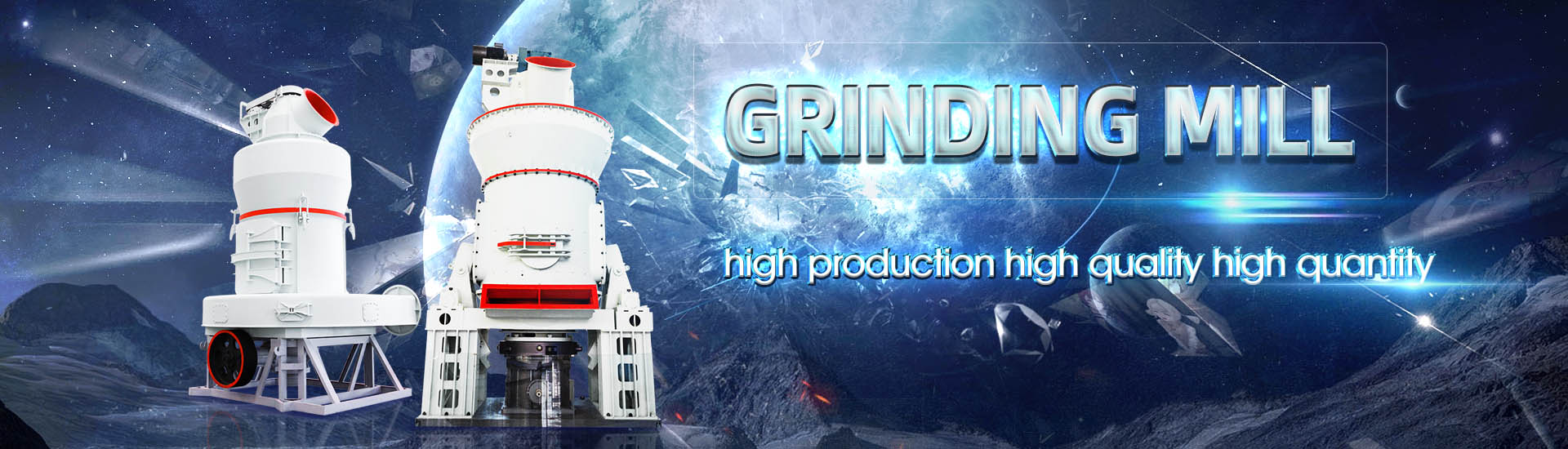
Suspension roller ore mill main shaft diameter torque and speed
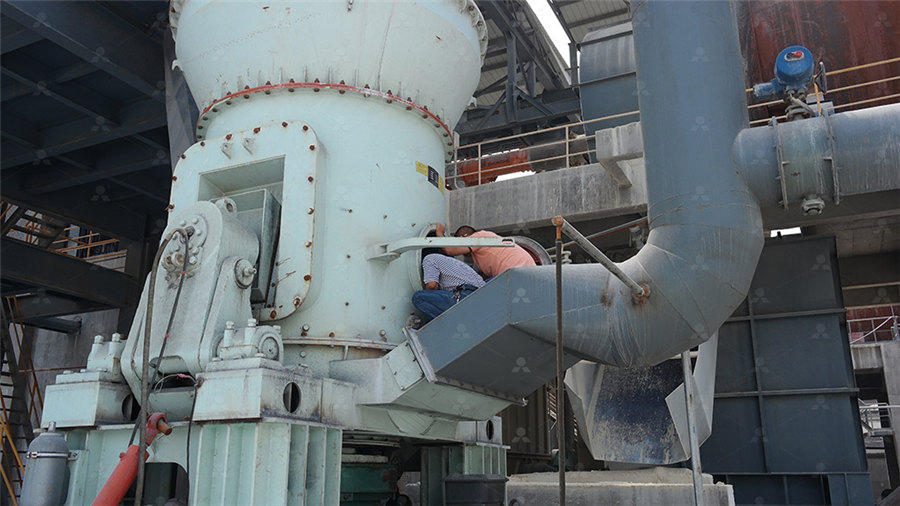
INVESTIGATION OF EFFECT OF OPERATIONAL PARAMETERS ON
parameters on vertical roller mill grinding performance In this context, systematic test plans have been generated According to test plans; dam ring height, grinding pressure, classifier rotor speed, airflow rate, mill differential parameters were testedThe scope of this paper is to analyse the strength and hardness of the sugarcane roller shaft, which has the main contribution in the sugarcane industries Forged steel is used for making (PDF) Roller Shafts for Sugar Cane Mills: FEA Analysis for Fatigue 2011年9月14日 This article describes a scientific design procedure that begins from a given product mix to a customized rolling mill The procedures were programmed into a pass (PDF) A JOURNEY TO OPTIMAL ROLLING MILL DESIGN FROM2016年9月1日 In vertical roller mills there are several factors that influence the performance of the grinding process [22] which are moisture content (mc), grinding table rotation speed (s), Operational parameters affecting the vertical roller mill
.jpg)
Roller Mill Springer
Roller mill is a type of grinding equipment for crushing materials by pressure between two or more rolling surfaces or between rolling grinding bodies (balls, rollers) and a track (plane, ring, and 2017年5月1日 Moreover, the changes in the torque and power consumption of a ball mill can be effectively explained using two important factors: lifter and particle area ratio 1 Introduction Effect of lifters and mill speed on particle behaviour, torque, and 1998年1月1日 A net of approximately 120 to 130 percent of running torque is required to cascade the charge in these mills The pullin torque is about 130 to 140 percent with the Rod and Ball Mills (d7a19c4ab72b4e31abb4bdb037d4fa45)1992年6月1日 Some recent contributions to modelling and optimization of speed control of the main drive for the horizontal stand in reversible roughing rolling mills aimed at performance Modelling and Optimization of Speed Control of the Main Drive in
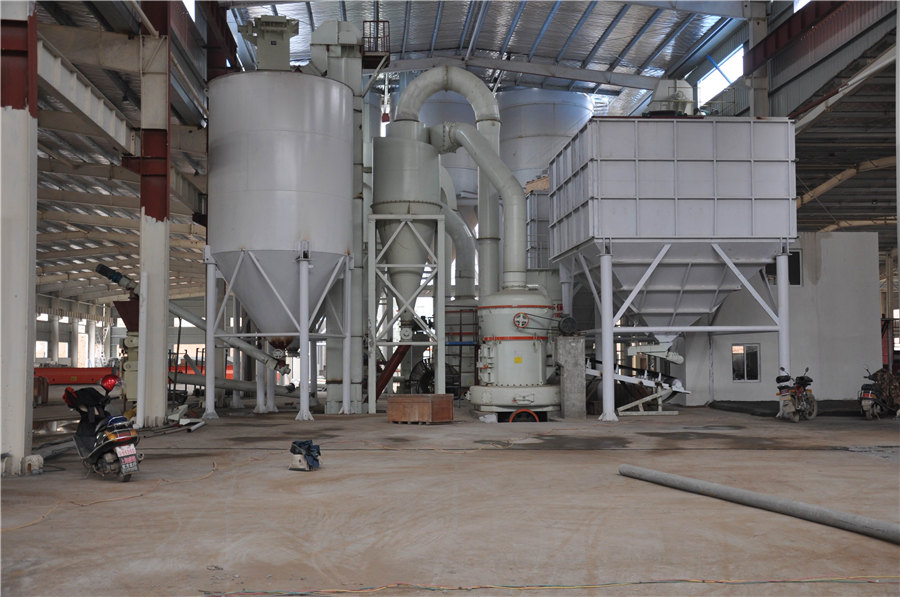
Operational parameters affecting the vertical roller mill
2017年4月1日 Pilot plant test results with various ores showed that low energy consumption feature of vertical roller mills is applicable to the ore industry Grinding test results for zinc ore MILL DATA Mill Size 161/2 56 x 66 4 High Mill Speed 350 / 700 FPM Separating Force 6,480,000 lbs maximum Stall Force 8,100,000 lbs maximum Tension 30,000 lbs maximum ROLLING MILL SPECIFICATIONS Ferrous Metal Processing2024年10月19日 Calculation Example: The design of a shaft involves determining the diameter of the shaft based on the power it transmits, its speed, and the allowable shear stress for the shaft material The torque transmitted by the shaft is calculated using the formula T = (P * 60) / (2 * π * N), where P is the power, N is the speed in revolutions per minute, and π is a mathematical Shaft Diameter Calculation Based on PowerSpeedStress 2018年5月14日 Sample Problem to calculate the shaft diameter from the torque Problem: A shaft is transmitting 200 kW at 1200RPM Find a suitable diameter for the shaft, if the maximum torque transmitted exceeds the mean by 30% Take How to calculate the shaft diameter from the torque?
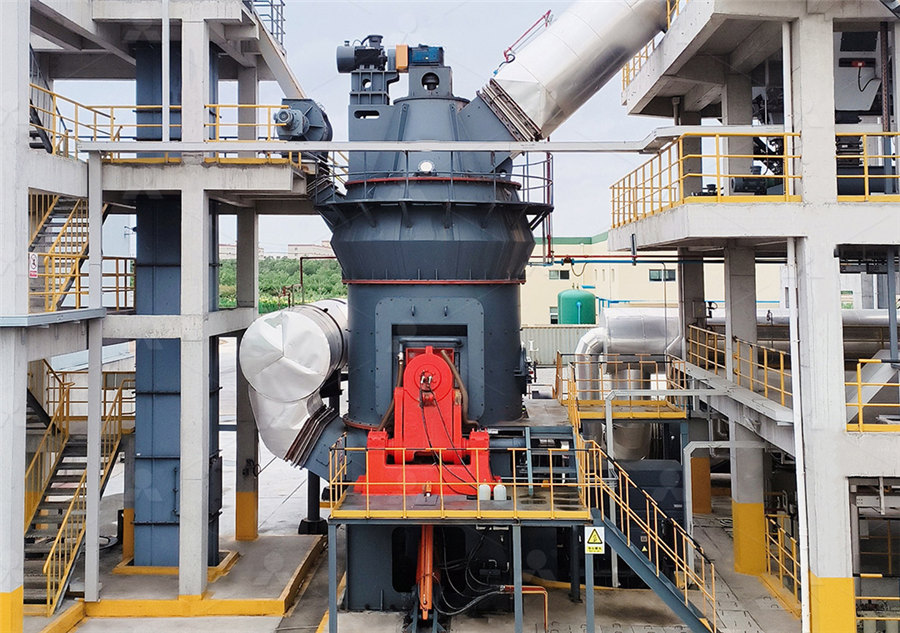
Paper # 25 Copper Mountain Overview on the Grinding Mills
Mountain, the inching mode in the ABB drives are currently set to turn the SAG mill at about 10 % of rated speed and the ball mills at about 3% of rated speed (mill speed 040 rpm) Furthermore tests during the hot commissioning have shown that the drives can even operate in inching mode at as little as 1% rated speed (mill speed 010 rpm)2011年12月17日 Example 2 For the 200hp (150kW), 1,800rpm motor from Example 1, the minimum shaft size to limit torsional deflection would be: The minimum shaft diameters calculated by the torque transmission and torsional deflection methods are essentially the same for Examples 1 and 2Relationship of Torque and Shaft Size Pumps Systems2019年12月23日 3472 Determination of Shaft Diameter Due to Only Twisting Moment Error! Bookmark not defined 3473 Determination of Shaft Diameter on the Basis of Rigidity Error!DEVELOPMENT OF A HORIZONTAL SHAFT HAMMER MILL CHAPTER 2015年7月24日 torque The top roller is most highly stressed, since it consumes about half of the mill torque The forces on the top roller are because of power transmission, crushing, and hydraulic load For safety and long life of top, feed discharge roller shaft diameter is considered as Ø570 mm for Ø40”x80”conventional sugar mill But due to heavyStatic Structural Analysis of Conventional Sugar Mill Roller Shaft
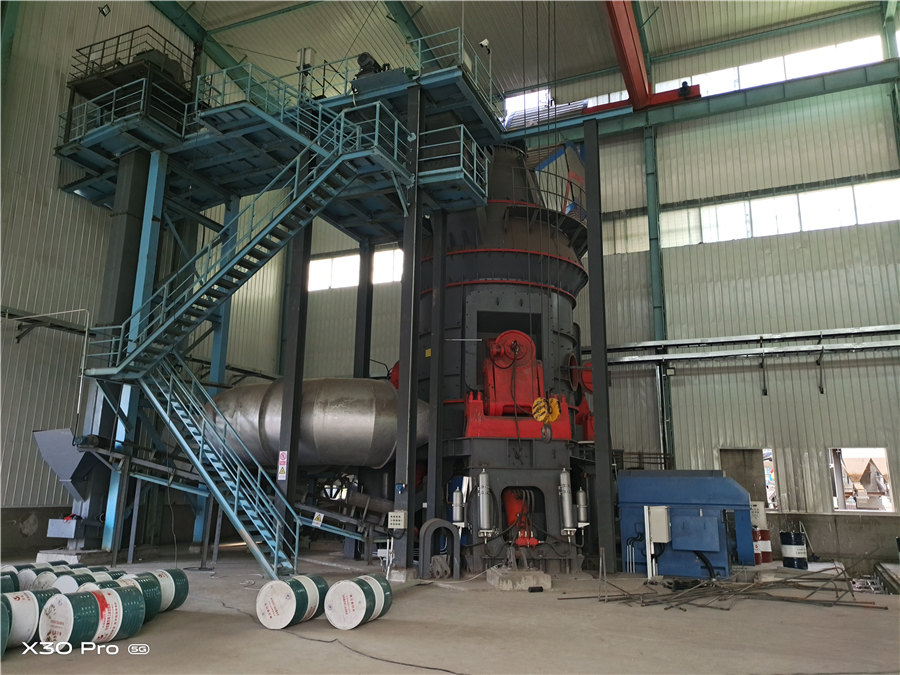
DEVELOPMENT OF A HORIZONTAL SHAFT HAMMER MILL CHAPTER
This project is all about Hammer mill failure during flux crushing The Hammer Mill consists of roller; hammer beams Bookmark not defined 3474 Shaft Diameter Due to % Torsional deflection or angle of rad twist 𝜃 Torsional shear stress N/m2 TM g Shaft diameter d m Shaft speed N rpm Shaft torque Ts Nm Pout Download scientific diagram Torque as function of main shaft rotation from publication: Modeling of Wind Turbine Gearbox Mounting In this paper three bushing models are evaluated to find a Torque as function of main shaft rotation ResearchGatewound roll diameter Therefore, constant torque at the drum will result in constant tension on the web Surface winders are, then, constant torque drive applications Relatively straightforward speed controls involved Centerwinds are significantly more complex As the web is wound, the diameter (or radius) increases The circumference also TENSION CONTROL AND WINDER Dynamatic® OEM2022年11月10日 Mill drum speed is one of process variables due to which it is possible to control ore destruction mechanisms when choosing speed operation mode of adjustable electric mill driveMonitoring of grinding condition in drum mills based on resulting shaft
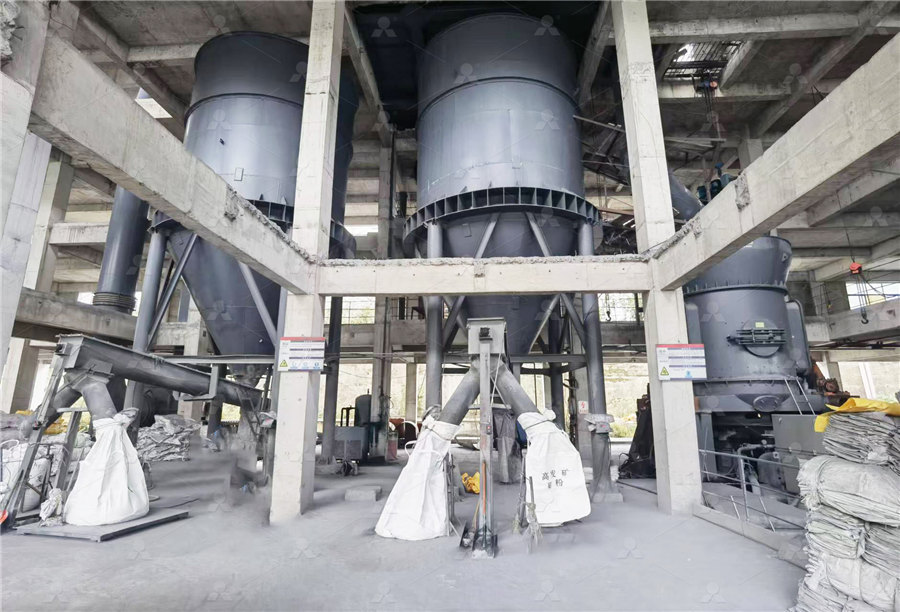
Effect of lifters and mill speed on particle behaviour, torque, and
2017年5月1日 This study examines how the ball mill's torque, power consumption, particle behaviour, and kinetic energy are affected by new helical lift bar forms and mill speed through an analysis utilising 2020年8月12日 VRM has been widely researched in processing of cement (Ito et al 1997;Jorgensen 2005;Wang et al 2009, Ghalandari et al 2021), coal (Tontu 2020), iron ore (Reichert et al 2015), zinc ore (van An investigation of performance characteristics and 2022年12月15日 It can be concluded that the HPGRStirred mill combination was a more energyefficient grinding circuit than the HPGRBall mill combination for PGE bearing chromite oreSize reduction performance evaluation of HPGR/ball 2019年10月8日 For example, at about 15% full load speed the required torque typically is around 5% or 10% full load torque As shown below, the pump torquespeed curve follows the square law: Overlaying TorqueSpeed Curves to Match Motors to Pumps Like pumps, motors produce a torquespeed curve of their ownUnderstanding Centrifugal Pump and Motor TorqueSpeed
.jpg)
Relationship of torque and shaft size Plant Engineering
2015年4月13日 But changes in horsepower and speed (rpm) affect torque, as the following equation shows: Torque (lbft) Since the calculated shaft diameter for a 200 hp motor is designed to withstand twice the rated torque, the shaft diameter of 2371 in is at the absolute minimum for the 400 hp ratingabout half of the mill torque The forces on the top roller are because of power transmission, crushing, and hydraulic load The loads on the roller are divided into horizontal and vertical component of loading Power(p)= 900 kw Roller Speed (n)= 5 rpm Roller dia= 1200 mm Shaft dia at roller=710mm Shaft dia at bearing support=610mmStatic Structural Analysis of Crushing Rollers of Three Roller Sugar Mill2016年12月31日 The performance of 12065 mm (475 in) bore high speed design, tapered roller bearings was investigated at shaft speeds to 20,000 rpm (24 million DN) under combined thrust and radial loadDesign and Test Rig Experiments of a High Speed Tapered Roller Bearing International Journal of Engineering and Management Research eISSN: 22500758 pISSN: 23946962 Volume11, Issue2 (April 2021)Design and Analysis of Rotor Assembly of Hammer Mill Machine
.jpg)
(PDF) The Ball Mill Driving Device Fault and the Main Bearing
2013年4月1日 Ball mill hollow shaft diameter and ball mill cylinder clearance diameter is about 03~055 With the normal operating voltage, because the hollow shaft is la rger in size, so theAbstract Crushing and grinding consume most of the energy in mineral processing Ball mill is an important kind of grinding equipment used to decrease the size of ore particles The power consumption of a ball mill is one of the most important parameters to consider in the design of a ball mill because it determines its economic efficiency The power consumption is usually Effect of lifters and mill speed on particle behaviour, torque, and In this video, we'll take you inside a rolling mill to show you how the drive shaft works to transmit torque and power to the mill's rollers You'll see how Inside Look: How Rolling Mill Drive Shaft Transmits Torque2016年10月23日 Motor speeds should be between 580 and 1160 rpm The lower speeds apply to large diameter mills, the higher speeds to the smaller DIRECT CONNECTED Ball Ball Mill SPEED REDUCER DRIVE The Ball Mill Drives 911Metallurgist
.jpg)
Design of Shafts IIT Bombay
Most shafts will transmit torque through a portion of the shaft Typically the torque comes into the shaft at one gear and leaves the shaft at another gear A free body diagram of the shaft will allow the torque at any section to be determined The torque is often relatively constant at steady state operation The shear stress due to the torsionFig 3 Side view of roller mill shaft Rollers Shaft inputs data are as follows: D 1, D 2, D 3, D 4, D 5, D 6 is diameter of shaft section 1, roller, shaft section 2, support 1, key section and support 2 L 1, L 2, L 3, L 4, L 5, L 6 is length of shaft section1, roller, shaft section 2, support 1, key section and support 2 D 1= 305 mm, D 2 Titanium Alloy is Best Material for Roller Shaft in Sugar Mill IJITEEthat the main shaft speed of 9135 rpm transmitted by a belt drive from a three horse power Determination of the Torque and Power Transmitted for the Shaft Power = 1 T 2 V, r 1 T 2 R Determination of Hammer Shaft Diameter I b max s M Y 1 allowable Z M Z Y I b V s max Spolt, 1988 (10) Where Y maxDESIGN, FABRICATION AND TESTING OF A LABORATORY SIZE HAMMER MILLT rm = Rolling torque which is converted to motor shaft taking into account the gear ratio between motor shaft and the rolls T fm = Torque for overcoming friction in the roll neck bearing (converted to motor shaft) T trm = Torque to overcome friction in transmission system (converted to motor shaft) The system may consist of couplings, gear box for speed reduction, pinion box for How to Obtain Rolling Torque? Metals Metallurgy
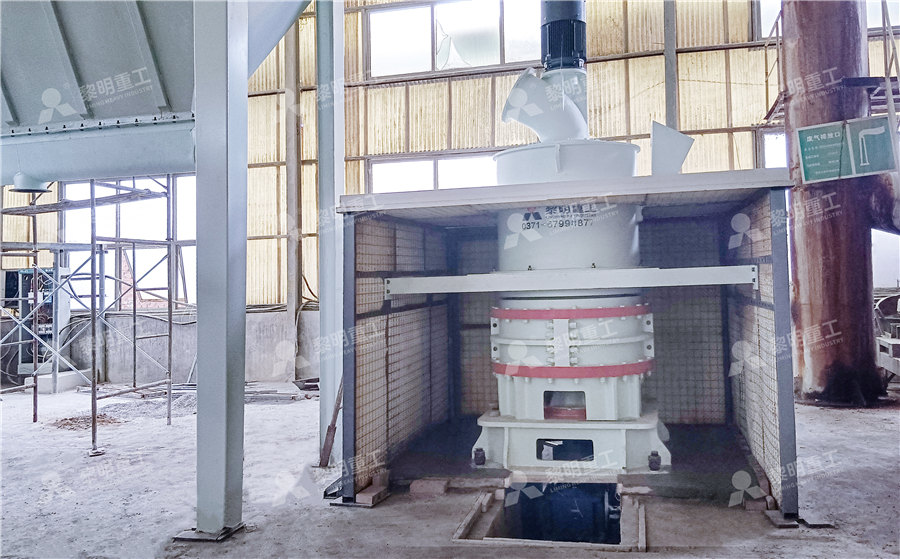
Shaft Speed Calculator Engineering
2020年5月21日 Calculates shaft speed of high spindle machines using the shaft's diameter and revolutions per minute (RPM) Skip to content Subscribe Technology Back Technology Browse All All 3D Printing Advanced Manufacturing hs Highspeed shaft/coupling mb1,mb2 Upwind and downwind main bearing for fourpoint suspension mb Main bearing for threepoint suspension ms Main shaft ms,i Inner main shaft norm Normal stress range p Planet r Rotor ra Radial rb Rotor–main bearing RNA Rotor–nacelle assembly s Sun rg Ring t Transformer T F Transformer TW TowerAn Analytical Formulation for Sizing and Estimating the 2014年10月24日 Figure 1: The 3point mount SRB design supports the main shaft bearing and two reactionary torque arms on the gearbox Contributing Factors High thrust load on a radial SRB bearing: While there is no official maximum limit, a conventional ratio of permissible thrusttoradial load for tworow spherical roller bearings is between 015 and 020Designing Reliable, Costeffective Wind Turbine Shaft Systems2015年6月19日 The basic parameters used in ball mill design (power calculations), rod mill or any tumbling mill sizing are; material to be ground, characteristics, Bond Work Index, bulk density, specific density, desired mill tonnage capacity DTPH, operating % solids or pulp density, feed size as F80 and maximum ‘chunk size’, product size as P80 and maximum and finally the type of Ball Mill Design/Power Calculation 911Metallurgist
.jpg)
Shaft Diameter Calculation Based on PowerSpeedStress
2024年10月19日 Calculation Example: The design of a shaft involves determining the diameter of the shaft based on the power it transmits, its speed, and the allowable shear stress for the shaft material The torque transmitted by the shaft is calculated using the formula T = (P * 60) / (2 * π * N), where P is the power, N is the speed in revolutions per minute, and π is a mathematical 2018年5月14日 Sample Problem to calculate the shaft diameter from the torque Problem: A shaft is transmitting 200 kW at 1200RPM Find a suitable diameter for the shaft, if the maximum torque transmitted exceeds the mean by 30% Take How to calculate the shaft diameter from the torque?Mountain, the inching mode in the ABB drives are currently set to turn the SAG mill at about 10 % of rated speed and the ball mills at about 3% of rated speed (mill speed 040 rpm) Furthermore tests during the hot commissioning have shown that the drives can even operate in inching mode at as little as 1% rated speed (mill speed 010 rpm)Paper # 25 Copper Mountain Overview on the Grinding Mills 2011年12月17日 Example 2 For the 200hp (150kW), 1,800rpm motor from Example 1, the minimum shaft size to limit torsional deflection would be: The minimum shaft diameters calculated by the torque transmission and torsional deflection methods are essentially the same for Examples 1 and 2Relationship of Torque and Shaft Size Pumps Systems
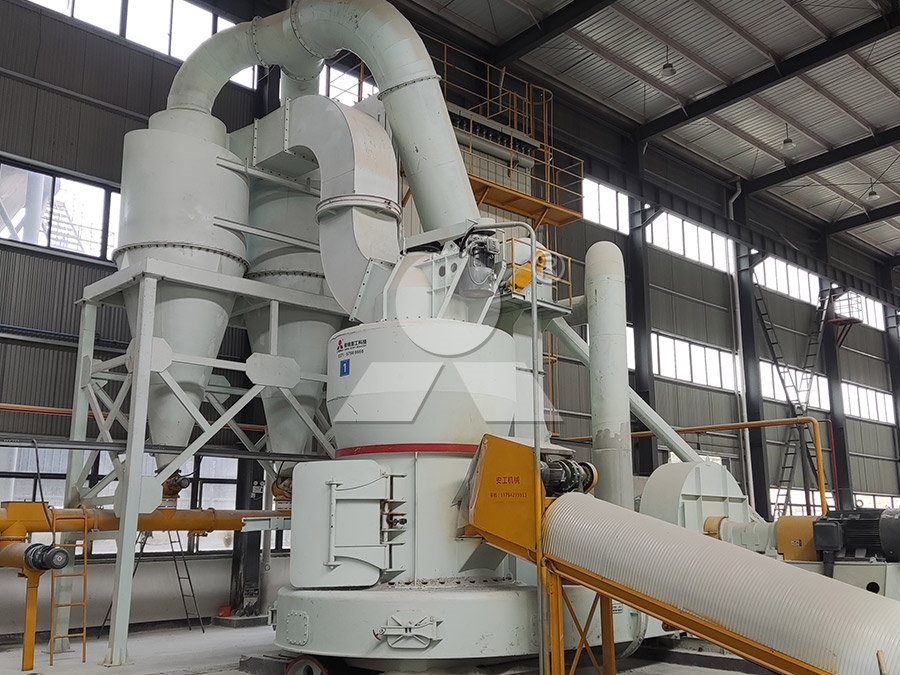
DEVELOPMENT OF A HORIZONTAL SHAFT HAMMER MILL CHAPTER
2019年12月23日 3472 Determination of Shaft Diameter Due to Only Twisting Moment Error! Bookmark not defined 3473 Determination of Shaft Diameter on the Basis of Rigidity Error!2015年7月24日 torque The top roller is most highly stressed, since it consumes about half of the mill torque The forces on the top roller are because of power transmission, crushing, and hydraulic load For safety and long life of top, feed discharge roller shaft diameter is considered as Ø570 mm for Ø40”x80”conventional sugar mill But due to heavyStatic Structural Analysis of Conventional Sugar Mill Roller Shaft This project is all about Hammer mill failure during flux crushing The Hammer Mill consists of roller; hammer beams Bookmark not defined 3474 Shaft Diameter Due to % Torsional deflection or angle of rad twist 𝜃 Torsional shear stress N/m2 TM g Shaft diameter d m Shaft speed N rpm Shaft torque Ts Nm Pout DEVELOPMENT OF A HORIZONTAL SHAFT HAMMER MILL CHAPTER Download scientific diagram Torque as function of main shaft rotation from publication: Modeling of Wind Turbine Gearbox Mounting In this paper three bushing models are evaluated to find a Torque as function of main shaft rotation ResearchGate

TENSION CONTROL AND WINDER Dynamatic® OEM
wound roll diameter Therefore, constant torque at the drum will result in constant tension on the web Surface winders are, then, constant torque drive applications Relatively straightforward speed controls involved Centerwinds are significantly more complex As the web is wound, the diameter (or radius) increases The circumference also 2022年11月10日 Mill drum speed is one of process variables due to which it is possible to control ore destruction mechanisms when choosing speed operation mode of adjustable electric mill driveMonitoring of grinding condition in drum mills based on resulting shaft