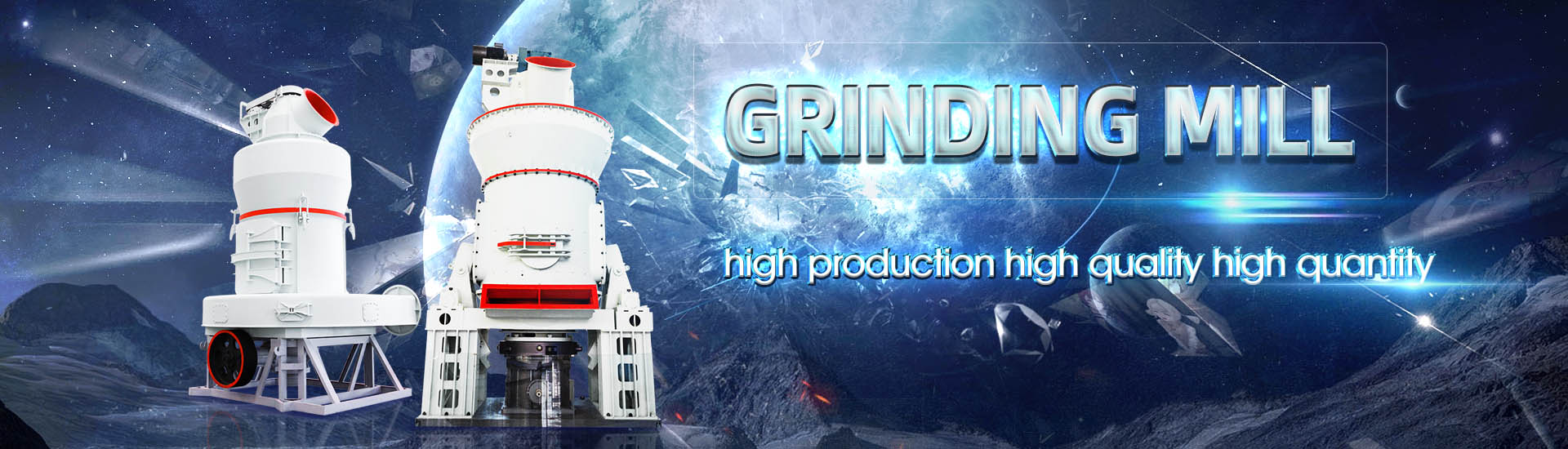
Tin powder processing tailings recovery rate
.jpg)
A valueadded multistage utilization process for the gradient
2019年10月1日 In this study, a multistage utilization process was put forward to get the utmost out of the valuable elements (tin and iron) from the tailings, and a gradientrecovery method with three2017年8月21日 The proven global tin reserves were reported to be approximately 47 million tons (Mts) in 2016, and among these resources, only approximately 22 Mts can be recovered economically(PDF) Extraction and Separation of Tin from Tin 2018年1月12日 The greatest recovery of Sn (>95%) was obtained when using CaCO3 as the flux, the purity of Sn was 96% A slag equivalent to 25% of the mass of the initial concentrate was produced during the(PDF) Recovery and Purification of Tin from Tailings 2017年8月21日 A selective reduction volatilization (SRV) process for tin recovery and pellet preparation for blast furnace ironmaking from a tinbearing magnetite concentrate (with 644 Extraction and Separation of Tin from TinBearing Secondary

A valueadded multistage utilization process for the gradient
In this study, a multistage utilization process was put forward to get the utmost out of the valuable elements (tin and iron) from the tailings, and a gradientrecovery method with three 2016年6月17日 In this study, a process of magnetizing roasting followed by magnetic separation, which is used to separate or recover tin and iron from the high calcium type tin Selective separation and recovery of iron and tin from high 2020年1月1日 The study was performed by analyzing the composition of Bangka tin tailing using XRF Based on these information, flow diagram of processing and refining technology of Processing and Refining of Tin Tailing Mining IOPsciencePercent recovery of the processing and refining of minerals to separate impurities generally reached a maximum of 80%, thus 20% will become tailing Tailing is byproduct of the mining orProcessing and Refining of Tin Tailing Mining ResearchGate
.jpg)
An environmentallyfriendly process for recovering, solidifying As
2021年11月10日 We developed an affordable and environmentalfriendly process for the recovery of Sn and reduction of Asbearing hazardous waste from tinbearing middling using 2017年8月21日 It is impossible to sepa rate and recover la ttice Sn 4+ by Powder Technol 301, 102 (2016) 61 After processing tin (Sn) [9, 10] the tailings slag occurs, (PDF) Extraction and Separation of Tin from Tin 2015年4月30日 Conventional tailings have a fine powder deposition that can create dust pollution Studies indicate thickened paste tailings can reduce tailings dam construction up to 40 percent, both in material quantities and capital Paste thickening optimizes tailings disposal and water ported rutile recovery from Bangka tin tailings using an HCl leaching process Ismael et al [7] achieved a 79% rutile recovery by applying a combination of alkaline roasting and acid leaching from solid waste tailings, and Kurniawan et al [8] reported a rutile recovery of 926% from tin oreOptimization of Titanium Recovery from Tin Tailings Using
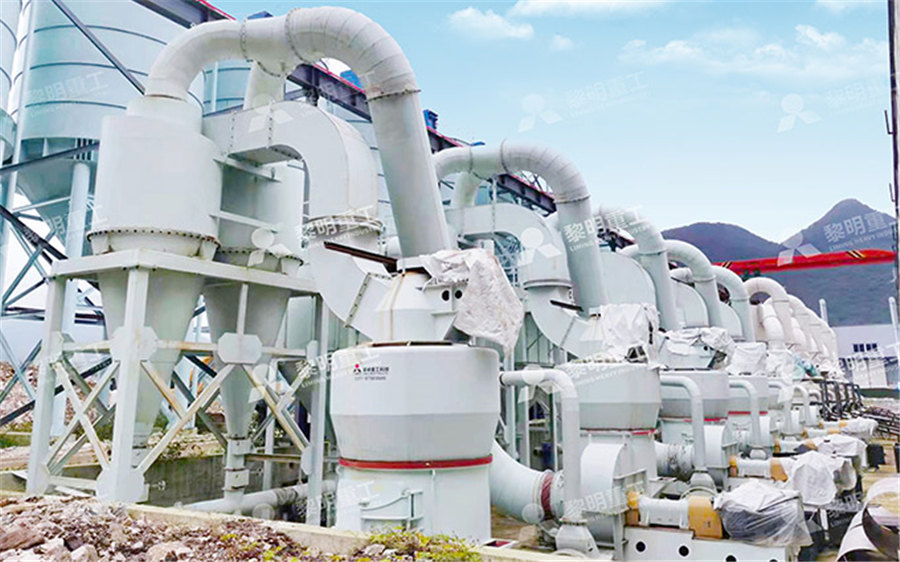
Ore Reserves Statement Taronga Tin Project, New South Wales
953 Taronga Tin FS 2024 Mining Finaldocx • This Ore Reserves Statement, 1921AMDTarongaReservesStatementFinal Ron Goodman (TMPL’s Consultant Metallurgical Adviser) Process performance predictions including tin recovery and ore processing rate Processing facility design and associated capital cost estimatestechnologies for the beneficiation of ore processing tailings, metallurgical slags, flue dusts, etc and then Cu in leachate is recovered with iron powder (Cankut, 1973) In some plants, flash smelting furnace slag (162% Cu) and converter slag (57% Cu) tin from the slags produced during the refining of blister copper Development of a Flowsheet for Recovering Copper and Tin from It has been shown that the use of selective concentration of the +20 μm class using a thermomorphic polymer (TMPF) for flotation of tin ores allows not only to reduce the loss of tin with thin classes, but also significantly increase the flotation rate of cassiterite and technological parameters when beneficiating mature tailings of tinsulfide ore processingFlotation extraction of tin from tailings of sulfidetin ore dressing 2020年8月1日 The aim of this study was to investigate the technoeconomic feasibility of producing critical raw materials from mine tailings Data from 477 Chilean tailings facilities were analyzed and used in the technoeconomic assessment of the valorization of mine tailings in the form of CRMs recoveryTowards mine tailings valorization: Recovery of critical materials
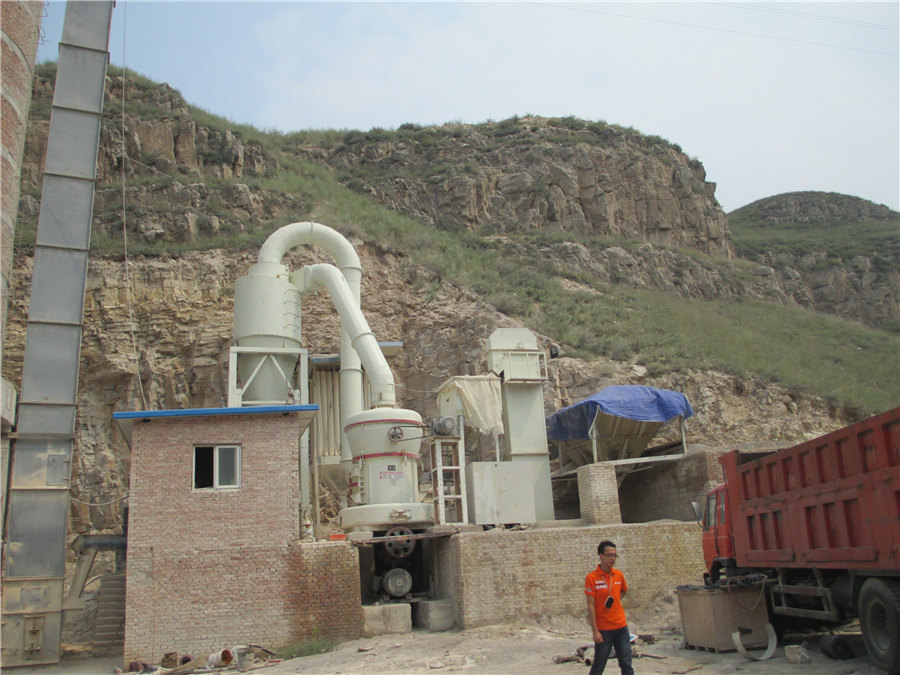
A valueadded multistage utilization process for the gradientrecovery
2019年10月1日 Recovery of iron Two tailings were mixed as mass ratio of 1:1, and the mixed samples were balled into 8–10 mm green pellets in a disk pelletizer2019年11月1日 Tin is an important component and widely applied in electrical and electronic equipment (EEE) [1], [2]Since the third revolution of science and technology, global tin consumption demand increases annually, however, the tin reserves reduce rapidly and will be exhaust in 20 years [1]Hence, more attention have been paid on the recovery of tin from New understanding on the separation of tin from magnetitetype, tin 5 天之前 Usually, there is often one or more equipment being used for processing and beneficiation tin ores, thus the finally tin concentrate can get an ideal grade and high recovery rate Below are the three beneficiaiton flow used in tin ore beneficiation Tin ore gravity Separation: In fact, most of the tin concentrates come from cassiterite depositsTin Ore Beneficiation Methods And Some PracticeThe general recovery rate of gold processing and melting is 804% The general recovery rate of silver processing and melting is 382% The value of tailings is brought into full play, and also brings efficiency to the processing plant 2 A gold tailings processing equipment, gold tailings
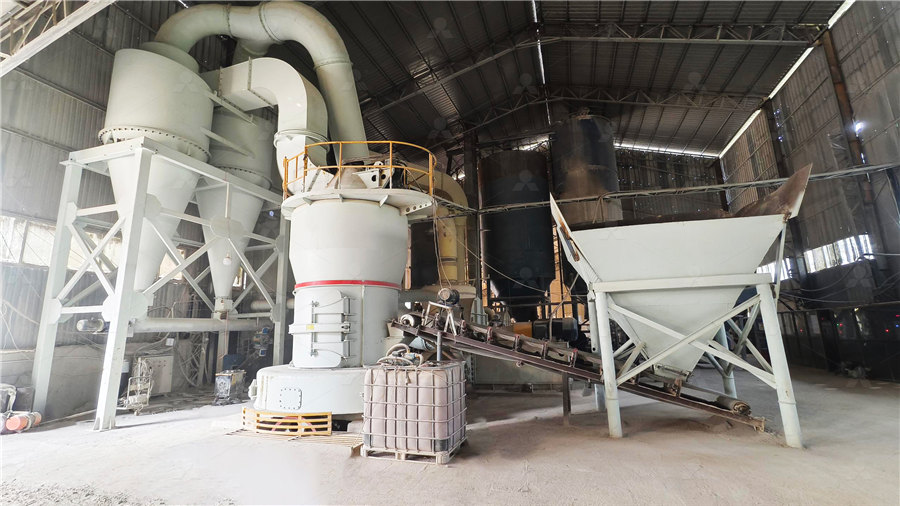
A valueadded multistage utilization process for the gradientrecovery
Materials Two typical tinbearing tailings (tailing A and tailing B) used in this study were taken from Yunnan province, China The major chemical compositions of them were determined by XRF, the total Fe and Sn content were detected by ICPAES, and the results are shown in Table 1The tin content of the tailings was respectively 0792 wt% and 0358 wt%, while the iron Other metallurgical tailings involve slags/sludges and flue dusts produced from smelting or byproducts of electrometallurgical processes [121] In the following sections, analyses of the presence of Se, Te, As, Sb, and Bi in mineral processing tailings and extractive metallurgical residues are outlinedProgress, challenges, and perspectives of critical elements recovery GeoScience Engineering geoscience Vol 68 (2022), No 2 pp 195–207, ISSN 18025420 DOI 1035180/gse20220081 206 5 CONCLUSION This research focused on the possibility of tailings processing at the Habatu Mining Company limited and the influence of the ore body's characteristics on existing tailings processing procedures, such as ground The Efficiency of Mechanized Mineral Processing Techniques to Recover 2020年2月1日 In addition, the separation of iron minerals and cassiterite from tin tailings by MRMS was studied and a highquality iron concentrate with a grade of 6468% and recovery of 8747% from the tin tailing assaying 1456% Fe was obtained [21]Recovery of iron from hazardous tailings using fluidized roasting
.jpg)
A Novel Technology for the Recovery and Separation of
2024年10月21日 Finally, a tinrich middling with a tin grade of 293% and a recovery ratio of 7088%, as well as an iron concentrate with an iron grade of 6195% and a recovery ratio of 6808% were obtained2024年10月21日 Therefore, it is difficult to recover and separate cassiterite and ironcontaining minerals using traditional mineral processing methods The study proposed a novel technology involving preconcentration, reduction roasting, and magnetic separation for the treatment of tincontaining tailings with a tin grade of 014% and an iron grade of 1279%A Novel Technology for the Recovery and Separation of MDPIThe results suggest that microwave heating accelerates the heating rate and shortens the melting time Tin recovery rate was 9779%, with a slag ratio of only 165% and other losses accounting for less than 056% The unit energy consumption was only 017 (kWh)kgApplication of Microwave Melting for the Recovery of Tin Powder 2022年12月1日 The proposed mechanized techniques were found to increase the efficiency of tin and tantalum recovery from 6075% to 8185% and from 229% to 4857%, respectively, and the grades of the tin and The Efficiency of Mechanized Mineral Processing Techniques to Recover
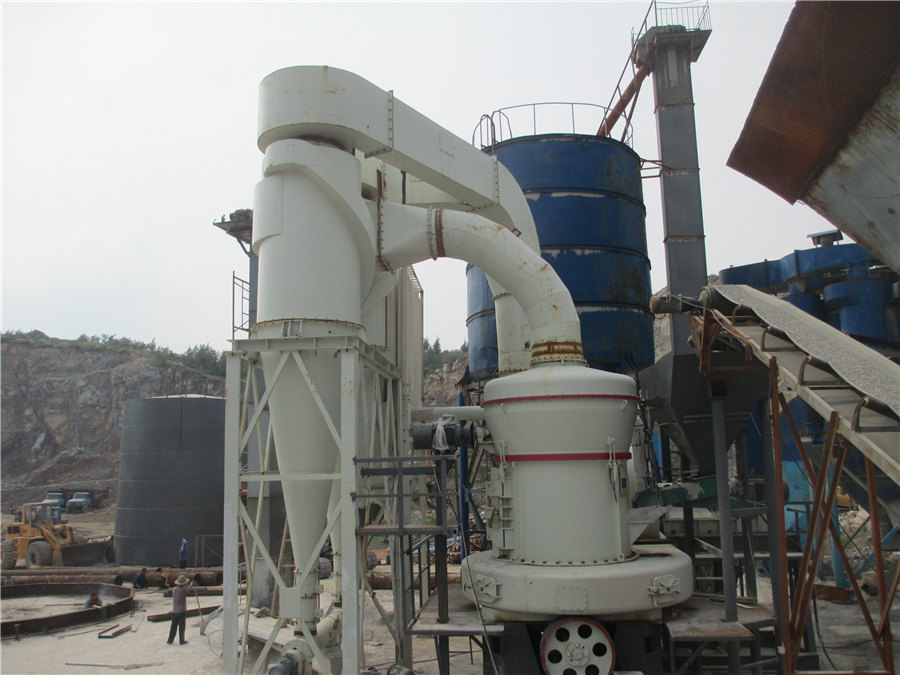
RENISON TAILINGS RETREATMENT PROJECT (“RENTAILS”) UPDATED DFS
5,400 tonnes of tin (Sn) and 2,200 tonnes of copper (Cu) per year, through the reprocessing and recovery of tin and copper from the existing historical tailings at Renison Renison produces approximately 7,000 tonnes of Sn in tin concentrate per year The planned tailings treatment rate is nominally 2 million tonnes per year over 11 years2022年3月1日 The proposed mechanized techniques were found to increase the efficiency of tin and tantalum recovery from 6075% to 8185% and from 229% to 4857%, respectively, and the grades of the tin and (PDF) Evaluation of Efficiency of Using Mechanized Processing 2022年11月1日 1 Introduction Tin (Sn) is widely used in a variety of industries due to its unique physical and chemical properties, and therefore its demand has surged worldwide [1, 2]The worldwide Sn reserves amount to approximately 7 million tons, which only guarantees an approximately 23year supply assuming a production rate of 300,000 tons of tin per yearCoroasting of tin tailings and waste cathode carbon for the recovery Tin ore processing plant beneficiation machine separate Se mining , Condition: New Origin: Henan, China Capacity: 02500 Ton/h Method: Gravity plant , gravityflotation plant Used for: widely used in all kinds of tin ore, gold Tin ore processing plant beneficiation machine
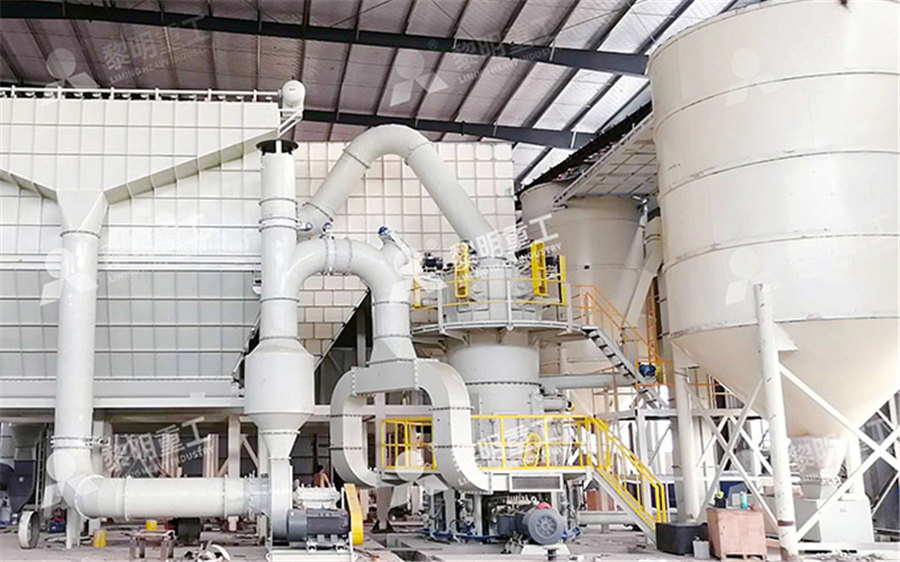
(PDF) Recovery of Fine Cassiterite from Tailing Dump in Jarin Tin
Minerals, 2022 Rwanda is known to be among the top producers of tin and tantalum, despite having low recovery and grades This study was carried out to evaluate the efficiency of using mechanized methods to increase the recovery rate and grades of tin and tantalum mined in Gatsibo, Eastern Province, Rwanda, since the general separation techniques used are artisanal2023年12月18日 01 Magnetic iron mineral recovery technology from iron tailings In view of the different iron contents in the gangue minerals in the tailings, the differences in magnetic materials, the large differences in specific gravity, and the difficulty in recovering iron minerals, a combined magnetic and gravity management process that combines strong magnetic separation and Tailings Reprocessing Technologies for Metal Minerals(2)2020年2月1日 Both the iron grade and recovery rate increased when the roasting time increased from 10 to 25 min; subsequently, the values of these parameters leveled off after the roasting time exceeded 25 min The maximum recovery rate of the magnetic concentrate achieved a peak that was approximately 9011% with an iron grade of 6084%Recovery of iron from hazardous tailings using fluidized roasting 2022年1月11日 Xi’an Dasen Mining Machinery Equipment Co, LTD Tel: +86 29 8113 7393 Whatsapp:+86 133 1927 7356 Address: Yongwei Times Center, Hightech Industry Zone, Xi’an, Shaanxi, China PC: What are the commonly used tin processing methods?
.jpg)
mine tailings reprocessing, gold tailings processing equipment,
Xinhai tailings reprocessing line, Tin(Cassiterite) Ore Mining Process Titanium Mining Process Finally, gold recovery rate is 804% while silver is 382% The process fully exploit the value of tailings and enhances the efficiency of plant [Related Products] Click depressants The final concentrate contained 1328% Sn, with a recovery rate of 6156%, and 1851% Cu, with a recovery rate of 8652% This method proved effective for the exploitation and use of this type of copper–tin resource in Tajikistan Keywords: mushistonite; copper–tin tailings; flotation; benzohydroxamic acid 1 IntroductionTailings of Copper–Tin Minerals in TajikistanGeoScience Engineering Vol 68 (2022), No 2 geoscience pp 195–207, ISSN 18025420 DOI 1035180/gse20220081 THE EFFICIENCY OF MECHANIZED MINERAL PROCESSINGTHE EFFICIENCY OF MECHANIZED MINERAL PROCESSING TECHNIQUES TO RECOVER 2017年8月21日 It is impossible to sepa rate and recover la ttice Sn 4+ by Powder Technol 301, 102 (2016) 61 After processing tin (Sn) [9, 10] the tailings slag occurs, (PDF) Extraction and Separation of Tin from Tin
.jpg)
Paste thickening optimizes tailings disposal and water
2015年4月30日 Conventional tailings have a fine powder deposition that can create dust pollution Studies indicate thickened paste tailings can reduce tailings dam construction up to 40 percent, both in material quantities and capital ported rutile recovery from Bangka tin tailings using an HCl leaching process Ismael et al [7] achieved a 79% rutile recovery by applying a combination of alkaline roasting and acid leaching from solid waste tailings, and Kurniawan et al [8] reported a rutile recovery of 926% from tin oreOptimization of Titanium Recovery from Tin Tailings Using 953 Taronga Tin FS 2024 Mining Finaldocx • This Ore Reserves Statement, 1921AMDTarongaReservesStatementFinal Ron Goodman (TMPL’s Consultant Metallurgical Adviser) Process performance predictions including tin recovery and ore processing rate Processing facility design and associated capital cost estimatesOre Reserves Statement Taronga Tin Project, New South Walestechnologies for the beneficiation of ore processing tailings, metallurgical slags, flue dusts, etc and then Cu in leachate is recovered with iron powder (Cankut, 1973) In some plants, flash smelting furnace slag (162% Cu) and converter slag (57% Cu) tin from the slags produced during the refining of blister copper Development of a Flowsheet for Recovering Copper and Tin from
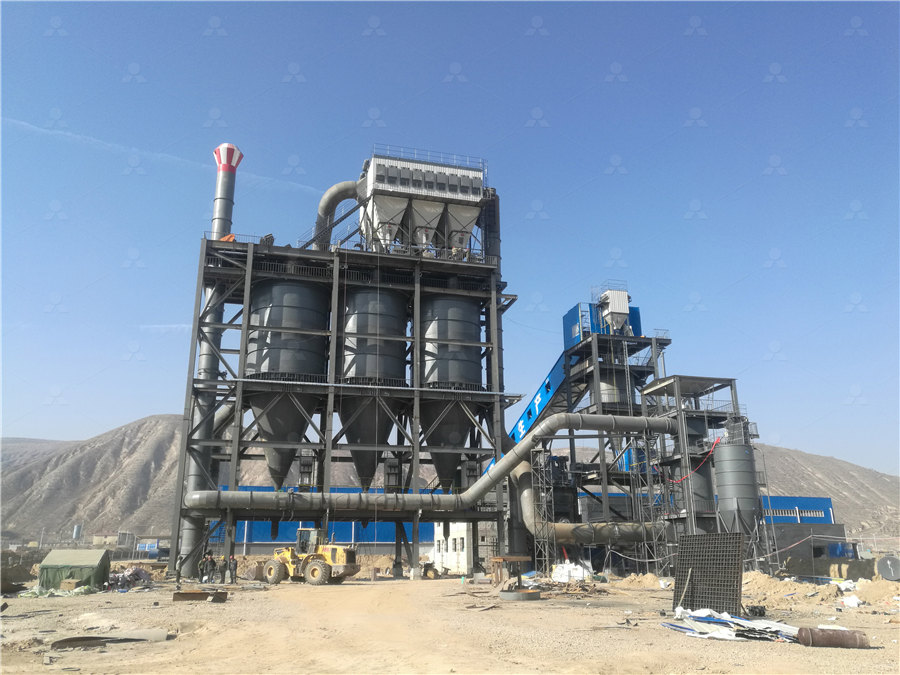
Flotation extraction of tin from tailings of sulfidetin ore dressing
It has been shown that the use of selective concentration of the +20 μm class using a thermomorphic polymer (TMPF) for flotation of tin ores allows not only to reduce the loss of tin with thin classes, but also significantly increase the flotation rate of cassiterite and technological parameters when beneficiating mature tailings of tinsulfide ore processing2020年8月1日 The aim of this study was to investigate the technoeconomic feasibility of producing critical raw materials from mine tailings Data from 477 Chilean tailings facilities were analyzed and used in the technoeconomic assessment of the valorization of mine tailings in the form of CRMs recoveryTowards mine tailings valorization: Recovery of critical materials 2019年10月1日 Recovery of iron Two tailings were mixed as mass ratio of 1:1, and the mixed samples were balled into 8–10 mm green pellets in a disk pelletizerA valueadded multistage utilization process for the gradientrecovery 2019年11月1日 Tin is an important component and widely applied in electrical and electronic equipment (EEE) [1], [2]Since the third revolution of science and technology, global tin consumption demand increases annually, however, the tin reserves reduce rapidly and will be exhaust in 20 years [1]Hence, more attention have been paid on the recovery of tin from New understanding on the separation of tin from magnetitetype, tin
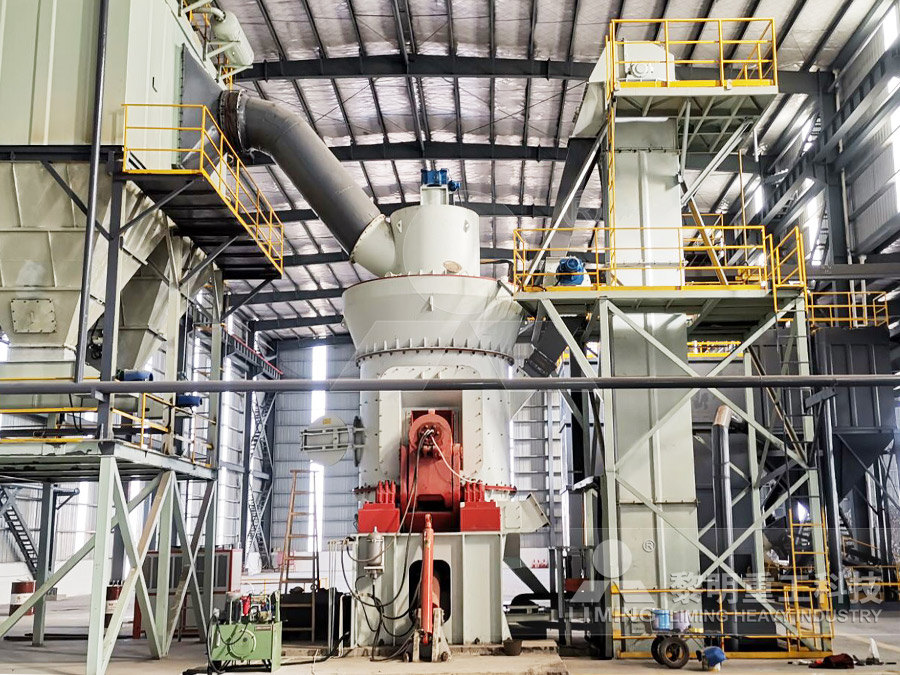
Tin Ore Beneficiation Methods And Some Practice
5 天之前 Usually, there is often one or more equipment being used for processing and beneficiation tin ores, thus the finally tin concentrate can get an ideal grade and high recovery rate Below are the three beneficiaiton flow used in tin ore beneficiation Tin ore gravity Separation: In fact, most of the tin concentrates come from cassiterite deposits