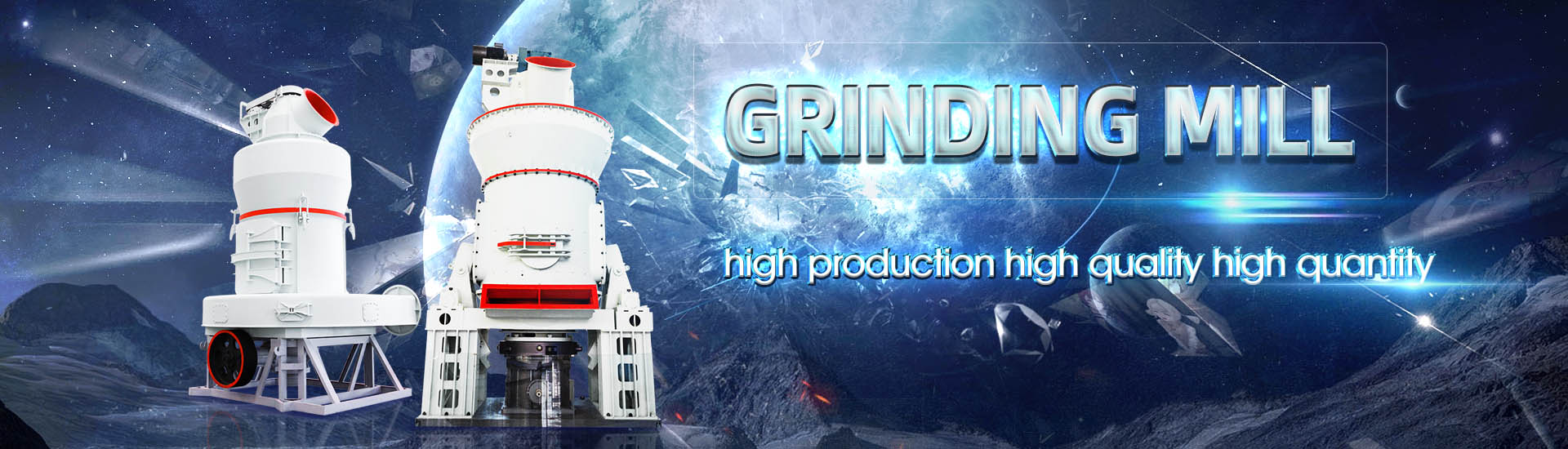
Water slag microcrystalline powder
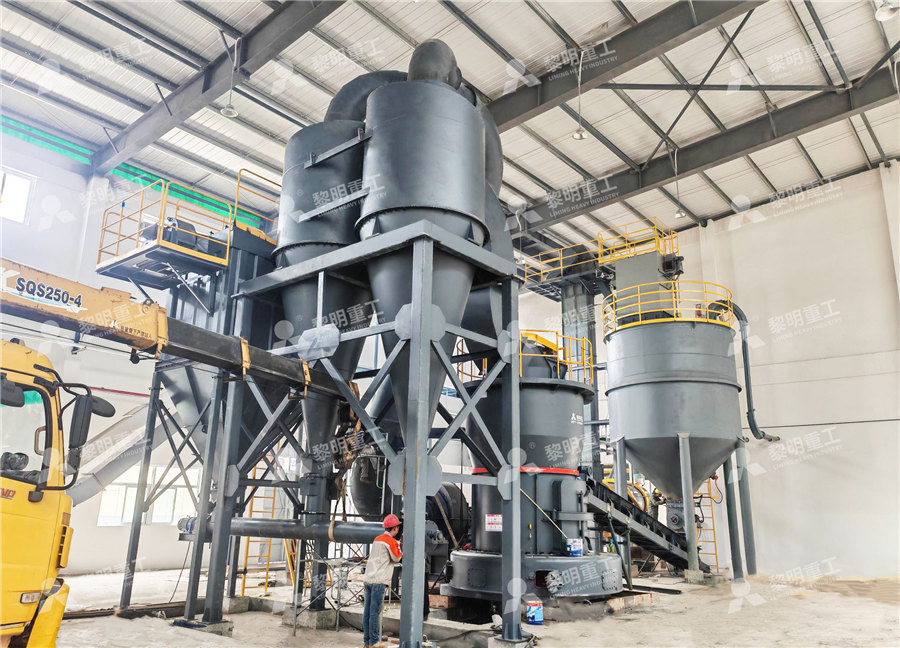
OneStep Microcrystalline Glass Preparation Using
2022年11月18日 The melting–sintering method is a process in which raw materials are melted and quenched by water to obtain a glass powder that is then further ground and pressed into shape and finally sintered at a high 2022年6月1日 After the thermal plasma melting, the molten slag is vitrified into microcrystalline materials by cooling with water It is called water quenched slag (WQS) Based on the Water quenched slag from incinerator ash used as artificial stone2024年1月1日 In order to solve the problem of high accumulation of siliconmanganese slag, this paper proposes a method to prepare foam ceramics with high porosity using silicon Preparation and properties of microcrystalline foam ceramics from There are three main processes for preparing microcrystalline glass: the melting method involves adding a certain amount of a nucleating agent to a solid waste raw material, melting and OneStep Microcrystalline Glass Preparation Using Smelting Slag
.jpg)
Preparation and Performance of UltraFine High
2023年12月11日 The composite micronized powder is prepared by using blast furnace slag (BFS), waterquenched manganese slag (WQMS), manganese tailing slag (MTS) and desulfurization gypsum (DG) and grinding aid (GA) Specifically, adding 20 wt% ultrafine slag powder slightly reduces the compressive strength, while incorporating 30 wt% ultrafine fly ash substantially enhances the MKPC paste’s compressive Influence of Ultrafine Fly Ash and Slag Powder on Microstructure 2024年10月8日 To utilize blast furnace slag in an environment friendly, economically efficient and high valueadded manner, this study successfully prepared glass–ceramics by directly Preparation of Glass–Ceramics Using LowPressure Sintering 2024年2月25日 The specific surface area, particle size distribution, phase analysis and particle morphology of waterquenched silicomanganese slag powder were discussed with laser Mechanical Grinding Characteristics of Water Quenched Si
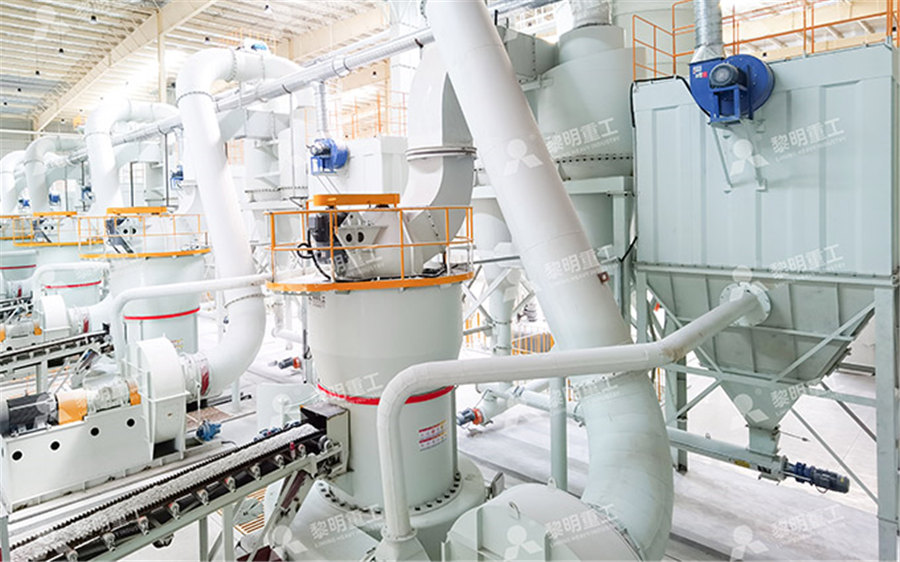
Preparation of SteelSlagBased Hydrotalcite and Its Adsorption
2023年11月28日 Steel slag can also be applied to prepare microcrystalline glass Zhao Guizhou et al prepared microcrystalline glass with varying alkalinity using steel slag, via a onestep 2024年11月15日 This study examines the effects of slag replacement rates (0 %, 10 %, and 20 %) and curing conditions (natural and water curing) on the fluidity, setting time, mechanical Influence of slag on water resistance of magnesium silicon Slag can be used as a mixture to produce ordinary portland cement and slag portland cement The research shows that ground granulated blastfurnace slag powder can significantly change the properties of cement and concrete The GGBS Production Line Slag Mill for Slag Powder 2024年9月1日 The mineral composition in steel slag powder is similar to that of cement, including C 3 S, C 2 S, etc, which can react with water, enabling steel slag powder to be used as supplementary cementitious material [3]However, deficiencies such as limited activity and poor stability of steel slag powder significantly restrict its applicability [4, 5]Insitu wet carbonation of steel slag powder paste made with
.jpg)
Microcrystalline cellulosewater interaction a novel approach
Microcrystalline cellulosewater interaction a novel approach using thermoporosimetry Pirjo Luukkonen1*, Thad Maloney2, Jukka Rantanen1, Hannu Paulapuro2 and Jouko Yliruusi1 1 Pharmaceudcal The invention discloses a microcrystalline glass using slag as a main material, which is prepared from the following raw materials in parts by weight: 6065 parts of slag, 1618 parts of potash feldspar, 812 parts of silica powder, 810 parts of albite, 68 parts of calcium fluoride, 58 parts of magnesium fluoride, 557 parts of gypsum, CNA Microcrystalline glass using slag as main 2023年2月1日 The mixing ratio of mineral powder and deionized water was 5:3 (wt/wt) The coal gangues modified by above four types of slurry were abbreviated as KCG, KWCG, KBCG and KFCG, Frost resistance of coal gangue aggregate concrete modified by steel fiber and slag powder Appl Sci, 10 (2020), p 3229, 103390/appEnhancement of coal gangue performance by surface microcrystalline 2017年3月31日 Objective: This study was aimed to prepare microcrystalline cellulose (MCC) powder from αcellulose of water hyacinth, find its characteristics and purity compared to Avicel PH 101 as reference Preparation of Microcrystalline Cellulose from Water Hyacinth Powder
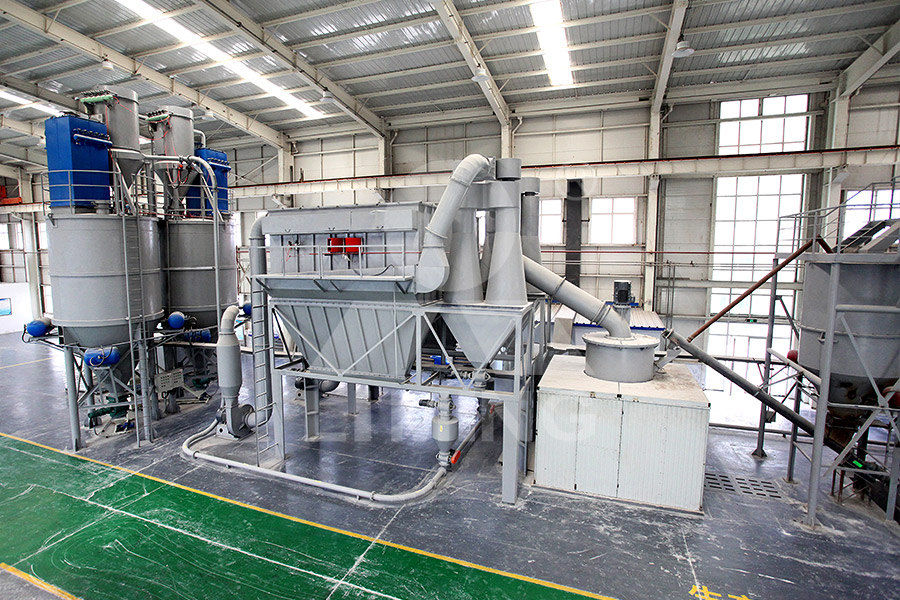
OneStep Microcrystalline Glass Preparation Using Smelting Slag
2022年11月18日 conditions to obtain finished microcrystalline glass The melting–sintering method is a process in which raw materials are melted and quenched by water to obtain a glass powder that is then further ground and pressed into shape and finally sintered at a high temperature to obtain the desired microcrystalline glass productsThe invention provides a method for preparing microcrystalline glass by utilizing gasified slag, microcrystalline glass and application thereof, wherein the method comprises the following steps: (1) screening the gasified slag to obtain lowcarbon slag; (2) grinding the lowcarbon slag obtained in the step (1) to obtain base glass powder; (3) carrying out compression molding on the base CNB Method for preparing microcrystallineThe method for preparing the microcrystalline glass by utilizing the power plant slag comprises the following steps: step 1, adding a small amount of dolomite powder into a coalfired vertical cyclone furnace while adding coal powder into the coalfired vertical cyclone furnace; step 2, after the combustion is finished, preserving the heat of CNA Microcrystalline glass prepared from power plant slag 2023年2月1日 Results showed that after calcining with mineral powders, the crushing rate of coal gangue decreased from 168 % to 161132 %, and water absorption decreased from 529 % to 274390 %, among which the coal gangue treated by Kfeldspar and blast furnace slag had the lowest water absorption (274 %), reducing by 482 % compared to raw coal gangueEnhancement of coal gangue performance by surface micro
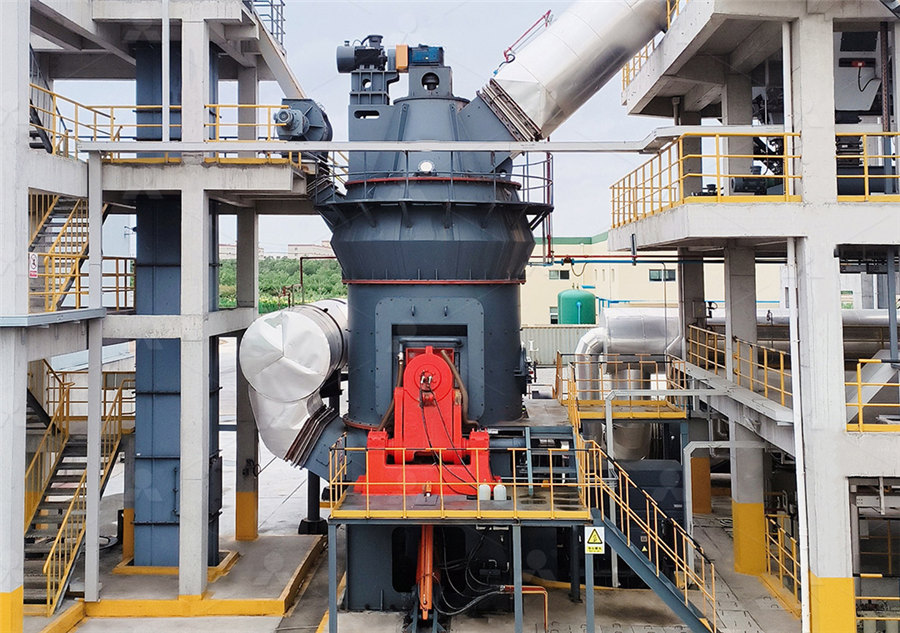
Preparation and properties of microcrystalline foam ceramics
2024年1月1日 The silica manganese slag used in the experiment was all from Ningxia, China, including the Huiyi silica manganese slag (HYSM) from Shizuishan City (Ningxia, China), Tianyuan silica manganese slag (TYSM) from Zhongwei City (Ningxia, China), blowing agent SiC powder from Guangzhou Metal Metallurgy Co, LTD, and borax (Na 2 B 4 O 7 10H 2 O) from 2024年1月1日 The silica manganese slag used in the experiment was all from Ningxia, China, including the Huiyi silica manganese slag (HYSM) from Shizuishan City (Ningxia, China), Tianyuan silica manganese slag (TYSM) from Zhongwei City (Ningxia, China), blowing agent SiC powder from Guangzhou Metal Metallurgy Co, LTD, and borax (Na 2 B 4 O 7 10H 2 O) from Preparation and properties of microcrystalline foam ceramics 2018年1月30日 1 Introduction Steel slag is a byproduct of steel manufacturing []Approximately 160 kg of steel slag is generated per ton of steel produced []The common chemical compounds in steel slag are SiO 2, CaO, Fe 2 O 3, Al 2 O Applications of Steel Slag Powder and Steel Slag 2023年2月22日 Granulated blast furnace slag (GBFS) is a glassy calciumaluminum silicate coproduct with latent hydration activity produced during the blast furnace ironmaking process [21]When the GBFS is in contact with water, a layer of calciumdeficient aluminosilicate protective film would be formed rapidly on the surface, and only a small amount of calcium ions and Hydration superposition effect and mechanism of steel slag powder
.jpg)
Preparation and properties of foam ceramic from nickel slag and
2020年10月15日 Waste glass, a common household and industrial solid waste, has begun to be used as a supplementary cementitious material in concrete [[11], [12], [13]]Si et al [14] investigated the effects of waste glass powder (WGP) on the shrinking behaviour and microstructures of metakaolinbased geopolymersResults showed that a glass powder The invention discloses a highwaterresistance microcrystalline glass and a preparation method thereof, relating to the technical field of microcrystalline glass The highwaterresistance microcrystalline glass is mainly prepared from quartz sand, pandermite, diabase, waste glass, potassium fluozirconate, blast furnace water quenching slag, silica fume, desulfurized CNA Highwaterresistance microcrystalline glass 2022年11月18日 The slag was dried at 105 °C for 12 h after water cooling; some of the microcrystalline glass obtained after drying was taken, crushed, and ground into a fine powder; and regularshaped blocks of microcrystalline glass were taken and finely ground with an agate mortar and sieved through No 200 mesh to obtain a fine powderOneStep Microcrystalline Glass Preparation Using Smelting Slag The invention provides a lithium slag microcrystalline floor tile blank which is prepared from 7075 parts of a mixture of lithium slag and feldspar powder, 2530 parts of glass powder and 911 parts of water in parts by weight The invention also provides a lithium slag microcrystalline floor tile, which is obtained by molding and sintering a lithium slag microcrystalline floor tile blank at CNA Lithium slag microcrystalline floor tile and
.jpg)
纤维素 microcrystalline, powder SigmaAldrich
纤维素 microcrystalline, powder; CAS Number: ; EC Number: 2326749; Synonyms: 棉短绒,纤维素粉末 at SigmaAldrichCellulose microcrystalline, powder; CAS Number: ; EC Number: 2326749; Synonyms: Cellulose powder,Cotton linters at SigmaAldrich Skip to Content Products GB EN Products Products Applications Services Documents Support Account Order Lookup Quick Order All Photos (3) Documents COO/ COA More Cellulose microcrystalline, powder MilliporeSigma2023年7月21日 112 The Lhasa method (RASA) The Lhasa method (RASA) water granulated slag treatment system was developed by Nippon Steel Pipe and the British trading company RASA and was first applied on blast furnace No 1 at Fukuyama Steel Works in Japan [Citation 4]The principle of the RASA method is that after the blast furnace slag has been water Comprehensive utilisation of blast furnace slag Taylor Francis the mono and multilayer water adsorbed at the surfaces, and to the water absorbed into the internal structure of solid (8) MCC is manufactured from wood pulp by acid hydrolysis After being washed with water the suspension is spray dried into microcrystalline powder The manufacturing process shortens the cellulose chains and removes the Microcrystalline CelluloseWater Interaction—A Novel
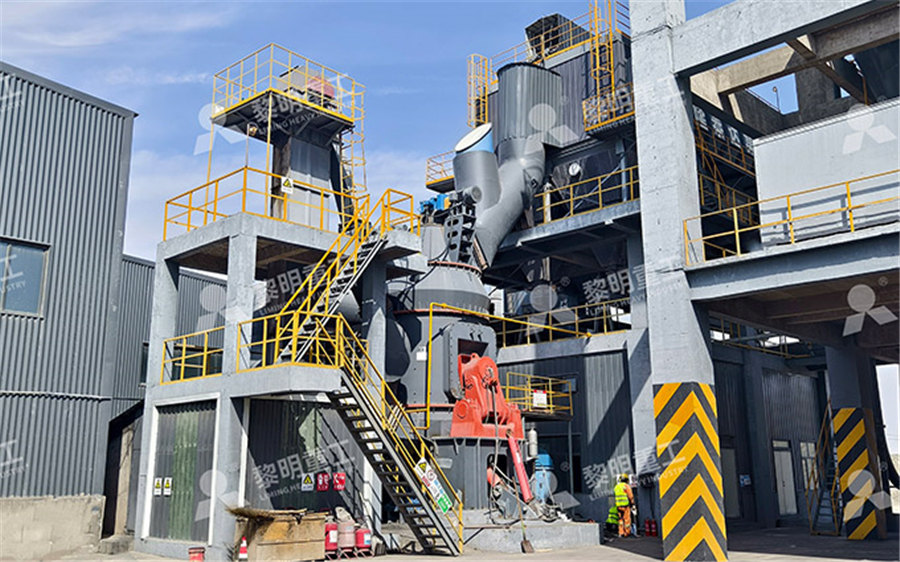
Method using slag for manufacturing microcrystalline material
A method using slag for manufacturing a microcrystalline material The method comprises the following steps: 1) using a quartz slag, metallurgical slag, tailing, and sludge incineration slag as raw materials, and mixing the raw materials in a mass ratio of 1:1:1:1; 2) heating the mixed material in a high temperature furnace to a temperature of 14001600°C for 34 hours to 1987年8月1日 International Journal of Pharmaceutics, 38 (1987) 227229 Eisevier 227 UP 01301 The rheology of microcrystalline cellulose powder/water mixes measurement using a mixer torque rheometer RC Rowe and GR Sadeghnejad * ICI Pharmaceuticals Division, Macclesfield, Cheshire (UK) (Received 8 December 1986) (Accepted 30 March 1987) Key The rheology of microcrystalline cellulose powder/water mixes 2023年5月3日 The research aims to examine the effects of microcrystalline cellulose (MCC) as additive in Portland cementbased (OPC) and sodium hydroxide slagfly ash blend (AAM) with the objective of Application of microcrystalline cellulose as additive in Portland microcrystalline glass obtained from final smelting slag through heat treatment can enhance the stabilization of harmful elements The findings of this study can be applied to the treatment of bulkOneStep Microcrystalline Glass Preparation Using Smelting Slag
.jpg)
Microcrystalline cellulose powders: structure, surface features and
g water/g MCC 045 0091 0072 mol water/glucosidic unit 409 081 065 The curve shows an initial rising part and levels off to a quasiplateau region after about 160–170 h of equilibration The amount of water sorbed in correspondence with the The dry powder is magnetically separated from slag particles (8), screened (9) and homogenized (10), and eventually transported in special containers (11) to the works at Höganäs for further processing high flow rate and microcrystalline structure During water atomization of a melt, the water atomizing process 2 Total MateriaThe invention discloses a method for preparing microcrystalline glass by directly pouring molten copper slag, controlling temperature, condensing and forming, belonging to the field of comprehensive utilization of solid waste resources, which comprises the steps of heating the molten copper slag to 15501650 ℃, adding a reducing agent and an auxiliary agent into the CNA Method for preparing microcrystallinemicrocrystalline, powder Synonym(s): Cellulose powder, Cotton linters Sign In to View Organizational Contract Pricing Select a Size 250 G ₹4,97000 1 KG ₹11,85000 250G ₹4,97000 Availability Available to ship on 21 November 2024 Details Add to Cart Request a Bulk Order All Photos (3) Select a Size Change View 250 GCellulose microcrystalline, powder MilliporeSigma
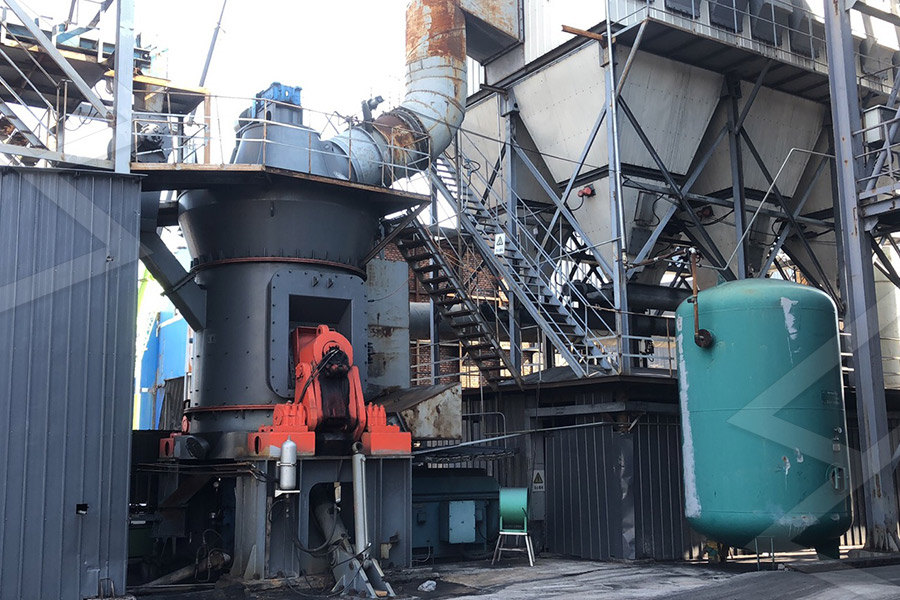
GGBS Production Line Slag Mill for Slag Powder
Slag can be used as a mixture to produce ordinary portland cement and slag portland cement The research shows that ground granulated blastfurnace slag powder can significantly change the properties of cement and concrete The 2024年9月1日 The mineral composition in steel slag powder is similar to that of cement, including C 3 S, C 2 S, etc, which can react with water, enabling steel slag powder to be used as supplementary cementitious material [3]However, deficiencies such as limited activity and poor stability of steel slag powder significantly restrict its applicability [4, 5]Insitu wet carbonation of steel slag powder paste made with Microcrystalline cellulosewater interaction a novel approach using thermoporosimetry Pirjo Luukkonen1*, Thad Maloney2, Jukka Rantanen1, Hannu Paulapuro2 and Jouko Yliruusi1 1 Pharmaceudcal Microcrystalline cellulosewater interaction a novel approach The invention discloses a microcrystalline glass using slag as a main material, which is prepared from the following raw materials in parts by weight: 6065 parts of slag, 1618 parts of potash feldspar, 812 parts of silica powder, 810 parts of albite, 68 parts of calcium fluoride, 58 parts of magnesium fluoride, 557 parts of gypsum, CNA Microcrystalline glass using slag as main
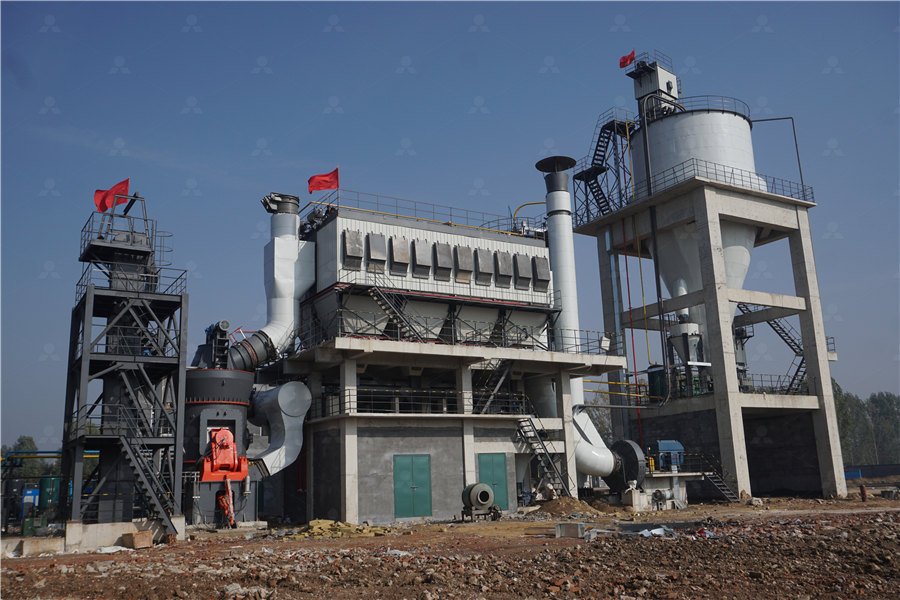
Enhancement of coal gangue performance by surface microcrystalline
2023年2月1日 The mixing ratio of mineral powder and deionized water was 5:3 (wt/wt) The coal gangues modified by above four types of slurry were abbreviated as KCG, KWCG, KBCG and KFCG, Frost resistance of coal gangue aggregate concrete modified by steel fiber and slag powder Appl Sci, 10 (2020), p 3229, 103390/app2017年3月31日 Objective: This study was aimed to prepare microcrystalline cellulose (MCC) powder from αcellulose of water hyacinth, find its characteristics and purity compared to Avicel PH 101 as reference Preparation of Microcrystalline Cellulose from Water Hyacinth Powder 2022年11月18日 conditions to obtain finished microcrystalline glass The melting–sintering method is a process in which raw materials are melted and quenched by water to obtain a glass powder that is then further ground and pressed into shape and finally sintered at a high temperature to obtain the desired microcrystalline glass productsOneStep Microcrystalline Glass Preparation Using Smelting Slag The invention provides a method for preparing microcrystalline glass by utilizing gasified slag, microcrystalline glass and application thereof, wherein the method comprises the following steps: (1) screening the gasified slag to obtain lowcarbon slag; (2) grinding the lowcarbon slag obtained in the step (1) to obtain base glass powder; (3) carrying out compression molding on the base CNB Method for preparing microcrystalline
.jpg)
CNA Microcrystalline glass prepared from power plant slag
The method for preparing the microcrystalline glass by utilizing the power plant slag comprises the following steps: step 1, adding a small amount of dolomite powder into a coalfired vertical cyclone furnace while adding coal powder into the coalfired vertical cyclone furnace; step 2, after the combustion is finished, preserving the heat of 2023年2月1日 Results showed that after calcining with mineral powders, the crushing rate of coal gangue decreased from 168 % to 161132 %, and water absorption decreased from 529 % to 274390 %, among which the coal gangue treated by Kfeldspar and blast furnace slag had the lowest water absorption (274 %), reducing by 482 % compared to raw coal gangueEnhancement of coal gangue performance by surface micro