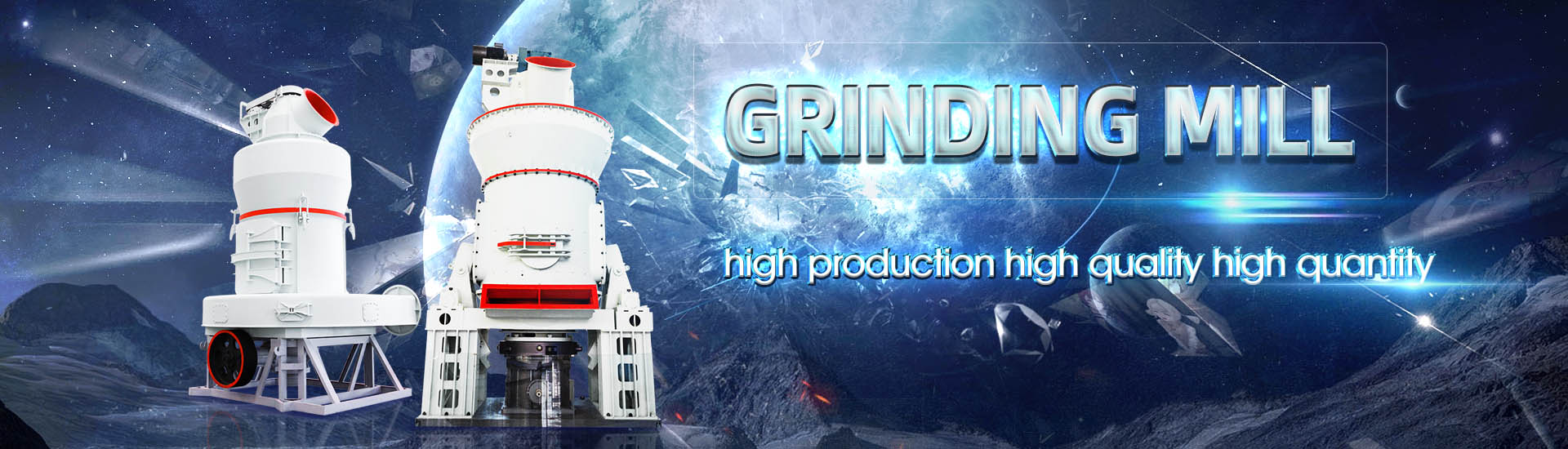
Selection of fine crushing equipment in the production of reduced iron oxide
.jpg)
Comminution and classification technologies of iron ore
2022年1月1日 Hematite and magnetite iron ores are the most prominent raw materials for iron and steel production Most of the highgrade hematite iron ores are typically subjected to We conducted a comprehensive literature review of LiFePO 4 (LFP) and LiMn x Fe 1x PO Comminution and classification technologies of iron ore2019年7月22日 RECYRON® is a highly flexible process to utilize fine ore as well as all possible iron ore and carbon containing wastes to produce DRI A comparative description of these Cold briquetting of iron ore fines for DRI production: challenges 2024年8月2日 In primary crushing, both the jaw and gyratory crushers are used with the selection of equipment based on the ore grade, mineralogy, and hardness Primary crushing is Exploring LowGrade Iron Ore Beneficiation Techniques: A MDPI

HydrogenBased Direct Reduction of Iron Oxides: A Review on the
2023年8月30日 Directreduced iron (DRI) can be treated in the electric arc furnace (EAF) by itself or in combination with scrap to produce crude steel That being said, using large amounts 2024年4月1日 Introduces a unique evaluative approach to IOTs, prioritizing environmental and economic viability in recycling Assesses a variety of beneficiation and metallurgical recovery A critical review on metallurgical recovery of iron from iron ore 2014年1月1日 Natural gas cannot be used directly in the reduction of iron ore because it decomposes to form soot at a temperature below that which iron oxide can be reduced The Direct Reduction of Iron ScienceDirect2020年7月9日 Hot briquetting tests with mixtures of direct reduced iron (DRI) pellets and residues of the Midrex direct reduction process are conducted on a hydraulic piston press with Investigation into the Hot Briquetting of Fine‐Grained Residual
.jpg)
Reduction of Iron Ore Pellets: A Microstructural Perspective?
2023年12月8日 Twenty different iron ore pellets, consisting primarily of Hematite (Fe 2 O 3) phase, were subjected to ‘simulated’ reduction studies A wide range of reduction time periods, 2024年5月18日 For this reason, this paper investigates the properties and characteristics of ultrafine iron powder prepared by hydrogen reduction Highpurity ultrafine iron powder was Production of ultrafine iron powder by lowtemperature hydrogen 2015年1月1日 Iron is one of the major constituents of the rocks in the Earth's crust and is always present in varying degrees in sedimentary formations It is ranked fourth in terms of the quantity of all the elements occurring (Smith, 1990) and has been mined in small quantities at a vast selection of sites in many countries to feed the localized production of iron and steelIron ore extraction techniques ScienceDirect2017年1月1日 Production of red iron oxide pigment based on haematite ores of the Yakovlevskoe deposit is promising and it makes it possible to satisfy the demand for high quality and inexpensive pigment(PDF) Effective Processing of the Iron Ores ResearchGate
.jpg)
Factors affecting the performance of crushing plant
2014年1月1日 To achieve optimal performance of a crushing plant, not only the design of the individual machines but also the cost of running them should be taken into accountIn this paper a novel method for 2022年8月3日 1 Iron ore crushing process: In the iron ore crushing process, the feeder, first crushing, secondary crushing, screening, fine crushing and dry selection are generally used For the sake of economy, generally the finer the ore particle size entering the dry separator, the higher the proportion of ironbearing ore that is dry selectedIron ore crushing and screening process SBM Ultrafine Powder 2023年10月30日 The selection and design of crushing equipment in the mineral processing industry are influenced by several key factors, all of which are critical for achieving efficient and effective ore processing Chief among these factors is the material's inherent characteristics The hardness, abrasiveness, moisture content, and size distribution of the ore significantly impact The selection and design of Crushing equipment Performance 2023年4月5日 The blast furnace and direct reduction processes have been the major iron production routes for various iron ores (ie goethite, hematite, magnetite, maghemite, siderite, etc) in the past few decades, but the challenges of maintaining the iron and steelmaking processes are enormous The challenges, such as cumbersome production routes, scarcity of Recent Trends in the Technologies of the Direct Reduction and
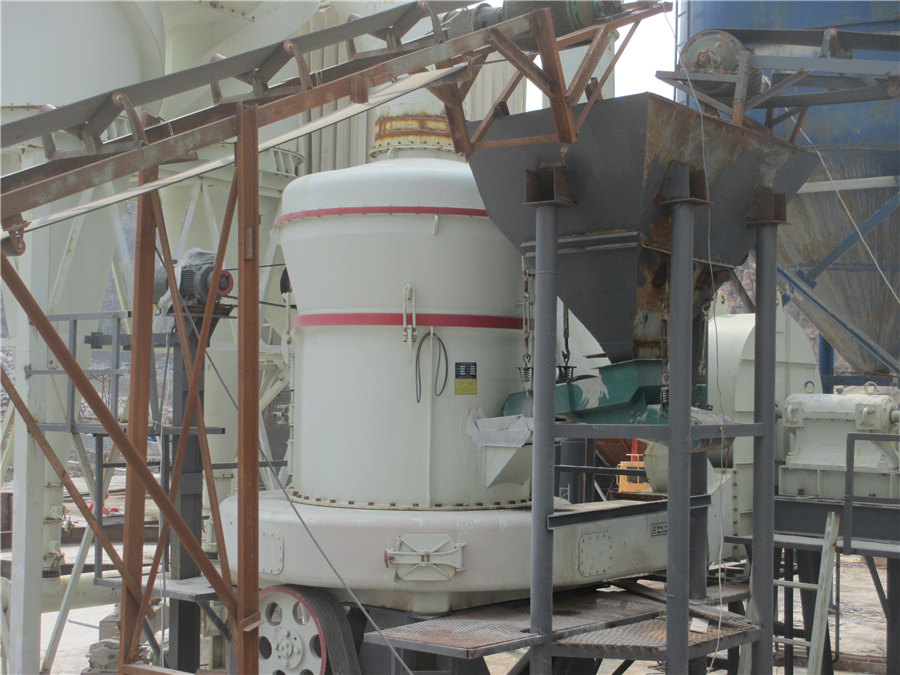
Overview on production of reduced iron powder from mill scale
2021年1月1日 Mill Scale, generated in a rolling steel mill can be a potential material for iron powder production Mill scale is a combination of different oxides like Hematite (Fe 2 O 3), Magnetite (Fe 3 O 4), and Wustite (FeO) [2], [3]Besides, this multioxide mill scale's conversion into single oxide (Fe 2 O 3) is the bestsuited route for further reduction into iron powder due to 2018年10月23日 The ore is Hematite, chemical name is iron III oxide, the chemical formula is Fe 3 O 4, It has a blood red colour, it is more easily reduced, Iron is from 5060 %, place of deposits is Oasis area (western desert) and western part of Aswan The ore is Limonite, chemical name is Hydrated iron III oxide, the chemical formula is 2Fe 2 O 33H 2 O, It has a yellow hydrated Extraction of Iron from its ores, Iron dressing, Reduction production In contrast to iron oxide reduction in a BF, direct reduction occurs in the solid state, and none of the components are melted While this is good from an energy perspective, there is little or no way to remove impurities from the system, which are then carried with the direct reduced iron (DRI) product to the steelmaking furnaceIron Ore Pellet an overview ScienceDirect Topics2019年8月8日 The importance of iron ore crushing process; Before dry selection, the lean iron ore requires millimeterscale fine crushing by the fine crusher If the particle size of the iron ore is not small enough in the crushing stage, lowgrade iron ore is difficult to be selected later, which will cause serious waste of resources The selection of iron Challenges and opportunities in the iron ore crusher market
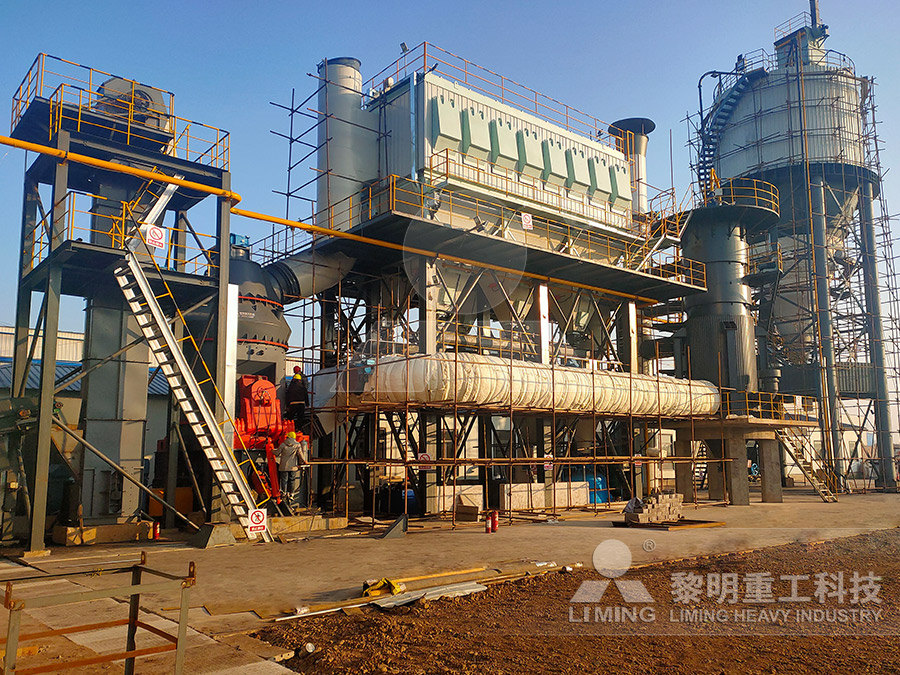
Redox reaction induced morphology and microstructure evolution of iron
2018年7月15日 Our results indicated that the surface area of Fe 2 O 3 particles decreased during the redox cycles even though more macropores (>1000 nm) formed for these particles Sintering was attributed to the surface area decrease of Fe 2 O 3 particles in the redox process Because of the outward Fe cation diffusion, porous structure in the interior of Fe 2 O 3 Because the cone crusher can provide a smaller product size, from the overall process, the use of laminated equipment to complete the main crushing task of iron ore is the most economical production method The general iron ore dressing plant’s processes are crushing of raw ore, ore grinding, spiral chute selection, spiral chute sweeping and Iron ore washing process and equipment LZZG2012年5月1日 Reduction tests were carried out in an electric furnace as shown in Fig 1The prepared oxide pellets were reduced in a thermo gravimetric apparatus at 900 °CTotal gas flow was maintained at 30 l/minThe superficial gas velocity at standard state was 30 cm/s and sufficiently high to prevent reduction gas starvation in the gas phase [18]Mechanisms of strength decrease in the initial reduction of iron 2020年11月8日 Crusher; Crushing; and Classification Equipment 1 Mineral Processing: Crusher and Crushing by Hassan Z Harraz hharraz2006@yahoo Ancient and Modern Local Quality and High quality Intranational and Country/Hand made •DOI: 1013140/RG221398236167Crusher; Crushing; and Classification Equipment PPT SlideShare
.jpg)
Waste glass in the production of cement and concrete – A review
2014年9月1日 It is unclear exactly when, where, or how people first learned to make glass The first manufactured glass was found in Mesopotamia about 3000 BC and the first glass vessels were made, about 1500 BC, in Mesopotamia and Egypt [3, 4]In that time the glass industry was slow and costly because of the small furnaces, the poor quality of the clay pots, and the heat 2020年3月19日 Iron Oxide Nanoparticle, maghemite (γFe2O3) has received great interest and extensively used in biomedical field Optimization studies were carried out in the production of γFe2O3 (PDF) Production of Iron Oxide Nanoparticles by Co2024年10月11日 Iron tailing slag is a solid waste produced by iron ore mining enterprises during the crushing, screening, grinding and grading process of raw iron ores It is a bulk solid waste with extremely low iron content remaining after separation of iron minerals and other useful minerals through magnetic separation, gravity separation, flotation and other mineral technologies [1] Investigation on utilization and microstructure of fine iron tailing 2024年4月26日 Iron ore, a naturally occurring mineral composed primarily of iron oxides, is mined and processed to extract iron for various industrial applications This article provides a comprehensive overview of the iron ore processing journey, from extraction to manufacturing, highlighting the key stages and technologies involvedIron Ore Processing: From Extraction to Manufacturing
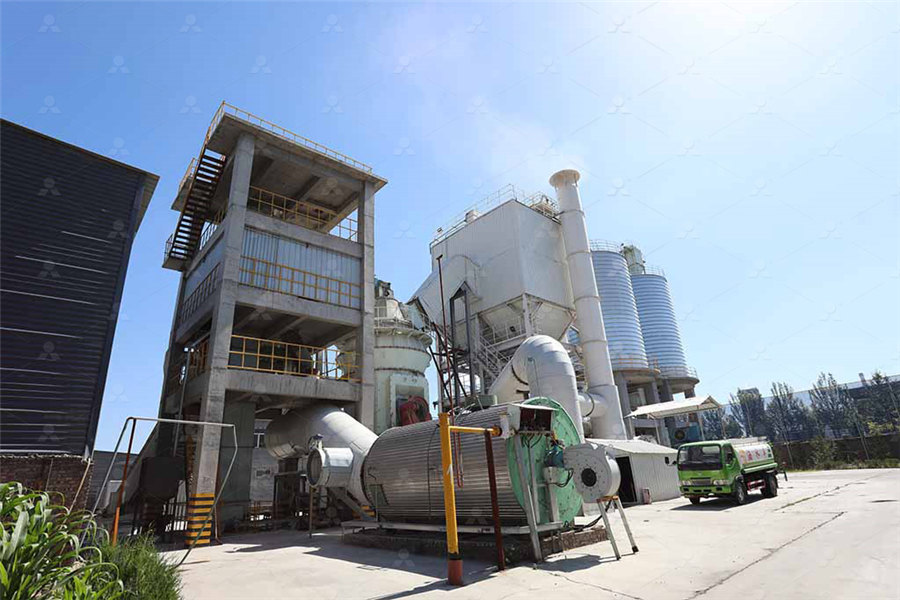
(PDF) Ore mineralogy and its relevance for selection of concentration
2003年4月1日 All major companies now operating in the production of iron ore in Brazil currently employ or are planning to employ some sort of concentration method to upgrade their fine sized products (sinter Pelletizing is the process of converting iron ore fi nes into “Uniformed Sized Iron Ore Pellets” that can be charged into the blast furnaces or for Production of Direct Reduced Iron (DRI) [1] 1 Process objective is to transform fi ne iron ore concentrate into pellets suitable to feed Blast Furnace or Direct Reduction plant or COREX 2Study and Implementation of Quality Improvement Techniques to 2018年9月1日 The aim of this review is to collate and summarize selected information concerning the characterisation and processing of oolitic iron ores There are many types of iron ore deposits that have been historically important as sources of iron minerals which hematite, magnetite, goethite and martite (hematite that has replaced primary magnetite) are dominantA review on the characterisation and processing of oolitic iron oresIn conclusion, single cylinder hydraulic cone crushers are essential fine crushing equipment in the iron ore beneficiation process They provide precise control over the particle size, improve efficiency, and contribute to the overall productivity of the beneficiation plantProduction and processing equipment for fine crushing of iron
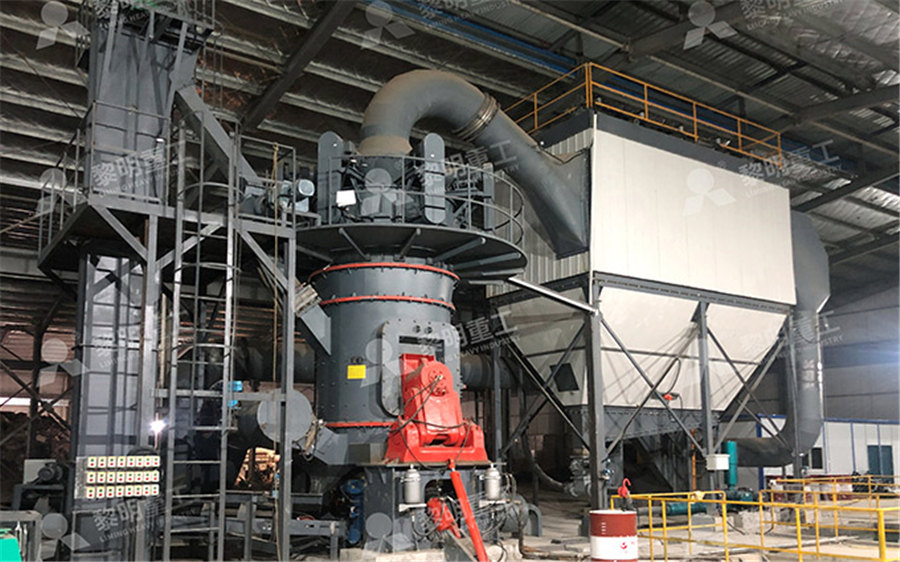
Recovery of Iron from Copper Tailings Using a Combined Direct
2024年2月7日 As the world’s largest producer of refined copper, China accounts for about 1/3 of the world’s production At present, China’s refined copper is mainly produced by pyrometallurgy [1,2,3]The annual discharge of copper slag exceeds 10 million tons according to the calculation of 22 tons of copper slag per ton of refined copper produced in the copper smelting process [], 2020年7月7日 During the production of hot briquetted iron (HBI) from raw iron oxide pellets in the Midrex® process a wide variety of residues are generated These residues are sludges, screened fines and dustBriquetting of Fine‐Grained Residues from Iron and Steel Production 2007年1月31日 Iron oxide feed stocks Pellets, lump, and fine ore Pellets, lump, and fine ore, green balls, iron oxide waste materials Reduction temperatures ( C) 850–950 C 950–1050 C(PDF) Properties and features of direct reduced ironDirect Reduced Iron has become a widely accepted source of premium iron units for steel making Its advantages as a virgin iron product and diluent for impurities, introduced with scrap, are well documented Direct Reduction plants produce different materials that are based on: DRI (Direct Reduced Iron) or HBI (Hot Briquetted Iron)No 117 HBI – Hot Briquetting of Direct Reduced Iron
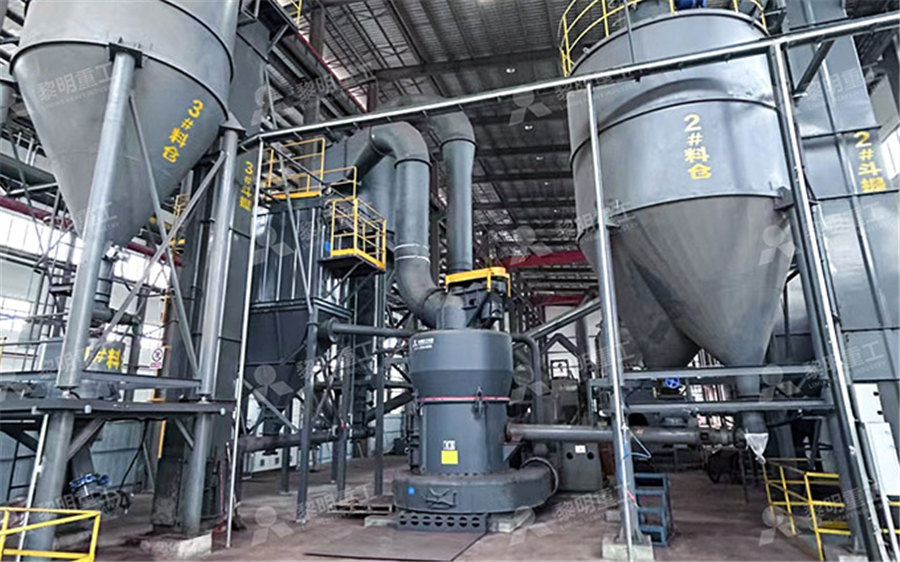
Iron ore sintering ScienceDirect
2015年1月1日 Like other sintering processes, iron ore sintering converts iron ore fines of often − 8 mm sizing into larger agglomerates, namely, sinter, between 5 and 50 mm particle size, which possess the physical and metallurgical characteristics and gas permeability required for efficient blast furnace operationAs shown in Figure 141, iron ore sintering is carried out in three It not only has a large processing capacity in the crushing and processing of materials, but also the crushed nickel ore particles are uniform and complete, which can effectively improve the efficiency of the equipment in production 1 The crushing cavity is deep, and the nickel ore can be crushed comprehensively, which improves the unit Selection Of Nickel Ore Beneficiation Process Equipment2020年1月1日 The pandemic has resulted in unsustainable plastic waste management and exacerbated the plastic pollution problems worldwide Global surveys indicate that consumers discard at least 2% of their A Review on the Technology of Size Reduction Equipment2022年1月1日 Finally, lines 5, 6, and 7 consist of primary jaw crushing, secondary and tertiary cone crushing, closed circuit HPGR and closedcircuit ball milling, wet magnetic separation, reverse flotation, further magnetic separation, filtration and concentrate regrinding in a HPGR to achieve a final concentrate with fine product size for pellet plant feed (Valery et al, 2019) (Fig Comminution and classification technologies of iron ore
.jpg)
Iron ore extraction techniques ScienceDirect
2015年1月1日 Iron is one of the major constituents of the rocks in the Earth's crust and is always present in varying degrees in sedimentary formations It is ranked fourth in terms of the quantity of all the elements occurring (Smith, 1990) and has been mined in small quantities at a vast selection of sites in many countries to feed the localized production of iron and steel2017年1月1日 Production of red iron oxide pigment based on haematite ores of the Yakovlevskoe deposit is promising and it makes it possible to satisfy the demand for high quality and inexpensive pigment(PDF) Effective Processing of the Iron Ores ResearchGate2014年1月1日 To achieve optimal performance of a crushing plant, not only the design of the individual machines but also the cost of running them should be taken into accountIn this paper a novel method for Factors affecting the performance of crushing plant 2022年8月3日 1 Iron ore crushing process: In the iron ore crushing process, the feeder, first crushing, secondary crushing, screening, fine crushing and dry selection are generally used For the sake of economy, generally the finer the ore particle size entering the dry separator, the higher the proportion of ironbearing ore that is dry selectedIron ore crushing and screening process SBM Ultrafine Powder
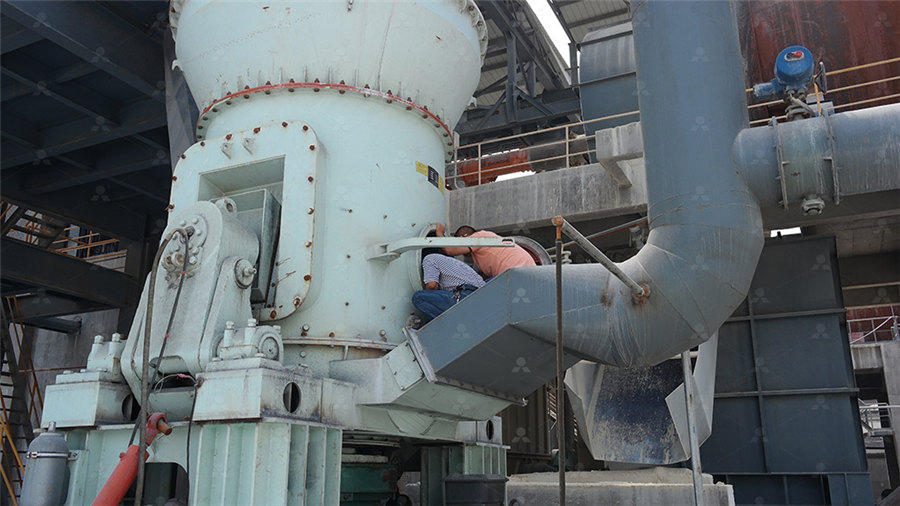
The selection and design of Crushing equipment Performance
2023年10月30日 The selection and design of crushing equipment in the mineral processing industry are influenced by several key factors, all of which are critical for achieving efficient and effective ore processing Chief among these factors is the material's inherent characteristics The hardness, abrasiveness, moisture content, and size distribution of the ore significantly impact 2023年4月5日 The blast furnace and direct reduction processes have been the major iron production routes for various iron ores (ie goethite, hematite, magnetite, maghemite, siderite, etc) in the past few decades, but the challenges of maintaining the iron and steelmaking processes are enormous The challenges, such as cumbersome production routes, scarcity of Recent Trends in the Technologies of the Direct Reduction and 2021年1月1日 Mill Scale, generated in a rolling steel mill can be a potential material for iron powder production Mill scale is a combination of different oxides like Hematite (Fe 2 O 3), Magnetite (Fe 3 O 4), and Wustite (FeO) [2], [3]Besides, this multioxide mill scale's conversion into single oxide (Fe 2 O 3) is the bestsuited route for further reduction into iron powder due to Overview on production of reduced iron powder from mill scale 2018年10月23日 The ore is Hematite, chemical name is iron III oxide, the chemical formula is Fe 3 O 4, It has a blood red colour, it is more easily reduced, Iron is from 5060 %, place of deposits is Oasis area (western desert) and western part of Aswan The ore is Limonite, chemical name is Hydrated iron III oxide, the chemical formula is 2Fe 2 O 33H 2 O, It has a yellow hydrated Extraction of Iron from its ores, Iron dressing, Reduction production
.jpg)
Iron Ore Pellet an overview ScienceDirect Topics
In contrast to iron oxide reduction in a BF, direct reduction occurs in the solid state, and none of the components are melted While this is good from an energy perspective, there is little or no way to remove impurities from the system, which are then carried with the direct reduced iron (DRI) product to the steelmaking furnace2019年8月8日 The importance of iron ore crushing process; Before dry selection, the lean iron ore requires millimeterscale fine crushing by the fine crusher If the particle size of the iron ore is not small enough in the crushing stage, lowgrade iron ore is difficult to be selected later, which will cause serious waste of resources The selection of iron Challenges and opportunities in the iron ore crusher market