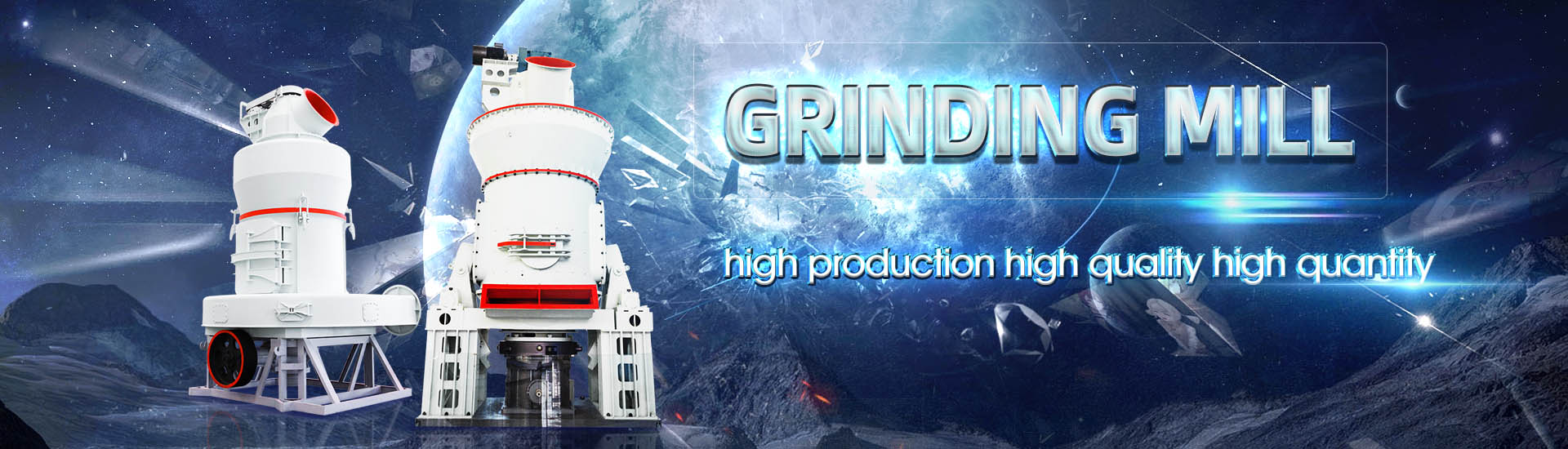
Basic equipment for electrolytic iron oxide processing

Fact sheet Electrolysis in ironmaking
Electrolysis of iron ore has been demonstrated at the laboratory scale, producing metallic iron and oxygen as a coproduct Current status The EU ULCOS project examined the prospects for 2011年4月19日 This programme evaluates technologies that incorporate hydrogen or biomass, CCS and direct electrolysis The latter involves electrolysis of iron ore (Allanore, Ortiz and Sadoway, 2011)Molten Oxide Electrolysis for Iron Production: 2024年3月20日 Here, we report a chloriron process that could be powered by renewable electricity to produce iron from ore and purified seawater The design uses components Electrochemical chloriron process for iron production from iron motivated by the production of iron metal from an iron oxide containing electrolyte as a carbon neutral approach to replace current pyrometallurgical processes that result in copious amounts Chapter 10 Electrolysis of Iron Ores: Most Efficient Springer
.jpg)
Molten Oxide Electrolysis for Iron Production: Identification of Key
help reach CO2 mitigation targets relies on the intensive use of electricity: molten oxide electrolysis (MOE) This paper presents the key process parameters that need to be tuned toMolten oxide electrolysis (MOE) is a carbonneutral, electrochemical technique to decompose metal oxide directly into liquid metal and oxygen gas upon use of an inert anodeMIT Open Access Articles Massachusetts Institute of Technology2023年3月14日 In an electrochemical process, an electric current is applied between two electrodes to provide the electromotive force needed to break an iron ore into metal iron and Research progress in the preparation of iron by electrochemical 2018年1月5日 To ensure that metal iron production results from a faradaic phenomenon, the contribution of the thermal level to iron oxide decomposition and electronic current in the Electrolysis of iron in a molten oxide electrolyte
.jpg)
Molten Oxide Electrolysis for Iron Production: Identification of Key
2011年2月28日 Energy Balance on an Electrolysis Cell What Conditions for an Energetically Competitive Process? What Conditions for a CO 2 Mitigation? Conclusion2022年9月1日 Microstructural evolution of the Working Electrode (WE) during the electrochemical reduction to Fe in 10 M NaOH and at 90 ° C in a (A) Fe 2 O 3 ceramic suspension and as a (B) Fe 2 O 3 ceramic Prospects and challenges of the electrochemical 2023年7月31日 Electrolytic Polishing Process: Degreasing — Water Washing — Rust Removal — Water Washing — Electrolytic Polishing — Water Washing — Neutralization — Water Washing — Packaging V Types of Electrolytic Electrolytic Polishing Techniques: Basic Guide2014年7月1日 Oxide dispersion strengthened (ODS) steels are considered as the future structural material of interest for nuclear power plants, due to their elevated creep resistance at higher operation temperaturesIn this study, a 03 wt% nanoyttria (Y 2 O 3) dispersed iron cast trial was elaborated using rapid solidification processing (RSP) The nanosized Y 2 O 3 Comprehensive study on the sintering behavior of yttria nano
.jpg)
Iron Ore Processing an overview ScienceDirect Topics
Resource Recovery and Recycling from Metallurgical Wastes S Ramachandra Rao, in Waste Management Series, 2006 98 Production of Ceramic Tiles from Iron Ore Tailings Current practice of washing iron ore before it is processed for extractive metallurgical operation results in three products, coarse ore lumps with sizes in the range 1080 mm, which are directly charged 3 with additions of copper oxide and transition metals Cu, Ni, Co, and Fe were obtained Changes in the phase content of materials based on iron oxide were shown, and the electrical conductivity of the obtained composites was studied Samples of inert anodes were tested in an electrolytic cell; high resistance of cermets NiFe 2OMetalCeramic Composites Based on Iron Oxide for Low2011年4月19日 This novel technology electrolyzes iron oxide into metallic iron that is of crude steel quality (Allanore, Ortiz and Sadoway, 2011; Allanore, 2014;Wiencke et al, 2018)Molten Oxide Electrolysis for Iron Production: Identification of expertise in iron precipitation, nickel and cobalt producers benefit from environmentally acceptable iron residue storage or further use Manganese, an impurity often associated with these raw materials, can be precipitated as manganese oxide either together with iron or separately From iron and manganese removal, the pregnant leachHydrometallurgical nickel and cobalt plants and processes
.jpg)
Copper Cathode Production LineHydrometallurgy
In a copper cathode production line, the copper anode and stainlesssteel cathode forming into pair are placed in the electrolytic cell DC current is continuously applied across the anodecathode pair to stimulate the anode copper dissolve into the electrolyte to get copper ions and other soluble cations, while copper ions get electrons and deposit on the cathode surface to 2018年1月5日 Abstract Direct iron production at molten metal state from iron oxides by the sole application of electrical energy represents a possible route to decarbonize steel industry Although chemically simple, this reaction is difficult to implement due to the problem of the multiple valence states of iron and to an operating temperature above 1811 K Thermal, chemical, and Electrolysis of iron in a molten oxide electrolyte2024年8月5日 llustrations of electrolysis reactors that produce iron from ore (1) Author's own work derived from Boston Metal website; (2) From Lomax et al [22] and (3) From Hervé [28])Economics of Electrowinning Iron from Ore for Green Steel 2023年9月15日 Iron powder is a powdered form of elemental iron It is commonly used in many industrial and manufacturing applications due to its unique properties and versatility This comprehensive guide will provide an overview of iron powder, its types, characteristics, applications, design considerations, suppliers, installation, operation and maintenanceIron Powder: Characteristics,types,Specifications Additive
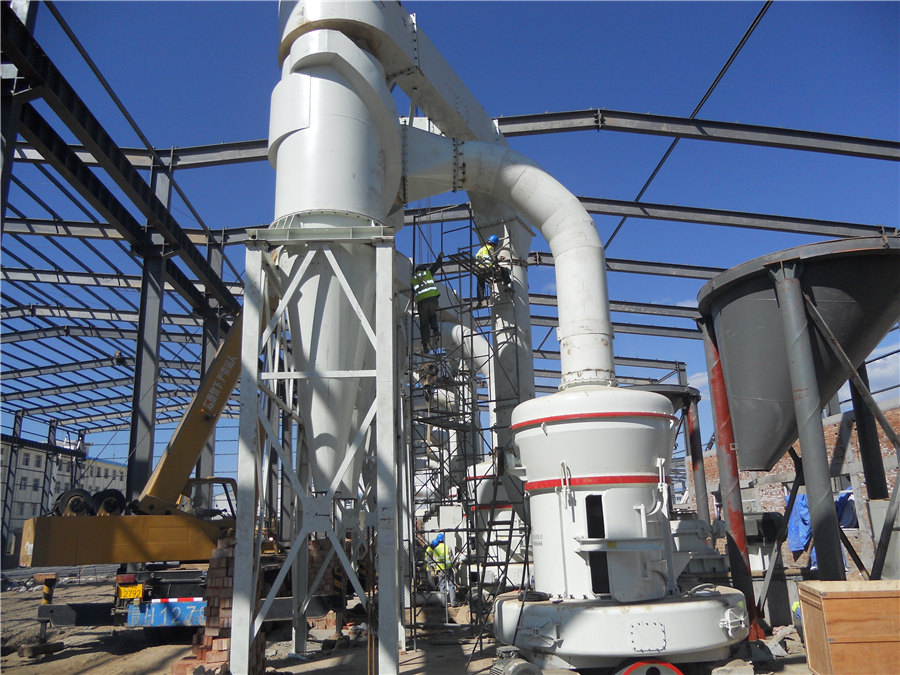
Electrolysis of iron in a molten oxide electrolyte Springer
22 Formulation of an iron oxide concentration to carry out MIDEIO Finally, thermodynamic calculations were carried out with the thermochemical software CECQSI [25] to take into account the effect of the chemical dissolution of iron oxide in the proposed electrolyte composition A concentration of 15% in weight of iron oxide, named in Fe#15,Fig 1 Integration of the chloriron process with lowcarbon electricity, Cl 2, and electric arc furnace markets (A) Iron ore electrolysis, fed by abundant iron oxide, seawater, and zerocarbon electricity, can support further deployment of infrastructure for a netzeroemissions energy system (B) Colocation ofElectrochemical ChlorIron Process for Iron Production from Iron Oxide 2011年2月15日 In this work, plasma electrolytic surface carburizing of pure iron in aqueous solution consisting of water, glycerin and NH 4 Cl was investigated Surface carburizing was carried out in 20% glycerin solution treated at 750 °C, 800 °C, 900 °C and 950 °C temperatures for 5, 10 and 30 minThe formation of hard carbonrich layer on the surface of pure iron was Kinetics and mechanical study of plasma electrolytic carburizing Li et al [28] used the FFC to directly reduce iron oxide to iron electrochemically The process can produce two useful products at the cathode and anode, providing a zero emission technology for the steel smelting industry However, at present, FFC process still needs a relatively pure iron oxide raw material, the electronegative metal thanResearch progress in the preparation of iron by electrochemical
.jpg)
Electrolytic Cleaning Equipment Selection Guide: Types, Features
Passivation equipment utilizes passivation chemicals or electrochemical processes to passivate or to reduce surface reactivity to protect a metal against corrosion Excess iron and oxide scale from welding and other thermal processing can result in reduced corrosion resistance or nonpassivated conditionproducts (7) Thus, the discovery of an inert anode is critical in enabling the electrolytic recovery of iron from a molten oxide electrolyte without generation of byproduct CO/CO2 Under such conditions, electrolytic steelmaking possesses distinct advantages over conventional technology There is no need for coke ovens, blast furnaces and BOF'sElectrochemical Processing in Molten SaltsSTUDY ON ELECTROLYTIC REDUCTION WITH CONTROLLED OXYGEN FLOW FOR IRON FROM MOLTEN OXIDE SLAG CONTAINING FeO YM Gaoa,*, B Wanga, SB Wanga, S Penga a Key Laboratory for Ferrous Metallurgy and STUDY FLOW ON FOR ELECTROLYTIC IRON FROM MOLTEN REDUCTION OXIDE 3 solution, and the iron oxide and iron hydroxide were removed by EPP within 30 s, reported by Kumruoglu (Ref 10) Lowcarbon steel (AISI 1018) and highstrength AISI 4340 steel were cleaned in the Na 2CO 3 and/or NaHCO 3 solutions by Smith et al (Ref 9, 11, 12) Gupta (Ref 13) has mentioned that EPP could be used to processDual Electrolytic Plasma Processing for Steel Surface Cleaning
.jpg)
Microscopic characterization and modeling of oxide layer for
Microscopic characterization and modeling of oxide layer for electrolytic inprocess dressing (ELID) grinding with focus on processing, the oxide layer appearedas a examination by SEM Fig 3 Schematic illustration of the basic experimental setup Int J Adv Manuf Technol (2019) 105:4853–4862 4855 24 Experimental setup The experimental The starting material for electrolytic smelting of aluminum is pure, anhydrous aluminum oxide (Al 2 O 3) called alumina In the Western World, the Bayer 1 process, invented in the 19th century, is by far the most important process used in the production of aluminum oxide from bauxite The process has been refined and improved since its inceptionChapter 2 Production and Processing of Aluminum The Iron oxide from whole duration of electrolysis tests in the range bauxite residue (mainly haematite) is reduced to of –12 V to –14 V which coincide fully with the metallic iron in the region of cathodic potentials region of haematite reduction to metallic iron as from –12 V to –14 V with a peak at –136 V shown in the voltammogram of Figure 3(PDF) Electrolytic Iron Production from Alkaline Bauxite Residue verization and electrolytic deposition In the ongoing research a noble approach has been made to recover iron powder directly from mild steel scrap using monopolar and multipolar electrolytic cell arragements in an optimized process parameter of 15 A current, voltage 7–10 V, pH 3–5, current density 05 A/cm2, time 3 h and elecRecovery of Iron Powder Through Process Optimization and
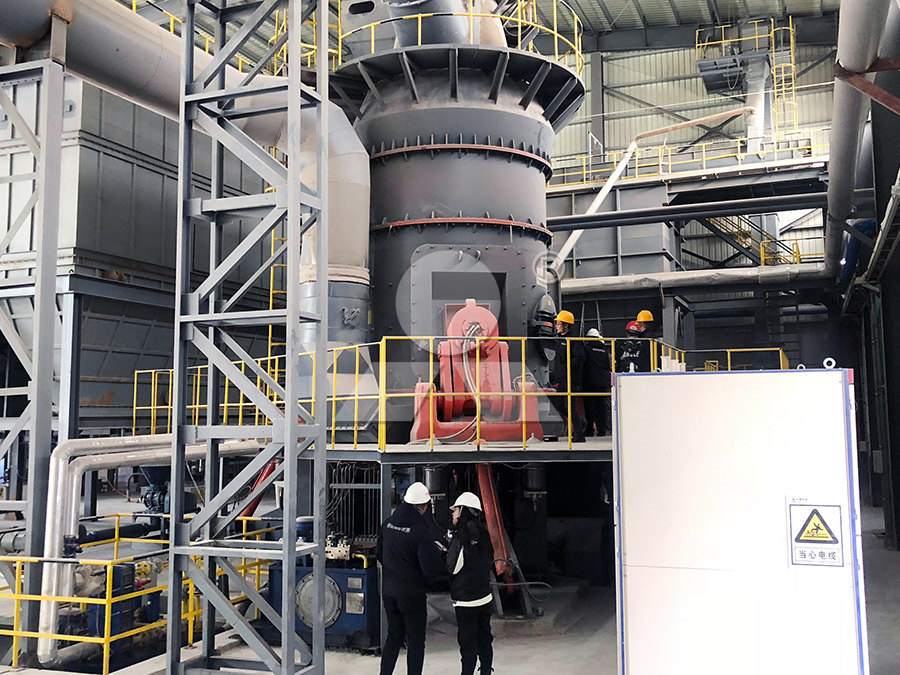
Bibliography on Methods for the Production of Iron Powders
BIBLIOGRAPHY ON METHODS FOR THE PRODUCTION OF IRON POWDERS 351 TABLE I Basic Types of Iron Powders 1 Reduced powder 2 Electrolytic powder 3 Atomized powder 4 Carbonyl powder 21 A Boulle et aI, "The Electrolytic Reduction of Iron Oxide," Congr Intern Chim Pure Appi 16 (Paris, 1957), Mem Sect Chim Minerale, 916 (1958)2024年4月26日 The final stage in iron ore processing is ironmaking, where the iron ore is transformed into molten iron through a process called reduction The most common method of ironmaking is the blast furnace route In a blast furnace, iron ore, coke (carbon), and fluxes (limestone or dolomite) are loaded into the furnace from the topIron Ore Processing: From Extraction to ManufacturingMetalcess offers design service for small electrorefining and electrowining project,related equipment are available including FRP cell, polymer concrete cell, permanent anode and cathode, cathode stripping machine, ER/EW crane, filter press, etcElectrolytic Equipment MetalcessThe purity of the iron was y 90% wt% and electrolytic energy consumption was 2 ?8 kWh kg 2 1 Keywords: Molten salt, Sodium hydroxide, Haematite, Iron, Electrochemical reduction, Inert anode, CO 2 emissions Introduction The vast majority of iron is obtained by the reduction of iron oxide in a blast furnace by metallurgical coke TheElectrolytic formation of iron from haematite in molten sodium
.jpg)
Research progress in the preparation of iron by electrochemical
2023年3月14日 Wang et al produced liquid metal iron through the decomposition of iron oxide dissolved in a solvent electrolyte of molten magnesium oxide–calcium oxide–silica–alumina During constantcurrent electrolysis, an electrolyte composed of magnesium oxide (16 wt%), calcium oxide (18 wt%), aluminum oxide (20 wt%), and silicon dioxide (46 wt%) were used, 2016年6月1日 Request PDF Plasma electrolytic oxide layers as promising systems for catalysis The paper overviews the various approaches for obtaining the metalsupported PEO layers with a developed surfacePlasma electrolytic oxide layers as promising systems for catalysis 2013年1月1日 The industrial production of aluminium is based, since the end of the nineteenth century, on the electrolysis process Aluminium is in fact not present in the nature in its pure metallic form but as an oxide called Alumina (Al 2 O 3) and an adapted processing (electrolysis) is to be used to extract the metalAluminium electrolysis is performed in large HallHéroult cells, The Electrolytic Process for Aluminium Production2022年9月1日 Microstructural evolution of the Working Electrode (WE) during the electrochemical reduction to Fe in 10 M NaOH and at 90 ° C in a (A) Fe 2 O 3 ceramic suspension and as a (B) Fe 2 O 3 ceramic Prospects and challenges of the electrochemical
.jpg)
Electrolytic Polishing Techniques: Basic Guide
2023年7月31日 Electrolytic Polishing Process: Degreasing — Water Washing — Rust Removal — Water Washing — Electrolytic Polishing — Water Washing — Neutralization — Water Washing — Packaging V Types of Electrolytic 2014年7月1日 Oxide dispersion strengthened (ODS) steels are considered as the future structural material of interest for nuclear power plants, due to their elevated creep resistance at higher operation temperaturesIn this study, a 03 wt% nanoyttria (Y 2 O 3) dispersed iron cast trial was elaborated using rapid solidification processing (RSP) The nanosized Y 2 O 3 Comprehensive study on the sintering behavior of yttria nano Resource Recovery and Recycling from Metallurgical Wastes S Ramachandra Rao, in Waste Management Series, 2006 98 Production of Ceramic Tiles from Iron Ore Tailings Current practice of washing iron ore before it is processed for extractive metallurgical operation results in three products, coarse ore lumps with sizes in the range 1080 mm, which are directly charged Iron Ore Processing an overview ScienceDirect Topics3 with additions of copper oxide and transition metals Cu, Ni, Co, and Fe were obtained Changes in the phase content of materials based on iron oxide were shown, and the electrical conductivity of the obtained composites was studied Samples of inert anodes were tested in an electrolytic cell; high resistance of cermets NiFe 2OMetalCeramic Composites Based on Iron Oxide for Low
.jpg)
Molten Oxide Electrolysis for Iron Production: Identification of
2011年4月19日 This novel technology electrolyzes iron oxide into metallic iron that is of crude steel quality (Allanore, Ortiz and Sadoway, 2011; Allanore, 2014;Wiencke et al, 2018)expertise in iron precipitation, nickel and cobalt producers benefit from environmentally acceptable iron residue storage or further use Manganese, an impurity often associated with these raw materials, can be precipitated as manganese oxide either together with iron or separately From iron and manganese removal, the pregnant leachHydrometallurgical nickel and cobalt plants and processesIn a copper cathode production line, the copper anode and stainlesssteel cathode forming into pair are placed in the electrolytic cell DC current is continuously applied across the anodecathode pair to stimulate the anode copper dissolve into the electrolyte to get copper ions and other soluble cations, while copper ions get electrons and deposit on the cathode surface to Copper Cathode Production LineHydrometallurgy2018年1月5日 Abstract Direct iron production at molten metal state from iron oxides by the sole application of electrical energy represents a possible route to decarbonize steel industry Although chemically simple, this reaction is difficult to implement due to the problem of the multiple valence states of iron and to an operating temperature above 1811 K Thermal, chemical, and Electrolysis of iron in a molten oxide electrolyte
.jpg)
Economics of Electrowinning Iron from Ore for Green Steel
2024年8月5日 llustrations of electrolysis reactors that produce iron from ore (1) Author's own work derived from Boston Metal website; (2) From Lomax et al [22] and (3) From Hervé [28])