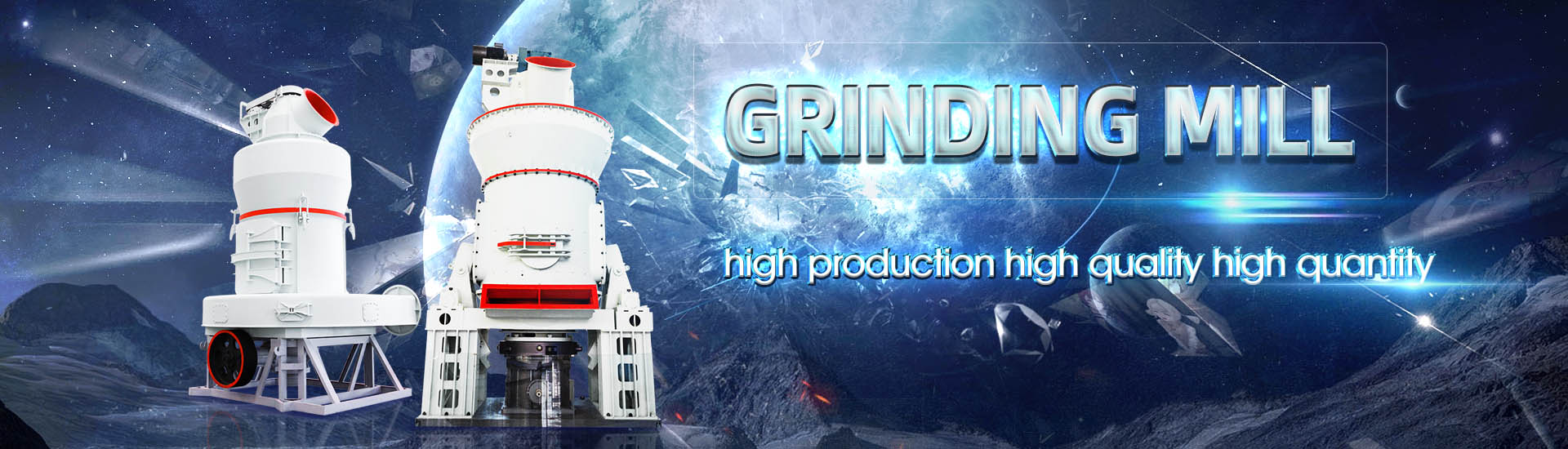
Cement manufacturing principle Cement manufacturing principle Cement manufacturing principle
.jpg)
The Cement Plant Operations Handbook International Cement
The Cement Plant Operations Handbook is a concise, practical guide to cement manufacturing and is the standard reference used by plant operations personnel worldwide Providing a Manufacturing of cement involves various raw materials and processes Each process is explained chemical reactions for manufacture of Portland Cement Cement is a greenish grey colored powder, made of calcined mixtures of clay Manufacture of Cement Materials and Manufacturing This article will guide readers through each step in the manufacturing of cement, detailing critical processes such as blending, hydration, and the role of calcium carbonate, silica, alumina, and iron oxide in cement productionStepbyStep Guide to the Manufacturing of CementCEMENT MANUFACTURE The cementmaking process can be divided into two basic steps: Clinker (the main constituent of cement) is first made in a kiln with gas up to 2000°C, which heats raw materials such as limestone (calcium The story of cement manufacture Cembureau
.jpg)
How Cement is Made Portland Cement Association
Cement is manufactured from materials heated together at high temperatures to form a rocklike substance that is ground into a fine powder Limestone, marl, and clay are commonly used sources of these primary elements Other materials The principle is based on the relation between the flow of air through the cement bed and the specific area of the particles comprising the cement bed Hence, the surface area per unit 1 Manufacturing Process of Cement Indus University2023年12月20日 Cement manufacturing is a complex process that begins with mining and then grinding raw materials that include limestone and clay, to a fine powder, called raw meal, which is then heated to a sintering temperature as The Cement Manufacturing Process Thermo Fisher The most important raw materials for making cement are limestone, clay, and marl These are extracted from quarries by blasting or by ripping using heavy machinery Wheel loaders and dumper trucks transport the raw material to the How cement is made Heidelberg Materials
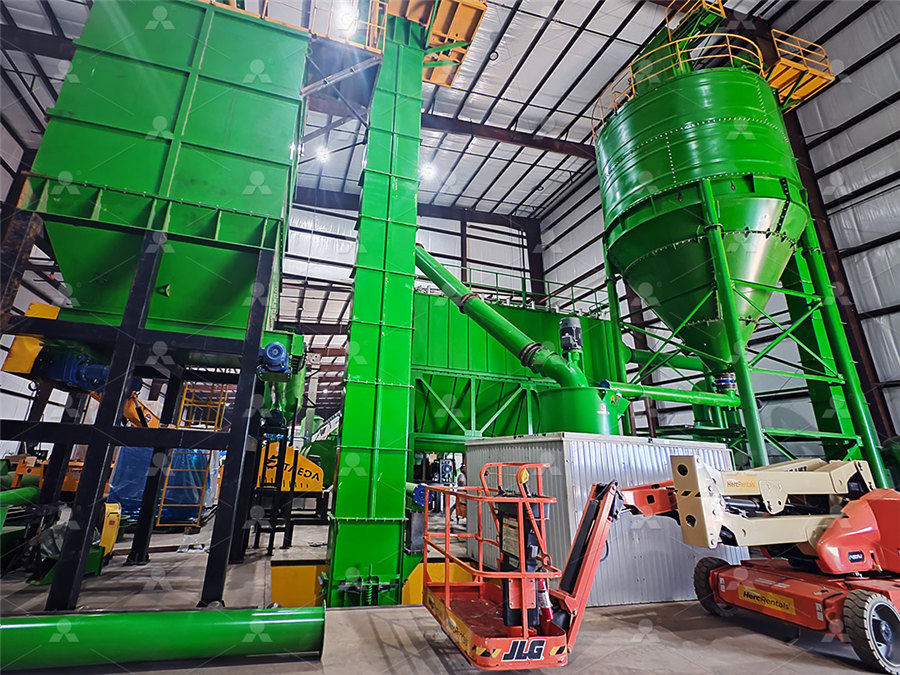
How Cement is Made Cement Manufacturing Process
Stage of Cement Manufacture There are six main stages of the cement manufacturing process Stage 1: Raw Material Extraction/Quarry The raw cement ingredients needed for cement production are limestone (calcium), sand and clay (silicon, aluminum, iron), shale, fly ash, mill scale, and bauxite The ore rocks are quarried and crushed into smaller pieces of about 6 inches5 CEMENT –HISTORY In India, Portland cement was first manufactured in 1904 near Madras, by the South India Industrial LtdBut this venture failed Between 1912 and 1913, the Indian Cement Co Ltd, was established at Porbander (Gujarat) and by 1914 this Company was able to deliver about1000 tons of Portland cement By 1918 three factories were established1 Manufacturing Process of Cement Indus University2020年10月15日 We take a Φ900 x 900mm single rotor, irreversible multirow hinged hammer crusher as an example to introduce its structure and parts This type of hammer crusher is commonly seen in cement plants and is suitable for Hammer Crusher Working Principle AGICO Cement Request PDF On Dec 1, 2022, Kassu Jilcha published Minimizing Clinker Production Operational Cost Using Lean Manufacturing Principle: A Case of Clinker Production in Mugher Cement Factory By Minimizing Clinker Production Operational Cost Using Lean Manufacturing
}@~3SRDG`IA1KP_ICWAA.jpg)
Cement Manufacturing 1 PDF Cement Concrete
CementManufacturing1pptx Free download as Powerpoint Presentation (ppt / pptx), PDF File (pdf), Text File (txt) or view presentation slides online The document discusses the history and manufacturing process of cement It describes how ancient Egyptians and Romans used early forms of cement made from lime and pozzolana The modern dry process is then outlined, 2014年10月4日 Cement manufacturing Download as a PDF or view online for free Submit Cement manufacturing Four Principle minerals in OPC are designated as under C3 A – 4 to 14% C3 AF – 10 to 18% C3 S – 45 to 65% C2 S – 15 to 35% 12Cement manufacturing PPT Free Download SlideShare2021年4月28日 Therefore, in the cement manufacturing context, automation would mean a largescale shift from laborintensive methods to skillintensive methods The accelerated incorporation of realtime monitoring systems, advanced control systems would constitute the first step in realizing a genuinely 21stcentury cement manufacturing processDemystifying Automation in Cement Manufacturing BirlasoftAlthough the basic cement manufacturing principle (dry process) of all cement plants is same, however the equipment installed vary according to the selection made by cement plant supplier We understand the different requirements and equipment being used in the cement plants and can offer same as per your requirementEquipment And Spares For All Stages Of Cement Manufacturing
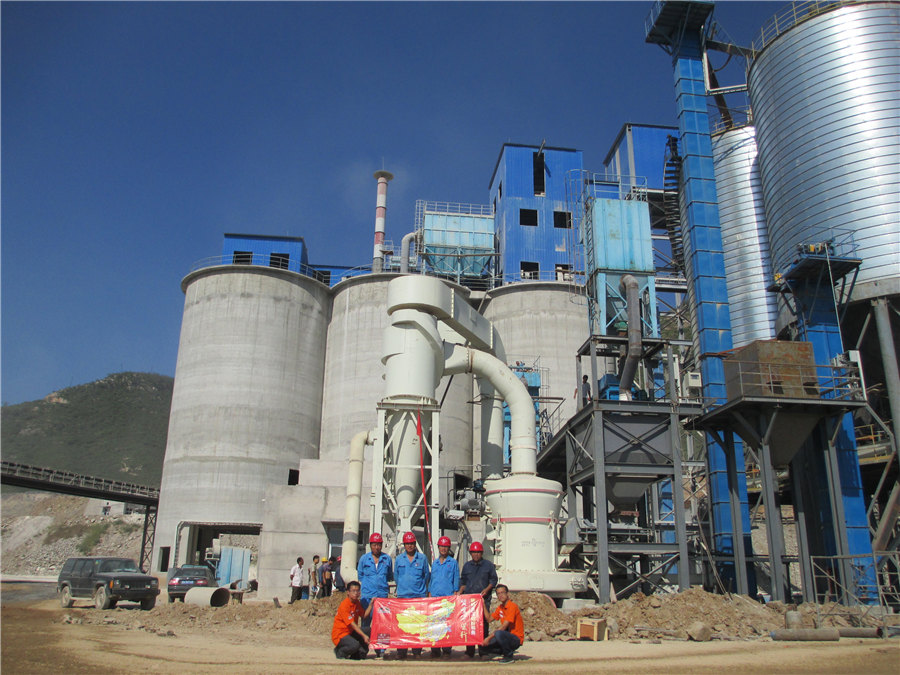
Guidelines for CoProcessing Fuels and Raw Materials in Cement
use of waste in the cement manufacturing process, but rather outlines the most important principles and procedures which must be undertaken in the responsible use of coprocessing in cement manufacturing These guidelines should therefore be used in conjunction with other internationally recognized guidance documents, most notably:Cement Manufacturing with Air Lift Pumps The principle behind its operation involves injecting air into the lower part of the pipe, reducing the density of the mixture inside, causing it to rise and move upwards This simple yet effective mechanism is particularly suited for handling cement and other bulk materialsCement Manufacturing with Air Lift Pumps2016年7月8日 Report on Cement manufacturing process Download as a PDF or view online for free It is made by manganese steel Working principle The main working part of the Crusher is the rotor with hammer rings The rotor is Report on Cement manufacturing process PDFThe cement roller press is a type of material crushing machine which is often used in cement plants It usually works together with a ball mill to form a pregrinding or finalgrinding system for the grinding of raw materials, coal, and Hydraulic Roller Press AGICO Cement Plant
.jpg)
Cement Manufacturing Processpptx Free Download
2023年3月5日 Cement Manufacturing Processpptx The cyclone separator is a device for separating solid particles from contaminated gas streams Working principle : A cyclone is a centrifugal separator in which particles, due to their PDF On Dec 9, 2015, Momen Marwan Mohsen published Cement Manufacturing Find, read and cite all the research you need on ResearchGate Research Proposal PDF Available Cement Manufacturing(PDF) Cement Manufacturing ResearchGateCement Manufacturing Process by TIZITA MOGES , SELAMU ABULE DEREJE ENDALAMAW IF YOU NEED THIS GUIDE AND ALL OTHER USEFUL EXCEL SHEETS WHICH WILL MAKE YOU MASTER THE PRODUCTION , PROCESS , MAINTENANCE ACTIVITY IN YOUR CEMENT PLANT KINDLY CLICK HERE Raw Material Preparation and Cement Manufacturing Process INFINITY FOR CEMENT EQUIPMENTJaw crushers are used for the crushing of very hard and abrasive raw materials for cement manufacturing Jaw crushers are a type of earlier crushing equipment, which is still widely used in smelting, building materials, electric power, water conservancy, transportation, and Cement Crusher Crushers for Cement Plant AGICO Cement
.jpg)
1Cement Manufacturing Process and System
The document describes the cement manufacturing process Raw materials like limestone, clay, and iron ore are quarried and crushed They are then blended and ground in a raw mill The raw mix is preheated and calcined in a kiln at high temperatures, resulting in clinker The clinker is then ground with gypsum to produce cement Key chemical reactions occur during burning to 2013年5月4日 SUSTAINABLE MANUFACTURING – PRINCIPLES, APPLICATIONS AND DIRECTIONS May 2013; Conference: • Cement manufacturing and precast concrete productsSUSTAINABLE MANUFACTURING – PRINCIPLES, APPLICATIONS AND DIRECTIONScement manufacturing process pdf wikipedia india, Cement Manufacturing Process Ppt pdf Download Free Cement Cement Cement Manufacturing Process pdf and ppt principles of Cement Manufacturing – Process crusher Go to Product Center wet cement process CGM mining application, Cement Process Cement Process Raw Materialsprinciples of cement manufacturing process2018年4月26日 This multidisciplinary title on cement production technology covers the entire process spectrum of cement production, starting from extraction and winning of natural raw materials to the finished products including the environmental impacts and research trends The book has an overtone of practice supported by the backup principlesCement Production Technology Principles and Practice Anjan
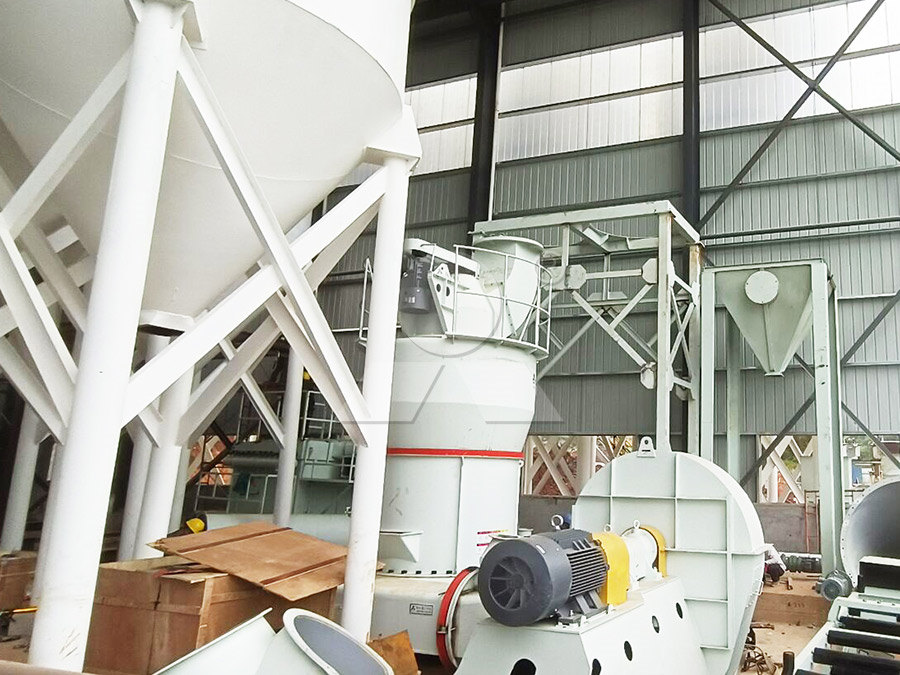
PORTLAND CEMENT TO GET PRINCIPLE SCHEME ResearchGate
2024年2月14日 This document presents a concise overview of the principles underlying the manufacturing process of Portland cement, a fundamental construction materialetasr Masmali: Implementation of Lean Manufacturing in a Cement Industry Implementation of Lean Manufacturing in a Cement Industry Majed Masmali Industrial Engineering Department College of Engineering Northern Border University Arar, Saudi Arabia Abstract The lean manufacturing concept is a systematicEngineering, Technology Applied Science Research cement at four cement plants in South Africa and a blending plant in Swaziland Its maintenance inventories for the plant equipment are kept at five warehouses situated at these cement plantsManaging the maintenance inventory of a cement manufacturerThe cyclone preheating system Phase IV: Calcination The calcination is the core phase of the cement making dry process The calcination of the preheated raw meal takes place in the rotary kiln of the cement plant The rotary kiln is a huge rotating furnace in which the raw meal is heated up to 1450 ⁰C and turned to clinkerHow Is Cement Produced in Cement Plants Cement Making
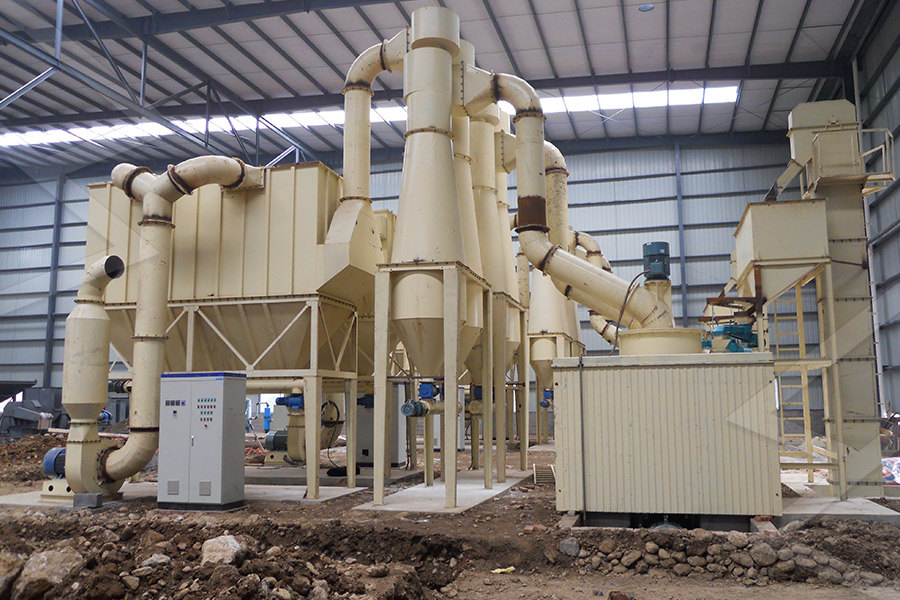
Manufacturing of Portland Cement – Process and Materials
1 天前 This all about the manufacturing of cement One of the interesting points about cement is that the strength properties of cement depend upon the cooling rate of the clinker, because the rate of cooling influences the degree of crystallization, the size of the crystal and the number of amorphous materials present in the clinker You’ll also Like:2013年3月20日 The successful launch of the German standard work on cement by Prof Locher in 2000 is now being followed by the publication of the widely requested English language version "Cement" which takes special countryspecific features and standards into account The book is aimed at chemists, physicists, engineers and technologists in the cement industry, in machine Cement: principles of production and use Google Books2019年1月3日 Clinker grinding technology is the most energyintensive process in cement manufacturing Traditionally, it was treated as "low on technology" and "high on energy" as grinding circuits use more than 60 per cent of total energy consumed and account for most of the manufacturing cost Since the increasing energy cost started burning the benefits significantly, Clinker grinding technology in cement manufacturingII METHODOLOGY The methodology has four main stages A Identification of Wastes In this stage, Waste Relationship Matrix (WRM) method is applied to identify wastes and then validated using WasteMinimizing Waste Using Lean Manufacturing: A Case in Cement
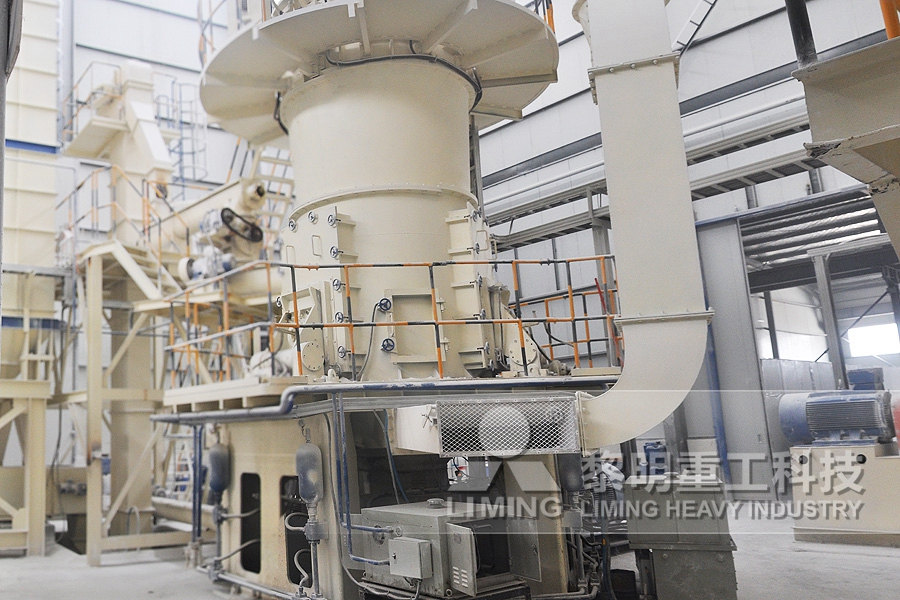
Strategic Quality Management Practices And Operational
cement manufacturing firms as opposed to all manufacturing firms in Kenya Therefore, it is required that future researchers should do a facsimile of this study to include all manufacturing firms in Kenya so as to do a comparison of findings after which a more exhaustive and reliable conclusion may be drawnProper understanding of these barriers is necessary to implement GM effectively (Mittal, 2013) The cement industry is one of the growing industries in Ethiopia following the Ethiopia’s commitment to have manufacturing industries to substitute imports with country products and the ambition of becoming the east African cement manufacturing (PDF) GREEN MANUFACTURING PRACTICES IN ETHIOPIAN CEMENT Stage of Cement Manufacture There are six main stages of the cement manufacturing process Stage 1: Raw Material Extraction/Quarry The raw cement ingredients needed for cement production are limestone (calcium), sand and clay (silicon, aluminum, iron), shale, fly ash, mill scale, and bauxite The ore rocks are quarried and crushed into smaller pieces of about 6 inchesHow Cement is Made Cement Manufacturing Process5 CEMENT –HISTORY In India, Portland cement was first manufactured in 1904 near Madras, by the South India Industrial LtdBut this venture failed Between 1912 and 1913, the Indian Cement Co Ltd, was established at Porbander (Gujarat) and by 1914 this Company was able to deliver about1000 tons of Portland cement By 1918 three factories were established1 Manufacturing Process of Cement Indus University
.jpg)
Hammer Crusher Working Principle AGICO Cement
2020年10月15日 We take a Φ900 x 900mm single rotor, irreversible multirow hinged hammer crusher as an example to introduce its structure and parts This type of hammer crusher is commonly seen in cement plants and is suitable for Request PDF On Dec 1, 2022, Kassu Jilcha published Minimizing Clinker Production Operational Cost Using Lean Manufacturing Principle: A Case of Clinker Production in Mugher Cement Factory By Minimizing Clinker Production Operational Cost Using Lean Manufacturing CementManufacturing1pptx Free download as Powerpoint Presentation (ppt / pptx), PDF File (pdf), Text File (txt) or view presentation slides online The document discusses the history and manufacturing process of cement It describes how ancient Egyptians and Romans used early forms of cement made from lime and pozzolana The modern dry process is then outlined, Cement Manufacturing 1 PDF Cement Concrete2014年10月4日 Cement manufacturing Download as a PDF or view online for free Submit Cement manufacturing Four Principle minerals in OPC are designated as under C3 A – 4 to 14% C3 AF – 10 to 18% C3 S – 45 to 65% C2 S – 15 to 35% 12Cement manufacturing PPT Free Download SlideShare
.jpg)
Demystifying Automation in Cement Manufacturing Birlasoft
2021年4月28日 Therefore, in the cement manufacturing context, automation would mean a largescale shift from laborintensive methods to skillintensive methods The accelerated incorporation of realtime monitoring systems, advanced control systems would constitute the first step in realizing a genuinely 21stcentury cement manufacturing processAlthough the basic cement manufacturing principle (dry process) of all cement plants is same, however the equipment installed vary according to the selection made by cement plant supplier We understand the different requirements and equipment being used in the cement plants and can offer same as per your requirementEquipment And Spares For All Stages Of Cement Manufacturinguse of waste in the cement manufacturing process, but rather outlines the most important principles and procedures which must be undertaken in the responsible use of coprocessing in cement manufacturing These guidelines should therefore be used in conjunction with other internationally recognized guidance documents, most notably:Guidelines for CoProcessing Fuels and Raw Materials in Cement Cement Manufacturing with Air Lift Pumps The principle behind its operation involves injecting air into the lower part of the pipe, reducing the density of the mixture inside, causing it to rise and move upwards This simple yet effective mechanism is particularly suited for handling cement and other bulk materialsCement Manufacturing with Air Lift Pumps