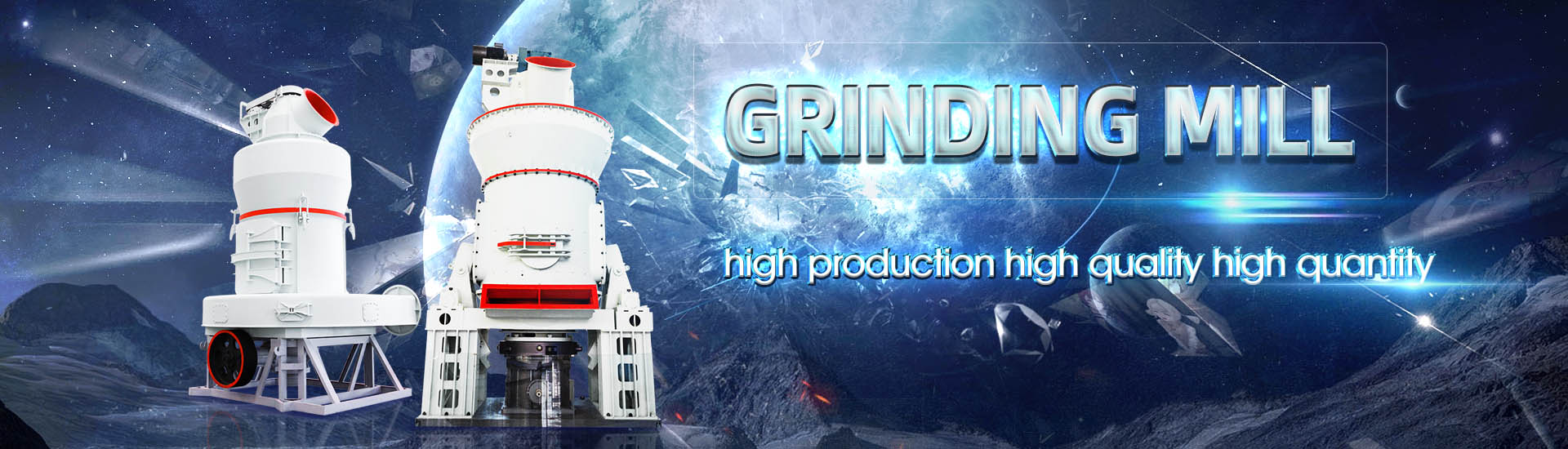
Grinding system ore mill size and weight
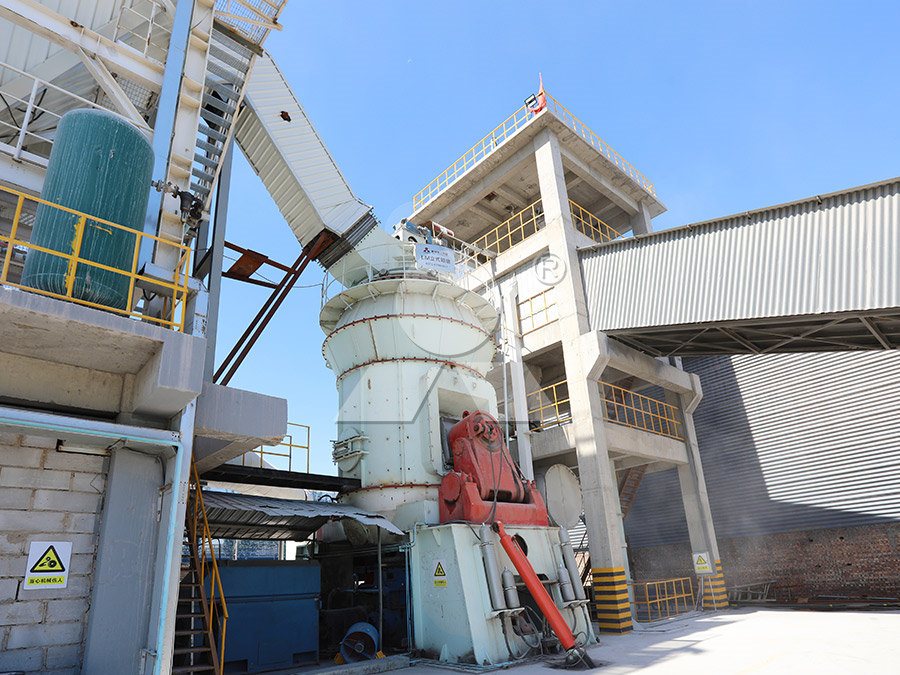
SAG Mill Optimization using Model Predictive Control Andritz
SemiAutogenous Grinding mills can be optimized for maximum ore throughput or maximum grinding energy efficiency In both cases, precise control of the mill weight is critical Model predictive control provides an additional tool to improve the control oSemif Autogenous 2023年7月20日 According to the particle sizes of grinding products, the grinding process is divided into coarse grinding, medium grinding, fine grinding, microfine grinding, and ultrafine Ore Grinding SpringerLinkGrinding of ore is one of the most important and power intensive operation in mining In order to process the ore at faster rate, sizes of mills have gone bigger and bigger While mill diameters OVERVIEW OF GRINDING SYSTEMS AND MV DRIVE In the present state of technological development for primary grinding mills, there is a wide choice of acceptable options with respect to type and size, grinding flowsheet and grinding mediaPrimary Grinding Mills: Selection, Sizing And Current Practices
.jpg)
(PDF) OptimalSetting for Ore and Water Feeding in Grinding
2021年6月23日 In this paper, a novel expert system is proposed for guiding the operating variables to keep the product stable with the wildly varying ore properties First, casebased 2023年10月25日 This study introduced the use of machine learning models tailored to the identification of distinct operational regions within SAG mills, focusing on ore type properties such as rock hardness and particle sizeMachine Learning Algorithms for SemiAutogenous Nowadays, conducting grindability tests requiring only a few kilos of material on several samples, is a more typical approach to grinding mill design This paper summarises the requirements SAG Mill Testing Test Procedures to Characterize Ore Grindability According to the particle fi sizes of grinding products, the grinding process is divided into coarse grinding, medium grinding, ne grinding, micro ne grinding, and ultrane fi fi fi grinding Ore Grinding Methods and Process of Ore Grinding

OptimalSetting for Ore and Water Feeding in Grinding
2021年6月23日 The grinding product particle size is the most crucial operational index of mineral grinding processes The size and consistency of the product directly affects the subsequent dressing and sintering In this paper, a novel 2024年1月1日 Measurement and control for ore grinding and classification is the process of detecting and controlling the key equipment and key parameters in grinding and classification Measurement and Control for Ore Grinding and Classification2024年7月31日 Ultimately, the optimal grinding performance was achieved with Bondtype ball distribution No 6, considering ball size, mill speed, and feedrate interactions, albeit with considerations Effect of Grinding Conditions on Clinker Grinding Efficiency: Ball Size 2015年6月7日 In the present work, the effects of some key grinding parameters such as ball size (20–40 mm), grinding time (10–30 min), solids content (65–80%), and also ore work index (12–154 kWh/t Investigating of the effect of ore work index and particle size on
.jpg)
Grinding System Zeta® NETZSCH Grinding
Machine Sizes The Zeta ® grinding system is available in sizes ranging from the Mini/MicroSeries laboratory mills with grinding chamber volumes of 008 l to production machines with grinding chamber volumes of 400 l Full scaleup of 2023年7月20日 (2) Various working parameters of grinding mill, including fraction of critical speed for grinding mill, filling rate for grinding mill, grinding concentration, grinding cycle load, etc (3) And grinding material properties, including ore grindability, feeding particle size, etc Huge energy and steel consumption in ore grinding process greatly affect the subsequent separation Ore Grinding SpringerLinkBond Rod Mill 0305 127 Any 118 15 10 Lockedcycle Y Y Bond Ball Mill 0305 335 Any 0149 10 5 Lockedcycle Y Y Mod Bond 0305 335 Any N/A 2 12 Batch N Y Table 1 – Summary of Grindability Test Procedures 1Weight requested for the test, for typical ores (SG = 28g/cm3) Denser samples require more weight, proportional to the SGSAG Mill Testing Test Procedures to Characterize Ore GrindabilityRoller mill: Particle size = 841 µm; std deviation (sgw) = 2134 841 µm ÷ 2134 = 394 µm 841 µm × 2134 = 1,792 µm Thus, 67% of the material would be between 394 and 1,792 µm Grinding equipment Both roller mills and hammermills have been applied to the task of particle size reduction or grinding in feed milling applicationsGrinding considerations when pelleting livestock feeds
.jpg)
How to Size Design a Regrind Ball Mill 911Metallurgist
2018年4月8日 Referring to Table VI the L/D can be between 175 and 20 or even greater Referring to Table VII a 305 meter (10 foot) by 305 meter (10 foot) overflow ball mill with a 40 percent by mill volume ball charge, new liners and 50 mm (2″) balls draws 491 HP Using equation 5 there will be a loss of 055 Kw (074 Hp) per metric tonnes of ballsThe efficiency of the mill to break ore is a function of both the feed size distribution and the relative hardness of the ore When the feed size of a SAG mill becomes coarser, ie α r increases Correlation Between F80 and Mill Performance for a SAG Millsample is calculated The present investigation focuses on utilizing the calculated retention time of the iron ore as a standard grinding reference time to the laboratory ball mill for optimizing the grinding time of each ore The desired P 80 (150 μm) with an acceptable range of hematite liberation (>75%) was obtained in the laboratory ball Estimation of Grinding Time for Desired Particle Size Distribution2013年8月3日 In Grinding, selecting (calculate) the correct or optimum ball size that allows for the best and optimum/ideal or target grind size to be achieved by your ball mill is an important thing for a Mineral Processing Engineer AKA Metallurgist to do Often, the ball used in ball mills is oversize “just in case” Well, this safety factor can cost you much in recovery and/or mill liner Calculate and Select Ball Mill Ball Size for Optimum Grinding
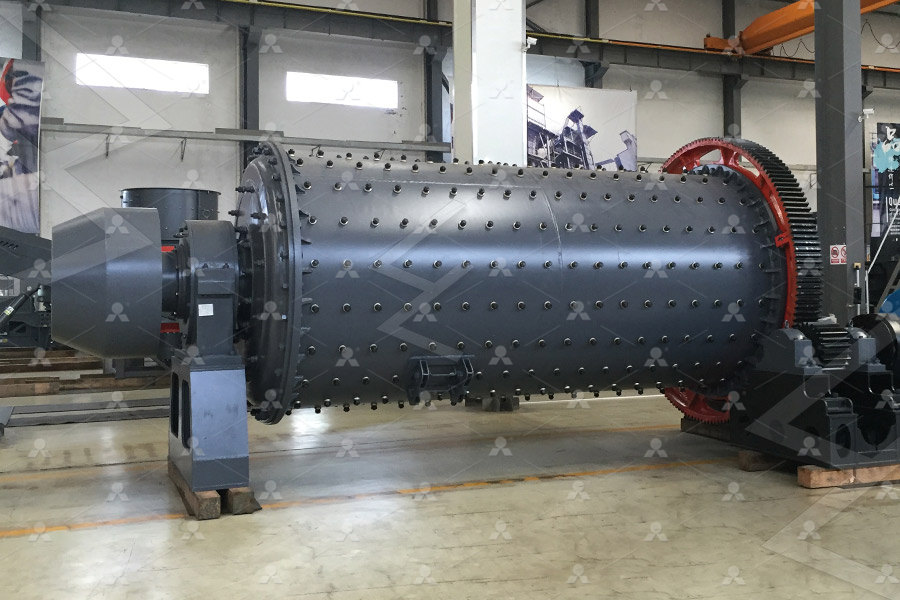
Ore characterisation for––and simulation of––primary autogenous
2003年1月1日 Parameter A is the maximum value of t 10, ie, the highest level of size reduction from a single impact eventThe value of A∗b, the derivative of Eq (1) at Ecs=0, can be used to compare the samples as there is an interaction between these parameters A high value of A∗b means that the ore has a low resistant to impact breakage and vice versa2016年4月1日 The amount of feed was set at 1175 g, which was proportional to industrial scaleThe ball mill speed was constantly set at 768% CsExperiments were conducted at different ball sizes (between 20 and 40 mm), grinding time (10–30 min), solids content (65–80%) and work index of copper sulphide ore (12–154)RSM and Box–Behnken design were used for the Investigating of the effect of ore work index and particle size on 2018年6月18日 Ore pretreatment methods for grinding: journey and prospects, Mineral Processing and Extractive Metallurgy Review, DOI: 101080/2018 To link to this article: https://doior g/10 Ore Pretreatment Methods for Grinding: Journey and 2015年11月30日 In this paper the effects of flow rate, slurry solid content and feed size distribution on the rod mill efficiency have been investigated It is difficult to achieve highest grinding efficiency (PDF) Effects of Flow Rate, Slurry Solid Content and Feed Size
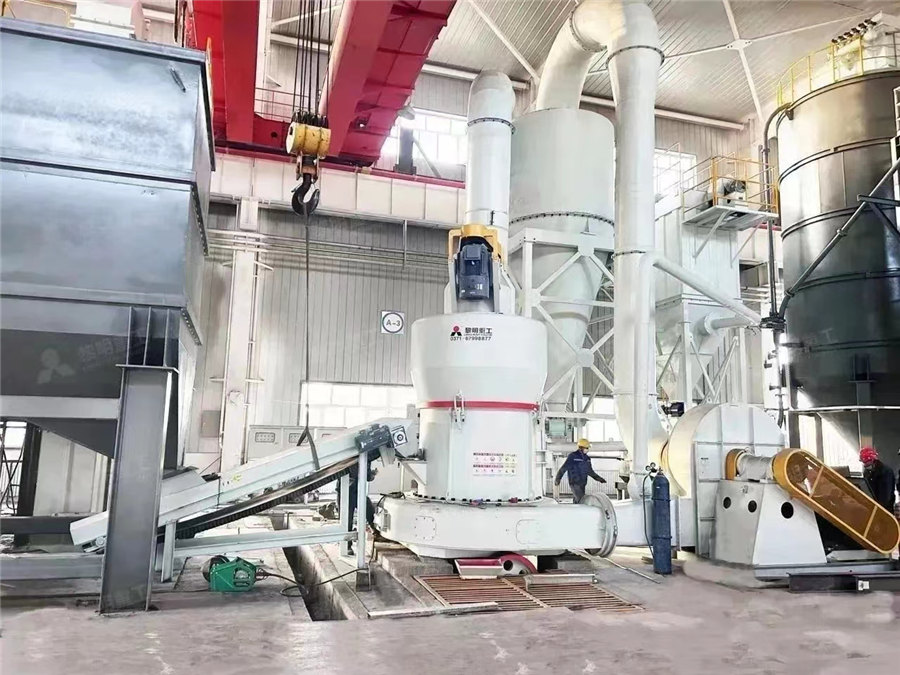
I203 I204 INTRODUCTION SMC Testing
Top size (mm) Mill Weight Power Top Size Figure 4: Feed Top Size vs SAG Mill Performance 5000 5500 6000 6500 7000 7500 8000 8500 9000 9500 10000 13:00 14:00 15:00 16:00 17:00 kW 00 500 1000 1500 2000 2500 3000 3500 4000 Top size (mm) Top Size Power Mill Weight Figure 5: Feed Top Size vs AG Mill Performance2023年4月24日 liberation for downstream separation processes Particle breakage is attained by the collisions between the ore and the grinding media During the interaction of ore and grinding media, a complex physical and chemical system is formed, causing changes in particle size, pulp chemistry, surface chemistry, and crystal structure of minerals [13]Grinding Media in Ball MillsA Review Preprints2020年9月22日 Grinding machine has been widely used in gold mines in South Africa since 1905 At that time, the grinding machine used river pebble as the grinding medium, which was essentially a gravel mill Later, in order to improve the production capacity of the mill, cast iron balls were used as the medium, so normal gravel mills were evolved into ball mills and rod millsGrinding Machines: Types and Selection Principles MiningpediaAn 8 x 7 diaphragm type ball mill grinding 05″ copper ore to 96% passing 65 mesh HP=HP per ft of mill length W=Weight of grinding charge and material per ft of mill length If the feed to such a system can be top size limited, Grinding Mills 911Metallurgist
.jpg)
Grinding System Discus Intensive
We are the only manufacturer in the world able to build them in size from 1 ltr to 15,000 ltr and from 3 kW to 4000 kW With the introduction of the new disc geometry TetraNex ® /TetraNex ® Plus, a significant increase in the efficiency of the grinding system was achieved Now the grinding system has been modified again2021年11月1日 It is worth noticing here that the ball mill loading, ie, grinding media (steel balls) and product (chalcopyrite ore), is the system parameter that influences the most the mill torque The total grinding energy associated with all batch and continuous ball milling tests (replicates 1 and 2) carried out in this work are summarized in Table 6 Experimental characterization of chalcopyrite ball mill grinding 2017年2月20日 When choosing primary autogenous grinding, run of mine ore up to 200300 mm in size is fed to the mill A closed circuit dry grinding system is very space consuming because of the classifier, Typical grinding mill size of feed: coarse (1″ to 2″); medium (¼” to ¾”),Grinding Mill Design Ball Mill Manufacturer 911Metallurgist2021年11月1日 All content in this area was uploaded by Pramod Aradwad on Dec 02, 2021(PDF) Key issues and challenges in spice grinding
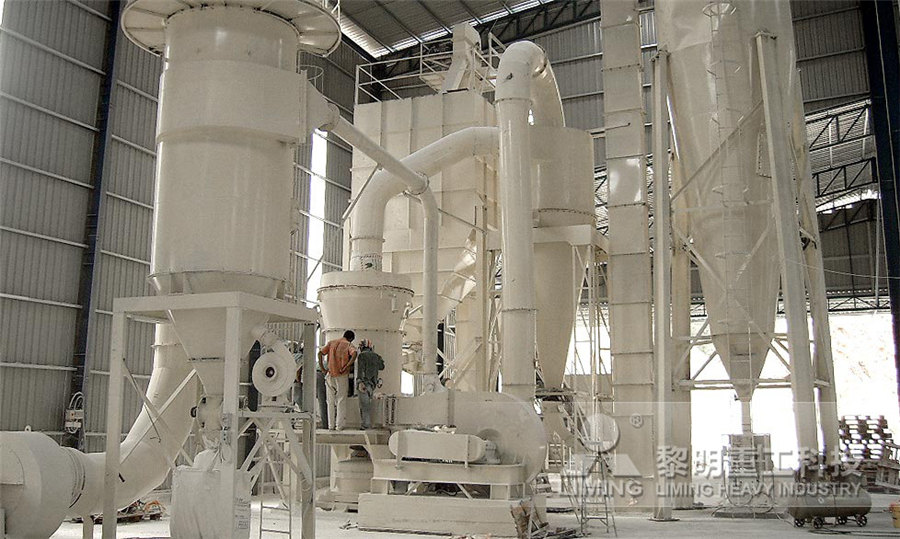
Taking your grinding to the next level Mill lining solutions for
influence on grinding efficiency It transforms the mill rotation into charge motion, and both profile and spacing must be selected to suit each specific mill When designing a shell lining, the type of ore, mill size and speed, maintenance schedules, safety, impact levels and efficient use of materials should all be considered Discharge systems2021年11月1日 The various empirical energysize reduction relationships from Bond [1] to Morrell [2] have served the industry well as methods that rely on relatively simple experiments and that provide estimates of the specific energy consumption in industrial mills with some confidence on the basis of a single size markerAlthough these are particularly useful with the aim of Mechanistic modeling and simulation of grinding iron ore pellet 2018年8月8日 One of the most effective methods of grinding Portland cement is the use of an electromagnetic mill, which has proven its advantage in creating clinkerless binders [2], regulating the kinetics of (PDF) Grinding Kinetics Adjustment of Copper Ore Grinding in The grinding media—their type and size—are also of significance [19] The ratio between the size of the grinding media and the size of the comminuted particles is especially important Research performed on this aspect demonstrates that the size of the particles in the mill feed significantly influences the energyEnergy Efficiency Analysis of Copper Ore Ball Mill Drive Systems
.jpg)
SWECO Vibratory Grinding and Particle Size Reduction Equipment
High Amplitude Wet or Dry Mills Vibratory Grinding Mills Size Reduction Equipment Specifically designed for wet or dry grinding, the high amplitude VibroEnergy Grinding Mills range from 1 ft³ (36 liters) to 75 ft³ (1,934 liters) of volume Wet or Dry Grinding Mill Models: DM1, DM4, DM10, DM20, DM28, DM70 Low Amplitude Wet Mills Vibratory Grinding Mills Size Reduction MILL OPTIMIZATION IN IRON ORE GRINDING* Patrícia Mundim Campos Faria1 Luís Marcelo Tavares 2 Raj K Rajamani 3 the size distribution in a tumbling mill grinding as a function of time in batch grinding concentration in weight varied from 72 to 80% After reaching a POPULATION BALANCE MODEL APPROACH TO BALL MILL OPTIMIZATION IN IRON ORE 2021年1月22日 Grinding operation is used extensively in the industry of beneficiation, metallurgy, chemical engineering, and electric power Assisted by the impact and abrasion between media (steel ball, steel rod, gravel, ceramic ball) and ore, the grinding operation reduces the particle size in the mill [[1], [2], [3]]To produce the qualified size and high liberation of An innovative approach for determining the grinding media system Bond Rod Mill 0305 127 Any 118 15 10 Lockedcycle Y Y Bond Ball Mill 0305 335 Any 0149 10 5 Lockedcycle Y Y Mod Bond 0305 335 Any N/A 2 12 Batch N Y Table 1 – Summary of Grindability Test Procedures 1Weight requested for the test, for typical ores (SG = 28g/cm3) Denser samples require more weight, proportional to the SGSAG Mill Testing Test Procedures to Characterize Ore
.jpg)
Effect of Grinding Conditions on Clinker Grinding Efficiency: Ball Size
2024年7月31日 Ultimately, the optimal grinding performance was achieved with Bondtype ball distribution No 6, considering ball size, mill speed, and feedrate interactions, albeit with considerations 2015年6月7日 In the present work, the effects of some key grinding parameters such as ball size (20–40 mm), grinding time (10–30 min), solids content (65–80%), and also ore work index (12–154 kWh/t Investigating of the effect of ore work index and particle size on Machine Sizes The Zeta ® grinding system is available in sizes ranging from the Mini/MicroSeries laboratory mills with grinding chamber volumes of 008 l to production machines with grinding chamber volumes of 400 l Full scaleup of Grinding System Zeta® NETZSCH Grinding2023年7月20日 (2) Various working parameters of grinding mill, including fraction of critical speed for grinding mill, filling rate for grinding mill, grinding concentration, grinding cycle load, etc (3) And grinding material properties, including ore grindability, feeding particle size, etc Huge energy and steel consumption in ore grinding process greatly affect the subsequent separation Ore Grinding SpringerLink
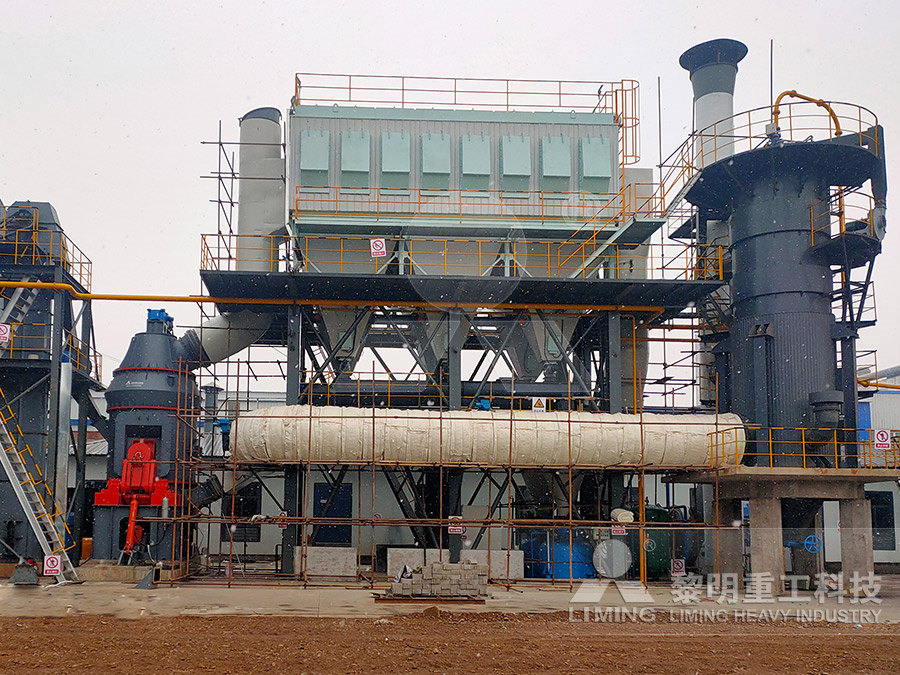
SAG Mill Testing Test Procedures to Characterize Ore Grindability
Bond Rod Mill 0305 127 Any 118 15 10 Lockedcycle Y Y Bond Ball Mill 0305 335 Any 0149 10 5 Lockedcycle Y Y Mod Bond 0305 335 Any N/A 2 12 Batch N Y Table 1 – Summary of Grindability Test Procedures 1Weight requested for the test, for typical ores (SG = 28g/cm3) Denser samples require more weight, proportional to the SGRoller mill: Particle size = 841 µm; std deviation (sgw) = 2134 841 µm ÷ 2134 = 394 µm 841 µm × 2134 = 1,792 µm Thus, 67% of the material would be between 394 and 1,792 µm Grinding equipment Both roller mills and hammermills have been applied to the task of particle size reduction or grinding in feed milling applicationsGrinding considerations when pelleting livestock feeds2018年4月8日 Referring to Table VI the L/D can be between 175 and 20 or even greater Referring to Table VII a 305 meter (10 foot) by 305 meter (10 foot) overflow ball mill with a 40 percent by mill volume ball charge, new liners and 50 mm (2″) balls draws 491 HP Using equation 5 there will be a loss of 055 Kw (074 Hp) per metric tonnes of ballsHow to Size Design a Regrind Ball Mill 911MetallurgistThe efficiency of the mill to break ore is a function of both the feed size distribution and the relative hardness of the ore When the feed size of a SAG mill becomes coarser, ie α r increases Correlation Between F80 and Mill Performance for a SAG Mill
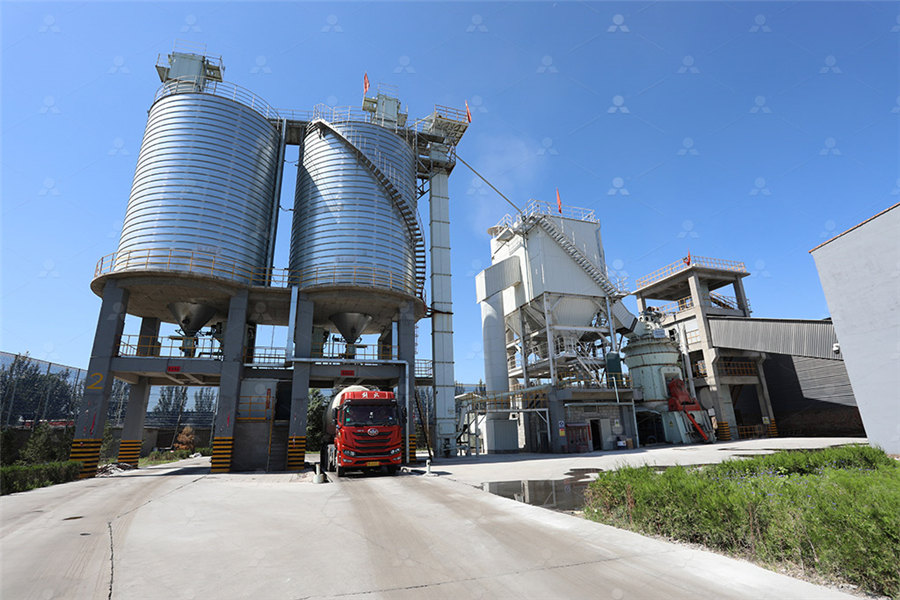
Estimation of Grinding Time for Desired Particle Size Distribution
sample is calculated The present investigation focuses on utilizing the calculated retention time of the iron ore as a standard grinding reference time to the laboratory ball mill for optimizing the grinding time of each ore The desired P 80 (150 μm) with an acceptable range of hematite liberation (>75%) was obtained in the laboratory ball 2013年8月3日 In Grinding, selecting (calculate) the correct or optimum ball size that allows for the best and optimum/ideal or target grind size to be achieved by your ball mill is an important thing for a Mineral Processing Engineer AKA Metallurgist to do Often, the ball used in ball mills is oversize “just in case” Well, this safety factor can cost you much in recovery and/or mill liner Calculate and Select Ball Mill Ball Size for Optimum Grinding