsPDF On Mar 29, 2019, Sukanto and others published Parameter Optimization of Ball Milling Process for Silica Sand Tailing Find, read and cite all the research you need on ResearchGate(PDF) Parameter Optimization of Ball Milling Process for Silica Development of a Cutting Force Prediction Model for Silica/Phenolic Composite in Millgrinding To cite this article: parameter, k1, k2, k3, was obtained using response surface methodDevelopment of a Cutting Force Prediction Model for Silica2014年2月26日 Process Parameters Optimization of Silica Sand Nanoparticles Production Using Low Speed Ball Milling Method February 2014 Chinese Journal of Engineering 2014(8):14Process Parameters Optimization of Silica Sand Nanoparticles
.jpg)
Effect of operational parameters on the breakage mechanism of silica
Fine grinding of silica was carried out in a jet mill, varying operational parameters such as feed rate, classifier rotational speed and grinding pressure The size reduction of silica was intensive as the jet mill is energy intensive Abrasive and destructive breakage mechanisms took place varying according to the operating conditions of the jet mill The minimum particle size 2008年4月1日 Fine grinding of silica was carried out in a jet mill, varying operational parameters such as feed rate, classifier rotational speed and grinding pressure The size reduction of silica was intensive as the jet mill is energy intensive Abrasive and destructive breakage mechanisms took place varying according to the operating conditions of the jet millEffect of operational parameters on the breakage mechanism of silica Fine grinding process of silica was carried out in a jet mill by varying the operational parameters such as feed rate, classifier rotational speed and grinding pressure The size reduction and mechanochemical effect of silica take place simultaneously as the jet mill is an energy intensive grinding mill The minimum particle size obtained was 315 mu m with span value of 130 and Mechanochemistry of silica on jet mill University of Queensland2008年7月1日 In this paper, ball milling parameters: weight ratio of ball to powder, size of milling balls, type of medium, volume of milling medium and rotation speed in the planetary ball milling of (PDF) Parameters optimization in the planetary ball milling of
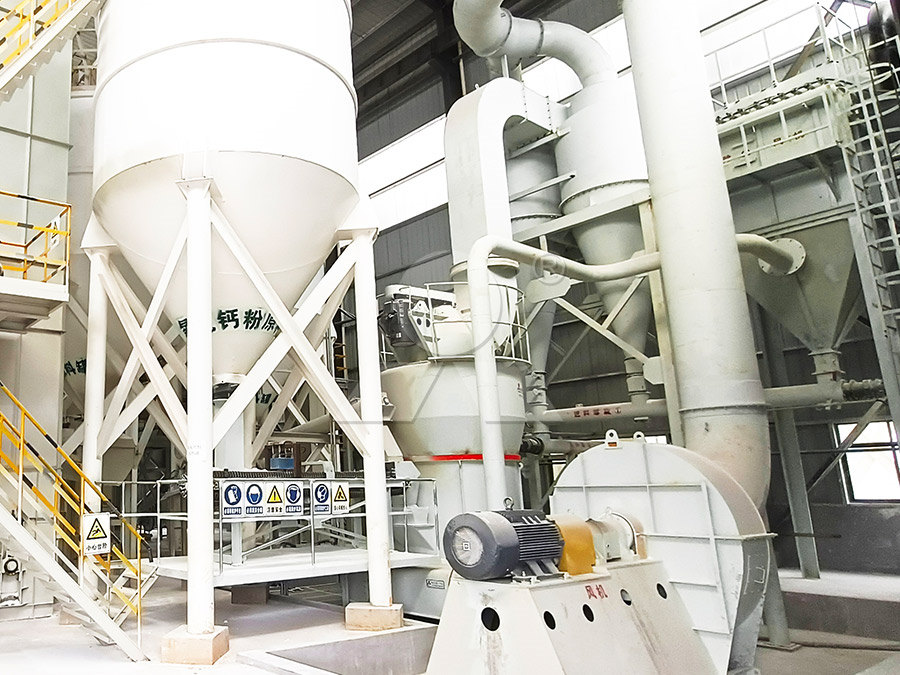
Silicon Powder Properties Produced in a Planetary Ball Mill as a
2020年10月1日 The current study investigates the type of ratio for ball mill jars listed in Table 3 and [63,80,168,181,183] Different balltojar ratios can affect the milling kinetics, the size, and Comparative Study on Improving the Ball Mill Process Parameters Influencing on the Synthesis of Ultrafine Silica Sand: A Taguchi Coupled Optimization Technique https: Geier, N, Szalay, T (2017) Optimisation of process parameters for the orbital and conventional drilling of unidirectional carbon fibrereinforced polymers (UDCFRP Comparative Study on Improving the Ball Mill Process Parameters In this study, silica nanoparticles (SiO2 NPs) were fabricated using a handmade ball mill as a novel, simple, rapid, costeffective, and green approach The sol–gel method was also used to produce these NPs as a comparative method The SiO2 NPs produced by both methods were characterized using highresolution transmission electron microscopy (HRTEM), dynamic light Facile, fast, and green preparation of highpurity and quality silica Download Table Breakage parameter values for different ball mill fill ing from publication: Identification of Optimal Mill Operating Parameters during Grinding of Quartz with the Use of Breakage parameter values for different ball mill fill ing
.jpg)
The designation and structural parameters of silicas
Download Table The designation and structural parameters of silicas from publication: Characterization of Multimodal Silicas Using TG/DTG/DTA, QTG, and DSC Methods The formation of A laboratorycontrolled milling process of silica sand was carried out using aluminum oxide balls of three different sizes The ball wear kinetic equations were experimentally obtained from the evolution curves of the ball diameter as a function of the operating time From a generalized model, the ball entrance flux and ball wear consumption were calculated using exact two Generalized mathematical model applied to a silica sand 2021年2月19日 Taguchibased experimental design technique has been a major research area for making systematic approaches to understand the complex process of ball mill process parameters influencing on the synthesis of ultrafine silica sand monolayer degradation To determine an optimal setting, Taguchi coupled optimization technique has been applied with a Comparative Study on Improving the Ball Mill Process Parameters 2021年7月25日 Therefore, this study investigates the feasibility of using seudoboehmite and its calcination product (γAl2O3) for silica adsorption from a paper mill effluentSilica Removal from a Paper Mill Effluent by Adsorption on

The Effects of Mill Conditions on Breakage
2022年3月1日 In this study, specific rate of breakage values of Şile region quartz sand in three different monosize intervals were determined For this purpose, Şile region quartz sand was prepared in monosize intervals of Read Comparative Study on Improving the Ball Mill Process Parameters Influencing on the Synthesis of Ultrafine Silica Sand: A Taguchi Coupled Optimization Technique ScienceGate AdvancedComparative Study on Improving the Ball Mill Process Parameters 2024年6月20日 The mechanism for MgTR has been the subject of investigation as its deep understanding can help choose appropriate reaction parameters to avoid the formation of unwanted products and to achieve the desired physical properties for energy storage applications 67 It is agreed in the literature that the reaction occurs through the diffusion of Mg vapor into Key developments in magnesiothermic reduction of silica: insights 2008年8月26日 Fine grinding process of silica was carried out in a jet mill by varying the operational parameters such as feed rate, classifier rotational speed and grinding pressure The size reduction and mechanochemical effect of silica take place simultaneously as the jet mill is an energy intensive grinding mill The minimum particle size obtained was 315 μm with span Mechanochemistry of silica on jet milling ScienceDirect
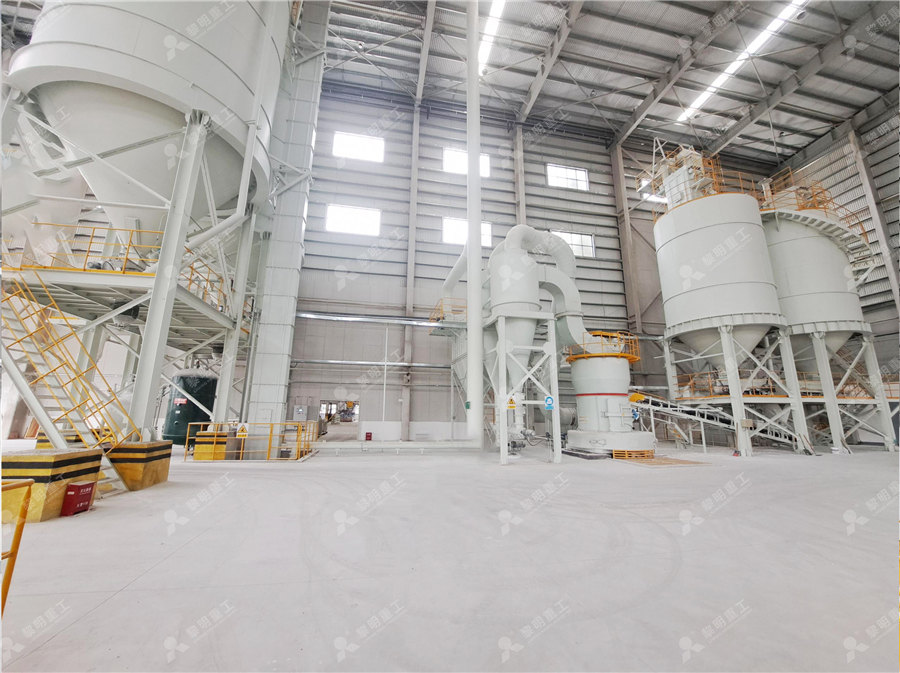
How to choose a silica grinding mill for grinding 120 mesh silica?
Usually, in industrial applications, silica needs to go through a crushing process Usually, it is divided into several product categories according to the particle size of silica: raw silica ore, silica sand, and silica powder Among them, 120140 mesh silica powder has a large demand and great market potential2020年11月22日 and paper mill and found that the val ue s of pH, BOD, COD, suspended solid and total dissolved so l ids were 76, 1140 mg/L, 3288 m g/L, 185 mg/L and 655 mg/L respect iv e ly (PDF) Characteristics and Treatment of Pulp and Paper Mill 2008年4月1日 Effect of operational parameters on the breakage mechanism of silica in a jet mill Authors Samayamutthirian Palaniandy; Khairun Azizi Mohd Azizli; Hashim Hussin; Syed Fuad Saiyid Hashim; Publication date 1 April 2008 Publisher 'Elsevier BV' Doi Cite Abstract Abstract is not availableEffect of operational parameters on the breakage mechanism of silica PIH 1414 Hammer Mill Capacity Chart Rotor dia in mm: Rotor width in mm: Capacity in T/H (Min/Max) Power in kW: 1400: 1400: 140250 110160: Note: The Capacity and parameters indicated in the above chart are approximate and subjected to change with latest versions Features Best Suited for Limestone, Coal, PIH 1414 Puzzolana
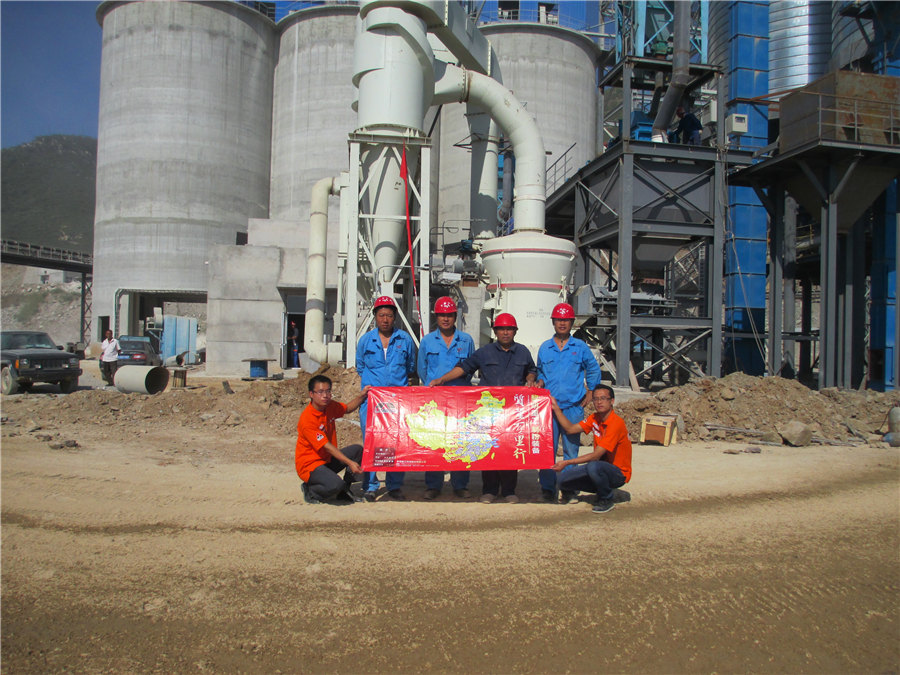
CHARACTERIZATION OF SILICA NANOPARTICLES
2017年5月14日 The silica (SiO2) nanoparticles were synthesized from colloidal silica via thermos mechanical route method using ball mill The parameters, which are affecting the milling process has been The optimum process parameters setting concluded that balls to powder weight ratio are 20:1, the optimum ball mill working capacity is 2 L while the optimum speed of the ball mill is 105 rpm Using SEM characterization, the improved particles Comparative Study on Improving the Ball Mill Process Parameters 2016年7月1日 The chemical properties of the natural amorphous silica sample used experimentally were presented in Table 1The SiO 2 content of the amorphous silica appeared very high (about 90%), on the other hand, the quantities of alkali metal (Na 2 O, K 2 O), the oxide components of alkaline earth metals (CaO, MgO) and sulfur (SO 3) contents were lowIts An investigation on the effects of the ball filling on the breakage PDF On Oct 8, 2019, Zhang Chong and others published Development of a Cutting Force Prediction Model for Silica/Phenolic Composite in Millgrinding Find, read and cite all the research you (PDF) Development of a Cutting Force Prediction Model for Silica
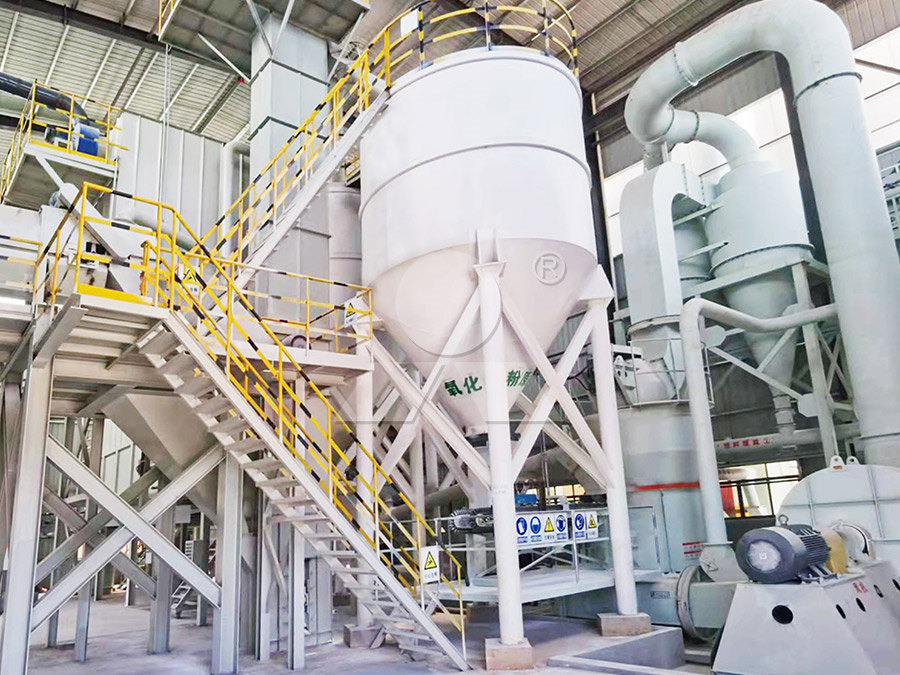
Shape parameters of silica particles of ball mill products with
Download Table Shape parameters of silica particles of ball mill products with 250+212 particle sizes and flotation test for each 10 seconds from publication: 2019年12月13日 Parameter Optimization of Ball Milling Process for Silica Sand Tailing To cite this article: Sukanto et al 2019 IOP Conf Ser: Mater Sci Eng 494 View the article online for updates and enhancements This content was downloaded from IP address 2074613217 on 13/12/2019 at 11:24PAPER OPEN ACCESS Parameter Optimization of Ball Milling 2018年11月1日 Silica nanoparticles were synthesized from rice husk ash at room temperature by using a high energy planetary ball mill The milling time and mill rotational speed were varied at four levelsOPTIMIZATION OF MILLING PARAMETERS OF PLANETARY BALL MILL PDF On Mar 29, 2019, Sukanto and others published Parameter Optimization of Ball Milling Process for Silica Sand Tailing Find, read and cite all the research you need on ResearchGate(PDF) Parameter Optimization of Ball Milling Process for Silica
.jpg)
Development of a Cutting Force Prediction Model for Silica
Development of a Cutting Force Prediction Model for Silica/Phenolic Composite in Millgrinding To cite this article: parameter, k1, k2, k3, was obtained using response surface method2014年2月26日 Process Parameters Optimization of Silica Sand Nanoparticles Production Using Low Speed Ball Milling Method February 2014 Chinese Journal of Engineering 2014(8):14Process Parameters Optimization of Silica Sand Nanoparticles