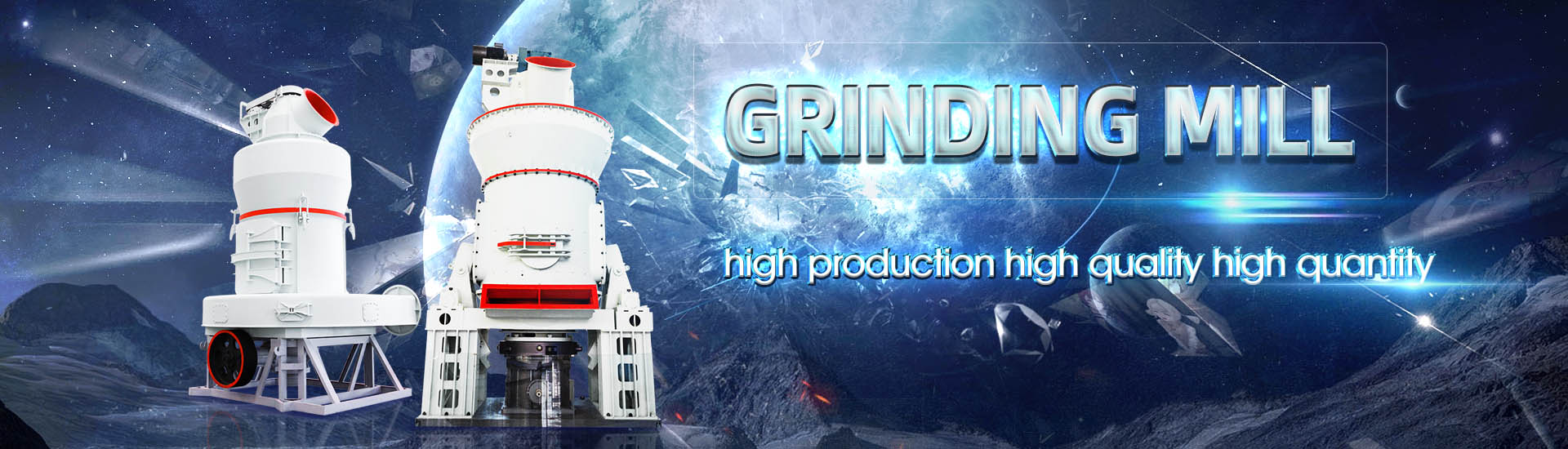
Vertical air flow mill
.jpg)
OptimizationofVerticalRawMillOperationpdf
2023年1月19日 The document provides information on optimizing the operation of vertical roller mills (VRMs) It discusses monitoring relevant process parameters like product rate, fineness, classifier speed, grinding force, power 2017年9月11日 In this study, an extensive sampling study was carried out at vertical roller mill of ESCH Cement Plant in Luxemburg Samples were collected from mill inside and around the circuit to(PDF) Performance Evaluation of Vertical Roller Mill in 2017年4月1日 Vertical roller mills (VRM) have found applications mostly in cement grinding operations where they were used in raw meal and finish grinding stages and in power plants Operational parameters affecting the vertical roller mill Vertical Roller Mills How to Calculate your Dust Load ? Dust Load = Mill Product (t/h) X 1000 X 1000 Air Flow at Mill Outlet (am3/h) in (g/am3) Typical Numbers = 400 Typical: 400 – 800 Optimization of VRM Operation RUCEMRU
.jpg)
Vertical roller mill for raw Application p rocess materials
The vertical roller mill has high energy efficiency and the installation space is smaller compared with tube mills These days, the vertical roller mills have been widely adopted The rollers are The mill provides the technical options to vary process parameters like airflow, mass flow, grinding force and classifier speed in a wide range and is equipped to analyze the internal Operational parameters affecting the vertical roller mill performanceVertical roller mill is a type of grinder used to grind materials into extremely fine powder for use in mineral dressing processes, paints, pyrotechnics, cements and ceramics It is an energy Vertical roller mill Wikipedia2014年5月1日 Air flow distribution at the mill throat, as well as inside the mill, significantly influences the mill performance in terms of separation, drying, coal/air flow uniformity at the mill outlet(PDF) Matrix Model Simulation of a Vertical Roller Mill
.jpg)
An energy based comparison of vertical roller mills and tumbling
2015年3月10日 The VRM200 is a laboratory scale vertical roller mill with two truncated conical grinding rollers (LOESCHE system) of 133 mm mean diameter, a cross flow rotary cage The document discusses ball mill ventilation air and its functions Ball mill ventilation air provides forward movement of material to increase retention time, takes out fine particles to reduce coating risk, and cools material in the mill It Ball Mill Ventilation Air PDF ScribdRequest PDF On Mar 1, 2016, Hong Li and others published Performance of the static air classifier in a Vertical Spindle Mill Find, read and cite all the research you need on ResearchGatePerformance of the static air classifier in a Vertical Spindle MillDynamic classifiers allow instant adjustment to provide wide flexibility of operation and size specifications The vertical blade classifier (VBC) is the Bradley standard classifier for efficient classification of fine ground powders The BLVT reduces the recirculating load in the mill system which results in higher throughput and less wearAirswept Roller Mills Bradley Pulverizer Company
.jpg)
LM Vertical Grinding Mill SMMVIK Machinery
LM Vertical Grinding Mill has two pairs of grinding rollers, each pair of roller composed of two narrow rollers, In the gas flow is small, the meal can not be increased to enhance air flow, they would fall through the nozzle discharged outside the mill, 2024年11月1日 The results showed that, with the increase in the width of blade, the air flow trajectory and the distribution of vorticity improved, which was conducive to the transport of particles Analysis of vertical roller mill performance with changes in material properties and operating conditions using DEM Miner Eng (2022)Numerical Study of Flow Field and Particle Motion Characteristics Vertical roller mill is a type of grinder used to grind materials into extremely fine powder for use in mineral dressing processes, paints, products Established through the mill in the pneumatic conveying of materials, a larger air flow rate, which can use waste heat of gas, at the same time dry grinding operations PrincipleVertical roller mill Wikipedia2016年8月1日 In order to investigate the classification performance of static air classifier in an industrial Vertical Spindle Mill (VSM), sampling ports were drilled on the mill shell and new online sampling methods were designed while significant deviation existed between velocity vectors of 500 μm coal particles and airflow [13]Performance of the static air classifier in a Vertical Spindle Mill
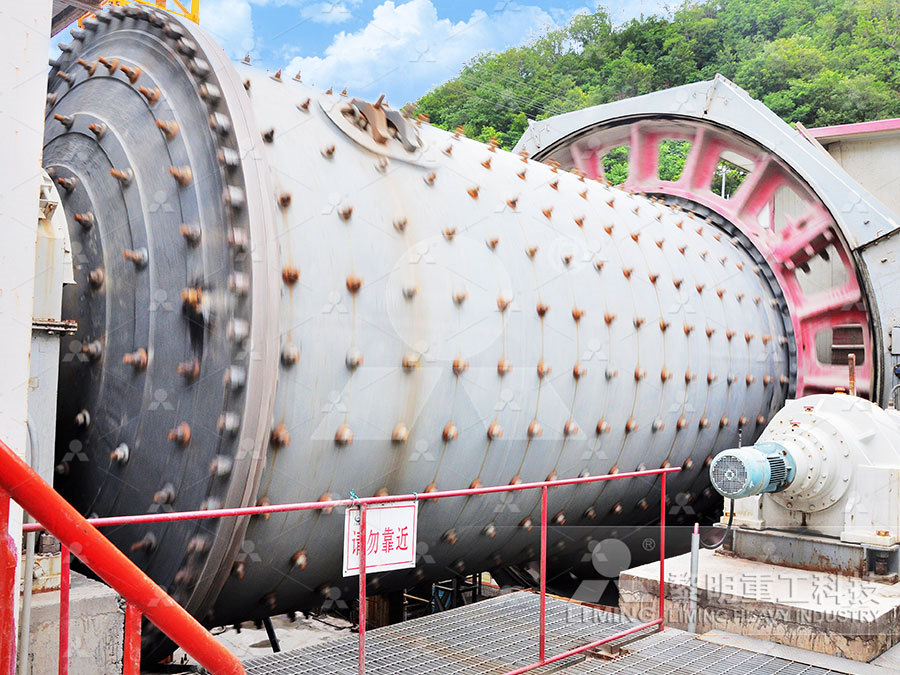
How to operate an air classifier mill to meet your fine grinding goals
vertical mill Combined drive In this classifier mill, as shown in Figure 2b, the classifier wheel and rotor disc are mounted on one shaft and rotate at the same speed As a result, the mill is smaller, has a lower purchase cost, and requires less installed horsepower than the vertical mill However, the apFigure 1 Vertical air classifier 2017年4月1日 Separator air flow (m 3 /h) 1500–5000: Loesche OGP mobile can be operated in two grinding modes characterized by location of the classification systems as airswept and overflow mode In the airswept mode, the verticalrollermill and a high efficiency dynamic classifier are suited above each other as a single unit (Fig 1)Operational parameters affecting the vertical roller mill Part 1: Structure of Vertical Roller Mill (VRM) Crusher shell: Covers the internal parts of the crusher and creates a crushing cavity The crusher shell is composed of a cylindrical part and a conical part The upper part of the crusher shell is fitted with a separator motor and an exhaust pipe that brings the crushed product to the sump (cyclone) to recover the crushed productOPERATION OF VERTICAL ROLLER MILL (VRM) NATIONAL 2016年8月1日 The consistency or a slight fluctuation of the air flow speed means the point is less affected by the turbulences and the whole sampling process is in a steady state Flow visualisation and velocity measurements in a vertical spindle coal mill static classifier Fuel, 82 (2003), pp 21152123Performance of the static air classifier in a Vertical Spindle Mill
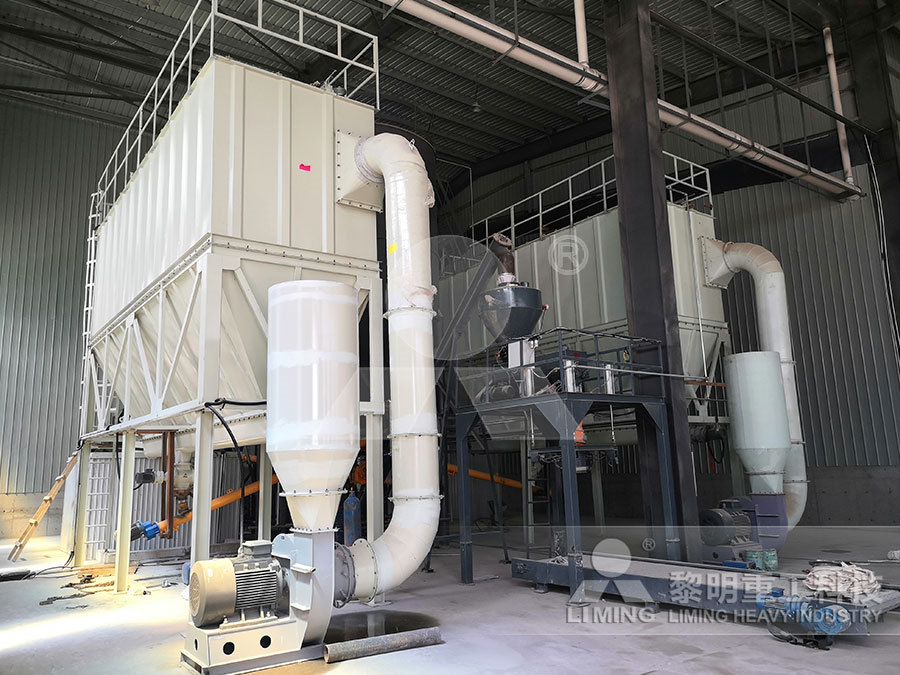
Coal mill, gypsum mill, clay mill, etc Pfeiffer MPS mills
The MPS mill also grinds, dries, calcines, and classifies gypsum without any problem, all in a single machine, for any fineness requested and considering individual requirements The MPS vertical roller mill built to last, reliable and VSM Vertical spindle mill APPENDIX K: MILL POWER VS AIR FLOW 89 APPENDIX L: GRINDING TABLE FEED VS FRICTION FACTOR 90 APPENDIX M: MILL FRICTIONAL FACTOR VS PRESSURE ON BALLS 91 xiv LIST OF TABLES Table 31: Mill arrangement schematic illustration of mill coal and air flow (Power Performance optimisation of vertical spindle coal pulverisers2024年11月1日 Numerical Study of Flow Field and Particle Motion Characteristics on Raw Coal Vertical Roller Mill Circuits Author links open overlay panel Hailiang Hu a, Yiming Li a, Yunlong Lu a, Yunlong Li a, Guiqiu Song a, Xuejun Wang b Show more Add to and the flow field is stabilized When the air flow moves to the bottom of the helical Numerical Study of Flow Field and Particle Motion Characteristics 2023年1月19日 OptimizationofVerticalRawMillOperationpdf Download as a PDF or view online for free X 1000 X 1000 Air Flow at Mill Outlet (am3/h) in (g/am3) Typical Numbers = 400 – 800 g/am3 Typical: 400 – 800 g/am3 17 Vertical Roller Mills What determines your Dust Load ? 18 Vertical Roller Mills Why a Lower Pressure Loss ?OptimizationofVerticalRawMillOperationpdf SlideShare
.jpg)
Increase productivity of vertical roller mill using seven QC tools
2021年1月29日 Vertical roller mills, VRMs, are widely used for grinding raw materials in factories engaged in the extraction and processing of minerals Any machine used for grinding or crushing consumes around This vertical mill machine is applied in electric power, metallurgy, chemical and nonmetallic industries, such as portland cement and blended cements, limestone, slag, manganese, gypsum, coal, barite, calcite etc HLM vertical grinding mill has proven to be a versatile grinding tool that exhibits many advantages over traditional ball milling, it is also faster to install than a traditional Best HLM Vertical Roller Mill Manufacturer and Factory2021年1月1日 Grinding Mill Vertical Roller Mill or Ball Mill: The reclaimed raw mix fed to Raw Mills, for drying and fine grinding of Raw meal for kiln feed: 4: Coal Grinding: Grinding Mill Vertical Roller Mill or Ball Mill: Coal is ground in Coal mill, which is a fuel for use in Kiln firing: 5: Pyro Section, Clikerization: In line calciner six stage Review on vertical roller mill in cement industry its 2003年10月1日 One method of controlling the particle size from a coal mill is the use of a vertical spindle mill static classifier, see Fig 1 The vertical spindle mill static classifier resembles the wellknown cyclone, except that it has a much shorter ‘barrel’ or cylindrical section, an inner pipe located on its central axis, a different path for the ‘rejected’ particles and an inlet flow which Flow visualisation and velocity measurements in a vertical
.jpg)
Operational parameters affecting the vertical roller mill
Request PDF On Sep 1, 2016, Deniz Altun and others published Operational parameters affecting the vertical roller mill performance Find, read and cite all the research you need on ResearchGateBy the rotating rotor, the raw material is classified into required particle size by the balance between the centrifugal force and the air flow force passing through the rotor STEP4 Fine particle which passing through the rotor is taken as UBE Vertical Mill UBE Machinery Corporation, Ltd2015年3月10日 The Institute of Mineral Processing at the Montanuniversitaet Leoben in cooperation with the company CEMTEC has developed a pilot scale, 200 mm table diameter, vertical roller mill for energy controlled laboratory testsThe mill provides the technical options to vary process parameters like airflow, mass flow, grinding force and classifier speed in a wide An energy based comparison of vertical roller mills and LUM series superfine vertical mil, integrating superfine grinding, selection and conveying together, is a professional and intelligent largescale superfine milling equipment The main motor drives the millstone to rotate through the LUM series superfine vertical roller grinding mill
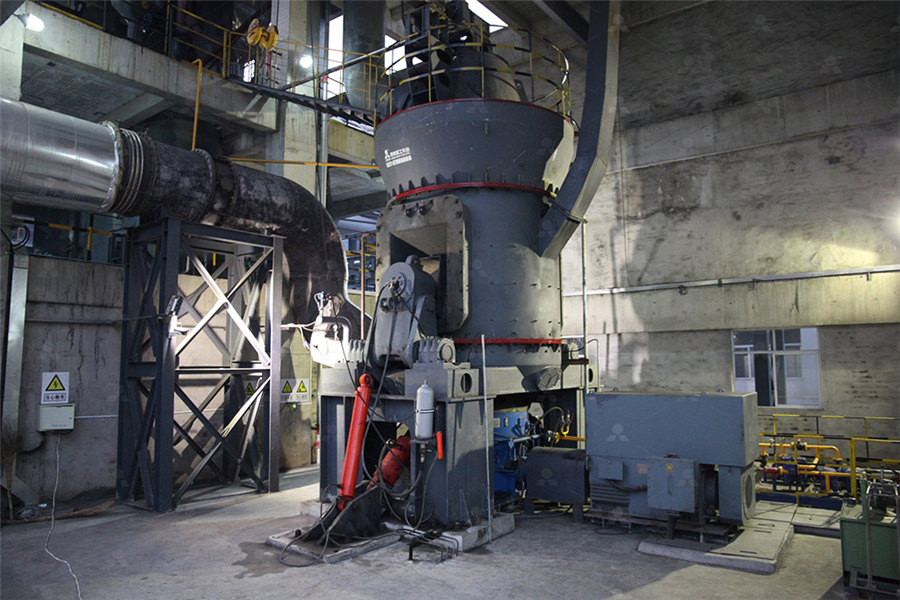
Vertical Raw Mill Optimization: Efficient Grinding Energy Use
This is particularly important for consistent control in the dynamic environment of a Vertical Raw Mill Temperature Resistance up to 1000 °C/1800 °F: The ability to withstand high temperatures in a Vertical Raw Mill allows for accurate measurement and control under extreme conditions, contributing to the efficiency of the milling processof an online Mill Energy Balance The Particle Size Analyser evaluation identified five key test parameters which caused inaccuracies in results Relationships were established enabling one to commission this Figure 11: Vertical Spindle Mill (A) and Tube Mill (B) Condition Monitoring and Performance Optimisation of Pulverised 2020年11月4日 Dou et al adopted the CFD (Computational Fluid Dynamics) technology to simulate the flow field of the vertical roller mill and studied the reasons for the large pressure difference in the mill To explore the influence of structural and operational parameters on the flow field, Ze et al [ 11 ] considered the effect of different gas fluxes on the gassolid coupling flow Effects of Blade Parameters on the Flow Field and Classification 2020年8月12日 To understand the performance of a vertical roller coal mill, the real operational tests have been performed considering three different coal sources Obtained results indicate that grinding pressure, primary air (PA) temperature and mill motor current have a tendency to rise by increasing coal feeding mass flow rates for all used coalAn investigation of performance characteristics and energetic
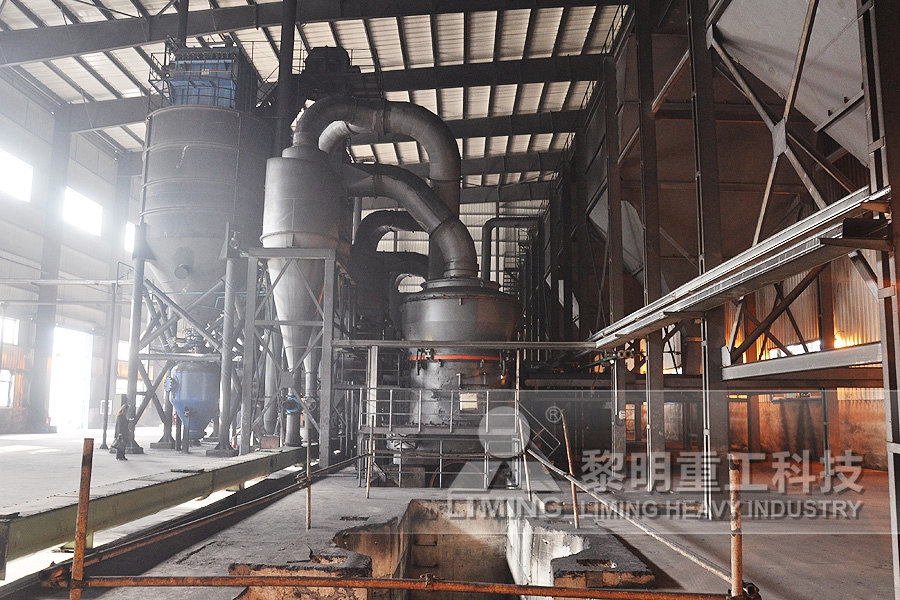
PROCESS CONTROL FOR CEMENT GRINDING IN VERTICAL ROLLER MILL
Mill motor speed Classifier speed Material temperature Mill air flow Mill fan speed Material moisture Mill differential pressure Water injection Mixture composition Product transport volume Grinding aid injection Composition of raw material Temperature after the mill Hot gas Grinding roller wear Mill vibrations Fresh air Figure2The mill provides the technical options to vary process parameters like airflow, mass flow, grinding force and classifier speed in a wide range M, Gorby, L, Terembula, J, 2005 Operational experience from the United States’ first vertical mill for cement grinding In: Cement Industry Technical Conference IEEE, pp 241–249 Operational parameters affecting the vertical roller mill Globally, cement plants are striving to improve their energy efficiency Therefore, it is critical for cement plant operations to increase the monitoring and control of a vertical raw mill energy process This technology has attracted the interest of the cement industry with its proven benefitAssessment of the thermodynamics efficiency of a cement vertical The document discusses ball mill ventilation air and its functions Ball mill ventilation air provides forward movement of material to increase retention time, takes out fine particles to reduce coating risk, and cools material in the mill It Ball Mill Ventilation Air PDF Scribd
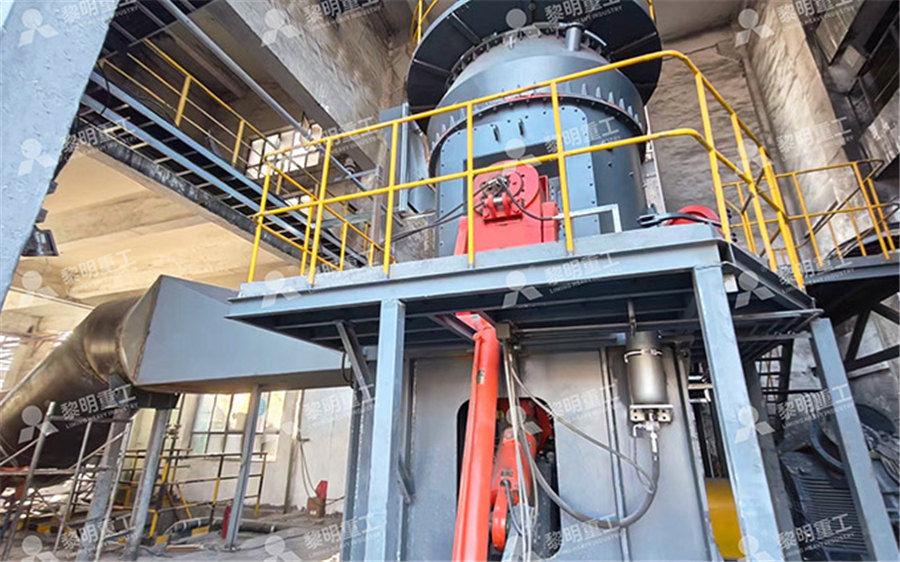
Performance of the static air classifier in a Vertical Spindle Mill
Request PDF On Mar 1, 2016, Hong Li and others published Performance of the static air classifier in a Vertical Spindle Mill Find, read and cite all the research you need on ResearchGateDynamic classifiers allow instant adjustment to provide wide flexibility of operation and size specifications The vertical blade classifier (VBC) is the Bradley standard classifier for efficient classification of fine ground powders The BLVT reduces the recirculating load in the mill system which results in higher throughput and less wearAirswept Roller Mills Bradley Pulverizer CompanyLM Vertical Grinding Mill has two pairs of grinding rollers, each pair of roller composed of two narrow rollers, In the gas flow is small, the meal can not be increased to enhance air flow, they would fall through the nozzle discharged outside the mill, LM Vertical Grinding Mill SMMVIK Machinery2024年11月1日 The results showed that, with the increase in the width of blade, the air flow trajectory and the distribution of vorticity improved, which was conducive to the transport of particles Analysis of vertical roller mill performance with changes in material properties and operating conditions using DEM Miner Eng (2022)Numerical Study of Flow Field and Particle Motion Characteristics
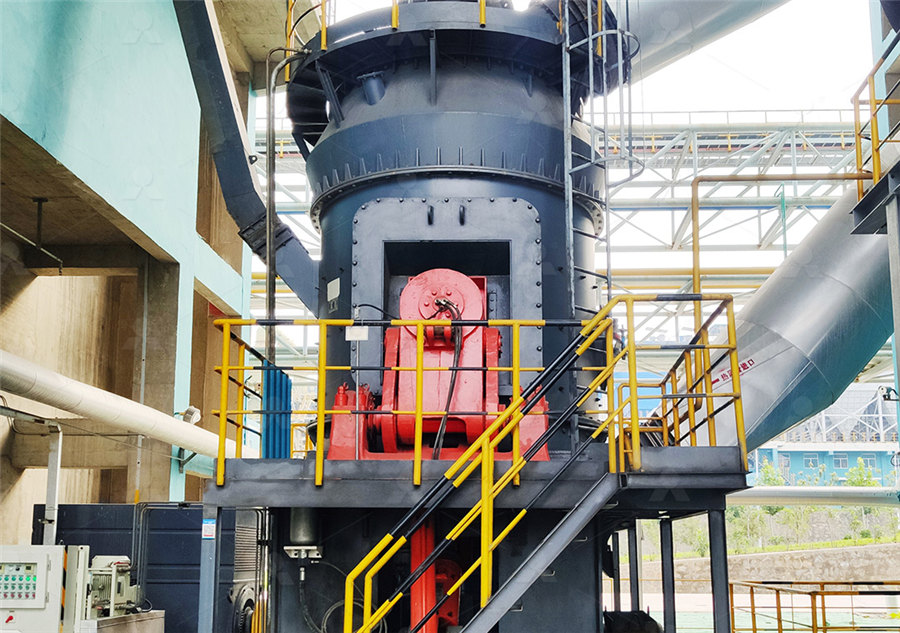
Vertical roller mill Wikipedia
Vertical roller mill is a type of grinder used to grind materials into extremely fine powder for use in mineral dressing processes, paints, products Established through the mill in the pneumatic conveying of materials, a larger air flow rate, which can use waste heat of gas, at the same time dry grinding operations Principle2016年8月1日 In order to investigate the classification performance of static air classifier in an industrial Vertical Spindle Mill (VSM), sampling ports were drilled on the mill shell and new online sampling methods were designed while significant deviation existed between velocity vectors of 500 μm coal particles and airflow [13]Performance of the static air classifier in a Vertical Spindle Millvertical mill Combined drive In this classifier mill, as shown in Figure 2b, the classifier wheel and rotor disc are mounted on one shaft and rotate at the same speed As a result, the mill is smaller, has a lower purchase cost, and requires less installed horsepower than the vertical mill However, the apFigure 1 Vertical air classifier How to operate an air classifier mill to meet your fine grinding goals2017年4月1日 Separator air flow (m 3 /h) 1500–5000: Loesche OGP mobile can be operated in two grinding modes characterized by location of the classification systems as airswept and overflow mode In the airswept mode, the verticalrollermill and a high efficiency dynamic classifier are suited above each other as a single unit (Fig 1)Operational parameters affecting the vertical roller mill
.jpg)
OPERATION OF VERTICAL ROLLER MILL (VRM) NATIONAL
Part 1: Structure of Vertical Roller Mill (VRM) Crusher shell: Covers the internal parts of the crusher and creates a crushing cavity The crusher shell is composed of a cylindrical part and a conical part The upper part of the crusher shell is fitted with a separator motor and an exhaust pipe that brings the crushed product to the sump (cyclone) to recover the crushed product