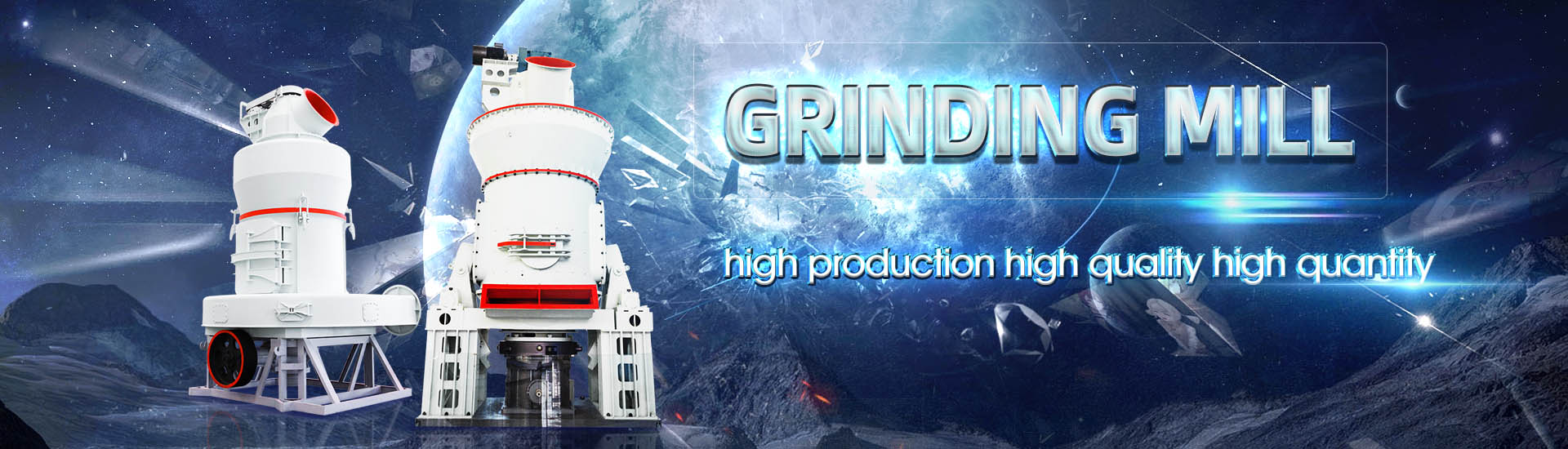
Slag vertical mill waste gas recovery
.jpg)
CNA Slag vertical mill tail gas waste heat cascade
The invention relates to the technical field of tail gas waste heat utilization, and provides a 2013年12月1日 Molten slag exhausted with critically high temperature of about 1450–1550 °C A review of waste heat recovery technologies towards molten slag 2024年9月15日 The new process for molten steel slag gas quenching and carbon An efficient molten steel slag gas quenching process: Integrating 2015年3月12日 Waste heat recovery from high temperature slags represents the latest (PDF) Heat Recovery from High Temperature Slags: A
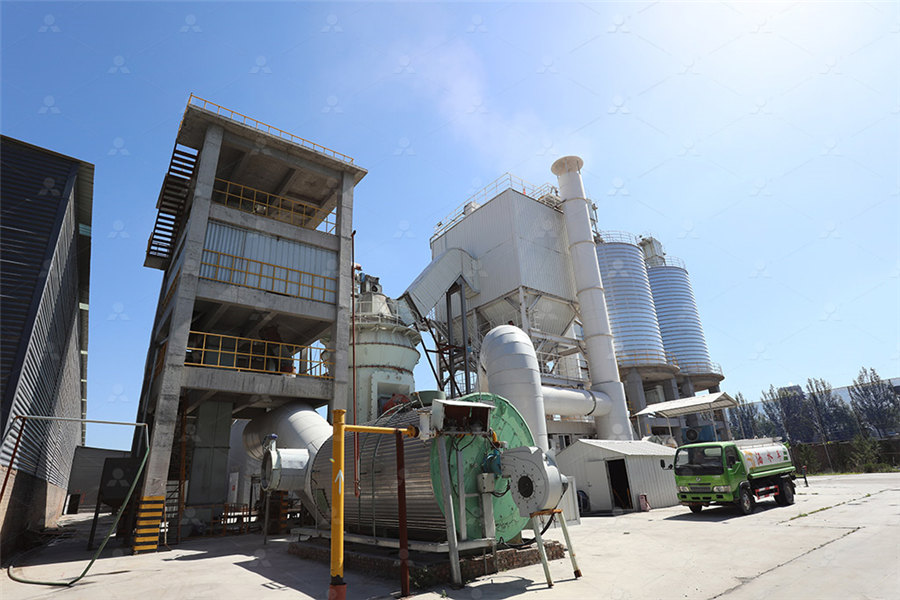
Loesche Mills for Metal Recovery and Filler Production from Steel Slag
Following coarse slag processing (recovery of metal eg + 20 mm, crushing of the mineral components to 20 mm) by means of crushing, screening and sorting technologies such as handpicking, sensor sorting, magnetic separation and/or dry density separation, a precrushed slag fraction is fed into the Loesche mill2024年7月1日 The steel industry consumes a lot of energy, and produces a lot of solid waste, accompanied by a lot of greenhouse gas emissions (Haghanimanesh et al, 2022)Further improving energy efficiency and reducing carbon dioxide emissions has become the huge challenge in the 21st century (Yokoi et al, 2022)An important measure is the heat recovery of Waste heat recovery of blast furnace slag in moving bed: 2024年11月1日 The green, efficient, and pollutionfree recycling of metallurgical waste slag has garnered global attention This study reviews the latest technologies for the recycling of steel slag (SS) and ladle refining slag (LFS), as well as the recent advancements in impurity element recovery using an applied electric fieldRecent research progress on recycling metallurgical waste slag 2024年9月15日 The new process for molten steel slag gas quenching and carbon sequestration waste heat recovery is outlined as follows: the source of gas quenching process is replaced with lime kiln flue gas Granulated steel slag undergoes secondary crushing in a fan mill, carbonation reaction of the steel slag takes place in a fluidized bed reactor, where the CO 2 supply is An efficient molten steel slag gas quenching process: Integrating
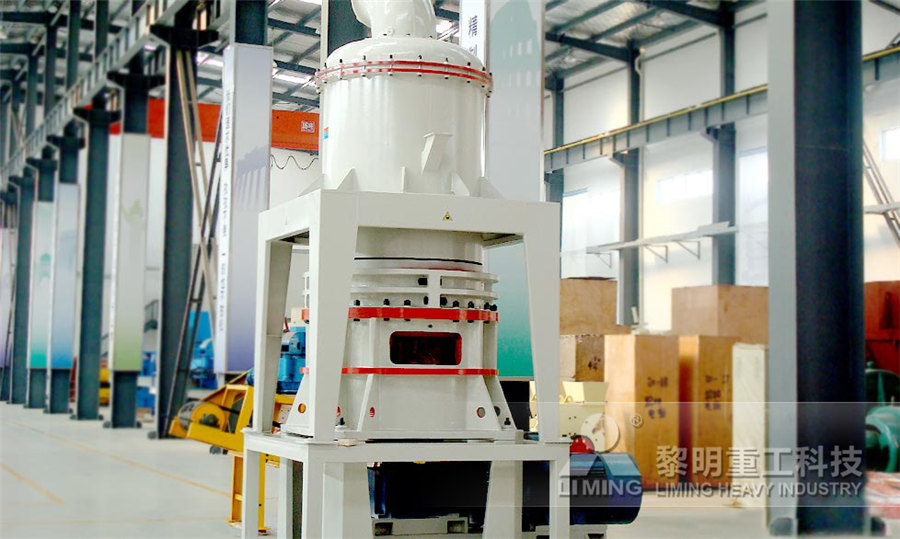
RESEARCH OVERVIEW ON RECOVERY OF WASTE HEAT FROM HIGH TEMPERATURE SLAG
waste heat recovery process of liquid slag into dry centrifugal granulation process and waste heat recovery process After dry centrifugal granulation, the temperature of blast furnace slag particles was about 900°C Then the particles entered the packed bed for heat transfer, resulting in hot air of 500600°C [5]2023年1月10日 Equipment configuration: LM vertical roller mill Treatment process: dry method Raw material source: selfgenerated solid waste from the Group's thermal power plant Finished product use: new marble material Process of Slag Grinding Plant Slag grinding is an important part of slag powder productionSlag Vertical Roller Milla Loesche mill, with a grinding track diameter of only 11 metres, was used as long ago as 1935 However, the breakthrough in grinding this type of material on the vertical roller mill did not take place until the beginning of the 1990’s 1935 The first Loesche mill for grinding cement clinker, an LM 11, was commissioned in Joao Pessao, Brazil2 µm 5 µm LoescheThe GRMSS steel slag vertical mill of CHAENG is a kind of special equipment for grinding industrial waste such as steel slag and water slag into powder +79Steel Slag Vertical Mill CHAENG
.jpg)
MPS vertical roller mills for slag and slag cements
2007年11月1日 The first industrialscale vertical roller mill for slag cement, an MPS 3750 C, went into operation in Hannover 25 years ago 1 and is still in operation today (Figure 3) The capacity of this mill ranges from 60t/h slag with 4100cm²/g to 70t/h CEM III A or 45t/h CEM III B with slag content between 50–80% and fineness of 3600cm²/g and 4300cm²/g2012年7月31日 Blast furnace (BF) slag, which is the main byproduct in the ironmaking process, contains large amounts of sensible heat To recover the heat, a new waste heatrecovery system—granulating molten Waste Heat Recovery from Blast Furnace Slag by Chemical 600,000 t/a slag grinding line with vertical roller mill, with a waste slag (like blast furnace slag,Steel slag and nickel slag) analysis center Metal recovery of per ton slag(%) 0203: 0203: in this course materials and hot gas got a fully heat exchange, slag grinding plant,vertical roller mill,slag mill,grinding mill2020年10月1日 Slag waste heat recovery: 31 Packed bed Patro and Dash [174] studied dilute, turbulent gas–solid flows in vertical pipes using EulerEuler method and plotted velocity profiles, turbulent intensity and pressure drop over a wide range of operating conditions and particle propertiesTechnologies and fundamentals of waste heat recovery from
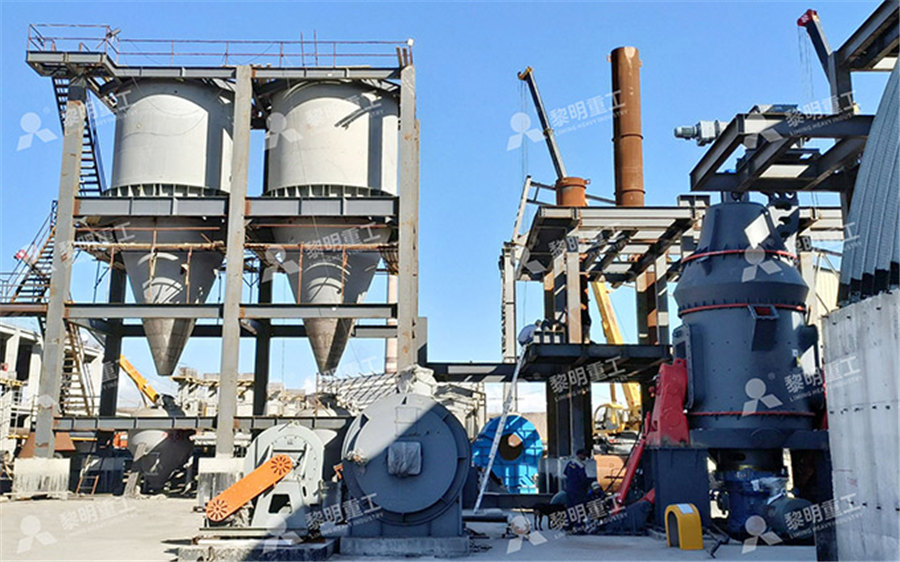
Recovery And Reuse Method of Laterite Nickel Ore Waste Slag
In the process of sulfuric acid decomposition of laterite nickel ore, the waste residue of laterite nickel ore has become a factor restricting the wet nickel extraction process As a manufacturer of nickel slag vertical grinding mill, HCMilling(Guilin Hongcheng) will introduce the methods of recovery and reuse of lateritic nickel ore waste slag to you below2018年6月1日 High temperature WHR consists of recovering waste heat at temperatures greater than 400 °C, the medium temperature range is 100–400 °C and the low temperature range is for temperatures less than 100 °C [2]Usually most of the waste heat in the high temperature range comes from direct combustion processes, in the medium range from the exhaust of Waste heat recovery technologies and applications【Product description】: GRMSS steel slag vertical roller mill made by CHAENG is special equipment for grinding industrial waste steel slag into powder CHAENG steel slag vertical mill has complete models and strengthens the iron dressing process, with the feeding size of ≤ 5mm 【Product capacity】: 200,0001,500,000t/aSteel Slag Vertical Roller Mill【Product description】: GGBS (Slag product applications) vertical roller mill is the equipment to grind Ground Granulated Blast furnace Slag (GGBFS) into small particlesGGBS (fineness:42004500cm2/g) produced by vertical roller mills are being used to substitute clinker in conventional cement manufacturing, for which the percentage of GGBS usage is typically at 1015% and 20 GGBS Vertical Roller Mill
.jpg)
Slag recycling recovery
Slag imports accounted for 52 % of the total in 2017 The 2015 recovery quantities for blast furnace slag are shown in Fig 15 Granulated slag makes up 86 %, of which almost the entire amount is used in the cement industry] } v W Okorie O (2020) High Temperature Rheological Characteristics of Iron and Steel Making Slag and its Waste Heat RecoveryA Review Adv Metallurg Mater Eng 3(1):104116High Temperature Rheological Characteristics of Iron and Steel 2013年12月1日 Hightemperature waste heat from the iron and steel industry, as shown in Fig 1, are mainly stored in products, molten slag and waste gas [2]Molten slag, as a kind of byproduct during the steelmaking process, is exhausted in extremely high temperature and thus, it carries a great deal of highgrade heat accounting for 10% of waste energy in steel industry A review of waste heat recovery technologies towards molten slag Request PDF On Jun 27, 2024, Shuting Wang and others published An efficient molten steel slag gas quenching process: Integrating carbon solidification and waste heat recovery Find, read and An efficient molten steel slag gas quenching process: Integrating

Rheological Characteristics of Iron and Steel Making Slag and its Waste
Rheological Characteristics of Iron and Steel Making Slag and its Waste Heat Recovery At High Temperatures Mathew Gas emission, Waste heat recovery 10 Introduction Iron and steel making practice today is extremely complex in view of the optimization of the various unit mill CO2 Iron and steel sector releases 7% of the total CO The GRMSS steel slag vertical mill of CHAENG is a kind of special equipment for grinding industrial waste such as steel slag and water slag into powder Integrating crushing, transporting, grinding and drying, the steel slag vertical mill is a kind Steel Slag Vertical MillInsulated exhaust gas ducting was routed across the plant by Hauri according to Gebr Pfeiffer’s specifications This serves as a hot gas supplier for the grinding plant Since the kiln exhaust gas has a lower dew point than the mill exhaust MPS mill now uses waste heat from a PFR kiln, saving In the process of sulfuric acid decomposition of laterite nickel ore, the waste residue of laterite nickel ore has become a factor restricting the wet nickel extraction process As a manufacturer of nickel slag vertical grinding mill, HCMilling(Guilin Hongcheng) will introduce the methods of recovery and reuse of lateritic nickel ore waste slag to you belowRecovery And Reuse Method of Laterite Nickel Ore Waste Slag
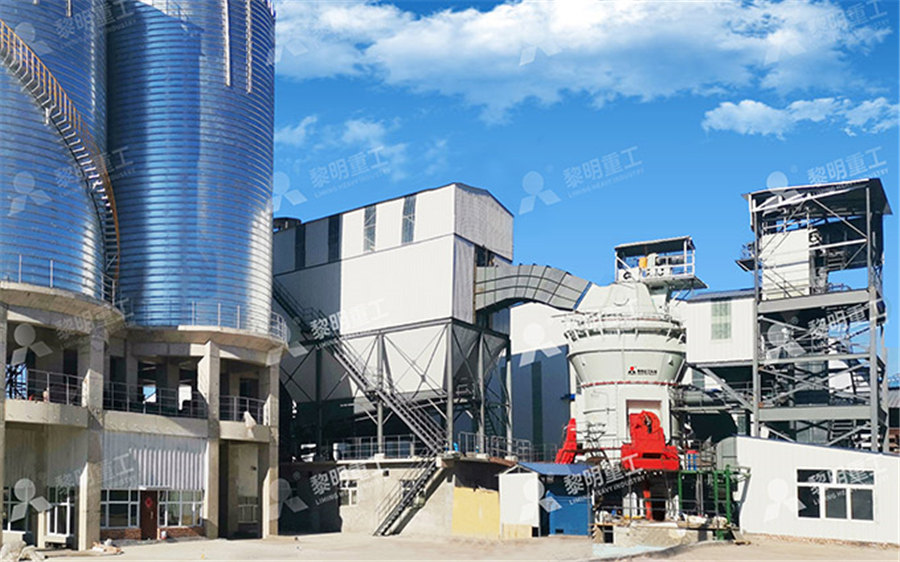
Cement Pulverisation Steel Slag Vertical Roller Mill Technology
Our vertical roller mills are able to pulverise steel slag into powder Cement Pulverisation Steel Slag Vertical Roller Mill Technology 01403 223 101 enquiriesUK@loesche2024年10月15日 This review provides a comprehensive analysis of the role of steel slag in mitigating carbon dioxide (CO 2) emissions in the steel industry through waste heat recovery, carbon sequestration, and resource utilizationAs a significant global source of CO 2 emissions, the steel industry holds substantial potential for CO 2 reduction through the effective The positive contributions of steel slag in reducing carbon dioxide Almost 30 years ago LOESCHE introduced the first vertical roller mill to grind both, cement clinker and granulated blast furnace slag, in one process The concept of M and Srollers was established in 1992, which is one of the most cost effective and Cement Blast Furnace Slag LoescheDanieli slag recovery plant in ABS Italy; and detail of slag recovery plant A secondary magnet processes the material treated by the jaw crusher which, by means of a reversible conveyor, is transported to the primary screen By reversing the direction of this conveyor, it is possible to complete the treatment withoutEAF SLAG RECOVERY TURNS A WASTE DISPOSAL PROBLEM INTO A BUSINESS
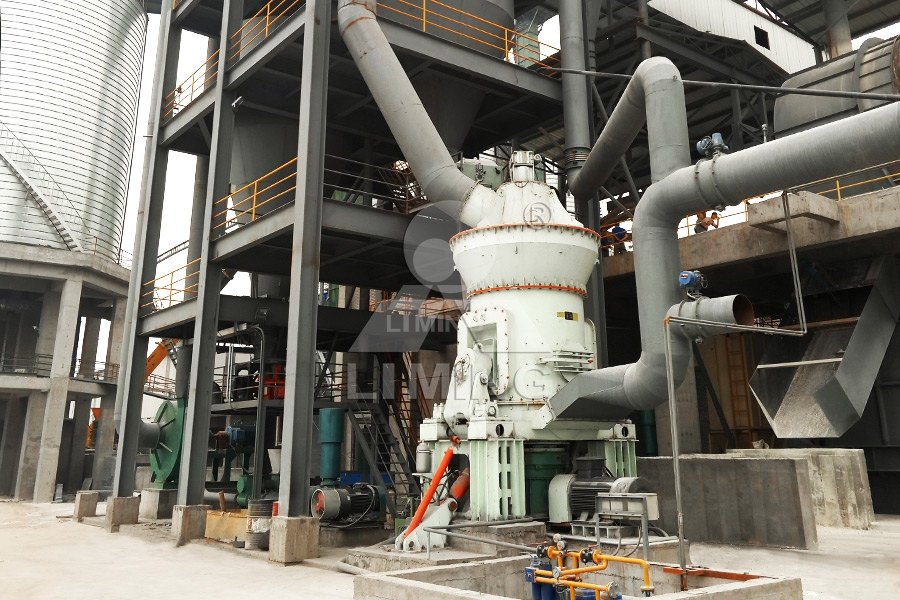
Waste Heat Recovery Technologies and Applications
2018年4月1日 Industrial waste heat is the energy that is generated in industrial processes which is not put into any practical use and is lost, wasted and dumped into the environmentDownload scientific diagram VERTICAL ROLLER MILL TECHNICAL DETAILS from publication: Grinding process optimization — Featuring case studies and operating results of the modular vertical roller VERTICAL ROLLER MILL TECHNICAL DETAILS ResearchGateFollowing coarse slag processing (recovery of metal eg + 20 mm, crushing of the mineral components to 20 mm) by means of crushing, screening and sorting technologies such as handpicking, sensor sorting, magnetic separation and/or dry density separation, a precrushed slag fraction is fed into the Loesche millLoesche Mills for Metal Recovery and Filler Production from Steel Slag2024年7月1日 The steel industry consumes a lot of energy, and produces a lot of solid waste, accompanied by a lot of greenhouse gas emissions (Haghanimanesh et al, 2022)Further improving energy efficiency and reducing carbon dioxide emissions has become the huge challenge in the 21st century (Yokoi et al, 2022)An important measure is the heat recovery of Waste heat recovery of blast furnace slag in moving bed:
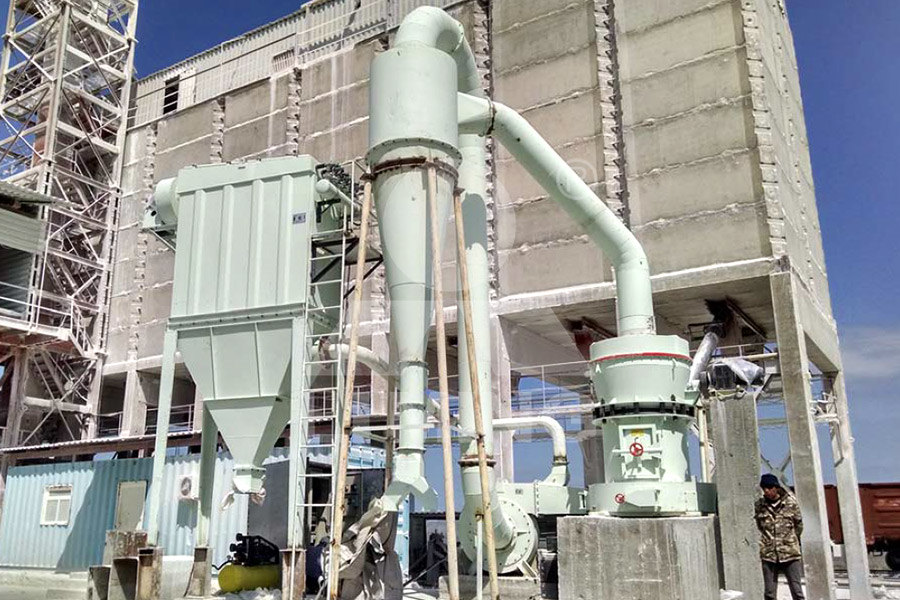
Recent research progress on recycling metallurgical waste slag
2024年11月1日 The green, efficient, and pollutionfree recycling of metallurgical waste slag has garnered global attention This study reviews the latest technologies for the recycling of steel slag (SS) and ladle refining slag (LFS), as well as the recent advancements in impurity element recovery using an applied electric field2024年9月15日 The new process for molten steel slag gas quenching and carbon sequestration waste heat recovery is outlined as follows: the source of gas quenching process is replaced with lime kiln flue gas Granulated steel slag undergoes secondary crushing in a fan mill, carbonation reaction of the steel slag takes place in a fluidized bed reactor, where the CO 2 supply is An efficient molten steel slag gas quenching process: Integrating waste heat recovery process of liquid slag into dry centrifugal granulation process and waste heat recovery process After dry centrifugal granulation, the temperature of blast furnace slag particles was about 900°C Then the particles entered the packed bed for heat transfer, resulting in hot air of 500600°C [5]RESEARCH OVERVIEW ON RECOVERY OF WASTE HEAT FROM HIGH TEMPERATURE SLAG 2023年1月10日 Equipment configuration: LM vertical roller mill Treatment process: dry method Raw material source: selfgenerated solid waste from the Group's thermal power plant Finished product use: new marble material Process of Slag Grinding Plant Slag grinding is an important part of slag powder productionSlag Vertical Roller Mill
.jpg)
2 µm 5 µm Loesche
a Loesche mill, with a grinding track diameter of only 11 metres, was used as long ago as 1935 However, the breakthrough in grinding this type of material on the vertical roller mill did not take place until the beginning of the 1990’s 1935 The first Loesche mill for grinding cement clinker, an LM 11, was commissioned in Joao Pessao, BrazilThe GRMSS steel slag vertical mill of CHAENG is a kind of special equipment for grinding industrial waste such as steel slag and water slag into powder +79Steel Slag Vertical Mill CHAENG2007年11月1日 The first industrialscale vertical roller mill for slag cement, an MPS 3750 C, went into operation in Hannover 25 years ago 1 and is still in operation today (Figure 3) The capacity of this mill ranges from 60t/h slag with 4100cm²/g to 70t/h CEM III A or 45t/h CEM III B with slag content between 50–80% and fineness of 3600cm²/g and 4300cm²/gMPS vertical roller mills for slag and slag cements2012年7月31日 Blast furnace (BF) slag, which is the main byproduct in the ironmaking process, contains large amounts of sensible heat To recover the heat, a new waste heatrecovery system—granulating molten Waste Heat Recovery from Blast Furnace Slag by Chemical