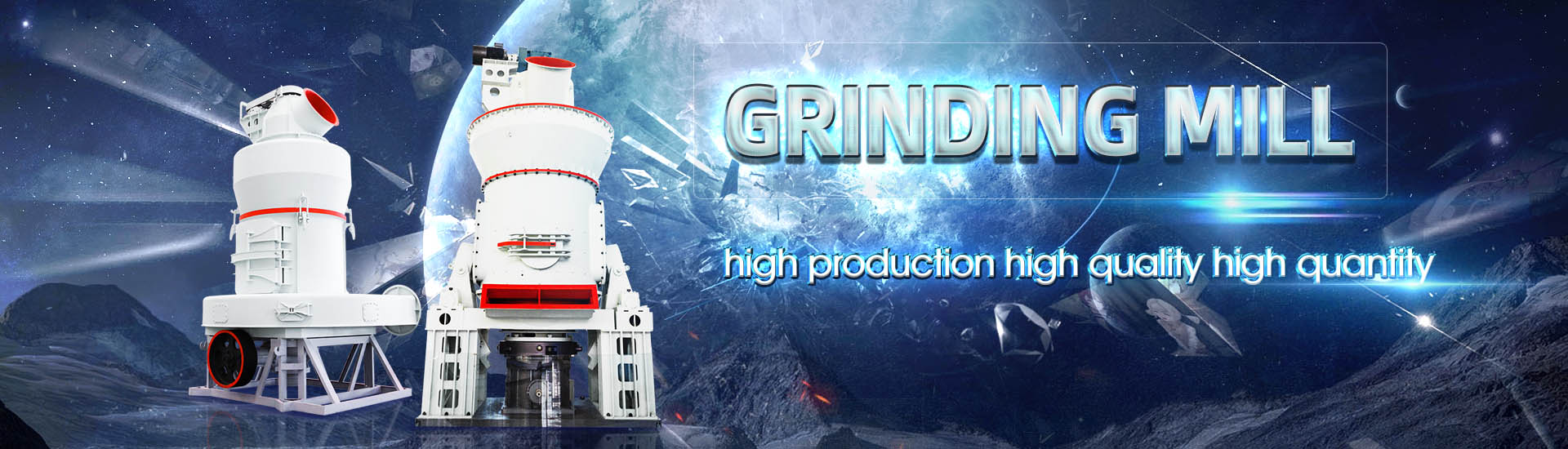
Coal mill rooting
.jpg)
Modeling and Control of Coal Mill
Coal mill is an important component of the thermal power plant It is used to grind and dry the moisturized raw coal and transport the pulverized coal – air mixture to the boiler Poor dynamic 2016年7月7日 In this paper, a modelbased residual evaluation approach, which is capable of online fault detection and diagnosis of major faults occurring in the milling system, is proposed Intelligent Decision Support System for Detection and Root Cause 2012年5月1日 The paper presents development and validation of a coal mill model to be used for improved mill control, which may lead to a better load following capability of power plants Derivation and validation of a coal mill model for controlMonitoring, optimization control, and diagnosis of coal mill faults can be mathematically modeled from mass flow analysis, heat exchange, and energy transfer balance All entering or leaving Decision Support System for Coal Mill Fault Diagnosis in Coal
.jpg)
Intelligent Decision Support System for Detection and Root Cause
2017年8月1日 Fuzzy logic is employed for residual evaluation to determine the type and magnitude of the fault, while Bayesian network is used for troubleshooting the root cause The 2016年7月7日 Coal mill is an essential component of a coal fired power plant that affects the performance, reliability and downtime of the plant The availability of the milling system is Intelligent Decision Support System for Detection and Root Cause By knowing charateristics of the coal mill operating parameters and the probability of the root cause of failure, the operating pattern can be determined in several steps by changing the Coal IJSER2015年8月1日 As the significant ancillary equipment of coalfired power plants, coal mills are the key to ensuring the steady operation of boilers In this study, a fault diagnosis model was Review of control and fault diagnosis methods applied to coal mills
36.jpg)
Research on early fault warning system of coal mills based on the
2019年9月9日 This paper presents a fault early warning approach of coal mills based on the Thermodynamic Law and data mining The Thermodynamic Law is used to describe the 2015年11月1日 Coal mills are bottleneck in coal–fired power generation process due to difficulty in developing efficient controls and faults occurring inside the mills In this paper, a dynamic A unified thermomechanical model for coal mill operation2021年8月1日 A root cause failure analysis of coal mill vertical shaft used in thermal power plant has been carried out The failed parts of the shaft showed the signature of fatigue failures(PDF) Fault analysis and optimization technology of HP2016年7月7日 In Agrawal et al (2016), a Bayesian Network (BN) is constructed for each type of fault, in order to diagnose root causes in a coal mill in a thermal power plant However, Intelligent Decision Support System for Detection and Root
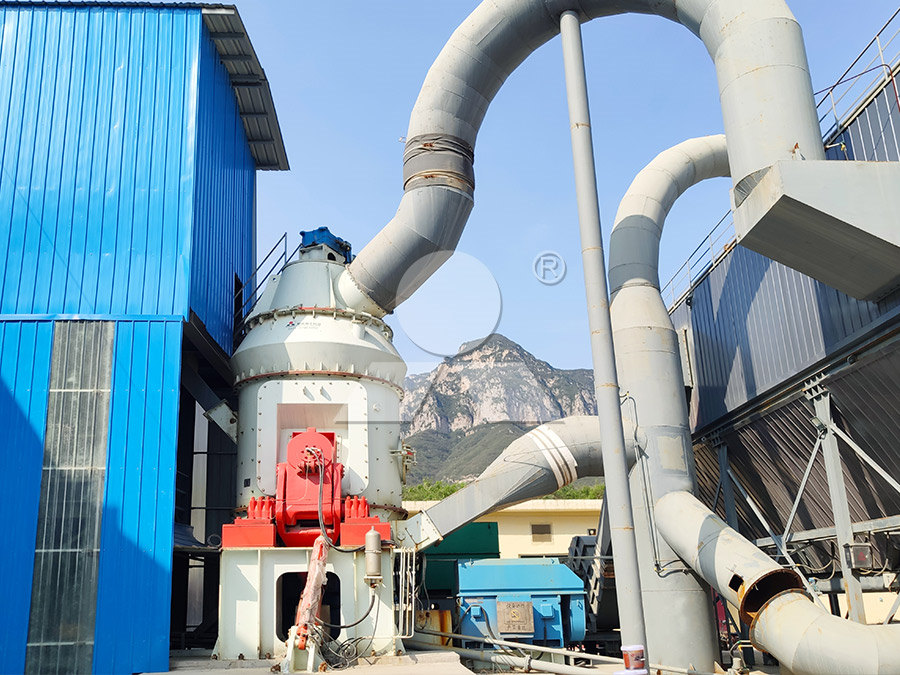
A unified thermomechanical model for coal mill operation
2015年11月1日 As presented by Andersen et al (2009) and Odgaard, Stoustrup, and Mataji (2007), coal moisture imposes limit on the maximum load at which a coal mill can be operated and the load gradient (how fast the mill may change its operating point), if it is desired that the pulverized coal entering the furnace has moisture content less than or equal to a certain value • Coal characteristics profoundly influence risk – Lower rank coals are generally more easily ignited inside the coal mill – High volatile matter and highly reactive coals encourage preignition inside the mill – Higher moisture content requires temperature extremes inside the millMill Inerting and Pulverizer/Mill Explosion Mitigation2010年6月22日 A root cause failure analysis of coal mill vertical shaft used in thermal power plant has been carried out The failed parts of the shaft showed the signature of fatigue failuresRoot cause failure analysis of coal mill vertical shaft ResearchGateOptimization Control for Coal Mill Fault Diagnosis in CoalFired Steam Power Plant Ronny Cahyadi Utomo1, 2, a), Joga Dharma Setiawan1, b)*, Toni Prahasto1, c) ROOT CAUSE FOR RECOMMENDATION OPERATION PATTERN COAL MILL Rank Root Cause (Based on FMEA Data PLTU Rembang) Probability /Belief (%) 1 Improper Input 80 11 Air Fuel Ratio LowCoal IJSER
.jpg)
ANALISA KEGAGALAN FUNGSI COAL FEEDER DAN COAL BUNKER
UBJOM PLTU tanjung Awarawar memiliki 6 Pulverizer, Pulverizer system secara lengkap terdiri dari coal bunker, Coal Feeder dan Coal Mill Dalam kondisi normal operasi 5 Pulverizer mampu menghasilkan beban 350 MWPermasalahan yang sering terjadi saat ini di UBJOM PLTU Tanjung Awarawar adalah sering terjadi plugging batubara2022年7月26日 Aiming at the typical faults in the coal mills operation process, the kernel extreme learning machine diagnosis model based on variational model feature extraction and kernel principal component analysis is offered Firstly, the collected signals of vibration and loading force, corresponding to typical faults of coal mill, are decomposed by variational model Fault Diagnosis of Coal Mill Based on Kernel Extreme LearningA coalpulverizing bowl mill (1) has a bull ring (12) fastened to the table, or bowl (4), as a single body with a surface alloy (17) of high chromium contentEPA2 Bull ring for a coal pulverizer Google PatentsThe coal mill is one of the important auxiliary engines in the coalfired power station Its operation status is directly related to the safe and steady operation of the unitsSchematic structure of the MPS mediumspeed mill
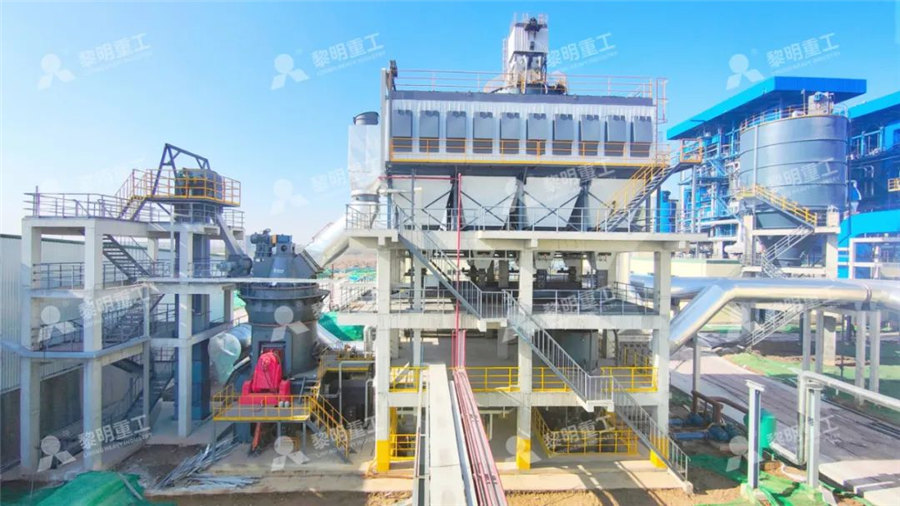
Root Cause Failure Analysis of Coal Mill Vertical Shaft DiVA portal
Coal pulverizing mills are employed to break down lumpy coal to fine coal for accelerating the combustion process by exposing large surface area to the action of oxygen The vertical shaft is used in the bowl mill, which is one type of pulverizing mill The diagram of vertical shaft is shown in Figure 2 Figure 2 Coal mill vertical shaftThis document provides standard operating procedures for coal mill and coal feeder operations at a 1x525 MW thermal power plant in Tuticorin, Tamil Nadu, India It outlines responsibilities for personnel, safety and environmental 15sop For Coal Mill and Feeder PDF Scribd2021年8月1日 Yukio et al [7] proposed a model consisting of blending, grinding and classifying processes for pulverizer control Agarawal et al [8] differentiated coal powder into ten size groups, divided the bowl mill into four zones, and developed a unified model Palizban et al [9] derived nonlinear differential mass equations of raw coal, recirculation coal and suspension coal in Coal mill model considering heat transfer effect on mass 2019年1月1日 The work in this part is based on a ZGM113N medium speed coal mill equipped in a subcritical 600MW unit Combined with existing research [1, 53] and relevant theoretical knowledge [54], 15 Abnormal Condition Monitoring and Diagnosis for Coal Mills
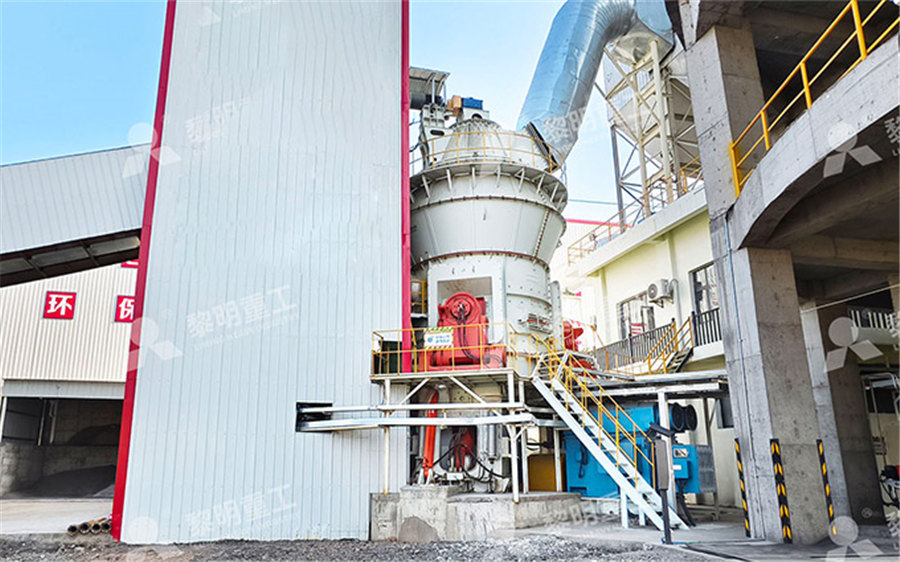
ANALISA PENYEBAB DAN PENCEGAHAN KEAUSAN GUIDE VANE COAL MILL
GUIDE VANE COAL MILL PABRIK TUBAN 4 (STUDI KASUS PT SEMEN GRESIK TUBAN, JAWA TIMUR) Nama Mahasiswa : Muhammad Irvan Anhar NRP : 2110 100 029 Jurusan : Teknik Mesin FTIITS Dosen Pembimbing : Ir Witantyo MEngSc ABSTRAK Coal mill merupakan salah satu equipment pada pabrik semen yang digunakan untuk menghaluskan 2020年8月12日 This study shows the performance of a currently running vertical roller coal mill (VRM) in an existing coalfired power plant In a power plant, the coal mill is the critical equipment, whose An investigation of performance characteristics and energetic The ATOX mill will grind and dry coal containing more than 20% moisture in one operation The possibility of customersupplied parts, along with the low civil costs that accompany compact mill installation, add to the excellent economy of the ATOX coal mill Working principles The raw coal enters the mill via a rotary sluice and feed chuteATOX COAL MILL FLSmidth Cement2020年1月1日 Coal mills have a significant influence on the reliability, efficiency, and safe operation of a coalfired power plant Coal blockage is one of the main reasons for coal mill malfunctionEarly Warning of Critical Blockage in Coal Mills Based on
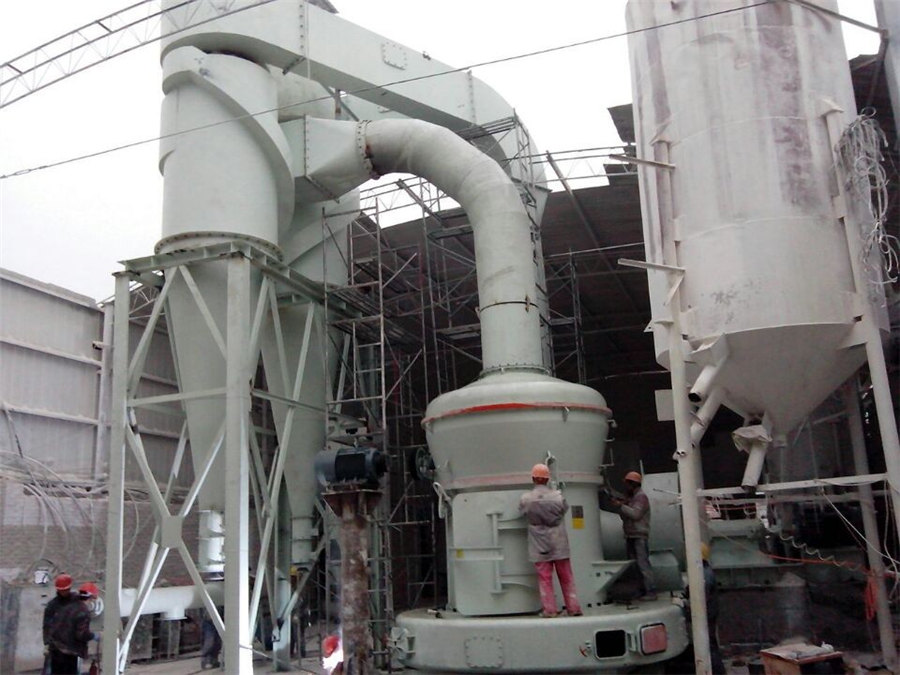
A brannew performance evaluation model of coal mill based on
2022年5月31日 Combining with the practical case of coal mill and carefully analyzing, Intelligent Decision Support System for Detection and Root Cause Analysis of Faults in Coal Mills IEEE Trans Fuzzy Systems, 25 (4) (2017), pp 934944 View in Scopus Google Scholar [9] SSTI Fagarasan2018年5月2日 Coal mill malfunctions are some of the most common causes of failing to keep the power plant crucial operating parameters or even unplanned power plant shutdowns Therefore, an algorithm has been developed that enable online detection of abnormal conditions and malfunctions of an operating mill Based on calculated diagnostic signals and defined Detection of Malfunctions and Abnormal Working Conditions of a Coal Mill2012年5月1日 Sensors for coal flow measurement from the mill to the furnace have become available on the market (Blankinship, 2004, Department of Trade and Industry, 2001, Laux et al, 1999)Unfortunately the equipment tends to be expensive and requires frequent calibration; thus it cannot be used directly for control purposes at this time of writingDerivation and validation of a coal mill model for controlA root cause failure analysis of coal mill vertical shaft used in thermal power plant has been carried out The failed parts of the shaft showed the signature of fatigue failuresRoot Cause Failure Analysis of Coal Mill Vertical Shaft
.jpg)
Review of control and fault diagnosis methods applied to coal
2015年8月1日 Intelligent Decision Support System for Detection and Root Cause Analysis of Faults in Coal Mills Vedika Agrawal B K Panigrahi PMV Subbarao Engineering Abstract The paper presents development and validation of coal mill model (including the action of classifier) to be used for improved coal mill control The model is Mill Training Manual Alstom Free download as PDF File (pdf), Text File (txt) or read online for freeMill Training Manual Alstom PDF Coal Mill (Grinding)2019年9月28日 Hence, reflecting the actual operation of the reallife coal mill pulverizers, the model simulator developed in the present work can be trusted for further use in rigorous control investigations ViewDetecting classifiercoal mill damage using a signal vibration analysisDOI: 101109/TFUZZ2016 Corpus ID: ; Intelligent Decision Support System for Detection and Root Cause Analysis of Faults in Coal Mills @article{Agrawal2017IntelligentDS, title={Intelligent Decision Support System for Detection and Root Cause Analysis of Faults in Coal Mills}, author={Vedika Agrawal and Bijaya Ketan Panigrahi and PMV Subbarao}, Intelligent Decision Support System for Detection and Root Cause
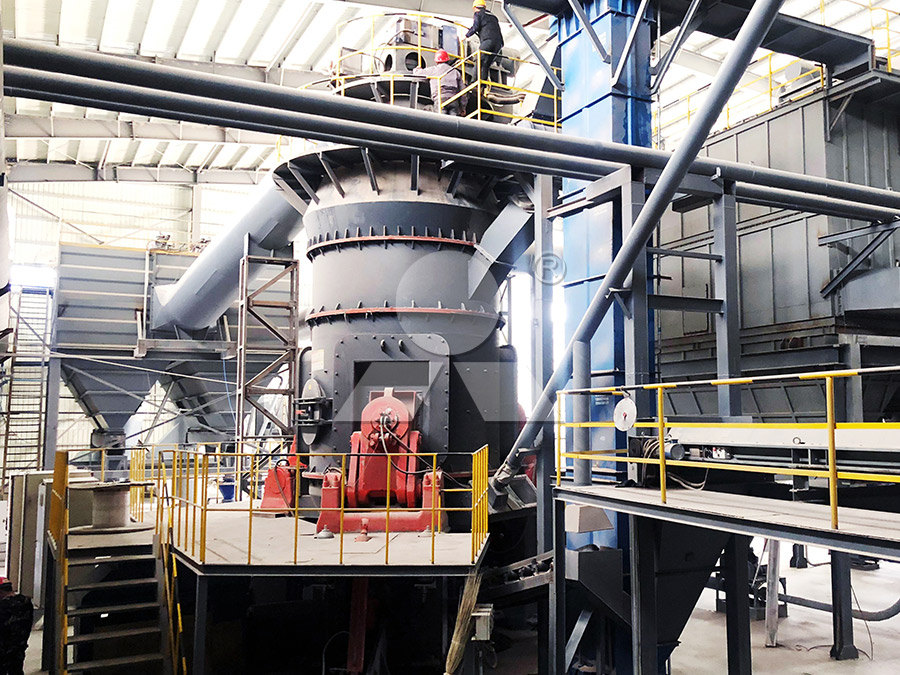
Research on fault diagnosis of coal mill system based on the
2020年9月1日 MPStype mediumspeed coal mill is designed and manufactured by Babcock, Germany, which is characterized by low energy consumption, long maintenance period and smooth output This paper takes the coal mill system of a 330 MW unit as the research object (Fig 1), which is equipped with an MPS180 HP II mediumspeed coal mill (Fig 2)A root cause failure analysis of coal mill vertical shaft used in thermal power plant has been carried out The failed parts of the shaft showed the signature of fatigue failures The fatigue crack Skip to search form Skip to main content Skip to account menu Semantic Root Cause Failure Analysis of Coal Mill Vertical ShaftSafe operation of coal grinding systems: Raw coal silo protection against fire and explosions Safe operation of coal grinding systems: Raw coal yard management The purchasing process for coal grinding systems needs changes Talk at a virtual seminar, November 2023 Accept the probability that the fire and explosion safety of your coal grinding system is nothing more than a mirageFire and explosion protection of coal grinding systems Where are 2015年8月1日 Substantial savings, owing to reduced maintenance costs and production losses, can be achieved through fewer mill choking incidents, fewer mill runbacks, optimal mill operation, and rapid diagnoses of mill faults [5]Over the years, considerable research has been carried out for improving the operation of coal mills using better controls and diagnosing faults in mills at Review of control and fault diagnosis methods applied to coal
.jpg)
(PDF) Fault analysis and optimization technology of HP
2021年8月1日 A root cause failure analysis of coal mill vertical shaft used in thermal power plant has been carried out The failed parts of the shaft showed the signature of fatigue failures2016年7月7日 In Agrawal et al (2016), a Bayesian Network (BN) is constructed for each type of fault, in order to diagnose root causes in a coal mill in a thermal power plant However, Intelligent Decision Support System for Detection and Root 2015年11月1日 As presented by Andersen et al (2009) and Odgaard, Stoustrup, and Mataji (2007), coal moisture imposes limit on the maximum load at which a coal mill can be operated and the load gradient (how fast the mill may change its operating point), if it is desired that the pulverized coal entering the furnace has moisture content less than or equal to a certain value A unified thermomechanical model for coal mill operation• Coal characteristics profoundly influence risk – Lower rank coals are generally more easily ignited inside the coal mill – High volatile matter and highly reactive coals encourage preignition inside the mill – Higher moisture content requires temperature extremes inside the millMill Inerting and Pulverizer/Mill Explosion Mitigation
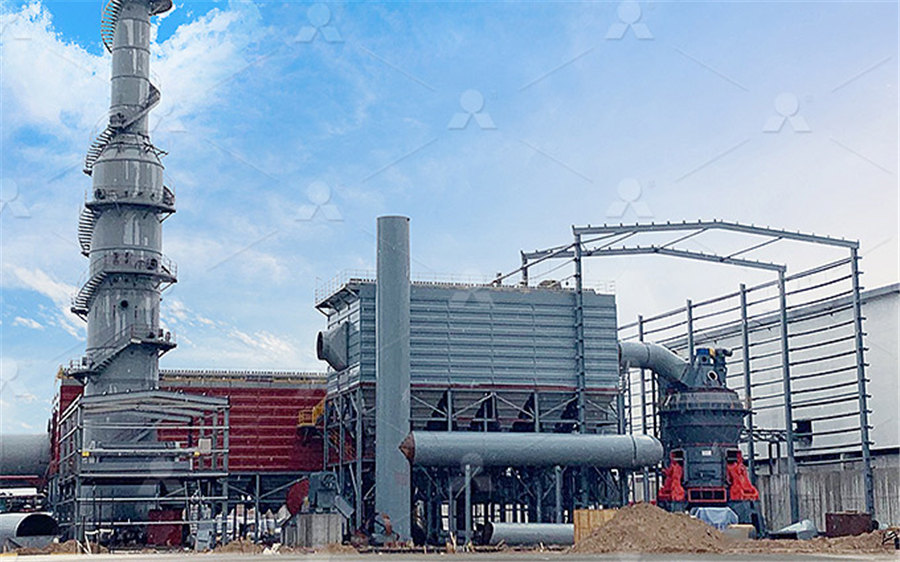
Root cause failure analysis of coal mill vertical shaft ResearchGate
2010年6月22日 A root cause failure analysis of coal mill vertical shaft used in thermal power plant has been carried out The failed parts of the shaft showed the signature of fatigue failuresOptimization Control for Coal Mill Fault Diagnosis in CoalFired Steam Power Plant Ronny Cahyadi Utomo1, 2, a), Joga Dharma Setiawan1, b)*, Toni Prahasto1, c) ROOT CAUSE FOR RECOMMENDATION OPERATION PATTERN COAL MILL Rank Root Cause (Based on FMEA Data PLTU Rembang) Probability /Belief (%) 1 Improper Input 80 11 Air Fuel Ratio LowCoal IJSERUBJOM PLTU tanjung Awarawar memiliki 6 Pulverizer, Pulverizer system secara lengkap terdiri dari coal bunker, Coal Feeder dan Coal Mill Dalam kondisi normal operasi 5 Pulverizer mampu menghasilkan beban 350 MWPermasalahan yang sering terjadi saat ini di UBJOM PLTU Tanjung Awarawar adalah sering terjadi plugging batubaraANALISA KEGAGALAN FUNGSI COAL FEEDER DAN COAL BUNKER 2022年7月26日 Aiming at the typical faults in the coal mills operation process, the kernel extreme learning machine diagnosis model based on variational model feature extraction and kernel principal component analysis is offered Firstly, the collected signals of vibration and loading force, corresponding to typical faults of coal mill, are decomposed by variational model Fault Diagnosis of Coal Mill Based on Kernel Extreme Learning
.jpg)
EPA2 Bull ring for a coal pulverizer Google Patents
A coalpulverizing bowl mill (1) has a bull ring (12) fastened to the table, or bowl (4), as a single body with a surface alloy (17) of high chromium contentThe coal mill is one of the important auxiliary engines in the coalfired power station Its operation status is directly related to the safe and steady operation of the unitsSchematic structure of the MPS mediumspeed mill